Wat is spuitgieten?
Spuitgietmatrijs is een gereedschap dat gebruikt wordt in het spuitgietproces om onderdelen te maken door materiaal in een matrijsholte te injecteren. Het is meestal gemaakt van staal (H13, P20, 1.2312, 1.2344, S136H, enz.) of aluminium en is zorgvuldig ontworpen om te voldoen aan de vorm en specificaties van het eindproduct.
De spuitgietmatrijs is verdeeld in twee helften: de holtehelft en de kernhelft. Deze helften worden tijdens het spuitgietproces aan elkaar geklemd en het materiaal wordt via een sprue in de matrijsholte geïnjecteerd, waar het afkoelt en stolt tot de gewenste vorm. Als het onderdeel gevormd is, gaat de mal open en wordt het onderdeel uitgeworpen. De mal kan opnieuw worden gebruikt om meerdere onderdelen te maken.

Wat is spuitgieten?
Soorten spuitgietmatrijzen
Onder de vele variëteiten injectiematrijzen vind je onder andere:
Holtespecifieke schimmel
Elke cyclus van het spuitgietproces kan slechts één onderdeel genereren als er een matrijs met één holte wordt gebruikt. Het maken van een onderdeel met deze matrijs is zo eenvoudig als het injecteren van plastic hars, wachten tot het is afgekoeld en dan het eindproduct verwijderen.
Als je de productiekosten van mallen met meerdere schoten vergelijkt met mallen met één holte, is de eerste meestal voordeliger. Als het te duur zou zijn om een klein aantal onderdelen in één keer te maken, zijn deze mallen ideaal voor prototypes en kleine productieseries.

Matrijs met enkele caviteit
De voordelen van single-shot mallen zijn onder andere:
- Effectief qua kosten: de productie van een single-shot mal is vaak goedkoper dan de productie van een multi-shot mal.
- Eenvoudig ontwerp: Productie- en onderhoudsgemak door eenvoud van ontwerp: Enkelvoudige matrijzen zijn vaak minder complex qua lay-out dan meervoudige matrijzen.
- Flexibiliteit: Een groot aantal toepassingen, zoals prototypes en kleine productieseries, zijn geschikt voor het gebruik van mallen met één holte.
De nadelen van single-shot mallen zijn onder andere:
- Beperkte productie: Deze beperking maakt mallen met één holte ongeschikt voor productieruns met grote volumes, omdat ze maar één onderdeel per cyclus kunnen maken.
- Complexe onderdelen: Matrijzen met één caviteit zijn niet geschikt voor het maken van ingewikkelde onderdelen met veel onderdelen; daarvoor heb je een matrijs met meerdere caviteiten of een familiematrijs nodig.
- Inefficiëntie: In vergelijking met mallen met meerdere caviteiten zijn single-shot mallen minder efficiënt omdat ze door hun beperkte capaciteit maar één onderdeel per cyclus kunnen maken.
Mallen met meerdere holtes:
Matrijzen met meerdere caviteiten zijn een type spuitgietmatrijs met meer dan één caviteit. Hierdoor kan het spuitgietproces tijdens elke beurt meer dan één onderdeel maken. Afhankelijk van de toepassing kunnen deze mallen worden gemaakt met dezelfde of verschillende gaten.
Omdat ze veel onderdelen in één cyclus kunnen maken, worden mallen met meerdere caviteiten meestal gebruikt voor spuitgieten in grote volumes productieruns. Hierdoor kunnen ze de productie-efficiëntie verhogen en tegelijkertijd de kosten per onderdeel verlagen.

meervoudige holtevorm
De voordelen van mallen met meerdere caviteiten zijn onder andere:
- Productie van grote volumes: Matrijzen met meerdere caviteiten zijn gemaakt voor grootschalige productieruns, waardoor het gemakkelijk is om veel onderdelen te maken.
- Kosteneffectief: mallen met meerdere caviteiten zijn meestal goedkoper dan mallen met één caviteit omdat ze meer onderdelen in één keer kunnen maken.
- Complexe onderdelen: Mallen met meerdere caviteiten kunnen worden gebruikt om onderdelen te maken die ingewikkeld zijn en veel onderdelen hebben.
De nadelen van mallen met meerdere caviteiten zijn onder andere:
- Complex ontwerp: Mallen met meerdere caviteiten zijn moeilijker te maken en bij te houden dan mallen met één caviteit omdat hun ontwerp ingewikkelder is.
- verhoogde de matrijskosten: Matrijzen met meerdere caviteiten kunnen duurder zijn dan matrijzen met één caviteit omdat verschillende caviteiten tijdens het spuitgietproces aan verschillende spanningen en slijtage onderhevig kunnen zijn. Dit kan leiden tot een minder efficiënte productie en hogere reparatiekosten.
Hotrunner-mal:
Warmlopermal is een type spuitgietmatrijs dat een hotrunnersysteem gebruikt om het gesmolten kunststofmateriaal in de matrijsholten te brengen. Het hot runnersysteem bestaat uit een verwarmd spruitstuk dat de gesmolten kunststof verdeelt over individuele spuitmondjes die vervolgens in de matrijsholten worden geleid.

Warmlopermal
De voordelen van hot runner-mallen zijn onder andere:
- Verbeterde onderdeelkwaliteit: Hotrunner-mallen kunnen onderdelen met een betere kwaliteit produceren, omdat ze de hoeveelheid kunststof die overblijft in de runners minimaliseren, waardoor het risico op defecten zoals flash, short shots en sink marks afneemt.
- Verhoogde productie-efficiëntie: Hotrunner-mallen kunnen de productie-efficiëntie verhogen omdat er geen handmatige ingrepen meer nodig zijn om de runners van de spuitgietproducten te verwijderen, waardoor de cyclustijd korter wordt en de algehele productiesnelheid toeneemt.
- Energie-efficiëntie: Hot runner-mallen zijn energiezuiniger dan traditionele cold runner-mallen, omdat ze de hoeveelheid kunststof die in de runners wordt verspild tot een minimum beperken.
De nadelen van hot runner-mallen zijn onder andere:
- Complex ontwerp: Hotrunner-mallen hebben een complexer ontwerp dan traditionele coldrunner-mallen, waardoor ze duurder zijn om te produceren en te onderhouden.
- Meer onderhoud: Hot runner mallen hebben meestal meer onderhoud nodig dan cold runner mallen, omdat ze een complexer verwarmingssysteem hebben dat goed onderhouden moet worden.
- Kwetsbaarheid voor verstopping: Hot runner-mallen kunnen gevoelig zijn voor verstopping, vooral bij het verwerken van materialen met een hoge viscositeit of met een lange vloeilengte, omdat de gesmolten kunststof dan kan stollen in de runners. Dit kan leiden tot een verminderde productie-efficiëntie en hogere onderhoudskosten.
Stapel mallen:
Stapelvorm is een type spuitgietmatrijs waarmee meerdere caviteiten tegelijk kunnen worden gevormd in één machinecyclus. Stapelvormen zijn in wezen twee of meer matrijzen die op elkaar gestapeld zijn, waarbij elke matrijs een enkel onderdeel produceert.

Stapelvorm
De voordelen van stapelmallen zijn onder andere:
- Verhoogde productie-efficiëntie: Stapelvormen maken het mogelijk om meerdere onderdelen tegelijk te gieten, waardoor de productie efficiënter verloopt en de cyclustijd korter wordt.
- Minder materiaalverspilling: Stapelmallen minimaliseren materiaalverspilling, omdat ze de productie van meerdere onderdelen mogelijk maken met een enkele hoeveelheid kunststofmateriaal.
- Lagere kosten: Stackmallen kunnen kosteneffectiever zijn dan mallen met één caviteit, omdat ze de productie van meerdere onderdelen met één machinecyclus mogelijk maken.
De nadelen van stapelmallen zijn onder andere:
- Complex ontwerp: Stack molds kunnen een complexer ontwerp hebben dan molds met één holte, waardoor ze duurder zijn om te produceren en te onderhouden.
- Verminderde kwaliteit van onderdelen: Stapelvormen kunnen onderdelen van mindere kwaliteit maken, omdat de aanwezigheid van meerdere holtes kan leiden tot een verhoogd risico op defecten zoals uitvloeiing, korte schotjes en verzinkplekken.
- Meer onderhoud: Stack molds hebben meestal meer onderhoud nodig dan single-cavity molds, omdat ze een complexer ontwerp hebben dat goed onderhouden moet worden.
Familieschimmels:
Family molds, ook wel bekend als multi-impression molds, wat vergelijkbaar is met multiple cavity mold, zijn een vorm van spuitgieten waarbij meerdere onderdelen met licht verschillende ontwerpen tegelijkertijd in één machinecyclus worden gevormd. Dit wordt bereikt door meerdere caviteiten in de matrijs te hebben die verschillende onderdelen met verschillende vormen en afmetingen kunnen produceren.
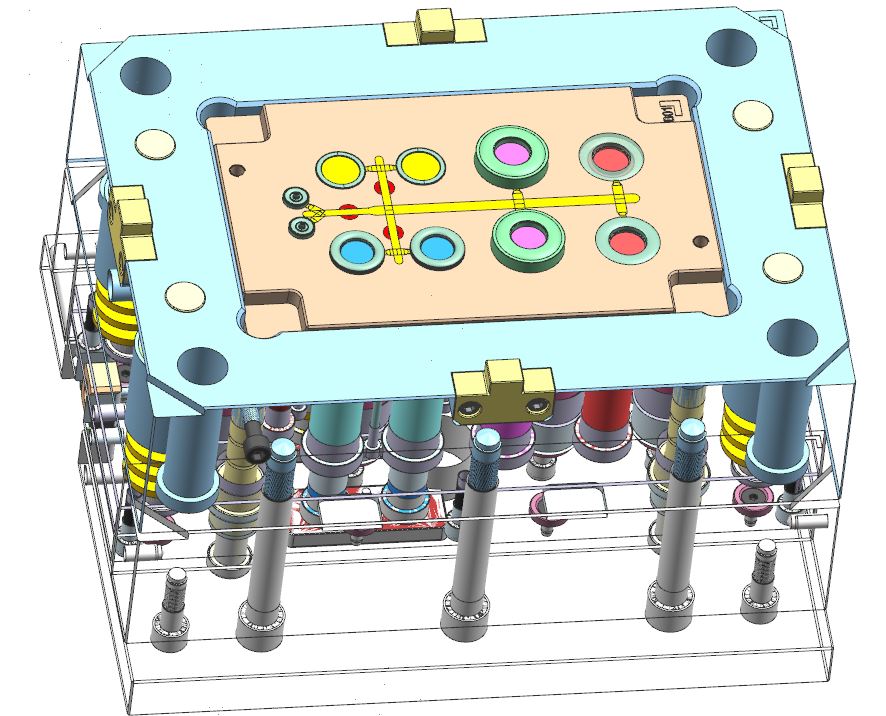
familie schimmel
De voordelen van familieschimmels zijn onder andere:
- Verhoogde productie-efficiëntie: Met familievormen kunnen meerdere onderdelen met verschillende ontwerpen tegelijk worden gegoten, wat de productie-efficiëntie verhoogt en de cyclustijd verkort.
- Lagere kosten: Familiemallen kunnen kosteneffectiever zijn dan het produceren van meerdere mallen met één holte voor elk onderdeel, omdat ze de productie van meerdere onderdelen met één machinecyclus mogelijk maken.
- Flexibiliteit: Gezinsmallen maken de productie van verschillende onderdelen met verschillende ontwerpen mogelijk, waardoor ze een veelzijdige optie zijn voor fabrikanten die een reeks producten moeten maken.
De nadelen van familieschimmels zijn onder andere:
- Complex ontwerp: Familievormen kunnen een complexer ontwerp hebben dan mallen met één holte, waardoor ze duurder zijn om te produceren en te onderhouden.
- Verminderde kwaliteit van onderdelen: Gezinsmallen kunnen onderdelen produceren met een verminderde kwaliteit, omdat de aanwezigheid van meerdere holtes kan leiden tot een verhoogd risico op defecten zoals flash, short shots en sink marks.
Tweeschots mallen:
Tweeschots schimmel (2-schots spuitgieten), ook bekend als overgieten of multi-shot mallen of 2K mallen, zijn een vorm van spuitgieten waarbij twee verschillende materialen in één machinecyclus samen worden gevormd. Bij dit proces wordt een eerste materiaal (basismateriaal) in een matrijs gespoten en vervolgens wordt een tweede materiaal (overmold materiaal) op het eerste materiaal gespoten.

Twee schots mal
De voordelen van mallen met twee schoten zijn onder andere:
- Verhoogde functionaliteit: Two-shot mallen maken de combinatie mogelijk van twee verschillende materialen met verschillende eigenschappen om onderdelen te maken met een verhoogde functionaliteit.
- Verbeterde esthetiek: Two-shot mallen maken de integratie van verschillende kleuren of texturen in een enkel onderdeel mogelijk, waardoor een visueel aantrekkelijker product ontstaat.
- Kortere assemblagetijd: Door twee materialen in één onderdeel te combineren, kunnen tweeschotsmallen de noodzaak voor extra assemblagestappen verminderen, waardoor de productietijd en -kosten afnemen.
De nadelen van mallen met twee schoten zijn onder andere:
- Complex ontwerp: Two-shot mallen zijn complexer in ontwerp dan single-shot mallen, waardoor ze duurder zijn om te produceren en te onderhouden.
- Langere cyclustijd: Two-shot mallen hebben meestal een langere cyclustijd in vergelijking met single-shot mallen, omdat bij dit proces twee materialen in één machinecyclus worden gevormd.
- Compatibiliteitsproblemen: Two-shot mallen vereisen dat de twee materialen die gegoten worden compatibel zijn met elkaar en goed zullen hechten, waardoor het belangrijk is om de materialen die gebruikt worden zorgvuldig te selecteren.
Mallen losschroeven:
Schroefmallen zijn een soort spuitgietmatrijzen die speciaal ontworpen zijn om onderdelen met schroefdraad te produceren, zoals doppen, deksels en containers. Deze mallen zijn uniek omdat ze een mechanisme hebben waarmee de kern van de mal kan draaien terwijl de holte stil blijft staan, waardoor het spuitgietproduct uit de mal kan worden geschroefd nadat het is afgekoeld en gestold.

mal losschroeven
Voordelen van het losschroeven van mallen zijn onder andere:
- Hoge efficiëntie: Met losschroevende mallen kunnen onderdelen met schroefdraad efficiënt in één machinecyclus worden geproduceerd, waardoor de productietijd en -kosten dalen.
- Verbeterde nauwkeurigheid: Met losdraaiende mallen kunnen onderdelen met schroefdraad nauwkeurig worden geproduceerd met een consistente steek en schroefdraaddiepte, waardoor de kwaliteit en prestaties van het eindproduct verbeteren.
- Veelzijdigheid: Met losschroevende mallen kunnen veel verschillende onderdelen met verschillende soorten en maten schroefdraad worden gemaakt, waardoor ze een veelzijdige optie zijn voor veel verschillende toepassingen.
Nadelen van het losschroeven van mallen zijn onder andere:
- Complex ontwerp: Niet-schroevende mallen hebben een complexer ontwerp dan andere soorten mallen, waardoor ze duurder zijn om te produceren en te onderhouden.
- Langere cyclustijd: Losdraaiende mallen hebben meestal een langere cyclustijd in vergelijking met andere soorten mallen, omdat de kern van de mal moet worden geroteerd.
- Slijtage: Het draaiende mechanisme van losdraaiende mallen kan na verloop van tijd aan slijtage onderhevig zijn, waardoor regelmatig onderhoud nodig is om de mal goed te laten functioneren.
Inklapbare kernvorm:
Matrijzen met een inklapbare kern zijn een vorm van spuitgieten die worden gebruikt om holle onderdelen met interne holtes te maken, zoals buizen, pijpen en andere complex gevormde onderdelen. Deze mallen gebruiken een uniek ontwerp waardoor de kern van de mal in zichzelf kan instorten, waardoor de interne holte van het onderdeel ontstaat.

Inklapbare kernvormcomponent
Voordelen van mallen met een inklapbare kern zijn onder andere:
- Verbeterde efficiëntie: Met opvouwbare kernmallen kunnen holle onderdelen in één enkele machinecyclus worden geproduceerd, waardoor de productietijd en -kosten dalen.
- Verbeterde productkwaliteit: Matrijzen met een inklapbare kern zorgen voor een preciezere en consistentere binnenholte, waardoor de algehele kwaliteit van het uiteindelijke onderdeel verbetert.
- Veelzijdigheid: Met mallen met een opvouwbare kern kunnen veel verschillende onderdelen met verschillende vormen en afmetingen worden gemaakt, waardoor ze een veelzijdige optie zijn voor veel verschillende toepassingen.
Nadelen van mallen met een inklapbare kern zijn onder andere:
- Complex ontwerp: Matrijzen met een opvouwbare kern hebben een complexer ontwerp dan andere matrijstypes, waardoor ze duurder zijn om te produceren en te onderhouden.
- Langere cyclustijd: Matrijzen met een inklapbare kern hebben meestal een langere cyclustijd in vergelijking met andere soorten matrijzen, omdat bij het proces de kern van de matrijs inklapt.
- Slijtage: Het inklapmechanisme van de kern kan na verloop van tijd aan slijtage onderhevig zijn, waardoor regelmatig onderhoud nodig is om de mal goed te laten functioneren.
Voordelen en nadelen van kunststof spuitgietmatrijzen
Voordelen van Spuitgieten:
- Productie van grote volumes: Spuitgieten is een zeer efficiënte methode om grote hoeveelheden identieke onderdelen te produceren. Dit maakt het ideaal voor massaproductie van consumptiegoederen, auto-onderdelen en andere producten die grote hoeveelheden gelijkaardige onderdelen vereisen.
- Precisie: Het proces maakt een zeer nauwkeurige controle mogelijk van de maatnauwkeurigheid en de consistentie van het product. Dit komt door het gebruik van streng gecontroleerde verwerkingsomstandigheden en de stijfheid van de spuitgietmachine en de matrijs.
- Snelheid: Spuitgieten is een snel proces, met cyclustijden van slechts enkele seconden voor kleine onderdelen. Hierdoor kunnen fabrikanten grote hoeveelheden onderdelen produceren in een relatief korte tijd.
- Rendabel: De kosten voor het produceren van onderdelen via spuitgieten worden voordeliger naarmate het productievolume toeneemt. Dit komt doordat de matrijs gebruikt kan worden om veel onderdelen te maken tijdens de levensduur en de kosten per onderdeel dalen naarmate het volume toeneemt.
- Veelzijdigheid: Spuitgieten kan worden gebruikt om onderdelen te maken van een groot aantal materialen, waaronder kunststoffen, metalen en elastomeren. Deze veelzijdigheid maakt het een populaire keuze voor fabrikanten die onderdelen van verschillende materialen moeten maken, afhankelijk van de specifieke vereisten van het product.
- Automatisering: Spuitgietmachines kunnen geautomatiseerd worden, waardoor het proces efficiënter verloopt en er minder handenarbeid nodig is. Dit kan ook de consistentie en kwaliteit van de spuitgietproducten verbeteren.
- Complexe vormen: Spuitgieten kan gebruikt worden om complexe vormen en ontwerpen te produceren, inclusief onderdelen met ingewikkelde details en strakke toleranties. Dit is mogelijk dankzij de nauwkeurige controle van het spuitgietproces en de mogelijkheid om zeer gedetailleerde matrijzen te ontwerpen.
- Materiaalkeuze: Bij spuitgieten kunnen fabrikanten kiezen uit een groot aantal materialen, elk met hun eigen unieke eigenschappen, zoals sterkte, flexibiliteit en weerstand tegen hitte, chemicaliën en slijtage. Dit maakt het mogelijk om voor elke toepassing het beste materiaal te kiezen en onderdelen met de gewenste eigenschappen te produceren.
Nadelen van spuitgieten:
- Hoge initiële kosten: De initiële kosten voor het maken van de matrijs kunnen hoog zijn, vooral voor complexe vormen en ontwerpen. Dit kan het proces minder kosteneffectief maken voor kleine hoeveelheden onderdelen of voor prototypes.
- Beperkte ontwerpflexibiliteit: Als de matrijs eenmaal gemaakt is, kan het moeilijk en duur zijn om het ontwerp te veranderen. Dit kan de mogelijkheid beperken om ontwerpwijzigingen of -verbeteringen aan te brengen als de matrijs eenmaal is gemaakt.
- Materiaalafval: Spuitgieten genereert een aanzienlijke hoeveelheid afvalmateriaal, dat duur kan zijn om af te voeren en schadelijk kan zijn voor het milieu. Dit kan ook de productiekosten verhogen en de algemene efficiëntie van het proces verlagen.
- Doorlooptijd: De doorlooptijd voor het maken van de matrijs en het opzetten van het spuitgietproces kan lang zijn, vooral voor complexe onderdelen. Dit kan het productontwikkelingsproces vertragen en de mogelijkheid om producten snel op de markt te brengen beperken.
- Beperkingen oppervlakteafwerking: Spuitgieten kan op sommige onderdelen geen oppervlakteafwerking van hoge kwaliteit produceren, vooral op onderdelen met ingewikkelde details of nauwe toleranties. Dit kan de mogelijkheid beperken om onderdelen te produceren met een esthetisch uitzicht van hoge kwaliteit.
- Materiaalcompatibiliteit: Compatibiliteit tussen het materiaal en de matrijs kan een uitdaging zijn, omdat sommige materialen niet goed werken met bepaalde soorten matrijzen of speciale verwerkingsomstandigheden vereisen. Dit kan de mogelijkheid om onderdelen van bepaalde materialen te maken beperken en de productiekosten verhogen.
- Beperkte onderdeelgrootte: Spuitgieten wordt beperkt door de grootte van de matrijs en de klemkracht van de spuitgietmachine. Dit kan de grootte van de onderdelen die geproduceerd kunnen worden beperken en de kosten voor het produceren van grotere onderdelen verhogen.
- Secundaire bewerkingen: Sommige onderdelen moeten na het spuitgieten nog nabewerkt worden, zoals bijsnijden of afwerken. Dit kan de productiekosten verhogen en de algehele efficiëntie van het proces beperken. Natuurlijk kunnen deze problemen soms worden opgelost door de spuitgietmatrijs te verbeteren.
Veelvoorkomende problemen met een spuitgietmatrijs
Als je eenmaal op het gebied van kunststof spuitgieten werkt, zijn er altijd problemen die je elke dag moet oplossen. Hier volgen enkele veelvoorkomende uitdagingen bij het spuitgieten:
Problemen met vervorming:
Vervorming is een veel voorkomend probleem bij spuitgieten en verwijst naar een vervorming van het spuitgietproduct nadat het uit de matrijs is gehaald. Dit kan gebeuren door verschillende factoren, waaronder:

Warp-vervorming
- Onjuiste koeling: Als het onderdeel te snel of ongelijkmatig afkoelt, kan het kromtrekken omdat het materiaal in verschillende mate krimpt en samentrekt.
- Restspanning: Spuitgieten creëert restspanning in het onderdeel door de hoge druk die gebruikt wordt tijdens het spuitgieten. Deze spanning kan kromtrekken veroorzaken als hij niet goed wordt weggenomen.
- Materiaalkeuze: Sommige materialen zijn gevoeliger voor kromtrekken dan andere. Zo zullen materialen met een lage hittebestendigheid of een lage dimensionale stabiliteit eerder kromtrekken.
- Vormontwerp: Het ontwerp van de mal kan ook bijdragen aan kromtrekken, vooral als de mal geen goede koeling of materiaalstroom toelaat.
- Verwerkingsomstandigheden: Inconsistente verwerkingsomstandigheden, zoals verschillende injectiesnelheden, matrijstemperaturen en drukniveaus, kunnen kromtrekken veroorzaken.
Om kromtrekken te voorkomen is het belangrijk om het juiste materiaal te kiezen, het matrijsontwerp en de verwerkingsomstandigheden te optimaliseren en de juiste koel- en materiaalbehandelingspraktijken toe te passen. Daarnaast kan het nodig zijn om nabewerkingen te doen, zoals gloeien, om de restspanning te verminderen en de dimensionale stabiliteit te verbeteren.
Flashproblemen:
Flashdefecten zijn een term die bij spuitgieten wordt gebruikt om te verwijzen naar het overtollige materiaal dat tijdens het spuitgieten uit de matrijs wordt geperst. Flash treedt op wanneer het materiaal buiten de bedoelde matrijsholte stroomt en in de deellijn, of de ruimte tussen de twee matrijshelften, terechtkomt.

Vormflits of bramen
Flitsen kan door verschillende factoren worden veroorzaakt, waaronder:
- Onjuist matrijsontwerp: Een slecht ontworpen matrijs kan flash veroorzaken doordat er materiaal in de deellijn lekt.
- Inconsistente verwerkingsomstandigheden: Wisselende verwerkingsomstandigheden, zoals injectiesnelheid en druk, kunnen flash veroorzaken.
- Materiaalcompatibiliteit: Sommige materialen zijn mogelijk niet compatibel met de matrijs en kunnen flash veroorzaken wanneer ze in de deellijn vloeien.
- Slijtage van de mal: Na verloop van tijd kan de mal verslijten en flash veroorzaken als het materiaal in de deellijn lekt.
Spatting kan verschillende negatieve effecten hebben, zoals het verminderen van de maatnauwkeurigheid van het onderdeel, het verhogen van het uitvalpercentage en het bemoeilijken van nabewerkingen. Om vervorming te minimaliseren is het belangrijk om het matrijsontwerp, de verwerkingsomstandigheden en de materiaalkeuze te optimaliseren en de matrijs regelmatig te onderhouden en te repareren als dat nodig is.
Laslijnen:
Laslijnen zijn een veel voorkomend probleem bij spuitgieten en verwijzen naar zichtbare markeringen op het oppervlak van het spuitgietproduct waar twee stromen gesmolten kunststofmateriaal samenkomen en stollen. Laslijnen ontstaan wanneer het materiaal niet volledig samensmelt wanneer het in de spuitgietmatrijs vloeit. kunststof mal holte, waardoor een zichtbare lijn op het oppervlak van het onderdeel achterblijft.

Laslijn
Laslijnen kunnen door verschillende factoren worden veroorzaakt, waaronder:
- Onvoldoende smeltstroom: Als het materiaal niet genoeg tijd heeft om te vloeien en volledig samen te smelten, kan er een laslijn ontstaan.
- Verkeerd ontwerp van de poort: Een slecht ontworpen poort, het punt waar het gesmolten materiaal de matrijsholte binnenkomt, kan een lasnaad veroorzaken.
- Inconsistente verwerkingsomstandigheden: Wisselende verwerkingsomstandigheden, zoals injectiesnelheid en druk, kunnen een laslijn veroorzaken.
- Materiaalcompatibiliteit: Sommige materialen zijn niet compatibel met de mal en kunnen een lasnaad veroorzaken wanneer ze in de malholte stromen.
Laslijnen kunnen de sterkte van het onderdeel verzwakken en de algemene kwaliteit ervan verminderen. Om laslijnen tot een minimum te beperken, is het belangrijk om het matrijsontwerp, de verwerkingsomstandigheden en de materiaalselectie te optimaliseren en de juiste materiaalbehandeling toe te passen. Daarnaast kan het nodig zijn om speciale verwerkingstechnieken te gebruiken, zoals mallen met meerdere caviteiten of hotrunnersystemen, om de vorming van laslijnen te verminderen.
Gootstenen:
Zinkvlekken, ook wel "sink", "vacuüm sink" of "skin" genoemd, zijn verzonken of ingedrukte gebieden op het oppervlak van een spuitgegoten kunststof onderdeel. Ze worden meestal veroorzaakt door een aantal factoren, waaronder:
- Harskrimp: Als de hars afkoelt en stolt, kan deze ongelijkmatig krimpen, wat kan leiden tot zinkvlekken.
- Slechte materiaalstroom: Als de hars niet gelijkmatig in alle gebieden van de mal vloeit, kunnen er holtes of verzonken gebieden ontstaan.
- Onvoldoende verpakkingsdruk: Als de injectiedruk niet hoog genoeg is, kan de hars de mal niet volledig vullen, wat leidt tot zinkvlekken.
- Problemen met matrijsontwerp: Het matrijsontwerp, inclusief de plaatsing en grootte van de poort, het runnersysteem en de ontluchting, kunnen allemaal de kwaliteit van het spuitgietproduct beïnvloeden en bijdragen aan zinksporen.
Zinkvlekken kunnen de esthetische kwaliteit en functionaliteit van een spuitgietproduct aantasten en een bron van frustratie zijn voor fabrikanten en eindgebruikers. Om zinkvlekken tot een minimum te beperken, is het belangrijk om zorgvuldig na te denken over de factoren die ertoe bijdragen, zoals materiaalselectie, matrijsontwerp, verwerkingsparameters en onderdeelontwerp, en waar nodig aanpassingen te doen om het spuitgietproces te optimaliseren.
Stromingsmerken:
Vloeisporen zijn een veel voorkomend probleem bij spuitgieten en verwijzen naar zichtbare sporen of strepen op het oppervlak van het spuitgietproduct die worden veroorzaakt door de stroming van het gesmolten kunststofmateriaal wanneer het de matrijsholte vult. Vloeisporen ontstaan wanneer het materiaal ongelijkmatig vloeit en een zichtbare markering achterlaat op het oppervlak van het spuitgietproduct.
Vloeimerken kunnen door verschillende factoren worden veroorzaakt, waaronder:
- Onvoldoende vloei van de smelt: Als het materiaal niet genoeg tijd heeft om te vloeien en de vormholte te vullen, kunnen er vloeisporen ontstaan.
- Verkeerd ontwerp van de poort: Een slecht ontworpen poort, het punt waar het gesmolten materiaal de matrijsholte binnenkomt, kan vloeimerken veroorzaken.
- Inconsistente verwerkingsomstandigheden: Wisselende verwerkingsomstandigheden, zoals injectiesnelheid en druk, kunnen stromingssporen veroorzaken.
- Materiaalcompatibiliteit: Sommige materialen zijn mogelijk niet compatibel met de mal en kunnen vloeisporen veroorzaken wanneer ze in de malholte stromen.
Vloeisporen kunnen de algehele kwaliteit en het cosmetische uiterlijk van het onderdeel verminderen. Om vloeiplekken te minimaliseren is het belangrijk om het matrijsontwerp, de verwerkingsomstandigheden en de materiaalkeuze te optimaliseren en de juiste materiaalbehandeling toe te passen. Daarnaast kan het nodig zijn om speciale verwerkingstechnieken te gebruiken, zoals mallen met meerdere caviteiten of hotrunnersystemen, om de vorming van vloeiplekken te verminderen.
Problemen met krassen:
Krasproblemen zijn zichtbare markeringen of krassen op het oppervlak van een spuitgegoten onderdeel die worden veroorzaakt door fysiek contact tussen het onderdeel en de matrijs of andere vreemde voorwerpen tijdens het spuitgietproces. Krasproblemen kunnen om verschillende redenen voorkomen, waaronder:
- Slecht matrijsontwerp: Onjuist ontworpen matrijzen of matrijsonderdelen kunnen krassen veroorzaken op het oppervlak van het onderdeel.
- Onvoldoende smering: Als de matrijs en de onderdelen van de matrijs niet goed gesmeerd zijn, kunnen er krassen ontstaan op het oppervlak van het onderdeel.
- Slechte materiaalbehandeling: Slechte behandeling van het ruwe materiaal of afgewerkte onderdelen kan krassen veroorzaken op het oppervlak van het onderdeel.
- Puin in de matrijs: Vreemde voorwerpen of puin in de matrijsholte kunnen krassen veroorzaken op het oppervlak van het onderdeel.
Krasproblemen kunnen de algehele kwaliteit en het cosmetische uiterlijk van het onderdeel verminderen. Om krasproblemen tot een minimum te beperken, is het belangrijk om een goed matrijsontwerp, smering, materiaalbehandeling en onderhoudspraktijken te implementeren. Daarnaast kunnen regelmatige reiniging en inspectie van de matrijs en matrijsonderdelen helpen om krasproblemen te voorkomen.
Uitwerpsporen:
Uitwerpsporen zijn zichtbare sporen op het oppervlak van een spuitgegoten onderdeel die worden veroorzaakt door de uitwerppennen of andere uitwerpmechanismen tijdens het spuitgietproces. Uitwerpsporen ontstaan wanneer de uitwerppennen het spuitgietproduct uit de matrijsholte duwen en zichtbare sporen achterlaten op het oppervlak van het spuitgietproduct.
Uitwerpsporen kunnen door verschillende factoren worden veroorzaakt:
- Verkeerd ontwerp van de uitwerppennen: Als de uitwerppennen niet goed ontworpen zijn, kunnen ze zichtbare sporen achterlaten op het oppervlak van het onderdeel.
- Overmatige kracht: Als de uitwerppinnen te veel kracht uitoefenen op het onderdeel tijdens het uitwerpen, kunnen ze diepere en beter zichtbare sporen achterlaten op het oppervlak van het onderdeel.
- Inconsistente uitwerpkracht: Als de uitwerpkracht niet consistent is van de ene uitwerppen naar de andere, kan dit resulteren in ongelijke uitwerpsporen op het oppervlak van het onderdeel.
- Slechte oppervlakteafwerking: Als de oppervlakteafwerking van de matrijsholte niet glad is, kan dit uitwerpsporen veroorzaken op het oppervlak van het onderdeel.
Uitwerpsporen kunnen de algehele kwaliteit en het cosmetische uiterlijk van het onderdeel verminderen. Om uitwerpsporen tot een minimum te beperken, is het belangrijk om het ontwerp van de uitwerppennen en de oppervlakteafwerking van de matrijsholte te optimaliseren en de juiste onderhouds- en inspectiepraktijken toe te passen. Daarnaast kan het nodig zijn om speciale uitwerpmechanismen te gebruiken, zoals luchtondersteunde uitwerping of zijwaartse uitwerping, om uitwerpsporen te minimaliseren.
Problemen met korte schoten:
Een short shot is een veel voorkomend probleem bij spuitgieten dat optreedt wanneer het gesmolten kunststofmateriaal de matrijsholte niet volledig vult, wat resulteert in een spuitgietproduct dat kleiner is dan de gewenste grootte. Short shots kunnen om verschillende redenen voorkomen:
- Onvoldoende materiaal: Als er niet genoeg materiaal is om de matrijsholte te vullen, kan er een kort schot ontstaan.
- Verkeerde verwerkingsomstandigheden: Als de verwerkingsomstandigheden, zoals de injectiesnelheid en -druk, niet goed zijn ingesteld, kan er een kort schot ontstaan.
- Slecht ontwerp van de mal: Een slecht ontworpen matrijs kan een kort schot veroorzaken, omdat het materiaal mogelijk niet in alle delen van de matrijsholte kan stromen.
- Degradatie van materiaal: Als het materiaal is aangetast of niet goed is opgeslagen, kan dit een kortsluiting veroorzaken.
Korte shots kunnen de algemene kwaliteit en functionaliteit van het onderdeel verminderen en resulteren in verspilling van materiaal en verwerkingstijd. Om short shots tot een minimum te beperken, is het belangrijk om het matrijsontwerp, de verwerkingsomstandigheden en de materiaalselectie te optimaliseren en de juiste materiaalbehandelingspraktijken toe te passen. Daarnaast kunnen regelmatige controle en onderhoud van de spuitgietapparatuur short shots helpen voorkomen.
Luchtval en brandplekken:
Luchtvallen en brandvlekken zijn veelvoorkomende problemen bij spuitgieten die kunnen ontstaan door onjuiste verwerkingsomstandigheden of een verkeerd matrijsontwerp.
Luchtinsluitingen ontstaan wanneer er tijdens het spuitgietproces lucht vast komt te zitten in de matrijsholte, waardoor het materiaal rond de luchtzak stroomt in plaats van hem te vullen. Dit kan leiden tot zichtbare holtes of pockets in het spuitgietproduct. Luchtinsluitingen kunnen door verschillende factoren veroorzaakt worden, waaronder:
- Onvoldoende materiaalstroom: Als het materiaal niet goed in de matrijsholte stroomt, kan er lucht worden ingesloten.
- Verkeerd ontwerp van de poort: Als de poort niet goed ontworpen is, kan er lucht in de matrijsholte terechtkomen.
- Onvoldoende ontluchting: Als de schimmel niet goed wordt ontlucht, kan er lucht in de holte van de schimmel komen.
Brandvlekken ontstaan wanneer het kunststofmateriaal te lang wordt blootgesteld aan hoge temperaturen, waardoor het wordt afgebroken en er zichtbare vlekken of verkleuringen ontstaan op het oppervlak van het onderdeel. Brandvlekken kunnen door verschillende factoren worden veroorzaakt, waaronder:
- Te hoge verwerkingstemperaturen: Als de verwerkingstemperaturen te hoog worden ingesteld, kan het materiaal afbreken en kunnen er brandplekken ontstaan.
- Onvoldoende koeltijd: Als het onderdeel niet goed wordt gekoeld, kan het materiaal afbreken en kunnen er brandplekken ontstaan.
- Slecht ontwerp van de mal: Een slecht ontworpen mal kan ervoor zorgen dat het materiaal te lang wordt blootgesteld aan hoge temperaturen, wat kan leiden tot brandplekken.
Om luchtinsluitingen en brandvlekken tot een minimum te beperken, is het belangrijk om de verwerkingsomstandigheden en het matrijsontwerp te optimaliseren en de juiste controle- en onderhoudspraktijken toe te passen. Daarnaast kan het nodig zijn om speciale verwerkingstechnieken te gebruiken, zoals gieten bij lage temperatuur of vacuümgieten, om luchtinsluitingen en brandvlekken te minimaliseren.
Verwerking om een spuitgietmatrijs te maken:
Het maken van een spuitgietmatrijs bestaat uit verschillende stappen:
Vormontwerp:
Het ontwerp van spuitgietmatrijzen is een kritisch aspect van het spuitgietproces, omdat het een directe invloed heeft op de kwaliteit, efficiëntie en kosten van de spuitgietproducten.
Een goed ontworpen spuitgietmatrijs produceert onderdelen die voldoen aan de gewenste grootte, vorm en kwaliteitseisen, terwijl ze ook efficiënt te produceren en gemakkelijk te onderhouden zijn.
De belangrijkste factoren waarmee je rekening moet houden bij het ontwerpen van een spuitgietmatrijs zijn onder andere:
- Geometrie van het onderdeel: Bij het ontwerp van het spuitgietproduct moet rekening worden gehouden met de gewenste grootte, vorm en kenmerken van het product.
- Materiaalkeuze: Het materiaal dat gebruikt wordt voor de matrijs en het spuitgietproduct moet geselecteerd worden op basis van factoren zoals kosten, sterkte en thermische stabiliteit.
- Matrijsholten: Het aantal en de opstelling van de matrijsholtes moet worden gekozen om te voldoen aan de eisen van het productievolume.
- Afsluitsysteem: Het ontwerp van het afsluitsysteem is kritisch, omdat het bepaalt hoe het kunststofmateriaal in de matrijsholte stroomt.
- Uitwerpsysteem: Het uitwerpsysteem moet zo ontworpen zijn dat de gegoten onderdelen zonder schade uit de matrijs gehaald kunnen worden.
- Koelsysteem: Het koelsysteem moet zo worden ontworpen dat de spuitgietproducten gelijkmatig en snel afkoelen, waardoor de cyclustijd wordt verkort en de kwaliteit wordt verbeterd.
- Trekhoeken: Het ontwerp van de matrijs moet de juiste trekhoeken bevatten om de gevormde onderdelen uit de matrijs te kunnen halen.
- Ontluchting: De mal moet worden ontlucht zodat de lucht uit de holte van de mal kan ontsnappen, waardoor het risico op luchtinsluitingen en brandplekken wordt verminderd.
- Onderhoud en reparatie: De matrijs moet ontworpen zijn voor eenvoudig onderhoud en reparatie, om stilstand te minimaliseren en de productie-efficiëntie te verhogen.
Het ontwerpen van een spuitgietmatrijs is een complex proces dat expertise vereist op gebieden als werktuigbouwkunde, materiaalkunde en productie. Het is belangrijk om samen te werken met een gerenommeerde matrijsontwerper om ervoor te zorgen dat de matrijs correct wordt ontworpen en aan je behoeften voldoet.
CNC-programmering:
CNC (Computer Numerical Control) programmeren is een essentiële stap in de productie van een spuitgietmatrijs. Zodra het matrijsontwerp klaar is, is de volgende stap CNC-programmering. Hieronder volgen de belangrijkste stappen van het CNC programmeren voor de productie van spuitgietmatrijzen:
- Vertaling CAD-model: Het CAD-model wordt vertaald naar een CAM-programma (Computer Aided Manufacturing), dat wordt gebruikt om de CNC-code voor de matrijs te maken.
- CNC-code maken: De CNC-code wordt gemaakt in het CAM-programma, dat instructies geeft aan de CNC-machine over hoe de matrijsonderdelen moeten worden verplaatst en gesneden. De code houdt rekening met het materiaal en de dikte van de matrijsonderdelen en met de gewenste vormen en kenmerken.
- Gereedschapspad maken: Het gereedschapspad wordt gemaakt in het CAM-programma, dat het pad bepaalt dat het snijgereedschap zal volgen om de matrijsonderdelen te bewerken. Het freespad houdt rekening met de vormen en eigenschappen van de matrijsonderdelen en de mogelijkheden van de CNC-machine.
- Simulatie: De CNC-code en het gereedschapspad worden gesimuleerd in het CAM-programma om ervoor te zorgen dat de matrijsonderdelen correct en volgens de juiste specificaties worden bewerkt.
- CNC-bewerking: De CNC-code wordt in de CNC-machine geladen, die vervolgens de code en het gereedschapspad gebruikt om de matrijsonderdelen te bewerken.
CNC programmering is een kritieke stap in het productieproces van spuitgietmatrijzen, omdat het de nauwkeurigheid en kwaliteit van de matrijsonderdelen bepaalt. Het is belangrijk om samen te werken met een CNC-programmeur die ervaring heeft met het programmeren voor spuitgietmatrijzen om ervoor te zorgen dat de CNC-code correct en volgens de juiste specificaties wordt gemaakt. In deze stap worden ook de koelkanalen, het uitwerpsysteem en andere functies aan de matrijsonderdelen toegevoegd om ervoor te zorgen dat ze goed functioneren.
Mallen BOM-lijst inkoop
Een BOM-lijst (Bill of Materials) voor matrijzen is een uitgebreide lijst van alle onderdelen en materialen die nodig zijn om een spuitgietmatrijs te maken. De lijst bevat de volgende onderdelen:
- Staal voor de malbasis en kern/holte-inzetstukken
- Onderdelen voor warmlopers
- Onderdelen van het koelsysteem, zoals waterleidingen en koelblokken
- Onderdelen van het uitwerpsysteem, zoals uitwerppennen en -hulzen
- Onderdelen voor spruestrekker
- Verwarmingsbanden en temperatuurregelaars
- Gietvormonderdelen, zoals bussen, geleidepennen en vergrendelingen
- Inzetstukken voor matrijzen, zoals schuiven en lifters
- Speciale artikelen, zoals datumstempels en aangepaste logo's
De BOM-lijst voor matrijzen is een belangrijk hulpmiddel voor inkoop en productie, omdat het een duidelijke en gedetailleerde lijst geeft van de onderdelen en materialen die nodig zijn om de matrijs te maken. De lijst wordt gebruikt om ervoor te zorgen dat alle benodigde onderdelen besteld en bij de hand zijn wanneer de mal klaar is om geproduceerd te worden.
Het is belangrijk om met een gerenommeerde leverancier te werken als je onderdelen voor een spuitgietmatrijs koopt, omdat de kwaliteit en betrouwbaarheid van deze onderdelen een grote invloed kunnen hebben op de efficiëntie en kwaliteit van het spuitgietproces.
Ruwe bewerking van vormen:
Met voorbewerking van spuitgietmatrijzen wordt de eerste bewerking van de stalen onderdelen van een spuitgietmatrijs bedoeld om de basisvorm en -grootte van de matrijs te verkrijgen. Deze stap wordt meestal uitgevoerd met CNC-machines (Computer Numerical Control). Hieronder volgen de belangrijkste stappen voor het voorbewerken van spuitgietmatrijzen:
- Staalselectie: De eerste stap is het selecteren van het juiste type staal voor de matrijs, zoals P20 of H13, gebaseerd op de gewenste eigenschappen van het gegoten onderdeel.
- Staal snijden: Het staal wordt met een CNC-machine in de juiste maat en vorm gesneden. Deze stap kan ook het boren en tappen van gaten voor de koel- en uitwerpsystemen omvatten.
- Staalprofilering: De stalen onderdelen worden vervolgens bewerkt om de basisvorm van de mal te verkrijgen, inclusief de kern en holte-inzetstukken.
- Staalinspectie: De bewerkte onderdelen worden vervolgens geïnspecteerd om te garanderen dat ze voldoen aan de vereiste toleranties en specificaties.
- Reinigen van staal: De bewerkte onderdelen worden gereinigd en ontbraamd om ruwe randen of vuil te verwijderen.
Het voorbewerkingsproces is een belangrijke stap in het spuitgietproces, omdat het de basis legt voor de laatste, zeer nauwkeurige bewerkings- en polijststappen die zullen volgen. Het is belangrijk om ervoor te zorgen dat de voorbewerking nauwkeurig en volgens de juiste specificaties gebeurt, zodat de matrijs goed functioneert en onderdelen met de gewenste kwaliteit produceert.
Warmtebehandeling van gietstaal:
Warmtebehandeling van gietstaal is het proces van verwarmen en koelen van de stalen onderdelen van een spuitgietmatrijs om hun mechanische eigenschappen en maatvastheid te verbeteren. Het doel van warmtebehandeling is om het staal te harden, restspanningen te verlichten en de slijtvastheid en taaiheid te verbeteren. Dit is speciaal voor het geharde staal van spuitgietmatrijzen, als je voorgehard staal gebruikt om de spuitgietmatrijs te maken, hoef je deze warmtebehandeling niet uit te voeren. Hieronder volgen de belangrijkste stappen voor de warmtebehandeling van matrijzenstaal:
- Uitgloeien: De stalen onderdelen worden verhit tot een specifieke temperatuur, meestal tussen 800-900°C, en dan langzaam afgekoeld om de interne spanningen te verlichten en de bewerkbaarheid van het staal te verbeteren.
- Harden: De stalen onderdelen worden verhit tot een hoge temperatuur, meestal boven de kritieke temperatuur, en dan snel afgekoeld, meestal door afschrikken in olie of water. Dit proces verhardt het staal en verbetert de slijtvastheid.
- Temperen: Na het harden worden de stalen onderdelen getemperd door ze gedurende een bepaalde tijd op een lagere temperatuur te verhitten om de taaiheid en maatvastheid van het staal te verbeteren.
Het warmtebehandelingsproces is cruciaal om ervoor te zorgen dat de stalen onderdelen van een spuitgietmatrijs de gewenste mechanische eigenschappen en maatvastheid hebben, die essentieel zijn voor het produceren van hoogwaardige spuitgietproducten. Het is belangrijk om samen te werken met een warmtebehandelingsbedrijf dat ervaring heeft met het behandelen van matrijsstaal om ervoor te zorgen dat de warmtebehandeling correct en volgens de juiste specificaties wordt uitgevoerd.
Schimmelholte en kern fijnbewerken:
Mould cavity and core fine machining is het proces van het nauwkeurig bewerken van de interne oppervlakken van de matrijsholte en de kerninzetstukken om de uiteindelijke vorm en grootte van de matrijs te verkrijgen. Deze stap wordt meestal uitgevoerd met CNC-machines (Computer Numerical Control) met hoge precisie en nauwkeurigheid. Hieronder volgen de belangrijkste stappen voor het machinaal bewerken van de matrijsholte en de kern:
- Oppervlaktevoorbereiding: Het oppervlak van de matrijsholte en de kerninzetstukken worden gereinigd en gepolijst om restpuin of ruwheid te verwijderen.
- Oppervlaktebewerking: De interne oppervlakken van de matrijsholte en de kerninzetstukken worden bewerkt met CNC-machines om de uiteindelijke vorm en grootte van de matrijs te verkrijgen. Dit omvat het maken van de ingewikkelde details en kenmerken van het spuitgietproduct, zoals tekst, logo's en ondersnijdingen.
- Oppervlakte-inspectie: De bewerkte oppervlakken worden geïnspecteerd om er zeker van te zijn dat ze voldoen aan de vereiste toleranties en specificaties.
- Oppervlaktepolijsten: De interne oppervlakken van de matrijsholte en de kerninzetstukken worden hoogglans gepolijst om de oppervlaktekwaliteit van de spuitgietproducten te verbeteren en het risico op defecten te verkleinen.
Fijnbewerking is een kritieke stap in het spuitgietproces, omdat het de kwaliteit en nauwkeurigheid van de spuitgietproducten bepaalt. Het is belangrijk om samen te werken met een leverancier die ervaring heeft met de fijne bewerking van matrijsholtes en -kerndelen om ervoor te zorgen dat de bewerking correct en volgens de juiste specificaties wordt uitgevoerd. In deze stap worden ook het uitwerpsysteem, de koelkanalen en andere functies van de matrijs toegevoegd om ervoor te zorgen dat de matrijs goed werkt.
Vonkverspaning:
EDM (Electrical Discharge Machining) is een proces dat wordt gebruikt om ingewikkelde en zeer nauwkeurige vormen te maken in metalen onderdelen, waaronder die in een spuitgietmatrijs. Het proces maakt gebruik van elektrische vonken om materiaal van het matrijsoppervlak te verwijderen, waardoor de gewenste vorm ontstaat. Hieronder volgen de belangrijkste stappen van EDM-bewerking:
- Oppervlaktevoorbereiding: Het oppervlak van het te bewerken matrijsonderdeel wordt gereinigd en gepolijst om restpuin of ruwheid te verwijderen.
- EDM instellen: De EDM-machine wordt ingesteld met de juiste parameters, waaronder de vonkafstand, pulsduur en het elektrodemateriaal, gebaseerd op het materiaal en de vorm van het matrijsonderdeel.
- Vonkerosie: De EDM-machine produceert elektrische vonken die materiaal van het matrijsonderdeel verwijderen, waardoor de gewenste vorm ontstaat. Dit proces vindt stapsgewijs plaats, waarbij de vonkmachine het materiaal geleidelijk erodeert totdat de uiteindelijke vorm is bereikt.
- Oppervlakte-inspectie: Het bewerkte oppervlak wordt geïnspecteerd om er zeker van te zijn dat het voldoet aan de vereiste toleranties en specificaties.
EDM-bewerking wordt vaak gebruikt voor matrijsonderdelen met complexe vormen of kleine, ingewikkelde details die moeilijk te realiseren zijn met andere bewerkingsprocessen. Het wordt ook gebruikt om de scherpe randen en hoeken te produceren die essentieel zijn voor het goed functioneren van een spuitgietmatrijs.
Het proces is zeer nauwkeurig en accuraat, waardoor het ideaal is voor het produceren van hoogwaardige spuitgietproducten. Het is belangrijk om samen te werken met een EDM-leverancier die ervaring heeft met EDM-bewerking voor spuitgietmatrijzen om er zeker van te zijn dat het proces correct en volgens de juiste specificaties wordt uitgevoerd.
Polijsten van het schimmeloppervlak:
Spuitgietpolijsten is de laatste stap in het productieproces van spuitgietmatrijzen. Het gaat om het gladmaken van de oppervlakken van de matrijsonderdelen om ervoor te zorgen dat het eindproduct een glad en gelijkmatig oppervlak heeft. Hieronder volgen de belangrijkste stappen voor het polijsten van spuitgietmatrijzen:

polijsten van kunststof mallen
- Oppervlaktevoorbereiding: De oppervlakken van de matrijsonderdelen worden gereinigd en voorbereid op het polijsten. Alle resterende ruwe plekken of bewerkingssporen worden verwijderd om een glad oppervlak voor het polijsten te garanderen.
- Ruw polijsten: De eerste stap in het polijsten is ruw polijsten, waarbij grote onvolkomenheden in het oppervlak van de matrijsonderdelen worden verwijderd. Deze stap wordt meestal uitgevoerd met een schuurmiddel met een grove korrel, zoals schuurpapier of een schuurborstel.
- Fijn polijsten: Fijn polijsten is de volgende stap, waarbij het oppervlak van de matrijsonderdelen fijner wordt gemaakt. Deze stap wordt uitgevoerd met een schuurmiddel met een fijnere korrel, zoals fijner schuurpapier of een schuurborstel.
- Polijsten: Polijsten is de laatste stap in het polijsten, waarbij een polijstschijf en polijstpasta worden gebruikt om een hoogglanzende afwerking op de matrijsonderdelen te krijgen.
- Inspectie: Na het polijsten worden de matrijsonderdelen grondig geïnspecteerd om er zeker van te zijn dat ze een glad en gelijkmatig oppervlak hebben, zonder krassen, barsten of andere onvolkomenheden.
Het polijsten van spuitgietmatrijzen is belangrijk omdat het de kwaliteit van het eindproduct beïnvloedt. Een goed gepolijste matrijs resulteert in een product met een glad en gelijkmatig oppervlak, wat belangrijk is voor de functionaliteit en esthetiek van het product. Het is belangrijk om samen te werken met een ervaren schimmelpolijster om ervoor te zorgen dat de onderdelen van de matrijs worden gepolijst volgens de juiste specificaties en op het gewenste kwaliteitsniveau.
Vorm fitting
Matrijzen maken is een gespecialiseerde functie binnen het spuitgieten en omvat het assembleren, installeren en testen van spuitgietmatrijzen. Matrijsmonteurs moeten ervoor zorgen dat de onderdelen van de matrijs correct worden gemonteerd en correct functioneren en dat de matrijs onderdelen produceert met de gewenste kwaliteits- en prestatienormen. Enkele van de belangrijkste verantwoordelijkheden van matrijzenmakers zijn:
- De matrijsonderdelen assembleren: Matrijsmeesters zijn verantwoordelijk voor het assembleren van de verschillende onderdelen van een spuitgietmatrijs, waaronder de holte en kernonderdelen, het runnersysteem en eventuele hulponderdelen.
- De mal monteren op de pasmachine: Moldmaster moet in staat zijn om de mal te monteren op de mal montage machine op een manier die zorgt voor een goede uitlijning en werking van de mal, als heeft geen enkele mal montage machine gebruik dan handmatige manier om de mal monteren, dit is de meeste bedrijven doen.
- De matrijs testen: De matrijsmeester is verantwoordelijk voor het testen van de matrijs om ervoor te zorgen dat deze onderdelen produceert met de gewenste kwaliteit en prestatienormen. Dit omvat het inspecteren van de onderdelen op defecten, zoals kromtrekken, krimpen of andere kwaliteitsproblemen.
- De matrijs aanpassen: Als er problemen worden gevonden tijdens de testfase, is moldmaster verantwoordelijk voor het maken van de nodige aanpassingen aan de matrijs om ervoor te zorgen dat deze onderdelen produceert die voldoen aan de gewenste specificaties.
- Problemen oplossen: Moldmaster moet in staat zijn om problemen te identificeren en op te lossen die zich kunnen voordoen tijdens het matrijsmontageproces.
Voor het maken van mallen is een combinatie van technische kennis, handvaardigheid en oog voor detail nodig. Matrijzenmakers moeten kunnen werken met een breed scala aan gereedschappen en machines en de complexe processen begrijpen die komen kijken bij het spuitgieten. Het is belangrijk dat mallenmakers het spuitgietproces goed begrijpen en ervaring hebben met het werken met verschillende soorten mallen en materialen.
Eerste spuitgietproef of opname:
Het spuitgieten van spuitgietmatrijzen verwijst naar het testen van de spuitgietmatrijs om een proefstuk te maken met behulp van het spuitgietproces. Dit proces is een kritieke stap in het spuitgietproces omdat het de fabrikant in staat stelt om de prestaties van de matrijs te evalueren en eventueel aanpassingen te doen voordat een grote hoeveelheid onderdelen wordt geproduceerd.
Het proces van spuitgieten bestaat meestal uit de volgende stappen:
- Voorbereiding: De mal wordt op de spuitgietmachine geplaatst en de machine wordt klaargezet voor de spuitgieting. De trechter wordt gevuld met de kunststof.
- Regeling smelttemperatuur: De smelttemperatuur wordt geregeld om ervoor te zorgen dat de kunststofhars wordt verwarmd tot de juiste temperatuur om onderdelen van hoge kwaliteit te produceren.
- Injectie: De gesmolten kunststof wordt onder hoge druk in de mal gespoten. De druk wordt gehandhaafd totdat de mal gevuld is met de kunststof.
- Koelen: De mal wordt afgekoeld om de kunststof te laten stollen en het onderdeel te vormen. De afkoeltijd wordt bepaald door het type kunststof dat wordt gebruikt en de grootte en vorm van het onderdeel dat wordt gemaakt.
- Uitwerpen: Als het onderdeel gestold is, wordt het uit de matrijs gehaald. De uitwerppennen worden gebruikt om het onderdeel uit de matrijs te duwen.
- Inspectie: Het onderdeel dat uit de mal wordt geproduceerd, wordt grondig geïnspecteerd om ervoor te zorgen dat het voldoet aan de gewenste specificaties en kwaliteitsnormen.
- Aanpassingen: Indien nodig kan het spuitgietproces worden aangepast om de prestaties van de matrijs en de kwaliteit van de geproduceerde onderdelen te verbeteren.
Het proces van proefspuitgieten is een belangrijke stap in het spuitgietproces, omdat het de fabrikant in staat stelt om de prestaties van de matrijs te evalueren en eventueel aanpassingen te doen voordat er een grote hoeveelheid onderdelen wordt geproduceerd. Dit proces helpt ervoor te zorgen dat de matrijs onderdelen van hoge kwaliteit produceert met de gewenste specificaties.
Vorm verpakt en klaar voor productie:
Zodra de matrijs volledig af is door de matrijzenmaker, is de volgende stap de massaproductie. Het verpakken van de mal en de voorbereiding voor productie is de laatste stap in het spuitgietproces voordat de massaproductie kan beginnen. Deze stap omvat de volgende taken:
- Reiniging en onderhoud: De schimmel wordt grondig gereinigd en geïnspecteerd om er zeker van te zijn dat er geen puin, vuil of schade aan de schimmel is.
- Verpakking en opslag: De mal wordt zorgvuldig verpakt en opgeslagen op een veilige locatie om schade te voorkomen en ervoor te zorgen dat hij klaar is voor gebruik wanneer nodig.
- Testen en afstellen: De matrijs wordt getest op eventuele problemen, zoals lekken, slechte vulling of onjuiste uitwerping van onderdelen, en er worden de nodige aanpassingen gedaan om ervoor te zorgen dat de matrijs goed werkt.
- Productie-instelling: De matrijs wordt in de spuitgietmachine geïnstalleerd en alle noodzakelijke instellingen, zoals temperatuur, druk en injectiesnelheid, worden aangepast om aan de specifieke productievereisten te voldoen.
- Start van de productie: De eerste partij onderdelen wordt geproduceerd en het proces wordt gecontroleerd om te garanderen dat de onderdelen voldoen aan de vereiste specificaties en kwaliteitsnormen. Eventueel noodzakelijke aanpassingen worden doorgevoerd om het productieproces te optimaliseren en een consistente kwaliteit te garanderen.
In het algemeen is het voorbereiden van de matrijs voor productie een belangrijke stap in het spuitgietproces die helpt om het succes en de efficiëntie van de productie te garanderen.
Bovenstaande informatie is procedures voor het maken van een spuitgietmatrijs, misschien zijn er een aantal kleine dingen gemist, maar de meeste dingen zijn hierboven, zoals je kunt zien het maken van een spuitgietmatrijs is geen gemakkelijke zaak, als je een spuitgietmatrijs project in handvat, moet u een professionele spuitgietmatrijs maker om u van dienst, dit zal ervoor zorgen dat uw project met succes wordt uitgevoerd.
Sincere Tech is een professionele Chinese mal fabriek die gespecialiseerd is in de productie van aangepaste spuitgietmatrijzen. Ze hebben ervaring en expertise in het ontwerpen, ontwikkelen en produceren van hoogwaardige spuitgietmatrijzen voor verschillende industrieën en toepassingen.
Ze bieden een scala aan diensten, waaronder matrijsontwerp, prototyping, matrijsproductie en post-mold verwerking, om ervoor te zorgen dat hun klanten de best mogelijke resultaten ontvangen. Met hun focus op kwaliteit, precisie en klanttevredenheid is Sincere Tech een betrouwbare partner voor al je spuitgietbehoeften. Neem nu contact met ons op om e prijs voor uw project te krijgen.