Wanneer de vereisten voor polymeeronderdelen verder gaan dan 3D-printen en bewerken, wordt productengineers aangeraden om over te stappen op spuitgieten. Conventioneel spuitgieten houdt in dat u de juiste gereedschapsleverancier moet identificeren en vervolgens het gereedschap moet kopen, wat meerdere maanden kan duren. Het kan lang duren en is erg vermoeiend, maar de kosten per eenheid zijn relatief laag, vooral bij het maken van veel onderdelen van de items. Gelukkig is er een alternatief: kunststof spuitgieten in korte oplages.
Begrip korte termijn kunststof spuitgieten
Wanneer er sprake is van een kleine productie van het product, worden bij spuitgieten op korte termijn goedkopere gereedschappen gebruikt dan bij spuitgieten op lange termijn (of spuitgieten in grote volumes). Dit proces doet ook afstand van het conventionele productiesysteem met grote volumes dat veel stijfheid, lange cyclustijd en grote kapitaalinvesteringen vereist. In dit geval is spuitgieten op korte termijn echter geschikter dan op lange termijn.
De tijdelijke mallen zijn van aluminium, terwijl de 'harde' productiegereedschappen van gecementeerd gereedschapsstaal zijn. Dit metaal wordt gekenmerkt door een hoge thermische geleidbaarheid en goede bewerkbaarheid. Aluminium mallen zijn iets minder stijf dan stalen mallen, maar ze zijn het meest geschikt voor series van minder dan 10.000 stuks. Bovendien zijn ze goedkoper dan stalen mallen en worden de uiteindelijke onderdelen in weken gemaakt, niet in maanden, zoals bij stalen mallen.
Spuitgieten in kleine oplages is het meest geschikt voor elke organisatie die hoogwaardige kunststofonderdelen nodig heeft tegen een betaalbare prijs en binnen een korte tijd.
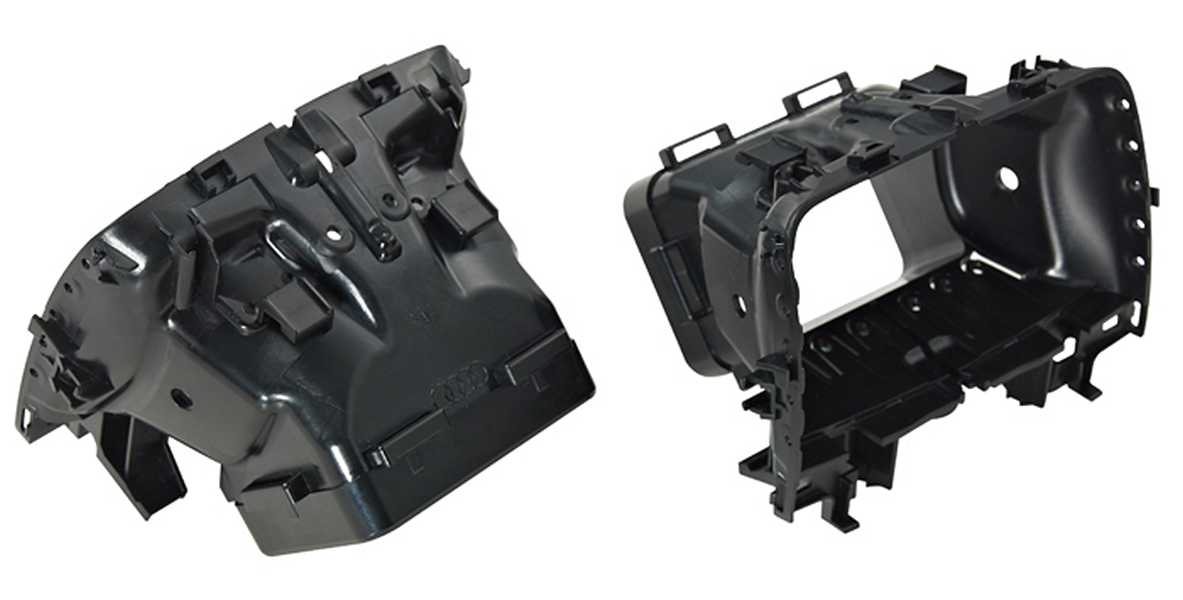
Voordelen van spuitgieten op korte termijn
De voordelen van spuitgieten in kleine series zijn als volgt:
Aluminium spuitgietmatrijzen zijn goedkoper vergeleken met versterkte stalen matrijzen die tegenwoordig op de markt verkrijgbaar zijn. De mate van besparing is afhankelijk van het aantal holtes, de geometrie van het onderdeel en de gietproblemen zoals ondersnijdingen of inzetstukken. Het verschil in kosten is echter normaal gesproken vrij groot.
Maar dit is niet het enige voordeel dat hieruit kan worden afgeleid, de kostenfactor moet worden overwogen. De mogelijkheid om wijzigingen aan te brengen en de korte cyclustijden kunnen dus nuttig zijn om de tijd die nodig is om producten te ontwikkelen te verkorten en zo de time-to-market te verkorten. In tegenstelling tot de meeste organisaties, bindt onze service voor spuitgieten op korte termijn de klanten echter niet om grote hoeveelheden te bestellen. Ze zijn gemaakt van materialen van productiekwaliteit en hebben adequate oppervlakteafwerkingen die kunnen worden gebruikt.
Korte termijn spuitgietkosten voor onderdelenproductie
Het is ook belangrijk om te weten dat de kosten voor het vervaardigen van de spuitgietmatrijs voor de productie van kleine aantallen en het instellen ervan vastliggen en over het aantal bestellingen moeten worden gespreid.
Over het algemeen is spuitgieten in korte oplage geschikt voor onderdelen van 1 tot 10.000. Bij Sincere Tech bieden we twee gereedschapsopties: prototypemallen, die normaal gesproken worden geassocieerd met een garantie van ten minste 2000 shots en on-demand productiemallen, die worden geassocieerd met een garantie op de levensduur van de mal. Als het aluminium gereedschap kapot is, vervangt het bedrijf het zonder de klant iets in rekening te brengen. Wat betreft de hoeveelheid van het geproduceerde product, zijn beide opties redelijk goedkoop.
Andere speciale diensten zijn eerste artikelinspectie, capaciteitsrapporten, wetenschappelijke gietprocesontwikkelingsrapporten en PPAP. Sommige klanten hebben ontdekt dat een aluminium mal voor korte oplage kan worden gebruikt als eindproductmal.
Als de volumes in de miljoenen lopen, is productiegereedschap wellicht geschikter. Aan de andere kant kan 3D-printen goedkoper zijn in het geval van de productie van een paar onderdelen. Sommige fabrikanten gebruiken 3D-printen om de prototypes te maken en gebruiken vervolgens kleine series spuitgieten.
Toepassingen van korte-serie spuitgieten
De beste strategie is relatief aan de behoeften van de organisatie en de situatie in de organisatie. Bijvoorbeeld, een fabrikant van medische hulpmiddelen die een nieuw medisch hulpmiddel heeft ontwikkeld maar twijfelt over de marktsituatie, kan een korte-run injectie-instrument gebruiken. Dit is in het voordeel van een "pay-as-you-go"-benadering tijdens de introductie van het product. Als ze op een later tijdstip besluiten om te investeren in een stalen gereedschap, kan de aluminium mal worden gebruikt als een interim-gereedschap totdat de productiemal is gemaakt.
Het is ook belangrijk om op te merken dat bridge tools niet beperkt zijn tot de ramp-up fase van de productintroductie. Ze kunnen een vrij goedkope manier zijn om een verzekeringspolis te hebben voor volwassen programma's. Bijvoorbeeld, een fabrikant van apparaten was in een positie om door te gaan met het productieproces omdat hij of zij een bridge tool gebruikte om de hoofdtool te repareren. Ze hebben nu een extra mal die ze in de toekomst kunnen gebruiken, bijvoorbeeld als de vraag naar het product stijgt of als de huidige tool niet effectief is.
Het spuitgieten op korte termijn is een goede middenweg voor ontwerpers om het beste matrijsontwerp en de prestaties van het eindproduct te krijgen met een relatief laag risico in vergelijking met het directe gebruik van stalen productietools van de 3D-geprinte modellen. Dit geldt des te meer in sectoren zoals medische hulpmiddelen, waar het belangrijk is om de tijd die nodig is om deze producten te ontwikkelen te verkorten en tegelijkertijd te garanderen dat de producten voldoen aan de vastgestelde wettelijke normen, aangezien dit kosteneffectief is.
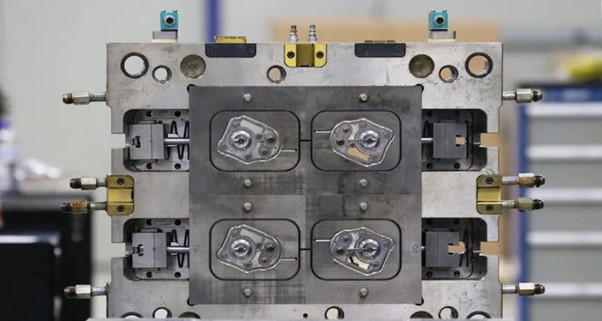
Spuitgieten in grote volumes
Ons digitale netwerk is in staat om grotere en complexere onderdelen in grote volumes te produceren, voor het geval dat spuitgieten op korte termijn niet van toepassing is op uw geval. Ons uitbreidbare scala aan diensten omvat;
- Projecten voor gegoten elementen die groot, zwaar en uitgebreid van ontwerp zijn
- Offertes voor meer dan 100.000 componenten
- Vormgevingsmogelijkheden voor onderdelen tot 79 inch (2 meter) groot
- Mold-Tech afwerkingen en diverse oppervlakteafwerkingen (A1-A3, B1-B3, C1-C3, D1-D3).
- Gereedschappen zoals gereedschapsstaal P20 en aluminium en staal, kleurafstemming van gereedschappen op de vereisten van de klant.
- Wilt u meer weten over spuitgieten op korte termijn? Upload een bestand voor een gratis gietbaarheidstest en spreek vervolgens met een lid van het Protolabs-gietteam. Start de snelle en effectieve productie van onderdelen met onze services.
Zijn de kosten van spuitgieten op korte termijn hoog?
Enkele van de alledaagse producten waarvan de onderdelen zijn gemaakt door middel van spuitgieten zijn elektrische waterkokers, lichtregelaars en toetsenbordtoetsen. Meestal worden dergelijke producten in grote volumes geproduceerd, beginnend bij honderdduizenden sets.
Deze bouwmethode heeft verschillende voordelen, zoals kosteneffectiviteit, veelzijdigheid van materialen en flexibiliteit.
Deze techniek is het meest geschikt voor massaproductie vanwege de veelzijdigheid, beschikbaarheid van talloze soorten materialen en het feit dat het goedkoper is per onderdeel. Deze procedure maakt de huidige betaalbare prijzen mogelijk omdat de kosten van elementen in centen zijn en de cyclustijden in seconden. Het is ook van toepassing op de keuze van materialen, die flexibele elastomeren en polymeren kunnen zijn die kunnen worden gebruikt waar normaal gesproken metalen worden gebruikt.
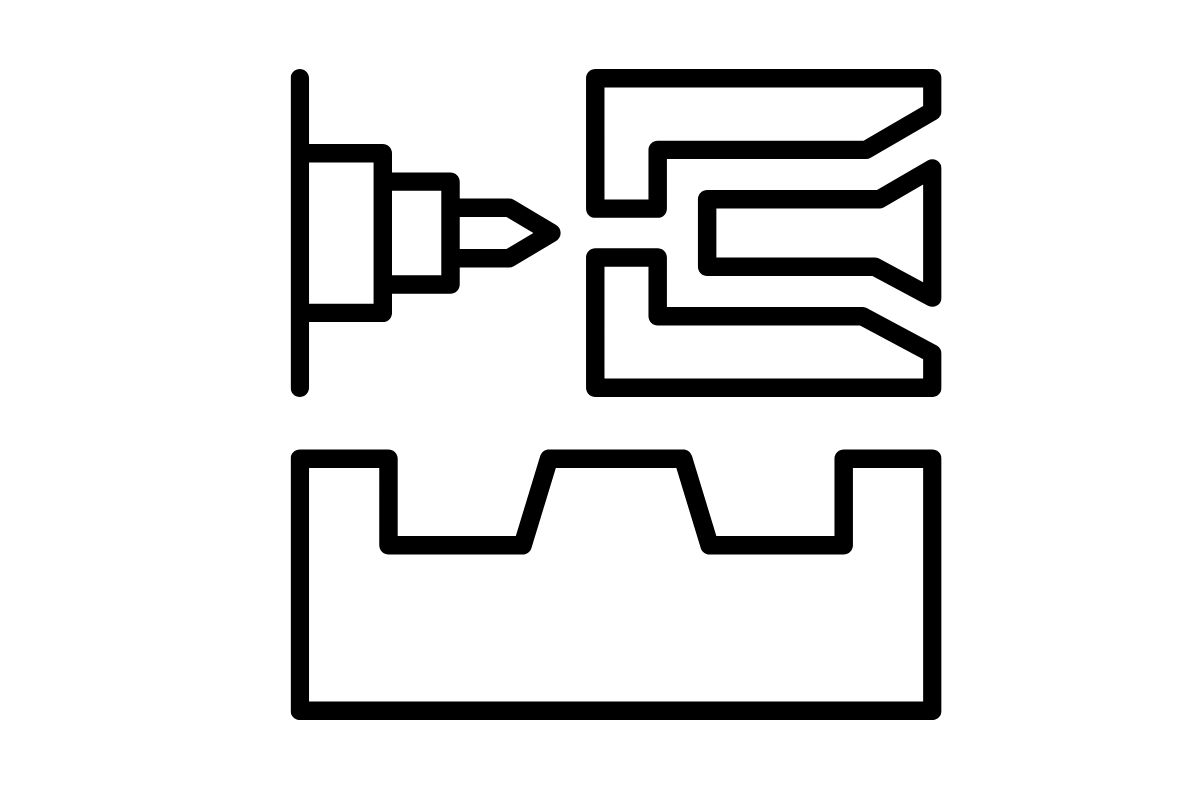
Wat als u minder componenten nodig hebt?
De kosten van gereedschap vormen een belangrijk onderdeel wanneer er een klein aantal onderdelen moet worden vervaardigd. De traditionele methode van het vervaardigen van gereedschap is duur en kost ook veel tijd. Er zijn echter veel moderne tegenhangers die kunnen worden aangewezen om de kosten vandaag de dag te minimaliseren.
De belangrijkste kostenfactoren zijn de opstart- en de terugkerende kosten.
Het gereedschap bevindt zich in de gietpers, het materiaal/de kleur wordt gedroogd en geleverd, de gietcondities worden ingesteld en de eerste kwaliteitscontrolemonsters worden genomen tijdens de opstelling. Het gereedschap moet worden beschermd, de rest van het materiaal moet worden verwijderd en de mal moet worden geopend en opgeslagen na de gietcyclus. Deze opstelling wordt meestal per onderdeel gefactureerd, met name voor kleine series, en kan variëren van een uur tot een halve dag, afhankelijk van de grootte van het gereedschap en het aantal materiaal-/kleurwisselingen.
De procedure van het vormgeven
De kosten die worden gemaakt in de vormfase omvatten de kosten van het gebruikte materiaal, de kosten van de pers en de handmatige of automatische bediening van de media. De kosten van materialen zijn ook afhankelijk van het type materiaal dat wordt gebruikt en de hoeveelheid materiaal die is gekocht, er is een groot verschil tussen het kopen van een kleine hoeveelheid materiaal en een grote hoeveelheid van hetzelfde materiaal. Gespecialiseerde pigmenten kunnen ook een stijging van de kosten veroorzaken, omdat ze worden gebruikt in het proces van het produceren van het eindproduct.
De factoren die de kosten van de pers beïnvloeden, zijn onder andere het schotgewicht, wat de hoeveelheid plastic is die in één cyclus wordt geïnjecteerd, en het tonnage, wat de kracht is die wordt gebruikt om de mal te sluiten tijdens het injecteren. Grote persen zijn duur vanwege de hoge bedrijfskosten en afschrijving van de apparatuur. De kosten kunnen ook worden beïnvloed door de noodzaak van handmatige handelingen, bijvoorbeeld het laden en lossen van inserts of andere post-molding-bewerkingen.
Er zijn twee soorten gereedschappen die volledig geautomatiseerd zijn en continu volume creëren: gereedschappen die bedoeld zijn voor kleine partijen en die handmatig verplaatst en verpakt moeten worden.
Alternatieven voor prototyping
Prototyping in het beoogde productiemateriaal is zeer voordelig. In het geval van prototype- en korte-serieproductie zijn er veel keuzes in gereedschap en is het mogelijk om slechts twee onderdelen te vormen. De snelheid van prototyping en onderdelenproductie kan echter variëren en sommige gebeurtenissen kunnen dagen duren. Dit is afhankelijk van het oppervlak, het materiaal en de geometrie van de te coaten structuur. De vertragingen liggen normaal gesproken tussen de twee en vier weken.
Uitgaven voor gereedschap
De kosten van gereedschap zijn afhankelijk van de complexiteit van het element, de grootte en de tijd die nodig is om het te maken. Mallen zijn niet goedkoop; ze beginnen bij £ 2.000 voor de eenvoudige, maar de meer complexe variëren van £ 5.000 tot £ 7.000. De prijs van grote of complexe items kan oplopen tot £ 30.000. De gegevens van het specifieke project en de gedetailleerde offerte vormen de basis voor een nauwkeurige kostenraming.
Voor projecten met lage volumes spuitgieten is het raadzaam om advies in te winnen bij professionals om een breder begrip te krijgen van de mogelijke kosten en de mogelijke haalbare oplossingen. Als u overweegt om korte series spuitgieten te gebruiken voor uw project en u wilt weten wat de kosten zijn van de benodigde hoeveelheden, neem dan gerust contact met ons op voor een offerte.
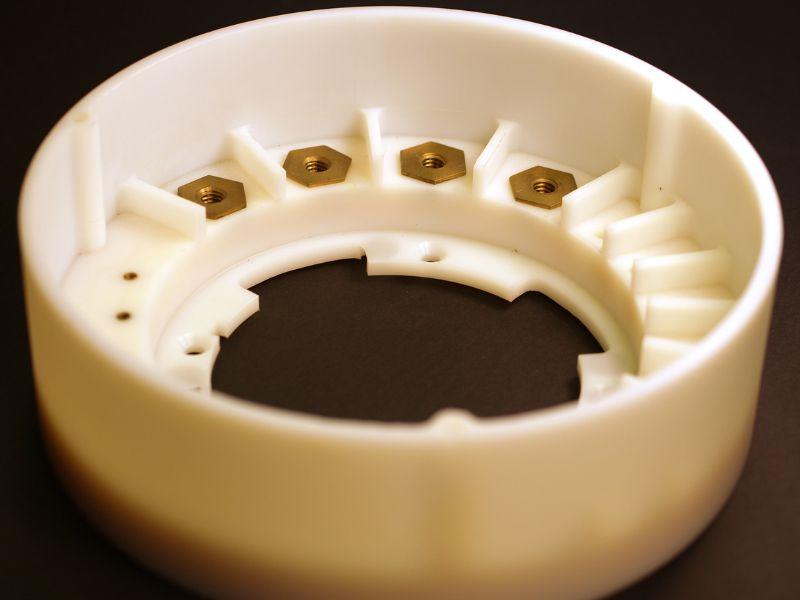
Spuitgietdiensten aangeboden door Sincere Tech
Sincere Tech is een van de 10 kunststof spuitgietbedrijven in China dat meer dan tien jaar geleden werd opgericht en betrokken is geweest bij het ontwerp en de productie van kunststof spuitgegoten onderdelen en goederen. Vanwege onze uitgebreide expertise zijn we in staat om alle fasen van korte-termijn spuitgietprojecten effectief te beheren, waaronder Met deze uitgebreide expertise zijn we in staat om alle fasen van korte-termijn spuitgietprojecten effectief te beheren, waaronder:
Vormontwerp: Wij gebruiken de beste technologieën en matrijstechnologieën om instrumenten te produceren die voldoen aan de behoeften van uw product. Wij maken gereedschapsontwerpen op basis van uw originele tekeningen, schema's of modellen, of we kunnen ze voor u maken. Wij hebben expertise in het gebruik van AutoCAD, SolidWorks, ProE, Cimatron en CADKey CAD-formaten.
Ons team voor het vervaardigen van mallen gebruikt up-to-date CNC-bewerkingstechnologieën om mallen van hoge kwaliteit en nauwkeurig gedimensioneerd te produceren in de kortst mogelijke tijd nadat het ontwerp van de spuitgietmatrijs is voltooid. Dit is een voorbeeld van aangepaste gereedschappen. Wij kunnen prototypes maken voor verschillende thermoplasten, waaronder ABS, HDPE, LDPE, PE, HIPS, TPU en PET.
Prototyping: We gebruiken 3D-printing om elk onderdeel snel te bouwen om ervoor te zorgen dat het in de vorm past en werkt zoals het hoort, voordat de spuitgiettool wordt gebouwd. We bieden FDM-geprinte prototypes in verschillende soorten materialen, zoals ABS, PLA en TPU. We werken samen met andere dienstverleners voor aanvullende prototypingdiensten, zoals urethaangieten, SLS en SLA.
Spuitgieten: De spuitgieten faciliteit wordt gerund door ervaren personeel en de apparatuur kan een klemkracht van 28 tot 240 ton produceren en kan ook reproduceerbaarheid vertonen. Het materiaal dat we verwerken tijdens onze gietbewerkingen varieert van 0 tot 16 ounces per cyclus. Sincere Tech is ook in staat om spuitgietdiensten te leveren voor kleine en grote hoeveelheden producten.
Wij garanderen dat de op maat gemaakte kunststof spuitgietonderdelen die wij bij Sincere Tech leveren van de beste kwaliteit zijn, op tijd worden geleverd en tegen een redelijke prijs.