Enjeksiyon kalıp nedir?
Enjeksiyon kalıbı enjeksiyon kalıplama sürecinde kalıp boşluğuna malzeme enjekte ederek parça üretmek için kullanılan bir araçtır. Genellikle çelikten (H13, P20, 1.2312, 1.2344, S136H, vb.) veya alüminyumdan yapılır ve son ürünün şekline ve özelliklerine uyacak şekilde dikkatlice tasarlanmıştır.
Enjeksiyon kalıbı, boşluk yarısı ve çekirdek yarısı olmak üzere iki yarıya bölünmüştür, kalıplama işlemi sırasında birbirine kenetlenir ve malzeme, kalıp boşluğuna bir döküm deliğinden enjekte edilir ve burada soğutulur ve istenen şekle katılaşır. Parça oluşturulduktan sonra kalıp açılır ve parça dışarı atılır. Kalıp, birden fazla parça üretmek için yeniden kullanılabilir.

Enjeksiyon Kalıbı Nedir
Enjeksiyon Kalıp Çeşitleri
Enjeksiyon kalıplarının birçok çeşidi arasında şunları bulabilirsiniz:
Boşluk-özel kalıp
Enjeksiyon kalıplama işleminin her döngüsü, tek boşluklu bir kalıp kullanıldığında yalnızca bir parça üretebilir. Bu kalıpla bir parça yapma süreci, içine plastik reçine enjekte etmek, soğumasını beklemek ve ardından bitmiş ürünü çıkarmak kadar basittir.
Çok atışlı kalıpların üretim maliyetleri tek boşluklu kalıplarla karşılaştırıldığında, ilki genellikle daha uygun fiyatlıdır. Aynı anda az sayıda bileşen yapmak çok pahalı olacağında, prototipleme ve düşük hacimli üretim çalışmaları için bunlar tercih edilir.

Tek boşluklu kalıp
Tek atışlı kalıpların avantajları şunlardır:
- Maliyet açısından etkilidir: Tek atışlı bir kalıbın üretimi genellikle çok atışlı bir kalıbın üretiminden daha az maliyetlidir.
- Basit tasarım: Tasarımın basitliği sayesinde üretim ve bakım kolaylığı: Tek atışlı kalıplar genellikle çok atışlı kalıplara göre düzen açısından daha az karmaşıktır.
- Esneklik: Prototipleme ve düşük hacimli üretim çalışmaları gibi çok çeşitli uygulamalar tek boşluklu kalıpların kullanımına uygundur.
Tek atışlı kalıpların dezavantajları şunlardır:
- Sınırlı üretim: Bu sınırlama, tek boşluklu kalıpların yüksek hacimli kalıplama üretim çalışmaları için uygunsuz olmasına neden olur, çünkü her çevrimde yalnızca tek bir parça üretebilirler.
- Karmaşık parçalar: Tek boşluklu kalıplar, çok sayıda parçadan oluşan karmaşık parçalar yapmak için uygun değildir; bu tür parçalar için çok boşluklu kalıba veya aile kalıbına ihtiyacınız olacaktır.
- Verimsizlik: Çok boşluklu kalıplarla karşılaştırıldığında, tek atışlı kalıplar daha az verimlidir çünkü sınırlı kapasiteleri nedeniyle her döngüde yalnızca tek bir parça oluşturabilirler.
Çok boşluklu kalıplar:
Çok boşluklu kalıplar, birden fazla boşluğa sahip bir enjeksiyon kalıbı türüdür. Bu, enjeksiyon kalıplama işleminin her turda birden fazla parça yapmasını sağlar. Uygulamanın ihtiyacına bağlı olarak, bu kalıplar aynı veya farklı deliklerle yapılabilir.
Tek bir çevrimde birçok parça oluşturma yeteneğinin bir sonucu olarak, çok boşluklu kalıplar genellikle aşağıdakiler için kullanılır: yüksek hacimli enjeksiyon kalıplama üretim çalışmaları. Bu özellik, parça başına maliyeti düşürürken üretim verimliliğini artırmalarına olanak tanır.

çoklu boşluklu kalıp
Çok boşluklu kalıpların avantajları şunlardır:
- Yüksek hacimli üretim: Çok gözlü kalıplar, büyük ölçekli üretim çalışmaları için yapılır ve bu da çok sayıda parçanın üretilmesini kolaylaştırır.
- Maliyet etkinliği: Çok boşluklu kalıplar genellikle tek boşluklu kalıplardan daha ucuzdur çünkü tek seferde daha fazla parça üretilebilir.
- Karmaşık parçalar: Çok boşluklu kalıplar, karmaşık ve çok sayıda parçadan oluşan parçaları yapmak için kullanılabilir.
Çok boşluklu kalıpların dezavantajları şunlardır:
- Karmaşık tasarım: Çok boşluklu kalıpların yapımı ve bakımı, tek boşluklu kalıplara göre daha zordur çünkü tasarımları daha karmaşıktır.
- kalıp maliyetini artırdı: Çok boşluklu kalıplar, enjeksiyon döküm işlemi sırasında farklı boşlukların farklı miktarlarda stres ve aşınmaya maruz kalması nedeniyle tek boşluklu kalıplardan daha pahalı olabilir. Bu, daha az verimli üretime ve onarımlar için daha yüksek maliyetlere yol açabilir.
Sıcak yolluk kalıbı:
Sıcak yolluk kalıbı eritilmiş plastik malzemeyi kalıp boşluklarına iletmek için sıcak yolluk sistemi kullanan bir enjeksiyon kalıbı türüdür. Sıcak yolluk sistemi, eritilmiş plastiği daha sonra kalıp boşluklarına yönlendirilen ayrı nozul uçlarına dağıtan ısıtılmış bir manifolddan oluşur.

Sıcak yolluk kalıbı
Sıcak yolluklu kalıpların avantajları şunlardır:
- Gelişmiş parça kalitesi: Sıcak yolluklu kalıplar, yolluklarda kalan plastik miktarını en aza indirerek, parlama, kısa atışlar ve çökme izleri gibi kusurların riskini azalttığından, gelişmiş kalitede parçalar üretebilir.
- Artan üretim verimliliği: Sıcak yolluklu kalıplar, kalıplanmış parçalardan yollukları çıkarmak için manuel müdahaleye olan ihtiyacı ortadan kaldırarak üretim verimliliğini artırabilir, böylece çevrim süresini azaltır ve genel üretim hızını iyileştirir.
- Enerji verimliliği: Sıcak yolluklu kalıplar, yolluklarda israf edilen plastik miktarını en aza indirdiği için geleneksel soğuk yolluklu kalıplara kıyasla daha enerji verimlidir.
Sıcak yolluklu kalıpların dezavantajları şunlardır:
- Karmaşık tasarım: Sıcak yolluklu kalıplar, geleneksel soğuk yolluklu kalıplara kıyasla tasarım açısından daha karmaşıktır, bu da bunların üretimi ve bakımının daha pahalı olmasına neden olur.
- Arttırılmış bakım: Sıcak yolluklu kalıplar, iyi çalışma düzeninde tutulması gereken daha karmaşık bir ısıtma sistemine sahip olduklarından, genellikle soğuk yolluklu kalıplara kıyasla daha fazla bakım gerektirir.
- Tıkanmaya karşı hassasiyet: Sıcak yolluk kalıpları, özellikle yüksek viskoziteli veya uzun akış uzunluklarına sahip malzemeler işlenirken tıkanmaya karşı hassas olabilir, çünkü bunlar erimiş plastiğin yolluklarda katılaşmasına neden olabilir. Bu, üretim verimliliğinin azalmasına ve bakım maliyetlerinin artmasına neden olabilir.
Yığın kalıpları:
Yığın kalıp tek bir makine döngüsünde aynı anda birden fazla boşluğun kalıplanmasına olanak tanıyan bir enjeksiyon kalıbı türüdür. Yığın kalıpları esasen birbirinin üstüne istiflenmiş iki veya daha fazla kalıptır ve her kalıp tek bir parça üretir.

Yığın Kalıbı
Yığın kalıpların avantajları şunlardır:
- Artan üretim verimliliği: Yığın kalıplar, birden fazla parçanın aynı anda kalıplanmasına olanak tanır, üretim verimliliğini artırır ve çevrim süresini azaltır.
- Azaltılmış malzeme atığı: Yığın kalıpları, tek bir plastik malzeme atığı kullanılarak birden fazla parçanın üretilmesine olanak tanıdığı için malzeme atığını en aza indirir.
- Daha düşük maliyetler: Yığın kalıplar, tek boşluklu kalıplara kıyasla daha uygun maliyetli olabilir, çünkü tek bir makine döngüsünde birden fazla parçanın üretilmesine olanak tanır.
Yığın kalıpların dezavantajları şunlardır:
- Karmaşık tasarım: Yığın kalıpları, tek boşluklu kalıplara kıyasla tasarım açısından daha karmaşık olabilir, bu da bunların üretimi ve bakımının daha pahalı olmasına neden olur.
- Azalmış parça kalitesi: Yığın kalıplar, birden fazla boşluğun varlığı, parlama, kısa atışlar ve çökme izleri gibi kusur riskini artırabileceğinden, düşük kalitede parçalar üretebilir.
- Arttırılmış bakım: Yığın kalıplar, iyi çalışma düzeninde tutulması gereken daha karmaşık bir tasarıma sahip oldukları için, genellikle tek boşluklu kalıplara kıyasla daha fazla bakım gerektirir.
Aile kalıpları:
Çoklu boşluklu kalıba benzeyen çoklu baskı kalıpları olarak da bilinen aile kalıpları, tek bir makine döngüsünde aynı anda hafifçe farklı tasarımlara sahip birden fazla parçanın kalıplanmasına olanak tanıyan bir enjeksiyon kalıplama türüdür. Bu, kalıpta farklı şekil ve boyutlarda farklı parçalar üretebilen birden fazla boşluk olmasıyla elde edilir.
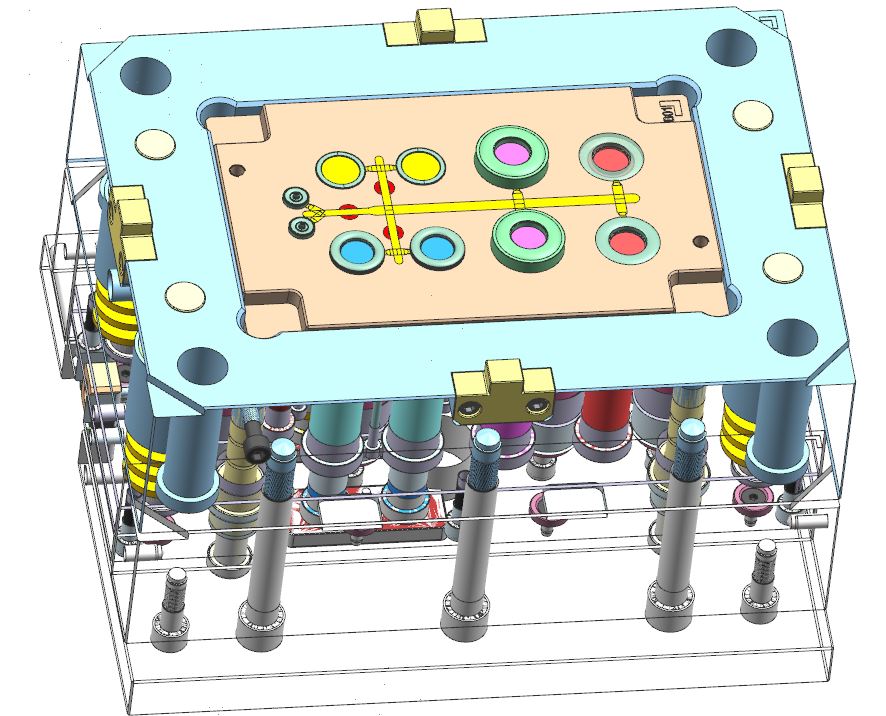
aile kalıbı
Aile kalıplarının avantajları şunlardır:
- Artan üretim verimliliği: Aile kalıpları, farklı tasarımlara sahip birden fazla parçanın aynı anda kalıplanmasına olanak tanır, böylece üretim verimliliği artar ve çevrim süresi azalır.
- Azaltılmış maliyetler: Aile kalıpları, her parça için birden fazla tek boşluklu kalıp üretmeye kıyasla daha uygun maliyetli olabilir, çünkü tek bir makine döngüsünde birden fazla parçanın üretilmesine olanak tanır.
- Esneklik: Aile kalıpları, farklı tasarımlara sahip farklı parçaların üretimine olanak tanır ve bu da onları, çeşitli ürünler üretmesi gereken üreticiler için çok yönlü bir seçenek haline getirir.
Aile kalıplarının dezavantajları şunlardır:
- Karmaşık tasarım: Aile kalıpları, tek boşluklu kalıplara kıyasla tasarım açısından daha karmaşık olabilir, bu da bunların üretimi ve bakımının daha pahalı olmasına neden olur.
- Azalmış parça kalitesi: Aile kalıpları, birden fazla boşluğun varlığı, parlama, kısa atışlar ve çökme izleri gibi kusur riskini artırabileceğinden, düşük kalitede parçalar üretebilir.
İki atışlı kalıplar:
İki atışlı kalıp (2 atışlı enjeksiyon kalıplama), olarak da bilinir aşırı kalıplama veya çoklu atış kalıpları veya 2K kalıp, iki farklı malzemenin tek bir makine döngüsünde birlikte kalıplanmasına olanak tanıyan bir enjeksiyon kalıplama türüdür. Bu işlem, birinci bir malzemenin (taban malzemesi) bir kalıba kalıplanmasını ve ardından ikinci bir malzemenin (üst kalıp malzemesi) birinci malzemeye kalıplanmasını içerir.

İki atışlı kalıp
İki atışlı kalıpların avantajları şunlardır:
- Arttırılmış işlevsellik: İki atışlı kalıplar, farklı özelliklere sahip iki farklı malzemenin birleştirilerek işlevselliği artırılmış parçalar oluşturulmasına olanak tanır.
- Gelişmiş estetik: İki aşamalı kalıplar, farklı renklerin veya dokuların tek bir parçaya entegre edilmesini sağlayarak görsel olarak daha çekici bir ürün yaratılmasına olanak tanır.
- Azaltılmış montaj süresi: İki malzemeyi tek bir parçada birleştirerek, iki atışlı kalıplar ek montaj adımlarına olan ihtiyacı azaltarak üretim süresini ve maliyetlerini düşürebilir.
İki atışlı kalıpların dezavantajları şunlardır:
- Karmaşık tasarım: İki atışlı kalıplar, tek atışlı kalıplara kıyasla tasarım açısından daha karmaşıktır, bu da bunların üretimi ve bakımının daha pahalı olmasına neden olur.
- Artan çevrim süresi: İki atışlı kalıplar, tek atışlı kalıplara kıyasla genellikle daha uzun bir çevrim süresine sahiptir, çünkü işlem tek bir makine çevriminde iki malzemenin kalıplanmasını içerir.
- Uyumluluk sorunları: İki aşamalı kalıplar, kalıplanan iki malzemenin birbirleriyle uyumlu olmasını ve düzgün bir şekilde yapışmasını gerektirir; bu nedenle kullanılan malzemelerin dikkatli seçilmesi önemlidir.
Kalıpların sökülmesi:
Sökme kalıpları, kapaklar, kapaklar ve kaplar gibi vida dişli parçalar üretmek için özel olarak tasarlanmış bir enjeksiyon kalıplama türüdür. Bu kalıplar, kalıbın çekirdeğinin dönmesine izin veren ve boşluk sabit kalırken kalıplanmış parçanın soğuduktan ve katılaştıktan sonra kalıptan sökülmesine olanak tanıyan bir mekanizmaya sahip olmaları bakımından benzersizdir.

kalıp sökme
Kalıpların sökülmesinin avantajları şunlardır:
- Yüksek verimlilik: Sökülebilir kalıplar, tek bir makine çevriminde dişli parçaların verimli bir şekilde üretilmesini sağlayarak üretim süresini ve maliyetlerini azaltır.
- Gelişmiş doğruluk: Sökme kalıpları, tutarlı diş aralığı ve diş derinliğine sahip dişli parçaların hassas bir şekilde üretilmesini sağlayarak, nihai ürünün kalitesini ve performansını artırır.
- Çok Yönlülük: Sökme kalıpları, farklı diş tipleri ve boyutlarına sahip çeşitli farklı parçalar üretmek için kullanılabilir ve bu da onları birçok farklı uygulama için çok yönlü bir seçenek haline getirir.
Kalıpların sökülmesinin dezavantajları şunlardır:
- Karmaşık tasarım: Sökme kalıpları, diğer kalıp türlerine kıyasla tasarım açısından daha karmaşıktır, bu da bunların üretimi ve bakımının daha pahalı olmasına neden olur.
- Artan çevrim süresi: Kalıp sökme işlemi, kalıbın çekirdeğinin dönmesini içerdiğinden, diğer kalıp tiplerine kıyasla genellikle daha uzun bir çevrim süresine sahiptir.
- Aşınma ve yıpranma: Sökme kalıplarının döner mekanizması zamanla aşınma ve yıpranmaya maruz kalabilir ve kalıbın düzgün çalışmasını sağlamak için düzenli bakım gerektirir.
Katlanabilir çekirdekli kalıp:
Katlanabilir çekirdek kalıpları, borular, borular ve diğer karmaşık şekilli parçalar gibi iç boşlukları olan içi boş parçalar üretmek için kullanılan bir enjeksiyon kalıplama türüdür. Bu kalıplar, kalıbın çekirdeğinin kendi içine çökmesine ve parçanın iç boşluğunu oluşturmasına izin veren benzersiz bir tasarım kullanır.

Katlanabilir çekirdek kalıp bileşeni
Katlanabilir çekirdekli kalıpların avantajları şunlardır:
- Gelişmiş verimlilik: Katlanabilir çekirdekli kalıplar, içi boş parçaların tek bir makine döngüsünde üretilmesine olanak sağlayarak üretim süresini ve maliyetlerini azaltır.
- Gelişmiş parça kalitesi: Katlanabilir çekirdekli kalıplar, daha hassas ve tutarlı bir iç boşluk sağlayarak, nihai parçanın genel kalitesini artırır.
- Çok Yönlülük: Katlanabilir çekirdek kalıpları, farklı şekil ve boyutlarda çok çeşitli parçaların üretiminde kullanılabilir ve bu da onları birçok farklı uygulama için çok yönlü bir seçenek haline getirir.
Katlanabilir çekirdekli kalıpların dezavantajları şunlardır:
- Karmaşık tasarım: Katlanabilir kalıplar, diğer kalıp türlerine kıyasla tasarım açısından daha karmaşıktır, bu da bunların üretimi ve bakımının daha pahalı olmasına neden olur.
- Artan çevrim süresi: Katlanabilir çekirdekli kalıplar, kalıp çekirdeğinin çökmesini içeren işlem nedeniyle, diğer kalıp türlerine kıyasla genellikle daha uzun bir çevrim süresine sahiptir.
- Aşınma ve yıpranma: Çekirdeğin katlanabilir mekanizması zamanla aşınma ve yıpranmaya maruz kalabilir ve kalıbın düzgün çalışmasını sağlamak için düzenli bakım gerektirir.
Plastik Enjeksiyon Kalıbının Avantajları ve Dezavantajları
Avantajları Enjeksiyon Kalıplama:
- Yüksek Hacimli Üretim: Enjeksiyon kalıplama, yüksek hacimli özdeş parçalar üretmek için oldukça verimli bir yöntemdir. Bu, onu tüketim malları, otomotiv parçaları ve büyük miktarlarda benzer parça gerektiren diğer ürünlerin seri üretimi için ideal hale getirir.
- Hassasiyet: İşlem, boyutsal doğruluk ve parça tutarlılığının çok hassas bir şekilde kontrol edilmesine olanak tanır. Bu, sıkı bir şekilde kontrol edilen işleme koşullarının kullanımı ve kalıplama makinesinin ve kalıbın sertliğinden kaynaklanmaktadır.
- Hız: Enjeksiyon kalıplama, küçük parçalar için çevrim sürelerinin birkaç saniye kadar kısa olduğu hızlı bir işlemdir. Bu, üreticilerin nispeten kısa bir sürede büyük miktarda parça üretmesine olanak tanır.
- Maliyet etkinliği: Enjeksiyon kalıplama yoluyla parça üretmenin maliyeti, üretim hacmi arttıkça daha ekonomik hale gelir. Bunun nedeni, kalıbın kullanım ömrü boyunca birçok parça üretmek için kullanılabilmesi ve hacim arttıkça parça başına maliyetin azalmasıdır.
- Çok yönlülük: Enjeksiyon kalıplama, plastikler, metaller ve elastomerler dahil olmak üzere çok çeşitli malzemelerden parçalar üretmek için kullanılabilir. Bu çok yönlülük, ürünün özel gereksinimlerine bağlı olarak farklı malzemelerden parçalar üretmesi gereken üreticiler için popüler bir seçim haline getirir.
- Otomasyon: Enjeksiyon kalıplama makineleri otomatikleştirilebilir, bu da süreci daha verimli hale getirir ve manuel işgücüne olan ihtiyacı azaltır. Bu ayrıca parça tutarlılığını ve kalitesini de iyileştirebilir.
- Karmaşık Şekiller: Enjeksiyon kalıplama, karmaşık şekiller ve tasarımlar üretmek için kullanılabilir; bunlara karmaşık detaylara ve sıkı toleranslara sahip parçalar da dahildir. Bu, kalıplama sürecinin hassas kontrolü ve oldukça ayrıntılı kalıplar tasarlama yeteneği sayesinde mümkündür.
- Malzeme Seçimi: Enjeksiyon kalıplama, üreticilerin her biri mukavemet, esneklik ve ısıya, kimyasallara ve aşınmaya karşı direnç gibi kendine özgü özelliklere sahip çok çeşitli malzemeler arasından seçim yapmalarına olanak tanır. Bu, her uygulama için en iyi malzemeyi seçmeyi ve istenen özelliklere sahip parçalar üretmeyi mümkün kılar.
Enjeksiyon Kalıplamanın Dezavantajları:
- Yüksek İlk Maliyet: Kalıbı oluşturmanın ilk maliyeti, özellikle karmaşık şekiller ve tasarımlar için yüksek olabilir. Bu, süreci küçük miktardaki parçalar veya prototipler için daha az maliyet etkin hale getirebilir.
- Sınırlı Tasarım Esnekliği: Kalıp yapıldıktan sonra, tasarımı değiştirmek zor ve pahalı olabilir. Bu, kalıp oluşturulduktan sonra tasarım değişiklikleri veya iyileştirmeleri yapma yeteneğini sınırlayabilir.
- Malzeme Atığı: Enjeksiyon kalıplama, bertarafı maliyetli ve çevreye zararlı olabilen önemli miktarda hurda malzeme üretir. Bu ayrıca üretim maliyetine eklenebilir ve sürecin genel verimliliğini azaltabilir.
- Teslim Süresi: Kalıbı oluşturma ve enjeksiyon kalıplama sürecini kurma teslim süresi, özellikle karmaşık parçalar için uzun olabilir. Bu, ürün geliştirme sürecini yavaşlatabilir ve ürünleri pazara hızlı bir şekilde sunma yeteneğini sınırlayabilir.
- Yüzey Kaplama Sınırlamaları: Enjeksiyon kalıplama, özellikle karmaşık detaylara veya sıkı toleranslara sahip olan bazı parçalarda yüksek kaliteli bir yüzey kaplaması üretemeyebilir. Bu, yüksek kaliteli estetik görünüme sahip parçalar üretme yeteneğini sınırlayabilir.
- Malzeme Uyumluluğu: Malzeme ve kalıp arasındaki uyumluluk zor olabilir, çünkü bazı malzemeler belirli kalıp tipleriyle iyi çalışmayabilir veya özel işleme koşulları gerektirebilir. Bu, belirli malzemelerden parça üretme yeteneğini sınırlayabilir ve üretim maliyetini artırabilir.
- Sınırlı Parça Boyutu: Enjeksiyon kalıplama, kalıbın boyutu ve kalıplama makinesinin sıkıştırma kuvvetiyle sınırlıdır. Bu, üretilebilecek parçaların boyutunu sınırlayabilir ve daha büyük parçaları üretmenin maliyetini artırabilir.
- İkincil İşlemler: Bazı parçalar kalıplandıktan sonra, düzeltme veya sonlandırma gibi ikincil işlemler gerektirebilir. Bu, üretim maliyetine eklenebilir ve sürecin genel verimliliğini sınırlayabilir, elbette bazen bu sorunlar enjeksiyon kalıbını iyileştirerek çözülebilir
Enjeksiyon Kalıbı ile Karşılaşılan Yaygın Sorunlar
Plastik enjeksiyon kalıplama alanında çalışmaya başladığınızda, her gün çözmeniz gereken bazı sorunlar olacaktır. Enjeksiyon kalıplamada karşılaşılan bazı yaygın zorluklar şunlardır:
Eğrilme sorunları:
Çarpılma, enjeksiyon kalıplamada karşılaşılan yaygın bir sorundur ve kalıptan çıkarıldıktan sonra kalıplanmış parçanın deformasyonu veya bozulması anlamına gelir. Bu, aşağıdakiler de dahil olmak üzere çeşitli faktörlerden dolayı olabilir:

Çarpıtma Bozulması
- Uygunsuz soğutma: Parça çok hızlı veya düzensiz bir şekilde soğursa, malzeme farklı hızlarda büzülüp büzüleceğinden eğrilmeye neden olabilir.
- Kalıntı gerilim: Enjeksiyon kalıplama, kalıplama işlemi sırasında kullanılan yüksek basınç nedeniyle parçada kalıntı gerilim yaratır. Bu gerilim, düzgün bir şekilde giderilmezse eğrilmeye neden olabilir.
- Malzeme seçimi: Bazı malzemeler diğerlerinden daha fazla eğilmeye eğilimlidir. Örneğin, düşük ısı direncine veya düşük boyutsal kararlılığa sahip malzemelerin eğilme olasılığı daha yüksektir.
- Kalıp tasarımı: Kalıbın tasarımı da, özellikle kalıp uygun soğutmaya veya malzeme akışına izin vermiyorsa, eğrilmeye katkıda bulunabilir.
- İşleme koşulları: Değişen enjeksiyon hızları, kalıp sıcaklıkları ve basınç seviyeleri gibi tutarsız işleme koşulları eğrilmeye neden olabilir.
Çarpılmayı önlemek için uygun malzemeyi seçmek, kalıp tasarımını ve işleme koşullarını optimize etmek ve uygun soğutma ve malzeme işleme uygulamalarını uygulamak önemlidir. Ek olarak, kalıntı gerilimi azaltmak ve boyutsal kararlılığı iyileştirmek için tavlama gibi kalıplama sonrası işlemlerin kullanılması gerekebilir.
Flash sorunları:
Flaş kusurları, enjeksiyon kalıplamada kalıplama işlemi sırasında kalıptan dışarı atılan fazla malzemeyi ifade etmek için kullanılan bir terimdir. Flaş, malzeme amaçlanan kalıp boşluğunun ötesine ve ayırma çizgisine veya kalıbın iki yarısı arasındaki boşluğa aktığında meydana gelir.

Kalıplama Flaşı veya çapaklar
Flaş, aşağıdakiler de dahil olmak üzere çeşitli faktörlerden kaynaklanabilir:
- Uygunsuz kalıp tasarımı: Kötü tasarlanmış bir kalıp, malzemenin ayırma çizgisine sızmasına izin vererek çapak oluşumuna neden olabilir.
- Tutarlı olmayan işleme koşulları: Enjeksiyon hızı ve basıncı gibi değişken işleme koşulları, parlamaya neden olabilir.
- Malzeme uyumluluğu: Bazı malzemeler kalıpla uyumlu olmayabilir ve ayırma çizgisine akarken çapaklanmaya neden olabilir.
- Kalıbın aşınması ve yıpranması: Zamanla kalıp aşınabilir ve malzemenin ayırma çizgisine sızması sonucu çapak oluşabilir.
Flaşın, parçanın boyutsal doğruluğunu azaltma, hurda oranını artırma ve kalıplama sonrası işlemleri daha zor hale getirme gibi çeşitli olumsuz etkileri olabilir. Flaşı en aza indirmek için kalıp tasarımını, işleme koşullarını ve malzeme seçimini optimize etmek ve kalıbı gerektiği gibi düzenli olarak bakımını yapmak ve onarmak önemlidir.
Kaynak Hatları:
Kaynak çizgileri, enjeksiyon kalıplamada yaygın bir sorundur ve eritilmiş plastik malzemenin iki akışının bir araya gelip katılaştığı kalıplanmış parçanın yüzeyindeki görünür izlere atıfta bulunur. Kaynak çizgileri, malzeme akarken tam olarak kaynaşmadığında oluşur plastik kalıp boşluk oluşur ve parçanın yüzeyinde görünür bir çizgi kalır.

Kaynak hattı
Kaynak çizgileri aşağıdakiler de dahil olmak üzere çeşitli faktörlerden kaynaklanabilir:
- Yetersiz eriyik akışı: Malzemenin akması ve tam olarak kaynaşması için yeterli zamana sahip olmaması durumunda kaynak hattı oluşabilir.
- Uygunsuz kalıp tasarımı: Erimiş malzemenin kalıp boşluğuna girdiği nokta olan kötü tasarlanmış bir kalıp, kaynak hattına neden olabilir.
- Tutarlı olmayan işleme koşulları: Enjeksiyon hızı ve basıncı gibi değişken işleme koşulları, kaynak hattına neden olabilir.
- Malzeme uyumluluğu: Bazı malzemeler kalıpla uyumlu olmayabilir ve kalıp boşluğuna akarken kaynak çizgisine neden olabilir.
Kaynak çizgileri parçanın mukavemetini zayıflatabilir ve genel kalitesini düşürebilir. Kaynak çizgilerini en aza indirmek için kalıp tasarımını, işleme koşullarını ve malzeme seçimini optimize etmek ve uygun malzeme işleme uygulamalarını uygulamak önemlidir. Ek olarak, kaynak çizgilerinin oluşumunu azaltmak için çok boşluklu kalıplar veya sıcak yolluk sistemleri gibi özel işleme tekniklerinin kullanılması gerekebilir.
Çökme izleri:
"Çökme", "vakumlu çökme" veya "deri" olarak da bilinen çöküntü izleri, enjeksiyonla kalıplanmış plastik bir parçanın yüzeyindeki çökük veya çöküntü alanlarıdır. Bunlar genellikle aşağıdakiler de dahil olmak üzere bir dizi faktörden kaynaklanır:
- Reçine büzülmesi: Reçine soğudukça ve katılaştıkça eşit olmayan bir şekilde büzülebilir ve bu da çökme izlerine yol açabilir.
- Zayıf malzeme akışı: Reçine kalıbın tüm alanlarına eşit şekilde akmazsa, boşluklar veya çökük alanlar oluşabilir.
- Yetersiz paketleme basıncı: Enjeksiyon basıncı yeterince yüksek değilse, reçine kalıbı tam olarak dolduramayabilir ve bu da çökme izlerine yol açabilir.
- Kalıp tasarım sorunları: Kalıp yerleşimi ve boyutu, yolluk sistemi ve havalandırma dahil olmak üzere kalıp tasarımı, kalıplanmış parçanın kalitesini etkileyebilir ve çökme izlerine katkıda bulunabilir.
Çökme izleri kalıplanmış bir parçanın estetik kalitesini ve işlevselliğini etkileyebilir ve üreticiler ve son kullanıcılar için bir hayal kırıklığı kaynağı olabilir. Çökme izlerini en aza indirmek için, malzeme seçimi, kalıp tasarımı, işleme parametreleri ve parça tasarımı gibi bunlara katkıda bulunan faktörleri dikkatlice değerlendirmek ve enjeksiyon kalıplama sürecini optimize etmek için gerektiği gibi ayarlamalar yapmak önemlidir.
Akış izleri:
Akış izleri, enjeksiyon kalıplamada yaygın bir sorundur ve eritilmiş plastik malzemenin kalıp boşluğunu doldururken akışından kaynaklanan kalıplanmış parçanın yüzeyindeki görünür izlere veya çizgilere atıfta bulunur. Akış izleri, malzeme düzensiz aktığında ve parçanın yüzeyinde görünür bir iz bıraktığında oluşur.
Akma izleri çeşitli faktörlerden kaynaklanabilir, bunlar arasında şunlar yer alır:
- Yetersiz eriyik akışı: Malzemenin kalıp boşluğunu dolduracak ve akacak yeterli zamanı olmazsa, akış izleri oluşabilir.
- Uygunsuz kapak tasarımı: Erimiş malzemenin kalıp boşluğuna girdiği nokta olan kötü tasarlanmış bir kapak, akış izlerine neden olabilir.
- Tutarlı olmayan işleme koşulları: Enjeksiyon hızı ve basıncı gibi değişken işleme koşulları akış izlerine neden olabilir.
- Malzeme uyumluluğu: Bazı malzemeler kalıpla uyumlu olmayabilir ve kalıp boşluğuna akarken akış izlerine neden olabilir.
Akış izleri, parçanın genel kalitesini ve kozmetik görünümünü azaltabilir. Akış izlerini en aza indirmek için kalıp tasarımını, işleme koşullarını ve malzeme seçimini optimize etmek ve uygun malzeme işleme uygulamalarını uygulamak önemlidir. Ek olarak, akış izlerinin oluşumunu azaltmak için çok boşluklu kalıplar veya sıcak yolluk sistemleri gibi özel işleme tekniklerinin kullanılması gerekebilir.
Çizik sorunları:
Çizik sorunları, kalıplama işlemi sırasında parça ile kalıp veya diğer yabancı nesneler arasındaki fiziksel temastan kaynaklanan enjeksiyon kalıplı bir parçanın yüzeyindeki görünür izler veya çizikleri ifade eder. Çizik sorunları, aşağıdakiler dahil olmak üzere çeşitli nedenlerle ortaya çıkabilir:
- Kötü kalıp tasarımı: Uygun şekilde tasarlanmamış kalıplar veya kalıp bileşenleri parçanın yüzeyinde çiziklere neden olabilir.
- Yetersiz yağlama: Kalıp ve kalıp parçaları uygun şekilde yağlanmazsa parça yüzeyinde çizikler oluşabilir.
- Kötü malzeme elleçleme: Hammadde veya bitmiş parçaların kötü elleçlenmesi, parçanın yüzeyinde çiziklere neden olabilir.
- Kalıptaki kalıntılar: Kalıp boşluğundaki yabancı cisimler veya kalıntılar parçanın yüzeyinde çiziklere neden olabilir.
Çizik sorunları, parçanın genel kalitesini ve kozmetik görünümünü azaltabilir. Çizik sorunlarını en aza indirmek için, uygun kalıp tasarımı, yağlama, malzeme taşıma ve bakım uygulamalarını uygulamak önemlidir. Ek olarak, kalıbın ve kalıp bileşenlerinin düzenli olarak temizlenmesi ve incelenmesi, çizik sorunlarının oluşmasını önlemeye yardımcı olabilir.
Ejektör izleri:
Ejektör izleri, kalıplama işlemi sırasında ejektör pimleri veya diğer ejektör mekanizmaları tarafından oluşturulan enjeksiyon kalıplı bir parçanın yüzeyindeki görünür izlerdir. Ejektör izleri, ejektör pimleri kalıplanmış parçayı kalıp boşluğundan dışarı ittiğinde ve parçanın yüzeyinde görünür izler bıraktığında oluşur.
Ejektör izleri aşağıdakiler de dahil olmak üzere çeşitli faktörlerden kaynaklanabilir:
- Uygunsuz ejektör pimi tasarımı: Ejektör pimleri uygun şekilde tasarlanmazsa, parçanın yüzeyinde görünür izler bırakabilir.
- Aşırı kuvvet: Ejektör pimleri, çıkarma sırasında parçaya aşırı kuvvet uygularsa, parçanın yüzeyinde daha derin ve belirgin izler bırakabilir.
- Tutarlı olmayan çıkarma kuvveti: Çıkarma kuvveti bir çıkarma piminden diğerine tutarlı değilse, parçanın yüzeyinde eşit olmayan çıkarma izlerine neden olabilir.
- Kötü yüzey kalitesi: Kalıp boşluğunun yüzey kalitesi düzgün değilse, parçanın yüzeyinde ejektör izleri oluşabilir.
Ejektör izleri, parçanın genel kalitesini ve kozmetik görünümünü düşürebilir. Ejektör izlerini en aza indirmek için, ejektör pimlerinin tasarımını ve kalıp boşluğunun yüzey kaplamasını optimize etmek ve uygun bakım ve inceleme uygulamalarını uygulamak önemlidir. Ek olarak, ejektör izlerini en aza indirmek için hava destekli ejeksiyon veya yan etkili ejeksiyon gibi özel ejeksiyon mekanizmaları kullanmak gerekebilir.
Kısa vadeli sorunlar:
Kısa atış, eritilmiş plastik malzemenin kalıp boşluğunu tamamen doldurmaması ve bunun sonucunda istenen boyuttan daha küçük bir kalıplanmış parça oluşmasıyla sonuçlanan enjeksiyon kalıplamada yaygın bir sorundur. Kısa atışlar, aşağıdakiler de dahil olmak üzere çeşitli nedenlerle meydana gelebilir:
- Yetersiz malzeme: Kalıp boşluğunu dolduracak yeterli malzeme yoksa, kısa atış meydana gelebilir.
- Uygunsuz işleme koşulları: Enjeksiyon hızı ve basıncı gibi işleme koşulları doğru ayarlanmazsa kısa atış meydana gelebilir.
- Kötü kalıp tasarımı: Kötü tasarlanmış bir kalıp, malzemenin kalıp boşluğunun tüm alanlarına akmaması nedeniyle kısa atışa neden olabilir.
- Malzemenin bozulması: Malzeme bozulmuşsa veya uygun şekilde depolanmamışsa kısa atışa neden olabilir.
Kısa atışlar, parçanın genel kalitesini ve işlevselliğini azaltabilir ve boşa harcanan malzeme ve işleme süresiyle sonuçlanabilir. Kısa atışları en aza indirmek için kalıp tasarımını, işleme koşullarını ve malzeme seçimini optimize etmek ve uygun malzeme işleme uygulamalarını uygulamak önemlidir. Ek olarak, kalıplama ekipmanının düzenli olarak izlenmesi ve bakımı, kısa atışların meydana gelmesini önlemeye yardımcı olabilir.
Hava sıkışması ve yanık izleri:
Hava sıkışmaları ve yanık izleri, enjeksiyon kalıplamada uygunsuz işleme koşulları veya kalıp tasarımı nedeniyle ortaya çıkabilen yaygın sorunlardır.
Hava sıkışmaları, enjeksiyon kalıplama işlemi sırasında havanın kalıp boşluğunda sıkışması ve malzemenin hava cebini doldurmak yerine etrafından akmasına neden olmasıyla oluşur. Bu, kalıplanmış parçada görünür boşluklar veya cepler oluşmasına neden olabilir. Hava sıkışmaları, aşağıdakiler de dahil olmak üzere çeşitli faktörlerden kaynaklanabilir:
- Yetersiz malzeme akışı: Malzeme kalıp boşluğuna düzgün bir şekilde akmıyorsa, hava sıkışabilir.
- Uygunsuz kapı tasarımı: Kapı doğru şekilde tasarlanmazsa, kalıp boşluğunda hava sıkışabilir.
- Yetersiz havalandırma: Kalıp düzgün bir şekilde havalandırılmazsa, kalıp boşluğunda hava sıkışabilir.
Yanık izleri, plastik malzeme çok uzun süre yüksek sıcaklıklara maruz kaldığında oluşur ve bu da bozulmasına ve parçanın yüzeyinde görünür izler veya renk bozulması oluşmasına neden olur. Yanık izleri, aşağıdakiler de dahil olmak üzere çeşitli faktörlerden kaynaklanabilir:
- Aşırı işleme sıcaklıkları: İşleme sıcaklıkları çok yüksek ayarlanırsa, malzeme bozulabilir ve yanık izleri oluşabilir.
- Yetersiz soğutma süresi: Parça uygun şekilde soğutulmazsa, malzeme bozulabilir ve yanık izleri oluşabilir.
- Kötü kalıp tasarımı: Kötü tasarlanmış bir kalıp, malzemenin çok uzun süre yüksek sıcaklıklara maruz kalmasına ve bunun sonucunda yanık izlerinin oluşmasına neden olabilir.
Hava tuzaklarını ve yanık izlerini en aza indirmek için, işleme koşullarını ve kalıp tasarımını optimize etmek ve uygun izleme ve bakım uygulamalarını uygulamak önemlidir. Ek olarak, hava tuzaklarını ve yanık izlerini en aza indirmek için düşük sıcaklıkta kalıplama veya vakum kalıplama gibi özel işleme tekniklerinin kullanılması gerekebilir.
Enjeksiyon kalıbı yapımı için işlem:
Enjeksiyon kalıbı yapım süreci birkaç adımdan oluşur:
Kalıp Tasarımı:
Enjeksiyon kalıp tasarımı, kalıplanmış parçaların kalitesini, verimliliğini ve maliyetini doğrudan etkilediği için enjeksiyon kalıplama sürecinin kritik bir yönüdür.
İyi tasarlanmış bir enjeksiyon kalıbı, istenilen ölçü, şekil ve kalite gereksinimlerini karşılayan parçaların üretilmesini sağlarken, aynı zamanda üretimi verimli ve bakımı kolaydır.
Enjeksiyon kalıbı tasarlanırken dikkate alınması gereken temel faktörler şunlardır:
- Parça geometrisi: Kalıplanacak parçanın tasarımında parçanın istenilen boyutu, şekli ve özellikleri dikkate alınmalıdır.
- Malzeme seçimi: Kalıp ve kalıplanan parça için kullanılacak malzeme; maliyet, mukavemet, ısıl kararlılık gibi faktörler göz önünde bulundurularak seçilmelidir.
- Kalıp boşlukları: Kalıp boşluklarının sayısı ve düzenlenmesi üretim hacmi gereksinimlerini karşılayacak şekilde seçilmelidir.
- Kalıp geçiş sistemi: Kalıp geçiş sisteminin tasarımı kritik öneme sahiptir, çünkü plastik malzemenin kalıp boşluğuna nasıl akacağını belirler.
- Çıkarma sistemi: Çıkarma sistemi, kalıplanmış parçaların kalıptan hasar görmeden çıkarılabilmesini sağlayacak şekilde tasarlanmalıdır.
- Soğutma sistemi: Soğutma sistemi, kalıplanan parçaların eşit ve hızlı bir şekilde soğumasını sağlayacak şekilde tasarlanmalı, böylece çevrim süresi azaltılmalı ve kalite artırılmalıdır.
- Taslak açıları: Kalıbın tasarımı, kalıplanmış parçaların kalıptan çıkarılmasına izin verecek uygun taslak açılarını içermelidir.
- Havalandırma: Kalıbın havalandırılması, kalıp boşluğundan havanın kaçmasına izin verecek şekilde yapılmalıdır; bu, hava sıkışması ve yanık izi riskini azaltır.
- Bakım ve onarım: Kalıp, duruş süresini en aza indirmek ve üretim verimliliğini artırmak için kolay bakım ve onarım yapılabilecek şekilde tasarlanmalıdır.
Enjeksiyon kalıp tasarımı, makine mühendisliği, malzeme bilimi ve üretim gibi alanlarda uzmanlık gerektiren karmaşık bir süreçtir. Kalıbın doğru şekilde tasarlandığından ve ihtiyaçlarınızı karşıladığından emin olmak için saygın bir kalıp tasarımcısıyla çalışmak önemlidir.
CNC programlama:
CNC (Bilgisayar Sayısal Kontrol) programlama, bir enjeksiyon kalıbının üretiminde önemli bir adımdır. Kalıp tasarımı tamamlandıktan sonraki adım CNC programlamadır. Enjeksiyon kalıbı üretimi için CNC programlamada yer alan ana adımlar şunlardır:
- CAD model çevirisi: CAD modeli, kalıp için CNC kodunu oluşturmak için kullanılan bilgisayar destekli üretim (CAM) programına çevrilir.
- CNC kod oluşturma: CNC kodu, CNC makinesine kalıp bileşenlerini nasıl hareket ettireceği ve keseceği konusunda talimatlar sağlayan CAM programında oluşturulur. Kod, kalıp bileşenlerinin malzemesini ve kalınlığını, ayrıca istenen şekilleri ve özellikleri dikkate alır.
- Takım yolu oluşturma: Takım yolu, kesici takımın kalıp bileşenlerini işlemek için izleyeceği yolu tanımlayan CAM programında oluşturulur. Takım yolu, kalıp bileşenlerinin şekillerini ve özelliklerini ve CNC makinesinin yeteneklerini dikkate alır.
- Simülasyon: Kalıp bileşenlerinin doğru şekilde ve doğru özelliklere göre işlenebilmesini sağlamak için CNC kodu ve takım yolu CAM programında simüle edilir.
- CNC işleme: CNC kodu CNC makinesine yüklenir ve makine daha sonra kalıp bileşenlerini işlemek için kodu ve takım yolunu kullanır.
CNC programlama, kalıp bileşenlerinin doğruluğunu ve kalitesini belirlediği için enjeksiyon kalıp üretim sürecinde kritik bir adımdır. CNC kodunun doğru ve doğru özelliklere göre oluşturulduğundan emin olmak için enjeksiyon kalıpları için programlama konusunda deneyimli bir CNC programcısıyla çalışmak önemlidir. Bu adım aynı zamanda kalıbın soğutma kanallarının, ejektör sisteminin ve diğer özelliklerin kalıp bileşenlerine eklenerek düzgün çalışmasının sağlandığı adımdır.
Kalıp BOM listesi satın alma
Bir Mold BOM (Malzeme Listesi) listesi, bir enjeksiyon kalıbı üretmek için gereken tüm bileşenlerin ve malzemelerin kapsamlı bir listesidir. Aşağıdaki öğeleri içerir:
- Kalıp tabanı ve çekirdek/boşluk ek parçaları için çelik
- Sıcak yolluk bileşenleri
- Su hatları ve soğutma blokları gibi soğutma sistemi bileşenleri
- Ejektör pimleri ve kovanları gibi fırlatma sistemi bileşenleri
- Kalıp sökücü bileşenleri
- Isıtıcı bantlar ve sıcaklık kontrol cihazları
- Burçlar, kılavuz pimleri ve kilitleme cihazları gibi kalıp bileşenleri
- Kızaklar ve kaldırıcılar gibi kalıp ekleri
- Tarih damgaları ve özel logolar gibi özel ürünler
Kalıp BOM listesi, kalıbı üretmek için gereken bileşenlerin ve malzemelerin açık ve ayrıntılı bir listesini sağladığı için tedarik ve üretim için önemli bir araçtır. Kalıp üretilmeye hazır olduğunda gerekli tüm bileşenlerin sipariş edildiğinden ve hazır olduğundan emin olmak için kullanılır.
Enjeksiyon kalıbı için komponent satın alırken saygın bir tedarikçi ile çalışmak önemlidir, çünkü bu komponentlerin kalitesi ve güvenilirliği enjeksiyon kalıplama sürecinin verimliliği ve kalitesi üzerinde önemli bir etkiye sahip olabilir.
Kalıp kaba işleme:
Enjeksiyon kalıbı kaba işleme, bir enjeksiyon kalıbının çelik bileşenlerinin, kalıbın temel şekline ve boyutuna ulaşmak için ilk işlenmesini ifade eder. Bu adım genellikle bilgisayar sayısal kontrol (CNC) makineleri kullanılarak yapılır. Enjeksiyon kalıbı kaba işlemede yer alan ana adımlar şunlardır:
- Çelik seçimi: İlk adım, kalıplanacak parçanın istenilen özelliklerine göre kalıp için uygun çelik tipinin (örneğin P20 veya H13) seçilmesidir.
- Çelik kesimi: Çelik, bir CNC makinesi kullanılarak uygun boyut ve şekilde kesilir. Bu adım ayrıca soğutma ve çıkarma sistemleri için deliklerin delinmesini ve diş açılmasını da içerebilir.
- Çelik profilleme: Daha sonra, çekirdek ve boşluk ekleri de dahil olmak üzere kalıbın temel şeklini elde etmek için çelik bileşenler işlenir.
- Çelik muayenesi: İşlenmiş bileşenler daha sonra gerekli toleransları ve özellikleri karşıladığından emin olmak için muayene edilir.
- Çelik temizliği: İşlenmiş parçalar temizlenir ve çapakları alınarak pürüzlü kenarlar veya kalıntılar giderilir.
Kaba işleme süreci, enjeksiyon kalıplama sürecinde önemli bir adımdır, çünkü takip edecek son, yüksek hassasiyetli işleme ve parlatma adımları için temel oluşturur. Kalıbın düzgün çalışmasını ve istenen kalitede parçalar üretmesini sağlamak için kaba işlemenin doğru ve doğru özelliklere göre yapıldığından emin olmak önemlidir.
Kalıp çeliği ısıl işlemi:
Kalıp çeliği ısıl işlemi, mekanik özelliklerini ve boyut kararlılığını iyileştirmek için bir enjeksiyon kalıbının çelik bileşenlerini ısıtma ve soğutma işlemidir. Isıl işlemin amacı çeliği sertleştirmek, kalan gerilimleri gidermek ve aşınma direncini ve tokluğunu iyileştirmektir. Bu özellikle enjeksiyon kalıbının sertleştirilmiş çeliği içindir, enjeksiyon kalıbını yapmak için önceden sertleştirilmiş çelik kullanılıyorsa bu ısıl işlem işlerini yapmaya gerek yoktur. Kalıp çeliği ısıl işleminde yer alan ana adımlar şunlardır:
- Tavlama: Çelik bileşenler genellikle 800-900°C arasındaki belirli bir sıcaklığa kadar ısıtılır ve daha sonra iç gerilimleri gidermek ve çeliğin işlenebilirliğini artırmak için yavaşça soğutulur.
- Sertleştirme: Çelik bileşenler genellikle kritik sıcaklığın üzerinde yüksek bir sıcaklığa ısıtılır ve ardından genellikle yağ veya suda söndürme yoluyla hızla soğutulur. Bu işlem çeliği sertleştirir ve aşınma direncini artırır.
- Tavlama: Sertleştirme işleminden sonra çelik bileşenler, çeliğin tokluğunu ve boyut kararlılığını artırmak için belirli bir süre daha düşük bir sıcaklığa ısıtılarak tavlanır.
Isıl işlem süreci, enjeksiyon kalıbının çelik bileşenlerinin yüksek kaliteli kalıplanmış parçalar üretmek için gerekli olan istenen mekanik özelliklere ve boyutsal kararlılığa sahip olmasını sağlamak için kritik öneme sahiptir. Isıl işlem sürecinin doğru ve doğru özelliklere göre yapıldığından emin olmak için kalıp çeliğini işleme konusunda deneyimli bir ısıl işlem sağlayıcısıyla çalışmak önemlidir.
Kalıp boşluğu ve çekirdek ince işleme:
Kalıp boşluğu ve çekirdek ince işleme, kalıbın son şeklini ve boyutunu elde etmek için kalıp boşluğunun ve çekirdek ek parçalarının iç yüzeylerini hassas bir şekilde işleme sürecidir. Bu adım genellikle yüksek hassasiyet ve doğrulukla bilgisayar sayısal kontrol (CNC) makineleri kullanılarak yapılır. Kalıp boşluğu ve çekirdek ince işlemede yer alan ana adımlar şunlardır:
- Yüzey hazırlığı: Kalıp boşluğunun ve çekirdek ek parçalarının yüzeyi temizlenir ve parlatılarak kalıntılar ve pürüzler giderilir.
- Yüzey işleme: Kalıp boşluğunun ve çekirdek ek parçalarının iç yüzeyleri, kalıbın son şeklini ve boyutunu elde etmek için CNC makineleri kullanılarak işlenir. Bu, kalıplanmış parçanın metin, logolar ve alt kesimler gibi karmaşık ayrıntılarını ve özelliklerini oluşturmayı içerir.
- Yüzey muayenesi: İşlenmiş yüzeylerin gerekli toleransları ve özellikleri karşıladığından emin olmak için muayene edilir.
- Yüzey parlatma: Kalıp boşluğunun ve çekirdek ek parçalarının iç yüzeyleri, kalıplanmış parçaların yüzey kalitesini artırmak ve kusur riskini azaltmak için yüksek bir son katla parlatılır.
İnce işleme, kalıplanmış parçaların kalitesini ve doğruluğunu belirlediği için enjeksiyon kalıplama sürecinde kritik bir adımdır. İşlemenin doğru ve doğru özelliklere göre yapıldığından emin olmak için kalıp boşluğu ve çekirdek ince işleme konusunda deneyimli bir işleme sağlayıcısıyla çalışmak önemlidir. Bu adım aynı zamanda kalıbın ejeksiyon sisteminin, soğutma kanallarının ve diğer özelliklerin eklendiği ve kalıbın düzgün çalışmasının sağlandığı adımdır.
EDM işleme:
EDM (Elektriksel Deşarj İşleme), enjeksiyon kalıbındakiler de dahil olmak üzere metal parçalarda karmaşık ve son derece hassas şekiller yapmak için kullanılan bir işlemdir. İşlem, kalıp yüzeyinden malzemeyi çıkarmak için elektrik kıvılcımları kullanır ve istenen şekli oluşturur. EDM işlemede yer alan ana adımlar şunlardır:
- Yüzey hazırlığı: İşlenecek kalıp bileşeninin yüzeyi, kalan kalıntıları veya pürüzleri gidermek için temizlenir ve parlatılır.
- EDM kurulumu: EDM makinesi, kalıp bileşeninin malzemesine ve şekline bağlı olarak kıvılcım aralığı, darbe süresi ve elektrot malzemesi dahil olmak üzere doğru parametrelerle kurulur.
- Kıvılcım erozyonu: EDM makinesi, kalıp bileşeninden malzemeyi kaldıran ve istenen şekli oluşturan elektrik kıvılcımları üretir. Bu işlem, EDM makinesinin nihai şekil elde edilene kadar malzemeyi kademeli olarak aşındırmasıyla kademeli olarak yapılır.
- Yüzey muayenesi: İşlenen yüzeyin gerekli toleransları ve özellikleri karşıladığından emin olmak için muayene edilir.
EDM işleme genellikle karmaşık şekillere veya diğer işleme süreçleriyle elde edilmesi zor olan küçük, karmaşık ayrıntılara sahip kalıp bileşenleri için kullanılır. Ayrıca, bir enjeksiyon kalıbının düzgün çalışması için gerekli olan keskin kenarları ve köşeleri üretmek için de kullanılır.
İşlem son derece hassas ve doğrudur ve bu da onu yüksek kaliteli kalıplanmış parçalar üretmek için ideal hale getirir. İşlemin doğru ve doğru özelliklere göre yapıldığından emin olmak için enjeksiyon kalıpları için EDM işleme konusunda deneyime sahip bir EDM sağlayıcısıyla çalışmak önemlidir.
Kalıp yüzey parlatma:
Enjeksiyon kalıp parlatma enjeksiyon kalıp üretim sürecinin son adımıdır. Bitmiş ürünün pürüzsüz ve eşit bir yüzeye sahip olmasını sağlamak için kalıp bileşenlerinin yüzeylerinin düzeltilmesini içerir. Enjeksiyon kalıp cilalamada yer alan ana adımlar şunlardır:

plastik kalıp parlatma
- Yüzey hazırlığı: Kalıp bileşenlerinin yüzeyleri temizlenir ve cilalama için hazırlanır. Kalan pürüzlü noktalar veya işleme izleri, cilalama için pürüzsüz bir yüzey sağlamak amacıyla temizlenir.
- Kaba parlatma: Parlatmanın ilk adımı, kalıp bileşenlerinin yüzeyindeki büyük kusurları gidermeyi içeren kaba parlatmadır. Bu adım genellikle zımpara kağıdı veya aşındırıcı fırça gibi kaba taneli bir aşındırıcı ile yapılır.
- İnce parlatma: İnce parlatma, kalıp bileşenlerinin yüzeyini daha ince bir bitişe kadar düzeltmeyi içeren bir sonraki adımdır. Bu adım, daha ince bir zımpara kağıdı veya aşındırıcı fırça gibi daha ince taneli bir aşındırıcı ile yapılır.
- Parlatma: Parlatma, kalıp bileşenlerinde yüksek parlaklıkta bir yüzey elde etmek için parlatma tekerleği ve parlatma bileşiğinin kullanılmasını içeren parlatma işleminin son adımıdır.
- Muayene: Parlatma işleminden sonra kalıp parçaları, çizik, çatlak veya diğer kusurlar olmadan pürüzsüz ve eşit bir yüzeye sahip olduklarından emin olmak için iyice incelenir.
Enjeksiyon kalıp cilalama, nihai ürünün kalitesini etkilediği için önemlidir. İyi cilalanmış bir kalıp, ürünün işlevselliği ve estetiği için önemli olan pürüzsüz ve eşit bir yüzeye sahip bir ürünle sonuçlanır. Kalıp bileşenlerinin doğru özelliklere ve istenen kalite seviyesine göre cilalandığından emin olmak için deneyimli bir kalıp cilalayıcısıyla çalışmak önemlidir.
Kalıp montajı
Kalıp montajı, enjeksiyon kalıplama alanında uzmanlaşmış bir iştir ve enjeksiyon kalıplarının montajını, kurulumunu ve testini içerir. Kalıp ustaları, kalıp bileşenlerinin düzgün bir şekilde monte edilmesini ve doğru şekilde çalışmasını ve kalıbın istenen kalite ve performans standartlarına sahip parçalar üretmesini sağlamaktan sorumludur. Kalıp montajcılarının temel sorumluluklarından bazıları şunlardır:
- Kalıp bileşenlerinin montajı: Kalıp ustaları, enjeksiyon kalıbının boşluk ve çekirdek bileşenleri, yolluk sistemi ve tüm yardımcı bileşenler dahil olmak üzere çeşitli bileşenlerinin montajından sorumludur.
- Kalıbın kalıp montaj makinesine takılması: Moldmaster, kalıbın düzgün hizalanmasını ve çalışmasını sağlayacak şekilde kalıbı kalıp montaj makinesine monte edebilmelidir; eğer bir kalıp montaj makinesi yoksa kalıbı takmak için manuel yöntemi kullanın, çoğu şirket bunu yapar.
- Kalıbın test edilmesi: Kalıp ustası, istenen kalite ve performans standartlarına sahip parçalar ürettiğinden emin olmak için kalıbı test etmekten sorumludur. Bu, parçaların eğilme, büzülme veya diğer kalite sorunları gibi herhangi bir kusur açısından incelenmesini içerir.
- Kalıbın ayarlanması: Test aşamasında herhangi bir sorun bulunursa, kalıp ustası, istenilen özelliklere uygun parçalar üretildiğinden emin olmak için kalıbın gerekli ayarlamalarını yapmaktan sorumludur.
- Sorun Giderme: Kalıp ustası, kalıp montaj süreci sırasında ortaya çıkabilecek sorunları tespit edip giderebilmelidir.
Kalıp takma işleri teknik bilgi, el becerisi ve ayrıntılara dikkatin bir kombinasyonunu gerektirir. Kalıp ustaları çok çeşitli alet ve makinelerle çalışabilmeli ve enjeksiyon kalıplamada yer alan karmaşık süreçleri anlayabilmelidir. Kalıp montajcılarının enjeksiyon kalıplama süreci hakkında iyi bir anlayışa sahip olması ve farklı kalıp ve malzeme türleriyle çalışma deneyimine sahip olması önemlidir.
İlk Enjeksiyon kalıplama denemesi veya çekimi:
Enjeksiyon kalıplama deneme çekimi, enjeksiyon kalıplama sürecini kullanarak bir örnek parça üretmek için enjeksiyon kalıbını test etme sürecini ifade eder. Bu süreç, üreticinin kalıbın performansını değerlendirmesine ve büyük miktarda parça üretmeden önce gerekli ayarlamaları yapmasına olanak tanıdığı için enjeksiyon kalıplama sürecinde kritik bir adımdır.
Enjeksiyon kalıplama deneme atış süreci genellikle aşağıdaki adımları içerir:
- Hazırlık: Kalıp enjeksiyon kalıplama makinesine yerleştirilir ve makine atış için ayarlanır. Hazne plastik reçine ile doldurulur.
- Eriyik sıcaklığı kontrolü: Eriyik sıcaklığı, plastik reçinenin yüksek kaliteli parçalar üretmek için doğru sıcaklığa ısıtılmasını sağlamak amacıyla kontrol edilir.
- Enjeksiyon: Erimiş plastik yüksek basınç altında kalıba enjekte edilir. Basınç, kalıp plastik reçine ile dolana kadar korunur.
- Soğutma: Plastik reçineyi katılaştırmak ve parçayı oluşturmak için kalıp soğutulur. Soğutma süresi, kullanılan plastik reçinenin türüne ve üretilen parçanın boyutuna ve şekline göre belirlenir.
- Çıkarma: Parça katılaştığında kalıptan çıkarılır. Çıkarma pimleri parçayı kalıptan dışarı itmek için kullanılır.
- Muayene: Kalıptan çıkan parçanın istenilen özelliklere ve kalite standartlarına uygun olduğundan emin olmak için detaylı bir şekilde muayene edilir.
- Ayarlamalar: Gerektiğinde kalıbın performansını ve üretilen parçaların kalitesini iyileştirmek için kalıplama sürecinde ayarlamalar yapılabilir.
Enjeksiyon kalıplama deneme atış süreci, üreticinin kalıbın performansını değerlendirmesine ve büyük miktarda parça üretmeden önce gerekli ayarlamaları yapmasına olanak tanıdığı için enjeksiyon kalıplama sürecinde önemli bir adımdır. Bu süreç, kalıbın istenen özelliklere sahip yüksek kaliteli parçalar ürettiğinden emin olmaya yardımcı olur.
Kalıp paketleme ve üretime hazır hale getirme:
Kalıp, kalıp üreticisi tarafından tamamen tamamlandıktan sonra, bir sonraki adım seri üretimdir. Kalıp paketleme ve üretime hazırlık, seri üretim başlamadan önce enjeksiyon kalıplama sürecinin son adımıdır. Bu adım aşağıdaki görevleri içerir:
- Temizlik ve bakım: Kalıp, herhangi bir kalıntı, kir veya hasar olmadığından emin olmak için iyice temizlenir ve incelenir.
- Paketleme ve depolama: Kalıp, hasarı önlemek ve ihtiyaç duyulduğunda kullanıma hazır olmasını sağlamak için dikkatlice paketlenir ve güvenli bir yerde saklanır.
- Test ve ayarlama: Kalıp, sızıntı, kötü doldurma veya uygunsuz parça çıkarma gibi sorunlara karşı test edilir ve kalıbın düzgün çalıştığından emin olmak için gerekli ayarlamalar yapılır.
- Üretim Kurulumu: Kalıp enjeksiyon kalıplama makinesine yerleştirilir ve sıcaklık, basınç ve enjeksiyon hızı gibi tüm gerekli ayarlar, özel üretim gereksinimlerini karşılamak üzere ayarlanır.
- Üretim başlangıcı: İlk parça partisi üretilir ve parçaların gerekli özellikleri ve kalite standartlarını karşıladığından emin olmak için süreç izlenir. Üretim sürecini optimize etmek ve tutarlı kaliteyi sağlamak için gerekli ayarlamalar yapılır.
Genel olarak, kalıbın üretime hazırlanması, enjeksiyon kalıplama sürecinde üretim sürecinin başarısını ve verimliliğini sağlamaya yardımcı olan önemli bir adımdır.
Yukarıdaki bilgiler bir enjeksiyon kalıbı yapma prosedürleridir, belki bazı küçük şeyler gözden kaçmıştır ancak çoğu şey yukarıdadır, görebileceğiniz gibi bir enjeksiyon kalıbı yapmak kolay bir durum değildir, eğer elinizde bir enjeksiyon kalıbı projesi varsa, size hizmet verecek profesyonel bir enjeksiyon kalıbı üreticisi bulmanız gerekir, bu projenizin başarılı bir şekilde yürütülmesini sağlayacaktır.
Sincere Tech profesyoneldir Çin kalıbı özel enjeksiyon kalıpları üretiminde uzmanlaşmış fabrika. Çeşitli endüstriler ve uygulamalar için yüksek kaliteli enjeksiyon kalıplarının tasarımı, geliştirilmesi ve üretimi konusunda deneyim ve uzmanlığa sahiptirler.
Müşterilerinin mümkün olan en iyi sonuçları almasını sağlamak için kalıp tasarımı, prototipleme, kalıp üretimi ve kalıp sonrası işleme dahil olmak üzere bir dizi hizmet sunarlar. Kalite, hassasiyet ve müşteri memnuniyetine odaklanmalarıyla Sincere Tech, tüm enjeksiyon kalıplama ihtiyaçlarınız için güvenilir ve itibarlı bir ortaktır. Projeniz için hemen e-fiyat almak için bizimle iletişime geçin.