Når kravene til polymerdeler går utover 3D-printing og maskinering, anbefales det at produktutviklerne tyr til sprøytestøping. Konvensjonell sprøytestøping innebærer at man må finne den rette verktøyleverandøren og deretter kjøpe verktøyet, noe som kan ta flere måneder. Det kan ta lang tid og er veldig slitsomt, men kostnaden per enhet er relativt lav, spesielt når man lager mange eksemplarer av produktene. Heldigvis finnes det et alternativ: sprøytestøping av plast i korte serier.
Forståelse av plastsprøytestøping i korte serier
Når det er en liten produksjon av produktet, er det billigere å sprøytestøpe i korte serier sammenlignet med sprøytestøping i lange serier (eller sprøytestøping av store volumer). Denne prosessen fjerner også det konvensjonelle høyvolumsproduksjonssystemet som krever mye stivhet, lang syklustid og store kapitalinvesteringer. I dette tilfellet er imidlertid sprøytestøping mer hensiktsmessig på kort sikt enn på lang sikt.
De midlertidige formene er av aluminium, mens de "harde" produksjonsverktøyene er av sementert verktøystål. Dette metallet kjennetegnes av høy varmeledningsevne og god bearbeidbarhet. Aluminiumsformer er litt mindre stive enn stålformer, men de er best egnet for serier på mindre enn 10 000 stykker. I tillegg er de billigere enn stålformer, og de ferdige delene lages på uker, ikke måneder, slik tilfellet er med stålformer.
Sprøytestøping av korte serier er det mest hensiktsmessige for enhver organisasjon som trenger plastdeler av høy kvalitet til en rimelig pris og på kort tid.
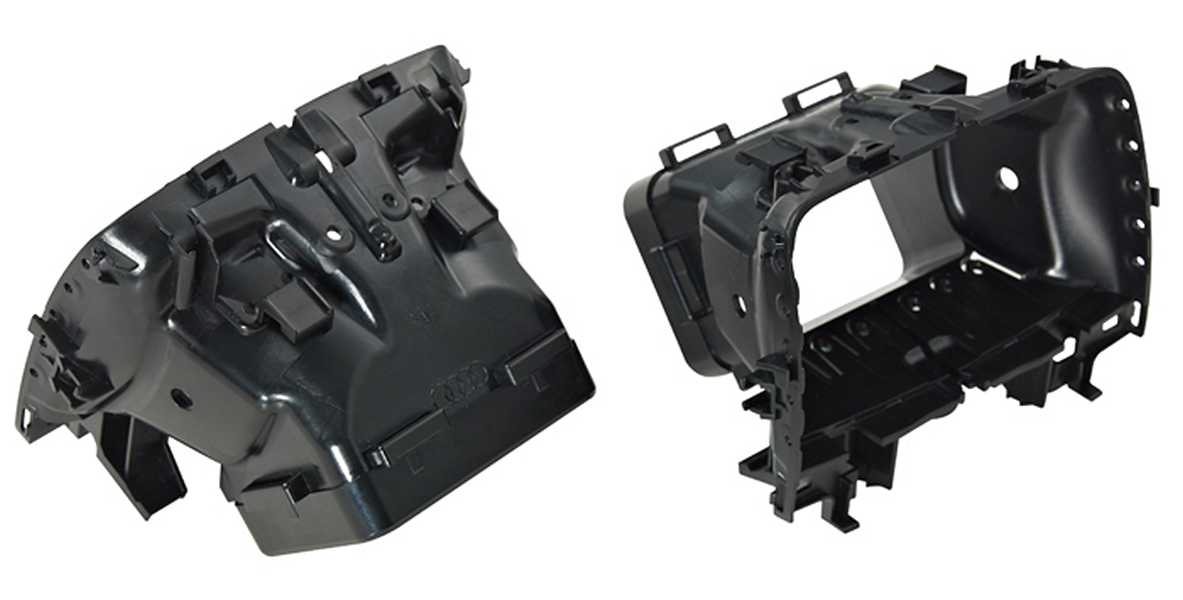
Fordeler med sprøytestøping av korte serier
Fordelene med sprøytestøping i korte serier er som følger:
Sprøytestøpeformer i aluminium er billigere sammenlignet med støpeformer i armert stål som er tilgjengelige på markedet i dag. Hvor mye man sparer, avhenger av antall kaviteter, emnets geometri og støpeproblemer som underskjæringer eller innstikk. Forskjellen i kostnader er imidlertid normalt ganske stor.
Men dette er ikke den eneste fordelen som kan utledes av dette, også kostnadsfaktoren må tas med i betraktningen. Muligheten til å gjøre endringer og de korte syklustidene kan dermed bidra til å redusere tiden det tar å utvikle produkter, og dermed redusere tiden det tar å få dem ut på markedet. I motsetning til de fleste organisasjoner binder ikke vår sprøytestøpingstjeneste for korte serier kundene til å bestille i store mengder. De er laget av materialer av produksjonskvalitet og har tilstrekkelig overflatebehandling som kan brukes.
Kortsiktige kostnader for produksjon av sprøytestøpte deler
Det er også viktig å merke seg at kostnadene for produksjon av korttidssprøytestøpeformen for produksjon av små serier og oppsett er faste og må fordeles på antall bestillinger.
Generelt er sprøytestøping i korte serier egnet for deler fra 1 til 10 000. Hos Sincere Tech tilbyr vi to verktøyalternativer: prototypformer, som normalt er forbundet med en garanti på minst 2000 skudd, og produksjonsformer på forespørsel, som er forbundet med en garanti for formens levetid. Hvis aluminiumsverktøyet blir ødelagt, vil selskapet erstatte det uten å belaste kunden noe. Når det gjelder mengden av det produserte produktet, er begge alternativene ganske rimelige.
Andre spesialtjenester er inspeksjon av første artikkel, kapabilitetsrapporter, rapporter om utvikling av vitenskapelige støpeprosesser og PPAP. Noen kunder har innsett at en kortsiktig aluminiumsform kan brukes som sluttproduktform.
Hvis det dreier seg om millioner av deler, kan det være mer hensiktsmessig å bruke produksjonsverktøy. På den annen side kan 3D-printing være billigere når det gjelder produksjon av et fåtall deler. Noen av produsentene bruker 3D-printing til å lage prototyper og bruker deretter sprøytestøping i små opplag.
Bruksområder for sprøytestøping av korte serier
Den beste strategien er avhengig av organisasjonens behov og situasjonen i organisasjonen. For eksempel kan et firma som produserer medisinsk utstyr, og som har utviklet et nytt medisinsk utstyr, men som er i tvil om markedssituasjonen, bruke et kortsiktig injeksjonsinstrument. Dette er til fordel for en "pay-as-you-go"-tilnærming under introduksjonen av produktet. Hvis de på et senere tidspunkt bestemmer seg for å investere i et stålverktøy, kan aluminiumsformen brukes som et midlertidig verktøy frem til produksjonsformen er laget.
Det er også viktig å merke seg at broverktøy ikke bare er begrenset til oppstartsfasen av produktlanseringen. De kan være en ganske billig måte å forsikre seg på for modne programmer. For eksempel kunne en produsent av hvitevarer fortsette med produksjonsprosessen siden han eller hun brukte et broverktøy for å fikse hovedverktøyet. De har nå en ekstra form som de kan bruke i fremtiden, for eksempel hvis etterspørselen etter produktet øker eller hvis det nåværende verktøyet ikke er effektivt.
Sprøytestøping i korte serier er en god mellomting for designerne, som kan få den beste formdesignen og ytelsen til sluttproduktet med relativt lav risiko sammenlignet med direkte bruk av produksjonsverktøy i stål fra 3D-printede modeller. Dette er spesielt viktig i bransjer som medisinsk utstyr, der det er viktig å forkorte tiden det tar å utvikle disse produktene, samtidig som man sikrer at produktene oppfyller de fastsatte lovbestemte standardene, siden dette er kostnadseffektivt.
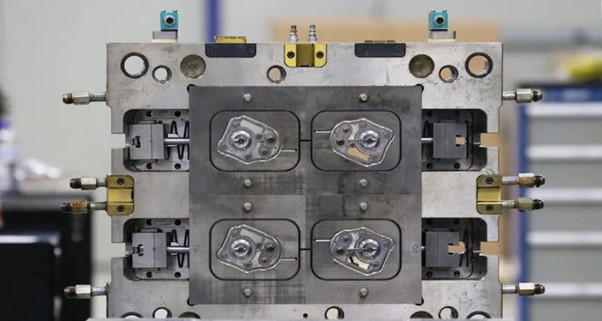
Sprøytestøping av store volumer
Vårt digitale nettverk er i stand til å produsere større og mer kompliserte deler i store volumer dersom sprøytestøping i små serier ikke er aktuelt for deg. Vårt utvidbare utvalg av tjenester inkluderer;
- Prosjekter for støpte elementer som er store, tunge og forseggjorte i design
- Tilbud på mer enn 100 000 komponenter
- Støpemuligheter for deler som er opptil 79 tommer (2 meter) store
- Mold-Tech-finish og en rekke ulike overflatebehandlinger (A1-A3, B1-B3, C1-C3, D1-D3).
- Verktøy som verktøystål P20 og aluminium og stål, fargematchende verktøy i henhold til kundens krav.
- Vil du vite mer om sprøytestøping av korte serier? Last opp en fil for en gratis formbarhetskontroll og snakk deretter med et medlem av Protolabs' støpeteam. Start rask og effektiv produksjon av deler med våre tjenester.
Er kostnadene ved sprøytestøping av korte serier høye?
Noen av hverdagsproduktene som har deler som er laget ved hjelp av sprøytestøping, er vannkokere, lyskontroller og tastaturtaster. Vanligvis produseres slike produkter i store volumer, fra hundretusener av sett.
Denne byggemetoden har flere fordeler, som kostnadseffektivitet, allsidighet i materialvalg og fleksibilitet.
Denne teknikken er best egnet for masseproduksjon på grunn av sin allsidighet, tilgjengeligheten av mange typer materialer og det faktum at den er billigere per del. Denne prosedyren muliggjør dagens rimelige priser fordi kostnadene for elementer er i øre, og syklustidene er i sekunder. Det gjelder også materialvalget, som kan være fleksible elastomerer og polymerer som kan brukes der man vanligvis bruker metaller.
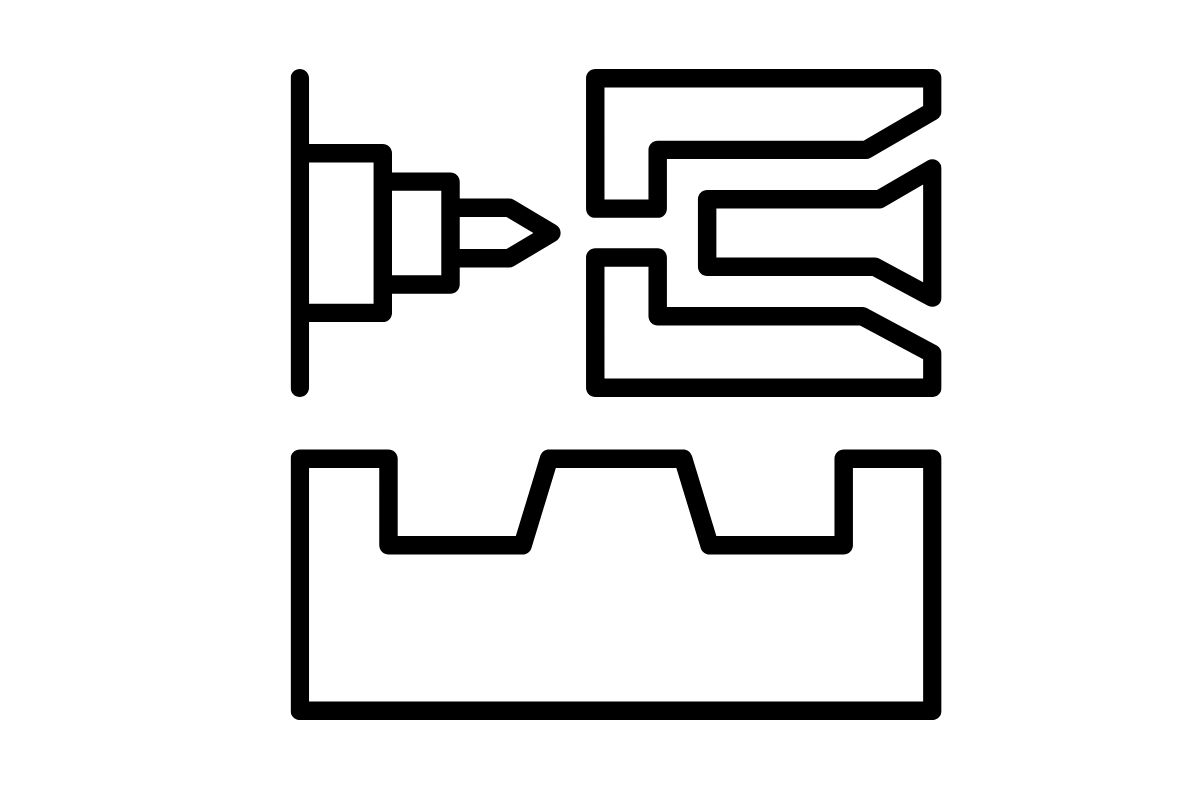
Hva om du trenger færre komponenter?
Verktøykostnadene utgjør en betydelig komponent når et lite antall deler skal produseres. Den tradisjonelle metoden for å produsere verktøy er dyr og tar også mye tid. Det finnes imidlertid mange moderne alternativer som kan brukes for å minimere utgiftene i dag.
De viktigste kostnadsfaktorene er oppsett og løpende kostnader.
Verktøyet plasseres i støpepressen, materialet/fargen tørkes og tilføres, støpeforholdene stilles inn, og de første kvalitetskontrollprøvene tas under oppsettet. Verktøyet må beskyttes, resten av materialet må fjernes, og formen må åpnes og lagres etter støpesyklusen. Denne klargjøringen faktureres vanligvis per del, spesielt for korte serier, og kan ta alt fra én time til en halv dag, avhengig av størrelsen på verktøyene og antall material-/fargeskift.
Prosedyren for å forme
Kostnadene som påløper i støpefasen inkluderer kostnadene for materialet som brukes, kostnadene for pressen og den manuelle eller automatiske driften av mediet. Materialkostnadene avhenger også av hvilken type materiale som brukes og hvor mye materiale som er kjøpt inn. Det er stor forskjell på å kjøpe en liten mengde materiale og en stor mengde av det samme materialet. Spesialpigmenter kan også føre til økte kostnader, siden de brukes i prosessen med å produsere det endelige produktet.
Faktorene som påvirker presskostnadene, er blant annet skuddvekt, som er mengden plast som sprøytes inn i løpet av en enkelt syklus, og tonnasje, som er kraften som brukes til å lukke formen under innsprøytingen. Store presser er kostbare på grunn av høye driftskostnader og avskrivning av utstyret. Kostnadene kan også påvirkes av behovet for manuelle operasjoner, for eksempel lasting og tømming av innsatsen eller andre operasjoner etter støping.
Verktøy som er helautomatiserte og skaper volum på en konstant basis, skiller seg fra verktøy som er laget for små partier og krever manuell overføring og pakking.
Alternativer til prototyping
Det er en stor fordel å lage prototyper i det tiltenkte produksjonsmaterialet. Når det gjelder prototyper og kortserieproduksjon, er det mange valgmuligheter når det gjelder verktøy, og det er mulig å støpe så få som to deler. Tempoet for prototyping og produksjon av deler kan imidlertid variere, og noen av hendelsene kan ta flere dager. Dette avhenger av overflaten, materialet og geometrien til strukturen som skal belegges. Forsinkelsestiden er normalt mellom to og fire uker.
Utgifter til verktøy
Kostnaden for verktøy avhenger av elementets kompleksitet, størrelse og hvor lang tid det tar å lage det. Formene er ikke billige; de koster fra 2 000 pund for de enkleste, mens de mer komplekse koster fra 5 000 til 7 000 pund. Prisen på store eller komplekse gjenstander kan gå opp til 30 000 pund. Opplysningene om det aktuelle prosjektet og det detaljerte tilbudet er grunnlaget for et nøyaktig kostnadsoverslag.
For sprøytestøpeprosjekter i små volumer anbefales det at du søker råd fra fagfolk for å få en bredere forståelse av mulige kostnader og mulige gjennomførbare løsninger. Hvis du tenker på å bruke sprøytestøping i korte serier til prosjektet ditt og ønsker å vite kostnadene for de nødvendige mengdene, er du velkommen til å kontakte oss for et tilbud.
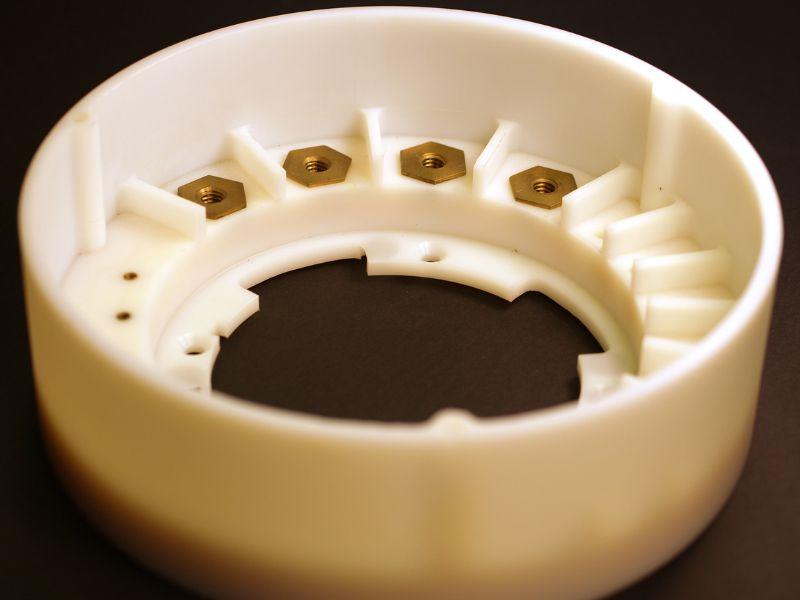
Sprøytestøpingstjenester som tilbys av Sincere Tech
Sincere Tech er en av 10 plastsprøytestøpefirmaer i Kina som ble grunnlagt for over ti år siden og har vært involvert i design og produksjon av sprøytestøpte deler og varer av plast. På grunn av vår omfattende ekspertise er vi i stand til effektivt å administrere alle faser av kortsiktige sprøytestøpeprosjekter, inkludert Med denne omfattende ekspertisen er vi i stand til effektivt å administrere alle faser av kortsiktige sprøytestøpeprosjekter, inkludert:
Formdesign: Vi bruker de beste teknologiene og formfremstillingsteknologiene for å produsere instrumenter som tilfredsstiller behovene til produktet ditt. Vi lager verktøydesign basert på dine originaltegninger, skjemaer eller modeller, eller vi kan lage dem for deg. Vi har ekspertise i bruk av AutoCAD, SolidWorks, ProE, Cimatron og CADKey CAD-formater.
Vårt team for produksjon av støpeformer bruker moderne CNC-maskineringsteknologi for å produsere høykvalitets og nøyaktig dimensjonerte støpeformer på kortest mulig tid etter at designen av sprøytestøpeformen er ferdig. Dette er et eksempel på spesialtilpasset verktøy. Vi kan lage prototyper for ulike termoplaster, inkludert ABS, HDPE, LDPE, PE, HIPS, TPU og PET.
Prototyping: Vi bruker 3D-printing til å bygge hver enkelt del raskt for å sikre at den passer til formen og fungerer som den skal før sprøytestøpeverktøyet konstrueres. Vi tilbyr FDM-printede prototyper i ulike typer materialer som ABS, PLA og TPU. Vi samarbeider med andre tjenesteleverandører for ytterligere prototypingstjenester, for eksempel uretanstøping, SLS og SLA.
Sprøytestøping: Den sprøytestøping Anlegget drives av erfarne medarbeidere, og utstyret kan produsere en klemkraft på 28 til 240 tonn og kan også vise til reproduserbarhet. Materialet som vi behandler under støpeoperasjonene våre, varierer fra 0 til 16 gram per syklus. Sincere Tech kan også tilby sprøytestøpingstjenester for små og store mengder produkter.
Vi garanterer at de spesialtilpassede sprøytestøpte plastdelene som vi leverer hos Sincere Tech vil være av beste kvalitet, leveres i tide og til en rimelig pris.