¿Qué son los insertos de cavidades y núcleos de moldes de inyección?
Insertos para núcleos y cavidades de moldes de inyección de plástico son componentes de un molde utilizados en la fabricación de piezas de plástico y metal.
Un núcleo de molde (a veces pequeños insertos que llamamos insertos de núcleo) es la parte interna del molde, que normalmente se encuentra en el lado del núcleo (lado móvil). Esto crea las características internas de la pieza que se está moldeando. El núcleo suele ser de acero, como 1.2344, S136, etc., y suele ser desmontable de la placa del molde (placa B o placa de bolsillo).
Un inserto de cavidad de molde de inyección tiene la misma función que el inserto de núcleo, pero se encuentra en el lado fijo. Es la parte externa del molde que crea la forma externa de la pieza que se está moldeando. El inserto de cavidad suele estar hecho de acero, como NAK 80, S136, 1.2344 y H13, y suele ser desmontable del molde.
Tanto el plástico núcleo de molde e inserto de cavidad suelen fabricarse mediante procesos de electroerosión (mecanizado por descarga eléctrica) y mecanizado CNC (control numérico por ordenador). A continuación, el núcleo y los insertos de cavidad se ensamblan en una base de molde para obtener el molde completo. molde de plástico. A continuación, el molde de inyección de plástico se utiliza en el proceso de moldeo por inyección o fundición para producir las piezas deseadas.
Por supuesto, hay muchos procesos de fabricación para hacer moldes de plástico, como el mecanizado de torno, mecanizado amoladora, pulido, corte de alambre, fresado, etc, pero CNC y EDM mecanizados son los procesos de fabricación más improtant para hacer un moldeo por inyección, a continuación se explican brevemente para EDM y mecanizado CNC:
EDM:
- En primer lugar, se crea un diseño de molde en un software de modelado 3D.
- A continuación, la pieza de trabajo (cavidad y núcleo de acero) se carga en la EDM que utiliza descargas eléctricas para erosionar la superficie de un material conductor (como el acero o el aluminio) con el fin de crear la forma deseada del núcleo o la cavidad de inserción.
- A continuación, la pieza acabada se pule o texturiza según las necesidades.

Proceso de mecanizado por electroerosión
CNC:
- El proceso es similar, pero en lugar de utilizar el mecanizado por descarga eléctrica, una máquina CNC utiliza herramientas de corte (como fresas o brocas) para eliminar material de un bloque de acero o aluminio y crear la forma deseada del inserto de núcleo o cavidad.
- La pieza acabada se somete a un tratamiento térmico para aumentar su resistencia y durabilidad, si la demanda de acero pre-endurecido entonces no hay necesidad de tratamiento térmico adicional, puede pasar al proceso de mecanizado por electroerosión directamente.
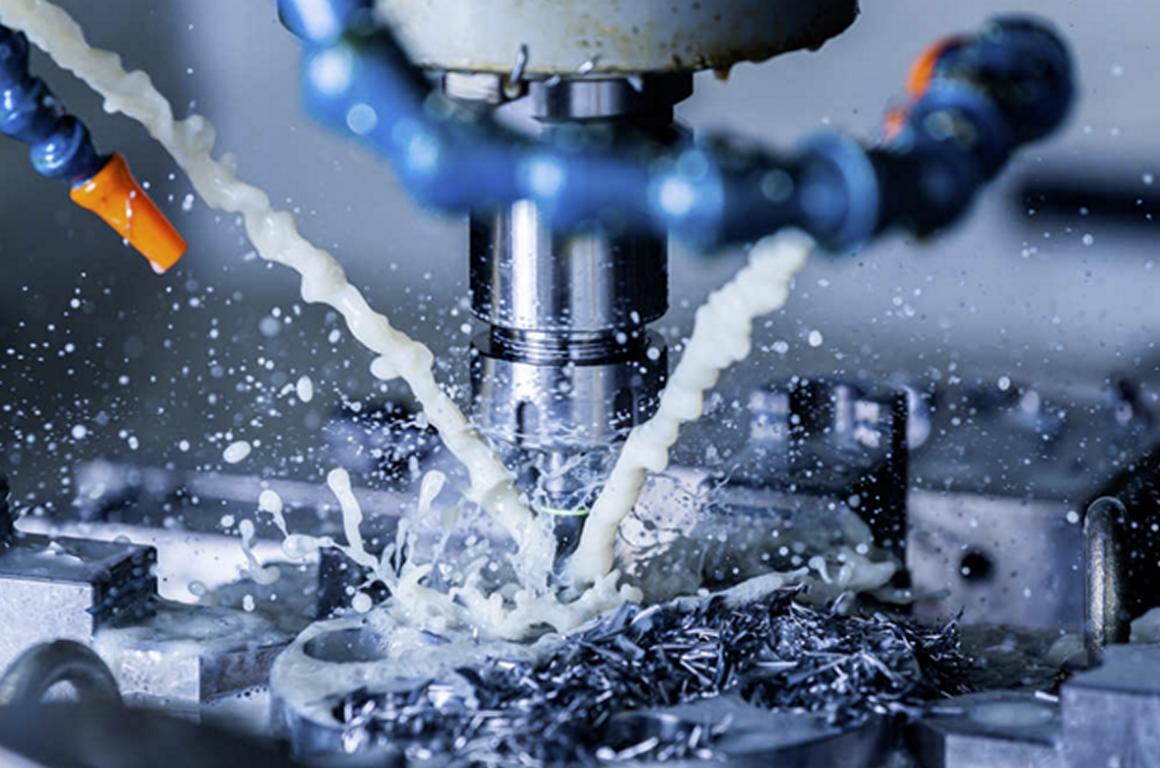
Proceso de mecanizado CNC
Tanto EDM como CNC pueden producir piezas muy precisas y exactas y son ampliamente utilizadas en la fabricación de núcleos de moldes de inyección e insertos de cavidad, un procedimiento importante que necesita ser explicado, la secuencia de trabajo entre EDM y CNC, normalmente el mecanizado CNC comenzará primero, luego se utiliza el mecanizado EDM para eliminar algunas de las áreas que el mecanizado CNC no puede hacer, por ejemplo, algunas esquinas, costillas, salientes, etc.
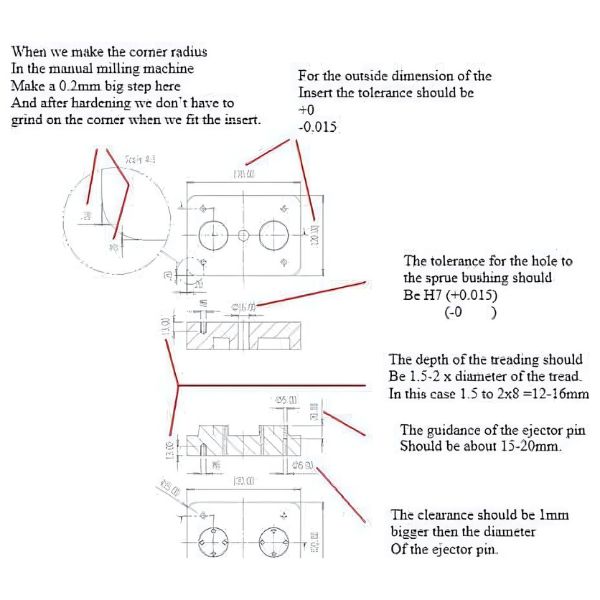
Directrices para la fabricación de cavidades y machos de moldes de inyección
Directrices para la fabricación de insertos para moldes y cavidades
Cuando fabricamos el insertos para núcleos y cavidades de moldes de inyección durante fabricación de moldes, hay algunas dimensiones que necesitamos fabricar con ciertas tolerancias para que encajen bien en el bolsillo de la placa de inserción o cavidad del molde o núcleo.
Esto ahorrará trabajo a la hora de ajustar la cavidad y el núcleo del molde. Una alta tolerancia y una buena tecnología de fabricación ahorrarán mucho tiempo al maestro de moldes. A continuación se presentan algunas directrices de fabricación de núcleo del molde y la cavidad de inserción que tenemos que prestar atención a hacer molde de plástico de alta calidad.
- Cuando hacemos el radio de la esquina En la fresadora manual, hacer un paso de 0,2 mm allí; después de endurecer, no tenemos que moler en la esquina cuando encajamos el inserto.
- Para la dimensión exterior del inyección de plástico molde cavidad o núcleo inserciones, la tolerancia debe ser de +/-0,015 mm; de este modo, será fácil de encajar en el bolsillo, suave y de buena calidad.
- La tolerancia del orificio del casquillo del bebedero debe ser H7 (0/+0,015 mm).
- La profundidad del escalón debe ser de 1,5 a 2 multiplicado por el diámetro del escalón. En este caso, para el tornillo M8, la profundidad del peldaño debe ser de 1,5 a 2 multiplicado por 8, igual a 12-16 mm.
- La guía del pasador eyector debe ser de unos 15-20 mm de largo; esto asegurará que los pasadores eyectores expulsen suavemente con una larga vida útil.
- La zona libre para los pasadores de expulsión debe ser 1 mm mayor que el diámetro de los pasadores de expulsión. Para cualquier pregunta sobre el molde, póngase en contacto con nosotros.
En cavidades e insertos para moldes de inyección no son fáciles, debe ser hecha por un fabricante de moldes de plástico profesional, si usted está funcionando un taller de moldeo por inyección, y la necesidad de hacer algunos insertos de cavidad del molde y el núcleo para reemplazar los insertos de edad, o si usted tiene un nuevo molde que desea hacer toda la cavidad y núcleos y el montaje de este en su taller de moldeo por inyección, que son welomce en contacto con nosotros, podemos hacer insertos de cavidad del molde de inyección y el núcleo o completamente cavtiy molde y el núcleo, moldbase, o completamente molde de inyección de plástico para usted.
Directrices para la fabricación de placas de cavidades y núcleos de moldes de inyección (placas de cavidades)
Como usted ya sabía la fabricación de moldes de inyección no es un trabajo fácil, si usted no tiene ningún buen equipo o experiencia en este campo, le sugiero que encuentre una empresa de moldes de plástico profesión para apoyarle, usted podría hacer el proceso de moldeo en su lado, pero hacer que el molde de subcontratar, porque hacer molde de plástico necesidad muy alta habilidad técnica para cada trabajador, en comparación con el proceso de moldeo por inyección, fabricación de moldes necesita más trabajos manuales que el servicio de moldeo por inyección, y la necesidad de alta exigencia técnica, así, a continuación es una de las directrices de fabricación de una placa de molde.
Cuando fabricamos las placas de cavidad y núcleo para un molde de plástico, hay algunas dimensiones que necesitamos fabricar con algunas tolerancias para que nuestros componentes de inserción de cavidad y núcleo o nuestros componentes de molde estándar puedan ensamblarse suavemente en el bolsillo de la placa, y los bloques de guía rectos puedan encajar bien en la base del molde, a continuación hay algunos puntos clave que necesitamos tener cuidado durante la fabricación de una placa.
Cuando tenemos enclavamientos rectos a cada lado de la base del molde (placas A y B), la tolerancia para esta dimensión debe ser H7 (0/+0.015mm), que los enclavamientos pueden fácil al ensamblaje en la base del molde pero mantener la función de guía de alta precisión.
Las dimensiones de la cavidad para los insertos de cavidad y núcleo, debemos seguir el requisito de tolerancia H7 (0/+0.015mm), para que nuestro inserto de cavidad/núcleo pueda ser guiado suavemente en la cavidad pero tenga dimensión de precisión.
La ubicación del agujero para el pasador de localización es importante, este es el montaje con la placa de sujeción, y la dimensión debe coincidir con el agujero relacionado en la placa de sujeción, por lo que la tolerancia para los pasadores de localización debe mantenerse en ± 0,01 mm, los agujeros de los pasadores de localización deben tener tolerancia relacionada H7 (0/+0,015 mm), para que el pasador de localización pueda entrar fácilmente.
Si el molde tiene el sistema de canal caliente para funcionar correctamente, el área de ajuste necesita tener una tolerancia de ± 0,01mm, por favor vea abajo la explicación.
Para la profundidad de la pista del anillo o, la tolerancia es ± 0.05mm, para el diámetro de la pista del anillo o
La tolerancia es de ± 0,25 mm, el mismo requisito para todas las juntas tóricas del molde.
Directrices para la fabricación de placas de sujeción
Cuando fabricamos el lado de la cavidad del molde de la placa de sujeción, hay algunas dimensiones que necesitamos controlar con algunas tolerancias para que nuestros componentes estándar del molde y otras piezas puedan encajar bien en la placa de sujeción.
Para los agujeros de localización, la tolerancia debe ser H7 (0/+0,015mm)
El diámetro del agujero para el anillo de localización, la tolerancia debe ser ±0.02mm
El diámetro del orificio para el inserto de soporte del colector de canal caliente, la tolerancia debe ser de ±0,05 mm.
La dimensión de la altura de la ranura de ventilación de aire en el inserto de soporte del colector de canal caliente, la tolerancia debe ser de ±0,01 mm.
La ranura para el pasador de fijación al casquillo del bebedero, la tolerancia debe ser de 0/+0,10 mm.
La ubicación del agujero para el pasador de localización es importante, esto es la conexión a otra placa, como la placa del colector de canal caliente, o la placa A, tolerancia ajustada nos aseguramos de que el conjunto de la base del molde muy bien, la tolerancia para ello debe ser ±0,01 mm.
Sincere Tech es uno de los 10 mejores fabricantes de moldes en China, si usted tiene un proyecto que necesita para hacer moldes o piezas moldeadas de China, que son bienvenidos a enviarnos su requisito para la cita, podemos enviarle un precio del molde o el molde y el precio de la unidad de moldeo, podemos hacer las primeras muestras rápido en 15 días para apoyar su negocio.
Más de 80% de nuestros moldes de inyección de plástico se exportan a América y Europa, no sólo estamos haciendo moldes de plástico para nuestros clientes, sino que también tienen taller de moldeo por inyección para ofrecer servicio de moldeo por inyección.
Póngase en contacto con nosotros para obtener un precio en 24 horas.