Hoe kunststof stoelvorm comfortabele moderne stoelen produceert
Plastic stoelen zie je bijna overal waar je kijkt, van de drukke cafés langs de straten van de stad tot de hoekjes van je eigen huis. Maar heb je er wel eens over nagedacht hoe deze stoelen tot leven komen?
Het verrassend simpele antwoord is niets anders dan de plastic stoelmal, het gereedschap dat de stoelen vormt waarop u elke dag zit
Een plastic stoelmal is niet alleen een negatieve ruimte. De mensen die in een plastic stoelmalfabriek werken, zijn als beeldhouwers die gesmolten plastic transformeren in comfortabele en functionele zitoplossingen.
Maar wat maakt de plastic mal stoel in de eerste plaats zo voordelig? Lees verder om meer te leren over de verborgen voordelen van plastic stoel mallen.
Efficiëntie opnieuw gedefinieerd: massaproductie voor maximaal comfort
Stel je een wereld voor waarin elke plastic stoel met de hand werd gemaakt. De kosten en tijd die ermee gemoeid zijn, zouden onbetaalbaar zijn! De plastic stoelmallen elimineren deze hindernis volledig. De plastic stoelmal stelt fabrikanten in staat om identieke stoelen te produceren met hoge snelheden, wat de productietijd en de totale kosten aanzienlijk verkort. Het resulteert in een bredere beschikbaarheid van betaalbare zitoplossingen voor iedereen, van eigenaren van drukke restaurants tot budgetbewuste gezinnen.
Consistente sterkte voor een comfortabele basis
Een slappe stoel kan ronduit oncomfortabel zijn, en bovendien een ernstig gevaar voor de veiligheid vormen. Een kunststof stoelmal garandeert een consistente dikte van de wanden en algehele structurele integriteit op alle geproduceerde stoelen. Het zorgt ervoor dat gebruikers altijd veilig zijn en biedt een betrouwbare basis van comfort, of u nu verdiept bent in een werkvergadering op kantoor of geniet van een ontspannen lunch.
Design Delights: Een stoel voor elke gelegenheid
Niet alle zitbehoeften zijn gelijk. Een plastic mold chair voorziet hierin, omdat het een verbazingwekkende reeks aan ontwerpmogelijkheden biedt. De ontwerpen van een plastic mold chair kunnen worden aangepast om de perfecte stoel voor elk doel te creëren, van ergonomische bureaustoelen met verstelbare lendensteun tot stapelbare bistrostoelen voor buitencafés. Het garandeert dat het niveau van functionaliteit en comfort is afgestemd op het specifieke beoogde gebruik.
Materiële wonderen: de juiste comfortformule kiezen
Een betrouwbare plastic stoel mallen fabriek gebruikt niet alleen één type plastic. Verschillende materialen kunnen worden gekozen op basis van de gewenste balans van gewicht, duurzaamheid en comfort.
Polypropyleen of PP is bijvoorbeeld een populaire keuze omdat het makkelijk schoon te maken en licht van gewicht is. Hierdoor is het een aanbevolen keuze voor tuinmeubilair.
Aan de andere kant biedt polyethyleen met hoge dichtheid of HDPE een ongeëvenaarde flexibiliteit en sterkte, wat ideaal is voor gebieden met veel verkeer, zoals scholen en restaurants. Deze flexibiliteit zorgt ervoor dat de stoel is vervaardigd met de juiste "comfortformule" voor het doel waarvoor hij bedoeld is.
Meer dan alleen zitplaatsen: een mal met vele toepassingen
De plastic keuzemal wordt niet alleen gebruikt voor traditionele stoelen. Ze kunnen ook van pas komen voor een verscheidenheid aan andere functionele en comfortabele producten, waaronder strandstoelen, speeltoestellen voor kinderen en ergonomische zitcomponenten voor rolstoelen. Deze veelzijdigheid maakt ze een waardevolle aanwinst in een breed scala aan industrieën.
1. De minimale levensduur van de kunststof stoelmal.
De normale standaard voor de levensduur van de stoelmal moet minimaal 0,5 miljoen shorts of zelfs meer zijn, dus de kwaliteit van het staal is erg belangrijk, sommige spuitgietbedrijven bieden staal van slechte kwaliteit aan om geld te besparen en de klant een lagere prijs te bieden, maar wanneer de klant de mal in hun fabriek heeft, kunnen er na een paar maanden problemen ontstaan, om de goede kwaliteit van de kunststof stoelmal te behouden, raden we onze klanten meestal aan om 718H of P20 malstaal te gebruiken. Dit zorgt ervoor dat de mal minimaal 0,5 miljoen zonder problemen meegaat.
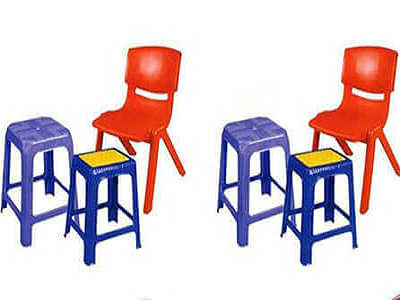
plastic tafel stoel mal
2. De cyclustijd van de kunststof stoelmal tijdens de productie,
3. Hoe optimaliseer je het gewicht van het kunststof stoelvormdeel, maar behoud je toch dezelfde sterkte?