Metoda Płynna guma silikonowa Formowanie
Kiedy mówimy o gumie silikonowej w postaci płynnej (LSR), jest to sieć podzielona na dwie części. W tej sieci długie łańcuchy polisiloksanu są wspierane przez krzemionkę. Część A zawiera katalizator platynowy, a część B zawiera wodorosiloksan metylu jako środek sieciujący i inhibitor alkoholu. Kauczuki silikonowe są kilkuczęściowymi polimerami i mogą zawierać wypełniacze w celu poprawy właściwości lub obniżenia kosztów. Kauczuk silikonowy jest w większości niereaktywny, stabilny i odporny na ekstremalne warunki i temperatury od -55 do 300 °C (-70 do 570 °F), zachowując jednocześnie swoje właściwości.
Definicja
Kiedy definiujemy kauczuk silikonowy w postaci płynnej, jest to polimer, który ma charakter nieorganiczny, zbudowany z krzemu (Si), tlenu (O), węgla (C) i wodoru (H). Niezwykle syntetyczny łańcuch, zwany kręgosłupem, jest otoczony krzemem i tlenem, zwanym siloksanem. Jest to silikon utwardzany platyną o wysokiej wartości i doskonałej gładkości. Jest on często wtryskiwany do silikonowej wnęki kształtowej w celu wytworzenia różnych części z dużą dokładnością. Ogólnie rzecz biorąc, płynna guma silikonowa ma niski zestaw kompresji, dobrą stabilność i odporność na ekstremalne temperatury. Materiał ten jest używany głównie do tworzenia uszczelek, membran uszczelniających, złączy elektrycznych, złączy wielostykowych, produktów dla niemowląt, w których wymagane są gładkie powierzchnie.
Nieorganiczna natura LSR czyni go idealnym do zastosowań medycznych i kontaktu ze skórą. LSR ma zdolność łączenia się z innymi grupami chemicznymi, co pozwala mu osiągnąć solidne parametry. LSR przewyższa wiele innych elastomerów i jest stosowany w przyciskach lub klawiaturach i jest preferowany do pompowania, szczególnie w kontakcie z płynami ustrojowymi lub substancjami chemicznymi.
Formowanie wtryskowe płynnej gumy silikonowej
Jest to bardzo zmechanizowany proces. Formowanie wtryskowe płynnego silikonu wykorzystuje mechaniczną metodę mieszania, która łączy ze sobą dwuskładnikowy utwardzany platyną materiał LSR, który wpływa do formy. Jednak ze względu na lepką naturę LSR, łatwo się przetwarza i doskonale nadaje się do produkcji wielkoseryjnej, stałej jakości części i zwiększonej wydajności. Narzędzie do wtrysku LSR jest umieszczone w specjalnej prasie do formowania wtryskowego LSR, która została specjalnie zaprojektowana do precyzyjnej kontroli wielkości wtrysku i umożliwia spójną produkcję elementów z płynnej gumy silikonowej. Ze względu na swoje właściwości i przetwarzalność, ciekła guma silikonowa stała się idealnym materiałem do skomplikowanych elementów konstrukcyjnych i wymagających zastosowań krytycznych.
Proces formowania wtryskowego LSR
Proces ten ma charakter termoutwardzalny i jest wykorzystywany do produkcji elastycznych, trwałych i odpornych na ciepło części i produktów silikonowych. W tym procesie mieszane są dwa związki, które zazwyczaj składają się z silikonu bazowego i katalizatora platynowego. Następnie mieszanina jest wtryskiwana i utwardzana termicznie wewnątrz formy, tworząc elastyczne części silikonowe. Jednak te dwa związki wymagają intensywnego mieszania dystrybucyjnego przy jednoczesnym utrzymywaniu ich w niskiej temperaturze przed wepchnięciem ich do ogrzewanej wnęki. Ciekła guma silikonowa jest utwardzana pod wpływem ciepła, tworząc stałe części lub produkty.
Proces ten jest szeroko stosowany w różnych gałęziach przemysłu, w tym w przemyśle motoryzacyjnym, medycznym, dóbr konsumpcyjnych i elektronicznym. Proces formowania wtryskowego LSR składa się głównie z następujących głównych etapów.
1. przygotowanie materiału
Związki LSR: LSR to dwuskładnikowy związek zwykle określany jako materiał bazowy i katalizator, który zazwyczaj jest oparty na platynie. Części te są mieszane w stosunku 1:1 i mogą zawierać dodatkowe składniki, takie jak pigmenty lub dodatki.
Przechowywanie i obsługa: Komponenty LSR są przechowywane w pojemnikach lub nabojach. W jednym pojemniku znajduje się materiał bazowy, a w drugim katalizator, zazwyczaj na bazie platyny. Właściwa obsługa jest bardzo ważna, aby zapobiec zanieczyszczeniu i zapewnić spójne właściwości materiału.
2. Mieszanie i dozowanie
Jednostka mieszająca: Specjalistyczna jednostka mieszająca dokładnie łączy oba związki. Jednostka ta może również zawierać pigmenty lub inne dodatki zgodnie z wymaganiami.
Mikser statyczny: Wymieszany LSR przechodzi następnie przez mieszalnik statyczny, zapewniając dokładną homogenizację składników. Ten etap jest niezbędny do zapewnienia spójnego utwardzania i właściwości produktu końcowego.
Pomiar: Na tym ważnym etapie zmieszany LSR jest dozowany do jednostki wtryskowej. Precyzyjne dozowanie jest niezbędne do utrzymania stałych rozmiarów wtrysku i ograniczenia strat materiału.
3. Maszyna do formowania wtryskowego
- Jednostka wtryskowa: Jednostka wtryskowa została specjalnie zaprojektowana do wtrysku LSR. LSR ma niską lepkość i wymaga specjalnej konstrukcji ślimaka. Na tym etapie materiał jest wpychany do gniazda formy.
- Jednostka zaciskowa: Na tym etapie zacisk jest używany do przytrzymywania formy i utrzymywania jej w pobliżu podczas wtrysku. Niemniej jednak wymagana moc zależy od rozmiaru i złożoności części.
4. Konstrukcja formy
- Uwagi dotyczące materiałów: Formy do LSR powinny być przeznaczone do wytrzymywania wysokich temperatur i naprężeń stosowanych podczas utwardzania. Najczęściej są one produkowane z doskonałej jakości stali lub aluminium.
- Wnęka i rdzeń: Silikonowa forma wtryskowa składa się z wnęk, które są negatywnymi kształtami części i rdzeni, które są pozytywnymi kształtami części. Powinny one być precyzyjnie obrobione, aby uzyskać idealne aspekty części i wykończenie powierzchni.
- Wentylacja: Powietrze jest uwięzione i musi zostać uwolnione, aby uniknąć wad, takich jak pęcherzyki powietrza lub puste przestrzenie w produkcie końcowym. Dlatego ważne jest zapewnienie odpowiedniego odpowietrzenia.
- System wyrzutnika: Ten etap obejmuje usunięcie części z formy, która jest utwardzana. System wyrzucania musi być starannie zaprojektowany, aby poradzić sobie z elastycznymi i lepkimi częściami LSR.
5. Wtrysk i utwardzanie
- Proces wtrysku: Forma jest mocno zamykana i zaciskana z odpowiednią siłą. LSR jest następnie wtryskiwany do wnęk formy z dużą prędkością. Następnie forma jest wypełniana, po czym nadmiar materiału jest usuwany.
- Proces utwardzania: Temperatura jest utrzymywana na wysokim poziomie (zwykle między 160-200°C), aby rozpocząć proces utwardzania. Czas utwardzania zależy od grubości i kształtu części. Z reguły wynosi on od kilku sekund do wielu minut.
6. Rozkładanie
- Chłodzenie: Po zakończeniu utwardzania, forma jest schładzana w celu usunięcia części i uniknięcia deformacji.
- Otwarcie: Następnie forma jest delikatnie otwierana, aby zapobiec uszkodzeniu delikatnych części LSR.
- Wyrzucanie: Na tym etapie części są wyrzucane z formy za pomocą systemu wyrzutników. Konieczne jest ostrożne obchodzenie się z częściami, ponieważ są one nadal ciepłe i mogą być nieco giętkie.
7. Przetwarzanie końcowe
- Inspekcja: Na tym etapie każda część jest sprawdzana pod kątem wad, takich jak wypływki, pęcherzyki powietrza lub niepełne wypełnienie. Można stosować zarówno zautomatyzowane, jak i ręczne metody kontroli.
- Przycinanie: Następnie nadmiar materiału, znany jako flash, jest przycinany z części. Można to zrobić ręcznie lub za pomocą zautomatyzowanego sprzętu.
- Operacje dodatkowe: Dodatkowe procesy, takie jak klejenie, montaż lub obróbka powierzchni, mogą być wykonywane w zależności od zastosowania i wymagań.
8. Kontrola jakości
- Testowanie: Aby zagwarantować, że dostarczane części spełniają niezbędne specyfikacje, przechodzą one różne testy. Testy te obejmują badania właściwości mechanicznych, kontrole wymiarów i badania wizualne.
- Dokumentacja: Szczegółowa dokumentacja procesu formowania, partii materiałów i wyników kontroli jakości jest regularnie prowadzona w celu zapewnienia identyfikowalności i zgodności z normami branżowymi.
9. Pakowanie i wysyłka
- Opakowanie: Gotowe części są następnie starannie pakowane, aby zabezpieczyć je podczas transportu. Techniki pakowania zmieniają się w zależności od rozmiaru, kształtu i wrażliwości części.
- Wysyłka: Zapakowane części są następnie wysyłane do klientów lub do zakładów dalszego przetwarzania, zapewniając terminową dostawę i zachowanie integralności części.
Zalety formowania wtryskowego LSR
Proces ten oferuje kilka głównych zalet, które są następujące:
1. precyzja i spójność
Formowanie wtryskowe LSR zapewnia wysoką spójność i precyzję w produkcji skomplikowanych, złożonych i szczegółowych części. Proces ten pozwala na wąskie tolerancje i dokładną replikację form, zapewniając jednorodność we wszystkich partiach.
2. szeroki zakres zastosowań
Oferuje to wiele zastosowań, ponieważ jest elastyczny i może być wykorzystywany w różnych branżach, w tym motoryzacyjnej, klinicznej, sprzętowej, produktów konsumenckich i wielu innych. Elastyczność, jaką zapewnia LSR, sprawia, że nadaje się on do produkcji wszystkiego, od implantów medycznych, przez uszczelki samochodowe, po komponenty elektroniki użytkowej.
3. trwałość i wytrzymałość
Części te wyróżniają się solidnością i wytrzymałością. Mogą wytrzymać ekstremalne temperatury, surowe związki syntetyczne i długotrwałą ekspozycję na promieniowanie UV bez osłabiania ich integralnych właściwości przez długi czas, co czyni je idealnymi do wielu zastosowań.
4. biokompatybilność
Materiały te są biokompatybilne i spełniają wymogi norm medycznych. Jakość ta sprawia, że są one odpowiednie do zastosowań klinicznych i medycznych, takich jak implanty, narzędzia chirurgiczne i gadżety kliniczne do noszenia. Ponadto są hipoalergiczne i bezpieczne w przypadku długotrwałego kontaktu ze skórą.
5. odporność chemiczna
Materiały te wykazują doskonałą ochronę przed wieloma substancjami syntetycznymi, w tym rozpuszczalnikami, olejami i środkami czyszczącymi. Ta właściwość sprawia, że są one odpowiednie do stosowania w warunkach, w których narażenie na substancje chemiczne jest normalne, takich jak motoryzacja i nowoczesne środowiska przemysłowe.
6. Elastyczność i sprężystość
Części te charakteryzują się niezwykłą sprężystością i elastycznością, dzięki czemu można je odkształcać i przywracać ich unikalny kształt bez długotrwałego odkształcania. Ta zdolność adaptacji sprawia, że idealnie nadają się do uszczelnień i uszczelek, w których wymagane jest szczelne, solidne uszczelnienie.
7. Krótkie czasy cyklu
Metoda ta oferuje krótki czas procesu w porównaniu do konwencjonalnych metod formowania gumy. Pozwala to na wysoką produkcję przy krótkim czasie realizacji, a jednocześnie jest opłacalne.
8.Zmniejszona ilość odpadów
Formowanie wtryskowe LSR generuje minimalną ilość odpadów w porównaniu z innymi procesami produkcyjnymi. Zdolność do precyzyjnej kontroli przepływu materiału i optymalizacji projektów form minimalizuje ilość odpadów materiałowych. W konsekwencji prowadzi to do oszczędności kosztów i korzyści dla środowiska.
9.Swoboda projektowania
Proces ten umożliwia opracowywanie skomplikowanych kształtów i złożonych geometrii, które mogą być trudne do osiągnięcia przy użyciu innych metod produkcji. Ta swoboda projektowania pozwala na tworzenie fantazyjnych projektów przedmiotów i dokonywanie wyborów w zakresie personalizacji.
10. wykończenie powierzchni
Części te mają gładkie i nieskazitelne wykończenie powierzchni bezpośrednio po wyjęciu z formy. W rezultacie zmniejsza to zapotrzebowanie na jakiekolwiek dodatkowe czynności wykończeniowe, takie jak czyszczenie lub malowanie. Oszczędza to czas i koszty pracy, czyniąc proces efektywnym kosztowo, przy jednoczesnym zapewnieniu wysokiej jakości produktu końcowego.
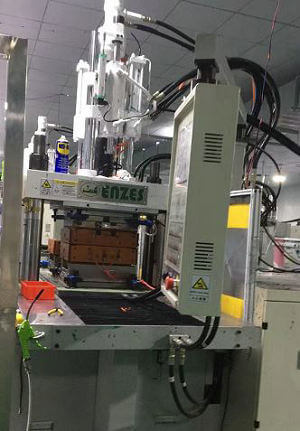
maszyny do formowania wtryskowego silikonu
Ograniczenia formowania płynnej gumy silikonowej
Proces ten oferuje różne korzyści, jednak jak każdy proces produkcyjny, ma pewne ograniczenia, które są następujące:
1. wysoka inwestycja początkowa
Podczas konfigurowania procesu formowania wtryskowego LSR wymagane są znaczne inwestycje początkowe, głównie w specjalistyczny sprzęt, formy i infrastrukturę. Dlatego może to stanowić barierę dla małych producentów lub tych z ograniczonym kapitałem.
2. kompleksowy projekt formy
Formy LSR są wyspecjalizowane, skomplikowane i złożone ze względu na niską lepkość materiału i wysoką temperaturę utwardzania. Projektowanie tych form wymaga więc specjalistycznej wiedzy i precyzji, co może zwiększyć koszty i czas realizacji.
3.Ograniczone opcje materiałowe
Chociaż LSR zapewnia doskonałe właściwości, takie jak elastyczność, odporność na ciepło i biokompatybilność, jego opcje materiałowe są nieco ograniczone w porównaniu z innymi rodzajami gumy. W konsekwencji może to ograniczać zakres zastosowań, w których LSR może być efektywnie wykorzystywany.
4. czas utwardzania
Czas utwardzania LSR może być dłuższy w porównaniu z innymi metodami formowania gumy. Może to mieć wpływ na cykl produkcyjny i całkowitą wydajność, szczególnie w przypadku produkcji wielkoseryjnej.
Aplikacje
Jest to unikalny proces z dużą liczbą zastosowań w różnych przedsięwzięciach ze względu na jego nowatorskie właściwości i korzyści. Główne zastosowania są następujące:
1. urządzenia medyczne
Jest szeroko i powszechnie wykorzystywany w branży klinicznej do produkcji różnych gadżetów i części, takich jak cewniki, rurki, uszczelki, uszczelnienia, zasłony oddechowe i gadżety do implantacji. Właściwości takie jak biokompatybilność, sterylność i wytrzymałość sprawiają, że jest on odpowiedni do zastosowań wymagających dokładności i niezachwianej jakości w warunkach klinicznych.
2. produkty do pielęgnacji niemowląt
Ze względu na swoje bezpieczeństwo, zdolność adaptacji i prostotę sterylizacji LSR jest zwykle wykorzystywany do tworzenia artykułów do pielęgnacji dzieci, takich jak smoczki, osłonki na butelki i przybory do pielęgnacji dzieci. Przedmioty te często wymagają materiałów, które powinny mieć właściwości nieszkodliwe, hipoalergiczne i nieprzepuszczalne dla wysokich temperatur, z których wszystkie zapewnia LSR.
3.Elektronika
Jest on dodatkowo wykorzystywany w sprzęcie do hermetyzacji i ochrony wrażliwych części przed wilgocią, kurzem i innymi zmiennymi ekologicznymi. Jest wykorzystywany w aplikacjach takich jak klawiatury, uszczelki, uszczelnienia, złącza i osłony ochronne ze względu na jego niesamowite właściwości ochrony elektrycznej, stabilność termiczną i ochronę przed niebezpiecznymi związkami chemicznymi.
4.Konfiguracje motoryzacyjne
Jest szeroko stosowany w zastosowaniach motoryzacyjnych do dostarczania części, takich jak uszczelki, uszczelnienia, złącza i tłumiki drgań. Jego ochrona przed ekstremalnymi temperaturami, olejami i substancjami syntetycznymi czyni go idealnym do zastosowań silnikowych i części zewnętrznych, w których wytrzymałość i niezawodność mają pierwszorzędne znaczenie.
5.Pozycje konsumenckie
Ze względu na swoje właściwości spożywcze, zdolność do adaptacji i ochronę przed wysokimi temperaturami, jest on dodatkowo wykorzystywany w różnych przedmiotach kupujących, takich jak naczynia kuchenne, naczynia do pieczenia, uszczelki i materiały do użytku na zewnątrz. Jego zdolność do wytrzymywania powtarzających się cykli ogrzewania i chłodzenia sprawia, że jest on odpowiedni dla przedmiotów wymagających ciągłego użytkowania i mycia.
6. zastosowania przemysłowe
Znajduje również zastosowanie w nowoczesnych rozwiązaniach do produkcji uszczelnień, uszczelek, o-ringów i innych części, w których ochrona przed ekstremalnymi temperaturami, materiałami syntetycznymi i zmiennymi czynnikami ekologicznymi jest koniecznością. Jego wytrzymałość, niezawodność i długoterminowa wydajność sprawiają, że jest idealny do nowoczesnych zastosowań.
7.Aerospace
W branży lotniczej LSR jest zwykle wykorzystywany do tworzenia uszczelnień, uszczelek, złączy i innych podstawowych części, w których wymagane są lekkie materiały o elitarnej wysokiej wydajności. Jego właściwości, takie jak ochrona przed wysokimi temperaturami, promieniowaniem i związkami syntetycznymi, sprawiają, że jest odpowiedni do zastosowań lotniczych, w których niezachwiana jakość i bezpieczeństwo mają kluczowe znaczenie.
8. oświetlenie LED
Znajduje również zastosowanie w oświetleniu LED, poprawiając jego ekspozycję, solidność i żywotność. Właściwości takie jak przezroczystość, stabilność termiczna i odporność na promieniowanie UV sprawiają, że jest to dobry materiał do ochrony części LED przed wilgocią, kurzem i innymi elementami ekologicznymi.
9. wojsko i obrona
Jest on wykorzystywany w zastosowaniach wojskowych do produkcji uszczelnień, uszczelek, złączy i różnych części, które wymagają dominującej wydajności w ekstremalnych warunkach. Elementy wyprodukowane przy jego użyciu zapewniają niezwykłą wydajność w trudnych warunkach, takich jak wysokie temperatury, wilgotność i otwartość na związki syntetyczne i paliwa.
Wniosek
Proces formowanie wtryskowe Kauczuk silikonowy w postaci płynnej wyróżnia się jako elitarna technika dostarczania części silikonowych z wysoką dokładnością. Jest to elastyczny i wydajny proces produkcyjny, który oferuje różne korzyści w porównaniu z innymi metodami. Elastyczność projektu, wysoka dokładność i spójność w połączeniu z wrodzonymi właściwościami materiału sprawiają, że jest on idealny do wielu zastosowań w różnych firmach. Dzięki postępowi innowacji procedura ta stale się rozwija i ulepsza, oferując znacznie większy potencjał rozwoju i ulepszania produktów w wielu obszarach.