Ce este matrița de injecție?
Matriță de injecție este o unealtă utilizată în procesul de turnare prin injecție pentru a produce piese prin injectarea materialului într-o cavitate de turnare. Acesta este de obicei fabricat din oțel (H13, P20, 1.2312, 1.2344, S136H etc.) sau aluminiu și este proiectat cu atenție pentru a se potrivi formei și specificațiilor produsului final.
Matrița de injecție este împărțită în două jumătăți, jumătate cavitate și jumătate miez, care sunt fixate împreună în timpul procesului de turnare, materialul fiind injectat printr-un canal de scurgere în cavitatea matriței, unde se răcește și se solidifică în forma dorită. Odată ce piesa este formată, matrița se deschide și piesa este ejectată. Matrița poate fi reutilizată pentru a produce mai multe piese.

Ce este turnarea prin injecție
Tipuri de matrițe de injecție
Printre numeroasele varietăți de matrițe de injecție, puteți găsi:
Mucegai specific cavității
Fiecare ciclu al procesului de turnare prin injecție poate genera o singură piesă atunci când se utilizează o matriță cu o singură cavitate. Procesul de fabricare a unei piese cu această matriță este la fel de simplu ca injectarea rășinii plastice în ea, așteptarea răcirii și apoi îndepărtarea produsului finit.
Atunci când se compară costurile de producție ale matrițelor multi-shot cu cele ale matrițelor cu o singură cavitate, primele sunt de obicei mai accesibile. Atunci când fabricarea unui număr mic de componente deodată ar fi prea costisitoare, acestea sunt soluția de bază pentru prototipuri și producții de volum redus.

Matriță cu o singură cavitate
Avantajele matrițelor cu o singură lovitură includ:
- Eficace din punct de vedere al costurilor: producția unei matrițe cu o singură lovitură este adesea mai puțin costisitoare decât producția unei matrițe cu mai multe lovituri.
- Design simplu: Ușurința producției și a întreținerii datorită simplității designului: Matrițele cu o singură lovitură sunt adesea mai puțin complexe în ceea ce privește aspectul decât matrițele cu mai multe lovituri.
- Flexibilitate: O mare varietate de aplicații, cum ar fi prototiparea și producția de volum redus, sunt potrivite pentru utilizarea matrițelor cu o singură cavitate.
Dezavantajele matrițelor single-shot includ:
- Producție limitată: Această limitare face ca matrițele cu o singură cavitate să fie nepotrivite pentru serii de producție de turnare de volum mare, deoarece acestea sunt capabile să producă o singură piesă în timpul fiecărui ciclu.
- Piese complexe: Matrițele cu o singură cavitate nu sunt bune pentru fabricarea pieselor complicate cu multe piese; pentru acestea, veți avea nevoie de o matriță cu cavități multiple sau de o matriță de familie.
- Ineficiență: În comparație cu matrițele cu cavități multiple, matrițele cu o singură lovitură sunt mai puțin eficiente, deoarece pot crea o singură piesă în timpul fiecărui ciclu datorită capacității lor limitate.
Forme cu cavități multiple:
Matrițele cu cavități multiple sunt un tip de matrițe de injecție care au mai mult de o cavitate. Acest lucru permite procesului de turnare prin injecție să producă mai mult de o piesă în timpul fiecărei rotații. În funcție de nevoile aplicației, aceste matrițe pot fi realizate cu găuri identice sau diferite.
Ca urmare a capacității sale de a crea mai multe piese într-un singur ciclu, matrițele multi-cavități sunt utilizate de obicei pentru turnare prin injecție în volume mari serii de producție. Această caracteristică le permite să crească eficiența producției, reducând în același timp costul pe piesă.

matriță cu cavități multiple
Avantajele matrițelor multi-cavități includ:
- Producție în volume mari: Matrițele cu cavități multiple sunt realizate pentru producții pe scară largă, ceea ce facilitează realizarea unei cantități mari de piese.
- Rentabile: matrițele cu mai multe cavități sunt de obicei mai ieftine decât matrițele cu o singură cavitate, deoarece pot produce mai multe piese într-o singură execuție.
- Piese complexe: Matrițele cu cavități multiple pot fi utilizate pentru a realiza piese complicate și cu multe părți.
Dezavantajele matrițelor multi-cavități includ:
- Design complex: Matrițele cu cavități multiple sunt mai dificil de realizat și de întreținut decât matrițele cu o singură cavitate, deoarece modelele lor sunt mai complicate.
- a crescut costul matriței: Matrițele cu cavități multiple pot fi mai costisitoare decât matrițele cu o singură cavitate, deoarece diferitele cavități pot fi supuse unor eforturi și uzuri diferite în timpul procesului de turnare prin injecție. Acest lucru ar putea duce la o producție mai puțin eficientă și la costuri mai mari pentru reparații.
Matriță cu canal cald:
Matriță cu canal cald este un tip de matriță de injecție care utilizează un sistem cu canal cald pentru a introduce materialul plastic topit în cavitățile matriței. Sistemul cu canal cald constă într-un colector încălzit care distribuie plasticul topit la vârfurile duzelor individuale, care sunt apoi direcționate în cavitățile matriței.

Matriță cu canal cald
Avantajele matrițelor cu canal cald includ:
- Îmbunătățirea calității pieselor: matrițele cu canal cald pot produce piese cu o calitate îmbunătățită, deoarece minimizează cantitatea de plastic care rămâne în canale, reducând riscul apariției unor defecte cum ar fi sclipiri, lovituri scurte și urme de scufundare.
- Creșterea eficienței producției: Matrițele cu canal cald pot crește eficiența producției, deoarece elimină necesitatea intervenției manuale pentru îndepărtarea canalelor de pe piesele turnate, reducând timpul de ciclu și îmbunătățind viteza generală de producție.
- Eficiență energetică: Matrițele cu canal cald sunt mai eficiente din punct de vedere energetic în comparație cu matrițele tradiționale cu canal rece, deoarece minimizează cantitatea de plastic care este irosită în canale.
Dezavantajele matrițelor cu canal cald includ:
- Design complex: Designul matrițelor cu canal cald este mai complex în comparație cu matrițele tradiționale cu canal rece, ceea ce le face mai costisitoare pentru producție și întreținere.
- Întreținere sporită: Matrițele cu canal cald necesită de obicei mai multă întreținere în comparație cu matrițele cu canal rece, deoarece au un sistem de încălzire mai complex care trebuie menținut în stare bună de funcționare.
- Vulnerabilitatea la înfundare: Matrițele cu canal cald pot fi vulnerabile la înfundare, în special atunci când procesează materiale cu vâscozitate ridicată sau cu lungimi de curgere mari, deoarece acestea pot determina solidificarea plasticului topit în canale. Acest lucru poate duce la reducerea eficienței producției și la creșterea costurilor de întreținere.
Stivuiți matrițele:
Mold Stack este un tip de matriță de injecție care permite ca mai multe cavități să fie turnate simultan într-un singur ciclu de mașină. Matrițele stivuite sunt, în esență, două sau mai multe matrițe stivuite una peste alta, fiecare matriță producând o singură piesă.

Stack Mold
Avantajele matrițelor stivuite includ:
- Creșterea eficienței producției: Matrițele stivuite permit turnarea simultană a mai multor piese, crescând eficiența producției și reducând durata ciclului.
- Reducerea risipei de material: Matrițele stivuite minimizează risipa de material, deoarece permit producerea mai multor piese folosind o singură cantitate de material plastic.
- Costuri mai mici: Matrițele stivuite pot fi mai rentabile în comparație cu matrițele cu o singură cavitate, deoarece permit producția de mai multe piese cu un singur ciclu de mașină.
Dezavantajele matrițelor stivuite includ:
- Design complex: Designul matrițelor cu stivă poate fi mai complex în comparație cu cel al matrițelor cu o singură cavitate, ceea ce le face mai costisitoare pentru producție și întreținere.
- Reducerea calității pieselor: Matrițele stivuite pot produce piese cu o calitate redusă, deoarece prezența mai multor cavități poate duce la creșterea riscului de defecte cum ar fi strălucirea, loviturile scurte și semnele de scufundare.
- Întreținere sporită: De obicei, matrițele cu stivă necesită mai multă întreținere în comparație cu matrițele cu o singură cavitate, deoarece au un design mai complex care trebuie menținut în stare bună de funcționare.
Mucegaiuri de familie:
Matrițele de familie, cunoscute și sub denumirea de matrițe multi-impresie, care este similară cu matrița cu cavități multiple, sunt un tip de turnare prin injecție care permite ca mai multe piese cu modele ușor diferite să fie turnate simultan într-un singur ciclu de mașină. Acest lucru se realizează prin existența mai multor cavități în matriță care pot produce diferite piese cu forme și dimensiuni diferite.
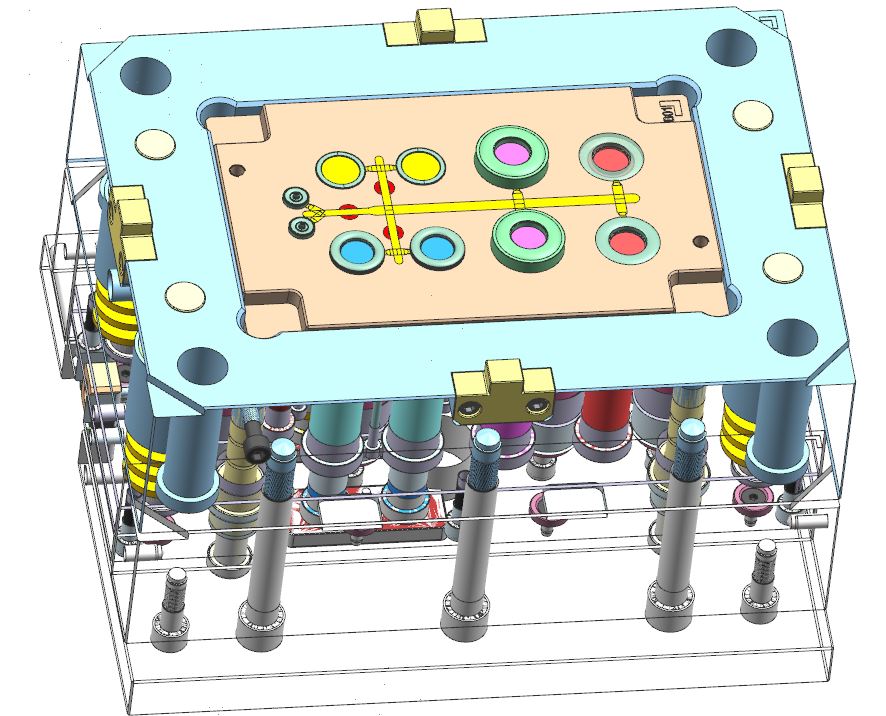
mucegai de familie
Avantajele matrițelor familiale includ:
- Creșterea eficienței producției: Matrițele familiale permit turnarea simultană a mai multor piese cu modele diferite, crescând eficiența producției și reducând durata ciclului.
- Costuri reduse: Matrițele de familie pot fi mai rentabile în comparație cu producerea mai multor matrițe cu o singură cavitate pentru fiecare piesă, deoarece permit producerea mai multor piese cu un singur ciclu de mașină.
- Flexibilitate: Matrițele de familie permit producția de piese diferite cu modele diferite, ceea ce le face o opțiune versatilă pentru producătorii care trebuie să producă o gamă largă de produse.
Dezavantajele mucegaiurilor familiale includ:
- Design complex: Designul matrițelor familiale poate fi mai complex în comparație cu matrițele cu o singură cavitate, ceea ce le face mai costisitoare pentru producție și întreținere.
- Reducerea calității pieselor: Matrițele familiale pot produce piese cu o calitate redusă, deoarece prezența mai multor cavități poate duce la creșterea riscului de defecte cum ar fi strălucirea, loviturile scurte și semnele de scufundare.
Mucegaiuri cu două fotografii:
Matriță cu două lovituri (Turnare prin injecție cu 2 lovituri), cunoscut și sub numele de supramoulare sau matrițe multi-shot sau matrițe 2K, sunt un tip de turnare prin injecție care permite ca două materiale diferite să fie turnate împreună într-un singur ciclu de mașină. Acest proces implică turnarea unui prim material (material de bază) într-o matriță și apoi turnarea unui al doilea material (material de supramuiere) pe primul material.

Matriță cu două fotografii
Avantajele matrițelor cu două lovituri includ:
- Funcționalitate crescută: Matrițele cu două lovituri permit combinarea a două materiale diferite cu proprietăți diferite pentru a crea piese cu funcționalitate sporită.
- Estetică îmbunătățită: Matrițele cu două lovituri permit integrarea diferitelor culori sau texturi într-o singură piesă, creând un produs mai atrăgător din punct de vedere vizual.
- Reducerea timpului de asamblare: Prin combinarea a două materiale într-o singură piesă, matrițele cu două injecții pot reduce necesitatea unor etape suplimentare de asamblare, reducând timpul și costurile de producție.
Dezavantajele matrițelor cu două lovituri includ:
- Design complex: Designul matrițelor cu două lovituri este mai complex în comparație cu cel al matrițelor cu o singură lovitură, ceea ce le face mai costisitoare pentru producție și întreținere.
- Creșterea timpului de ciclu: Matrițele cu două lovituri au de obicei un timp de ciclu mai lung în comparație cu matrițele cu o singură lovitură, deoarece procesul implică turnarea a două materiale într-un singur ciclu de mașină.
- Probleme de compatibilitate: Matrițele cu două lovituri necesită ca cele două materiale turnate să fie compatibile între ele și să adere corect, ceea ce face importantă selectarea cu atenție a materialelor utilizate.
Deșurubarea matrițelor:
Matrițele cu deșurubare sunt un tip de turnare prin injecție special concepute pentru a produce piese cu filet, cum ar fi capacele, capacele și recipientele. Aceste matrițe sunt unice prin faptul că au un mecanism care permite miezului matriței să se rotească în timp ce cavitatea rămâne staționară, permițând ca piesa turnată să fie deșurubată din matriță după ce aceasta s-a răcit și s-a solidificat.

deșurubarea matriței
Avantajele matrițelor de deșurubare includ:
- Eficiență ridicată: Matrițele de deșurubare permit producția eficientă de piese filetate într-un singur ciclu de mașină, reducând timpul și costurile de producție.
- Precizie îmbunătățită: Matrițele de deșurubare permit producția precisă de piese filetate cu pas și adâncime a filetului constante, îmbunătățind calitatea și performanța produsului final.
- Versatilitate: Matrițele de deșurubare pot fi utilizate pentru a produce o varietate de piese diferite cu diferite tipuri și dimensiuni de filet, ceea ce le face o opțiune versatilă pentru multe aplicații diferite.
Dezavantajele matrițelor de deșurubare includ:
- Design complex: Designul matrițelor cu deșurubare este mai complex în comparație cu alte tipuri de matrițe, ceea ce le face mai costisitoare pentru producție și întreținere.
- Creșterea timpului de ciclu: Matrițele de deșurubare au de obicei un timp de ciclu mai lung în comparație cu alte tipuri de matrițe, deoarece procesul implică rotirea miezului matriței.
- Uzură și rupere: Mecanismul rotativ al matrițelor de deșurubare poate fi predispus la uzură și rupere în timp, necesitând o întreținere regulată pentru a menține funcționarea corectă a matriței.
Matriță cu miez colapsabil:
Matrițele cu miez colapsabil sunt un tip de turnare prin injecție care sunt utilizate pentru a produce piese goale cu cavități interne, cum ar fi tuburi, țevi și alte piese de formă complexă. Aceste matrițe utilizează un design unic care permite miezului matriței să se prăbușească în sine, creând cavitatea internă a piesei.

Componentă de matriță cu miez colapsabil
Avantajele matrițelor cu miez pliabil includ:
- Eficiență îmbunătățită: Matrițele cu miez colapsibil permit producția de piese goale într-un singur ciclu de mașină, reducând timpul și costurile de producție.
- Îmbunătățirea calității pieselor: Matrițele cu miez colapsibil oferă o cavitate internă mai precisă și mai consistentă, îmbunătățind calitatea generală a piesei finale.
- Versatilitate: Matrițele cu miez colapsibil pot fi utilizate pentru a produce o gamă largă de piese diferite, cu forme și dimensiuni diferite, ceea ce le face o opțiune versatilă pentru multe aplicații diferite.
Dezavantajele matrițelor cu miez pliabil includ:
- Design complex: Designul matrițelor cu miez colapsibil este mai complex în comparație cu alte tipuri de matrițe, ceea ce le face mai costisitoare pentru producție și întreținere.
- Timp de ciclu mai lung: Matrițele cu miez colapsabil au de obicei un timp de ciclu mai lung comparativ cu alte tipuri de matrițe, deoarece procesul implică colapsarea miezului matriței.
- Uzură și rupere: Mecanismul pliabil al miezului poate fi predispus la uzură și rupere în timp, necesitând întreținere periodică pentru a menține buna funcționare a matriței.
Avantaje și dezavantaje ale turnării prin injecție a plasticului
Avantaje ale Turnare prin injecție:
- Producție în volume mari: Turnarea prin injecție este o metodă extrem de eficientă pentru producerea unor volume mari de piese identice. Acest lucru o face ideală pentru producția în masă de bunuri de consum, piese auto și alte produse care necesită cantități mari de piese similare.
- Precizie: Procesul permite un control foarte precis al preciziei dimensionale și al consistenței pieselor. Acest lucru se datorează utilizării unor condiții de prelucrare strict controlate și rigidității mașinii de turnare și a matriței.
- Viteză: turnarea prin injecție este un proces rapid, cu timpi de ciclu de doar câteva secunde pentru piesele mici. Acest lucru permite producătorilor să producă cantități mari de piese într-un timp relativ scurt.
- Rentabilitate: Costul de producție a pieselor prin turnare prin injecție devine mai economic pe măsură ce volumul de producție crește. Acest lucru se datorează faptului că matrița poate fi utilizată pentru a produce multe piese pe durata sa de viață, iar costul per piesă scade pe măsură ce volumul crește.
- Versatilitate: Turnarea prin injecție poate fi utilizată pentru a produce piese dintr-o gamă largă de materiale, inclusiv materiale plastice, metale și elastomeri. Această versatilitate o face o alegere populară pentru producătorii care trebuie să producă piese din materiale diferite, în funcție de cerințele specifice ale produsului.
- Automatizare: Mașinile de turnare prin injecție pot fi automatizate, ceea ce face procesul mai eficient și reduce nevoia de muncă manuală. Acest lucru poate îmbunătăți, de asemenea, consistența și calitatea pieselor.
- Forme complexe: Turnarea prin injecție poate fi utilizată pentru a produce forme și modele complexe, inclusiv piese cu detalii complicate și toleranțe strânse. Acest lucru este posibil datorită controlului precis al procesului de turnare și capacității de a proiecta matrițe foarte detaliate.
- Selectarea materialelor: Turnarea prin injecție permite producătorilor să aleagă dintr-o gamă largă de materiale, fiecare având propriile proprietăți unice, cum ar fi rezistența, flexibilitatea și rezistența la căldură, substanțe chimice și uzură. Acest lucru face posibilă alegerea celui mai bun material pentru fiecare aplicație și producerea de piese cu proprietățile dorite.
Dezavantaje ale turnării prin injecție:
- Cost inițial ridicat: Costul inițial de creare a matriței poate fi ridicat, în special pentru forme și modele complexe. Acest lucru poate face procesul mai puțin rentabil pentru cantități mici de piese sau pentru prototipuri.
- Flexibilitate limitată a designului: Odată ce matrița este realizată, modificarea designului poate fi dificilă și costisitoare. Acest lucru poate limita capacitatea de a face modificări sau îmbunătățiri de proiectare odată ce matrița a fost creată.
- Deșeuri de materiale: Turnarea prin injecție generează o cantitate semnificativă de deșeuri de material, a căror eliminare poate fi costisitoare și dăunătoare mediului. Acest lucru poate, de asemenea, să crească costul de producție și să reducă eficiența generală a procesului.
- Timpul de execuție: Timpul de execuție pentru crearea matriței și configurarea procesului de turnare prin injecție poate fi lung, în special pentru piesele complexe. Acest lucru poate încetini procesul de dezvoltare a produsului și poate limita capacitatea de a lansa rapid produsele pe piață.
- Limitări ale finisajului suprafeței: Este posibil ca turnarea prin injecție să nu producă un finisaj de suprafață de înaltă calitate pe unele piese, în special pe cele cu detalii complicate sau toleranțe strânse. Acest lucru poate limita capacitatea de a produce piese cu un aspect estetic de înaltă calitate.
- Compatibilitatea materialelor: Compatibilitatea dintre material și matriță poate fi o provocare, deoarece unele materiale nu pot funcționa bine cu anumite tipuri de matrițe sau necesită condiții speciale de prelucrare. Acest lucru poate limita capacitatea de a produce piese din anumite materiale și poate crește costul de producție.
- Dimensiuni limitate ale pieselor: Turnarea prin injecție este limitată de dimensiunea matriței și de forța de strângere a mașinii de turnare. Acest lucru poate limita dimensiunea pieselor care pot fi produse și poate crește costul de producție al pieselor mai mari.
- Operații secundare: Unele piese pot necesita operațiuni secundare, cum ar fi tunderea sau finisarea, după ce au fost turnate. Acest lucru poate crește costul de producție și poate limita eficiența generală a procesului; desigur, în unele cazuri, aceste probleme pot fi rezolvate prin îmbunătățirea matriței de injecție
Probleme comune cu care se confruntă o matriță de injecție
Odată ce lucrați în domeniul turnării prin injecție a plasticului, vor exista întotdeauna unele probleme pe care trebuie să le rezolvați în fiecare zi, Iată câteva provocări comune cu care vă confruntați în turnarea prin injecție:
Probleme de deformare:
Deformarea este o problemă comună cu care se confruntă turnarea prin injecție și se referă la o deformare sau distorsiune a piesei turnate care apare după ce aceasta a fost scoasă din matriță. Acest lucru se poate întâmpla din cauza unei varietăți de factori, inclusiv:

Distorsiune Warp
- Răcire necorespunzătoare: Dacă piesa se răcește prea repede sau neuniform, se pot produce deformări, deoarece materialul se contractă și se micșorează la viteze diferite.
- Tensiuni reziduale: Turnarea prin injecție creează tensiuni reziduale în piesă datorită presiunii ridicate utilizate în timpul procesului de turnare. Acest stres poate provoca deformări dacă nu este eliminat în mod corespunzător.
- Selectarea materialului: Unele materiale sunt mai predispuse la deformare decât altele. De exemplu, materialele cu rezistență scăzută la căldură sau cu stabilitate dimensională scăzută sunt mai predispuse la deformare.
- Designul matriței: Designul matriței poate contribui, de asemenea, la deformare, în special dacă matrița nu permite răcirea corespunzătoare sau curgerea materialului.
- Condiții de prelucrare: Condițiile de prelucrare inconsecvente, cum ar fi vitezele de injecție, temperaturile matrițelor și nivelurile de presiune variabile, pot provoca deformarea.
Pentru a preveni deformarea, este important să alegeți materialul adecvat, să optimizați proiectarea matriței și condițiile de prelucrare și să implementați practici adecvate de răcire și manipulare a materialului. În plus, poate fi necesar să se utilizeze tratamente după turnare, cum ar fi recoacerea, pentru a reduce tensiunile reziduale și a îmbunătăți stabilitatea dimensională.
Probleme cu blițul:
Defectele flash sunt un termen utilizat în turnarea prin injecție pentru a se referi la materialul în exces care este forțat să iasă din matriță în timpul procesului de turnare. Defectele flash apar atunci când materialul curge dincolo de cavitatea prevăzută a matriței și intră în linia de separare sau în spațiul dintre cele două jumătăți ale matriței.

Mucegai Flash sau bavuri
Flash-ul poate fi cauzat de mai mulți factori, inclusiv:
- Proiectarea necorespunzătoare a matriței: O matriță prost proiectată poate cauza strălucirea prin scurgerea materialului în linia de separare.
- Condiții de prelucrare inconsecvente: Condițiile de procesare variabile, cum ar fi viteza și presiunea de injectare, pot provoca sclipiri.
- Compatibilitatea materialelor: Este posibil ca unele materiale să nu fie compatibile cu matrița și să provoace scântei pe măsură ce curg în linia de separare.
- Uzura și ruperea matriței: În timp, matrița se poate uza și poate provoca scântei, deoarece materialul se scurge în linia de separație.
Flash-ul poate avea mai multe efecte negative, inclusiv reducerea preciziei dimensionale a piesei, creșterea ratei de rebuturi și îngreunarea operațiunilor ulterioare turnării. Pentru a minimiza strălucirea, este important să se optimizeze proiectarea matriței, condițiile de prelucrare și selectarea materialelor și să se întrețină și să se repare matrița în mod regulat, după caz.
Linii de sudură:
Liniile de sudură sunt o problemă frecventă în turnarea prin injecție și se referă la semne vizibile pe suprafața piesei turnate, unde două fluxuri de material plastic topit se întâlnesc și se solidifică. Liniile de sudură apar atunci când materialul nu fuzionează complet pe măsură ce curge în matriță din plastic cavitatea, lăsând o linie vizibilă pe suprafața piesei.

Linie de sudare
Liniile de sudură pot fi cauzate de mai mulți factori, inclusiv:
- Curgere insuficientă a topiturii: Dacă materialul nu are suficient timp să curgă și să fuzioneze complet, se poate forma o linie de sudură.
- Proiectarea necorespunzătoare a porții: O poartă prost proiectată, care este punctul în care materialul topit intră în cavitatea matriței, poate cauza o linie de sudură.
- Condiții de prelucrare inconsecvente: Condițiile de prelucrare variabile, cum ar fi viteza și presiunea de injectare, pot cauza o linie de sudură.
- Compatibilitatea materialelor: Unele materiale pot să nu fie compatibile cu matrița și pot provoca o linie de sudură atunci când curg în cavitatea matriței.
Liniile de sudură pot slăbi rezistența piesei și pot reduce calitatea generală a acesteia. Pentru a reduce la minimum liniile de sudură, este important să se optimizeze proiectarea matriței, condițiile de prelucrare și selectarea materialelor și să se pună în aplicare practici adecvate de manipulare a materialelor. În plus, poate fi necesar să se utilizeze tehnici speciale de prelucrare, cum ar fi matrițele cu cavități multiple sau sistemele cu canal cald, pentru a reduce formarea liniilor de sudură.
Semne de scufundare:
Urmele de scufundare, cunoscute și sub numele de "scufundare", "scufundare în vid" sau "piele", sunt zone scufundate sau depresionare pe suprafața unei piese din plastic turnate prin injecție. Acestea sunt de obicei cauzate de o serie de factori, inclusiv:
- Contracția rășinii: Pe măsură ce rășina se răcește și se solidifică, aceasta se poate contracta neuniform, ceea ce duce la apariția unor urme de scufundare.
- Curgere slabă a materialului: Dacă rășina nu curge uniform în toate zonele matriței, se pot crea goluri sau zone înfundate.
- Presiune de ambalare inadecvată: Dacă presiunea de injectare nu este suficient de mare, rășina poate să nu umple complet matrița, ceea ce duce la apariția unor urme de scufundare.
- Probleme de proiectare a matriței: Designul matriței, inclusiv amplasarea și dimensiunea porții, sistemul de canal și ventilația, pot avea un impact asupra calității piesei turnate și pot contribui la apariția urmelor de scufundare.
Urmele de înfundare pot afecta calitatea estetică și funcționalitatea unei piese turnate și pot fi o sursă de frustrare pentru producători și utilizatorii finali. Pentru a minimiza semnele de scufundare, este important să se ia în considerare cu atenție factorii care contribuie la apariția acestora, cum ar fi selectarea materialului, proiectarea matriței, parametrii de prelucrare și proiectarea piesei, și să se facă ajustările necesare pentru a optimiza procesul de turnare prin injecție.
Marcaje de curgere:
Urmele de curgere sunt o problemă comună în turnarea prin injecție și se referă la urme sau dungi vizibile pe suprafața piesei turnate care sunt cauzate de curgerea materialului plastic topit pe măsură ce umple cavitatea matriței. Urmele de curgere apar atunci când materialul curge neuniform, lăsând în urmă o urmă vizibilă pe suprafața piesei.
Urmele de curgere pot fi cauzate de mai mulți factori, inclusiv:
- Curgere insuficientă a topiturii: Dacă materialul nu are suficient timp să curgă și să umple cavitatea matriței, se pot forma urme de curgere.
- Proiectarea necorespunzătoare a porții: O poartă prost proiectată, care este punctul în care materialul topit intră în cavitatea matriței, poate cauza urme de curgere.
- Condiții de prelucrare inconsecvente: Condițiile de procesare variabile, cum ar fi viteza și presiunea de injectare, pot cauza urme de curgere.
- Compatibilitatea materialelor: Este posibil ca unele materiale să nu fie compatibile cu matrița și să provoace urme de curgere pe măsură ce curg în cavitatea matriței.
Urmele de curgere pot reduce calitatea generală și aspectul cosmetic al piesei. Pentru a minimiza semnele de curgere, este important să se optimizeze proiectarea matriței, condițiile de prelucrare și selectarea materialelor și să se pună în aplicare practici adecvate de manipulare a materialelor. În plus, poate fi necesar să se utilizeze tehnici speciale de prelucrare, cum ar fi matrițele cu cavități multiple sau sistemele cu canal cald, pentru a reduce formarea urmelor de curgere.
Probleme de zgârieturi:
Problemele de zgârieturi se referă la semne sau zgârieturi vizibile pe suprafața unei piese turnate prin injecție, cauzate de contactul fizic dintre piesă și matriță sau alte obiecte străine în timpul procesului de turnare. Problemele de zgârieturi pot apărea din mai multe motive, inclusiv:
- Proiectarea necorespunzătoare a matriței: Proiectarea necorespunzătoare a matrițelor sau a componentelor matrițelor poate cauza zgârieturi pe suprafața piesei.
- Lubrifierea insuficientă: Dacă matrița și componentele matriței nu sunt lubrifiate corespunzător, acestea pot cauza zgârieturi pe suprafața piesei.
- Manipularea necorespunzătoare a materialelor: Manipularea necorespunzătoare a materiei prime sau a pieselor finite poate cauza zgârieturi pe suprafața piesei.
- Deșeuri în matriță: Obiectele străine sau resturile din cavitatea matriței pot cauza zgârieturi pe suprafața piesei.
Problemele de zgârieturi pot reduce calitatea generală și aspectul cosmetic al piesei. Pentru a minimiza problemele legate de zgârieturi, este important să implementați practici adecvate de proiectare, lubrifiere, manipulare a materialelor și întreținere a matrițelor. În plus, curățarea și inspectarea regulată a matriței și a componentelor matriței pot contribui la prevenirea apariției problemelor de zgârieturi.
Urme de ejecție:
Urmele de ejecție sunt urme vizibile pe suprafața unei piese turnate prin injecție care sunt cauzate de pinii de ejecție sau de alte mecanisme de ejecție în timpul procesului de turnare. Urmele de ejecție apar atunci când pinii de ejecție împing piesa turnată în afara cavității matriței și lasă în urmă urme vizibile pe suprafața piesei.
Urmele de ejecție pot fi cauzate de mai mulți factori, inclusiv:
- Proiectarea necorespunzătoare a pinilor de ejecție: Dacă știfturile de ejecție nu sunt proiectate corespunzător, acestea pot lăsa urme vizibile pe suprafața piesei.
- Forță excesivă: Dacă știfturile de ejecție aplică o forță excesivă asupra piesei în timpul ejecției, acestea pot lăsa urme mai adânci și mai vizibile pe suprafața piesei.
- Forță de ejecție inconsecventă: Dacă forța de ejecție nu este constantă de la un pin de ejecție la altul, pot apărea urme de ejecție neuniforme pe suprafața piesei.
- Finisaj de suprafață slab: Dacă finisajul de suprafață al cavității matriței nu este neted, pot apărea urme de ejecție pe suprafața piesei.
Urmele de ejecție pot reduce calitatea generală și aspectul cosmetic al piesei. Pentru a reduce la minimum urmele de ejecție, este important să se optimizeze proiectarea pinilor de ejecție și finisarea suprafeței cavității matriței și să se pună în aplicare practici adecvate de întreținere și inspecție. În plus, poate fi necesar să se utilizeze mecanisme speciale de ejecție, cum ar fi ejecția asistată de aer sau ejecția cu acțiune laterală, pentru a minimiza urmele de ejecție.
Probleme de tragere scurtă:
O lovitură scurtă este o problemă comună în turnarea prin injecție care apare atunci când materialul plastic topit nu umple complet cavitatea matriței, rezultând o piesă turnată mai mică decât dimensiunea dorită. Shot-urile scurte pot apărea din mai multe motive, inclusiv:
- Material insuficient: Dacă nu există suficient material pentru a umple cavitatea matriței, poate apărea o lovitură scurtă.
- Condiții de procesare necorespunzătoare: Dacă condițiile de procesare, cum ar fi viteza și presiunea de injectare, nu sunt setate corect, poate apărea o lovitură scurtă.
- Design necorespunzător al matriței: O matriță prost proiectată poate cauza o lovitură scurtă, deoarece materialul nu poate curge în toate zonele cavității matriței.
- Degradarea materialului: În cazul în care materialul s-a degradat sau nu a fost depozitat corespunzător, acesta poate provoca un scurtcircuit.
Împușcăturile scurte pot reduce calitatea și funcționalitatea generală a piesei și pot duce la pierderi de material și timp de prelucrare. Pentru a reduce la minimum loviturile scurte, este important să se optimizeze proiectarea matriței, condițiile de prelucrare și selectarea materialelor și să se implementeze practici adecvate de manipulare a materialelor. În plus, monitorizarea și întreținerea regulată a echipamentelor de turnare pot contribui la prevenirea apariției loviturilor scurte.
Capcană de aer și urme de arsură:
Capcanele de aer și semnele de arsură sunt probleme comune în turnarea prin injecție care pot apărea din cauza condițiilor necorespunzătoare de prelucrare sau a designului matriței.
Capcanele de aer apar atunci când aerul rămâne blocat în cavitatea matriței în timpul procesului de turnare prin injecție, ceea ce face ca materialul să curgă în jurul buzunarului de aer în loc să îl umple. Acest lucru poate duce la apariția unor goluri sau buzunare vizibile în piesa turnată. Capcanele de aer pot fi cauzate de mai mulți factori, inclusiv:
- Curgerea insuficientă a materialului: Dacă materialul nu curge corect în cavitatea matriței, aerul poate rămâne blocat.
- Proiectarea necorespunzătoare a porții: Dacă poarta nu este proiectată corect, aerul poate rămâne blocat în cavitatea matriței.
- Ventilație necorespunzătoare: Dacă mucegaiul nu este ventilat corespunzător, aerul poate rămâne blocat în cavitatea mucegaiului.
Urmele de ardere apar atunci când materialul plastic este expus la temperaturi ridicate pentru o perioadă prea lungă de timp, ceea ce duce la degradarea acestuia și produce urme vizibile sau decolorare pe suprafața piesei. Urmele de ardere pot fi cauzate de mai mulți factori, inclusiv:
- Temperaturi de prelucrare excesive: Dacă temperaturile de prelucrare sunt prea ridicate, materialul se poate degrada și poate produce urme de arsură.
- Timp de răcire insuficient: Dacă piesa nu este răcită corespunzător, materialul se poate degrada și poate produce urme de arsură.
- Design necorespunzător al matriței: O matriță prost proiectată poate face ca materialul să fie expus la temperaturi ridicate prea mult timp, rezultând urme de arsură.
Pentru a minimiza capcanele de aer și semnele de arsură, este important să se optimizeze condițiile de prelucrare și proiectarea matriței și să se pună în aplicare practici adecvate de monitorizare și întreținere. În plus, poate fi necesar să se utilizeze tehnici speciale de prelucrare, cum ar fi turnarea la temperatură scăzută sau turnarea în vid, pentru a reduce la minimum capcanele de aer și urmele de arsură.
Prelucrarea pentru a face o matriță de injecție:
Procesul de realizare a unei matrițe de injecție implică mai multe etape:
Designul mucegaiului:
Proiectarea matrițelor de injecție este un aspect critic al procesului de turnare prin injecție, deoarece afectează în mod direct calitatea, eficiența și costul pieselor turnate.
O matriță de injecție bine concepută va produce piese care îndeplinesc cerințele de dimensiune, formă și calitate dorite, fiind în același timp eficientă în producție și ușor de întreținut.
Factorii cheie de luat în considerare la proiectarea unei matrițe de injecție includ:
- Geometria piesei: Proiectarea piesei turnate trebuie să ia în considerare dimensiunea, forma și caracteristicile dorite ale piesei.
- Selectarea materialului: Materialul care urmează să fie utilizat pentru matriță și pentru piesa turnată trebuie selectat pe baza unor factori precum costul, rezistența și stabilitatea termică.
- Cavitățile matriței: Numărul și dispunerea cavităților matriței trebuie să fie selectate pentru a satisface cerințele volumului de producție.
- Sistemul de închidere: Proiectarea sistemului de închidere este esențială, deoarece determină modul în care materialul plastic curge în cavitatea matriței.
- Sistemul de ejecție: Sistemul de ejecție trebuie proiectat astfel încât să se asigure că piesele turnate pot fi scoase din matriță fără a fi deteriorate.
- Sistemul de răcire: Sistemul de răcire trebuie să fie proiectat pentru a asigura răcirea uniformă și rapidă a pieselor turnate, reducând timpul de ciclu și îmbunătățind calitatea.
- Unghiuri de tragere: Proiectarea matriței trebuie să includă unghiuri de tragere adecvate pentru a permite scoaterea pieselor turnate din matriță.
- Aerisire: Mucegaiul trebuie să fie ventilat pentru a permite aerului să iasă din cavitatea mucegaiului, reducând riscul de capcane de aer și urme de arsuri.
- Întreținerea și repararea: Matrița trebuie să fie proiectată astfel încât să fie ușor de întreținut și reparat, pentru a minimiza timpii morți și pentru a crește eficiența producției.
Proiectarea matrițelor de injecție este un proces complex care necesită expertiză în domenii precum ingineria mecanică, știința materialelor și producția. Este important să lucrați cu un proiectant de matrițe de renume pentru a vă asigura că matrița este proiectată corect și vă satisface nevoile.
Programare CNC:
Programarea CNC (Computer Numerical Control) este o etapă esențială în fabricarea unei matrițe de injecție. Odată ce proiectarea matriței este finalizată, următorul pas este programarea CNC. Următoarele sunt principalele etape implicate în programarea CNC pentru fabricarea matrițelor de injecție:
- Traducerea modelului CAD: Modelul CAD este tradus într-un program de fabricație asistată de calculator (CAM), care este utilizat pentru a crea codul CNC pentru matriță.
- Crearea codului CNC: Codul CNC este creat în programul CAM, care furnizează instrucțiuni mașinii CNC cu privire la modul de deplasare și tăiere a componentelor matriței. Codul ia în considerare materialul și grosimea componentelor matriței, precum și formele și caracteristicile dorite.
- Crearea traseului sculei: Traseul sculei este creat în programul CAM, care definește traseul pe care scula de tăiere îl va urma pentru a prelucra componentele matriței. Traseul sculei ia în considerare formele și caracteristicile componentelor matriței și capacitățile mașinii CNC.
- Simulare: Codul CNC și calea sculei sunt simulate în programul CAM pentru a se asigura că componentele matriței vor fi prelucrate corect și la specificațiile corecte.
- Prelucrare CNC: Codul CNC este încărcat în mașina CNC, care utilizează apoi codul și traseul sculei pentru a prelucra componentele matriței.
Programarea CNC este o etapă critică în procesul de fabricație a matrițelor de injecție, deoarece determină precizia și calitatea componentelor matriței. Este important să lucrați cu un programator CNC care are experiență în programarea matrițelor de injecție pentru a vă asigura că codul CNC este creat corect și conform specificațiilor corecte. Această etapă este, de asemenea, cea în care canalele de răcire ale matriței, sistemul de ejecție și alte caracteristici sunt adăugate la componentele matriței pentru a asigura funcționarea lor corespunzătoare.
Achiziționarea listei BOM pentru mucegai
O listă BOM (Bill of Materials) pentru matrițe este o listă completă a tuturor componentelor și materialelor necesare pentru fabricarea unei matrițe de injecție. Aceasta include următoarele elemente:
- Oțel pentru baza matriței și inserțiile miezului/cavității
- Componente ale canalelor fierbinți
- Componente ale sistemului de răcire, cum ar fi conductele de apă și blocurile de răcire
- Componente ale sistemului de ejecție, cum ar fi știfturile și manșoanele ejectoare
- Componente pentru extractorul de tuburi
- Benzile de încălzire și regulatoarele de temperatură
- Componente ale matriței, cum ar fi bucșe, pini de ghidare și dispozitive de blocare
- Inserții pentru matrițe, cum ar fi glisiere și dispozitive de ridicare
- Articole speciale, cum ar fi ștampile cu dată și logo-uri personalizate
Lista BOM pentru matrițe este un instrument important pentru achiziții și producție, deoarece oferă o listă clară și detaliată a componentelor și materialelor necesare pentru producerea matriței. Aceasta este utilizată pentru a se asigura că toate componentele necesare sunt comandate și disponibile atunci când matrița este gata să fie fabricată.
Este important să lucrați cu un furnizor de renume atunci când achiziționați componente pentru o matriță de injecție, deoarece calitatea și fiabilitatea acestor componente pot avea un impact semnificativ asupra eficienței și calității procesului de turnare prin injecție.
Prelucrarea brută a matriței:
Prelucrarea brută a matriței de injecție se referă la prelucrarea inițială a componentelor din oțel ale unei matrițe de injecție pentru a obține forma și dimensiunea de bază a matriței. Această etapă se realizează de obicei cu ajutorul mașinilor cu control numeric computerizat (CNC). Următoarele sunt principalele etape implicate în prelucrarea brută a matrițelor de injecție:
- Selectarea oțelului: Primul pas este selectarea tipului adecvat de oțel pentru matriță, cum ar fi P20 sau H13, pe baza proprietăților dorite ale piesei turnate.
- Tăierea oțelului: Oțelul este tăiat la dimensiunea și forma corespunzătoare cu ajutorul unei mașini CNC. Această etapă poate include, de asemenea, găurirea și filetarea găurilor pentru sistemele de răcire și ejecție.
- Profilarea oțelului: Componentele din oțel sunt apoi prelucrate pentru a obține forma de bază a matriței, inclusiv miezul și inserțiile cavității.
- Inspecția oțelului: Componentele prelucrate sunt apoi inspectate pentru a se asigura că acestea îndeplinesc toleranțele și specificațiile necesare.
- Curățarea oțelului: Componentele prelucrate sunt curățate și debavurate pentru a îndepărta orice muchii aspre sau resturi.
Procesul de prelucrare brută este o etapă importantă în procesul de turnare prin injecție, deoarece pune bazele etapelor finale de prelucrare și lustruire de înaltă precizie care vor urma. Este important să vă asigurați că prelucrarea brută este efectuată cu precizie și conform specificațiilor corecte pentru a garanta că matrița funcționează corect și produce piese cu calitatea dorită.
Tratament termic pentru oțelul de turnare:
Tratamentul termic al oțelului pentru matrițe este procesul de încălzire și răcire a componentelor din oțel ale unei matrițe de injecție pentru a le îmbunătăți proprietățile mecanice și stabilitatea dimensională. Scopul tratamentului termic este de a întări oțelul, de a elimina tensiunile reziduale și de a-i îmbunătăți rezistența la uzură și duritatea. Acest tratament se aplică în special oțelului întărit al matriței de injecție; dacă se utilizează oțel preîntărit pentru fabricarea matriței de injecție, atunci nu este necesar să se efectueze acest tratament termic. Următoarele sunt principalele etape implicate în tratamentul termic al oțelului pentru matrițe:
- Recoacere: Componentele din oțel sunt încălzite la o anumită temperatură, de obicei între 800-900°C, și apoi răcite lent pentru a elimina tensiunile interne și a îmbunătăți prelucrabilitatea oțelului.
- Călire: Componentele din oțel sunt încălzite la o temperatură ridicată, de obicei peste temperatura critică, și apoi răcite rapid, de obicei prin călire în ulei sau apă. Acest proces întărește oțelul și îi îmbunătățește rezistența la uzură.
- Revenire: După călire, componentele din oțel sunt călite prin încălzirea lor la o temperatură mai scăzută pentru un anumit timp, pentru a îmbunătăți duritatea și stabilitatea dimensională a oțelului.
Procesul de tratare termică este esențial pentru asigurarea faptului că componentele din oțel ale unei matrițe de injecție au proprietățile mecanice și stabilitatea dimensională dorite, care sunt esențiale pentru producerea de piese turnate de înaltă calitate. Este important să lucrați cu un furnizor de tratament termic care are experiență în tratarea oțelului pentru matrițe pentru a vă asigura că procesul de tratament termic este realizat corect și conform specificațiilor corecte.
Prelucrarea fină a cavității matriței și a miezului:
Prelucrarea fină a cavității matriței și a miezului este procesul de prelucrare precisă a suprafețelor interne ale cavității matriței și ale inserțiilor miezului pentru a obține forma și dimensiunea finală a matriței. Această etapă se realizează de obicei cu ajutorul mașinilor cu control numeric computerizat (CNC) cu precizie și acuratețe ridicate. Următoarele sunt principalele etape implicate în prelucrarea fină a cavității matriței și a miezului:
- Pregătirea suprafeței: Suprafața cavității matriței și a inserțiilor de miez sunt curățate și lustruite pentru a îndepărta orice resturi sau rugozități reziduale.
- Prelucrarea suprafețelor: Suprafețele interne ale cavității matriței și ale inserțiilor miezului sunt prelucrate cu ajutorul mașinilor CNC pentru a obține forma și dimensiunea finală a matriței. Aceasta include crearea detaliilor și caracteristicilor complicate ale piesei turnate, cum ar fi textul, logo-urile și adânciturile.
- Inspecția suprafețelor: Suprafețele prelucrate sunt inspectate pentru a se asigura că acestea respectă toleranțele și specificațiile necesare.
- Șlefuirea suprafeței: Suprafețele interne ale cavității matriței și ale inserțiilor miezului sunt șlefuite la un finisaj înalt pentru a îmbunătăți calitatea suprafeței pieselor turnate și a reduce riscul de defecte.
Prelucrarea fină este o etapă critică în procesul de turnare prin injecție, deoarece determină calitatea și precizia pieselor turnate. Este important să lucrați cu un furnizor de prelucrare care are experiență în prelucrarea fină a cavității matriței și a miezului pentru a vă asigura că prelucrarea este efectuată corect și conform specificațiilor corecte. Această etapă este, de asemenea, cea în care se adaugă sistemul de ejecție al matriței, canalele de răcire și alte caracteristici pentru a asigura funcționarea corectă a matriței.
Prelucrare EDM:
EDM (prelucrare prin descărcare electrică) este un proces utilizat pentru a realiza forme complicate și extrem de precise în piese metalice, inclusiv cele dintr-o matriță de injecție. Procesul utilizează scântei electrice pentru a îndepărta materialul de pe suprafața matriței, creând forma dorită. În continuare sunt prezentate principalele etape implicate în prelucrarea prin electroeroziune:
- Pregătirea suprafeței: Suprafața componentei matriței care urmează să fie prelucrată este curățată și lustruită pentru a îndepărta orice resturi sau rugozități reziduale.
- Configurarea EDM: Mașina EDM este configurată cu parametrii corecți, inclusiv distanța dintre scântei, durata impulsului și materialul electrodului, în funcție de materialul și forma componentei matriței.
- Eroziunea prin scântei: Mașina EDM produce scântei electrice care îndepărtează materialul din componenta matriței, creând forma dorită. Acest proces se realizează progresiv, mașina EDM erodând treptat materialul până la obținerea formei finale.
- Inspecția suprafeței: Suprafața prelucrată este inspectată pentru a se asigura că îndeplinește toleranțele și specificațiile necesare.
Prelucrarea prin EDM este adesea utilizată pentru componente de matrițe care au forme complexe sau detalii mici și complicate care sunt dificil de realizat cu alte procese de prelucrare. De asemenea, este utilizată pentru a produce marginile și colțurile ascuțite care sunt esențiale pentru buna funcționare a unei matrițe de injecție.
Procesul este extrem de precis și exact, ceea ce îl face ideal pentru producerea de piese turnate de înaltă calitate. Este important să lucrați cu un furnizor EDM care are experiență în prelucrarea EDM pentru matrițe de injecție pentru a vă asigura că procesul este realizat corect și conform specificațiilor corecte.
Șlefuirea suprafeței mucegaiului:
Lustruirea matrițelor de injecție este etapa finală în procesul de fabricare a matrițelor de injecție. Aceasta implică netezirea suprafețelor componentelor matriței pentru a se asigura că produsul finit are o suprafață netedă și uniformă. Următoarele sunt principalele etape implicate în lustruirea matrițelor de injecție:

șlefuirea matrițelor din plastic
- Pregătirea suprafeței: Suprafețele componentelor matriței sunt curățate și pregătite pentru lustruire. Orice asperități sau urme de prelucrare rămase sunt îndepărtate pentru a asigura o suprafață netedă pentru lustruire.
- Șlefuirea grosieră: Prima etapă a șlefuirii este șlefuirea grosieră, care implică îndepărtarea oricăror imperfecțiuni mari de pe suprafața componentelor matriței. Această etapă se realizează de obicei cu un abraziv cu granulație grosieră, cum ar fi un șmirghel sau o perie abrazivă.
- Șlefuirea fină: Șlefuirea fină este următoarea etapă, care implică netezirea suprafeței componentelor matriței până la un finisaj mai fin. Această etapă se realizează cu un abraziv cu granulație mai fină, cum ar fi un șmirghel mai fin sau o perie abrazivă.
- Șlefuirea: Șlefuirea este etapa finală a lustruirii, care implică utilizarea unei roți de șlefuire și a unui compus de lustruire pentru a obține un finisaj foarte lucios pe componentele matriței.
- Inspecție: După lustruire, componentele matriței sunt inspectate cu atenție pentru a se asigura că au o suprafață netedă și uniformă, fără zgârieturi, fisuri sau alte imperfecțiuni.
Șlefuirea matrițelor de injecție este importantă deoarece afectează calitatea produsului final. O matriță bine lustruită are ca rezultat un produs cu o suprafață netedă și uniformă, ceea ce este important pentru funcționalitatea și estetica produsului. Este important să lucrați cu un polizor de matrițe cu experiență pentru a vă asigura că componentele matriței sunt lustruite la specificațiile corecte și la nivelul de calitate dorit.
Racord de mucegai
Montarea matrițelor este un post specializat în domeniul turnării prin injecție și implică asamblarea, instalarea și testarea matrițelor de injecție. Ajustorii de matrițe sunt responsabili pentru asigurarea faptului că componentele matriței sunt asamblate și funcționează corect și că matrița produce piese cu standardele de calitate și performanță dorite. Unele dintre principalele responsabilități ale montatorilor de matrițe includ:
- Asamblarea componentelor matriței: Maeștrii de matrițe sunt responsabili pentru asamblarea diferitelor componente ale unei matrițe de injecție, inclusiv cavitatea și componentele de bază, sistemul de canal și orice componente auxiliare.
- Instalarea matriței pe mașina de montare a matriței: Moldmaster trebuie să fie capabil să monteze mucegaiul pe mașina de montare a mucegaiului într-un mod care să asigure alinierea și funcționarea corectă a mucegaiului, în cazul în care nu are nici o mașină de montare a mucegaiului, atunci utilizați modul manual de montare a mucegaiului, aceasta este cea mai mare parte a companiilor fac.
- Testarea matriței: Stăpânul matriței este responsabil de testarea matriței pentru a se asigura că aceasta produce piese cu standardele de calitate și performanță dorite. Aceasta include inspectarea pieselor pentru orice defecte, cum ar fi deformarea, contracția sau alte probleme de calitate.
- Reglarea matriței: În cazul în care se constată probleme în timpul fazei de testare, moldmaster este responsabil pentru efectuarea oricăror ajustări necesare la matriță pentru a se asigura că aceasta produce piese care îndeplinesc specificațiile dorite.
- Rezolvarea problemelor: Moldmaster trebuie să fie capabil să identifice și să rezolve orice probleme care pot apărea în timpul procesului de montare a matriței.
Posturile de montare a matrițelor necesită o combinație de cunoștințe tehnice, dexteritate manuală și atenție la detalii. Ajustorii de matrițe trebuie să fie capabili să lucreze cu o gamă largă de instrumente și utilaje, precum și să înțeleagă procesele complexe implicate în turnarea prin injecție. Este important ca ajustorii de matrițe să aibă o bună înțelegere a procesului de turnare prin injecție, precum și experiență de lucru cu diferite tipuri de matrițe și materiale.
Primul proces de turnare prin injecție sau fotografiere:
Încercarea de turnare prin injecție se referă la procesul de testare a matriței de injecție pentru a produce o piesă de probă folosind procesul de turnare prin injecție. Acest proces este o etapă critică în procesul de turnare prin injecție, deoarece permite producătorului să evalueze performanța matriței și să facă orice ajustări necesare înainte de a produce o cantitate mare de piese.
Procesul de fotografiere prin injecție implică de obicei următorii pași:
- Pregătire: Matrița este instalată pe mașina de turnare prin injecție și mașina este pregătită pentru injecție. Rezervorul este umplut cu rășină de plastic.
- Controlul temperaturii de topire: Temperatura de topire este controlată pentru a se asigura că rășina de plastic este încălzită la temperatura corectă pentru a produce piese de înaltă calitate.
- Injectare: Plasticul topit este injectat în matriță sub presiune ridicată. Presiunea este menținută până când matrița este umplută cu rășină plastică.
- Răcirea: Matrița este răcită pentru a solidifica rășina de plastic și a forma piesa. Timpul de răcire este determinat de tipul de rășină plastică utilizată și de dimensiunea și forma piesei produse.
- Ejectarea: Odată ce piesa este solidificată, aceasta este scoasă din matriță. Pinii de ejecție sunt utilizați pentru a împinge piesa afară din matriță.
- Inspecție: Partea produsă din matriță este inspectată cu atenție pentru a se asigura că îndeplinește specificațiile dorite și standardele de calitate.
- Ajustări: Dacă este necesar, pot fi efectuate ajustări ale procesului de turnare pentru a îmbunătăți performanța matriței și calitatea pieselor produse.
Procesul de testare a turnării prin injecție este o etapă importantă în procesul de turnare prin injecție, deoarece permite producătorului să evalueze performanța matriței și să facă orice ajustări necesare înainte de a produce o cantitate mare de piese. Acest proces ajută la asigurarea faptului că matrița produce piese de înaltă calitate cu specificațiile dorite.
Ambalarea matriței și gata pentru producție:
Odată ce matrița este complet finalizată de către producătorul de matrițe, următorul pas este producția de masă. Ambalarea matriței și pregătirea pentru producție este etapa finală în procesul de turnare prin injecție înainte de începerea producției în masă. Acest pas implică următoarele sarcini:
- Curățarea și întreținerea: Mucegaiul este curățat temeinic și inspectat pentru a se asigura că nu există resturi, murdărie sau deteriorări ale mucegaiului.
- Ambalare și depozitare: Matrița este ambalată cu grijă și depozitată într-un loc sigur pentru a preveni deteriorarea și pentru a se asigura că este gata de utilizare atunci când este necesar.
- Testarea și ajustarea: Matrița este testată pentru depistarea oricăror probleme, cum ar fi scurgeri, umplere necorespunzătoare sau ejecție necorespunzătoare a pieselor, și se fac toate ajustările necesare pentru a se asigura că matrița funcționează corect.
- Configurarea producției: Matrița este instalată în mașina de turnare prin injecție și toate setările necesare, cum ar fi temperatura, presiunea și viteza de injecție, sunt ajustate pentru a îndeplini cerințele specifice de producție.
- Începerea producției: Se produce primul lot de piese, iar procesul este monitorizat pentru a se asigura că piesele îndeplinesc specificațiile și standardele de calitate necesare. Se fac toate ajustările necesare pentru a optimiza procesul de producție și a asigura o calitate constantă.
În general, pregătirea matriței pentru producție este o etapă importantă în procesul de turnare prin injecție, care contribuie la asigurarea succesului și eficienței producției.
Informațiile de mai sus sunt proceduri pentru realizarea unei matrițe de injecție, poate că există unele lucruri mici ratate, dar majoritatea lucrurilor sunt de mai sus, după cum puteți vedea, realizarea unei matrițe de injecție nu este un caz ușor, dacă aveți un proiect de matriță de injecție în mâner, trebuie să găsiți un producător profesionist de matrițe de injecție pentru a vă servi, acest lucru vă va asigura că proiectul dvs. se desfășoară cu succes.
Sincere Tech este un profesionist China mucegai fabrică specializată în fabricarea de matrițe de injecție personalizate. Ei au experiență și expertiză în proiectarea, dezvoltarea și producția de matrițe de injecție de înaltă calitate pentru diverse industrii și aplicații.
Aceștia oferă o gamă largă de servicii, inclusiv proiectare de matrițe, prototipuri, producție de matrițe și procesare după matrițare, pentru a se asigura că clienții lor primesc cele mai bune rezultate posibile. Cu accent pe calitate, precizie și satisfacția clienților, Sincere Tech este un partener de încredere pentru toate nevoile dvs. de turnare prin injecție. Contactați-ne pentru a obține un preț e pentru proiectul dvs. acum.