Hva er sprøytestøpeform?
Sprøytestøpeform er et verktøy som brukes i sprøytestøpeprosessen for å produsere deler ved å sprøyte materiale inn i et formhulrom. Det er vanligvis laget av stål (H13, P20, 1.2312, 1.2344, S136H osv.) eller aluminium og er nøye utformet for å matche formen og spesifikasjonene til det endelige produktet.
Sprøytestøpeformen er delt i to halvdeler, en hulromshalvdel og en kjernehalvdel, som klemmes sammen under støpeprosessen. Materialet sprøytes inn gjennom en innsprøytingskanal inn i formhulen, der det avkjøles og stivner til ønsket form. Når delen er ferdig formet, åpnes formen, og delen støpes ut. Formen kan gjenbrukes til å produsere flere deler.

Hva er sprøytestøpeform
Typer sprøytestøpeformer
Blant de mange variantene av sprøytestøpeformer kan du finne:
Hulromsspesifikk mugg
Hver syklus i sprøytestøpeprosessen kan bare generere én del når man bruker en enkeltkavitetsform. Prosessen med å lage en del med denne formen er så enkel som å injisere plastharpiks i den, vente på at den skal kjøle seg ned og deretter fjerne det ferdige produktet.
Når man sammenligner produksjonskostnadene for multi-shot-former med enkeltkavitetsformer, er førstnevnte vanligvis rimeligere. Når det blir for dyrt å lage et lite antall komponenter på én gang, er disse formene det beste alternativet for prototyping og produksjon av små volumer.

Form med ett hulrom
Fordelene med enkeltskuddsformer inkluderer:
- Kostnadseffektivt: Produksjonen av en enkeltstøpeform er ofte rimeligere enn produksjonen av en flerstøpeform.
- Enkel design: Enkel produksjon og vedlikehold på grunn av enkel design: Formene er ofte mindre komplekse i utformingen enn formene med flere støpeskudd.
- Fleksibilitet: En lang rekke bruksområder, for eksempel prototyping og lavvolumproduksjon, egner seg for bruk av støpeformer med én kavitet.
Ulempene med enkeltskuddsformer inkluderer:
- Begrenset produksjon: Denne begrensningen gjør at støpeformer med én kavitet ikke egner seg for produksjonskjøringer med store volumer, fordi de bare kan produsere én enkelt del i hver syklus.
- Komplekse deler: Former med én kavitet egner seg ikke til å lage kompliserte deler med mange deler; da trenger du en flerkavitetsform eller en familieform.
- Ineffektivitet: Sammenlignet med former med flere hulrom er former med ett skudd mindre effektive fordi de bare kan lage én enkelt del i hver syklus på grunn av sin begrensede kapasitet.
Former med flere hulrom:
Flerkavitetsformer er en type sprøytestøpeform som har mer enn ett hulrom. Dette gjør at sprøytestøpeprosessen kan lage mer enn én del i hver omgang. Avhengig av behovet for applikasjonen, kan disse formene lages med hull som er like eller forskjellige.
Som et resultat av dens evne til å lage mange deler i én syklus, brukes flerkavitetsformer vanligvis til sprøytestøping av store volumer produksjonskjøringer. Denne funksjonen gjør det mulig for dem å øke produksjonseffektiviteten og samtidig senke kostnadene per del.

flerkavitetsform
Fordelene med flerkavitetsformer er blant annet
- Produksjon av store volumer: Formene med flere hulrom er laget for storskalaproduksjon, noe som gjør det enkelt å lage mange deler.
- Kostnadseffektivt: Flerkavitetsformer er vanligvis billigere enn former med én kavitet fordi de kan lage flere deler på én gang.
- Komplekse deler: Flerkavitetsformer kan brukes til å lage deler som er kompliserte og består av mange deler.
Ulempene med flerkavitetsformer inkluderer:
- Kompleks design: Det er vanskeligere å lage og vedlikeholde former med flere hulrom enn former med bare ett hulrom, fordi de er mer kompliserte.
- økte formkostnadene: Støpeformer med flere hulrom kan være dyrere enn støpeformer med bare ett hulrom, fordi de ulike hulrommene kan utsettes for ulik belastning og slitasje under sprøytestøpeprosessen. Dette kan føre til mindre effektiv produksjon og høyere reparasjonskostnader.
Varmkanalsform:
Varmkanalsform er en type sprøytestøpeform som bruker et varmkanalsystem for å levere det smeltede plastmaterialet inn i formhulrommene. Varmkanalsystemet består av en oppvarmet manifold som fordeler den smeltede plasten til individuelle dysespisser, som deretter ledes inn i formhulrommene.

Varmkanalsform
Fordelene med varmkanalformer er blant annet
- Forbedret delkvalitet: Varmkanalformer kan produsere deler med forbedret kvalitet, ettersom de minimerer mengden plast som blir til overs i kanalsystemet, noe som reduserer risikoen for defekter som f.eks.
- Økt produksjonseffektivitet: Varmkanalformer kan øke produksjonseffektiviteten, ettersom de eliminerer behovet for manuell inngripen for å fjerne medløperne fra de støpte delene, noe som reduserer syklustiden og forbedrer den generelle produksjonshastigheten.
- Energieffektivitet: Varmkanalformer er mer energieffektive sammenlignet med tradisjonelle kaldkanalformer, ettersom de minimerer mengden plast som går til spille i kanalene.
Ulempene med varmkanalformer inkluderer:
- Kompleks design: Varmkanalformer er mer komplekse i design sammenlignet med tradisjonelle kaldkanalformer, noe som gjør dem dyrere å produsere og vedlikeholde.
- Økt vedlikehold: Varmkanalformer krever vanligvis mer vedlikehold sammenlignet med kaldkanalformer, ettersom de har et mer komplekst varmesystem som må holdes i god stand.
- Sårbarhet for tilstopping: Varmkanalformer kan være sårbare for tilstopping, spesielt ved behandling av materialer med høy viskositet eller lang strømningslengde, ettersom dette kan føre til at den smeltede plasten stivner i kanalsystemet. Dette kan føre til redusert produksjonseffektivitet og økte vedlikeholdskostnader.
Stabelformer:
Stabelform er en type sprøytestøpeform som gjør det mulig å støpe flere hulrom samtidig i en enkelt maskinsyklus. Stabelformer er i hovedsak to eller flere støpeformer som er stablet oppå hverandre, der hver form produserer en enkelt del.

Stabelform
Fordelene med stabelformer inkluderer:
- Økt produksjonseffektivitet: Stabelformer gjør det mulig å støpe flere deler samtidig, noe som øker produksjonseffektiviteten og reduserer syklustiden.
- Mindre materialavfall: Stabelformer minimerer materialavfallet, ettersom de gjør det mulig å produsere flere deler ved hjelp av ett enkelt skudd med plastmateriale.
- Lavere kostnader: Stabelformer kan være mer kostnadseffektive sammenlignet med støpeformer med én kavitet, ettersom de gjør det mulig å produsere flere deler med én enkelt maskinsyklus.
Ulempene med stabelformer inkluderer:
- Kompleks design: Stabelformer kan være mer komplekse i design sammenlignet med støpeformer med én kavitet, noe som gjør dem dyrere å produsere og vedlikeholde.
- Redusert delkvalitet: Stabelformer kan produsere deler med redusert kvalitet, ettersom tilstedeværelsen av flere hulrom kan resultere i økt risiko for defekter som f.eks. blafring, korte skudd og synkemerker.
- Økt vedlikehold: Stabelformer krever vanligvis mer vedlikehold sammenlignet med støpeformer med én kavitet, ettersom de har en mer kompleks konstruksjon som må holdes i god stand.
Familieformer:
Familieformer, også kjent som flerkavitetsformer, er en type sprøytestøping som gjør det mulig å støpe flere deler med litt forskjellig design samtidig i én enkelt maskinsyklus. Dette oppnås ved å ha flere hulrom i formen som kan produsere ulike deler med forskjellige former og størrelser.
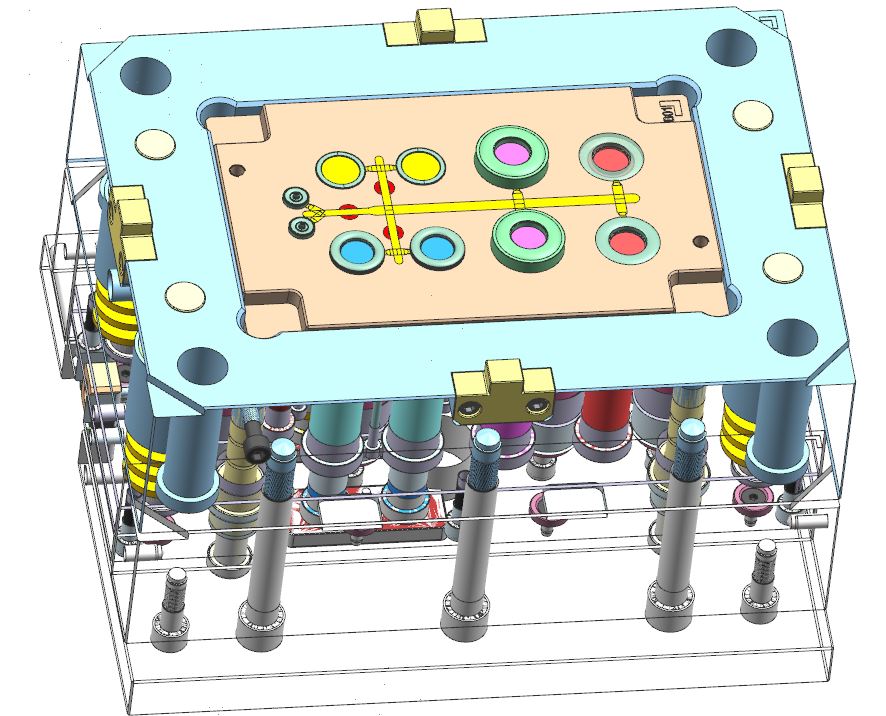
familieform
Fordelene med familieformer inkluderer:
- Økt produksjonseffektivitet: Familieformene gjør det mulig å støpe flere deler med ulike design samtidig, noe som øker produksjonseffektiviteten og reduserer syklustiden.
- Reduserte kostnader: Familieformer kan være mer kostnadseffektive sammenlignet med å produsere flere former med én kavitet for hver del, ettersom de gjør det mulig å produsere flere deler med én enkelt maskinsyklus.
- Fleksibilitet: Familieformene gjør det mulig å produsere ulike deler med varierende design, noe som gjør dem til et allsidig alternativ for produsenter som har behov for å produsere en rekke ulike produkter.
Ulempene med familieformer inkluderer:
- Kompleks design: Familieformer kan være mer komplekse i design sammenlignet med former med én kavitet, noe som gjør dem dyrere å produsere og vedlikeholde.
- Redusert delekvalitet: Familieformer kan produsere deler med redusert kvalitet, ettersom tilstedeværelsen av flere hulrom kan resultere i økt risiko for defekter som flash, korte skudd og synkemerker.
To-skuddsformer:
To-skuddsform (2-skudds sprøytestøping), også kjent som overstøping eller 2K-former, er en type sprøytestøping som gjør det mulig å støpe to ulike materialer sammen i én enkelt maskinsyklus. Denne prosessen innebærer at et første materiale (grunnmaterialet) støpes i en form, og deretter støpes et andre materiale (overstøpningsmaterialet) på det første materialet.

To skuddform
Fordelene med to-skuddsformer inkluderer:
- Økt funksjonalitet: To-shot-former gjør det mulig å kombinere to ulike materialer med forskjellige egenskaper for å skape deler med økt funksjonalitet.
- Forbedret estetikk: To-shot-former gjør det mulig å integrere forskjellige farger eller teksturer i en enkelt del, noe som skaper et mer visuelt tiltalende produkt.
- Redusert monteringstid: Ved å kombinere to materialer i én enkelt del kan to-shot-former redusere behovet for ytterligere monteringstrinn, noe som reduserer produksjonstiden og -kostnadene.
Ulempene med to-shot støpeformer inkluderer:
- Kompleks design: To-skuddsformer er mer komplekse i design sammenlignet med enkeltskuddsformer, noe som gjør dem dyrere å produsere og vedlikeholde.
- Økt syklustid: To-shot-former har vanligvis en lengre syklustid sammenlignet med enkelt-shot-former, ettersom prosessen innebærer å støpe to materialer i én enkelt maskinsyklus.
- Kompatibilitetsproblemer: To-skuddformer krever at de to materialene som støpes, er kompatible med hverandre og vil feste seg ordentlig, noe som gjør det viktig å velge materialene som skal brukes, med omhu.
Skru ut støpeformer:
Skrueformer er en type sprøytestøping som er spesielt utviklet for å produsere deler med skruegjenger, for eksempel lokk, lokk og beholdere. Disse formene er unike ved at de har en mekanisme som gjør at kjernen i formen kan rotere mens hulrommet forblir stasjonært, slik at den støpte delen kan skrus ut av formen etter at den er avkjølt og stivnet.

skru av støpeform
Fordelene med å skru av støpeformer inkluderer:
- Høy effektivitet: Skruformene gjør det mulig å produsere gjengede deler effektivt i én enkelt maskinsyklus, noe som reduserer produksjonstiden og -kostnadene.
- Forbedret nøyaktighet: Skruformene gjør det mulig å produsere gjengede deler med konsistent stigning og gjengedybde, noe som forbedrer kvaliteten og ytelsen til sluttproduktet.
- Allsidighet: Skruformene kan brukes til å produsere en rekke ulike deler med forskjellige gjengetyper og -størrelser, noe som gjør dem til et allsidig alternativ for mange ulike bruksområder.
Ulempene med å skru av støpeformer inkluderer:
- Kompleks design: Skrueformer er mer komplekse i design sammenlignet med andre typer støpeformer, noe som gjør dem dyrere å produsere og vedlikeholde.
- Økt syklustid: Utskruingsformer har vanligvis en lengre syklustid sammenlignet med andre typer former, ettersom prosessen innebærer rotasjon av formkjernen.
- Slitasje og slitasje: Den roterende mekanismen i skrueformene kan bli utsatt for slitasje over tid, noe som krever regelmessig vedlikehold for at formen skal fungere som den skal.
Form med sammenleggbar kjerne:
Støpeformer med sammenleggbar kjerne er en type sprøytestøping som brukes til å produsere hule deler med innvendige hulrom, for eksempel rør og andre komplekst formede deler. Disse formene har en unik design som gjør at kjernen i formen kan kollapse inn i seg selv og skape det indre hulrommet i delen.

Formkomponent med sammenleggbar kjerne
Fordelene med sammenleggbare kjerneformer er blant annet
- Forbedret effektivitet: Sammenleggbare kjerneformer gjør det mulig å produsere hule deler i én enkelt maskinsyklus, noe som reduserer produksjonstiden og -kostnadene.
- Forbedret delkvalitet: Sammenleggbare kjerneformer gir et mer presist og konsistent indre hulrom, noe som forbedrer den generelle kvaliteten på den endelige delen.
- Allsidighet: Sammenleggbare kjerneformer kan brukes til å produsere et bredt spekter av ulike deler med forskjellige former og størrelser, noe som gjør dem til et allsidig alternativ for mange forskjellige bruksområder.
Ulempene med støpeformer med sammenleggbar kjerne inkluderer:
- Kompleks design: Sammenleggbare støpeformer er mer komplekse i utformingen enn andre typer støpeformer, noe som gjør dem dyrere å produsere og vedlikeholde.
- Økt syklustid: Sammenleggbare kjerneformer har vanligvis en lengre syklustid sammenlignet med andre typer former, ettersom prosessen innebærer at kjernen i formen kollapser.
- Slitasje og slitasje: Den sammenleggbare mekanismen i kjernen kan bli utsatt for slitasje over tid, noe som krever regelmessig vedlikehold for at formen skal fungere som den skal.
Fordeler og ulemper med sprøytestøping av plast
Fordeler med Sprøytestøping:
- Produksjon av store volumer: Sprøytestøping er en svært effektiv metode for produksjon av store mengder identiske deler. Dette gjør den ideell for masseproduksjon av forbruksvarer, bildeler og andre produkter som krever store mengder like deler.
- Presisjon: Prosessen gir mulighet for svært presis kontroll av dimensjonsnøyaktighet og ensartethet. Dette skyldes bruken av strengt kontrollerte prosesseringsforhold og stivheten til støpemaskinen og støpeformen.
- Hastighet: Sprøytestøping er en rask prosess, med syklustider helt ned i noen få sekunder for små deler. Dette gjør at produsentene kan produsere store mengder deler på relativt kort tid.
- Kostnadseffektivt: Kostnadene ved å produsere deler ved hjelp av sprøytestøping blir mer økonomiske etter hvert som produksjonsvolumet øker. Dette skyldes at støpeformen kan brukes til å produsere mange deler i løpet av sin levetid, og kostnaden per del synker når volumet øker.
- Allsidighet: Sprøytestøping kan brukes til å produsere deler av en lang rekke materialer, inkludert plast, metaller og elastomerer. Denne allsidigheten gjør sprøytestøping til et populært valg for produsenter som har behov for å produsere deler av ulike materialer, avhengig av produktets spesifikke krav.
- Automatisering: Sprøytestøpemaskiner kan automatiseres, noe som gjør prosessen mer effektiv og reduserer behovet for manuelt arbeid. Dette kan også gi jevnere og bedre kvalitet.
- Komplekse former: Sprøytestøping kan brukes til å produsere komplekse former og design, inkludert deler med intrikate detaljer og trange toleranser. Dette er mulig på grunn av den nøyaktige kontrollen av støpeprosessen og muligheten til å designe svært detaljerte støpeformer.
- Valg av materiale: Sprøytestøping gjør det mulig for produsentene å velge mellom et bredt spekter av materialer, hvert med sine egne unike egenskaper, for eksempel styrke, fleksibilitet og motstand mot varme, kjemikalier og slitasje. Dette gjør det mulig å velge det beste materialet for hver enkelt applikasjon og produsere deler med de ønskede egenskapene.
Ulemper med sprøytestøping:
- Høye startkostnader: Den opprinnelige kostnaden for å lage støpeformen kan være høy, spesielt for komplekse former og design. Dette kan gjøre prosessen mindre kostnadseffektiv for små mengder deler eller for prototyper.
- Begrenset designfleksibilitet: Når formen først er laget, kan det være vanskelig og dyrt å endre designet. Dette kan begrense muligheten til å gjøre designendringer eller forbedringer når formen først er laget.
- Materialavfall: Sprøytestøping genererer en betydelig mengde skrapmateriale, noe som kan være kostbart å bli kvitt og miljøskadelig. Dette kan også øke produksjonskostnadene og redusere prosessens totale effektivitet.
- Ledetid: Det kan ta lang tid å lage støpeformen og sette i gang sprøytestøpeprosessen, spesielt når det gjelder komplekse deler. Dette kan forsinke produktutviklingsprosessen og begrense muligheten til å bringe produkter raskt ut på markedet.
- Begrensninger i overflatefinishen: Sprøytestøping gir kanskje ikke en overflatefinish av høy kvalitet på alle deler, spesielt ikke på deler med intrikate detaljer eller trange toleranser. Dette kan begrense muligheten til å produsere deler med et estetisk utseende av høy kvalitet.
- Materialkompatibilitet: Kompatibilitet mellom materiale og støpeform kan være en utfordring, ettersom noen materialer kanskje ikke fungerer godt med visse typer støpeformer eller krever spesielle prosesseringsforhold. Dette kan begrense muligheten til å produsere deler av visse materialer og øke produksjonskostnadene.
- Begrenset delstørrelse: Sprøytestøping begrenses av formens størrelse og støpemaskinens klemkraft. Dette kan begrense størrelsen på delene som kan produseres, og øke kostnadene ved å produsere større deler.
- Sekundære operasjoner: Noen deler kan kreve sekundære operasjoner, for eksempel trimming eller etterbehandling, etter at de er støpt. Dette kan øke produksjonskostnadene og begrense den totale effektiviteten i prosessen, men noen ganger kan disse problemene løses ved å forbedre sprøytestøpeformen.
Vanlige problemer med sprøytestøpeformer
Når du jobber innen sprøytestøping av plast, vil det alltid være noen problemer du trenger å løse hver dag, her er noen vanlige utfordringer du står overfor i sprøytestøping:
Problemer med skjevhet:
Forvrengning er et vanlig problem ved sprøytestøping og refererer til en deformasjon eller forvrengning av den støpte delen som oppstår etter at den er tatt ut av støpeformen. Dette kan skje på grunn av en rekke faktorer, inkludert:

Warp-forvrengning
- Feil avkjøling: Hvis delen kjøles ned for raskt eller ujevnt, kan det føre til skjevhet fordi materialet krymper og trekker seg sammen i ulik hastighet.
- Restspenninger: Sprøytestøping skaper restspenninger i delen på grunn av det høye trykket som brukes under støpeprosessen. Denne spenningen kan føre til skjevhet hvis den ikke avlastes på riktig måte.
- Valg av materiale: Noen materialer er mer utsatt for skjevhet enn andre. Materialer med lav varmebestandighet eller lav dimensjonsstabilitet er for eksempel mer utsatt for skjevhet.
- Formens utforming: Formens utforming kan også bidra til skjevhet, spesielt hvis formen ikke tillater riktig kjøling eller materialflyt.
- Prosesseringsforhold: Inkonsekvente prosesseringsforhold, for eksempel varierende sprøytehastigheter, formtemperaturer og trykknivåer, kan forårsake skjevhet.
For å unngå skjevhet er det viktig å velge riktig materiale, optimalisere formutformingen og prosessbetingelsene, og bruke riktige kjøle- og materialhåndteringsmetoder. I tillegg kan det være nødvendig å bruke behandlinger etter støping, for eksempel gløding, for å redusere restspenninger og forbedre dimensjonsstabiliteten.
Flash-problemer:
Flashdefekter er et begrep som brukes i sprøytestøping for å referere til overflødig materiale som presses ut av formen under støpeprosessen. Flash oppstår når materialet flyter utenfor det tiltenkte formhulen og inn i skillelinjen, eller mellomrommet mellom de to halvdelene av formen.

Støpeflammer eller grader
Blits kan skyldes flere faktorer, blant annet
- Feil utforming av støpeformen: En dårlig utformet form kan forårsake flammer ved at materiale lekker inn i skillelinjen.
- Inkonsekvente prosesseringsforhold: Varierende prosesseringsforhold, for eksempel injeksjonshastighet og trykk, kan forårsake flash.
- Materialkompatibilitet: Noen materialer er kanskje ikke kompatible med støpeformen og kan forårsake overslag når de flyter inn i skillelinjen.
- Slitasje på støpeformen: Over tid kan formen slites og forårsake blussing når materialet lekker inn i skillelinjen.
Flash kan ha flere negative effekter, blant annet redusert dimensjonsnøyaktighet, økt kassasjonsrate og vanskeliggjøring av etterstøpingsoperasjoner. For å minimere flash er det viktig å optimalisere formkonstruksjonen, prosessforholdene og materialvalget, og å vedlikeholde og reparere formen regelmessig etter behov.
Sveiselinjer:
Sveiselinjer er et vanlig problem ved sprøytestøping og er synlige merker på overflaten av den støpte delen der to strømmer av smeltet plastmateriale møtes og stivner. Sveiselinjer oppstår når materialet ikke smelter helt sammen når det strømmer inn i plastform hulrom, noe som etterlater en synlig linje på overflaten av delen.

Sveiselinje
Sveiselinjer kan skyldes flere faktorer, blant annet
- Utilstrekkelig smelteflyt: Hvis materialet ikke får nok tid til å flyte og smelte helt sammen, kan det dannes en sveiselinje.
- Feil utforming av porten: En dårlig utformet port, som er det punktet der det smeltede materialet kommer inn i formhulen, kan forårsake en sveiselinje.
- Inkonsekvente prosesseringsforhold: Varierende prosesseringsforhold, for eksempel injeksjonshastighet og trykk, kan forårsake en sveiselinje.
- Materialkompatibilitet: Noen materialer er kanskje ikke kompatible med støpeformen og kan forårsake en sveiselinje når de flyter inn i formhulen.
Sveiselinjer kan svekke emnets styrke og redusere den generelle kvaliteten. For å minimere sveiselinjer er det viktig å optimalisere formutformingen, bearbeidingsforholdene og materialvalget, og å implementere riktig materialhåndteringspraksis. I tillegg kan det være nødvendig å bruke spesielle bearbeidingsteknikker, for eksempel flerkavitetsformer eller varmkanalsystemer, for å redusere dannelsen av sveiselinjer.
Sinkmerker:
Senkemerker, også kjent som "synk", "vakuumsunk" eller "hud", er nedsunkne eller nedtrykte områder på overflaten av en sprøytestøpt plastdel. De skyldes vanligvis en rekke faktorer, blant annet
- Krymping av harpiks: Når harpiksen avkjøles og stivner, kan den krympe ujevnt, noe som kan føre til synkemerker.
- Dårlig materialflyt: Hvis harpiksen ikke flyter jevnt inn i alle områder av formen, kan det oppstå hulrom eller nedsunkne områder.
- Utilstrekkelig pakkingstrykk: Hvis injeksjonstrykket ikke er høyt nok, kan det hende at harpiksen ikke fyller formen helt, noe som fører til synkemerker.
- Problemer med formutformingen: Formens utforming, inkludert plassering og størrelse på porten, kanalsystem og utlufting, kan alle påvirke kvaliteten på den støpte delen og bidra til synkemerker.
Synkmerker kan påvirke den estetiske kvaliteten og funksjonaliteten til en støpt del, og kan være en kilde til frustrasjon for produsenter og sluttbrukere. For å minimere synkemerker er det viktig å nøye vurdere faktorene som bidrar til dem, for eksempel materialvalg, formdesign, prosessparametere og emnedesign, og foreta justeringer etter behov for å optimalisere sprøytestøpeprosessen.
Flytmerker:
Flytmerker er et vanlig problem ved sprøytestøping og refererer til synlige merker eller striper på overflaten av den støpte delen som er forårsaket av flyten av det smeltede plastmaterialet når det fyller formhulen. Flytmerker oppstår når materialet flyter ujevnt og etterlater seg et synlig merke på overflaten av detaljen.
Flytmerker kan skyldes flere faktorer, blant annet
- Utilstrekkelig smelteflyt: Hvis materialet ikke får nok tid til å flyte og fylle formhulen, kan det oppstå flytespor.
- Feil utforming av porten: En dårlig utformet port, som er det punktet der det smeltede materialet kommer inn i formhulen, kan forårsake strømningsmerker.
- Inkonsekvente prosesseringsforhold: Varierende prosesseringsforhold, for eksempel injeksjonshastighet og trykk, kan forårsake flytmerker.
- Materialkompatibilitet: Noen materialer er kanskje ikke kompatible med formen og kan forårsake flytespor når de flyter inn i formhulen.
Flytmerker kan redusere den generelle kvaliteten og det kosmetiske utseendet på detaljen. For å minimere flytespor er det viktig å optimalisere formutformingen, bearbeidingsforholdene og materialvalget, og å implementere riktig materialhåndteringspraksis. I tillegg kan det være nødvendig å bruke spesielle prosesseringsteknikker, for eksempel flerkavitetsformer eller varmkanalsystemer, for å redusere dannelsen av flytespor.
Problemer med riper:
Med riper menes synlige merker eller riper på overflaten av en sprøytestøpt del som skyldes fysisk kontakt mellom delen og støpeformen eller andre fremmedlegemer under støpeprosessen. Det kan være flere grunner til at det oppstår riper, blant annet
- Dårlig formdesign: Feil utformede støpeformer eller støpeformkomponenter kan forårsake riper på overflaten av delen.
- Utilstrekkelig smøring: Hvis formen og formkomponentene ikke smøres ordentlig, kan de forårsake riper på overflaten av delen.
- Dårlig materialhåndtering: Dårlig håndtering av råmaterialet eller ferdige deler kan forårsake riper på overflaten av delen.
- Avfall i støpeformen: Fremmedlegemer eller rusk i formhulen kan forårsake riper på overflaten av delen.
Riper kan redusere den generelle kvaliteten og det kosmetiske utseendet på detaljen. For å minimere ripeproblemer er det viktig å implementere riktig formdesign, smøring, materialhåndtering og vedlikeholdspraksis. I tillegg kan regelmessig rengjøring og inspeksjon av formen og formkomponentene bidra til å forhindre at det oppstår riper.
Ejektormerker:
Utstøtermerker er synlige merker på overflaten av en sprøytestøpt del som skyldes utstøterpinnene eller andre utstøtningsmekanismer under støpeprosessen. Utstøtermerker oppstår når utstøterpinnene skyver den støpte delen ut av formhulrommet og etterlater synlige merker på overflaten av delen.
Utstøtingsmerker kan skyldes flere faktorer, blant annet
- Feil utforming av utkasterpinnene: Hvis utkasterpinnene ikke er riktig utformet, kan de etterlate synlige merker på overflaten av delen.
- Overdreven kraft: Hvis utkasterpinnene bruker for stor kraft på delen under utkasterprosessen, kan de etterlate dypere og mer merkbare merker på overflaten av delen.
- Inkonsekvent utkasterkraft: Hvis utstøtingskraften ikke er konsekvent fra en utstøtingstapp til en annen, kan det føre til ujevne utstøtingsmerker på overflaten av delen.
- Dårlig overflatefinish: Hvis overflaten på formhulrommet ikke er glatt, kan det føre til utstøtingsmerker på overflaten av delen.
Utstøtermerker kan redusere den generelle kvaliteten og det kosmetiske utseendet på detaljen. For å minimere utstøtermerker er det viktig å optimalisere utformingen av utstøterpinnene og formhulrommets overflatefinish, og å implementere riktige vedlikeholds- og inspeksjonsrutiner. I tillegg kan det være nødvendig å bruke spesielle utstøtingsmekanismer, for eksempel luftassistert utstøting eller sideveis utstøting, for å minimere utstøtingsmerker.
Problemer med kortskudd:
Et kort skudd er et vanlig problem ved sprøytestøping som oppstår når det smeltede plastmaterialet ikke fyller formhulen helt, noe som resulterer i en støpt del som er mindre enn den ønskede størrelsen. Det kan være flere grunner til at det oppstår korte skudd, blant annet
- Utilstrekkelig materiale: Hvis det ikke er nok materiale til å fylle formhulen, kan det oppstå et kortskudd.
- Feil prosesseringsforhold: Hvis behandlingsforholdene, for eksempel innsprøytningshastighet og trykk, ikke er riktig innstilt, kan det oppstå et kort skudd.
- Dårlig formdesign: En dårlig utformet form kan føre til et kort skudd, ettersom materialet kanskje ikke kan strømme inn i alle områder av formhulrommet.
- Materialforringelse: Hvis materialet har blitt degradert eller ikke har blitt lagret på riktig måte, kan det føre til kortslutning.
Korte skudd kan redusere den generelle kvaliteten og funksjonaliteten til detaljen og resultere i bortkastet materiale og prosesseringstid. For å minimere forekomsten av korte skudd er det viktig å optimalisere formutformingen, prosessbetingelsene og materialvalget, og å implementere riktige materialhåndteringsrutiner. I tillegg kan regelmessig overvåking og vedlikehold av støpeutstyret bidra til å forhindre at det oppstår kortslutninger.
Luftfelle og brennmerker:
Luftfeller og brennmerker er vanlige problemer ved sprøytestøping som kan oppstå på grunn av feil prosesseringsforhold eller feil formdesign.
Luftfeller oppstår når luft blir fanget i formhulrommet under sprøytestøpeprosessen, noe som fører til at materialet flyter rundt luftlommen i stedet for å fylle den. Dette kan resultere i synlige hulrom eller lommer i den støpte delen. Luftfeller kan forårsakes av flere faktorer, blant annet
- Utilstrekkelig materialflyt: Hvis materialet ikke flyter ordentlig inn i formhulen, kan luft bli fanget.
- Feil utforming av porten: Hvis porten ikke er riktig utformet, kan luft bli fanget i formhulrommet.
- Mangelfull utlufting: Hvis formen ikke ventileres ordentlig, kan luft bli fanget i formhulrommet.
Brennmerker oppstår når plastmaterialet utsettes for høye temperaturer over for lang tid, noe som fører til at det brytes ned og gir synlige merker eller misfarging på overflaten av delen. Brennmerker kan skyldes flere faktorer, blant annet
- For høye prosesseringstemperaturer: Hvis prosesseringstemperaturen er satt for høyt, kan materialet brytes ned og gi brennmerker.
- Utilstrekkelig nedkjølingstid: Hvis delen ikke kjøles ned på riktig måte, kan materialet brytes ned og gi brennmerker.
- Dårlig formdesign: En dårlig utformet form kan føre til at materialet utsettes for høye temperaturer for lenge, noe som kan resultere i brennmerker.
For å minimere luftfeller og brennmerker er det viktig å optimalisere prosessforholdene og formutformingen, og å implementere riktige overvåkings- og vedlikeholdsrutiner. I tillegg kan det være nødvendig å bruke spesielle prosesseringsteknikker, for eksempel støping ved lav temperatur eller vakuumstøping, for å minimere luftfeller og brennmerker.
Bearbeiding for å lage en sprøytestøpeform:
Prosessen med å lage en sprøytestøpeform består av flere trinn:
Formdesign:
Utformingen av sprøytestøpeformen er et kritisk aspekt ved sprøytestøpeprosessen, ettersom den har direkte innvirkning på kvaliteten, effektiviteten og kostnadene for de støpte delene.
En godt utformet sprøytestøpeform vil produsere deler som oppfyller de ønskede størrelses-, form- og kvalitetskravene, samtidig som den er effektiv å produsere og enkel å vedlikeholde.
De viktigste faktorene å ta hensyn til ved utforming av en sprøytestøpeform er blant annet
- Delens geometri: Utformingen av den støpte delen må ta hensyn til ønsket størrelse, form og egenskaper på delen.
- Valg av materiale: Materialet som skal brukes til støpeformen og den støpte delen, må velges ut fra faktorer som kostnad, styrke og termisk stabilitet.
- Formhulrom: Antall og plassering av formhulrommene må velges for å oppfylle kravene til produksjonsvolum.
- Portsystem: Utformingen av grensesystemet er avgjørende, ettersom det bestemmer hvordan plastmaterialet flyter inn i formhulen.
- Utstøpingssystem: Utstøtingssystemet må være utformet slik at de støpte delene kan tas ut av støpeformen uten å bli skadet.
- Kjølesystem: Kjølesystemet må være utformet slik at de støpte delene avkjøles jevnt og raskt, noe som reduserer syklustiden og forbedrer kvaliteten.
- Utkastvinkler: Formen må være utformet med passende uttrekksvinkler slik at de støpte delene kan tas ut av formen.
- Ventilasjon: Formen må ventileres slik at luft kan slippe ut av hulrommet, noe som reduserer risikoen for luftfeller og brennmerker.
- Vedlikehold og reparasjon: Formen må være utformet slik at den er enkel å vedlikeholde og reparere, for å minimere nedetid og øke produksjonseffektiviteten.
Design av sprøytestøpeformer er en kompleks prosess som krever ekspertise innen områder som maskinteknikk, materialvitenskap og produksjon. Det er viktig å samarbeide med en anerkjent formdesigner for å sikre at formen er utformet riktig og oppfyller dine behov.
CNC-programmering:
CNC-programmering (Computer Numerical Control) er et viktig trinn i produksjonen av en sprøytestøpeform. Når formdesignet er ferdig, er neste trinn CNC-programmering. Følgende er de viktigste trinnene som er involvert i CNC-programmering for produksjon av sprøytestøpeform:
- Oversettelse av CAD-modellen: CAD-modellen oversettes til et CAM-program (Computer Aided Manufacturing), som brukes til å lage CNC-koden for støpeformen.
- Opprettelse av CNC-kode: CNC-koden opprettes i CAM-programmet, som gir instruksjoner til CNC-maskinen om hvordan formkomponentene skal flyttes og skjæres ut. Koden tar hensyn til materialet og tykkelsen på formkomponentene, samt de ønskede formene og funksjonene.
- Opprettelse av verktøybane: Verktøybanen opprettes i CAM-programmet, som definerer banen som skjæreverktøyet skal følge for å bearbeide formkomponentene. Verktøybanen tar hensyn til formkomponentens form og egenskaper og CNC-maskinens kapasitet.
- Simulering: CNC-koden og verktøybanen simuleres i CAM-programmet for å sikre at formkomponentene blir maskinert på riktig måte og i henhold til de riktige spesifikasjonene.
- CNC-maskinering: CNC-koden lastes inn i CNC-maskinen, som deretter bruker koden og verktøybanen til å maskinere formkomponentene.
CNC-programmering er et kritisk trinn i produksjonsprosessen for sprøytestøpeformer, ettersom det avgjør nøyaktigheten og kvaliteten på formkomponentene. Det er viktig å samarbeide med en CNC-programmerer som har erfaring med programmering av sprøytestøpeformer, for å sikre at CNC-koden opprettes korrekt og i henhold til de riktige spesifikasjonene. Det er også i dette trinnet at formens kjølekanaler, ejektorsystem og andre funksjoner legges til i formkomponentene for å sikre at de fungerer som de skal.
Innkjøp av BOM-liste for støpeformer
En Mold BOM-liste (Bill of Materials) er en omfattende liste over alle komponenter og materialer som trengs for å produsere en sprøytestøpeform. Den inneholder følgende elementer:
- Stål til formbunnen og kjerne-/kavitetsinnsatsene
- Varmkanalkomponenter
- Komponenter i kjølesystemet, for eksempel vannledninger og kjøleblokker
- Utskytningssystemets komponenter, for eksempel utkasterpinner og hylser
- Komponenter til granuttrekkeren
- Varmebånd og temperaturregulatorer
- Formkomponenter, for eksempel gjennomføringer, styrepinner og låseanordninger
- Forminnsatser, for eksempel glidere og løftere
- Spesialartikler, for eksempel datostempler og spesialtilpassede logoer
Mold BOM-listen er et viktig verktøy for innkjøp og produksjon, ettersom den gir en oversiktlig og detaljert liste over komponentene og materialene som trengs for å produsere formen. Den brukes til å sikre at alle nødvendige komponenter er bestilt og tilgjengelig når formen er klar til å produseres.
Det er viktig å samarbeide med en anerkjent leverandør når du kjøper komponenter til en sprøytestøpeform, ettersom kvaliteten og påliteligheten til disse komponentene kan ha stor innvirkning på effektiviteten og kvaliteten på sprøytestøpeprosessen.
Grovbearbeiding av støpeform:
Grovbearbeiding av sprøytestøpeformer refererer til den innledende bearbeidingen av stålkomponentene i en sprøytestøpeform for å oppnå den grunnleggende formen og størrelsen på formen. Dette trinnet utføres vanligvis ved hjelp av CNC-maskiner (Computer Numerical Control). Følgende er de viktigste trinnene som er involvert i grovbearbeiding av sprøytestøpeform:
- Valg av stål: Det første trinnet er å velge riktig type stål til støpeformen, for eksempel P20 eller H13, basert på de ønskede egenskapene til den støpte delen.
- Skjæring av stål: Stålet skjæres til riktig størrelse og form ved hjelp av en CNC-maskin. Dette trinnet kan også omfatte boring og gjengetapping av hull til kjøle- og utstøtingssystemene.
- Profilering av stål: Stålkomponentene blir deretter maskinert for å oppnå den grunnleggende formen på formen, inkludert kjernen og hulromsinnsatsene.
- Inspeksjon av stål: De maskinbearbeidede komponentene blir deretter inspisert for å sikre at de oppfyller de nødvendige toleransene og spesifikasjonene.
- Rengjøring av stål: De maskinbearbeidede komponentene rengjøres og avgrates for å fjerne ujevne kanter og rusk.
Grovbearbeidingsprosessen er et viktig trinn i sprøytestøpeprosessen, ettersom den legger grunnlaget for den endelige høypresisjonsbearbeidingen og poleringen som følger. Det er viktig å sørge for at grovbearbeidingen utføres nøyaktig og i henhold til de riktige spesifikasjonene for å sikre at formen fungerer som den skal og produserer deler med ønsket kvalitet.
Varmebehandling av formstål:
Varmebehandling av formstål er en prosess der stålkomponentene i en sprøytestøpeform varmes opp og kjøles ned for å forbedre de mekaniske egenskapene og dimensjonsstabiliteten. Hensikten med varmebehandling er å herde stålet, avlaste restspenninger og forbedre dets slitestyrke og seighet. Dette er spesielt for herdet stål av sprøytestøpeform, hvis du bruker forherdet stål for å lage sprøytestøpeformen, trenger du ikke å gjøre denne varmebehandlingsjobben. Følgende er de viktigste trinnene som er involvert i varmebehandling av formstål:
- Gløding: Stålkomponentene varmes opp til en bestemt temperatur, vanligvis mellom 800-900 °C, og kjøles deretter sakte ned for å redusere indre spenninger og forbedre stålets bearbeidbarhet.
- Herding: Stålkomponentene varmes opp til en høy temperatur, vanligvis over den kritiske temperaturen, og kjøles deretter raskt ned, vanligvis ved å slukke i olje eller vann. Denne prosessen herder stålet og forbedrer slitestyrken.
- Herding: Etter herding herdes stålkomponentene ved at de varmes opp til en lavere temperatur i en bestemt tidsperiode for å forbedre stålets seighet og formstabilitet.
Varmebehandlingsprosessen er avgjørende for å sikre at stålkomponentene i en sprøytestøpeform har de ønskede mekaniske egenskapene og dimensjonsstabiliteten, som er avgjørende for å produsere støpte deler av høy kvalitet. Det er viktig å samarbeide med en leverandør av varmebehandling som har erfaring med behandling av formstål, for å sikre at varmebehandlingsprosessen utføres korrekt og i henhold til de riktige spesifikasjonene.
Finbearbeiding av formhulrom og kjerne:
Finbearbeiding av formhulrom og kjerne er prosessen med nøyaktig bearbeiding av de innvendige overflatene i formhulrommet og kjerneinnsatsene for å oppnå den endelige formen og størrelsen på formen. Dette trinnet utføres vanligvis ved hjelp av CNC-maskiner (Computer Numerical Control) med høy presisjon og nøyaktighet. Følgende er de viktigste trinnene som er involvert i finbearbeiding av formhulrom og kjerne:
- Klargjøring av overflaten: Overflaten på formhulrommet og kjerneinnsatsene rengjøres og poleres for å fjerne eventuelle rester av rusk eller ujevnheter.
- Maskinering av overflaten: De innvendige overflatene på formhulrommet og kjerneinnsatsene bearbeides ved hjelp av CNC-maskiner for å oppnå den endelige formen og størrelsen på formen. Dette omfatter også å lage de intrikate detaljene og funksjonene på den støpte delen, for eksempel tekst, logoer og underskjæringer.
- Overflateinspeksjon: De maskinbearbeidede overflatene inspiseres for å sikre at de oppfyller de nødvendige toleransene og spesifikasjonene.
- Overflatepolering: De innvendige overflatene på formhulrommet og kjerneinnsatsene poleres til en høy finish for å forbedre overflatekvaliteten på de støpte delene og redusere risikoen for feil.
Finbearbeiding er et kritisk trinn i sprøytestøpeprosessen, ettersom det er avgjørende for kvaliteten og nøyaktigheten til de støpte delene. Det er viktig å samarbeide med en maskinleverandør som har erfaring med finbearbeiding av formhulrom og kjerner, for å sikre at bearbeidingen utføres korrekt og i henhold til de riktige spesifikasjonene. Det er også i dette trinnet at formens utstøpingssystem, kjølekanaler og andre funksjoner legges til for å sikre at formen fungerer som den skal.
EDM-maskinering:
EDM (Electrical Discharge Machining) er en prosess som brukes til å lage intrikate og svært presise former i metalldeler, blant annet i en sprøytestøpeform. Prosessen bruker elektriske gnister til å fjerne materiale fra formoverflaten og skape den ønskede formen. Følgende er de viktigste trinnene som inngår i EDM-maskinering:
- Forberedelse av overflaten: Overflaten på formkomponenten som skal bearbeides, rengjøres og poleres for å fjerne eventuelle rester av rusk og ujevnheter.
- EDM-oppsett: EDM-maskinen settes opp med de riktige parameterne, inkludert gnistgap, pulsvarighet og elektrodemateriale, basert på materialet og formen på formkomponenten.
- Gnisterosjon: EDM-maskinen produserer elektriske gnister som fjerner materiale fra formkomponenten og skaper den ønskede formen. Denne prosessen foregår trinnvis, der EDM-maskinen gradvis eroderer materialet til den endelige formen er oppnådd.
- Inspeksjon av overflaten: Den maskinbearbeidede overflaten inspiseres for å sikre at den oppfyller de nødvendige toleransene og spesifikasjonene.
EDM-maskinering brukes ofte til formkomponenter som har komplekse former eller små, intrikate detaljer som er vanskelige å oppnå med andre maskineringsprosesser. Den brukes også til å produsere skarpe kanter og hjørner som er avgjørende for at en sprøytestøpeform skal fungere som den skal.
Prosessen er svært presis og nøyaktig, noe som gjør den ideell for produksjon av støpte deler av høy kvalitet. Det er viktig å samarbeide med en EDM-leverandør som har erfaring med EDM-maskinering for sprøytestøpeformer, for å sikre at prosessen utføres korrekt og i henhold til de riktige spesifikasjonene.
Polering av formoverflaten:
Polering av sprøytestøpeformer er det siste trinnet i produksjonsprosessen for sprøytestøpeformer. Det innebærer å glatte ut overflatene på formkomponentene for å sikre at det ferdige produktet har en glatt og jevn overflate. Følgende er de viktigste trinnene som er involvert i polering av sprøytestøpeformer:

polering av plastformer
- Klargjøring av overflaten: Overflatene på formkomponentene rengjøres og klargjøres for polering. Eventuelle gjenværende ujevnheter eller maskineringsmerker fjernes for å sikre en glatt overflate for polering.
- Grovpolering: Det første trinnet i poleringen er grovpolering, som innebærer å fjerne eventuelle store ujevnheter i overflaten på formkomponentene. Dette trinnet gjøres vanligvis med et grovt slipemiddel, for eksempel sandpapir eller en slipebørste.
- Finpolering: Finpolering er det neste trinnet, som innebærer å glatte ut overflaten på formkomponentene til en finere finish. Dette trinnet gjøres med et finere slipemiddel, for eksempel et finere sandpapir eller en slipebørste.
- Pussing: Polering er det siste trinnet i poleringen, som innebærer bruk av en poleringsskive og poleringsmiddel for å oppnå en høyglanset overflate på formkomponentene.
- Inspeksjon: Etter polering inspiseres formkomponentene grundig for å sikre at de har en glatt og jevn overflate, uten riper, sprekker eller andre ujevnheter.
Polering av sprøytestøpeformer er viktig fordi det påvirker kvaliteten på sluttproduktet. En godt polert form resulterer i et produkt med en glatt og jevn overflate, noe som er viktig for produktets funksjonalitet og estetikk. Det er viktig å samarbeide med en erfaren formpolerer for å sikre at formkomponentene poleres i henhold til de riktige spesifikasjonene og til ønsket kvalitetsnivå.
Formtilpasning
Formtilpasning er en spesialisert jobb innen sprøytestøping og innebærer montering, installasjon og testing av sprøytestøpeformer. Formmontører er ansvarlige for å sikre at formkomponentene er riktig montert og fungerer som de skal, og at formen produserer deler med ønsket kvalitet og ytelsesstandarder. Noen av de viktigste ansvarsområdene til formstøpemontører inkluderer:
- Montering av formkomponentene: Formmestrene er ansvarlige for å montere de ulike komponentene i et sprøytestøpeverktøy, inkludert hulrommet og kjernekomponentene, kanalsystemet og eventuelle hjelpekomponenter.
- Montering av støpeformen på støpemaskin: Moldmaster må kunne montere formen på støpemaskinen på en måte som sikrer riktig justering og funksjon av formen, hvis den ikke har noen støpemaskin, bruk manuell måte å montere formen på, dette er det de fleste selskaper gjør.
- Testing av formen: Formmesteren er ansvarlig for å teste formen for å sikre at den produserer deler med ønsket kvalitet og ytelse. Dette innebærer blant annet å inspisere delene for å se etter eventuelle defekter, for eksempel skjevhet, krymping eller andre kvalitetsproblemer.
- Justering av formen: Hvis det oppdages problemer i testfasen, er moldmaster ansvarlig for å foreta nødvendige justeringer av formen for å sikre at den produserer deler som oppfyller de ønskede spesifikasjonene.
- Feilsøking: Moldmaster må være i stand til å identifisere og feilsøke eventuelle problemer som kan oppstå i løpet av formtilpasningsprosessen.
Jobben som formstøper krever en kombinasjon av teknisk kunnskap, manuell fingerferdighet og sans for detaljer. Formmontører må kunne arbeide med et bredt spekter av verktøy og maskiner, samt forstå de komplekse prosessene som er involvert i sprøytestøping. Det er viktig for formstøpere å ha god forståelse for sprøytestøpeprosessen, samt erfaring med å jobbe med ulike typer former og materialer.
Første sprøytestøpingsprøve eller skyting:
Prøvesprøyting av sprøytestøping refererer til prosessen med å teste sprøytestøpeformen for å produsere en prøvedel ved hjelp av sprøytestøpingsprosessen. Denne prosessen er et kritisk trinn i sprøytestøpeprosessen, ettersom den gjør det mulig for produsenten å evaluere formens ytelse og foreta eventuelle nødvendige justeringer før det produseres et stort antall deler.
Prøvesprøytingsprosessen for sprøytestøping omfatter vanligvis følgende trinn:
- Forberedelser: Formen monteres på sprøytestøpemaskinen, og maskinen klargjøres for sprøytestøping. Beholderen fylles med plastharpiks.
- Kontroll av smeltetemperaturen: Smeltetemperaturen kontrolleres for å sikre at plastharpiksen varmes opp til riktig temperatur for å produsere deler av høy kvalitet.
- Injeksjon: Den smeltede plasten sprøytes inn i formen under høyt trykk. Trykket opprettholdes til formen er fylt med plastharpiksen.
- Avkjøling: Formen kjøles ned for å få plastharpiksen til å stivne og forme delen. Avkjølingstiden bestemmes av hvilken type plastharpiks som brukes og størrelsen og formen på delen som skal produseres.
- Utstøping: Når delen er størknet, fjernes den fra formen. Utstøtingspinnene brukes til å skyve delen ut av formen.
- Inspeksjon: Delen som produseres fra støpeformen, inspiseres grundig for å sikre at den oppfyller de ønskede spesifikasjonene og kvalitetsstandardene.
- Justeringer: Om nødvendig kan det gjøres justeringer i støpeprosessen for å forbedre formens ytelse og kvaliteten på delene som produseres.
Prøvesprøytingsprosessen er et viktig trinn i sprøytestøpeprosessen, ettersom den gjør det mulig for produsenten å evaluere formens ytelse og foreta eventuelle nødvendige justeringer før det produseres et stort antall deler. Denne prosessen bidrar til å sikre at formen produserer deler av høy kvalitet med de ønskede spesifikasjonene.
Formen er pakket og klar for produksjon:
Når formen er helt ferdig av støperen, er neste trinn for den massive produksjonen. Formpakking og forberedelse til produksjon er det siste trinnet i sprøytestøpeprosessen før masseproduksjonen kan begynne. Dette trinnet innebærer følgende oppgaver:
- Rengjøring og vedlikehold: Formen rengjøres grundig og inspiseres for å sikre at det ikke finnes rusk, smuss eller skader på formen.
- Pakking og oppbevaring: Formen pakkes forsiktig og oppbevares på et sikkert sted for å forhindre skader og sikre at den er klar til bruk når den trengs.
- Testing og justering: Formen testes for eventuelle problemer, for eksempel lekkasjer, dårlig fylling eller feilaktig utstøting av deler, og eventuelle nødvendige justeringer gjøres for å sikre at formen fungerer som den skal.
- Produksjonsoppsett: Formen installeres i sprøytestøpemaskinen, og alle nødvendige innstillinger, som temperatur, trykk og innsprøytningshastighet, justeres for å oppfylle de spesifikke produksjonskravene.
- Produksjonen starter: Det første partiet med deler produseres, og prosessen overvåkes for å sikre at delene oppfyller de nødvendige spesifikasjonene og kvalitetsstandardene. Eventuelle nødvendige justeringer gjøres for å optimalisere produksjonsprosessen og sikre jevn kvalitet.
Alt i alt er klargjøring av formen for produksjon et viktig trinn i sprøytestøpeprosessen som bidrar til å sikre en vellykket og effektiv produksjonskjøring.
Ovennevnte informasjon er prosedyrer for å lage en injeksjonsform, kanskje det er noen små ting savnet, men de fleste tingene er over, som du kan se å lage en injeksjonsform er ikke lett sak, hvis du har et injeksjonsformprosjekt i håndtaket, må du finne en profesjonell injeksjonsformprodusent for å betjene deg, dette vil sørge for at prosjektet ditt kjører vellykket.
Sincere Tech er en profesjonell Kina mold fabrikk som spesialiserer seg på produksjon av tilpassede sprøytestøpeformer. De har erfaring og ekspertise innen design, utvikling og produksjon av sprøytestøpeformer av høy kvalitet for ulike bransjer og bruksområder.
De tilbyr en rekke tjenester, inkludert formdesign, prototyping, produksjon av støpeformer og etterbehandling av støpeformer, for å sikre at kundene får best mulig resultat. Med fokus på kvalitet, presisjon og kundetilfredshet er Sincere Tech en pålitelig og troverdig partner for alle dine behov innen sprøytestøping. Kontakt oss for å få en pris på prosjektet ditt nå.