Many industries cannot complete without plastic end caps that perform protective and finishing functions for pipes, tubes, and other materials with gaps at the ends. They protect products from dust, debris and the environment thus increasing the product’s longevity and the product’s looks. Plastic end caps come in some designs and sizes, and can even be purchased in custom sizes as well. In this article we will look at their application, how they are manufactured, and the advantages and disadvantages of plastics use in these applications.
What Are Plastic End Caps?
The plastic end caps are molded closures that cover the ends of pipes, tubes, and other cylindrical parts. Such caps, when they exist, can be of different designs, from small to large, and are normally designed for protection of the interior of the item against contaminants, humidity, or mechanical injury. Moreover, these plastic end caps are manufactured from polyethylene, polypropylene, or PVC. Besides this, they vary in size and use depending on the application, and the dimensions of the sleeve.
Different Types of Plastic End Caps
The following are different types of plastic end caps;
1. Standard End Caps
Fundamental coping mechanisms that occur to seal open pipe ends from dust, dirt, and other undesirable elements. Frequently used in construction, plumbing, and furniture for fast and firm operations to cover things. They give a neat appearance and help minimize cases of chances of people getting injured by sharp edges.
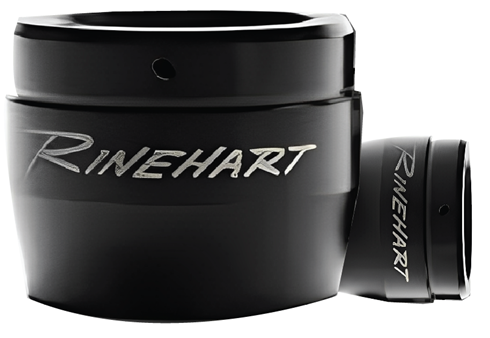
2. Threaded End Caps
Lids with internal thread interface directly with threaded pipes affording the system enhanced security against leakage while maintaining a snug fit. Heavily used in plumbing, automobile, and industrial applications where the hold is critical. Another is, that they proved capable of withstanding pressure differences and are also constructed to hold steady and secure despite the most erratic conditions.
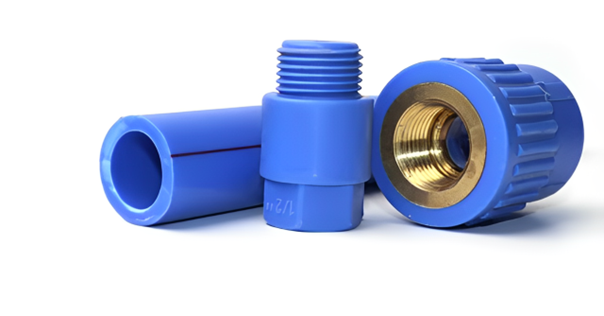
3. Push-On Caps
Sleeves that may be slipped onto pipe ends without any sort of press fit, retained only by their internal or external flutes. Performs best under conditions that involve temporary protection of the products whether in storage, transport, or assembly. Due to this, they can be easily wielded and unbended, and they come in handy since they easily suit several pipe diameters.
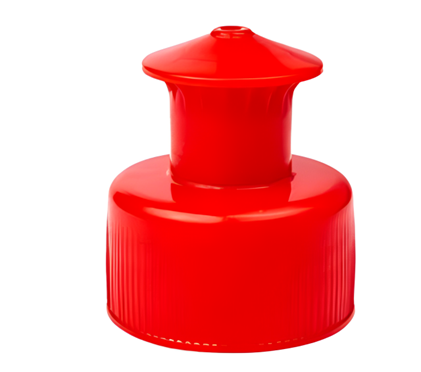
4. Flexible End Caps
It is flexible hoses made from soft stretchable plastics designed to fit a variety of pipe diameters which makes them suitable for uneven shapes or dimensions. Most frequently used in packaging and specific instances where close tolerance fit is desirable it minimizes movement and associated damage during shipping.
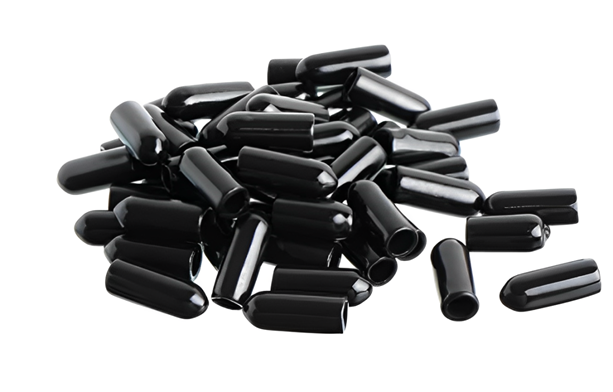
5. Tapered Caps and Plugs
Reduced flared shape also helps the device to fit so tightly across various pipes or holes suitable and at the same time, quickly removable. These caps are commonly employed in masking, painting, and coating industries as protective caps for surfaces during finishing stages; they do not melt or corrode under heat and chemical exposure.
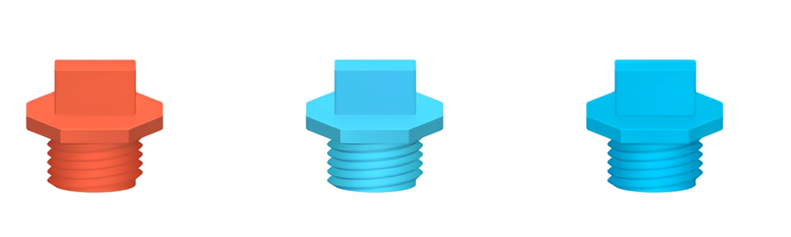
6. High-Temperature Caps
This type of cap is usually made of silicone or a certain polymer because these materials are heat resistant and safe for use in high-temperature applications such as powder coating and plating. Frequently encountered in industries they guard delicate materials against heat which is reciprocated again in terms of its providing heavy duty to endure the worst.
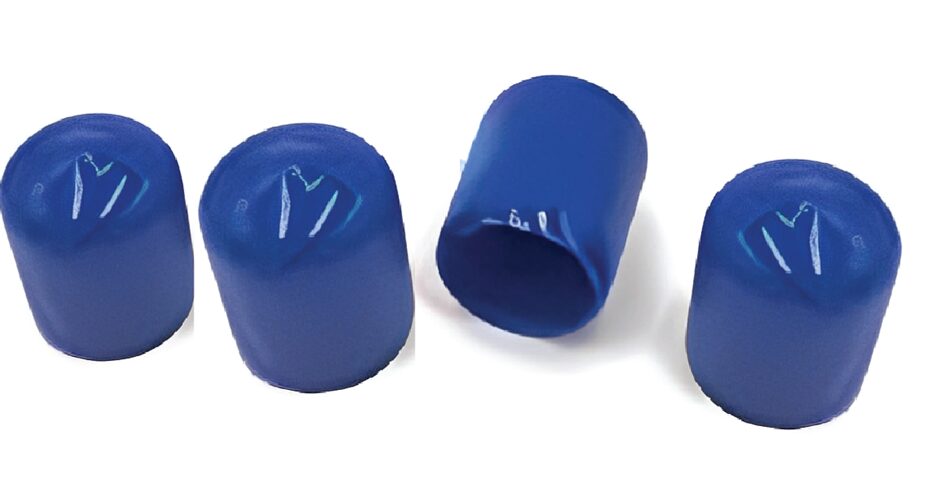
Size Guide Table for Plastic End Caps
Here is a detailed table for the different size guide for plastic end caps;
Pipe Diameter (inches) | Pipe Diameter (mm) | Wall Thickness (inches) | End Cap Outer Diameter (inches) | End Cap Inner Diameter (inches) | Suggested Use/Application |
0.5″ | 12.7 mm | 0.065″ | 0.6″ | 0.5″ | Small tubing and light protection |
1″ | 25.4 mm | 0.1″ | 1.1″ | 1″ | General-purpose pipes, moderate protection |
1.5″ | 38.1 mm | 0.1″ | 1.6″ | 1.5″ | Medium-duty pipes, indoor and outdoor use |
2″ | 50.8 mm | 0.15″ | 2.15″ | 2″ | Plumbing and structural applications |
2.5″ | 63.5 mm | 0.2″ | 2.7″ | 2.5″ | Heavy-duty pipes, industrial settings |
3″ | 76.2 mm | 0.25″ | 3.15″ | 3″ | Large tubes, high-impact environments |
4″ | 101.6 mm | 0.3″ | 4.3″ | 4″ | Outdoor piping, protection from debris |
6″ | 152.4 mm | 0.35″ | 6.4″ | 6″ | Large pipes, outdoor or industrial usage |
Custom Sizes end caps | Variable | Variable | Customizable | Customizable | For specialized applications, unique fits |
Complete Plastic End Cap Making Process
Plastic end caps are made through a protracted and meticulous process to ensure every cap is functional as well as visually appealing. Here’s a breakdown of each step in the production process:
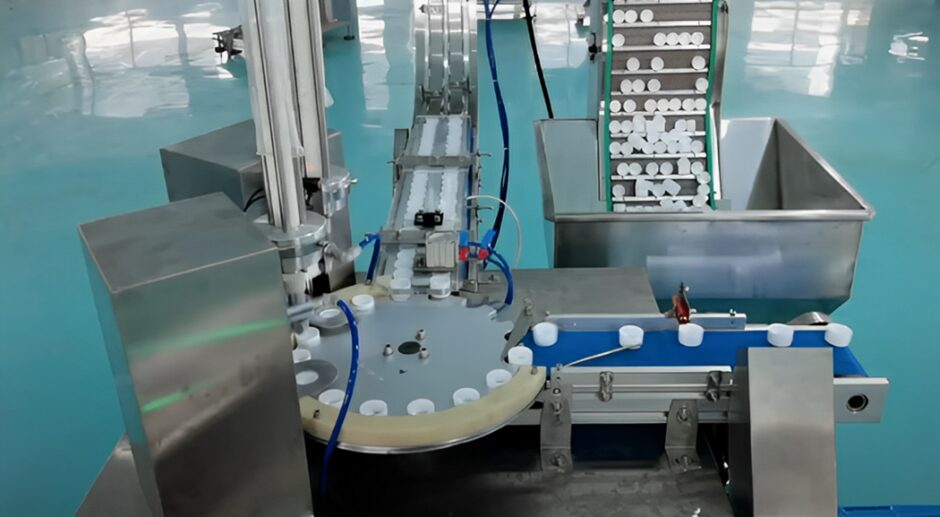
Design and Mold Preparation
The process begins with designing the end cap, based on its required size, shape, and intended function. These specifications might include whether the cap will be threaded, have a smooth finish, or have a particular color or texture. After the design is finalized, a custom mold is prepared. Molds are usually constructed from high-tensile steel or alloys such as cast aluminum as a result of the heat and pressure that is applied during the process. Straight from the mold, this creates the shape and style of the desired cap from the molten melted plastic.
Material Selection
Different plastic materials are appropriate for the cap’s use depending on its intended function and longevity.
- Polyethylene (PE), Polypropylene, and Polyvinyl Chloride (PVC) are the most used in packaging. Each has distinct properties:
- They also stretch easily, are extremely resistant to impact, and are useful in caps that might be roughly used.
- One advantage of PP the chemical resistance and rigidity; good for caps that may come in contact with oil, acid, or any chemicals.
- PVC is a strong material in any application as it can easily withstand the effects of UV light. The choice of the material mainly depends on the working conditions of the cap, the flexibility required, its cost, and the life expected.
Injection Molding
In this step, the chosen material, i.e. plastic is melted into a liquid state, and a mold is filled in an injection molding machine. The pressure is high to shape the plastic melt into the form of mold. After the mold fills, we allow the plastic to cool. This stage gives the part its proper shape after which the part is ejected.
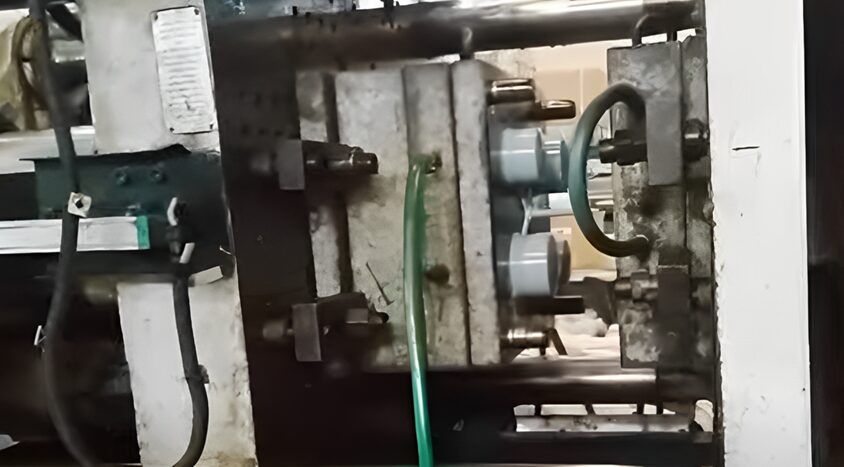
Finishing and Quality Check
In the post-molding process, caps may endure extra treatments to produce a more attractive appearance and functionality. Common finishing touches include:
- Edge Smoothing: These are fine silky edges that are free from any sharp edges or bits of fragments from the molding process, to ensure the best and safest corner is achieved.
- Surface Texturing: Additional structures may be built for enhancing efficiency or embedding aesthetic features.
- Coloring or Branding: There are certain types of caps under which additional color decoration, logo, or labeling as per the customer demand. Subsequently, quality checks are made to ascertain that they meet all the required specifications on the caps. This comprises dimensional qc, consistency, and general appearance, to ensure that there are no imperfections on the product that could affect its performance.
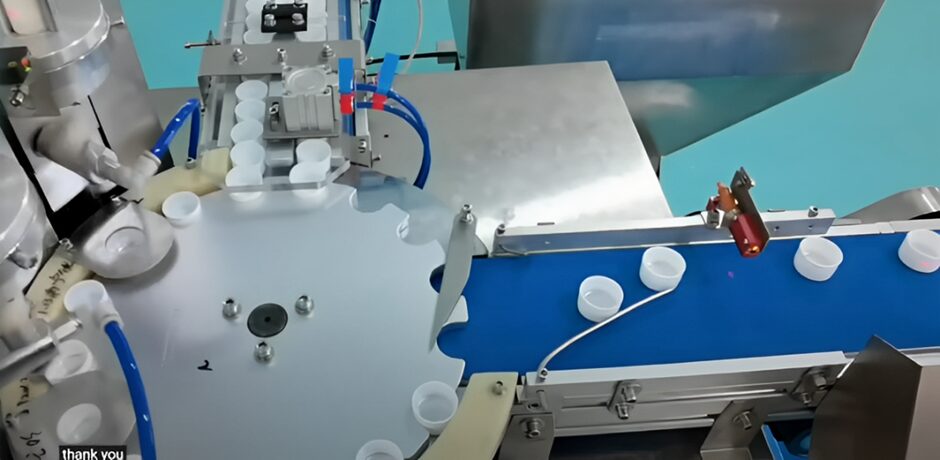
Packaging and Distribution
After passing through the inspection process the caps are packaged and ready for shipping. If the order quantity is high and or the customer has special requests on how they want their caps delivered then the caps might be packed in bulk or one at a time. They are then sold to retailers, industry customers, or other consumers who need them for various uses.
What are Plastic End Caps Used for?
Here are some points where we can use plastic end caps;
1. Protection Against Contaminants
Plastic end caps are extensively used to shield the open ends of pipes, tubes, and rods against dust, dirt, humidity, and other proprieties in the environment. Some of these include protection of the internal surfaces from fouling or from getting damaged when in storage or transport.
2. Preventing Damage
Caps help to protect the exposed ends of the pipes and tubes from mechanical harm. These protect these surfaces from any shocks, scrapes, or any other harm that might in some way compromise the strength or durability of such a surface in the future.
3. Safety Measures
Plastic end caps smooth over any exposed edges that may be raised or incompletely rounded off, thus increasing the safety of any area where pipes or tubes come into play. This is especially the case in construction and production facilities where one can easily sustain a cut in the course of working within the facility.
4. Sealing for Storage
In pipes and tubes, plastic end caps are usually placed on their ends to protect them from moisture when in storage for the moisture may lead to corrosion or other forms of degradation. This sealing plays an important role in protecting materials in their use and durability in particular, in outdoor conditions or in areas with high humidity.
5. Aesthetic Finishing
The cut ends of carpets are also an occasion where plastic end caps are used as they add the final all-polished look that offers functionality and durability many other instances one can see plastic end caps used in furniture and consumer products. First, they can improve the general appearance of products, as many of them need side cutting to create a final rim, which can become a good brand and attractive to buyers.
6. Facilitating Assembly
The temporary enclosure of components before moving to another section can be done by enclosing the product with plastic end caps in production lines. This can reduce manufacturing cycles since materials handling and transportation of parts can occur in a manner that will not compromise contamination or damage.
7. Custom Applications
Most industries apply end caps made of plastic that are also developed to meet a specific size and shape or serve a specific function. In some cases they can retain special features, for example, they may be used for insulation of electric wires, or they can meet certain standards necessary in the automobile industry, plumbing, or construction.
Design Guide for Custom Plastic Caps and Plastic Pipe End Caps
Creating custom plastic end caps involves considering;
- Material Selection: Select depending on the desired level of thickness, resistivity to high temperatures, and chemical solvents.
- Fit and Functionality: It can only cover the head without compromising the aim of protecting from the cold or rain.
- Color and Branding: Optional colors or logos will improve branding or help to distinguish the product in question.
- Shape and Texture: Having edges rounded or beveled enhances safety as well as the appearance of the Aluminum product, grooved textures enhance the grip on aluminum surfaces.
- Environmental Factors: Those to be worn outdoors might require either UV protection or coated or thicker materials.
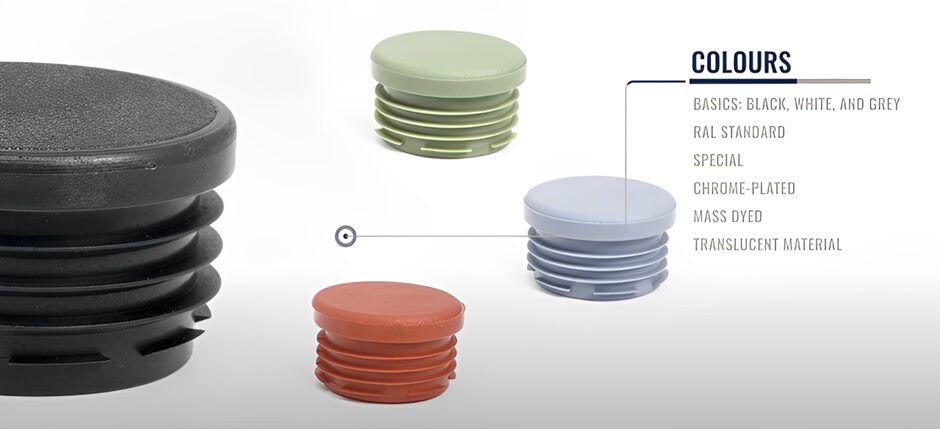
Advantages of Plastic End Caps
Here are some of the benefits of custom plastic end caps;
- Cost-Effective: The raw materials used in the product manufacturing are inexpensive, which makes them suitable for different uses.
- Lightweight: Since they are lightweight, the plastic end caps do not affect the final product’s overall weight. But it will easily fit for transportation and installation.
- Versatile: They come in many shapes and sizes and with customizable possibilities.
- Durable and Long-Lasting: Hard wearing and durable in the face of environmental variety.
- Eco-Friendly Options: Aesthetically pleasing designs can be created from recycled materials and help improve environmental conservation
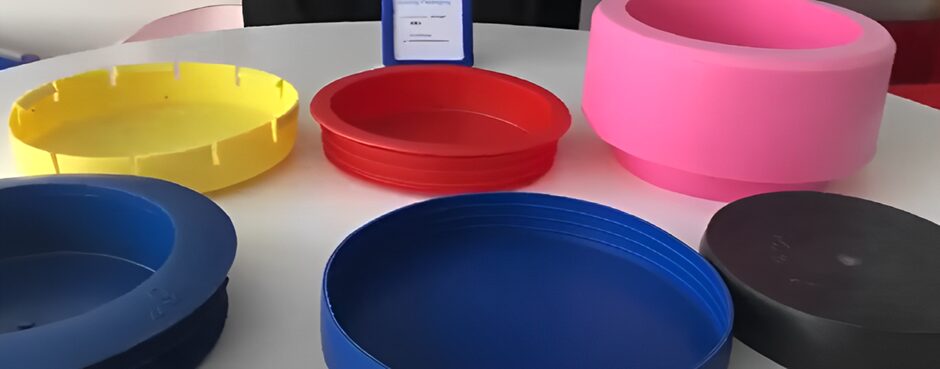
Limitations of Plastic End Caps
Plastic end caps also offer some limitations, such as;
- Heat Sensitivity: For some plastics, when exposed to high temperatures causes them to change shape.
- Less Durable than Metal: Under very severe conditions of temperature, they use metal often.
- UV Sensitivity: The plastic caps can be compromised when exposed to long sunlight.
- Limited Flexibility for Rigid Plastics: They are not versatile enough for applications where flexibility is needed especially when extreme bending.
- Environmental Concerns: People should recycle plastics because if they do not, they harm the environment.
Conclusion
In conclusion, plastic end caps are versatile tools in many industries because they provide protection, appearance, and branding for pipes, tubes, and products with open ends. Owing to their affordability, sturdiness, and adaptability, produced concrete tiles are suitable for use in many sectors. They have their drawbacks, but if a clear layout and choice of materials are used, they can be optimized. For purposes ranging from shielding delicate equipment to branding a finish on goods, plastic end caps effectively provide across-the-board solutions. So, if you are looking for a plastic end caps manufacturer, Get your Quote now.
Sincere Tech is one of top 10 plastic injection mold manufactuers in China that offer custom plastic injection mold and molding parts, part design and mold design, die casting tooling, CNC machining, assembly, and delivery.
FAQs
What are plastic end caps manufactured from?
Usually, plastic end caps are created from polyethylene, polypropylene, or PVC mainly because these materials are quite rigid and elastic to use.
Are the end caps made of plastic able to be customized?
It is still possible to order special plastic end caps that will be made according to specific dimensions, colors, or requested shapes.
To what extent are plastic end caps recyclable?
Some companies employ the use of reborn plastics, however, the non-biodegradable tamper caps can harm the environment if not disposed of appropriately.
For what industries are plastic end caps?
Some examples of applications are construction items, automotive items, furniture, household items, and electronics. Here plastic end caps are incorporated for protective as well as for aesthetic purposes.
Can plastic end caps be placed on tubes, in the outside environment?
Some plastic end caps are produced with built-in UV and other environmental protection features but the choice of material is vital if the end caps are to be used outdoors.
What are the most important factors when it comes to choosing the size of the plastic end caps?
Determine the diameter of the pipe or tube and put the cylindrical into the corresponding size to make a proper fit.
Can plastic end caps be recycled?
Indeed, this is true that plastic end caps have room for reusing, especially when they are robust and in actual condition when being removed.