Vad är formsprutning?
Formsprutning är ett verktyg som används i formsprutningsprocessen för att producera delar genom att injicera material i en formhålighet. Det är vanligtvis tillverkat av stål (H13, P20, 1.2312, 1.2344, S136H, etc.) eller aluminium och är noggrant utformat för att matcha slutproduktens form och specifikationer.
Formsprutan är uppdelad i två halvor som är kavitetshalva och kärnhalva, de kläms ihop under gjutningsprocessen, med materialet som injiceras genom en gran i formkaviteten där det svalnar och stelnar till önskad form. När detaljen är formad öppnas formen och detaljen matas ut. Formen kan återanvändas för att producera flera delar.

Vad är formsprutning
Olika typer av formsprutningsverktyg
Bland de många sorterna av formsprutningsformar kan du hitta:
Kavitetsspecifik form
Varje cykel i formsprutningsprocessen kan bara generera en del när man använder en form med en kavitet. Processen för att tillverka en del med denna form är så enkel som att injicera plastharts i den, vänta på att den ska svalna och sedan ta bort den färdiga produkten.
När man jämför produktionskostnaderna för formar med flera skott med formar med en kavitet är den förra vanligtvis billigare. När det skulle bli för dyrt att tillverka ett litet antal komponenter på en gång, är det dessa som gäller vid prototyptillverkning och tillverkning av små volymer.

Form med enkel kavitet
Fördelarna med enkelskottsformar inkluderar:
- Effektivt när det gäller kostnad: produktionen av en form med en skott är ofta billigare än produktionen av en form med flera skott.
- Enkel design: Enkel produktion och enkelt underhåll tack vare enkel design: Formar för enstaka skott är ofta mindre komplexa i sin layout än formar för flera skott.
- Flexibilitet: Ett stort antal olika applikationer, t.ex. prototyper och lågvolymsproduktion, är lämpliga för användning av formar med en kavitet.
Nackdelarna med enstaka skottformar inkluderar:
- Begränsad produktion: Denna begränsning gör enkelkavitetsformar olämpliga för gjutning av stora volymer eftersom de endast kan producera en enda detalj under varje cykel.
- Komplexa delar: Enkavitetsformar är inte bra för att göra komplicerade delar med många delar; för dessa behöver du en form med flera håligheter eller en familjeform.
- Ineffektivitet: I jämförelse med flerkavitetsformar är enkelformar mindre effektiva eftersom de på grund av sin begränsade kapacitet bara kan skapa en enda detalj under varje cykel.
Gjutformar med flera håligheter:
Multikavitetsformar är en typ av formsprutningsform som har mer än ett hålrum. Detta gör att formsprutningsprocessen kan göra mer än en del under varje sväng. Beroende på applikationens behov kan dessa formar tillverkas med hål som är desamma eller olika.
Som ett resultat av dess förmåga att skapa många delar i en cykel används multikavitetsformar vanligtvis för formsprutning av stora volymer produktionskörningar. Denna funktion gör det möjligt för dem att öka produktionseffektiviteten och samtidigt sänka kostnaden per detalj.

form med flera kaviteter
Fördelarna med flerkavitetsformar inkluderar:
- Produktion av stora volymer: Multikavitetsformar är gjorda för storskaliga produktionskörningar, vilket gör det enkelt att tillverka många delar.
- Kostnadseffektivt: flerkavitetsformar är vanligtvis billigare än enkelkavitetsformar eftersom de kan göra fler delar i en enda körning.
- Komplexa delar: Multikavitetsformar kan användas för att tillverka delar som är komplicerade och har många delar.
Nackdelarna med formar med flera kaviteter inkluderar:
- Komplex design: Flerkavitetsformar är svårare att tillverka och underhålla än enkelkavitetsformar eftersom deras design är mer komplicerad.
- ökade formkostnaden: Formar med flera kaviteter kan vara dyrare än formar med en kavitet eftersom olika kaviteter kan utsättas för olika mycket stress och slitage under formsprutningsprocessen. Detta kan leda till mindre effektiv produktion och högre kostnader för reparationer.
Varmkanalsform:
Varmkanalsform är en typ av formsprutningsform som använder ett varmkanalsystem för att leverera det smälta plastmaterialet in i formhålorna. Varmkanalsystemet består av ett uppvärmt grenrör som fördelar den smälta plasten till enskilda munstycksspetsar, som sedan riktas in i formhålorna.

Varmkanalsform
Fördelarna med varmkanalsformar är bland annat
- Förbättrad detaljkvalitet: Varmkanalsformar kan producera detaljer med förbättrad kvalitet, eftersom de minimerar mängden plast som blir över i kanalerna och minskar risken för defekter som t.ex. flash, korta skott och sinkmärken.
- Ökad produktionseffektivitet: Varmkanalsformar kan öka produktionseffektiviteten eftersom de eliminerar behovet av manuella ingrepp för att avlägsna kanalerna från de gjutna delarna, vilket minskar cykeltiden och förbättrar den totala produktionshastigheten.
- Energieffektivitet: Varmkanalsformar är mer energieffektiva jämfört med traditionella kallkanalsformar, eftersom de minimerar mängden plast som går till spillo i kanalerna.
Nackdelarna med varmkanalsformar inkluderar:
- Komplex design: Varmkanalsformar har en mer komplex design jämfört med traditionella kallkanalsformar, vilket gör dem dyrare att tillverka och underhålla.
- Ökat underhåll: Varmkanalsformar kräver normalt mer underhåll jämfört med kallkanalsformar, eftersom de har ett mer komplext värmesystem som måste hållas i gott skick.
- Sårbarhet för igensättning: Varmkanalsformar kan vara känsliga för igensättning, särskilt vid bearbetning av material med hög viskositet eller långa flödeslängder, eftersom detta kan leda till att den smälta plasten stelnar i kanalerna. Detta kan leda till minskad produktionseffektivitet och ökade underhållskostnader.
Stapla formar:
Stackform är en typ av formsprutningsverktyg som gör det möjligt att gjuta flera kaviteter samtidigt i en enda maskincykel. Stapelformar är i huvudsak två eller flera formar som är staplade ovanpå varandra, där varje form producerar en enda del.

Stackform
Fördelarna med stapelformar inkluderar:
- Ökad produktionseffektivitet: Stackformar gör det möjligt att gjuta flera detaljer samtidigt, vilket ökar produktionseffektiviteten och minskar cykeltiden.
- Minskat materialspill: Stapelformar minimerar materialavfallet eftersom de gör det möjligt att tillverka flera delar med en enda sats plastmaterial.
- Lägre kostnader: Stackformar kan vara mer kostnadseffektiva jämfört med enkelkavitetsformar, eftersom de möjliggör produktion av flera delar med en enda maskincykel.
Nackdelarna med stapelformar inkluderar:
- Komplex design: Stackformar kan ha en mer komplex design jämfört med enkelkavitetsformar, vilket gör dem dyrare att tillverka och underhålla.
- Försämrad kvalitet på detaljerna: Stapelformar kan producera detaljer med sämre kvalitet, eftersom förekomsten av flera håligheter kan leda till ökad risk för defekter som flash, korta skott och sinkmärken.
- Ökat underhåll: Stackformar kräver vanligtvis mer underhåll jämfört med enkelkavitetsformar, eftersom de har en mer komplex konstruktion som måste hållas i gott skick.
Familjeformar:
Familjeformar, även kända som multiimpressionsformar som liknar multipelkavitetsformar, är en typ av formsprutning som gör det möjligt att gjuta flera delar med något olika design samtidigt i en enda maskincykel. Detta uppnås genom att ha flera håligheter i formen som kan producera olika delar med olika former och storlekar.
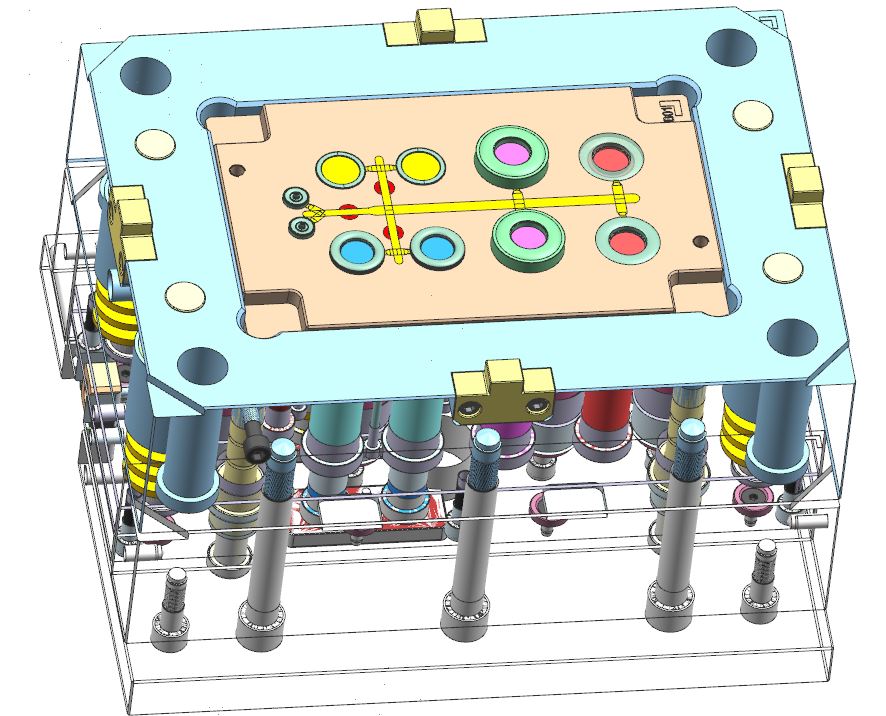
familjens mögel
Fördelarna med familjeformar inkluderar:
- Ökad produktionseffektivitet: Familjeformar gör det möjligt att gjuta flera delar med olika design samtidigt, vilket ökar produktionseffektiviteten och minskar cykeltiden.
- Lägre kostnader: Familjeformar kan vara mer kostnadseffektiva jämfört med att tillverka flera formar med en kavitet för varje detalj, eftersom de gör det möjligt att tillverka flera detaljer med en enda maskincykel.
- Flexibilitet: Familjeformar möjliggör tillverkning av olika delar med varierande design, vilket gör dem till ett mångsidigt alternativ för tillverkare som behöver tillverka en rad olika produkter.
Nackdelarna med familjemögel inkluderar:
- Komplex design: Familjeformar kan ha en mer komplex design jämfört med formar med en enda kavitet, vilket gör dem dyrare att tillverka och underhålla.
- Försämrad kvalitet på detaljerna: Familjeformar kan producera detaljer med lägre kvalitet, eftersom förekomsten av flera håligheter kan leda till ökad risk för defekter som flash, korta skott och sinkmärken.
Tvåskottsformar:
Tvåskottsform (Formsprutning med 2 skott), även känd som övergjutning eller flerskottsformar eller 2K-form, är en typ av formsprutning som gör det möjligt att gjuta ihop två olika material i en enda maskincykel. Processen innebär att ett första material (basmaterial) formas i en form och att ett andra material (överformningsmaterial) sedan formas på det första materialet.

Två skottform
Fördelarna med tvåskottsformar inkluderar:
- Ökad funktionalitet: Tvåskottsformar gör det möjligt att kombinera två olika material med olika egenskaper för att skapa delar med ökad funktionalitet.
- Förbättrad estetik: Tvåskottsformar gör det möjligt att integrera olika färger eller texturer i en enda del, vilket skapar en mer visuellt tilltalande produkt.
- Kortare monteringstid: Genom att kombinera två material till en enda del kan tvåstegsformar minska behovet av ytterligare monteringssteg, vilket minskar produktionstiden och kostnaderna.
Nackdelarna med tvåskottformar inkluderar:
- Komplex design: Tvåskottsformar är mer komplexa i sin utformning jämfört med enskottsformar, vilket gör dem dyrare att producera och underhålla.
- Ökad cykeltid: Tvåskottsformar har vanligtvis en längre cykeltid jämfört med enkelskottsformar, eftersom processen innebär att två material formas i en enda maskincykel.
- Kompatibilitetsproblem: Tvåskottsformar kräver att de två materialen som gjuts är kompatibla med varandra och kommer att fästa ordentligt, vilket gör det viktigt att noggrant välja de material som används.
Skruva loss formar:
Skruvformar är en typ av formsprutning som är särskilt utformad för att producera delar med skruvgängor, t.ex. lock, lock och behållare. Dessa formar är unika genom att de har en mekanism som gör att formens kärna kan rotera medan hålrummet förblir stillastående, vilket gör att den gjutna delen kan skruvas loss från formen efter att den har svalnat och stelnat.

skruva loss formen
Fördelarna med att skruva loss formar inkluderar:
- Hög effektivitet: Skruvformar möjliggör effektiv produktion av gängade detaljer i en enda maskincykel, vilket minskar produktionstiden och kostnaderna.
- Förbättrad noggrannhet: Skruvformar möjliggör exakt tillverkning av gängade detaljer med konsekvent stigning och gängdjup, vilket förbättrar slutproduktens kvalitet och prestanda.
- Mångsidighet: Skruvformar kan användas för att tillverka en mängd olika detaljer med olika gängtyper och storlekar, vilket gör dem till ett mångsidigt alternativ för många olika applikationer.
Nackdelar med att skruva loss formar inkluderar:
- Komplex design: Skruvformar är mer komplexa i sin utformning jämfört med andra typer av formar, vilket gör dem dyrare att producera och underhålla.
- Ökad cykeltid: Skruvformar har vanligtvis en längre cykeltid jämfört med andra typer av formar, eftersom processen innebär att formens kärna roteras.
- Slitage och förslitning: Den roterande mekanismen i skruvformar kan vara benägen att slitas med tiden, vilket kräver regelbundet underhåll för att formen ska fungera korrekt.
Form med hopfällbar kärna:
Formverktyg med hopfällbar kärna är en typ av formsprutning som används för att tillverka ihåliga delar med inre hålrum, t.ex. rör och andra komplexa delar. Dessa formar använder en unik design som gör att formens kärna kan kollapsa in i sig själv och skapa det inre hålrummet i delen.

Formkomponent med hopfällbar kärna
Fördelarna med formar med hopfällbar kärna inkluderar:
- Förbättrad effektivitet: Gjutformar med hopfällbar kärna möjliggör tillverkning av ihåliga detaljer i en enda maskincykel, vilket minskar produktionstiden och kostnaderna.
- Förbättrad kvalitet på detaljen: Gjutformar med hopfällbar kärna ger en mer exakt och konsekvent inre kavitet, vilket förbättrar den övergripande kvaliteten på den slutliga detaljen.
- Mångsidighet: Gjutformar med hopfällbar kärna kan användas för att producera en mängd olika detaljer med olika former och storlekar, vilket gör dem till ett mångsidigt alternativ för många olika applikationer.
Nackdelar med formar med hopfällbar kärna inkluderar:
- Komplex design: Gjutformar med hopfällbar kärna är mer komplexa i sin konstruktion jämfört med andra typer av gjutformar, vilket gör dem dyrare att tillverka och underhålla.
- Ökad cykeltid: Gjutformar med hopfällbar kärna har vanligtvis en längre cykeltid jämfört med andra typer av gjutformar, eftersom processen innebär att gjutformens kärna kollapsar.
- Slitage och förslitning: Kärnans hopfällbara mekanism kan bli utsatt för slitage med tiden, vilket kräver regelbundet underhåll för att formen ska fungera korrekt.
Fördelar och nackdelar med formsprutning av plast
Fördelar med Formsprutning:
- Produktion av stora volymer: Formsprutning är en mycket effektiv metod för att producera stora volymer av identiska delar. Detta gör den idealisk för massproduktion av konsumentvaror, bildelar och andra produkter som kräver stora mängder liknande delar.
- Precision: Processen möjliggör en mycket exakt kontroll av måttnoggrannhet och detaljkonsistens. Detta beror på användningen av noggrant kontrollerade bearbetningsförhållanden och på gjutmaskinens och formens styvhet.
- Snabbhet: Formsprutning är en snabb process med cykeltider på så lite som några sekunder för små detaljer. Detta gör att tillverkarna kan producera stora mängder detaljer på relativt kort tid.
- Kostnadseffektivt: Kostnaden för att tillverka detaljer genom formsprutning blir mer ekonomisk när produktionsvolymen ökar. Detta beror på att formen kan användas för att producera många delar under sin livslängd, och kostnaden per del minskar när volymen ökar.
- Mångsidighet: Formsprutning kan användas för att tillverka delar av en mängd olika material, bland annat plast, metall och elastomerer. Denna mångsidighet gör det till ett populärt val för tillverkare som behöver producera delar från olika material beroende på produktens specifika krav.
- Automatisering: Formsprutningsmaskiner kan automatiseras, vilket gör processen mer effektiv och minskar behovet av manuellt arbete. Detta kan också förbättra delens konsistens och kvalitet.
- Komplexa former: Formsprutning kan användas för att producera komplexa former och mönster, inklusive delar med invecklade detaljer och snäva toleranser. Detta är möjligt tack vare den exakta kontrollen av gjutningsprocessen och möjligheten att utforma mycket detaljerade formar.
- Val av material: Formsprutning gör det möjligt för tillverkare att välja mellan ett brett utbud av material, vart och ett med sina egna unika egenskaper, såsom styrka, flexibilitet och motståndskraft mot värme, kemikalier och slitage. Detta gör det möjligt att välja det bästa materialet för varje applikation och producera delar med önskade egenskaper.
Nackdelar med formsprutning:
- Hög initialkostnad: Den initiala kostnaden för att skapa formen kan vara hög, särskilt för komplexa former och mönster. Detta kan göra processen mindre kostnadseffektiv för små kvantiteter av delar eller för prototyper.
- Begränsad flexibilitet i designen: När formen väl är tillverkad kan det vara svårt och dyrt att ändra designen. Detta kan begränsa möjligheten att göra designändringar eller förbättringar när formen väl har skapats.
- Materialavfall: Formsprutning genererar en betydande mängd materialskrot, som kan vara kostsamt att ta hand om och skadligt för miljön. Detta kan också öka produktionskostnaden och minska processens totala effektivitet.
- Ledtid: Ledtiden för att skapa formen och sätta upp formsprutningsprocessen kan vara lång, särskilt för komplexa delar. Detta kan sakta ner produktutvecklingsprocessen och begränsa möjligheten att snabbt få ut produkter på marknaden.
- Begränsningar i ytfinish: Formsprutning kanske inte ger en högkvalitativ ytfinish på vissa delar, särskilt de med invecklade detaljer eller snäva toleranser. Detta kan begränsa möjligheten att producera delar med ett högkvalitativt estetiskt utseende.
- Materialkompatibilitet: Kompatibiliteten mellan material och form kan vara en utmaning, eftersom vissa material kanske inte fungerar bra med vissa typer av formar eller kräver speciella bearbetningsförhållanden. Detta kan begränsa möjligheten att tillverka delar av vissa material och öka produktionskostnaden.
- Begränsad storlek på detaljen: Formsprutning begränsas av formens storlek och gjutmaskinens klämkraft. Detta kan begränsa storleken på de delar som kan tillverkas och öka kostnaden för att tillverka större delar.
- Sekundära operationer: Vissa delar kan kräva sekundära operationer, till exempel trimning eller efterbehandling, efter att de har gjutits. Detta kan öka produktionskostnaden och begränsa processens totala effektivitet, naturligtvis kan dessa problem ibland lösas genom att förbättra formsprutan
Vanliga problem med en formsprutningsform
När du väl arbetar inom formsprutning av plast kommer det alltid att finnas några problem som du behöver lösa varje dag, här är några vanliga utmaningar som formsprutning står inför:
Problem med skevhet:
Vridning är ett vanligt problem vid formsprutning och avser en deformation eller förvrängning av den gjutna delen som uppstår efter att den har tagits bort från formen. Detta kan hända på grund av en mängd olika faktorer, inklusive:

Warp-förvrängning
- Felaktig kylning: Om detaljen kyls för snabbt eller ojämnt kan det leda till skevhet eftersom materialet krymper och drar ihop sig olika snabbt.
- Restspänning: Formsprutning skapar restspänning i detaljen på grund av det höga tryck som används under gjutningsprocessen. Denna spänning kan orsaka skevhet om den inte avlastas på rätt sätt.
- Val av material: Vissa material är mer benägna att bli skeva än andra. Material med låg värmebeständighet eller låg dimensionsstabilitet är t.ex. mer benägna att bli skeva.
- Formens utformning: Formens utformning kan också bidra till skevhet, särskilt om formen inte medger korrekt kylning eller materialflöde.
- Bearbetningsförhållanden: Inkonsekventa bearbetningsförhållanden, t.ex. varierande insprutningshastigheter, formtemperaturer och trycknivåer, kan orsaka skevhet.
För att förhindra skevhet är det viktigt att välja lämpligt material, optimera formkonstruktionen och bearbetningsförhållandena samt tillämpa korrekta kylnings- och materialhanteringsmetoder. Dessutom kan det vara nödvändigt att använda behandlingar efter gjutning, t.ex. glödgning, för att minska restspänningen och förbättra dimensionsstabiliteten.
Problem med blixten:
Flashdefekter är en term som används vid formsprutning för att hänvisa till det överflödiga material som tvingas ut ur formen under gjutningsprocessen. Flash uppstår när materialet flyter bortom den avsedda formkaviteten och in i avskiljningslinjen, eller utrymmet mellan formens två halvor.

Gjutning Flash eller grader
Flash kan orsakas av flera faktorer, bland annat:
- Felaktig utformning av gjutformen: En dåligt utformad form kan orsaka flash genom att låta material läcka in i skiljeväggen.
- Inkonsekventa bearbetningsförhållanden: Varierande bearbetningsförhållanden, t.ex. injektionshastighet och tryck, kan orsaka flash.
- Materialkompatibilitet: Vissa material kanske inte är kompatibla med formen och kan orsaka flammor när de flödar in i avstickaren.
- Slitage på gjutformen: Med tiden kan gjutformen slitas och orsaka flash när materialet läcker in i skiljeväggen.
Flash kan ha flera negativa effekter, bland annat minskad måttnoggrannhet hos detaljen, ökad kassationsgrad och försvårad efterbearbetning. För att minimera flash är det viktigt att optimera formkonstruktionen, bearbetningsförhållandena och materialvalet samt att regelbundet underhålla och reparera formen vid behov.
Svetslinjer:
Svetslinjer är ett vanligt problem vid formsprutning och avser synliga märken på ytan av den gjutna delen där två strömmar av smält plastmaterial möts och stelnar. Svetslinjer uppstår när materialet inte helt smälter samman när det flyter in i plastform hålrum, vilket lämnar en synlig linje på ytan av delen.

Svetslinje
Svetsränder kan orsakas av flera faktorer, bland annat:
- Otillräckligt smältflöde: Om materialet inte får tillräckligt med tid för att flöda och smälta samman helt kan det bildas en svetslinje.
- Felaktig utformning av grinden: En dåligt utformad grind, som är den punkt där det smälta materialet kommer in i formhålan, kan orsaka en svetslinje.
- Inkonsekventa bearbetningsförhållanden: Varierande bearbetningsförhållanden, t.ex. insprutningshastighet och tryck, kan orsaka en svetslinje.
- Materialets kompatibilitet: Vissa material kanske inte är kompatibla med formen och kan orsaka en svetslinje när de flyter in i formhålan.
Svetslinjer kan försvaga detaljens hållfasthet och försämra dess övergripande kvalitet. För att minimera antalet svetslinjer är det viktigt att optimera formkonstruktionen, bearbetningsförhållandena och materialvalet samt att tillämpa korrekta materialhanteringsrutiner. Dessutom kan det vara nödvändigt att använda speciella bearbetningstekniker, t.ex. flerkavitetsformar eller varmkanalsystem, för att minska bildandet av svetslinjer.
Sänkmärken:
Sänkmärken, även kända som "sink", "vacuum sink" eller "skin", är nedsänkta eller nedtryckta områden på ytan av en formsprutad plastdel. De orsakas vanligtvis av ett antal faktorer, bland annat:
- Krympning av harts: När hartset svalnar och stelnar kan det krympa ojämnt, vilket leder till sjunkmärken.
- Dåligt materialflöde: Om hartset inte flyter jämnt in i alla delar av formen kan det skapa hålrum eller nedsänkta områden.
- Otillräckligt packningstryck: Om injektionstrycket inte är tillräckligt högt kan det hända att hartset inte fyller formen helt, vilket leder till sjunkmärken.
- Problem med formkonstruktionen: Formens utformning, inklusive placering och storlek på grindar, kanalsystem och avluftning, kan alla påverka kvaliteten på den gjutna delen och kan bidra till sinkmärken.
Sänkmärken kan påverka den estetiska kvaliteten och funktionaliteten hos en gjuten detalj och kan vara en källa till frustration för tillverkare och slutanvändare. För att minimera sänkmärken är det viktigt att noggrant överväga de faktorer som bidrar till dem, t.ex. materialval, formkonstruktion, bearbetningsparametrar och detaljdesign, och göra justeringar efter behov för att optimera formsprutningsprocessen.
Flödesmarkeringar:
Flödesmärken är ett vanligt problem vid formsprutning och avser synliga märken eller ränder på ytan av den gjutna delen som orsakas av flödet av det smälta plastmaterialet när det fyller formhålan. Flödesmärken uppstår när materialet flödar ojämnt och lämnar efter sig ett synligt märke på ytan av detaljen.
Flödesmärken kan orsakas av flera faktorer, bland annat:
- Otillräckligt smältflöde: Om materialet inte får tillräckligt med tid för att flöda och fylla formhålan kan det bildas flödesmärken.
- Felaktig utformning av grinden: En dåligt utformad grind, som är den punkt där det smälta materialet kommer in i formhålan, kan orsaka flödesmärken.
- Inkonsekventa bearbetningsförhållanden: Varierande bearbetningsförhållanden, t.ex. injektionshastighet och tryck, kan orsaka flödesmärken.
- Materialets kompatibilitet: Vissa material kanske inte är kompatibla med formen och kan orsaka flödesmärken när de flyter in i formhålan.
Flödesmärken kan försämra detaljens övergripande kvalitet och kosmetiska utseende. För att minimera flödesmärken är det viktigt att optimera formkonstruktionen, bearbetningsförhållandena och materialvalet samt att tillämpa korrekta materialhanteringsrutiner. Dessutom kan det vara nödvändigt att använda speciella bearbetningstekniker, t.ex. flerkavitetsformar eller varmkanalsystem, för att minska uppkomsten av flödesmärken.
Problem med repor:
Med repor avses synliga märken eller repor på ytan av en formsprutad detalj som orsakas av fysisk kontakt mellan detaljen och formen eller andra främmande föremål under gjutningsprocessen. Repor kan uppstå av flera skäl, bland annat:
- Dålig formkonstruktion: Felaktigt utformade formar eller formkomponenter kan orsaka repor på detaljens yta.
- Otillräcklig smörjning: Om formen och formkomponenterna inte är ordentligt smorda kan de orsaka repor på detaljens yta.
- Dålig materialhantering: Dålig hantering av råmaterial eller färdiga detaljer kan orsaka repor på detaljens yta.
- Skräp i gjutformen: Främmande föremål eller skräp i formhålan kan orsaka repor på detaljens yta.
Repor kan försämra detaljens övergripande kvalitet och kosmetiska utseende. För att minimera repor är det viktigt att använda rätt metoder för formkonstruktion, smörjning, materialhantering och underhåll. Dessutom kan regelbunden rengöring och inspektion av formen och formkomponenterna bidra till att förhindra att repor uppstår.
Utskjutningsmärken:
Utskjutningsmärken är synliga märken på ytan av en formsprutad detalj som orsakas av utskjutningsstiften eller andra utskjutningsmekanismer under gjutningsprocessen. Utstötningsmärken uppstår när utstötningsstiften trycker ut den gjutna detaljen ur formhålan och lämnar synliga märken på detaljens yta.
Utskjutningsmärken kan orsakas av flera faktorer, bland annat:
- Felaktig utformning av utmatningsstiften: Om utmatningsstiften inte är korrekt utformade kan de lämna synliga märken på detaljens yta.
- Överdriven kraft: Om utskjutningsstiften utövar för stor kraft på detaljen under utskjutningen kan de lämna djupare och mer märkbara märken på detaljens yta.
- Inkonsekvent utskjutningskraft: Om utmatningskraften inte är konsekvent från ett utmatningsstift till ett annat kan det resultera i ojämna utmatningsmärken på detaljens yta.
- Dålig ytfinish: Om formkavitetens ytfinish inte är jämn kan det orsaka utskjutningsmärken på detaljens yta.
Utskjutningsmärken kan försämra detaljens övergripande kvalitet och kosmetiska utseende. För att minimera utstötningsmärken är det viktigt att optimera utformningen av utstötningsstiften och formkavitetens ytfinish samt att implementera korrekta underhålls- och inspektionsrutiner. Dessutom kan det vara nödvändigt att använda speciella utskjutningsmekanismer, t.ex. luftassisterad utskjutning eller sidoutskjutning, för att minimera utskjutningsmärken.
Kortfattade frågor:
Ett kort skott är ett vanligt problem vid formsprutning som uppstår när det smälta plastmaterialet inte fyller formhålan helt, vilket resulterar i en gjuten del som är mindre än önskad storlek. Korta skott kan uppstå av flera skäl, inklusive:
- Otillräckligt med material: Om det inte finns tillräckligt med material för att fylla formhålan kan ett kortskott uppstå.
- Felaktiga bearbetningsförhållanden: Om bearbetningsförhållandena, t.ex. insprutningshastighet och tryck, inte är korrekt inställda kan ett kort skott uppstå.
- Dålig formkonstruktion: En dåligt utformad form kan orsaka ett kortskott, eftersom materialet kanske inte kan flöda in i alla delar av formhålan.
- Nedbrytning av material: Om materialet har försämrats eller inte har förvarats på rätt sätt kan det orsaka en kortslutning.
Korta skott kan försämra detaljens övergripande kvalitet och funktionalitet och leda till slöseri med material och bearbetningstid. För att minimera korta skott är det viktigt att optimera formkonstruktionen, bearbetningsförhållandena och materialvalet samt att tillämpa korrekta materialhanteringsrutiner. Dessutom kan regelbunden övervakning och underhåll av gjututrustningen bidra till att förhindra att kortslutningar uppstår.
Luftlås och brännmärken:
Luftlås och brännmärken är vanliga problem vid formsprutning som kan uppstå på grund av felaktiga bearbetningsförhållanden eller formkonstruktion.
Luftfällor uppstår när luft fångas upp i formhålan under formsprutningsprocessen, vilket gör att materialet flyter runt luftfickan i stället för att fylla den. Detta kan resultera i synliga hålrum eller fickor i den gjutna delen. Luftfällor kan orsakas av flera faktorer, bland annat:
- Otillräckligt materialflöde: Om materialet inte flödar ordentligt in i formhålan kan luft fångas upp.
- Felaktig utformning av grinden: Om porten inte är korrekt utformad kan luft fastna i formhålan.
- Otillräcklig ventilation: Om formen inte är ordentligt ventilerad kan luft fångas i formhålan.
Brännmärken uppstår när plastmaterialet utsätts för höga temperaturer under för lång tid, vilket leder till att det bryts ned och ger synliga märken eller missfärgningar på detaljens yta. Brännmärken kan orsakas av flera faktorer, bland annat:
- För höga bearbetningstemperaturer: Om bearbetningstemperaturen är för hög kan materialet brytas ned och ge brännmärken.
- Otillräcklig kylningstid: Om detaljen inte kyls ordentligt kan materialet brytas ned och ge brännmärken.
- Dålig utformning av gjutformen: En dåligt utformad form kan leda till att materialet utsätts för höga temperaturer under för lång tid, vilket resulterar i brännmärken.
För att minimera luftfällor och brännmärken är det viktigt att optimera bearbetningsförhållandena och formkonstruktionen samt att införa lämpliga övervaknings- och underhållsmetoder. Dessutom kan det vara nödvändigt att använda speciella bearbetningstekniker, t.ex. lågtemperaturgjutning eller vakuumgjutning, för att minimera luftfällor och brännmärken.
Bearbetning för att tillverka en formsprutningsform:
Processen för att tillverka en formsprutningsform omfattar flera steg:
Formkonstruktion:
Formsprutningsdesign är en kritisk aspekt av formsprutningsprocessen, eftersom den direkt påverkar kvaliteten, effektiviteten och kostnaden för de gjutna delarna.
En väldesignad formsprutningsform producerar delar som uppfyller önskad storlek, form och kvalitetskrav, samtidigt som den är effektiv att producera och lätt att underhålla.
De viktigaste faktorerna att tänka på när man utformar en formsprutningsform inkluderar:
- Geometri för detaljen: Designen av den gjutna delen måste ta hänsyn till önskad storlek, form och egenskaper hos delen.
- Val av material: Materialet som ska användas för formen och den gjutna delen måste väljas utifrån faktorer som kostnad, styrka och termisk stabilitet.
- Kaviteter i gjutformen: Antalet och arrangemanget av formkaviteterna måste väljas för att uppfylla kraven på produktionsvolym.
- Angöringssystem: Utformningen av ingångssystemet är avgörande eftersom det avgör hur plastmaterialet flödar in i formhålan.
- Utstötningssystem: Utstötningssystemet måste vara konstruerat så att de gjutna delarna kan tas ut ur formen utan att skadas.
- Kylsystem: Kylsystemet måste vara utformat så att de gjutna delarna kyls jämnt och snabbt, vilket minskar cykeltiden och förbättrar kvaliteten.
- Utkastvinklar: Formens konstruktion måste inkludera lämpliga utdragsvinklar så att de gjutna delarna kan tas ut ur formen.
- Ventilation: Formen måste ventileras så att luft kan strömma ut från formhålan, vilket minskar risken för luftfällor och brännmärken.
- Underhåll och reparation: Formen måste vara konstruerad så att den är lätt att underhålla och reparera, för att minimera stilleståndstiden och öka produktionseffektiviteten.
Formsprutning är en komplex process som kräver expertis inom områden som maskinteknik, materialvetenskap och tillverkning. Det är viktigt att arbeta med en välrenommerad formkonstruktör för att säkerställa att formen är korrekt utformad och uppfyller dina behov.
CNC-programmering:
CNC-programmering (Computer Numerical Control) är ett viktigt steg i tillverkningen av en formsprutningsform. När formkonstruktionen är klar är nästa steg CNC-programmering. Följande är de viktigaste stegen i CNC-programmering för tillverkning av formsprutningsformar:
- Översättning av CAD-modell: CAD-modellen översätts till ett CAM-program (Computer Aided Manufacturing), som används för att skapa CNC-koden för gjutformen.
- Skapande av CNC-kod: CNC-koden skapas i CAM-programmet, som ger instruktioner till CNC-maskinen om hur man flyttar och skär formkomponenterna. Koden tar hänsyn till materialet och tjockleken på formkomponenterna samt önskade former och funktioner.
- Skapande av verktygsbana: Verktygsbanan skapas i CAM-programmet och definierar den bana som skärverktyget ska följa för att bearbeta formkomponenterna. Verktygsbanan tar hänsyn till formkomponenternas former och egenskaper samt CNC-maskinens kapacitet.
- Simulering: CNC-koden och verktygsbanan simuleras i CAM-programmet för att säkerställa att formkomponenterna bearbetas på rätt sätt och enligt rätt specifikationer.
- CNC-bearbetning: CNC-koden laddas in i CNC-maskinen, som sedan använder koden och verktygsbanan för att bearbeta formkomponenterna.
CNC-programmering är ett kritiskt steg i tillverkningsprocessen för formsprutningsverktyg, eftersom det avgör noggrannheten och kvaliteten på formkomponenterna. Det är viktigt att arbeta med en CNC-programmerare som har erfarenhet av programmering för formsprutning för att säkerställa att CNC-koden skapas korrekt och enligt rätt specifikationer. Det är också i detta steg som formens kylkanaler, ejektorsystem och andra funktioner läggs till i formkomponenterna för att säkerställa att de fungerar korrekt.
Inköp av BOM-lista för mögel
En Mold BOM-lista (Bill of Materials) är en omfattande lista över alla komponenter och material som behövs för att tillverka en formsprutningsform. Den innehåller följande artiklar:
- Stål för formbotten och kärn-/kavitetsinsatser
- Varmkanalkomponenter
- Komponenter i kylsystemet, t.ex. vattenledningar och kylblock
- Komponenter till utskjutningssystemet, t.ex. utskjutningsstift och hylsor
- Komponenter för granatutdragning
- Värmeband och temperaturregulatorer
- Formkomponenter, t.ex. bussningar, styrstift och låsanordningar
- Forminsatser, t.ex. slider och lyftare
- Specialprodukter, t.ex. datumstämplar och anpassade logotyper
Mold BOM-listan är ett viktigt verktyg för upphandling och tillverkning, eftersom den ger en tydlig och detaljerad lista över de komponenter och material som behövs för att producera formen. Den används för att säkerställa att alla nödvändiga komponenter är beställda och finns till hands när formen är klar att tillverkas.
Det är viktigt att arbeta med en välrenommerad leverantör när man köper komponenter till en formsprutningsform, eftersom kvaliteten och tillförlitligheten hos dessa komponenter kan ha en betydande inverkan på formsprutningsprocessens effektivitet och kvalitet.
Grovbearbetning av gjutform:
Grovbearbetning av formsprutningsformar avser den inledande bearbetningen av stålkomponenterna i en formsprutningsform för att uppnå formens grundläggande form och storlek. Detta steg utförs vanligtvis med hjälp av CNC-maskiner (Computer Numerical Control). Följande är de viktigaste stegen vid grovbearbetning av formsprutningsverktyg:
- Val av stål: Det första steget är att välja lämplig typ av stål för gjutformen, t.ex. P20 eller H13, baserat på de önskade egenskaperna hos den gjutna delen.
- Skärning av stål: Stålet skärs till lämplig storlek och form med hjälp av en CNC-maskin. Detta steg kan också omfatta borrning och gängtappning av hål för kyl- och utskjutningssystemen.
- Profilering av stål: Stålkomponenterna bearbetas sedan för att uppnå formens grundläggande form, inklusive kärnan och hålrumsinsatserna.
- Inspektion av stål: De bearbetade komponenterna inspekteras sedan för att säkerställa att de uppfyller de toleranser och specifikationer som krävs.
- Rengöring av stål: De bearbetade komponenterna rengörs och avgradas för att avlägsna alla grova kanter och skräp.
Grovbearbetningen är ett viktigt steg i formsprutningsprocessen eftersom den lägger grunden för den slutliga högprecisionsbearbetningen och poleringen som sedan följer. Det är viktigt att se till att grovbearbetningen görs exakt och enligt rätt specifikationer för att säkerställa att formen fungerar korrekt och producerar delar med önskad kvalitet.
Värmebehandling av formstål:
Värmebehandling av formstål är en process där stålkomponenterna i en formsprutningsform värms upp och kyls ned för att förbättra deras mekaniska egenskaper och dimensionsstabilitet. Syftet med värmebehandlingen är att härda stålet, lindra restspänningar och förbättra dess slitstyrka och seghet. Detta är speciellt för härdningsstålet i formsprutan, om du använder förhärdat stål för att göra formsprutan behöver du inte göra detta värmebehandlingsjobb. Följande är de viktigaste stegen som är involverade i värmebehandling av formstål:
- Glödgning: Stålkomponenterna värms upp till en viss temperatur, vanligtvis mellan 800-900°C, och kyls sedan långsamt för att minska de inre spänningarna och förbättra stålets bearbetbarhet.
- Härdning: Stålkomponenterna upphettas till en hög temperatur, vanligtvis över den kritiska temperaturen, och kyls sedan snabbt, vanligtvis genom kylning i olja eller vatten. Denna process gör stålet hårdare och förbättrar dess slitstyrka.
- Anlöpning: Efter härdningen anlöps stålkomponenterna genom att de värms till en lägre temperatur under en viss tid för att förbättra stålets seghet och dimensionsstabilitet.
Värmebehandlingsprocessen är avgörande för att säkerställa att stålkomponenterna i en formsprutningsform har de önskade mekaniska egenskaperna och dimensionsstabiliteten, vilket är avgörande för att producera högkvalitativa gjutna delar. Det är viktigt att arbeta med en värmebehandlingsleverantör som har erfarenhet av att behandla formstål för att säkerställa att värmebehandlingsprocessen utförs korrekt och enligt rätt specifikationer.
Finbearbetning av formkavitet och kärna:
Finbearbetning av formkavitet och kärna är processen för exakt bearbetning av de inre ytorna på formkaviteten och kärninsatserna för att uppnå formens slutliga form och storlek. Detta steg görs vanligtvis med hjälp av CNC-maskiner (Computer Numerical Control) med hög precision och noggrannhet. Följande är de viktigaste stegen som är involverade i finbearbetning av formkavitet och kärna:
- Förberedelse av ytan: Formkavitetens och kärninsatsernas yta rengörs och poleras för att avlägsna eventuella rester av skräp eller ojämnheter.
- Bearbetning av ytor: De inre ytorna på formhålan och kärninsatserna bearbetas med CNC-maskiner för att uppnå formens slutliga form och storlek. Detta inkluderar att skapa de invecklade detaljerna och funktionerna i den gjutna delen, till exempel text, logotyper och underskärningar.
- Inspektion av ytor: De bearbetade ytorna inspekteras för att säkerställa att de uppfyller de toleranser och specifikationer som krävs.
- Ytpolering: De inre ytorna på formhålan och kärninsatserna poleras till en hög finish för att förbättra de gjutna delarnas ytkvalitet och minska risken för defekter.
Finbearbetning är ett kritiskt steg i formsprutningsprocessen, eftersom det avgör kvaliteten och noggrannheten hos de gjutna delarna. Det är viktigt att arbeta med en bearbetningsleverantör som har erfarenhet av finbearbetning av formkaviteter och kärnor för att säkerställa att bearbetningen utförs korrekt och enligt rätt specifikationer. Det är också i detta steg som formens utmatningssystem, kylkanaler och andra funktioner läggs till för att säkerställa att formen fungerar korrekt.
EDM-bearbetning:
EDM (Electrical Discharge Machining) är en process som används för att skapa invecklade och mycket exakta former i metalldelar, inklusive de i en formsprutningsform. Processen använder elektriska gnistor för att avlägsna material från formytan och skapa den önskade formen. Följande är de viktigaste stegen i EDM-bearbetning:
- Förberedelse av ytan: Ytan på den formkomponent som ska bearbetas rengörs och poleras för att avlägsna eventuella rester av skräp eller ojämnheter.
- EDM-inställning: EDM-maskinen ställs in med rätt parametrar, inklusive gnistgap, pulslängd och elektrodmaterial, baserat på formkomponentens material och form.
- Erosion med gnistor: EDM-maskinen producerar elektriska gnistor som avlägsnar material från formkomponenten och skapar den önskade formen. Denna process sker stegvis, där EDM-maskinen gradvis eroderar materialet tills den slutliga formen har uppnåtts.
- Inspektion av ytan: Den bearbetade ytan inspekteras för att säkerställa att den uppfyller de toleranser och specifikationer som krävs.
EDM-bearbetning används ofta för formkomponenter som har komplexa former eller små, intrikata detaljer som är svåra att uppnå med andra bearbetningsprocesser. Det används också för att producera de skarpa kanter och hörn som är väsentliga för att en formsprutningsform ska fungera korrekt.
Processen är mycket exakt och noggrann, vilket gör den idealisk för att producera högkvalitativa gjutna delar. Det är viktigt att arbeta med en EDM-leverantör som har erfarenhet av EDM-bearbetning för formsprutningsformar för att säkerställa att processen utförs korrekt och enligt rätt specifikationer.
Polering av mögelytan:
Polering av formsprutningsform är det sista steget i tillverkningsprocessen för formsprutningsverktyg. Det handlar om att jämna ut ytorna på formkomponenterna för att säkerställa att den färdiga produkten har en slät och jämn yta. Följande är de viktigaste stegen vid polering av formsprutningsformar:

polering av plastformar
- Förberedelse av ytan: Ytorna på formkomponenterna rengörs och förbereds för polering. Eventuella kvarvarande ojämnheter eller bearbetningsmärken avlägsnas för att säkerställa en slät yta för polering.
- Grovpolering: Det första steget i poleringen är grovpolering, vilket innebär att man tar bort alla stora ojämnheter i ytan på formkomponenterna. Detta steg görs vanligtvis med ett grovkornigt slipmedel, t.ex. ett sandpapper eller en slipborste.
- Finpolering: Finpolering är nästa steg, som innebär att ytan på formkomponenterna jämnas ut till en finare finish. Detta steg görs med ett finkornigare slipmedel, t.ex. ett finare sandpapper eller en slipborste.
- Buffring: Buffring är det sista steget i poleringen, vilket innebär att man använder en buffertskiva och polermassa för att uppnå en högglansig yta på formkomponenterna.
- Inspektion: Efter poleringen inspekteras formkomponenterna noggrant för att säkerställa att de har en slät och jämn yta utan repor, sprickor eller andra brister.
Polering av formsprutningsformar är viktigt eftersom det påverkar slutproduktens kvalitet. En välpolerad form resulterar i en produkt med en slät och jämn yta, vilket är viktigt för produktens funktionalitet och estetik. Det är viktigt att arbeta med en erfaren formpolerare för att säkerställa att formkomponenterna poleras enligt rätt specifikationer och till önskad kvalitetsnivå.
Montering av gjutform
Formmontering är ett specialiserat jobb inom formsprutning och innebär montering, installation och testning av formsprutningsformar. Formmästare ansvarar för att säkerställa att formkomponenterna är korrekt monterade och fungerar korrekt, och att formen producerar delar med önskade kvalitets- och prestandastandarder. Några av de viktigaste ansvarsområdena för formmontörer inkluderar:
- Montering av formkomponenterna: Formmästarna är ansvariga för att montera de olika komponenterna i en formsprutningsform, inklusive kaviteten och kärnkomponenterna, löparsystemet och eventuella hjälpkomponenter.
- Installera gjutformen på gjutformsmaskinen: Moldmaster måste kunna montera formen på mögelmonteringsmaskinen på ett sätt som säkerställer korrekt inriktning och funktion av formen, om det inte finns någon mögelmonteringsmaskin, använd sedan manuellt sätt att montera formen, det här är de flesta företag gör.
- Testning av gjutformen: Formmästaren ansvarar för att testa formen för att säkerställa att den producerar delar med önskad kvalitet och prestandastandarder. Detta inkluderar inspektion av delarna för eventuella defekter, såsom skevhet, krympning eller andra kvalitetsproblem.
- Justering av gjutformen: Om några problem upptäcks under testfasen är moldmaster ansvarig för att göra nödvändiga justeringar av formen för att säkerställa att den producerar delar som uppfyller de önskade specifikationerna.
- Felsökning: Formmästaren måste kunna identifiera och felsöka eventuella problem som kan uppstå under formtillpassningsprocessen.
Jobbet som gjutformsmontör kräver en kombination av teknisk kunskap, manuell skicklighet och känsla för detaljer. Formmontörer måste kunna arbeta med ett brett utbud av verktyg och maskiner samt förstå de komplexa processer som ingår i formsprutning. Det är viktigt att du har en god förståelse för formsprutningsprocessen och erfarenhet av att arbeta med olika typer av formar och material.
Första provning eller fotografering av formsprutning:
Provskjutning av formsprutning avser processen att testa formsprutningsformen för att producera en provdel med hjälp av formsprutningsprocessen. Denna process är ett kritiskt steg i formsprutningsprocessen, eftersom det gör det möjligt för tillverkaren att utvärdera formens prestanda och göra eventuella nödvändiga justeringar innan de producerar en stor mängd delar.
Processen för provskjutning av formsprutning omfattar vanligtvis följande steg:
- Förberedelser: Formen installeras på formsprutningsmaskinen och maskinen ställs in för gjutning. Tratten fylls med plastharts.
- Kontroll av smälttemperaturen: Smälttemperaturen kontrolleras för att säkerställa att plasthartset värms upp till rätt temperatur för att producera högkvalitativa delar.
- Insprutning: Den smälta plasten sprutas in i formen under högt tryck. Trycket bibehålls tills formen är fylld med plasthartset.
- Kylning: Formen kyls för att plasthartset ska stelna och forma detaljen. Kyltiden bestäms av vilken typ av plastharts som används och storleken och formen på den del som ska tillverkas.
- Utstötning: När detaljen har stelnat tas den ut ur formen. Utmatningsstiften används för att trycka ut detaljen ur formen.
- Inspektion: Den del som produceras från formen inspekteras noggrant för att säkerställa att den uppfyller de önskade specifikationerna och kvalitetsstandarderna.
- Justeringar: Om det behövs kan justeringar göras i gjutprocessen för att förbättra formens prestanda och kvaliteten på de delar som produceras.
Provskjutningsprocessen för formsprutning är ett viktigt steg i formsprutningsprocessen, eftersom det gör det möjligt för tillverkaren att utvärdera formens prestanda och göra eventuella nödvändiga justeringar innan de producerar en stor mängd delar. Denna process hjälper till att säkerställa att formen producerar högkvalitativa delar med önskade specifikationer.
Formpackning och redo för produktion:
När formen är helt färdig av formtillverkaren är nästa steg för den massiva produktionen. Formpackning och förberedelse för produktion är det sista steget i formsprutningsprocessen innan massproduktionen kan börja. Detta steg innebär följande uppgifter:
- Rengöring och underhåll: Formen rengörs noggrant och inspekteras för att säkerställa att det inte finns några skräp, smuts eller skador på formen.
- Förpackning och förvaring: Formen förpackas noggrant och förvaras på en säker plats för att förhindra skador och säkerställa att den är redo att användas när den behövs.
- Testning och justering: Formen testas för eventuella problem, t.ex. läckage, dålig fyllning eller felaktig utmatning av delar, och eventuella nödvändiga justeringar görs för att säkerställa att formen fungerar korrekt.
- Produktionsinställning: Formen installeras i formsprutningsmaskinen och alla nödvändiga inställningar, t.ex. temperatur, tryck och formsprutningshastighet, justeras för att uppfylla de specifika produktionskraven.
- Produktionsstart: Det första partiet med delar produceras och processen övervakas för att säkerställa att delarna uppfyller de specifikationer och kvalitetsstandarder som krävs. Eventuella nödvändiga justeringar görs för att optimera produktionsprocessen och säkerställa en jämn kvalitet.
Överlag är förberedelsen av formen för produktion ett viktigt steg i formsprutningsprocessen som bidrar till att säkerställa att produktionen blir framgångsrik och effektiv.
Ovanstående information är förfaranden för att göra en formsprutning, kanske det finns några små saker som saknas men de flesta sakerna är ovan, som du kan se att göra en formsprutning är inte lätt fall, om du har ett formsprutningsprojekt i handtaget måste du hitta en professionell formsprutningstillverkare för att betjäna dig, detta kommer att se till att ditt projekt körs framgångsrikt.
Sincere Tech är en professionell Kina mögel fabrik som specialiserar sig på tillverkning av anpassade formsprutningsformar. De har erfarenhet och expertis inom design, utveckling och produktion av högkvalitativa formsprutningsformar för olika branscher och applikationer.
De tillhandahåller en rad tjänster, inklusive formdesign, prototyper, formtillverkning och bearbetning efter formning, för att säkerställa att deras kunder får bästa möjliga resultat. Med sitt fokus på kvalitet, precision och kundnöjdhet är Sincere Tech en pålitlig och pålitlig partner för alla dina formsprutningsbehov. Kontakta oss för att få ett pris för ditt projekt nu.