Как пластиковая форма для стульев позволяет изготавливать удобные современные сиденья
Пластиковые стулья можно увидеть практически везде, куда бы вы ни положили глаз, от оживленных кафе на городских улицах до уголков вашего собственного дома. Но задумывались ли вы когда-нибудь о том, как эти стулья вообще появляются на свет?
Удивительно простой ответ — это не что иное, как пластиковая форма для стульев, инструмент, который формирует стулья, на которых вы сидите каждый день.
Пластиковая форма для стульев — это не просто негативное пространство. Люди, работающие на заводе по производству пластиковых форм для стульев, подобны скульпторам, которые превращают расплавленный пластик в удобные и функциональные решения для сидения.
Но что делает пластиковый стул таким полезным в первую очередь? Читайте дальше, чтобы узнать больше о скрытых преимуществах пластиковых стульев.
Новое определение эффективности: массовое производство для максимального комфорта
Представьте себе мир, в котором каждый пластиковый стул изготавливался бы вручную. Стоимость и время, затраченные на это, были бы непомерно высокими! Пластиковые формы для стульев полностью устраняют это препятствие. Пластиковая форма для стульев позволяет производителям производить идентичные стулья на высокой скорости, что значительно сокращает время производства и общие затраты. Это приводит к более широкой доступности недорогих решений для сидения для всех, от владельцев оживленных ресторанов до экономных семей.
Постоянная прочность для надежного фундамента
Хлипкий стул может быть совершенно неудобным, не говоря уже о том, что он также может представлять серьезную угрозу безопасности. Пластиковая форма для стульев гарантирует постоянную толщину стенок и общую структурную целостность всех производимых стульев. Она гарантирует, что пользователи всегда в безопасности, предлагая надежную основу комфорта, независимо от того, поглощены ли вы рабочей встречей в офисе или наслаждаетесь неспешным обедом.
Изыски дизайна: стул на любой случай
Не все потребности в сидении одинаковы. Пластиковый формованный стул удовлетворяет этому требованию, поскольку он предлагает удивительный набор возможностей дизайна. Конструкции пластикового формованного стула можно адаптировать для создания идеального стула для любых целей, от эргономичных офисных стульев с регулируемой поясничной поддержкой до штабелируемых стульев для бистро для уличных кафе. Это гарантирует, что уровень функциональности и комфорта будет соответствовать конкретному предполагаемому использованию.
Чудеса материалов: выбор правильной формулы комфорта
Надежный завод по производству пластиковых стульев не использует только один тип пластика. Различные материалы могут быть выбраны в соответствии с желаемым балансом веса, прочности и комфорта.
Например, полипропилен или ПП является популярным выбором, поскольку он легко чистится и имеет небольшой вес, что делает его рекомендуемым выбором для уличной мебели.
С другой стороны, полиэтилен высокой плотности или HDPE обеспечивает несравненную гибкость и прочность, что идеально подходит для мест с высокой проходимостью, таких как школы и рестораны. Эта гибкость гарантирует, что кресло изготовлено с правильной «формулой комфорта» для той цели, для которой оно предназначено.
Помимо сидения: форма для многоцелевого использования
Пластиковые формы выбора используются не только для традиционных сидений. Они также могут пригодиться для множества других функциональных и удобных изделий, включая пляжные шезлонги, детское игровое оборудование, а также эргономичные компоненты сидений для инвалидных колясок. Эта универсальность делает их ценным активом в широком спектре отраслей.
1. Минимальный срок службы пластиковой формы для стула.
Нормальный стандарт срока службы формы для стульев должен соответствовать как минимум 0,5 миллионам коротких отрезков или даже больше, поэтому качество стали очень важно, некоторые компании, производящие литьевые формы, предлагают сталь низкого качества, чтобы сэкономить деньги и предложить более низкую цену для клиента, но когда у клиента есть форма на его заводе, через несколько месяцев могут возникнуть проблемы, чтобы сохранить хорошее качество пластиковой формы для стульев, мы обычно предлагаем нашим клиентам использовать сталь для форм 718H или P20. Это гарантирует, что форма прослужит как минимум 0,5 миллиона без каких-либо проблем.
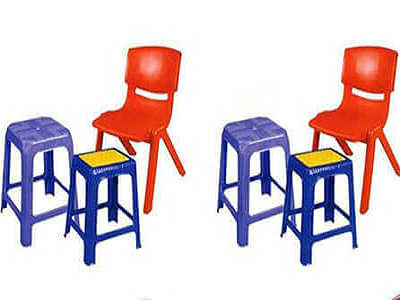
пластиковый стол стул форма
2. Время цикла пресс-формы пластикового стула во время производства,
3. Как оптимизировать вес пластиковой формованной детали стула, сохранив при этом ту же прочность.