What is pin point gate injection molding
Pin-point gate injection molding, also known as hot tip gating or direct gating, is a specialized injection molding technique used to produce plastic parts with precision and efficiency. In this process, the molten plastic is injected directly into the mold cavity through a small gate located at a specific point on the part. Unlike traditional injection molding, where the molten plastic enters the cavity through larger gates, pin-point gating allows for more controlled and targeted filling of the mold.
Pin-point gate injection molding normally use 3 plate injection mold with cold runner and some of hot runner that use hot tip gating This technique is used for multiple cavities of small parts, such as micro-electronic components or medical devices, or multiple pin point gates for a big part, where is not allowing the side wall having any gate marks, pin point gate solution is normally according to the part design and surface requirement.
The pin-point gate is typically located in a location that will be hidden after molding or having no any appearance influence. The small gate size allows for precise control of the flow of plastic into the mold, which helps to reduce the risk of defects such as short shots, air entrapment, and sink marks.
Pin-point injection molding requires careful control of the molding process, including the temperature and pressure of the plastic, the speed of the injection, and the cooling time. This type of molding also requires specialized tooling (3 plate injection mold), as the small size of the pin-point gate requires extra runner plate to pull the runner away from the A plate (cavity).
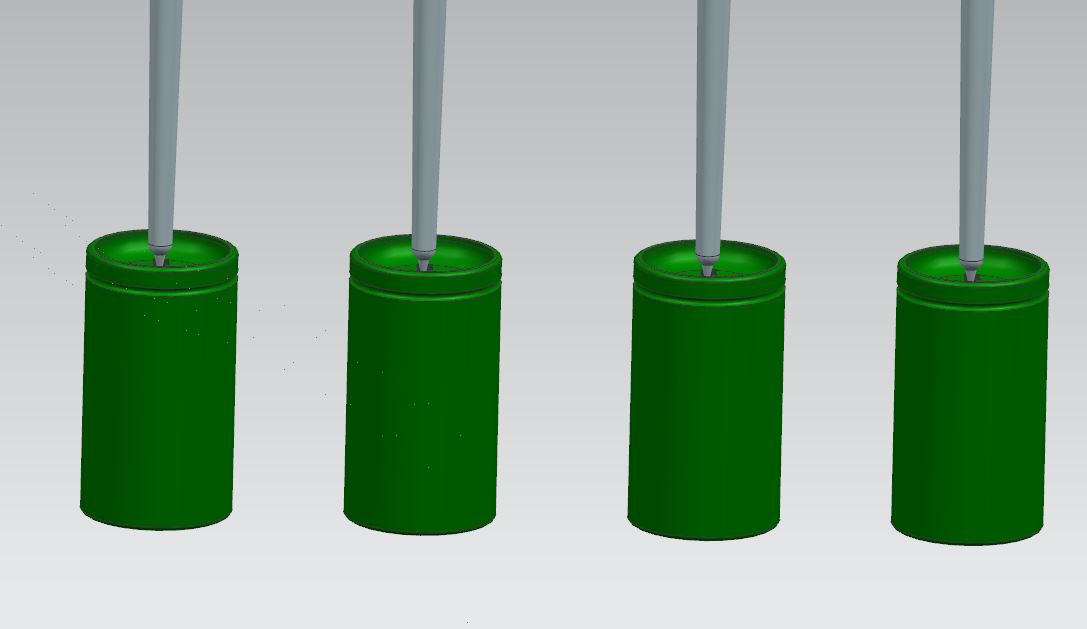
pin-point gate injection molding
How to design the pin pint gate
Designing a pin point gate for an injection mold involves several key steps:
- Determine the location: The location of the pin gate is an important consideration, as it affects the appearance of the finished part. The pin gate should be placed in an area that will be hidden with label after molding, or in an area that will not affect the functionality of the part.
- Consider the flow characteristics: The flow characteristics of the plastic should be considered when designing the pin gate, as this affects the filling of the mold. The size and shape of the pin gate should be selected to ensure that the pin gate can be easy divided by the runner plate, and the plastic flows evenly into the mold, reducing the risk of defects such as short shots, air trap, and sink marks.
- Determine the size: The size of the pin gate should be determined based on the type of material being molded and the size of the part. A smaller pin gate can help to minimize the gate mark, but may also increase the risk of defects if the plastic does not flow evenly into the mold so caused the short shot or sink mark issues. by experience should be diameter 0.8 to 2.5mm, this is depending on the part side,
- Minimize gate mark: The design of the pin gate should aim to minimize the size of the gate mark on the finished part. This can be achieved by choosing a small gate size, and positioning the gate in an area that will not affect the appearance of the part.
- Evaluate the process conditions: The process conditions, such as temperature, pressure, and cycle time, should be evaluated to ensure that they are appropriate for the pin gate design. Proper process control is essential for a successful pin gate design, normally the cycle time will be long than the side gate or sub-gate.
Advantages and Disadvantages of pin point gate injection molding
Pin gate offers some advantages over other gate types, but they also come with some disadvantages such as increased cost and complexity. The suitability of a pin gate for a specific application depends on several factors, including the type of material being molded, the size and shape of the part, and the desired level of quality. It is recommended to work with a mold designer or engineer who has experience in injection molding to determine the optimal gate design for a specific application.
Advantages of Pin Gates:
- Minimal Mark: Pin gates produce a small, circular gate mark that can be easily hidden or designing the pin gate as decoration mark on the part surface.
- Improved Aesthetics: Pin gate feeding produce a smaller gate mark than larger gate types, such as the sprue or edge gate, which improves the overall appearance of the finished part.
- Improved Quality: Pin gate feeding solution help to reduce the risk of defects such as short shots, air trap, and sink marks, as the plastic is injected into the mold through top of part, which promotes even flow and filling.
- Increased Versatility: Pin point gate solution can be used with a wide range of materials, making them suitable for a variety of applications, but for some very soft material may not good option, for example TPE share 30A is not good option use pin pot gate, because the gate will not possible to divide from the part.
Disadvantages of Pin Gates:
- Increased Complexity: Pin gate feeding solution designs are more complex than other gate types, and require careful consideration of factors such as gate location, gate size etc.
- Increased Cost: Pin gate feeding solution typically require more complex mold tooling and a higher level of process control, which can increase the overall cost of the molding process, pin point gate normally need 3 plate injection mold.
- Limited Applications: Pin gate feeding solution may not be suitable for large or heavy parts, because the feeding distance is longer than the other gate and may not able to full fill the part completely in the shot time. so that will cause some cold well issue in the molding part.
Pin-point gate injection molding can solve some multiple cavity molds with cold runner mold very easy by using the 3 plate injection mold, sometime you do not need to use hot runner and make multiple parts in one single mold to save the mold cost, there are many type of gates in injection molding, please go to injection mold design of gate page to know more detail.
If you want to save cost for you mold and do not know which type of mold that your parts should have? welcome to contact us. We are one of top 10 mold manufacturers in China.