Czym jest forma wtryskowa?
Forma wtryskowa to narzędzie używane w procesie formowania wtryskowego do produkcji części poprzez wtryskiwanie materiału do gniazda formy. Zazwyczaj jest ono wykonane ze stali (H13, P20, 1.2312, 1.2344, S136H itp.) lub aluminium i jest starannie zaprojektowane, aby pasowało do kształtu i specyfikacji produktu końcowego.
Forma wtryskowa jest podzielona na dwie połówki, które są połową wnęki i połową rdzenia, są one zaciśnięte razem podczas procesu formowania, a materiał jest wtryskiwany przez wlew do wnęki formy, gdzie stygnie i zestala się w pożądany kształt. Po uformowaniu części forma otwiera się i część jest wyrzucana. Forma może być ponownie użyta do produkcji wielu części.

Czym jest formowanie wtryskowe
Rodzaje form wtryskowych
Wśród wielu odmian form wtryskowych można znaleźć:
Forma specyficzna dla jamy
Każdy cykl procesu formowania wtryskowego może wygenerować tylko jedną część przy użyciu formy jednogniazdowej. Proces tworzenia części za pomocą tej formy jest tak prosty, jak wstrzyknięcie do niej żywicy z tworzywa sztucznego, odczekanie, aż ostygnie, a następnie usunięcie gotowego produktu.
Porównując koszty produkcji form wielostrzałowych z formami jednogniazdowymi, te pierwsze są zwykle bardziej przystępne cenowo. W przypadku, gdy produkcja niewielkiej liczby komponentów na raz byłaby zbyt kosztowna, są one idealnym rozwiązaniem do prototypowania i produkcji małoseryjnej.

Forma jednogniazdowa
Zalety form jednostrzałowych obejmują:
- Efektywność pod względem kosztów: produkcja formy jednostrzałowej jest często tańsza niż produkcja formy wielostrzałowej.
- Prosta konstrukcja: Łatwość produkcji i konserwacji dzięki prostocie konstrukcji: Formy jednostrzałowe są często mniej skomplikowane pod względem układu niż formy wielostrzałowe.
- Elastyczność: Szeroka gama zastosowań, takich jak prototypowanie i produkcja małoseryjna, nadaje się do wykorzystania form jednogniazdowych.
Wady form jednostrzałowych obejmują:
- Ograniczona produkcja: To ograniczenie sprawia, że formy jednogniazdowe nie nadają się do produkcji wielkoseryjnej, ponieważ są w stanie wyprodukować tylko jedną część w każdym cyklu.
- Złożone części: Formy jednogniazdowe nie nadają się do tworzenia skomplikowanych części z wieloma częściami; w takim przypadku potrzebna jest forma wielogniazdowa lub forma rodzinna.
- Nieefektywność: W porównaniu z formami wielogniazdowymi, formy jednostrzałowe są mniej wydajne, ponieważ mogą tworzyć tylko jedną część podczas każdego cyklu ze względu na ich ograniczoną pojemność.
Formy wielokomorowe:
Formy wielogniazdowe to rodzaj form wtryskowych, które mają więcej niż jedno gniazdo. Pozwala to procesowi formowania wtryskowego wykonać więcej niż jedną część podczas każdego obrotu. W zależności od potrzeb aplikacji, formy te mogą być wykonane z takimi samymi lub różnymi otworami.
Ze względu na możliwość tworzenia wielu części w jednym cyklu, formy wielokomorowe są zazwyczaj wykorzystywane do formowanie wtryskowe wielkoseryjne serii produkcyjnych. Ta funkcja pozwala im zwiększyć wydajność produkcji, jednocześnie obniżając koszt pojedynczej części.

forma wielogniazdowa
Zalety form wielokomorowych obejmują:
- Produkcja wielkoseryjna: Formy wielogniazdowe są przeznaczone do produkcji wielkoseryjnej, co ułatwia wytwarzanie dużej liczby części.
- Opłacalność: formy wielogniazdowe są zwykle tańsze niż formy jednogniazdowe, ponieważ mogą wytwarzać więcej części w jednym cyklu.
- Złożone części: Formy wielogniazdowe mogą być wykorzystywane do produkcji skomplikowanych części składających się z wielu elementów.
Wady form wielokomorowych obejmują:
- Złożona konstrukcja: Formy wielogniazdowe są trudniejsze do wykonania i utrzymania niż formy jednogniazdowe, ponieważ ich projekty są bardziej skomplikowane.
- zwiększa koszt formy: Formy wielogniazdowe mogą być droższe niż formy jednogniazdowe, ponieważ różne gniazda mogą być poddawane różnym naprężeniom i zużyciu podczas procesu odlewania wtryskowego. Może to prowadzić do mniej wydajnej produkcji i wyższych kosztów napraw.
Forma gorącokanałowa:
Forma gorącokanałowa to rodzaj formy wtryskowej, która wykorzystuje system gorących kanałów do dostarczania stopionego tworzywa sztucznego do gniazd formy. System gorącokanałowy składa się z podgrzewanego kolektora, który rozprowadza stopione tworzywo sztuczne do poszczególnych końcówek dysz, które są następnie kierowane do gniazd formy.

Forma gorącokanałowa
Zalety form gorącokanałowych obejmują:
- Lepsza jakość części: Formy gorącokanałowe mogą produkować części o lepszej jakości, ponieważ minimalizują ilość plastiku, który pozostaje w prowadnicach, zmniejszając ryzyko wad, takich jak błysk, krótkie strzały i ślady zatopienia.
- Zwiększona wydajność produkcji: Formy gorącokanałowe mogą zwiększyć wydajność produkcji, ponieważ eliminują potrzebę ręcznej interwencji w celu usunięcia kanałów z formowanych części, skracając czas cyklu i poprawiając ogólną szybkość produkcji.
- Efektywność energetyczna: Formy gorącokanałowe są bardziej energooszczędne w porównaniu z tradycyjnymi formami zimnokanałowymi, ponieważ minimalizują ilość plastiku marnowanego w prowadnicach.
Wady form gorącokanałowych obejmują:
- Złożona konstrukcja: Formy gorącokanałowe mają bardziej złożoną konstrukcję w porównaniu z tradycyjnymi formami zimnokanałowymi, co czyni je droższymi w produkcji i utrzymaniu.
- Zwiększona konserwacja: Formy gorącokanałowe zazwyczaj wymagają większej konserwacji w porównaniu z formami zimnokanałowymi, ponieważ mają bardziej złożony system grzewczy, który musi być utrzymywany w dobrym stanie.
- Podatność na zatykanie: Formy gorącokanałowe mogą być podatne na zatykanie, szczególnie w przypadku przetwarzania materiałów o wysokiej lepkości lub o długich długościach przepływu, ponieważ mogą one powodować zestalanie się stopionego tworzywa sztucznego w kanałach. Może to skutkować zmniejszoną wydajnością produkcji i zwiększonymi kosztami konserwacji.
Formy do układania w stosy:
Forma stosu to rodzaj formy wtryskowej, która pozwala na jednoczesne formowanie wielu wnęk w jednym cyklu maszynowym. Formy stosowe to zasadniczo dwie lub więcej form, które są ułożone jedna na drugiej, przy czym każda forma wytwarza pojedynczą część.

Forma do układania w stosy
Zalety form stosowych obejmują:
- Zwiększona wydajność produkcji: Formy stosowe pozwalają na jednoczesne formowanie wielu części, zwiększając wydajność produkcji i skracając czas cyklu.
- Mniejsze straty materiału: Formy stosowe minimalizują ilość odpadów materiałowych, ponieważ pozwalają na produkcję wielu części przy użyciu jednej porcji tworzywa sztucznego.
- Niższe koszty: Formy stosowe mogą być bardziej opłacalne w porównaniu z formami jednogniazdowymi, ponieważ umożliwiają produkcję wielu części w jednym cyklu maszynowym.
Wady form stosowych obejmują:
- Złożona konstrukcja: Formy stosowe mogą mieć bardziej złożoną konstrukcję w porównaniu z formami jednogniazdowymi, co czyni je droższymi w produkcji i utrzymaniu.
- Obniżona jakość części: Formy stosowe mogą wytwarzać części o obniżonej jakości, ponieważ obecność wielu wgłębień może skutkować zwiększonym ryzykiem wystąpienia wad, takich jak błysk, krótkie ujęcia i ślady zapadnięcia.
- Zwiększona konserwacja: Formy stosowe zazwyczaj wymagają większej konserwacji w porównaniu z formami jednogniazdowymi, ponieważ mają bardziej złożoną konstrukcję, którą należy utrzymywać w dobrym stanie technicznym.
Formy rodzinne:
Formy rodzinne, znane również jako formy z wieloma wgłębieniami, które są podobne do form z wieloma wgłębieniami, są rodzajem formowania wtryskowego, które pozwala na jednoczesne formowanie wielu części o nieco różnych wzorach w jednym cyklu maszynowym. Osiąga się to poprzez posiadanie wielu wnęk w formie, które mogą wytwarzać różne części o różnych kształtach i rozmiarach.
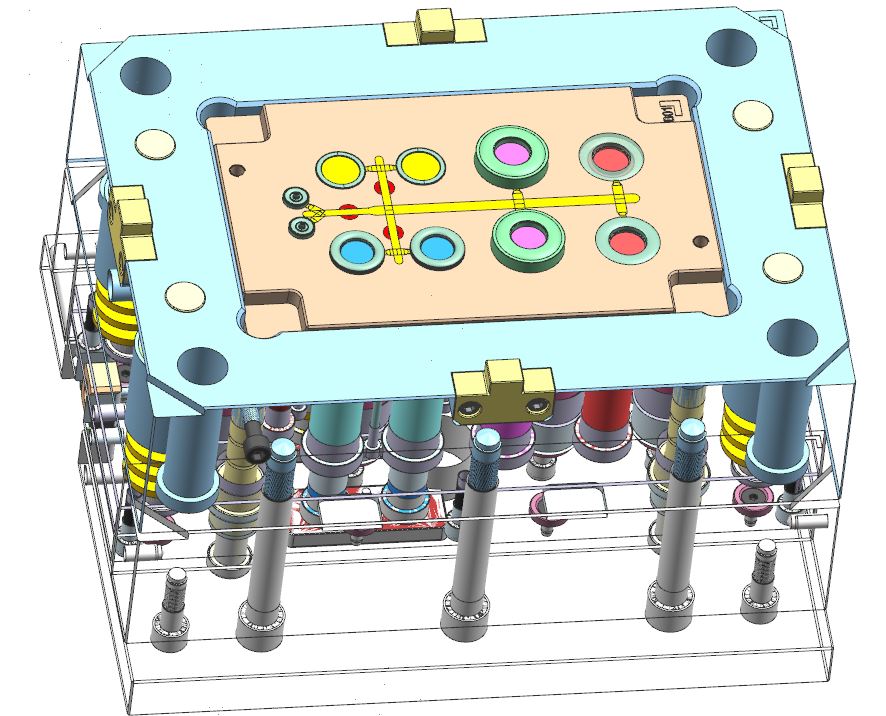
pleśń rodzinna
Zalety form rodzinnych obejmują:
- Zwiększona wydajność produkcji: Formy rodzinne pozwalają na jednoczesne formowanie wielu części o różnych wzorach, zwiększając wydajność produkcji i skracając czas cyklu.
- Niższe koszty: Formy rodzinne mogą być bardziej opłacalne w porównaniu do produkcji wielu form jednogniazdowych dla każdej części, ponieważ pozwalają na produkcję wielu części w jednym cyklu maszynowym.
- Elastyczność: Formy rodzinne pozwalają na produkcję różnych części o różnych wzorach, co czyni je wszechstronną opcją dla producentów, którzy muszą wytwarzać szereg produktów.
Wady form rodzinnych obejmują:
- Złożona konstrukcja: Formy rodzinne mogą mieć bardziej złożoną konstrukcję w porównaniu z formami jednogniazdowymi, co czyni je droższymi w produkcji i utrzymaniu.
- Obniżona jakość części: Formy rodzinne mogą produkować części o obniżonej jakości, ponieważ obecność wielu wgłębień może powodować zwiększone ryzyko wad, takich jak rozbłyski, krótkie strzały i ślady zapadnięcia.
Formy dwustrzałowe:
Forma dwustrzałowa (Formowanie wtryskowe 2-stopniowe), znany również jako nadformowanie lub formy wielostrzałowe lub formy 2K, to rodzaj formowania wtryskowego, który pozwala na formowanie dwóch różnych materiałów w jednym cyklu maszynowym. Proces ten obejmuje formowanie pierwszego materiału (materiału bazowego) w formie, a następnie formowanie drugiego materiału (materiału obtryskiwanego) na pierwszym materiale.

Forma dwustrzałowa
Zalety form dwustrzałowych obejmują:
- Zwiększona funkcjonalność: Formy dwustrzałowe pozwalają na połączenie dwóch różnych materiałów o różnych właściwościach w celu stworzenia części o zwiększonej funkcjonalności.
- Lepsza estetyka: Formy dwustrzałowe pozwalają na integrację różnych kolorów lub tekstur w jednej części, tworząc bardziej atrakcyjny wizualnie produkt.
- Krótszy czas montażu: Łącząc dwa materiały w jedną część, formy dwustrzałowe mogą zmniejszyć potrzebę dodatkowych etapów montażu, skracając czas i koszty produkcji.
Wady form dwustrzałowych obejmują:
- Złożona konstrukcja: Formy dwustrzałowe mają bardziej złożoną konstrukcję w porównaniu do form jednostrzałowych, przez co są droższe w produkcji i utrzymaniu.
- Wydłużony czas cyklu: Formy dwustrzałowe mają zazwyczaj dłuższy czas cyklu w porównaniu do form jednostrzałowych, ponieważ proces obejmuje formowanie dwóch materiałów w jednym cyklu maszyny.
- Kwestie kompatybilności: Formy dwustrzałowe wymagają, aby dwa formowane materiały były ze sobą kompatybilne i prawidłowo przylegały, co sprawia, że ważne jest staranne dobranie używanych materiałów.
Odkręcanie form:
Formy do odkręcania to rodzaj formowania wtryskowego zaprojektowany specjalnie do produkcji części z gwintem, takich jak zakrętki, pokrywki i pojemniki. Formy te są wyjątkowe, ponieważ mają mechanizm, który pozwala na obracanie rdzenia formy, podczas gdy wnęka pozostaje nieruchoma, umożliwiając odkręcenie uformowanej części z formy po jej ostygnięciu i zestaleniu.

odkręcanie formy
Zalety odkręcania form obejmują:
- Wysoka wydajność: Formy odkręcające pozwalają na wydajną produkcję części gwintowanych w jednym cyklu maszyny, skracając czas i koszty produkcji.
- Większa dokładność: Odkręcane formy pozwalają na precyzyjną produkcję części gwintowanych o stałym skoku i głębokości gwintu, poprawiając jakość i wydajność produktu końcowego.
- Wszechstronność: Formy do odkręcania mogą być używane do produkcji wielu różnych części z różnymi rodzajami i rozmiarami gwintów, co czyni je wszechstronną opcją do wielu różnych zastosowań.
Wady odkręcania form obejmują:
- Złożona konstrukcja: Formy do odkręcania są bardziej złożone w porównaniu do innych rodzajów form, przez co są droższe w produkcji i utrzymaniu.
- Wydłużony czas cyklu: Odkręcanie form ma zazwyczaj dłuższy czas cyklu w porównaniu do innych typów form, ponieważ proces ten obejmuje obrót rdzenia formy.
- Zużycie: Mechanizm obrotowy form odkręcających może być podatny na zużycie z upływem czasu, wymagając regularnej konserwacji w celu utrzymania prawidłowego działania formy.
Forma ze składanym rdzeniem:
Formy ze składanym rdzeniem są rodzajem formowania wtryskowego, które są używane do produkcji pustych części z wewnętrznymi wnękami, takimi jak rury, rury i inne części o skomplikowanych kształtach. Formy te wykorzystują unikalną konstrukcję, która umożliwia zapadnięcie się rdzenia formy, tworząc wewnętrzną wnękę części.

Komponent formy ze składanym rdzeniem
Zalety form ze składanym rdzeniem obejmują:
- Zwiększona wydajność: Formy ze składanym rdzeniem pozwalają na produkcję wydrążonych części w jednym cyklu maszynowym, skracając czas i koszty produkcji.
- Lepsza jakość części: Formy ze składanym rdzeniem zapewniają bardziej precyzyjną i spójną wewnętrzną wnękę, poprawiając ogólną jakość końcowej części.
- Wszechstronność: Formy ze składanym rdzeniem mogą być używane do produkcji szerokiej gamy różnych części o różnych kształtach i rozmiarach, co czyni je wszechstronną opcją do wielu różnych zastosowań.
Wady form ze składanym rdzeniem obejmują:
- Złożona konstrukcja: Formy ze składanym rdzeniem mają bardziej złożoną konstrukcję w porównaniu z innymi typami form, przez co są droższe w produkcji i utrzymaniu.
- Wydłużony czas cyklu: Formy ze składanym rdzeniem mają zazwyczaj dłuższy czas cyklu w porównaniu z innymi typami form, ponieważ proces obejmuje składanie rdzenia formy.
- Zużycie: Składany mechanizm rdzenia może być z czasem podatny na zużycie, wymagając regularnej konserwacji w celu utrzymania prawidłowego działania formy.
Zalety i wady plastikowych form wtryskowych
Zalety Formowanie wtryskowe:
- Produkcja wielkoseryjna: Formowanie wtryskowe jest wysoce wydajną metodą produkcji dużych ilości identycznych części. Dzięki temu idealnie nadaje się do masowej produkcji towarów konsumpcyjnych, części samochodowych i innych produktów, które wymagają dużych ilości podobnych części.
- Precyzja: Proces ten pozwala na bardzo precyzyjną kontrolę dokładności wymiarowej i spójności części. Wynika to z zastosowania ściśle kontrolowanych warunków przetwarzania oraz sztywności maszyny do formowania i formy.
- Szybkość: formowanie wtryskowe jest szybkim procesem, z czasem cyklu wynoszącym zaledwie kilka sekund dla małych części. Pozwala to producentom na wytwarzanie dużych ilości części w stosunkowo krótkim czasie.
- Opłacalność: Koszt produkcji części za pomocą formowania wtryskowego staje się bardziej ekonomiczny wraz ze wzrostem wielkości produkcji. Wynika to z faktu, że forma może być używana do produkcji wielu części przez cały okres jej użytkowania, a koszt pojedynczej części zmniejsza się wraz ze wzrostem ilości.
- Wszechstronność: Formowanie wtryskowe może być wykorzystywane do produkcji części z szerokiej gamy materiałów, w tym tworzyw sztucznych, metali i elastomerów. Ta wszechstronność sprawia, że jest to popularny wybór dla producentów, którzy muszą produkować części z różnych materiałów w zależności od konkretnych wymagań produktu.
- Automatyzacja: Wtryskarki mogą być zautomatyzowane, co zwiększa wydajność procesu i zmniejsza zapotrzebowanie na pracę ręczną. Może to również poprawić spójność i jakość części.
- Złożone kształty: Formowanie wtryskowe może być wykorzystywane do produkcji złożonych kształtów i projektów, w tym części o skomplikowanych szczegółach i wąskich tolerancjach. Jest to możliwe dzięki precyzyjnej kontroli procesu formowania i możliwości projektowania bardzo szczegółowych form.
- Wybór materiału: Formowanie wtryskowe pozwala producentom wybierać spośród szerokiej gamy materiałów, z których każdy ma swoje unikalne właściwości, takie jak wytrzymałość, elastyczność i odporność na ciepło, chemikalia i zużycie. Umożliwia to wybór najlepszego materiału do każdego zastosowania i produkcję części o pożądanych właściwościach.
Wady formowania wtryskowego:
- Wysoki koszt początkowy: Początkowy koszt stworzenia formy może być wysoki, szczególnie w przypadku skomplikowanych kształtów i projektów. Może to sprawić, że proces ten będzie mniej opłacalny w przypadku małych ilości części lub prototypów.
- Ograniczona elastyczność projektu: Po wykonaniu formy zmiana projektu może być trudna i kosztowna. Może to ograniczyć możliwość wprowadzania zmian lub ulepszeń projektu po utworzeniu formy.
- Odpady materiałowe: Formowanie wtryskowe generuje znaczną ilość odpadów, których utylizacja może być kosztowna i szkodliwa dla środowiska. Może to również zwiększyć koszty produkcji i zmniejszyć ogólną wydajność procesu.
- Czas realizacji: Czas tworzenia formy i konfigurowania procesu formowania wtryskowego może być długi, szczególnie w przypadku złożonych części. Może to spowolnić proces rozwoju produktu i ograniczyć możliwość szybkiego wprowadzania produktów na rynek.
- Ograniczenia wykończenia powierzchni: Formowanie wtryskowe może nie zapewniać wysokiej jakości wykończenia powierzchni niektórych części, zwłaszcza tych o skomplikowanych detalach lub wąskich tolerancjach. Może to ograniczyć możliwość produkcji części o wysokiej jakości estetycznym wyglądzie.
- Kompatybilność materiałów: Kompatybilność między materiałem a formą może być wyzwaniem, ponieważ niektóre materiały mogą nie współpracować dobrze z niektórymi rodzajami form lub wymagać specjalnych warunków przetwarzania. Może to ograniczyć możliwość produkcji części z niektórych materiałów i zwiększyć koszty produkcji.
- Ograniczony rozmiar części: Formowanie wtryskowe jest ograniczone rozmiarem formy i siłą zacisku maszyny formującej. Może to ograniczyć rozmiar części, które można wyprodukować i zwiększyć koszt produkcji większych części.
- Operacje dodatkowe: Niektóre części po uformowaniu mogą wymagać dodatkowych operacji, takich jak przycinanie lub wykańczanie. Może to zwiększyć koszty produkcji i ograniczyć ogólną wydajność procesu, oczywiście czasami te kwestie można rozwiązać poprzez ulepszenie formy wtryskowej
Typowe problemy związane z formami wtryskowymi
Gdy pracujesz w dziedzinie formowania wtryskowego tworzyw sztucznych, zawsze będzie jakiś problem, który musisz rozwiązać każdego dnia, Oto kilka typowych wyzwań napotykanych w formowaniu wtryskowym:
Problemy z wypaczaniem:
Wypaczenie jest częstym problemem w formowaniu wtryskowym i odnosi się do deformacji lub zniekształcenia uformowanej części, która występuje po wyjęciu z formy. Może się to zdarzyć z powodu różnych czynników, w tym:

Zniekształcenie Warp
- Niewłaściwe chłodzenie: Zbyt szybkie lub nierównomierne chłodzenie części może powodować wypaczenia, ponieważ materiał kurczy się i rozkurcza w różnym tempie.
- Naprężenia szczątkowe: Formowanie wtryskowe powoduje powstawanie naprężeń szczątkowych w części ze względu na wysokie ciśnienie stosowane podczas procesu formowania. Naprężenia te mogą powodować wypaczenia, jeśli nie zostaną odpowiednio zredukowane.
- Wybór materiału: Niektóre materiały są bardziej podatne na wypaczanie niż inne. Na przykład materiały o niskiej odporności termicznej lub niskiej stabilności wymiarowej są bardziej podatne na wypaczenia.
- Konstrukcja formy: Konstrukcja formy może również przyczynić się do wypaczenia, zwłaszcza jeśli forma nie pozwala na prawidłowe chłodzenie lub przepływ materiału.
- Warunki przetwarzania: Niespójne warunki przetwarzania, takie jak różne prędkości wtrysku, temperatury formy i poziomy ciśnienia, mogą powodować wypaczenia.
Aby zapobiec wypaczaniu, ważne jest, aby wybrać odpowiedni materiał, zoptymalizować projekt formy i warunki przetwarzania oraz wdrożyć odpowiednie praktyki chłodzenia i obsługi materiałów. Ponadto może być konieczne zastosowanie obróbki po formowaniu, takiej jak wyżarzanie, w celu zmniejszenia naprężeń szczątkowych i poprawy stabilności wymiarowej.
Problemy z lampą błyskową:
Wady typu flash to termin używany w formowaniu wtryskowym w odniesieniu do nadmiaru materiału, który jest wypychany z formy podczas procesu formowania. Flash występuje, gdy materiał wypływa poza zamierzoną wnękę formy i do linii podziału lub przestrzeni między dwiema połówkami formy.

Wypływki lub zadziory formujące
Błysk może być spowodowany kilkoma czynnikami, w tym
- Niewłaściwa konstrukcja formy: Źle zaprojektowana forma może powodować wypływki, pozwalając na wyciek materiału do linii podziału.
- Niespójne warunki przetwarzania: Zmienne warunki przetwarzania, takie jak prędkość wtrysku i ciśnienie, mogą powodować błysk.
- Kompatybilność materiałowa: Niektóre materiały mogą być niekompatybilne z formą i mogą powodować wypływanie podczas przepływu do linii podziału.
- Zużycie formy: Z biegiem czasu forma może się zużywać i powodować wypływanie materiału do linii podziału.
Wypływki mogą mieć kilka negatywnych skutków, w tym zmniejszenie dokładności wymiarowej części, zwiększenie ilości odpadów i utrudnienie operacji po formowaniu. Aby zminimalizować wypływki, ważne jest, aby zoptymalizować projekt formy, warunki przetwarzania i dobór materiałów, a także regularnie konserwować i naprawiać formę w razie potrzeby.
Linie spawania:
Linie zgrzewu są częstym problemem w formowaniu wtryskowym i odnoszą się do widocznych śladów na powierzchni formowanej części, gdzie dwa strumienie stopionego tworzywa sztucznego spotykają się i zestalają. Linie zgrzewu powstają, gdy materiał nie jest w pełni stopiony, gdy wpływa do formy. forma plastikowa pozostawiając widoczną linię na powierzchni części.

Linia spawalnicza
Linie spoin mogą być spowodowane kilkoma czynnikami, w tym
- Niewystarczający przepływ stopionego materiału: Jeśli materiał nie ma wystarczająco dużo czasu, aby przepłynąć i w pełni się stopić, może powstać linia spoiny.
- Nieprawidłowa konstrukcja wlewu: Źle zaprojektowana brama, która jest punktem, w którym stopiony materiał wchodzi do gniazda formy, może powodować powstawanie linii spawu.
- Niespójne warunki przetwarzania: Zmienne warunki przetwarzania, takie jak prędkość wtrysku i ciśnienie, mogą powodować powstawanie linii zgrzewu.
- Kompatybilność materiałowa: Niektóre materiały mogą nie być kompatybilne z formą i mogą powodować powstawanie linii zgrzewu, gdy wpływają do gniazda formy.
Linie spawu mogą osłabić wytrzymałość części i obniżyć jej ogólną jakość. Aby zminimalizować powstawanie linii zgrzewu, ważne jest, aby zoptymalizować projekt formy, warunki przetwarzania i dobór materiałów, a także wdrożyć odpowiednie praktyki obsługi materiałów. Ponadto może być konieczne zastosowanie specjalnych technik przetwarzania, takich jak formy wielogniazdowe lub systemy gorącokanałowe, aby ograniczyć powstawanie linii spawu.
Znaki zlewu:
Ślady zlewu, znane również jako "zlew", "zlew próżniowy" lub "skóra", to zapadnięte lub wgłębione obszary na powierzchni formowanej wtryskowo części z tworzywa sztucznego. Zwykle są one spowodowane wieloma czynnikami, w tym
- Kurczenie się żywicy: Gdy żywica stygnie i krzepnie, może kurczyć się nierównomiernie, prowadząc do powstawania śladów zapadania się.
- Słaby przepływ materiału: Jeśli żywica nie spływa równomiernie do wszystkich obszarów formy, mogą powstać puste przestrzenie lub zapadnięcia.
- Nieodpowiednie ciśnienie pakowania: Jeśli ciśnienie wtrysku nie jest wystarczająco wysokie, żywica może nie wypełnić formy całkowicie, co prowadzi do powstawania śladów zatopienia.
- Kwestie związane z konstrukcją formy: Konstrukcja formy, w tym umiejscowienie i rozmiar wlewu, system kanałów i odpowietrzanie, mogą mieć wpływ na jakość formowanej części i mogą przyczyniać się do powstawania zapadnięć.
Ślady zatopienia mogą wpływać na jakość estetyczną i funkcjonalność formowanej części i mogą być źródłem frustracji dla producentów i użytkowników końcowych. Aby zminimalizować powstawanie śladów zapadnięć, ważne jest, aby dokładnie rozważyć czynniki, które się do nich przyczyniają, takie jak wybór materiału, konstrukcja formy, parametry przetwarzania i konstrukcja części, a także dokonać niezbędnych korekt w celu optymalizacji procesu formowania wtryskowego.
Znaki przepływu:
Ślady płynięcia są częstym problemem w formowaniu wtryskowym i odnoszą się do widocznych śladów lub smug na powierzchni formowanej części, które są spowodowane przepływem stopionego tworzywa sztucznego podczas wypełniania gniazda formy. Ślady przepływu występują, gdy materiał przepływa nierównomiernie, pozostawiając widoczny ślad na powierzchni części.
Ślady przepływu mogą być spowodowane kilkoma czynnikami, w tym
- Niewystarczający przepływ stopionego materiału: Jeśli materiał nie ma wystarczająco dużo czasu, aby przepłynąć i wypełnić gniazdo formy, mogą powstać ślady płynięcia.
- Nieprawidłowa konstrukcja wlewu: Źle zaprojektowana brama, która jest punktem, w którym stopiony materiał wchodzi do gniazda formy, może powodować ślady przepływu.
- Niespójne warunki przetwarzania: Zmienne warunki przetwarzania, takie jak prędkość wtrysku i ciśnienie, mogą powodować powstawanie śladów przepływu.
- Kompatybilność materiałowa: Niektóre materiały mogą nie być kompatybilne z formą i mogą powodować ślady płynięcia, gdy wpływają do gniazda formy.
Ślady płynięcia mogą obniżyć ogólną jakość i kosmetyczny wygląd części. Aby zminimalizować powstawanie śladów wypływek, ważne jest, aby zoptymalizować projekt formy, warunki przetwarzania i dobór materiału, a także wdrożyć odpowiednie praktyki obsługi materiałów. Ponadto może być konieczne zastosowanie specjalnych technik przetwarzania, takich jak formy wielokomorowe lub systemy gorącokanałowe, aby ograniczyć powstawanie śladów przepływu.
Problemy z zadrapaniami:
Problemy z zarysowaniami odnoszą się do widocznych śladów lub zadrapań na powierzchni części formowanej wtryskowo, które są spowodowane fizycznym kontaktem części z formą lub innymi ciałami obcymi podczas procesu formowania. Zarysowania mogą wystąpić z kilku powodów, w tym:
- Zła konstrukcja formy: Nieprawidłowo zaprojektowane formy lub ich elementy mogą powodować zarysowania na powierzchni części.
- Niewystarczające smarowanie: Jeśli forma i elementy formy nie są odpowiednio nasmarowane, mogą powodować zarysowania na powierzchni części.
- Niewłaściwe obchodzenie się z materiałem: Niewłaściwe obchodzenie się z surowcem lub gotowymi częściami może powodować zadrapania na powierzchni części.
- Zanieczyszczenia w formie: Ciała obce lub zanieczyszczenia w gnieździe formy mogą powodować zadrapania na powierzchni części.
Zarysowania mogą obniżyć ogólną jakość i kosmetyczny wygląd części. Aby zminimalizować ryzyko zarysowań, ważne jest wdrożenie odpowiedniej konstrukcji formy, smarowania, obsługi materiałów i praktyk konserwacyjnych. Dodatkowo, regularne czyszczenie i kontrola formy oraz jej komponentów może pomóc w zapobieganiu powstawania zarysowań.
Ślady po wyrzutniku:
Ślady po wypychaczach to widoczne ślady na powierzchni części formowanej wtryskowo, które są spowodowane przez sworznie wypychaczy lub inne mechanizmy wypychające podczas procesu formowania. Ślady wypychacza powstają, gdy kołki wypychacza wypychają uformowaną część z gniazda formy i pozostawiają widoczne ślady na powierzchni części.
Ślady po wypychaczach mogą być spowodowane kilkoma czynnikami, w tym
- Nieprawidłowa konstrukcja sworznia wypychacza: Jeśli kołki wypychacza nie są prawidłowo zaprojektowane, mogą pozostawiać widoczne ślady na powierzchni części.
- Nadmierna siła: Jeśli trzpienie wypychacza wywierają nadmierną siłę na część podczas wypychania, mogą pozostawić głębsze i bardziej zauważalne ślady na powierzchni części.
- Niespójna siła wyrzutu: Jeśli siła wyrzutu nie jest równomierna w zależności od sworznia wyrzutnika, może to skutkować nierównymi śladami wyrzutu na powierzchni części.
- Słabe wykończenie powierzchni: Jeśli wykończenie powierzchni gniazda formy nie jest gładkie, może to powodować ślady wypychacza na powierzchni części.
Ślady po wypychaczach mogą obniżyć ogólną jakość i kosmetyczny wygląd części. Aby zminimalizować ślady wypychaczy, ważne jest, aby zoptymalizować konstrukcję sworzni wypychaczy i wykończenie powierzchni gniazda formy oraz wdrożyć odpowiednie praktyki konserwacji i kontroli. Dodatkowo może być konieczne zastosowanie specjalnych mechanizmów wypychania, takich jak wypychanie wspomagane powietrzem lub wypychanie boczne, aby zminimalizować ślady wypychaczy.
Problemy z krótkimi strzałami:
Krótki wtrysk jest częstym problemem w formowaniu wtryskowym, który występuje, gdy stopione tworzywo sztuczne nie wypełnia całkowicie gniazda formy, co powoduje, że uformowana część jest mniejsza niż pożądany rozmiar. Krótkie strzały mogą wystąpić z kilku powodów, w tym:
- Niewystarczająca ilość materiału: Jeśli nie ma wystarczającej ilości materiału do wypełnienia wnęki formy, może dojść do krótkiego wystrzału.
- Nieprawidłowe warunki przetwarzania: Jeśli warunki przetwarzania, takie jak prędkość wtrysku i ciśnienie, nie są ustawione prawidłowo, może dojść do krótkiego strzału.
- Zła konstrukcja formy: Źle zaprojektowana forma może powodować krótkie wystrzały, ponieważ materiał może nie być w stanie przepłynąć do wszystkich obszarów wnęki formy.
- Degradacja materiału: Jeśli materiał uległ degradacji lub nie był prawidłowo przechowywany, może to spowodować zwarcie.
Krótkie strzały mogą obniżyć ogólną jakość i funkcjonalność części oraz spowodować marnowanie materiału i czasu przetwarzania. Aby zminimalizować liczbę krótkich wyprasek, ważne jest, aby zoptymalizować projekt formy, warunki przetwarzania i dobór materiałów, a także wdrożyć odpowiednie praktyki obsługi materiałów. Dodatkowo, regularne monitorowanie i konserwacja sprzętu do formowania może pomóc w zapobieganiu powstawania krótkich strzałów.
Pułapka powietrzna i ślady oparzeń:
Pułapki powietrzne i ślady wypalenia są częstymi problemami w formowaniu wtryskowym, które mogą wystąpić z powodu niewłaściwych warunków przetwarzania lub konstrukcji formy.
Pułapki powietrzne występują, gdy powietrze zostaje uwięzione w gnieździe formy podczas procesu formowania wtryskowego, powodując przepływ materiału wokół kieszeni powietrznej zamiast jej wypełnienia. Może to skutkować widocznymi pustkami lub kieszeniami w formowanej części. Pułapki powietrzne mogą być spowodowane kilkoma czynnikami, w tym
- Niewystarczający przepływ materiału: Jeśli materiał nie przepływa prawidłowo do gniazda formy, powietrze może zostać uwięzione.
- Nieprawidłowa konstrukcja bramy: Jeśli brama nie jest prawidłowo zaprojektowana, powietrze może zostać uwięzione we wnęce formy.
- Nieodpowiednia wentylacja: Jeśli forma nie jest odpowiednio wentylowana, powietrze może zostać uwięzione w jej wnęce.
Ślady wypalenia powstają, gdy tworzywo sztuczne jest wystawione na działanie wysokich temperatur przez zbyt długi czas, co powoduje jego degradację i powstawanie widocznych śladów lub przebarwień na powierzchni części. Ślady po oparzeniach mogą być spowodowane przez kilka czynników, w tym:
- Zbyt wysokie temperatury przetwarzania: Jeśli temperatura przetwarzania jest ustawiona zbyt wysoko, materiał może ulec degradacji i spowodować powstanie śladów przypalenia.
- Niewystarczający czas chłodzenia: Jeśli część nie zostanie odpowiednio schłodzona, materiał może ulec degradacji i spowodować powstanie śladów wypalenia.
- Zła konstrukcja formy: Źle zaprojektowana forma może powodować zbyt długie wystawienie materiału na działanie wysokich temperatur, co prowadzi do powstawania śladów wypalenia.
Aby zminimalizować liczbę pułapek powietrznych i śladów wypalenia, ważne jest zoptymalizowanie warunków przetwarzania i konstrukcji formy oraz wdrożenie odpowiednich praktyk monitorowania i konserwacji. Ponadto może być konieczne zastosowanie specjalnych technik przetwarzania, takich jak formowanie w niskiej temperaturze lub formowanie próżniowe, w celu zminimalizowania pułapek powietrznych i śladów przypaleń.
Przetwarzanie w celu wykonania formy wtryskowej:
Proces tworzenia formy wtryskowej obejmuje kilka etapów:
Projektowanie form:
Projektowanie form wtryskowych jest krytycznym aspektem procesu formowania wtryskowego, ponieważ bezpośrednio wpływa na jakość, wydajność i koszt formowanych części.
Dobrze zaprojektowana forma wtryskowa będzie produkować części, które spełniają pożądany rozmiar, kształt i wymagania jakościowe, a jednocześnie są wydajne w produkcji i łatwe w utrzymaniu.
Kluczowe czynniki, które należy wziąć pod uwagę przy projektowaniu formy wtryskowej obejmują:
- Geometria części: Projekt formowanej części musi uwzględniać pożądany rozmiar, kształt i cechy części.
- Wybór materiału: Materiał, który ma być użyty do wykonania formy i formowanej części, musi być wybrany w oparciu o takie czynniki, jak koszt, wytrzymałość i stabilność termiczna.
- Wnęki formy: Liczba i rozmieszczenie gniazd formy muszą być dobrane tak, aby spełnić wymagania dotyczące wielkości produkcji.
- System wlewowy: Konstrukcja systemu wlewowego ma kluczowe znaczenie, ponieważ określa sposób, w jaki tworzywo sztuczne wpływa do gniazda formy.
- System wypychania: System wyrzucania musi być zaprojektowany tak, aby zapewnić, że uformowane części mogą być usunięte z formy bez uszkodzeń.
- Układ chłodzenia: System chłodzenia musi być zaprojektowany tak, aby zapewnić równomierne i szybkie chłodzenie formowanych części, skracając czas cyklu i poprawiając jakość.
- Kąty zanurzenia: Projekt formy musi uwzględniać odpowiednie kąty zanurzenia, aby umożliwić wyjęcie uformowanych części z formy.
- Wentylacja: Forma musi być wentylowana, aby umożliwić wydostawanie się powietrza z wnęki formy, zmniejszając ryzyko powstawania pułapek powietrznych i śladów poparzeń.
- Konserwacja i naprawa: Forma musi być zaprojektowana z myślą o łatwej konserwacji i naprawie, aby zminimalizować przestoje i zwiększyć wydajność produkcji.
Projektowanie form wtryskowych jest złożonym procesem, który wymaga specjalistycznej wiedzy w takich dziedzinach jak inżynieria mechaniczna, materiałoznawstwo i produkcja. Ważne jest, aby współpracować z renomowanym projektantem form, aby upewnić się, że forma jest zaprojektowana prawidłowo i spełnia Twoje potrzeby.
Programowanie CNC:
Programowanie CNC (Computer Numerical Control) jest niezbędnym krokiem w produkcji form wtryskowych. Po zakończeniu projektowania formy, następnym krokiem jest programowanie CNC. Poniżej przedstawiono główne etapy programowania CNC do produkcji form wtryskowych:
- Tłumaczenie modelu CAD: Model CAD jest tłumaczony na program komputerowego wspomagania produkcji (CAM), który jest używany do tworzenia kodu CNC dla formy.
- Tworzenie kodu CNC: Kod CNC jest tworzony w programie CAM, który dostarcza maszynie CNC instrukcje dotyczące przesuwania i cięcia elementów formy. Kod uwzględnia materiał i grubość elementów formy, a także pożądane kształty i cechy.
- Tworzenie ścieżki narzędzia: Ścieżka narzędzia jest tworzona w programie CAM, który definiuje ścieżkę, którą będzie podążać narzędzie tnące w celu obróbki elementów formy. Ścieżka narzędzia uwzględnia kształty i cechy elementów formy oraz możliwości maszyny CNC.
- Symulacja: Kod CNC i ścieżka narzędzia są symulowane w programie CAM, aby zapewnić, że komponenty formy będą obrabiane prawidłowo i zgodnie z odpowiednimi specyfikacjami.
- Obróbka CNC: Kod CNC jest ładowany do maszyny CNC, która następnie wykorzystuje kod i ścieżkę narzędzia do obróbki elementów formy.
Programowanie CNC jest krytycznym krokiem w procesie produkcji form wtryskowych, ponieważ określa dokładność i jakość komponentów formy. Ważne jest, aby współpracować z programistą CNC, który ma doświadczenie w programowaniu form wtryskowych, aby upewnić się, że kod CNC jest tworzony poprawnie i zgodnie z odpowiednimi specyfikacjami. Na tym etapie do elementów formy dodawane są również kanały chłodzące, system wypychaczy i inne funkcje, aby zapewnić ich prawidłowe działanie.
Zakup listy BOM form
Lista BOM formy (Bill of Materials) to kompleksowa lista wszystkich komponentów i materiałów potrzebnych do wyprodukowania formy wtryskowej. Obejmuje ona następujące elementy:
- Stal na podstawę formy i wkładki rdzenia/wnęki
- Komponenty gorących kanałów
- Elementy układu chłodzenia, takie jak przewody wodne i bloki chłodzące
- Elementy systemu wyrzutowego, takie jak sworznie i tuleje wyrzutnika
- Elementy ściągacza wlewków
- Opaski grzejne i regulatory temperatury
- Elementy formy, takie jak tuleje, kołki prowadzące i urządzenia blokujące
- Wkładki do form, takie jak suwaki i podnośniki
- Artykuły specjalne, takie jak datowniki i niestandardowe logo
Lista BOM formy jest ważnym narzędziem dla zaopatrzenia i produkcji, ponieważ zawiera jasną i szczegółową listę komponentów i materiałów potrzebnych do wyprodukowania formy. Służy do zapewnienia, że wszystkie niezbędne komponenty są zamówione i dostępne, gdy forma jest gotowa do produkcji.
Ważne jest, aby przy zakupie komponentów do form wtryskowych współpracować z renomowanym dostawcą, ponieważ jakość i niezawodność tych komponentów może mieć znaczący wpływ na wydajność i jakość procesu formowania wtryskowego.
Obróbka zgrubna form:
Obróbka zgrubna formy wtryskowej odnosi się do wstępnej obróbki stalowych elementów formy wtryskowej w celu uzyskania podstawowego kształtu i rozmiaru formy. Ten etap jest zwykle wykonywany przy użyciu maszyn sterowanych numerycznie (CNC). Poniżej przedstawiono główne etapy obróbki zgrubnej form wtryskowych:
- Wybór stali: Pierwszym krokiem jest wybór odpowiedniego rodzaju stali dla formy, takiego jak P20 lub H13, w oparciu o pożądane właściwości formowanej części.
- Cięcie stali: Stal jest cięta do odpowiedniego rozmiaru i kształtu za pomocą maszyny CNC. Ten etap może również obejmować wiercenie i gwintowanie otworów dla systemów chłodzenia i wyrzutu.
- Profilowanie stali: Elementy stalowe są następnie obrabiane w celu uzyskania podstawowego kształtu formy, w tym rdzenia i wkładek wnękowych.
- Kontrola stali: Obrobione komponenty są następnie sprawdzane, aby upewnić się, że spełniają wymagane tolerancje i specyfikacje.
- Czyszczenie stali: Obrabiane elementy są czyszczone i gratowane w celu usunięcia wszelkich szorstkich krawędzi lub zanieczyszczeń.
Proces obróbki zgrubnej jest ważnym krokiem w procesie formowania wtryskowego, ponieważ kładzie podwaliny pod końcową, wysoce precyzyjną obróbkę i polerowanie, które nastąpią później. Ważne jest, aby upewnić się, że obróbka zgrubna jest wykonywana dokładnie i zgodnie z prawidłowymi specyfikacjami, aby zapewnić prawidłowe działanie formy i produkcję części o pożądanej jakości.
Obróbka cieplna stali formierskiej:
Obróbka cieplna stali formierskiej to proces podgrzewania i chłodzenia stalowych elementów formy wtryskowej w celu poprawy ich właściwości mechanicznych i stabilności wymiarowej. Celem obróbki cieplnej jest utwardzenie stali, zmniejszenie naprężeń szczątkowych oraz poprawa jej odporności na zużycie i wytrzymałości. Jest to specjalnie dla hartowanej stali formy wtryskowej, jeśli do wykonania formy wtryskowej używana jest stal wstępnie utwardzona, nie ma potrzeby wykonywania tej obróbki cieplnej. Poniżej przedstawiono główne etapy obróbki cieplnej stali formierskiej:
- Wyżarzanie: Elementy stalowe są podgrzewane do określonej temperatury, zwykle w zakresie 800-900°C, a następnie powoli schładzane w celu zmniejszenia naprężeń wewnętrznych i poprawy skrawalności stali.
- Hartowanie: Elementy stalowe są podgrzewane do wysokiej temperatury, zwykle powyżej temperatury krytycznej, a następnie szybko schładzane, zwykle poprzez hartowanie w oleju lub wodzie. Proces ten utwardza stal i poprawia jej odporność na zużycie.
- Odpuszczanie: Po hartowaniu elementy stalowe są odpuszczane poprzez podgrzanie ich do niższej temperatury przez określony czas, aby poprawić wytrzymałość stali i stabilność wymiarową.
Proces obróbki cieplnej ma kluczowe znaczenie dla zapewnienia, że stalowe elementy formy wtryskowej mają pożądane właściwości mechaniczne i stabilność wymiarową, które są niezbędne do produkcji wysokiej jakości wyprasek. Ważne jest, aby współpracować z dostawcą obróbki cieplnej, który ma doświadczenie w obróbce stali formierskiej, aby zapewnić, że proces obróbki cieplnej jest wykonywany prawidłowo i zgodnie z odpowiednimi specyfikacjami.
Precyzyjna obróbka gniazda formy i rdzenia:
Precyzyjna obróbka gniazda formy i rdzenia to proces precyzyjnej obróbki wewnętrznych powierzchni gniazda formy i wkładek rdzenia w celu uzyskania ostatecznego kształtu i rozmiaru formy. Ten etap jest zwykle wykonywany przy użyciu maszyn sterowanych numerycznie (CNC) z wysoką precyzją i dokładnością. Poniżej przedstawiono główne etapy obróbki precyzyjnej gniazda formy i rdzenia:
- Przygotowanie powierzchni: Powierzchnia gniazda formy i wkładek rdzeniowych jest czyszczona i polerowana w celu usunięcia wszelkich pozostałości lub chropowatości.
- Obróbka powierzchni: Wewnętrzne powierzchnie gniazda formy i wkładek rdzenia są obrabiane za pomocą maszyn CNC w celu uzyskania ostatecznego kształtu i rozmiaru formy. Obejmuje to tworzenie skomplikowanych szczegółów i cech formowanej części, takich jak tekst, logo i podcięcia.
- Kontrola powierzchni: Obrabiane powierzchnie są sprawdzane w celu zapewnienia, że spełniają one wymagane tolerancje i specyfikacje.
- Polerowanie powierzchni: Wewnętrzne powierzchnie gniazda formy i wkładek rdzenia są polerowane do wysokiego wykończenia, aby poprawić jakość powierzchni formowanych części i zmniejszyć ryzyko wad.
Obróbka precyzyjna jest krytycznym etapem procesu formowania wtryskowego, ponieważ decyduje o jakości i dokładności formowanych części. Ważne jest, aby współpracować z dostawcą obróbki skrawaniem, który ma doświadczenie w precyzyjnej obróbce wnęki formy i rdzenia, aby zapewnić, że obróbka jest wykonywana prawidłowo i zgodnie z odpowiednimi specyfikacjami. Na tym etapie dodawany jest również system wypychania formy, kanały chłodzące i inne funkcje zapewniające prawidłowe funkcjonowanie formy.
Obróbka elektroerozyjna:
EDM (Electrical Discharge Machining) to proces wykorzystywany do tworzenia skomplikowanych i bardzo precyzyjnych kształtów w częściach metalowych, w tym w formach wtryskowych. Proces ten wykorzystuje iskry elektryczne do usuwania materiału z powierzchni formy, tworząc pożądany kształt. Poniżej przedstawiono główne etapy obróbki EDM:
- Przygotowanie powierzchni: Powierzchnia elementu formy przeznaczonego do obróbki jest czyszczona i polerowana w celu usunięcia wszelkich pozostałości i chropowatości.
- Konfiguracja EDM: Maszyna EDM jest ustawiana z prawidłowymi parametrami, w tym przerwą iskrową, czasem trwania impulsu i materiałem elektrody, w oparciu o materiał i kształt elementu formy.
- Erozja iskrowa: Maszyna EDM wytwarza iskry elektryczne, które usuwają materiał z elementu formy, tworząc pożądany kształt. Proces ten odbywa się stopniowo, a maszyna EDM stopniowo eroduje materiał, aż do uzyskania ostatecznego kształtu.
- Kontrola powierzchni: Obrabiana powierzchnia jest sprawdzana w celu zapewnienia, że spełnia ona wymagane tolerancje i specyfikacje.
Obróbka EDM jest często stosowana w przypadku elementów form o złożonych kształtach lub małych, skomplikowanych szczegółach, które są trudne do osiągnięcia w innych procesach obróbki. Jest również wykorzystywana do produkcji ostrych krawędzi i narożników, które są niezbędne do prawidłowego funkcjonowania formy wtryskowej.
Proces ten jest bardzo precyzyjny i dokładny, dzięki czemu idealnie nadaje się do produkcji wysokiej jakości części formowanych. Ważne jest, aby współpracować z dostawcą EDM, który ma doświadczenie w obróbce EDM form wtryskowych, aby zapewnić, że proces jest wykonywany prawidłowo i zgodnie z odpowiednimi specyfikacjami.
Polerowanie powierzchni formy:
Polerowanie form wtryskowych jest ostatnim etapem procesu produkcji form wtryskowych. Obejmuje on wygładzanie powierzchni elementów formy, aby zapewnić, że gotowy produkt ma gładką i równą powierzchnię. Poniżej przedstawiono główne etapy polerowania form wtryskowych:

polerowanie form plastikowych
- Przygotowanie powierzchni: Powierzchnie elementów formy są czyszczone i przygotowywane do polerowania. Wszelkie pozostałe szorstkie miejsca lub ślady obróbki są usuwane, aby zapewnić gładką powierzchnię do polerowania.
- Polerowanie zgrubne: Pierwszym etapem polerowania jest polerowanie zgrubne, które polega na usunięciu wszelkich dużych niedoskonałości powierzchni elementów formy. Ten etap jest zwykle wykonywany przy użyciu gruboziarnistego materiału ściernego, takiego jak papier ścierny lub szczotka ścierna.
- Dokładne polerowanie: Dokładne polerowanie to kolejny krok, który obejmuje wygładzenie powierzchni elementów formy do dokładniejszego wykończenia. Ten etap jest wykonywany przy użyciu drobniejszego materiału ściernego, takiego jak drobniejszy papier ścierny lub szczotka ścierna.
- Polerowanie: Polerowanie to ostatni etap polerowania, który obejmuje użycie tarczy polerskiej i pasty polerskiej w celu uzyskania wysokiego połysku na elementach formy.
- Kontrola: Po polerowaniu elementy formy są dokładnie sprawdzane, aby upewnić się, że mają gładką i równą powierzchnię, bez zadrapań, pęknięć lub innych niedoskonałości.
Polerowanie form wtryskowych jest ważne, ponieważ wpływa na jakość produktu końcowego. Dobrze wypolerowana forma skutkuje produktem o gładkiej i równej powierzchni, co jest ważne dla funkcjonalności i estetyki produktu. Ważne jest, aby współpracować z doświadczonym polernikiem form, aby upewnić się, że elementy formy są polerowane zgodnie z odpowiednimi specyfikacjami i do pożądanego poziomu jakości.
Mocowanie formy
Montaż form wtryskowych to specjalistyczne zadanie w dziedzinie formowania wtryskowego, które obejmuje montaż, instalację i testowanie form wtryskowych. Mistrzowie form są odpowiedzialni za zapewnienie, że komponenty formy są prawidłowo zmontowane i działają poprawnie, a forma produkuje części o pożądanej jakości i standardach wydajności. Niektóre z głównych obowiązków monterów form obejmują:
- Montaż komponentów formy: Mistrzowie formy są odpowiedzialni za montaż różnych komponentów formy wtryskowej, w tym elementów gniazda i rdzenia, systemu kanałów i wszelkich elementów pomocniczych.
- Instalacja formy na maszynie do montażu form: Moldmaster musi być w stanie zamontować formę na maszynie do montażu form w sposób zapewniający prawidłowe wyrównanie i funkcjonowanie formy, jeśli nie ma żadnej maszyny do montażu form, należy użyć ręcznego sposobu montażu formy, tak robi większość firm.
- Testowanie formy: Mistrz formy jest odpowiedzialny za testowanie formy, aby upewnić się, że produkuje ona części o pożądanej jakości i standardach wydajności. Obejmuje to kontrolę części pod kątem wszelkich wad, takich jak wypaczenia, kurczenie się lub inne problemy jakościowe.
- Dostosowanie formy: W przypadku wykrycia jakichkolwiek problemów podczas fazy testowania, moldmaster jest odpowiedzialny za dokonanie wszelkich niezbędnych regulacji formy, aby zapewnić, że produkuje ona części spełniające pożądane specyfikacje.
- Rozwiązywanie problemów: Moldmaster musi być w stanie zidentyfikować i rozwiązać wszelkie problemy, które mogą pojawić się podczas procesu montażu form.
Praca montera form wtryskowych wymaga połączenia wiedzy technicznej, sprawności manualnej i dbałości o szczegóły. Monterzy form muszą być w stanie pracować z szeroką gamą narzędzi i maszyn, a także rozumieć złożone procesy związane z formowaniem wtryskowym. Ważne jest, aby monterzy form dobrze rozumieli proces formowania wtryskowego, a także mieli doświadczenie w pracy z różnymi rodzajami form i materiałów.
Pierwsza próba formowania wtryskowego lub strzelanie:
Próbne formowanie wtryskowe odnosi się do procesu testowania formy wtryskowej w celu wytworzenia próbki części przy użyciu procesu formowania wtryskowego. Proces ten jest krytycznym krokiem w procesie formowania wtryskowego, ponieważ pozwala producentowi ocenić wydajność formy i dokonać niezbędnych korekt przed wyprodukowaniem dużej ilości części.
Proces próbnego formowania wtryskowego obejmuje zazwyczaj następujące etapy:
- Przygotowanie: Forma jest instalowana na wtryskarce, a maszyna jest ustawiana do wtrysku. Zbiornik jest napełniany plastikową żywicą.
- Kontrola temperatury topnienia: Temperatura topnienia jest kontrolowana, aby zapewnić, że żywica plastikowa jest podgrzewana do odpowiedniej temperatury w celu wytworzenia wysokiej jakości części.
- Wtrysk: Stopione tworzywo sztuczne jest wtryskiwane do formy pod wysokim ciśnieniem. Ciśnienie jest utrzymywane do momentu wypełnienia formy plastikową żywicą.
- Chłodzenie: Forma jest chłodzona w celu zestalenia żywicy i uformowania części. Czas chłodzenia zależy od rodzaju zastosowanej żywicy z tworzywa sztucznego oraz rozmiaru i kształtu produkowanej części.
- Wyrzucanie: Po zestaleniu część jest usuwana z formy. Kołki wypychacza są używane do wypchnięcia części z formy.
- Kontrola: Część wyprodukowana z formy jest dokładnie sprawdzana, aby upewnić się, że spełnia pożądane specyfikacje i standardy jakości.
- Korekty: W razie potrzeby można dokonać korekt w procesie formowania, aby poprawić wydajność formy i jakość produkowanych części.
Proces próbnego formowania wtryskowego jest ważnym krokiem w procesie formowania wtryskowego, ponieważ pozwala producentowi ocenić wydajność formy i dokonać niezbędnych korekt przed wyprodukowaniem dużej ilości części. Proces ten pomaga zapewnić, że forma produkuje wysokiej jakości części o pożądanych specyfikacjach.
Forma zapakowana i gotowa do produkcji:
Gdy forma zostanie całkowicie ukończona przez producenta form, następnym krokiem jest masowa produkcja. Pakowanie formy i przygotowanie do produkcji jest ostatnim krokiem w procesie formowania wtryskowego przed rozpoczęciem masowej produkcji. Etap ten obejmuje następujące zadania:
- Czyszczenie i konserwacja: Forma jest dokładnie czyszczona i sprawdzana, aby upewnić się, że nie ma żadnych zanieczyszczeń, brudu ani uszkodzeń formy.
- Pakowanie i przechowywanie: Forma jest starannie pakowana i przechowywana w bezpiecznym miejscu, aby zapobiec uszkodzeniom i zapewnić, że będzie gotowa do użycia w razie potrzeby.
- Testowanie i regulacja: Forma jest testowana pod kątem wszelkich problemów, takich jak wycieki, słabe wypełnienie lub niewłaściwe wyrzucanie części, a wszelkie niezbędne regulacje są wprowadzane w celu zapewnienia prawidłowego działania formy.
- Konfiguracja produkcji: Forma jest instalowana we wtryskarce, a wszystkie niezbędne ustawienia, takie jak temperatura, ciśnienie i prędkość wtrysku, są dostosowywane w celu spełnienia określonych wymagań produkcyjnych.
- Rozpoczęcie produkcji: Produkowana jest pierwsza partia części, a proces jest monitorowany w celu zapewnienia, że części spełniają wymagane specyfikacje i standardy jakości. Wprowadzane są wszelkie niezbędne korekty w celu optymalizacji procesu produkcji i zapewnienia stałej jakości.
Ogólnie rzecz biorąc, przygotowanie formy do produkcji jest ważnym krokiem w procesie formowania wtryskowego, który pomaga zapewnić sukces i wydajność produkcji.
Powyższe informacje są procedurami tworzenia formy wtryskowej, może są jakieś małe rzeczy pominięte, ale większość rzeczy jest powyżej, jak widać, tworzenie formy wtryskowej nie jest łatwym przypadkiem, jeśli masz projekt formy wtryskowej w uchwycie, musisz znaleźć profesjonalnego producenta form wtryskowych do obsługi, to upewni się, że twój projekt przebiega pomyślnie.
Sincere Tech jest profesjonalistą Forma chińska Fabryka specjalizująca się w produkcji niestandardowych form wtryskowych. Posiada doświadczenie i wiedzę w zakresie projektowania, rozwoju i produkcji wysokiej jakości form wtryskowych dla różnych branż i zastosowań.
Zapewniają szereg usług, w tym projektowanie form, prototypowanie, produkcję form i przetwarzanie po formowaniu, aby zapewnić swoim klientom najlepsze możliwe wyniki. Koncentrując się na jakości, precyzji i zadowoleniu klienta, Sincere Tech jest niezawodnym i godnym zaufania partnerem dla wszystkich potrzeb związanych z formowaniem wtryskowym. Skontaktuj się z nami, aby uzyskać cenę za swój projekt już teraz.