It is not easy to select the right plastics for injection molding in the market today. There are hundreds of resins that are available in the market ranging from the general purpose polymers to the specific plastics and polymer alloys, all of which have their own characteristics and conditions for processing. Also, there are different grades within the same plastic material type, such as filled plastics with glass fibers, carbon fibers, or plastics with specific brand names.
Due to this wide range of options, it is often quite challenging to choose the right material for your project. Whether you are exploring medical plastic injection molding or manufacturing molded plastic parts for the automotive industry or any other industry, Sincere Tech’s team of professionals is capable enough to help you from the designing to the manufacturing phase to make it as smooth and fast as possible.
This article will discuss the most commonly employed plastic resins for injection molding, and you can go to injection molding materials slection page to know more tips on more plastics for injection molding.
Commonly Plastics For Injection Molding
The use of plastic injection molding provides a wide variety of materials that can be used in different areas of homes and industries. It is not possible to discuss all the materials in detail, so this write-up will cover some of the most used ones.
Acrylic (PMMA)
Acrylic or Poly (methyl methacrylate) is a thermoplastic material that has moderate mechanical strength, low density and is transparent in nature. While it is not very ductile, it has a good shatter resistance. One of the benefits of this product is that it can be easily machined after injection molding to meet the required changes and finishing. However, it is easily scratched and this affects its transparency and general outlook, and it is prone to absorbing oils and greases that alter the surface characteristics. Acrylic is widely applied in ornamental display cabinets, anti-UV enclosures for solar panels, and glass. Get to acrylic injection molding and PMMA injection molding page to know more about this material.
Acrylonitrile Butadiene Styrene (ABS)
ABS is yet another injection molding material that is widely used due to its strength, toughness, impact strength, and resistance to chemical attacks such as those by acids, bases, and oils. It is entirely transparent and can be produced in different colors. However, there are some limitations of using ABS such as it cannot be exposed to direct sunlight or used in moist areas. It is widely used in industrial applications such as automotive, sports equipment, and prototyping due to its economical and utility characteristics. Get to know more about ABS injection molding.
Nylon Polyamide (PA)
Nylon is a very useful material, which has high values of toughness, heat stability, and surface friction/wear. Its synthetic form, widely used in injection molding, is available in numerous types of grades for various uses. Nevertheless, injection molding nylon is not easy because of high shrinkage rates, and thus, specific attention must be paid to the mold. Some of the nylon products are gear components, bearings, fabrics that are water and wear-resistant, ropes, and others. Know more about Nylon injection molding.
Polycarbonate (PC)
PC is characterized by its high degree of hardness, shatterproof and impact proof, and the transparent type is even superior to glass in many cases. It has a good mechanical properties at high temperatures and, therefore, can be used in high-temperature applications. PC is widely employed in the production of helmet visors, protective machine shields, and goggles because of its high light transmittance. However, it is not recommended for industries such as food and beverages because it has been scientifically established to cause harm to the human reproductive system. Get to know more about polycarbonate injection molding.
All these materials have their own characteristics and benefits, which makes them useful for injection molding in various industries.
Polyoxymethylene (POM)
Polyoxymethylene (POM), also referred to as acetal, is highly accurate and dimensionally stable, which is why it is widely used in applications where high accuracy is required. The material is very stiff, and this makes it have good dimensional stability, this means that the parts being produced will have good dimensions. POM also has a low COF and good lubricity and therefore is suitable for parts that are in constant contact with each other. Also, it does not lose its properties at low temperatures, which are very low in this case.
POM is widely used in injection molding of hard automotive parts such as handles and switches because of its strength and accuracy in dimension. It is also used in other applications such as cutleries, spoons, gears, furniture, and ball bearings. Lear more about POM injection molding.
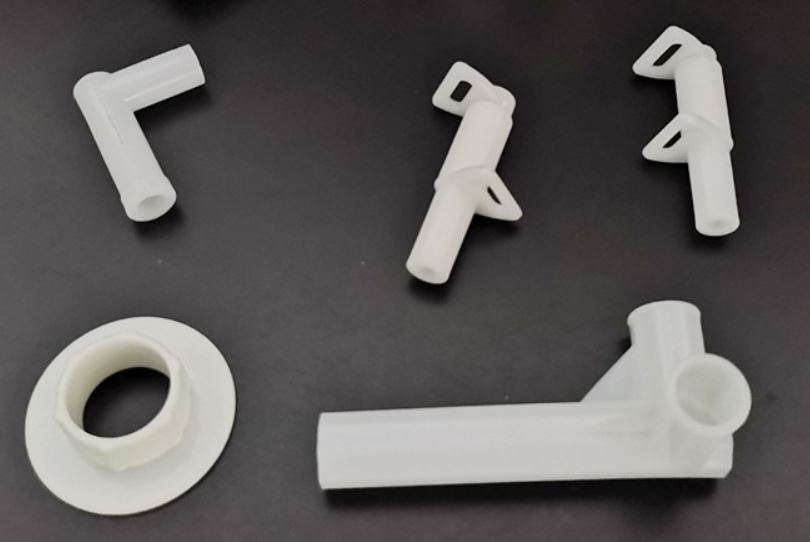
POM injection molding
Polypropylene (PP)
Polypropylene (PP) is one of the most widely used polymers that has found its application in almost all fields and is approved by the FDA for use in food packaging materials. It provides hardness, heat resistance, chemical resistance, and recyclability and is widely used in household utensils, food packing materials, and consumer goods. However, its high thermal expansion coefficient restricts its use in high-temperature applications, and it is sensitive to UV and flammability. Learn more about PP injection molding.
Polystyrene (PS)
Polystyrene (PS) is characterized by low density, resistance to moisture, and a uniform degree of shrinkage during the molding process. Despite being brittle, it is used in toys, appliances, and medical equipment because of its ability to withstand gamma radiation hence, it is used in sterilizable medical equipment. Go to polystyrene injection molding page to know more about this material.
Polyethylene (PE)
Polyethylene (PE) comprises different types, including High-Density Polyethylene (HDPE), Low-Density Polyethylene (LDPE), and Polyethylene Terephthalate (PET), which has different characteristics like ductility, impact strength, and chemical resistance. LDPE is used in flexible applications such as bags and films, while HDPE is used in more rigid applications such as jugs and pipes. Lear more about PE injection molding.
TPE
TPE is an elastomer that combines the characteristics of plastic and rubber; it is flexible, strong, and can be recycled. It is applied in sealing, footwear parts, and anti-vibration applications; however, it is not suitable for high temperatures and extended stretching. Learn more about TPE injection molding.
TPU
Thermoplastic Polyurethane (TPU) has polyurethane’s hardness and rebound resilience and is used in protective housing, power tools, and footwear. It is preferred for its high temperature and abrasion resistance, but it is hard and crystalline, which complicates molding. Learn more about TPU injection molding.
These materials have different types of properties and are used in injection molding for different sectors and products, go to injection molding materials page to learn more common plastics.
Below is table summarizing the characteristics, advantages, disadvantages, and typical applications of each injection molding material:
Material | Key Characteristics | Advantages | Disadvantages | Applications |
Acrylic (PMMA) | Transparent, moderate strength, low density | Shatter-resistant, easy to machine after molding | Prone to scratches, absorbs oils/greases | Display cabinets, anti-UV enclosures, glass substitutes |
Acrylonitrile Butadiene Styrene (ABS) | Tough, high impact strength, chemical resistant, available in colors | Strong, impact-resistant, economical | Not suitable for sunlight exposure, sensitive to moisture | Automotive parts, sports equipment, prototyping |
Nylon (Polyamide, PA) | High toughness, heat stable, wear-resistant | Durable, various grades available | High shrinkage rate, challenging to mold | Gears, bearings, water/wear-resistant fabrics, ropes |
Polycarbonate (PC) | High hardness, shatterproof, transparent | Superior to glass in impact resistance, good for high-temperature applications | Not food-safe, potential reproductive health risks | Helmet visors, machine shields, goggles |
Polyoxymethylene (POM) | High accuracy, stiff, dimensionally stable | Low friction, stable at low temperatures | Limited flexibility | Automotive parts (handles, switches), cutlery, gears, furniture, ball bearings |
Polypropylene (PP) | Hardness, heat-resistant, chemically resistant, FDA approved | Recyclable, suitable for food-related uses | High thermal expansion, sensitive to UV, flammable | Food packaging, household items, consumer goods |
Polystyrene (PS) | Low density, moisture resistant, uniform shrinkage | Sterilizable, durable in radiation exposure | Brittle | Toys, appliances, sterilizable medical equipment |
Polyethylene (PE) | Varies: HDPE (rigid), LDPE (flexible), PET (impact strength) | Chemical-resistant, impact-resistant, flexible (LDPE) | Not suitable for high-temperature applications (LDPE), UV-sensitive (HDPE) | Bags, films (LDPE); jugs, pipes (HDPE); bottles, containers (PET) |
Thermoplastic Elastomer (TPE) | Flexible, strong, combines plastic and rubber properties | Recyclable, used for flexible applications | Limited to low-temperature use, not for long-term stretching | Seals, footwear parts, anti-vibration applications |
Thermoplastic Polyurethane (TPU) | Hardness, abrasion-resistant, high rebound resilience | Good temperature and abrasion resistance | Difficult to mold due to hardness and crystallinity | Protective housing, power tools, footwear |
Selecting the Right Material for Injection Molding Success
Choosing the right plastic pellets for injection molding for your injection molding project can be quite challenging since there are so many materials to choose from. To make this process easier, it is necessary to provide a brief guide on material selection for injection molding projects.
Material Hardness: If your project requires a particularly hard material, then it is best to use a hard material for your project. Nylon grades exhibit good hardness properties while Thermoplastic Polyurethane (TPU) has good performance but at a higher cost.
Material Flexibility: In the case of flexibility, Thermoplastic elastomers and Polypropylene can be used for the application. TPE has better fatigue characteristics and high temperature, while PP is recyclable and safer.
Cost: Affordable materials are Polypropylene (PP) and Polystyrene (PS) because they are cheap and easy to obtain.
Temperature Resistance: Nylon and ABS are well known for their high-temperature stability, while POM is known to have good low-temperature characteristics.
Applications: Lastly, the material selected should meet the needs of the intended end-use applications as per your needs.
How to Choose the Appropriate Material for Your Injection Molding Project
By using these guidelines, designers are in a position to make the right decisions in relation to the choice of the materials depending on the intended use. For instance: In the case of plastic automotive parts, ABS is a good material to use because it has reasonable hardness and heat resistance at a reasonable price. The soles of the shoes require materials such as TPU for flexibility, lightweight, waterproof, and wear resistance, especially in the production of luxury shoes.
Power tools require Nylon, PET, ABS, or TPU injection molding materials because they are strong, do not vibrate, and may not be affected by heat. Want to know more injection molding materials? Go to how to choose best injection molding materials to know more.
Preliminary Material Preparation For Plastic Injection Molding
The following are the points that have been identified to help in understanding material preparation in plastic injection molding:
Preparation of the material is one of the most important steps in the process of plastic injection molding to achieve the best outcome in the production of the final product. Before initiating the actual injection molding process, several key considerations must be made regarding material preparation: Before initiating the actual injection molding process, several key considerations must be made regarding material preparation:
Pre-Processing Requirements:
However, after setting up the mold, it is crucial to process the purchased materials for injection molding to commence. An important part of this preparation is to remove moisture from the plastic material and to decrease the humidity in the components.
Importance of Drying:
The plastics must be dried to eliminate water, which, if left behind, will compromise the quality of the final product. Polycarbonate, PBT, PET, ABS, acrylic, and polyurethane are some of the hygroscopic resins that are known to absorb moisture from the surroundings. If these materials are not dried before injection, it leads to a reduction of the product strength during the molding process. For hygroscopic plastics, a desiccant dryer is used, while heated ambient airflow is used for non-hygroscopic resins to remove moisture.
Significance of Proper Drying:
The raw material should be dried appropriately because its condition determines the molding process’s results. The problems that arise from high moisture content include the steaming of the workpiece, surface defects like peeling and brittleness, and the formation of a silver-like appearance on the workpiece. Water also decomposes at high temperatures and when combined with the effects of radiation, it weakens the material even more. The moisture content of the material after drying should also be controlled to meet the required standard for the final product.
Therefore, it can be concluded that proper material preparation, especially drying, is the key to success in the processes of plastic injection molding.
Discover the Extraordinary with Sincere Tech’s Injection Molding Services
Sincere Tech is one of plastic injection molding companies in China, who committed to providing the highest quality injection molding services that include various types of plastics. This is in line with our policy of using the best manufacturing facilities, qualified human resources, and a wide range of materials to guarantee the best results for our clients.
The three core values of Sincere Tech are quality, cost, and customer. Our efficiency ensures that we provide quick quotations, elaborate DFM reports, and accurate molding tolerances with round-the-clock engineering support for the project.
Feel the difference with Sincere Tech’s injection molding services. Get in touch with us today to get your rapid prototyping needs met and unleash the full potential of your projects!