Kunststofmallen voor beton worden vervaardigd uit verschillende soorten plastic in speciaal ontworpen vormen. Deze mallen worden gebruikt om de vereiste vormen en ontwerpen van betonproducten te leveren. Plastic mallen voor beton zijn herbruikbaar en bieden ook flexibiliteit om een zeer groot scala aan producten te creëren die van beton zijn gemaakt. Deze betonproducten kunnen zo eenvoudig zijn als een blok of kunnen ingewikkeld zijn als een complex decoratief item. De introductie van verschillende plastic mallen voor beton heeft een revolutie teweeggebracht in de manier waarop betonartikelen worden ontworpen en gevormd.
In de industriële sector en doe-het-zelftoepassingen kunststof betonmal biedt een kosteneffectieve oplossing die ook uniek is. Plastic mallen voor beton zijn veel beter dan de traditionele metalen mallen en houten mallen zijn zwaarder en minder duurzaam in vergelijking met plastic mallen voor beton. Bovendien hebben plastic mallen voor beton bewezen vrij gemakkelijk de gewenste complexe en ingewikkelde vormen te produceren, wat niet zo eenvoudig te bereiken is met behulp van metalen of houten mallen.
Er is een breed scala aan toepassingen van kunststofmallen voor beton, waaronder de constructie van architecturale items, betonnen meubels, het maken van decoratieve tuinornamenten en straatstenen. Kunststofmallen voor beton zijn eenvoudig te gebruiken en betaalbaar. Ze leveren resultaten van topkwaliteit in het moderne tijdperk van ontwerp en constructie.
Soorten plastic Concreet Mallen met een overzicht van productieprocessen, belangrijkste kenmerken en basistoepassingen
Er zijn veel soorten plastic betonmallen die worden vervaardigd voor specifieke toepassingen. De basisfactoren waarop verschillende soorten plastic mallen voor beton zijn gebaseerd, zijn de volgende.
- Grootte van het betonproduct
- Complexiteit van het betonproduct
- Verschillende details van het betonproduct
Hieronder worden de belangrijkste soorten kunststofmallen voor beton besproken, evenals hun kenmerken en toepassingen.
-
Spuitgegoten kunststof betonmallen
Deze mallen worden vervaardigd met behulp van een zeer nauwkeurig en goed gecontroleerd productieproces, het zogenaamde spuitgietproces.
Samenvatting van het productieproces van spuitgegoten kunststofbetonmallen
Het proces start met het maken van een gedetailleerd ontwerp van de benodigde kunststof betonmal. Dit wordt bereikt door CAD-software te gebruiken. Het geproduceerde CAD-model wordt vervolgens toegepast om een metalen mal te maken. Daarna worden kunststofkorrels van geselecteerde kunststofmaterialen bereid. In de spuitgietmachine worden deze kunststofkorrels verhit. Het resulterende gesmolten kunststof wordt uiteindelijk in de metalen malholte gespoten.
Dit gebeurt onder hoge druk. Het gesmolten plastic koelt af in de metalen mal en wordt hard. Vervolgens wordt dit gegoten plastic stuk uit de mal geworpen. Vervolgens wordt het trimproces toegepast om overtollig materiaal te verwijderen, zoals flash en worden er afwerkingsprocessen uitgevoerd om de spuitgegoten plastic mallen af te ronden. Dit productieproces is zeer geschikt voor massaproductie. De geproduceerde mallen zijn van consistente kwaliteit.
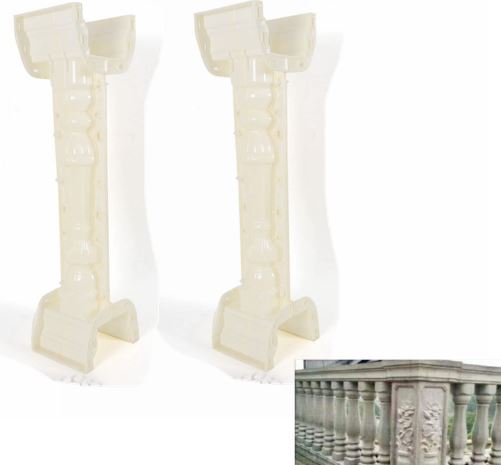
kunststof betonmal
Belangrijkste kenmerken
De belangrijkste kenmerken van deze mallen worden hieronder vermeld.
- Deze mallen zijn zeer nauwkeurig en kunnen fijne details en complexe ontwerpen produceren
- Deze mallen zijn zeer sterk en duurzaam
- Deze mallen zorgen voor hoge productiesnelheden
Basisgebruik
De basistoepassingen van spuitgegoten kunststofmallen omvatten het volgende.
- Ze worden gebruikt bij het vormen van talrijke decoratieve artikelen, zoals tuinornamenten en beelden
- Ze worden gebruikt bij de vorming van ingewikkelde architectonische elementen zoals sierlijke kroonlijsten en balusters
- Ze worden ook gebruikt bij het vormen van zeer gedetailleerde tegels en straatstenen
-
Vacuümgevormde kunststofmallen
Deze mallen worden vervaardigd door een plastic vel te verhitten. Deze hitte wordt gehandhaafd totdat het plastic vel buigzaam wordt. Daarna wordt vacuümzuiging toegepast om het over een mal te vormen.
Samenvatting van het productieproces van vacuümgevormde kunststofbetonmallen
Het proces van het maken van vacuümgevormde kunststofmallen voor beton begint hetzelfde als spuitgegoten kunststofmallen. In de eerste stap wordt het ontwerpen van de malvorm met behulp van CAD-software uitgevoerd. Daarna wordt een masterpatroon of model gemaakt van materialen zoals hout, schuim of hars. Deze materialen worden geselecteerd op basis van het vereiste ontwerp. Daarna wordt het geselecteerde kunststof plaatmateriaal gesneden op basis van de vereiste maat. Deze plaat wordt in een vacuümvormmachine geplaatst. Deze plaat wordt verwarmd totdat deze buigzaam wordt.
Het masterpatroon wordt vervolgens op de maltafel van de machine geplaatst. Het verwarmde plastic vel wordt op dit masterpatroon neergelaten. Het plastic wordt door een vacuümpomp tegen het patroon gezogen, waardoor de gewenste vorm ontstaat. Het geharde en gekoelde plastic wordt vervolgens uit de machine verwijderd. Het daaropvolgende trimproces wordt gebruikt om overtollig materiaal te verwijderen. De plastic mal wordt op een zorgvuldige manier van het masterpatroon gescheiden. De randen van de mal worden gladgestreken om een schone loslating van beton te garanderen wanneer het in toepassingen wordt gebruikt. Daarna ondergaat de mal een kwaliteitscontrole op defecten zoals bellen of onvolledige vorming.
Indien nodig wordt de kunststof betonmal verstevigd voor extra duurzaamheid. Er wordt een losmiddel of coating aangebracht om te helpen bij het ontvormen en de mal wordt getest met een kleine partij beton om te garanderen dat deze correct werkt. Hierna worden de mallen voorbereid voor productie, op de juiste manier opgeslagen om hun conditie te behouden en regelmatig schoongemaakt. Er wordt een laatste inspectie uitgevoerd om te garanderen dat de mallen klaar zijn voor gebruik in de betonproductie, om te garanderen dat ze nauwkeurig gevormd en duurzaam zijn.
Belangrijkste kenmerken
Deze mallen hebben de volgende kenmerken en eigenschappen.
- Deze mallen bieden een kosteneffectieve oplossing in vergelijking met spuitgegoten kunststofmallen, omdat ze veel goedkoper zijn om te produceren.
- Deze mallen hebben de eigenschap flexibel te zijn, waardoor ze ideaal worden geacht voor het maken van grote maar eenvoudige vormen en ontwerpen.
- In deze mallen worden kunststofplaten gebruikt, waardoor deze mallen gemakkelijk te vervoeren en te hanteren zijn.
Basisgebruik
Vacuümgevormde kunststofmallen worden in de volgende situaties gebruikt.
- De tegels en straatstenen die veel groter van formaat zijn, worden gemaakt door vacuümgevormde kunststofmallen
- Deze mallen worden gebruikt voor het vormgeven van tuinelementen en elementaire decoratieve producten
- Vacuümgevormde kunststofmallen worden ook gebruikt om vormen te maken voor doe-het-zelf-betonprojecten
-
Rotatiegegoten kunststofmallen
Deze mallen worden geproduceerd door middel van rotatiegieten. Bij deze methode wordt een roterende mal gevuld met kunststofhars terwijl deze tegelijkertijd wordt verhit vanuit een holle mal.
Samenvatting van het productieproces van kunststofbetonmallen
Het creëren van rotatiegegoten kunststof gietvorm voor beton omvat een gedetailleerd proces om hoge kwaliteit en duurzaamheid te garanderen. Het begint met het ontwerpen van de mal met behulp van CAD-software. Een metalen mal die is gemaakt van aluminium of staal wordt vervaardigd. De fabricagemethode en het materiaal worden geselecteerd op basis van het gewenste ontwerp. Vervolgens wordt de geselecteerde kunststofhars zoals polyethyleen berekend en in de mal geladen. De mal wordt vervolgens zeer goed afgesloten. Deze mal wordt in een oven geplaatst waar hij wordt verwarmd en tegelijkertijd op twee assen wordt gedraaid.
Hierdoor kan de gesmolten hars de binnenoppervlakken gelijkmatig bedekken. Daarna wordt de mal overgebracht naar een koelstation. De rotatie gaat door totdat het plastic is afgekoeld en uiteindelijk is gestold. Nadat het afkoelen en stollen is voltooid, wordt de mal op een voorzichtige manier geopend. Het gevormde plastic deel wordt verwijderd. Het overtollige materiaal wordt, indien aanwezig, afgesneden en de randen en het oppervlak worden gladgemaakt om een schone lossing te garanderen.
De mal wordt geïnspecteerd op defecten zoals bellen of onvolledige vorming en kan worden versterkt om de duurzaamheid te verbeteren. Er wordt een losmiddel of coating aangebracht om het ontvormen te vergemakkelijken en de mal wordt getest met een kleine partij beton om te verzekeren dat deze goed functioneert. Tot slot wordt de mal voorbereid voor herhaald gebruik of massaproductie, met regelmatige reiniging en onderhoud om de levensduur te verlengen en consistente prestaties te verzekeren. Dit uitgebreide proces resulteert in duurzame, nauwkeurig gevormde mallen die klaar zijn voor efficiënte betonproductcreatie.
Belangrijkste kenmerken
Deze mallen bieden de volgende eigenschappen en toepassingen.
- Deze mallen hebben een gelijkmatige wanddikte omdat het kunststofmateriaal gelijkmatig verdeeld is tijdens het productieproces
- Deze mallen zijn zeer geschikt voor het vormen van zware producten vanwege hun duurzaamheid en sterkte
- Rotatiegegoten kunststofmallen hebben de mogelijkheid om grote voorwerpen te vormen die met andere mallen niet mogelijk zijn.
Basisgebruik
- Rotatiegegoten kunststofmallen worden gebruikt om grote betonnen meubelproducten, waaronder tafels en banken, vorm te geven
- Deze mallen worden gebruikt om structurele elementen te vormen, zoals waterpartijen en plantenbakken
- Rotatiegegoten kunststofmallen worden ook gebruikt om grote decoratieve tuinartikelen vorm te geven
4.3D-geprinte kunststofmallen
3D-geprinte kunststofmallen worden vervaardigd uit thermoplastische materialen door een mal laag voor laag op te bouwen op basis van een digitaal model.
Samenvatting van het productieproces
Het proces van het maken van 3D-geprinte kunststof betonmallen wordt op dezelfde manier gestart als voor andere methoden voor het maken van mallen. In de eerste stap wordt het ontwerpen van de mal met behulp van CAD-software uitgevoerd. Deze stap wordt uitgevoerd omdat het helpt bij het maken van nauwkeurige en gedetailleerde vormen. Na voltooiing van het ontwerp wordt het omgezet in een bestandsformaat. Het is belangrijk om op te merken dat dit bestandsformaat compatibel moet zijn met 3D-printen. Over het algemeen worden de volgende twee materialen geselecteerd voor 3D-geprinte plastic mallen.
- Polymelkzuur
- Acrylonitril Butadieen Styreen
Deze geselecteerde materialen worden vervolgens in de 3D-printer geladen. De printer construeert vervolgens de mal laag voor laag, op basis van het digitale ontwerp. Na het printen wordt de mal zeer zorgvuldig uit de printer gehaald. Daarna worden de ondersteunende structuren en extra materialen gereinigd. De mal wordt vervolgens geïnspecteerd op nauwkeurigheid en er worden finishing touches zoals schuren of sealen toegepast om het oppervlak glad te maken.
Er wordt een losmiddel of coating toegevoegd om het verwijderen van het beton gemakkelijker te maken. De mal wordt getest met een kleine hoeveelheid beton om te verzekeren dat het correct presteert en het beton uithardt zoals verwacht. De mal is klaar voor gebruik zodra de effectiviteit ervan is bevestigd door de nodige aanpassingen te doen. Het is relevant om te vermelden dat regelmatige reiniging en onderhoud van de mallen erg belangrijk is vanwege de volgende twee redenen.
- Om de mal in goede conditie te houden
- Om de levensduur te verlengen
De methode van 3D-printen van kunststofmallen maakt de productie van zeer gedetailleerde en op maat gemaakte mallen mogelijk. Dit is zeer geschikt voor talloze betontoepassingen.
Belangrijkste kenmerken
3D-geprinte kunststofmallen bieden de volgende eigenschappen en toepassingen.
- Met 3D-geprinte kunststofmallen kunnen complexe en unieke ontwerpen worden geproduceerd, omdat deze mallen zeer aanpasbaar zijn
- Deze mallen maken snelle en herhaalde veranderingen mogelijk, waardoor deze mallen zeer geschikt zijn voor het vormgeven van nieuwe ontwerpen
- 3D-geprinte kunststofmallen hebben de kwaliteit om gedetailleerde en ingewikkelde vormen te produceren, waardoor deze mallen het meest geschikt zijn voor productie op kleine schaal.
Basisgebruik
- 3D-geprinte kunststofmallen worden gebruikt om op maat gemaakte en veelzijdige decoratieve artikelen te vormen
- Deze mallen worden gebruikt om prototypes te produceren om nieuwe ontwerpen en functies te testen
- De zeer gedetailleerde gespecialiseerde elementen die voornamelijk in de architectuur worden toegepast, worden gevormd door 3D-geprinte kunststofmallen
Voordelen van kunststofmallen voor beton
Kunststofmallen voor beton bieden veel voordelen voor het gieten van beton, waardoor ze een populaire keuze zijn in bouw- en decoratieve toepassingen. De belangrijkste voordelen van kunststofmallen voor beton zijn als volgt.
- Kosteneffectief
Plastic mallen zijn over het algemeen betaalbaarder dan metalen mallen. Ze zijn dus een aantrekkelijke keuze voor zowel kleine als grote projecten.
- Lichtgewicht
Kunststof mallen zijn veel lichter dan metalen mallen. Deze mallen zijn dus gemakkelijker te hanteren, te vervoeren en te positioneren. Dit vermogen leidt uiteindelijk tot lagere arbeidskosten en maakt het gietproces eenvoudiger.
- Flexibiliteit en veelzijdigheid
Kunststof mallen voor beton kunnen worden ontworpen en geproduceerd in een breed scala aan vormen en maten. Ze zijn zeer geschikt voor het creëren van complexe en ingewikkelde ontwerpen die moeilijk of kostbaar zijn met andere materialen.
- Gebruiksgemak
Kunststof mallen vereisen minder onderhoud vergeleken met metalen mallen en zijn eenvoudig te gebruiken. Ze kunnen worden voorgevormd met precieze details, waardoor de noodzaak voor extra afwerkingswerkzaamheden aan het beton wordt verminderd.
- Duurzaamheid
Moderne kunststof mallen voor beton worden vervaardigd van hoogwaardige materialen. Deze materialen hebben de kenmerken van duurzaamheid en kunnen vele malen worden hergebruikt. Bovendien zijn ze bestand tegen impact, slijtage en veel chemicaliën. Dit zal uiteindelijk helpen bij het behouden van hun vorm en functionaliteit in de loop van de tijd.
- Corrosiebestendigheid
Dit is een veel significanter voordeel van plastic mallen boven de metalen mallen. Plastic mallen roesten of corroderen niet, dus deze eigenschap is met name voordelig in de volgende scenario's.
- bij het werken met betonmengsels die corrosieve stoffen kunnen bevatten
- wanneer de mallen worden blootgesteld aan vocht
- Gladde oppervlakteafwerking
Kunststof mallen bieden een zeer gladde en goede oppervlakteafwerking op het beton. Vervolgens vermindert het de vereisten voor extra oppervlaktebehandelingen of afwerking. Dit verbetert als resultaat de esthetische kwaliteit van het eindproduct en biedt een kosteneffectieve oplossing.
- Snelle productie
Kunststof mallen zorgen voor snelle productiesnelheden, vooral met methoden als vacuümvormen of 3D-printen. Deze eigenschap van kunststof mallen is handig voor projecten met strakke deadlines.
- Herbruikbaar
Kunststof mallen zijn een duurzame optie voor beton omdat ze ontworpen zijn om herbruikbaar te zijn. Als ze regelmatig goed onderhouden worden, kan dit hun levensduur verlengen en de noodzaak voor constante vervanging verminderen.
- Aanpassing
Om te voldoen aan specifieke ontwerpvereisten kunnen plastic mallen eenvoudig worden aangepast. Deze flexibiliteit van maatwerk maakt de productie van veelzijdige of op maat gevormde betonnen items mogelijk.
- Anti-aanbak eigenschappen
Het is belangrijk om op te merken dat veel plastic mallen behandeld of gecoat zijn om de anti-aanbakeigenschappen te hebben. Dit voorkomt vervolgens dat het beton aan de mal blijft plakken. Zo wordt het ontvormen gemakkelijker, waardoor het risico op beschadiging van het eindproduct wordt verminderd.
Basisfactoren om te overwegen bij het gebruik van plastic Concreet Schimmels
Het gebruik van kunststofvormen voor beton vereist een aantal belangrijke factoren om te overwegen om de beste resultaten en levensduur van de mallen te bereiken. De details van deze factoren zijn als volgt.
- Materiaalkeuze
Het type en soort plastic dat wordt gebruikt bij de productie van de mallen is van groot belang. Het is bekend dat verschillende plastics verschillende eigenschappen hebben. Polyethyleen met hoge dichtheid biedt uitstekende duurzaamheid en slagvastheid in vergelijking met andere plastics. Het selecteren van het juiste plastic voor specifieke behoeften en vereisten zal dus helpen bij het behalen van de beste resultaten en het verlengen van de levensduur van de mal.
- Vormontwerp
Het is relevant om te vermelden dat de complexiteit van het ontwerp van de mal uiteindelijk het eindproduct beïnvloedt. Daarom moeten mallen met grote zorg worden ontworpen om functies en aspecten zoals ontwerphoeken en loslaatmechanismen op te nemen om ervoor te zorgen dat betonproducten soepel uitkomen en de mal intact blijft. Bovendien kunnen gedetailleerde ontwerpen extra precisie vereisen in zowel de malproductie- als de verwerkingsprocedures.
- Lossingsmiddelen
De belangrijkste factor om te overwegen bij het gebruik van de plastic mallen voor beton is de toepassing van het juiste losmiddel. Deze middelen worden gebruikt om te voorkomen dat het beton aan de mal blijft plakken. De algemeen gebruikte soorten losmiddelen zijn de volgende.
- Op olie gebaseerde losmiddelen
- Losmiddelen op waterbasis
- Losmiddelen op siliconenbasis
- Poedervrijmakingsmiddelen
- Natuurlijke en milieuvriendelijke losmiddelen
- Schuimlosmiddel
- Hogetemperatuur-losmiddelen
Het is belangrijk om op te merken dat de keuze van het lossingsmiddel compatibel moet zijn met het kunststofmateriaal van de mal. Dit is noodzakelijk om de kwaliteit en de integriteit van het betonproduct te behouden.
- Temperatuur en uitharding
Kunststof mallen voor beton kunnen behoorlijk gevoelig zijn voor temperatuurvariaties. Het is dus belangrijk om de uithardingsomstandigheden op een zorgvuldige manier te beheren. Dit is van groot belang vanwege het volgende.
- Overmatige hitte kan de mal kromtrekken
- Onvoldoende warmte kan de uitharding van beton beïnvloeden
De belangrijkste factor om ervoor te zorgen dat het gietproces acceptabel is, is om ervoor te zorgen dat de uithardingstemperatuur geschikt is voor zowel de mal als het betonmengsel.
- Reiniging en onderhoud
Reiniging en onderhoud van kunststof mallen voor beton is van vitaal belang en cruciaal. De basisreden hiervoor is dat restbeton problemen kan veroorzaken voor toekomstig gebruik van de mallen. Regelmatige reiniging en onderhoud met geschikte methoden is dus belangrijk. Bovendien moeten er regelmatig routinecontroles worden uitgevoerd op slijtage. Dit zal uiteindelijk helpen bij het behouden van de effectiviteit van de mal.
- Milieu-impact
Het is belangrijk om rekening te houden met de milieueffecten van de plastic mallen voor beton. Het plastic materiaal dat voor de mal is geselecteerd, kan, als het niet biologisch afbreekbaar en niet recyclebaar is, schadelijke effecten op het milieu hebben. Echter, in tegenstelling daarmee zal het selecteren van recyclebare of biologisch afbreekbare kunststoffen zeker een positieve impact op het milieu hebben. Bovendien is het op de juiste manier afvoeren of recyclen van oude mallen ook van groot belang om de negatieve en schadelijke impact op het milieu te verminderen.
Conclusie
Kunststof mallen zijn een praktische en kosteneffectieve keuze voor het gieten van beton, en bieden flexibiliteit en duurzaamheid. Kunststof mallen voor beton bieden effectieve oplossingen voor het gieten van beton en bieden waarde in complexe en ingewikkelde ontwerpen. Ze maken het gemakkelijk om gedetailleerde en aangepaste ontwerpen te produceren, terwijl ze lichtgewicht en corrosiebestendig zijn. Met de juiste behandeling en onderhoud bieden kunststof mallen betrouwbare prestaties en hoogwaardige resultaten in verschillende toepassingen. Kunststof mallen hebben de mogelijkheid om een breed scala aan betonmengsels te verwerken en gieten omgevingen effectief. Regelmatig onderhoud, zorgvuldige behandeling en geschikte opslag verbeteren de lange levensduur en prestaties van de kunststof betonmallen. Over het algemeen zijn ze een uitstekend hulpmiddel voor zowel decoratieve als structurele betonprojecten.