Мичиган В стране развита обрабатывающая промышленность, особенно в литье пластмасс под давлением. Процесс находит широкое применение в производстве высокоточных изделий в таких отраслях, как автомобилестроение, медицинское оборудование, электроника и упаковка. Мичиганские компании, занимающиеся литьем пластмасс под давлением завоевали репутацию надежных и инновационных компаний со всего мира.
Кроме того, эти компании по литью пластмасс под давлением в Мичигане предоставляют обширный перечень услуг в зависимости от требований производителя, начиная от быстрого прототипирования и изготовления оснастки и заканчивая крупносерийным производством. В этой статье мы расскажем о некоторых из них. Ведущие производители литья пластмасс под давлением в Мичигане регион и предлагаемые ими услуги.
1. Hi-Tech Mold & Engineering

Hi-Tech Mold & Engineering Является семейным производителем второго поколения. пластиковые литьевые формы и продукции, расположенная в Мендоне, штат Мичиган, и обслуживающая промышленность с тех пор, как 1994. Являясь ведущим производителем пластиковых форм, компания делает ставку на креативность, эффективность и высокое качество продукции.
Комплексные услуги в области литья под давлением
Компания Hi-Tech Mold & Engineering предоставляет различные решения в области литья под давлением для различных отраслей промышленности, включая автомобильную, аэрокосмическую, медицинскую и электротехническую промышленность включительно. Инновационные технологии и более чем 30-летний опыт работы позволяют компании предоставлять эффективные услуги для достижения целей разработки и производства продукции клиентов.
Спектр их услуг по литью под давлением включает в себя:
- Литье под давлением и компрессионное формование: Лучшее из обоих, инжекция и компрессия, специально для сложных конструкций и геометрии.
- Молдинг: Стратегия развития процесса, направленная на уменьшение количества материала и веса детали, но в то же время на повышение ее прочности и несущей способности.
- Вставка для формовки: Процесс введения металла или других материалов в пластиковую деталь за один прием для улучшения ее жесткости и других свойств.
- Формование под низким давлением: Применяется на тонких и сложных деталях, которые не должны подвергаться высокому давлению на этапе обработки.
- Формовка Smartfoil: Они используют гибкую пленку для изготовления тонких деталей сложной формы с низким расходом материала.
Центр передовых технологий для точного производства.
В компании используются самые современные и автоматизированные системы, обеспечивающие эффективность и качество. Здесь мы проводим испытания и проверку пресс-форм с использованием лучших технологий: Core Back, Coining и Injection-Compression Molding. Эти инновационные условия позволяют нам систематически соответствовать самым высоким требованиям отрасли и ожиданиям клиентов.
Экспертиза и глобальный охват
Hi-Tech Mold & Engineering зарекомендовала себя как компания, способная с высоким профессионализмом реализовать даже самые сложные программы. Мы предлагаем комплексные решения для всех этапов разработки продукции - от небольших комплектов инструментов до масштабных автомобильных платформ. Благодаря глобальным связям мы предоставляем клиентам полный спектр услуг, экономичные решения и эффективное выполнение проектов.
Сертификация и обеспечение качества
Их приверженность качеству подтверждается отраслевыми сертификатами, включая IATF 16949, AS9100D и ISO 9001:2015 отражает стремление к постоянному повышению эффективности и качества выпускаемой продукции. Если вам нужно разработать и изготовить новый продукт или увеличить производительность уже существующего, вам нужна компания Hi-Tech Mold & Engineering - вовремя, в срок, каждый раз.
Если вы ищете компании по литью пластмасс под давлением рядом со мной в Мичигане для литья под давлением с газовой опорой или литья со вставкой, то мы предлагаем вам связаться с ними, чтобы проверить ваш проект и предложить вам цену.
2. Айронвуд Пластикс
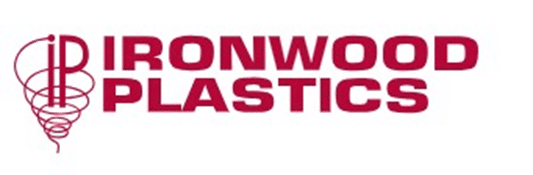
Айронвуд Пластикс начался в 1979 и зарекомендовала себя как инженерная компания с высокими стандартами производства. В состав компании входят два завода, расположенные в Айронвуде, штат Мичиган, и в Двух реках, штат Висконсин. Являясь лидером на рынке литья под давлением, компания не теряет из виду свою цель - постоянно обеспечивать высокое качество обслуживания клиентов благодаря современным инженерным и производственным технологиям.
Возможности и опыт
Компания Ironwood Plastics разработала широкий спектр решений для литья под давлением на заказ для удовлетворения различных потребностей. Их инженерно-технический персонал использует самые современные технологии и стандарты отрасли и способен точно выполнять как простые, так и сложные операции литья. Независимо от того, требуется ли вам небольшое или крупномасштабное производство для вашего проекта, у них есть опыт, который поможет нам достичь вашей цели.
Инвестиции в новейшее оборудование и постоянное обучение персонала позволяют нам работать с широким спектром технологий формовки, включая:
- Индивидуальное литье под давлением: Основная специализация компании - производство прецизионных литых изделий для автомобильной промышленности, производства медицинского оборудования, потребительских товаров и многих других.
- Вторичные услуги: Компания имеет полный набор вторичных операций, таких как сборка, декорирование и тестирование, чтобы обеспечить строгое качество конечной продукции.
- Advanced Materials Handling: Они производят все распространенные термопласты, а также высокоэффективные полимеры, поэтому мы всегда найдем идеальный вариант для вашего конкретного изделия.
- Сложные конструкции пресс-форм: Для создания сложных творений, требующих сложной техники лепки.
Как компания, Ironwood Plastics признает, что ее главная сила - это профессиональное проектирование в сочетании с опытом и профессионализмом. Они обеспечивают превосходные отношения с клиентами и гарантируют, что мы предоставляем услуги, которые отвечают техническим требованиям клиентов, а также помогают создать устойчивую стоимость бизнеса.
Идеальные места для позиционирования себя на службе
- Штаб-квартира компании находится в Айронвуде, штат Мичиган.
1235 Уолл-стрит, Айронвуд, MI 49938
Телефон: 906.932.5025
- Два Риверса, штат Висконсин
Почтовый ящик 2800, Две реки, Висконсин 54241
Телефон: 920.793.3060
Благодаря таким местам мы можем обращаться к клиентам по всей Северной Америке и в других частях света, предоставляя услуги быстрой доставки и бесплатного обслуживания клиентов.
Сертификация качества и соответствие требованиям
Они гордятся сертификатами ISO 9001 и IATF 16949:2016, которые подтверждают соблюдение стандартов управления качеством в компании. Кроме того, компания также применяет такие стандарты, как MAPP Manufacturing Alliance, ITAR и т. д.
Будучи членом группы компаний CTB, которая является мировым поставщиком оборудования для сельского хозяйства и пищевой промышленности, мы имеем все возможности для расширения нашего опыта и следования новейшим технологиям производства.
Ironwood Plastics - это не только литье под давлением, но и стратегический партнер, обеспечивающий инновационные инженерные решения и высочайшую точность. Если вам нужно разработать новый продукт или усовершенствовать существующий, у них есть все необходимые ресурсы и опыт, чтобы удовлетворить вас.
Если вы ищете компании по литью пластмасс под давлением в Мичигане, которые предоставляют услуги по сборке изделийСпециальный материал деталей для литья под давлением, вы можете подумать о них для справки, или использовать их для цитирования вашего проекта.
3. MMI Engineered Solutions

MMI Engineered Solutions является универсальным поставщиком решений для OEM-производителей, разрабатывающих и производящих легкие решения с меньшими затратами и более высокими эксплуатационными характеристиками. Сосредоточившись на передовых композитах и инженерных смолах, мы поставляем исключительные компоненты и узлы для высокопроизводительных приложений в автомобильной, аэрокосмической промышленности и на рынках обработки материалов.
Основными областями специализации компании являются инжиниринг, оснастка и производство. Чтобы воплотить в жизнь лучшие разработки с помощью технологических достижений, мы предлагаем продукцию, которая помогает инженерам и производителям решать самые сложные задачи. Будь то литье под давлением или выдувное формование или использование передовых материалов в изделиях, компания предлагает лучшее, когда речь идет о производительности на всех этапах производства.
Основные услуги:
- Литье под давлением и выдувное формование: Точные термопластичные компоненты, детали и узлы.
- Решения для обработки материалов: Специализация - новые композитные и инженерные смолы для погрузочно-разгрузочных работ.
- Инструменты: Инструментальный центр, способный разрабатывать и изготавливать сложные пресс-формы своими силами и в короткие сроки.
- Услуги по проектированию: Мы можем предложить более творческие решения, поскольку наша команда конструкторов работает с 3D-программами, Moldflow и FEA-анализом.
Глобальное присутствие и местоположение:
- Штаб-квартира: Салин, Мичиган, США
- Другие места нахождения: Трой, штат Мичиган, Уоррен, штат Мичиган, Монтеррей, Мексика
Дополнительные возможности:
- Собственные инструменты: Сокращение сроков изготовления и улучшение конкурентных позиций.
- Поддержка дизайна: Инструменты CAD, Moldflow и FEA как эффективные средства решения проблем.
- Процесс APQP: Знание DFMEA/PFMEA, планов управления и сроков реализации проектов.
Основываясь на своей истории успеха в разработке и поставке высокопроизводительных решений, MMI Engineered Solutions остается лидером на рынке OEM-производителей, предлагая инструменты и поддержку, необходимые для решения жизненно важных вопросов проектирования и производства.
Если вы ищете пластик компании по литью под давлением рядом со мной в Мичигане, которые предоставляют услуги по производству оснастки для литья под давлением, литью под давлением с раздувом или дизайну, вы можете подумать о них для справки или связаться с ними, чтобы предложить свой проект.
4. Джимди Пластик

Джимди Пластик является лидером в отрасли, предлагая передовые технологии литья пластмасс под давлением и вставное молдинг услуги. Она была основана в 1997Компания находится в городе Аллендейл, штат Мичиган. Основным видом деятельности компании является предоставление прецизионных деталей и узлов, изготовленных методом литья под давлением, для широкого спектра отраслей промышленности по всему миру. Эти принципы позволяют компании работать с клиентами из автомобильной промышленности, производства потребительских товаров, медицинского оборудования и многих других отраслей, предлагая бизнес-решения для глобального рынка.
Основные возможности
- Литье под давлением: В их состав входят 16 прессов весом от 110 до 1100 тонн, которые позволяют выпускать продукцию как в малых, так и в больших объемах. Кроме того, они используют различные типы материалов, и мы предоставляем такие специфические услуги, как формование со вставками и литье с избытком.
- Инструменты: Мы берем на себя полную ответственность за вашу оснастку, начиная с разработки и заканчивая испытанием. У нас есть хорошие связи с местными и зарубежными инструментальными мастерскими, поэтому мы можем предложить высококачественные алюминиевые инструменты и прототипы.
- Инженерия: Их профессиональные инженеры вместе с клиентами определяют подходящие материалы и наиболее подходящие технологии литья под давлением. Кроме того, они оказывают клиентам целый ряд услуг, начиная с создания прототипов и заканчивая обслуживанием в конце срока службы.
- Сборка и вторичные операции: Технологии сборочных линий включают в себя автоматические и ручные сборочные станции, а также звуковую сварку, шелкографию, тампопечать и лазерное травление.
Приверженность компаний качеству
Руководство Jimdi Plastics осознало, что качество - это результат целенаправленного подхода и упорного труда. Они строго придерживаются стандартов сертификации ISO, чтобы удовлетворять клиентов высококачественными деталями.
Почему стоит выбрать Jimdi Plastics?
- Широкий диапазон печати: Интеграция 16 печатных машин позволяет им с легкостью работать с различными объемами производства.
- Инновационные решения: Используя прогрессивные технологии формовки и материалы, мы можем удовлетворить потребности клиентов.
- Комплексная поддержка: Начиная с проектирования и конструирования изделия и заканчивая его сборкой, а также вторичными операциями, они предлагают полный комплекс производственных услуг.
- Глобальный охват: Они поставляют экономически эффективные детали, изготовленные методом литья под давлением, что позволяет их клиентам достигать целей на международном рынке.
Если вы ищете компании по литью пластмасс под давлением рядом со мной в Мичигане, которая предоставляет услуги по изготовлению оснастки, формовке вкладышей, сборке изделий и инжинирингу, вы можете подумать о них для справки или связаться с ними, чтобы предложить свой проект.
5. PTI Engineered Plastics

PTI Engineered Plastics, Inc. является ведущим литейщиком пластмасс и производителем пластмассовых деталей и узлов в штате Мичиган (США). За 3 десятилетия работы компания PTI обслуживала различные отрасли промышленности, такие как медицинская, оборонная/аэрокосмическая и другие. Благодаря своей точности и творческому подходу, PTI сегодня является ценным поставщиком для фирм, ищущих качественные пластиковые изделия.
Основные возможности
- Литье пластмасс под давлением: PTI предоставляет услуги от единичного прототипа до крупносерийного производства. Для прототипов и серийного производства, для мелкосерийного или контрактного производства PTI производит высококачественные детали по самым высоким стандартам.
- Собственные инструменты: Качество начинается с инструмента. Компания PTI имеет более чем 30-летний опыт изготовления пресс-форм и использует самые передовые технологии для создания точных форм для своих инструментальщиков. Этот собственный потенциал напрямую отражается в коротких сроках выполнения заказа и способности предоставить качественные пресс-формы, используемые в производстве ваших деталей на всех этапах - от разработки до завершения.
- Создание прототипов: В компании PTI вы получите детали для тестирования и проверки конструкции с помощью услуг литья под давлением прототипов. В некоторых сценариях применения деталей небольшого количества тот же прототип может служить в качестве первой производственной партии, что позволяет быстрее и дешевле вывести деталь на рынок.
- Формование в чистом помещении: В связи с растущим спросом на экологически чистое производство в медицинской и аэрокосмической промышленности, компания PTI увеличила свою Чистое помещение класса 8 пространство до 10 000 футов. Расширение производства повышает возможности PTI по выпуску деталей без загрязнений и соответствует стандартам ISO 13485.
- Промышленный дизайн: Группа промышленного дизайна PTI напрямую сотрудничает с клиентами, разрабатывая идеи для производства. Их прямое взаимодействие с инженерами и специалистами по оснастке сокращает процесс проб и ошибок, характерный для литья пластмасс, ускоряя тем самым переход от проектирования к производству.
Основные обслуживаемые рынки
- Медицина: Компания PTI соответствует стандарту ISO 13485 и поэтому предлагает детали медицинского класса для использования в устройствах, требующих точности и производительности. Будь то хирургические инструменты, диагностические аппараты или имплантаты, PTI гарантирует, что все детали соответствуют нормативным требованиям.
- Оборона/аэрокосмическая промышленность: Компания PTI предлагает специальные изделия, изготовленные методом литья под давлением, отвечающие требованиям оборонного и аэрокосмического рынков. Их литье в чистых помещениях и передовые методы обработки материалов позволяют удовлетворить самые сложные технологические требования.
- Потребительские товары: Компания PTI предлагает рынку потребительских товаров надежные и конкурентоспособные по цене формованные детали для общего пользования.
Почему стоит выбрать PTI Engineered Plastics?
- Экспертиза и опыт: Опыт PTI насчитывает более трех десятилетий, что позволяет компании предлагать техническую экспертизу при реализации сложных проектов по литью в различных отраслях промышленности.
- Передовые чистые помещения и формовочные мощности: Компания увеличила площадь помещения для формования в чистом помещении класса 8 и оснащена всем необходимым для удовлетворения самых строгих медицинских и аэрокосмических требований к неопрену.
- Комплексная поддержка: Как компания, разрабатывающая концепцию и дизайн, производящая оснастку и выпускающая продукцию, PTI предлагает комплексное решение, гарантирующее качество и короткие сроки поставки.
Если вы ищете компании по литью пластмасс под давлением в Мичигане, которые предоставляют медицинское литье под давлением с цехом в кладовой, изготовление прототипов и услуги по промышленному штампованию, вы можете подумать о них и предложить им свой проект.
6. Mdbio

В качестве компания по производству пластиковых форм Компания Medbio LLC, имеющая отличную репутацию в индустрии медицинского оборудования, специализируется на точных решениях, инновациях и прецизионной оснастке. Производители пресс-форм в компании Medbio имеют доступ к современному инструментальному цеху и располагают штатом опытных конструкторов, которые могут разработать производственные пресс-формы класса SPI, наилучшим образом отвечающие специфическим требованиям заказчика.
Основные возможности
Передовой дизайн и проектирование инструментов
Компания Medbio может разрабатывать инструменты с использованием самого современного программного обеспечения для проектирования пресс-форм и анализа потоков, представленного на рынке. Команда опытных инженеров использует обратный инжиниринг и 3D-моделирование пресс-формы для повышения надежности пресс-формы и целостности инструмента, а также улучшения характеристик детали. Это гарантирует, что каждый разработанный инструмент будет иметь лучший производственный процесс, а также лучшее качество продукции.
Анимация функций пресс-формы
Компания Medbio создала анимационные видеоролики работы пресс-формы с использованием современного программного обеспечения CAD. Эти анимации показывают открытие, закрытие и функционирование пресс-формы в ходе различных операций, таких как боковое воздействие, многоступенчатое выталкивание, а также совместное литье под давлением. Это помогает заказчикам проводить детальный анализ конструкции и значительно упрощает процесс создания формовочных команд.
Высокоточные формовочные прессы
Высокоскоростные обрабатывающие центры и вертикальные обрабатывающие центры используются в Medbio для повышения детализации при создании пресс-форм. Их оборудование включает в себя:
- Вертикальные обрабатывающие центры Milltronics VM20 для более тонкой работы.
- Родеры для обрабатывающего центра для высокой скорости и точности.
- Пресс-формы для высокоточного производства штамповочных головок Mitsubishi EX22
- Проволочные станки Sodick с точностью резки проволоки и сверления глубоких отверстий
Собственные инструментальные решения
От проектирования пресс-форм до изготовления инструментов - Medbio предлагает своим клиентам собственную инструментальную базу, которая позволяет увеличить время производства и повысить качество продукции. Благодаря ориентации на прецизионные инструменты мы можем гарантировать реализацию высокодетализированных проектов быстрее и эффективнее.
Программа стажировки:
Компания Medbio стремится к развитию будущих профессиональных производителей пресс-форм через аккредитованную программу стажировки, предоставляемую при поддержке Министерство труда США и Общественный колледж долины Каламазу. В намеченной программе сочетаются лекции с практическими занятиями и техническими навыками, необходимыми для работы с инструментами для медицинского оборудования.
Обслуживаемые отрасли
Промышленность медицинского оборудования:
Компания Medbio, специализирующаяся на производстве прецизионных пресс-форм для медицинского применения, знает, что такой бизнес подразумевает соблюдение высоких требований к регулированию и качеству в медицинской промышленности. Они производят инструментальные решения, которые гарантируют качество и производительность этих жизненно важных медицинских устройств.
Потребительские товары:
Medbio также предлагает решения по оснастке для потребительских товаров, которые предлагают клиентам разумные решения в области пресс-форм. Их услуги позволяют клиентам реализовать свои производственные потребности и ожидания, как ожидается на конкурентном потребительском рынке.
Почему стоит выбрать Medbio?
- Экспертный дизайн и проектирование: Компания Medbio использует обширный опыт в проектировании пресс-форм, а также передовые технологии, чтобы предложить точные и качественные решения по оснастке для медицинских приборов и других потребительских товаров.
- Современное производство: Компания Medbio располагает самыми современными инструментальными станками, чтобы гарантировать, что каждая изготовленная пресс-форма идеально подходит для вашей продукции и обеспечивает высокоскоростную точность обработки, являющуюся стандартом в отрасли.
- Инновационный подход: Компания использует самые современные технологии во всем, от моделирования до анимации функций пресс-формы, гарантируя уникальные решения, независимо от сложности проекта.
- Приверженность качеству: Компания Medbio имеет сертификаты качества ISO и стремится реализовать каждый проект с точностью до мелочей.
Связаться с компанией Medbio
Штаб-квартира:
5346 36-я улица Юго-Восточная, Гранд-Рапидс, Мичиган 49512
Телефон: Номер телефона: 616 245 0214 | Номер факса: 616 245 0244
Офис в Клинтон Тауншип
Телефон: (586) 954-2553
Офис в Орчард-Парке:
Телефон: (716) 662-8550
Сайт: www.medbiollc.com
Если вы ищете компании по литью пластмасс под давлением в Мичигане, которые предоставляют медицинское литье под давлением, а также экспертные услуги по штамповке и инжинирингу, вы можете подумать о них и обратиться к ним за ценой на ваш проект.
7. Вестфолл Техник, ООО

Вестфолл Техник, ООО является ведущей компанией в области литья пластмасс под давлением, предлагающей превосходные инструменты и качественные изделия на заказ. Расположенная в Темпе, штат Аризона, компания Westfall Technik имеет обширную клиентуру из различных отраслей промышленности, включая аэрокосмическую, медицинскую, автомобильную, производство потребительских товаров, электроники и промышленных изделий. Компания рассматривает себя как экологически сознательную компанию и является основным поставщиком для производителей, которым необходимы точность, скорость и инновационные решения в области литья под давлением.
Возможности
Индивидуальное литье под давлением
Westfall Technik является экспертом в производстве высокоточных и точных деталей с помощью ряда процессов формования, таких как микроформование и многозаходное литье под давлением. Компания зарекомендовала себя как надежный производитель, позволяющий клиентам получать компоненты, отвечающие самым высоким требованиям.
Передовые инструментальные решения
Кроме того, благодаря технологиям проектирования и изготовления оснастки Westfall Technik гарантирует, что каждая пресс-форма будет создана в соответствии с самыми высокими стандартами. Инженерный отдел компании использует новейшие Технология CAD и 3D-моделирование для создания наиболее эффективных пресс-форм, что позволяет сократить время выхода на рынок и общие производственные расходы.
Опыт в области микроформовки
Компания Westfall Technik известна своей способностью производить детали с использованием микроформовки, относительно небольшие и сложные.
Обслуживаемые отрасли
- Автомобильный
- Медицинские приборы
- Потребительские товары
- Электроника
- Аэрокосмическая промышленность
Почему стоит выбрать Westfall Technik?
- Комплексное обслуживание: Westfall Technik предлагает полный спектр решений, начиная с проектирования и изготовления оснастки и заканчивая окончательной сборкой в соответствии с требованиями литья под давлением.
- Передовые технологии: Кроме того, компания применяет самые современные технологии для обеспечения точности и качества процесса, начиная с изготовления пресс-формы и заканчивая выпуском готовой продукции.
- Обязательства в области устойчивого развития: Westfall Technik как организация поставила перед собой цель свести к минимуму воздействие на окружающую среду при производстве и реализации продукции.
- Опытная команда: В компании работает команда инженеров и дизайнеров, которые обладают достаточным опытом, чтобы преодолеть любые сложности при формовке.
Контактная информация
Расположение
9280 S. Kyrene Rd, Suite 106
Темпе, АЗ 85284
Телефон: +1 (702) 829-8681
Электронная почта: solutions@westfalltechnik.com
Рабочие часы
Пн - Пт: 8:00 утра - 6:00 вечера
Если вы ищете компании по литью пластмасс под давлением рядом со мной в Мичигане, которые предоставляют двойное литье под давлениемУслуги литья под давлением и микролитья под давлением, вы можете подумать о них и привлечь их к участию в вашем проекте.
8. Lacks Enterprises
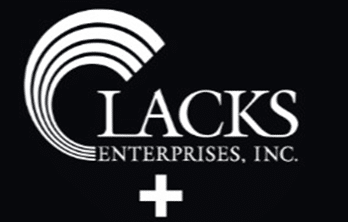
Lacks Enterprises является лидером в индустрии отделочного декора уже более 60 лет. Она изменила представления дизайнеров о том, как разрабатывать компоненты для интерьера и экстерьера автомобилей. Миссия Lacks заключается в предоставлении инновационных, совершенных и устойчивых решений. Их выдающиеся продукты, такие как Tessera® 3-D текстура и металлическая отделка Spinelle™ позволяют дизайнерам развивать гибкость в широком спектре автомобильных конструкций.
Основные возможности
Декор интерьера:
Компания Lacks представила новую серию натурального металла и хрома. Компания предлагает практически бесконечное множество текстур и цветов для отделки салона. Компания также помогает в дифференциации на уровне отделки, чтобы помочь автопроизводителям улучшить внешний вид интерьеров автомобилей.
Внешний декор:
Не просто украшения, а системы отделки экстерьера Lacks вносят инновации в автомобильный бизнес. От решеток до аппликаций, их продукция повышает привлекательность автомобиля и в то же время предлагает решение функциональных аспектов, таких как аэродинамика.
Легкие колесные решения:
Компания Lacks поставляет легкие колесные узлы и детали, помогая автомобильным дизайнерам по-новому взглянуть на возможности. Их колесные технологии используются не только для увеличения производительности автомобилей, но и для повышения их топливной экономичности за счет меньшего веса.
Технология углеродного волокна:
Не хватает Колеса из углеродного волокна предлагают высокую производительность и свободу дизайна. Их продукция используется в основном в автомобильной промышленности и отличается легкостью и прочностью.
Инновации последних лет и лидеры рынка
- Приобретение Forgeline Motorsports: Недавняя покупка компанией Lacks компании Forgeline Motorsports - это начало нового поколения в производстве колес. Это приобретение помогает Lacks укрепить свои позиции в качестве лидера рынка высокопроизводительных колес.
- Высокопроизводительные колеса для Dodge: Лакс была выбрана Dodge чтобы оснастить самый быстрый в мире серийный автомобиль Не хватает углеродного волокна™ Колеса, чтобы доказать, что они являются лучшими в области высокоточных высокопроизводительных автомобильных компонентов.
- Дизайн электромобилей с Lucid Motors: Лакс сыграл важную роль в разработке колесных решений для компании Lucid. Флагманский EV, Lucid Air, которая напрямую противостоит Mercedes, BMW и другим автомобильным гигантам.
Глобальный охват
Компания Lacks работает в глобальном масштабе, располагая предприятиями на ключевых автомобильных рынках.
Места
Штаб-квартира: Гранд-Рапидс, штат Мичиган, США
Не хватает Европы: Мюнхен, Германия
Отсутствует Япония: Токио, Япония
Отсутствует Южная Корея: Сеул, Южная Корея
Лакс Великобритания: Оксфордшир, Великобритания
Почему стоит выбрать Lacks Enterprises?
- Инновации: Компания Lacks работает уже более 60 лет и продолжает внедрять инновации в индустрию автомобильного декора и производительности.
- Настройка: Благодаря 3-D текстурам и индивидуальной отделке Lacks предоставляет клиентам гибкость в дизайне, которой нет у других компаний.
- Глобальное присутствие: Компания Lacks работает во многих странах, что позволяет ей работать с глобальными клиентами и в то же время оставаться актуальной для рынка конкретной страны.
Если вы ищете компании по литью пластмасс под давлением рядом со мной в Мичигане, которые предоставляют технологии углеродного волокна и услуги по проектированию электромобилей, вы можете подумать о них и привлечь их к работе над вашим проектом.
9. ADAC Automotive
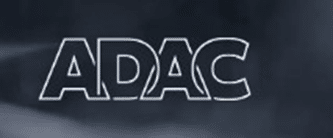
ADAC Automotive является ведущей в мире компанией по разработке, проектированию и производству автомобильных решений. Начиная с зарождения идеи и заканчивая созданием конечного продукта, ADAC Automotive предоставляет полный спектр услуг, который может похвастаться лучшими качество, креативность и экологичность.
Возможности
Дизайн и проектирование:
Дизайнеры и инженеры-эксперты ADAC используют новейшие технологии сканирования и метрологии для создания экологичных и точных продуктов. При разработке концепции и создании продукции ADAC гарантирует, что конечный продукт будет создан в результате детального и тщательного процесса проектирования.
Аддитивное производство и быстрое прототипирование:
Избежать высоких затрат на оснастку можно, воспользовавшись услугами быстрого прототипирования, которые создают возможности для малосерийного производства и многочисленных изменений. Опыт ADAC в области аддитивного производства позволяет предложить быстрые и экономичные инструменты, которые ускоряют цикл разработки продукта и позволяют воплотить дизайн в жизнь.
Литье под давлением:
В настоящее время ADAC владеет более чем 80 прессов для литья под давлениемкоторые находятся между 240 и 1200 тонн, что позволяет нам решать любые задачи. Возможности компании в области литья под давлением помогают в крупносерийном производстве продукции с высокой точностью формы и размеров выпускаемых деталей.
Настройка и отделка:
Услуги по покраске и индивидуальной отделке могут быть предоставлены в окрашенном виде или в соответствии с требованиями клиента, что придает автомобильным компонентам ADAC превосходную эстетическую и тактильную привлекательность.
Интеграция электроники:
Интеграция электроники - это действительно сильная сторона инженерной команды ADAC, которая использует интеллектуальные технологии, такие как датчики, приводы, а также освещение.
Контроль качества:
Контроль качества большинства продуктов, разрабатываемых в ADAC, регулируется в соответствии со стандартами ISO, что позволяет получать качественную продукцию на протяжении всего производственного процесса. Для обеспечения качества используются самые современные средства метрологии и целый ряд процедур контроля.
Обслуживаемые отрасли
- Автомобильный
- Бытовая электроника
- Аэрокосмическая промышленность
Почему стоит выбрать ADAC Automotive?
Комплексные решения:
ADAC выполняет полный комплекс услуг "под ключ" по проектированию, производству и интеграции электроники от первоначальной идеи до готового изделия. Такой плавный процесс позволяет значительно быстрее выводить продукцию на рынок в автомобильной промышленности, особенно сложные детали.
Передовые технологии:
Благодаря использованию аддитивного производства, высокотехнологичного формовочного оборудования и интеграции электроники ADAC гарантирует, что ее продукция не только передовая, но и функциональная, отвечающая самым современным технологическим требованиям.
Обязательства в области устойчивого развития:
Устойчивое развитие является ключевым направлением деятельности ADAC во всех аспектах производственного процесса, начиная с поиска материалов и заканчивая самой продукцией.
Обеспечение качества:
Высокое качество - главная задача ADAC, и, стремясь поставлять высококачественную продукцию, компания строго следит за качеством и предлагает результаты всестороннего тестирования и проверки.
Настройка и создание прототипов:
ADAC фокусируется на создании уникальных продуктов и быстрых прототипов, которые также позволяют доработать детали продукта за короткий промежуток времени.
Связаться с ADAC Automotive
Штаб-квартира: 5690 Eagle Dr. SE, Гранд-Рапидс, Мичиган 49512
Телефон: (616) 957-0520
Если вы ищете компании по литью пластмасс под давлением рядом со мной в Мичигане, которые предоставляют услуги по литью автомобилей под давлением и аэрокосмическому литью под давлением, вы можете подумать о них и предложить им свой проект.
10. Западный Мичиган Пластик
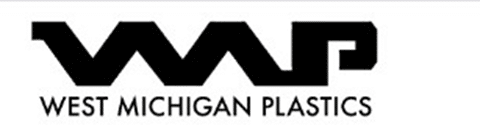
West Michigan Plastics Inc. занимается литьем пластмасс под давлением и была образована в 1986. Компания специализируется на производстве прецизионных пластмассовых изделий на заказ для различных отраслей промышленности, таких как автомобильная, медицинская, государственная и строительная. Будучи инновационной компанией, ориентированной на качество и эффективность, они сотрудничают с клиентами, чтобы предоставить лучший продукт для всех.
Основные возможности
Качественные изделия, изготовленные методом литья под давлением
Компания West Michigan Plastics гордится тем, что предоставляет лучшие литые изделия. Вместе с клиентами их команда работает в тандеме, чтобы достичь наилучшего дизайна изделия, определить подходящий материал и создать точную оснастку, соответствующую самым высоким стандартам. Каждый продукт, который они производят, проходит строгий процесс контроля качества перед выпуском на рынок.
Надежная доставка
Как уже упоминалось, благодаря использованию автоматизированных рабочих ячеек, их деятельность носит непрерывный характер, что позволяет им быстро доставлять заказы и удовлетворять как обычные, так и JIT-требования. В соответствии с нашей миссией, поставки осуществляются быстро и надежно, чтобы соответствовать производственным графикам клиентов.
Отрасли, которые они обслуживают
Мы обслуживаем широкий спектр отраслей промышленности, включая:
Автомобильная промышленность:
Наша продукция включает в себя специальные пластиковые компоненты, внутреннюю отделку и детали из конструкционного пластика, которые повышают производительность и снижают вес автомобиля.
Медицина:
Литье под давлением для медицинских целей, которое мы обеспечиваем, отличается высокой точностью и соответствует всем необходимым отраслевым стандартам. Наша область специализации - производство деталей для медицинских приборов, диагностического оборудования и других сопутствующих применений в сфере здравоохранения.
Строительство:
Мы производим ряд высокопрочных и износостойких пластмасс для нужд строительной отрасли, а также изделия для строительных материалов и строительной техники.
Местонахождение и контактная информация:
West Michigan Plastics, Inc.
5745 В. 143-я авеню
Холланд, MI 49423
Телефон: (616) 394-9269
Факс: (616) 394-5240
Электронная почта: info@wmiplastics.com
Если вы ищете пластик литьё под давлением компании рядом со мной в Мичигане, которые предоставляют автомобильное литье под давлениемУслуги по аддитивному производству и прототипированию, вы можете подумать о них и привлечь их к реализации своего проекта.
Заключение
Мичиган В компании имеется богатый выбор опытных компаний, занимающихся литьем пластмасс под давлением; они предоставляют различные услуги и продукты для удовлетворения многочисленных потребностей автомобильного, медицинского и электронного секторов, а также других отраслей. Эти компании хорошо известны своей точностью, креативностью и способностью удовлетворять потребности клиентов. Для компаний, которым нужны услуги литья под давлением, эти компании способны предоставить отличные услуги для предприятий в Мичигане.
Однако для тех, кто ищет решения за пределами Соединенных Штатов, особенно в Китае, Искренняя техника является надежным партнером, предоставляющим полный спектр услуг по формовке по разумным ценам. Компания Sincere Tech работает уже несколько десятилетий и предоставляет своим клиентам качественную продукцию, поэтому она может помочь вам найти производственные решения в Китае. Вы можете связаться с ними, чтобы узнать больше об их продукции или о том, как они могут помочь вашему бизнесу.