Plastic toys making entails the creation of toys from different forms of plastic material employing sophisticated molding methods. This industry has expanded greatly because plastic is multi-functional, long-lasting, and relatively affordable. Numerous industries use techniques, i.e. injection molding to ensure that toys produced are safe for children and attractive to them. A shift towards sustainability is being observed in the industry and sustainable materials and processes are also being tried out.
Besides this, an increase in awareness of consumer how these toys are made goes a long way in enabling them. So, they can make the right decision and encourage producers to adopt good practices. So, let’s explore the different ways of how.
What is Plastic Toy Manufacturing?
Plastic toys manufactuing is developing toys from plastic raw materials including the toy design and making models for final product production. It comprises different processes to fabricate, form, and polish plastic toys with safety and code requirements for this industry. There are a series of steps involved in the manufacturing process such as; raw material acquisition, designing of molds, and plastic molding toys molding process such as injection molding or blow molding. Here, particular interests ensure that toys created are safe and of high quality to meet consumer requests. The trend of using plastic as a toy material also transforms due to continuous improvement of design.
Common Methods of Creation of Plastic Toys
Here are some of the commonly used techniques for making Plastic Toys;
- Injection Molding: This method was explained above, and the quires usage of molds to inject molten plastic, yielding toys of high accuracy and fine details.
- Blow Molding: It helps produce hollow toy plastics, i.e. balls and bottles. It involves blowing a heated plastic tube (paring) into a mold, to the required shape.
- Rotational Molding: Here one pours the plastic intruder into a mold and the mixture is then rotated and heated. Due to heat melts the plastic that bakes the inside of the mold, and the large hallow structures such as ride-on toys.
- Thermoforming: This process occurs by melting a plastic sheet and placing the molded plastic in a vacuum that forms the sheet to the shape of the mold. It is frequently used to create flat toys or parts of toys that don’t require detailed cutting of the material.
- 3D Printing: A new approach, 3D printing is a technique of building toys through the accumulation of the required number of thin layers of various plastics. This technique produces fairly complex designs and it is very fast while making a prototype.
What is Injection Molding for Toys?
Injection molding is an industry where toys are produced by forcing hot melts into a mold that has been prepared in advance. This method can aa achieve a high degree of accuracy hence recommended in the development of shapes and designs. It entails the ming of plastic pellets and then forcing the liquid material through a mold using a pressure fan. When the toys have solidified mold mold is removed and the toy which is now complete is expelled.
The toy industry especially enjoys this technique due to its efficiency, productivity, rate, and usefulness in mass production at an affordable price.
How to Make Plastic Toys Using Injection Molding
So, let’s have an overview of how to make plastic toys using the injection molding method;
Step 1: Design the Toy
- Conceptualization: Start with an idea, and draw the idea and structure of the toy. One should examine the age of the consumer target, security measures, and capabilities and utility.
- 3D Modeling: Draw the geometry using CAD to develop the 3D model of the toy model types. Then further use this mold design and the overall appearance of the final product.
Step 2: Create the Mold
- Mold Design: Afterwards, use the 3D model created and design the injection mold. This consists of the cavity that contains the molten plastic and the core for the inner shape of the product.
- Material Selection: Selecting the proper material for the mold out of steel or aluminum, depends on the degree of production and its difficulty.
- Mold Fabrication: Subsequently, create the mold using CNC machining or any other processes to enhance intensity. The mold can also be more polished to acquire a smooth surface.
Step 3: Select the Plastic Material
- Material Choice: Take time to choose your plastic resin. So, your polypropylene, your polyethylene,ne, or an ABS. It will depend on your required flexibility, durability, or safety.
- Color and Additives: Decide whether coloring agents or other materials are required for clarity or resistance to ultraviolet light.
Step 4: Prepare the Injection Molding Machine
Place the mol into the injection molding machine. Make sure that it is firmly clamped. With the chosen plastic pellets, feed them on a hopper that is in the machine.
Step 5: Injection Molding Process
- Melting the Plastic: Melt the plastic pellet by heating the machine to the required temperature. Molten plastic injection at high pressure into the mold cavity. This pressure compels the plastic to make the mold’s shape while maintaining all the details within the mold.
- Cooling: Let the plastic melt cool and solidify inside the mold. Cooling time depends on the material and the size of the toys.
Step 6: Ejecting the Toy
- Opening the Mold: When the melt has cooled, the injection molding machine releases the mold.
- Ejection: The ejector pins help push out the finished toy from the mold.
Step 7: Post-Processing
- Trimming: Clean the toy with a brush to avoid any extruded plastic (flash), around the mold lines, if any.
- Assembly (if needed): Assembling is only required in cases and specific toys with parts that need to be connected in a certain way In case the toy has more parts then they should be arranged in the way as is appropriate.
- Surface Finishing: Paint the toy if you would like to change the color, or add decals or texturing for a professional look.
Materials and Design Considerations for Plastic Toy Molds
Let’s explore different materials and design considerations that will make the manufacturing of plastic molding toys more effective.
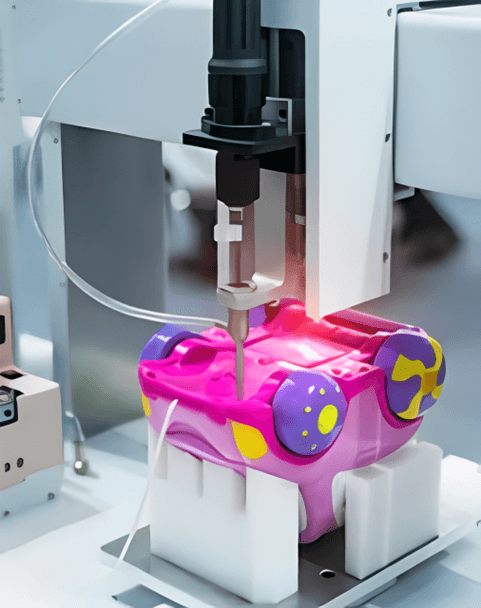
plastic injection molding toys
Category | Consideration | Details |
Mold Material | Steel | Durable, high-volume; long-lasting, higher cost. |
Aluminum | Lightweight, medium-volume; easier to machine, lower cost. | |
Beryllium Copper | High heat dissipation; used for thin walls. | |
Plastic Material | PP, PE, ABS | PP: Flexible, impact-resistant. PE: Lightweight, weatherproof. ABS: Strong, detailed. |
Mold Design | Cavity Count | Multiple cavities boost production speed; ideal for high-volume. |
Parting Line & Gate Location | Critical for smooth release and quality; gates placed on non-visible parts. | |
Wall Thickness | Uniform Thickness | Prevents warping; standard: 1.5-3.0 mm. |
Draft Angle | Aids release; 1-3° for smooth, up to 5° for textures. | |
Cooling System | Conformal Cooling Channels | It enhances cooling efficiency and prevents deformation. |
Surface Finish | Texturing | Adds grip, hides imperfections; enhances aesthetics. |
Safety Considerations | Non-Toxic, Rounded Edges | Essential for safety standards (e.g., ASTM F963); reduces injury risk. |
Cost Considerations | Material & Maintenance | Steel is high-cost but durable; aluminum is cheaper but wears faster. Maintenance needed. |
Common Types of Plastics Used in Toys
The following are certain types of Plastics we can use to make molded toys;
- Polypropylene (PP): Another component that is used in most toys due to its versatility and toughness is polypropylene which is used for toys that need to have the ability to bounce back after having been knocked about. go to polypropylene injection molding page to know more.
- Polyethylene (PE): This lightweight plastic is often applied to products for outdoor use such as toys and equipment because of its weatherproof and nonslippery characteristics. Go to polyethylene injection molding page to know more.
- Polyvinyl Chloride (PVC): PVC is highly used in toys that need the features of rigidity and strength though their usage is declining due to health effects. Got to fitting mold page to know more.
- Acrylonitrile Butadiene Styrene (ABS): ABS is considered ideal for its strength and durability, it can also take abuse hence correct for action figures and building blocks. Got to ABS injection molding page to know more.
- Thermoplastic Elastomers (TPE): It is a rubber plastic material, which is very useful for soft toys that need to possess a good feel and elasticity. Got to TPE injection molding page to know more.
Surface Printing On Plastic Toys
Surface printing enhances toy aesthetics and adds features, using methods like:
- Pad Printing: Makes good contact with curved or textured surfaces; best used for fine and intricate designs.
- Screen Printing: I use this mechanism to spread ink through a screen for smooth surfaces; best used for large and thick single colors.
- Heat Transfer Printing: Transfer images via heat and that can be used for intricate and color graphics.
- Digital Printing: Produces a high-resolution image, suitable for artwork or small-scale logos.
Things to Consider When Designing Toy Injection Molds
Let’s follow the below tips when designing the Plastic Toy for Injection Molding;
- Material Selection: High-volume molds should be made of steel while those for a low volume should be made of aluminum to help cut down on the overall cost although the molds will be blasting.
- Precision and Tolerance: Control should be set to very narrow in order to achieve desired details as much as necessary for toys with complex connections interlocking.
- Cooling System Design: The other possible areas to improve the design are associated with cooling channels aimed at shortening the cycle time and avoiding warping or deformation of the part.
- Ejection Mechanism: Correct positioning of ejector pins and lock release draft angles between 1-3° helps in reducing defects.
- Safety Compliance: Design molds should also reflect child safety features such as rounded edges and molding free of toxic metals.
Benefits of Plastic Injection Molded Plastic Toys
Here are some benefits of injection molded plastic toys
- High Production Efficiency: Conveyance of mass production at a faster pace has minimized production time.
- Precision and Tolerance: Cost-effectively advantageous for extensive production.
- Precision and Detail: These methods facilitate designing and creating complex geometries with par exceed license precision.
- Precision and Tolerance: It is stronger and more durable than the outer part of the body and vehicle’s body.
- Customizability: Stain color is simple to change/ISE outlook.
Drawbacks of Injection Molded Toys
The following are some limitations of injection molded plastic toys;
- High Initial Setup Costs: High cost of mold development.
- Environmental Concerns: Contamination of water and accumulation of plastics.
- Limited Material Choices: Policies limit choices regarding matters of safety.
- Production Waste: There is a potential for the generation of more plastics.
- Lack of Flexibility: Downsides: Takes time to design and takes very many resources; also changes in designs cost a lot after a mold has been made.
Applications of Plastic Injection Molded Toys
Here are some of the popular applications of injection molded plastic toys;
- Educational Toys: Support Education/ Learning and Brain/ Mental Growth/Development.
- Collectibles and Figurines: Well-defined and accurate collectible objects.
- Outdoor Play Equipment: Durable toys for outdoor use.
- Action Figures and Dolls: Popular lines with tight technical specifications.
- Board Game Components: Generally, the game pieces and tokens of a number of common games should be equal or, at least, similar in size and material.
Environmental and Recycling Options and Sustainable Practices for Toy Manufacturing
Sustainable practices in toy manufacturing include:
- Switch into eco-friendly products, for example, exchanging normal plastics with the ones that are recycled or biodegradable.
- Scrap plastic recycling and such efficient methods.
- Catalyzing recycling at the time when the product is no longer functional.
- Sustainable packaging materials in the packaging and processing industry.
- Lower carbon dioxide emissions through efficient machines.
Conclusion
In conclusion, this article will also reveal that plastic injection molded toys have numerous benefits such as cost, durability, and design advantages that make them common in toy manufacturing industries. , However, the following chaos remains; high initial cost and environmental issues have to be given due consideration to ensure environmentally sound production is practiced. BY rejecting alternative approaches to manufacturing, producers can lower their ecological footprint and continue to create new and exciting products for children to play with.
FAQ
Q1: What are the advantages of toys produced using the Injection molding process?
A1: Energy efficiency, low cost long-term term usability, accuracy, and personalization.
Q2: What are the most typical use of such toys?
A2: Learning aids, memorabilia, recreational and sporting accessories, models and plastic toys, and games including accessories and parts.
Q3: What might be the average cost of making a plastic toy?
A3: Regardless, costs range mostly from a few cents to a few dollars per unit.
Q4: Which practices can be put in place in relation to the environment?
A4: Select materials for reuse, minimize wastes, involve product design for easy disassembly, use environmentally friendly packing, and produce energy-efficient products.
Q5: Are all the injection molding processes disadvantageous?
A5: Yes, high initial costs, emission of bad odor and pollution, restriction in the availability of materials, wastes generated when producing the raw material, and rigidness in designing