Kalıp akış analiz raporu nedir?
Kalıp Akış Analizi (MFA), enjeksiyon kalıplama işlemi sırasında bir kalıptaki plastik reçinenin akışını tahmin etmek ve optimize etmek için kullanılan bir simülasyon aracıdır. Simülasyon, reçinenin özelliklerini ve kalıbın geometrisini hesaba katar ve plastiğin kalıbı doldururken ve soğurken davranışını tahmin eder.
Kalıp Akış Analizi raporu Enjeksiyon kalıplama sürecinde oluşan kısa paslar, eğilme, kaynak çizgileri, hava hapsi, çökme izleri vb. gibi potansiyel sorunların belirlenmesine ve çözülmesine yardımcı olabilir. Kalıp Akış Analizi raporu Ayrıca, kapılar ve koşucular için en iyi konumu belirleyerek, optimum enjeksiyon hızını belirleyerek ve en iyi soğutma süresini ve sıcaklığını tahmin ederek enjeksiyon kalıplama sürecini optimize etmek için de kullanılabilir. Bu, çevrim süresini azaltmaya, parça kalitesini iyileştirmeye ve üretim verimliliğini artırmaya yardımcı olabilir.
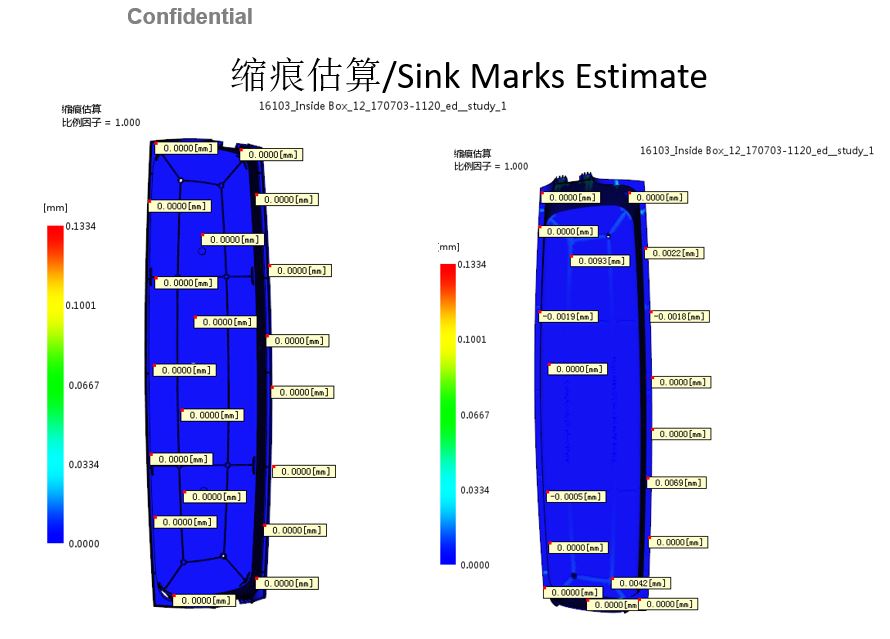
Kalıp akış analiz raporu
Kalıp Akış Analizi Sonuçları Özeti
Kalıp tasarımını bitirdiğimizde, kalıp imalatına başlamadan önce, her şeyin sorunsuz olduğundan emin olmak için, şunları yapmamız gerekir: kalıp akış analizi Olası sorunları kontrol etmek, özellikle büyük kalıplar için hatalardan kaçınmanın güvenli bir yoludur. Aşağıda kalıp akış analizi raporu hazırlarken kontrol etmemiz gereken bazı noktalar bulunmaktadır.
Kalıp Doldurma Süresi – Doldurma süresi, parça boşluğunu doldurmak için gereken süredir. Doldurma süresi grafiği ayrıca kalıp boşluğunun doldurulmasının bir animasyonunu da sağlar. Doldurma süresi, yüksek kesme gerilmeleri gibi kalite sorunlarını çözmek için analiz sırasında da kontrol edilebilir.
Enjeksiyon Basıncı – Standart bir enjeksiyon kalıplama makinesi eriyik akışını 20.000 psi'ye (2.000 psi hidrolik gösterge basıncı) kadar basınçlandırabilir. Basıncın bir kısmı plastiği kanal sisteminden itmek için kullanılır, basıncın bir kısmı plastiği kanal sistemine itmek için kullanılır. kalıp boşluğuve basıncın bir kısmı, doldurulduktan sonra parçayı "paketlemek" için kullanılır. Parça ve koşucu sistemi, makinenin kapasitesinden daha fazla basınç gerektiriyorsa, parça kısa bir atış olacak veya derin olacaktır batma izleri.
Kaynak Hatları Kusurlar – Kaynak çizgileri, iki akış cephesi bir araya geldiğinde ve birlikte “kaynaklandığında” oluşur. Kaynak çizgileri genellikle parça üzerinde görünür bir çizgidir ve bir görünüm sorunu olabilir. Kaynak çizgileri ayrıca parçanın mukavemetini 10% – 20% oranında azaltabilir ve konumlarına bağlı olarak yapısal bir soruna yol açabilir. Kalıp akış analizi, alet üretilmeden önce bu sorunları gidermek için kullanılmazsa, kalıpçı şunları yapmak zorunda kalacaktır: enjeksiyon basıncını artırmak, eriyik sıcaklığını artırmak, kalıp sıcaklığını artırmak, havalandırma deliklerini genişletmek, kapının yerini değiştirmek ve/veya parçanın kalınlığını değiştirmek. Tüm bu “çözümler” uygulamak için zaman ve para gerektirir ve/veya parçanın maliyetini artırır.
Hava Tuzakları Kusurlar – Erimiş plastik, parça boşluğunu doldururken havayı hapsettiğinde hava tuzakları oluşur. Bu hava tuzakları havalandırılmazsa yanık izleri, kısa atışlar, belirgin kaynak çizgileri ve eksik doldurma gibi kalite sorunlarına yol açabilir. Hava tuzağı çizimlerimiz, kalıp üreticisinin alet yapılırken havalandırma deliklerinin tam olarak nereye yerleştirilmesi gerektiğini bilmesini sağlar. Havalandırması zor yerlerde bulunan hava tuzakları, kapı hareket ettirilerek daha iyi yerlere taşınabilir. Bu işi alet yapılmadan önce yapmak, gereken hata ayıklama ve kalıp değişikliği miktarından tasarruf sağlayabilir.
Kalite – Kaliteli kalıplanmış bir parçanın tanımı yalnızca parçanın tamamen dolması değildir. Kaliteli kalıplanmış bir parça aynı zamanda malzeme bozulmasından arınmış ve kalıplanmış gerilimde düşük olmalıdır. Kalite grafiği, kalite sorunlarının ciddiyetini ve yaşandığı alanları gösterir. Tespit edilen sorunlar arasında aşırı kayma gerilimi ve kayma hızı ve paketlenmesi zor alanlar bulunur. Kalite sorunlarını ortadan kaldırmak için kalınlık ayarlamaları, işleme koşulu değişiklikleri ve dolum süresi ayarlamaları gibi öneriler denenebilir.
Çökme izleri Kusurlar – Çökme izleri, enjeksiyon kalıplı parçaların yüzeyinde, soğutma sırasında plastiğin düzgün olmayan bir şekilde büzülmesi nedeniyle oluşan lokal çöküntülerdir. Kozmetik açıdan kritik parçalarda ciddi bir sorun olabilirler. Çökme izleri genellikle alet tamamlandığında sürpriz olarak ortaya çıkar. Çökme izleri müşteri için sakıncalıysa, kalıpçı genellikle "bunları ortadan kaldırmakla" görevlendirilir. Bu genellikle kalıplama makinesini işlem penceresinin uç noktalarında çalıştırmak anlamına gelir, bu da çevrim sürelerini uzatabilir ve kalıplanmış gerilim miktarını ve malzeme bozulmasını artırabilir.
Soğutma Süresi – Soğutma süresinin kalıplama döngüsünün ortalama 50%'si olduğu gösterilmiştir. Kullanılan malzeme bir emtia reçinesiyse, kalıplama maliyeti malzeme maliyetinden çok daha fazladır. Bu durumda, soğutma süresindeki bir azalma parça maliyetinde büyük bir azalmaya neden olur. Soğutma Analizimiz soğutma döngünüzü azaltabilir ve soğutma sisteminizi optimize ederek sıcak noktaları ve eğrilmeyi ortadan kaldırabilir.
MFA, plastik reçinenin kalıptan akarken ve soğurken davranışını simüle ederek enjeksiyon kalıplama sürecinin verimliliğini ve kalitesini iyileştirmeye yardımcı olabilen güçlü bir araçtır. Potansiyel sorunları belirlemeye ve kusurları en aza indirmek ve nihai ürün kalitesini iyileştirmek için süreci optimize etmeye yardımcı olur.
Projeniz için kalıp akış analizi yapıyoruz
Çok fazla endişe duyduğunuz bir projeniz varsa lütfen bizimle iletişime geçin, tüm parça çizimlerinizi kontrol edip, DFM raporu Ve kalıp akışı Sizin için analizler hazırlayıp, olası tüm sorunları veri sayfasında özetleyip size geri gönderiyoruz.