Ważny przemysł produkcji form - Chiny
Chińskie firmy produkujące formy wtryskowe stoją obecnie w obliczu silnej presji ze względu na wysoką konkurencyjność firm zajmujących się formowaniem wtryskowym z Indii i Wietnamu. Powód silnej presji na chińskie firmy zajmujące się formowaniem wtryskowym tworzyw sztucznych został szczegółowo opisany poniżej.
- Wiele firm produkujących formy wtryskowe do tworzyw sztucznych znajduje się w Indiach i Wietnamie, co przyczyni się do zwiększenia udziału Chin w rynku produkcji form.
- Inflacja spowodowała, że chińskie firmy zajmujące się produkcją form od czasu wojny musiały ponosić wyższe koszty materiałów, takich jak stal formierska i inne materiały, zwłaszcza miedź. Dodatkowo spowodowało to znaczny wzrost wynagrodzeń. Od 2009 do 2011 roku ogólna pensja wzrosła o 40%, ale nie rosła bardziej z roku na rok.
- Ze względu na globalną recesję gospodarczą, wiele chińskich firm zajmujących się formowaniem doświadczyło spadku zamówień. Dlatego też, gdy wymagane jest jakiekolwiek zamówienie, wszystkie konkurują ze sobą ceną formy, co prowadzi do ciągłego spadku ceny. W międzyczasie nie mogą zagwarantować jakości formy.
Producent form w Chinach jest jednym z najważniejszych producentów form na świecie. Chiny są domem dla różnych kategorii producenci form, A to zwykle stanowi wyzwanie dla każdego, kto szuka producenta form w kraju. Wielu kupujących po raz pierwszy jest często zdumionych samą dostępnością producentów form, ale wkrótce zdają sobie sprawę, że powinni byli poświęcić więcej czasu na wybór najbardziej odpowiedniego i odpowiedniego producenta form.
W większości krajów rozwiniętych, takich jak Wielka Brytania, Ameryka czy Japonia, stosunkowo łatwo jest znaleźć godny zaufania sklep z formami. Oczywiście cena jest bardzo wysoka, ale w Chinach sprawa wygląda zupełnie inaczej. Wynika to z faktu, że wielu producentów form w tym kraju nie produkuje form wysokiej jakości. Zamiast tego wielu z tych producentów form zazwyczaj produkuje formy niskiej jakości, które przede wszystkim zaspokajają potrzeby lokalnego rynku.

Zalety Forma porcelanowa
Jak wspomniano powyżej, wyjaśniliśmy, że chińskie firmy zajmujące się produkcją form stoją w obliczu presji związanej z wytwarzaniem form, ale w porównaniu z formami indyjskimi i wietnamskimi, chińskie formy nadal mają swoje zalety. Oczywiście zalety te nie są tak duże, jak 10 lat temu. Ale nawet dziś wiele indyjskich firm nadal kupuje chińskie formy do swoich indyjskich produktów. firmy zajmujące się formowaniem wtryskowym tworzyw sztucznych.
Prosta informacja, którą otrzymałem od jednego z moich indyjskich klientów (który pracuje dla dużej firmy zajmującej się formowaniem wtryskowym tworzyw sztucznych w Indiach) jest taka, że Hindusi nie potrafią wykonać dobrej jakości plastikowej formy wtryskowej; jeśli mają jakieś drobne problemy, będą trzymać się projektu i nie zrobią nic, aby rozwiązać problem. Z drugiej strony, indyjskie formy wtryskowe mają duże problemy z jakością i czasem realizacji.
Oto kilka zalet korzystania z chińskich form:
Jeśli szukasz plastikowych form wtryskowych do swojego projektu, jaka jest najbardziej opłacalna opcja? Pod względem jakości i czasu realizacji, chińska forma okaże się najbardziej opłacalną opcją. Wyjazd do Chin w celu wykonania formy może początkowo wydawać się nieco zniechęcający, ale czytając dalej ten artykuł, zrozumiesz, dlaczego większość ludzi wybiera tę opcję. Oto kilka powodów, dla których ludzie kupują formy wtryskowe z Chin:

Koszty są niższe niż w USA i Europie.
Koszty produkcji dla chińskiego producenta form są znacznie niższe niż w przypadku zamówienia formy w USA lub Europie. Wynika to przede wszystkim z różnic ekonomicznych - zwłaszcza niższych kosztów pracy w Chinach. Nie jest to powód do zmartwień, ponieważ jest to dość związane z kosztami życia i porównywalne z kosztami pracy w wielu branżach.
Jakość jest dobra.
Ponieważ Chiny mają tak duży krajobraz przemysłowy, specjalizują się w formach z tworzyw sztucznych i innych produktach przemysłowych. Możesz wybierać spośród wielu chińskich fabryk form, z których wszystkie mają duże doświadczenie w produkcji wysokiej jakości form.
Łatwy do zorganizowania.
Korzystając z Internetu, bardzo łatwo jest komunikować się bezpośrednio z chińskimi producentami form plastikowych. Ponieważ są oni przyzwyczajeni do kontaktów z USA, można łatwo znaleźć przedstawiciela, który mówi po angielsku, i można z nim pracować w tę i z powrotem, aż do uzyskania satysfakcji.
Personalizacja
Chińscy producenci form mogą produkować niestandardowe formy zgodnie z określonymi wymaganiami, standardami form, takimi jak DME, HASCO i tak dalej, co zapewnia, że otrzymasz formę, która dokładnie spełnia Twoje potrzeby.
Duża zdolność produkcyjna
Dzięki ogromnej puli wykwalifikowanej siły roboczej i najnowocześniejszym zakładom produkcyjnym Chiny mają duże zdolności produkcyjne w zakresie form wtryskowych. Oznacza to, że mogą produkować formy w dużych ilościach i szybko je dostarczać.
Szeroki zakres materiałów
Chińscy producenci form mogą produkować formy z szerokiej gamy materiałów, w tym tworzyw sztucznych, metalu i materiałów kompozytowych.
Biorąc pod uwagę wszystko, co wspomniano powyżej, jeśli rozważasz zatrudnienie chińskiego producenta form do pomocy w zadaniach związanych z produkcją, powinieneś wziąć pod uwagę kilka kluczowych czynników, aby zapewnić pomyślny wynik. Na przykład, jasno określ konkretne cele, które masz nadzieję osiągnąć z pomocą renomowanej firmy. Może to być precyzja lub jakakolwiek inna ważna rzecz, która pomoże usprawnić działania produkcyjne. Precyzja gwarantuje, że dane zadanie zostanie wykonane dokładnie zgodnie z instrukcjami.
Oprócz wyżej wymienionych wymagań, należy również poważnie rozważyć wymagania tego wysoce konkurencyjnego sektora przemysłowego. Po uwzględnieniu nowych osiągnięć technologicznych, punktualność odgrywa kluczową rolę w zapewnieniu sprawnego przebiegu produkcji towarów. Mówiąc prościej, im szybciej otrzymasz zamówione części z tworzyw sztucznych, tym szybciej możesz zakończyć produkcję, osiągając w ten sposób bardzo potrzebną efektywność kosztową.
Powinieneś również poświęcić trochę czasu na zapoznanie się ze wszystkimi istotnymi usługami formowania tworzyw sztucznych związanymi z Twoją działalnością produkcyjną. Pomoże to podjąć właściwe decyzje i zacząć czerpać korzyści z globalnych operacji. Najlepsze miejsce narzędzia do wtrysku tworzyw sztucznych jest w Chiny; W związku z tym należy o tym pamiętać, szukając współpracy z dowolnym Chińska firma produkująca formy. Montaż i wykończenie powinny być wykonywane później, w Meksyku. Mówiąc prościej, zalecenia te biorą pod uwagę podstawowe wymagania, którymi są efektywność kosztowa i szybkość.
Równie ważne jest, aby pamiętać, że najlepsza globalna firma powinna mieć doświadczenie w pracy z różnymi globalnymi klientami. Ma to kluczowe znaczenie, ponieważ zapewnia płynną dostawę wszystkich form z tworzyw sztucznych do dowolnej lokalizacji na świecie. Ogólnie rzecz biorąc, aby odnieść sukces w produkcji, należy podążać za pojawiającymi się trendami.
Następnym razem, gdy będziesz potrzebować form wtryskowych do tworzyw sztucznych, upewnij się, że współpracujesz wyłącznie z firmami, które posiadają kompleksowe zrozumienie globalnych operacji. Jest to ważne, ponieważ pomoże również znacznie ułatwić plany globalnej ekspansji.
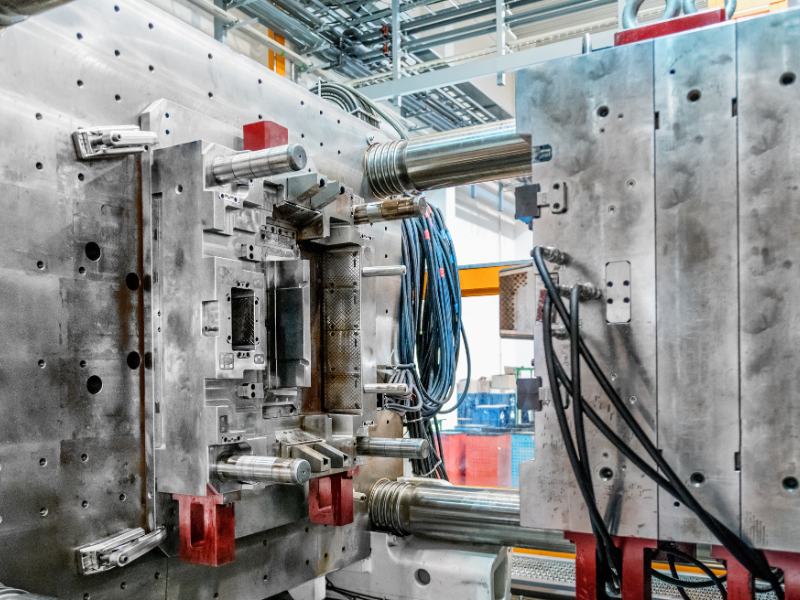
Jak pozyskać formy od chińskiego producenta form?
Proces ten jest o wiele łatwiejszy, niż mogłoby się wydawać. Chińskich producentów form można znaleźć w Internecie, wyszukując lub szukając rekomendacji od innych osób. Następnie można nawiązać kontakt i rozpocząć negocjacje warunków. Zwykle można zlecić sporządzenie planów w USA i wysłać je do przeglądu lub pracować nad nimi bezpośrednio z dostawcami form w Chinach.
Oto kilka kroków do pozyskiwania form z Chin:
- Określenie specyfikacji formy: Określ rodzaj potrzebnej formy, w tym jej rozmiar, materiał i inne specyfikacje. Powinieneś także mieć pojęcie o swoim budżecie i wielkości produkcji.
- Zbadaj i wybierz potencjalnych dostawców form w Chinach: Skorzystaj z katalogów online, targów handlowych, poleceń, badań online i stowarzyszeń branżowych, aby zidentyfikować potencjalnych dostawców form w Chinach. Oceń dostawców na podstawie ich doświadczenia, reputacji i zdolności do spełnienia określonych wymagań.
- Skontaktuj się z chińskimi producentami form: Skontaktuj się z chińskimi producentami form i prześlij im swoje specyfikacje. Poproś o wycenę od każdego dostawcy i poproś o próbki, referencje i certyfikaty.
- Ocena ofert i próbek: Oceń oferty i próbki od każdego dostawcy i porównaj je z budżetem i specyfikacjami. Należy również wziąć pod uwagę takie czynniki, jak czas realizacji zamówienia przez dostawcę, warunki płatności i procesy kontroli jakości.
- Negocjuj i sfinalizuj umowę: Po wybraniu dostawcy negocjuj warunki umowy, w tym warunki płatności, czas realizacji i kontrolę jakości. Upewnij się, że umowa zawiera szczegóły, takie jak zakres prac, specyfikacje i terminy dostaw.
- Monitorowanie produkcji i kontrola jakości: Należy ściśle monitorować proces produkcji, aby upewnić się, że forma jest produkowana zgodnie ze specyfikacjami. Można również zatrudnić zewnętrzną firmę kontroli jakości do sprawdzenia formy przed wysyłką.
- Odbiór i kontrola formy: Gdy forma jest już gotowa, należy ją odebrać i dokładnie sprawdzić, aby upewnić się, że spełnia ona wymagania klienta. Przetestuj formę, aby upewnić się, że produkuje wysokiej jakości części.
Jeśli jest to nowy projekt, zawsze należy wykonać kilka prototypów przed zamówieniem form. Gdy będziesz zadowolony z prototypu, możesz zacząć zamawiać formy i czekać na dostawę. Pomimo pakowania i wysyłki, koszt będzie znacznie niższy niż w USA czy Europie.
Sincere Tech jest jednym z 10 najlepszych producenci form w Chinach. Oferujemy niestandardowy plastik i części do formowania wtryskowego tworzyw sztucznych na cały świat. Mamy klientów z Niemiec, Kanady, Ameryki, Hiszpanii, Tajlandii, Litwy itp.
Szukasz profesjonalnego i długiego partnera Chiński producent form?
SINCERE TECH jest jedną z 10 najlepszych firm produkujących formy wtryskowe z tworzyw sztucznych w Chinach, która oferuje Usługa formowania wtryskowego do różnych krajów na świecie z najlepszą jakością i Doskonałe usługi posprzedażowe. Firma, która jest znana z bycia liderem na rynku Chiński producent formz całym swoim poświęceniem opracowała i wyprodukowała odmiany części formowane wtryskowo. Optymalna obsługa, wiodący sprzęt i zaawansowana technologia są cennymi przyczynami sukcesu firmy.
Sincere tech optymalizuje projekt w oparciu o wymagania klienta i jest bardzo uważny podczas projektowania formy, ponieważ może zaoszczędzić pieniądze, skracając czas przetwarzania i naprawy formy dla swoich klientów.
Zespół projektantów form plastikowych w firmie składa się z 15 ekspertów, którzy wykonują w pełni kompletny projekt formy, czterech inżynierów, którzy sprawdzają projekt formy oraz dwóch kierowników technicznych, którzy weryfikują strukturę formy przed jej wyprodukowaniem. Zespół ten jest biegły w obsłudze oprogramowania UG i PRO-E z pełnym zaangażowaniem.
Inżynierowie firmy specjalizują się w danym produkcie, dzięki czemu mogą zapewnić swoim klientom wartościowe sugestie i wsparcie techniczne. Inżynierowie projektowi oferują DFM (projektowanie pod kątem możliwości produkcyjnych) w ciągu dwóch dni roboczych, a w ciągu pięciu dni dostarczają klientom w pełni uformowane projekty.
Rozwój form wtryskowych z doskonałym projektem i najlepsze technologie przetwarzania form wtryskowych z ciągłą pracą są ich kluczem do sukcesu. Doskonały nacisk kładziony na projektowanie, zaawansowane urządzenia robocze i idealne systemy przetwarzania zapewniają klientom większą satysfakcję.
Firma Sincere Tech uruchomiła trzy automatyczne linie produkcyjne do obróbki powierzchni i warsztaty, które są pyłoszczelne i są używane do teksturowania powierzchni, natryskiwania powierzchni, IMD itp. Zapewniają swoim klientom usługi produkcji form wtryskowych i formowania wtryskowego po niskich kosztach, których nie mogliby zapewnić ich konkurenci. Jeśli szukasz formy wtryskowej lub partnera do formowania wtryskowego w Chinach aby wesprzeć swoją firmę, możesz skontaktować się z naszym zespołem, a my odpowiemy w ciągu dwóch dni roboczych.
Mamy ponad 18 lat bogatego doświadczenia zawodowego oraz 15 lat wykwalifikowanej komunikacji w języku angielskim technicznym.
Dobra cena, dobra jakość i dobra obsługa to nasze założenia.
Gwarantujemy, że Twój projekt zakończy się sukcesem, spójrz na poniższe zdjęcie, co mówią nasi zadowoleni klienci.
Czy jesteś gotowy, aby rozpocząć projekt formy z chińskim producentem form teraz?
Wyślij nam swoje wymagania dotyczące wyceny, nic nie stracisz, ale otrzymasz konkurencyjną cenę formy wtryskowej w Chinach. Sprawdź poniżej, co mówi zadowolony klient
