Plastformer for betong er produsert av forskjellige typer plast i spesialdesignede former. Disse formene brukes til å gi nødvendige former og design av betongprodukter. Plastformer for betong kan gjenbrukes, og de gir også fleksibilitet til å lage et veldig stort utvalg av produkter som er laget av betong. Disse betongproduktene kan være så enkle som en blokk eller kan være kompliserte som komplekse dekorative gjenstander. Introduksjonen av ulike plastformer for betong har ført til en revolusjon i måten betongprodukter designes og formes på.
I industrisektoren og DIY (Do It Yourself)-applikasjoner støpeform av plastbetong gir en kostnadseffektiv løsning som også er unik. Plastformer for betong er mye bedre enn de tradisjonelle metallformene, og treformer er tyngre og mindre holdbare sammenlignet med plastformer for betong. Dessuten har plastformer for betong vist seg å ganske enkelt produsere de ønskede komplekse og intrikate formene som ikke er så lett å oppnå ved å bruke metall- eller treformer.
Det finnes et bredt spekter av bruksområder for plastformer for betong, som inkluderer konstruksjon av arkitektoniske gjenstander, betongmøbler, produksjon av dekorative hageornamenter og belegningsstein. Plastformer for betong er enkle å bruke og er rimelige. De gir resultater av topp kvalitet i den moderne æraen av design og konstruksjon.
Typer plast Betong Støpeformer med en kort beskrivelse av produksjonsprosesser, viktige egenskaper og grunnleggende bruksområder
Det finnes mange typer støpeformer av plastbetong som er produsert for spesifikke bruksområder. De grunnleggende faktorene som forskjellige typer plastformer for betong er basert på, er følgende.
- Størrelse på betongproduktet
- Kompleksiteten til det konkrete produktet
- Ulike detaljer om betongproduktet
Nedenfor beskrives de viktigste typene av plastformer for betong, deres egenskaper og bruksområder.
Sprøytestøpte betongformer av plast
Disse formene fremstilles og produseres ved hjelp av en svært nøyaktig og godt kontrollert produksjonsprosess som kalles sprøytestøping.
Kort om produksjonsprosessen for sprøytestøpte betongformer av plast
Prosessen starter med å lage en detaljert design av den nødvendige plastbetongformen. Dette gjøres ved hjelp av CAD-programvare. Den produserte CAD-modellen brukes deretter til å lage metallformen. Deretter tilberedes plastpellets av utvalgte plastmaterialer. I sprøytestøpemaskinen varmes disse plastpelletsene opp. Den resulterende smeltede plasten injiseres til slutt i metallformhulen.
Dette gjøres under høyt trykk. Den smeltede plasten kjøles ned i metallformen og stivner. Deretter skyves det støpte plaststykket ut av formen. Trimmingsprosessen blir deretter tatt i bruk for å fjerne overflødig materiale som blits og etterbehandlingsprosesser utføres for å fullføre de sprøytestøpte plastformene. Denne produksjonsprosessen er veldig egnet for masseproduksjon. De produserte formene er av jevn kvalitet.
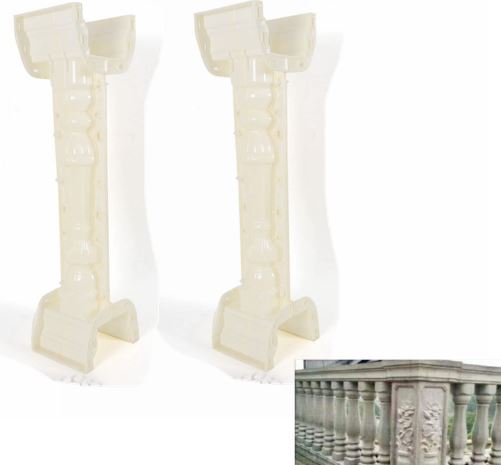
støpeform av plastbetong
Viktige kjennetegn
De viktigste egenskapene til disse formene er nevnt nedenfor.
- Disse formene har høy presisjon og har evnen til å produsere fine detaljer og komplekse design
- Disse formene har høy styrke og holdbarhet
- Disse formene gir høy produksjonshastighet
Grunnleggende utnyttelse
Den grunnleggende bruken av sprøytestøpte plastformer inkluderer følgende.
- De brukes til å forme mange dekorative gjenstander som hageornamenter og statuer
- De brukes til å danne intrikate arkitektoniske elementer som utsmykkede gesimser og balustre
- De brukes også til å forme detaljerte fliser og belegningsstein
Støpeformer av vakuumformet plast
Disse formene produseres ved å varme opp en plastplate. Denne varmen opprettholdes til plastplaten blir bøyelig. Deretter brukes vakuumsug for å forme den over en form.
Kort om produksjonsprosessen for vakuumformede støpeformer av plastbetong
Prosessen med å lage vakuumformede plastformer for betong starter på samme måte som for sprøytestøpte plastformer. I det første trinnet designes formen ved hjelp av CAD-programvare. Deretter lages et hovedmønster eller en modell av materialer som tre, skum eller harpiks. Disse materialene velges ut fra ønsket design. Deretter skjæres det valgte plastmaterialet til i henhold til ønsket størrelse. Denne platen plasseres i en vakuumformingsmaskin. Platen varmes opp til den blir bøyelig.
Hovedmønsteret plasseres deretter på maskinens formbord. Den oppvarmede plastplaten senkes ned på dette hovedmønsteret. Plasten suges av en vakuumpumpe mot mønsteret, noe som skaper den ønskede formen. Den herdede og avkjølte plasten fjernes deretter fra maskinen. Den påfølgende trimmingsprosessen brukes til å fjerne overflødig materiale. Plastformen skilles fra hovedmønsteret på en forsiktig måte. Kantene på formen glattes ut for å sikre at betongen frigjøres på en ren måte når den brukes i applikasjoner. Deretter gjennomgår formen en kvalitetskontroll for å se etter feil som bobler eller ufullstendig forming.
Om nødvendig forsterkes plastbetongformen for økt holdbarhet. Et slippmiddel eller belegg påføres for å lette avformingen, og formen testes med en liten mengde betong for å sikre at den fungerer som den skal. Etter dette klargjøres formene for produksjon, lagres på riktig måte for å opprettholde tilstanden, og rengjøres regelmessig. En siste inspeksjon utføres for å sikre at formene er klare til bruk i betongproduksjonen, og at de er nøyaktig formet og holdbare.
Viktige kjennetegn
Disse formene har følgende kjennetegn og egenskaper.
- Disse formene gir en kostnadseffektiv løsning sammenlignet med sprøytestøpte plastformer fordi de er mye rimeligere å produsere
- Disse formene har egenskapen fleksibilitet, og derfor anses disse formene som ideelle for å skape store, men enkle former og design
- Plastplater brukes i disse formene, slik at de er enkle å transportere og håndtere
Grunnleggende utnyttelse
Vakuumformede plastformer brukes i følgende scenarier.
- Flisene og belegningssteinene, som er mye større i størrelse, er laget av vakuumformede plastformer
- Disse formene brukes til å forme hageelementer og grunnleggende dekorative produkter
- Vakuumformede plastformer brukes også til å lage former for DIY-betongprosjekter
Rotasjonsstøpte plastformer
Disse formene produseres ved hjelp av rotasjonsstøping. I denne metoden fylles en roterende form med plastharpiks samtidig som den varmes opp fra en hul form.
Kort om produksjonsprosessen for plastbetongform
Opprettelse av rotasjonsstøpte plaststøping for betong innebærer en detaljert prosess for å sikre høy kvalitet og holdbarhet. Det starter med å designe formen ved hjelp av CAD-programvare. En metallform som er laget av aluminium eller stål, blir produsert. Fremstillingsmetode og materiale velges på grunnlag av ønsket design. Deretter beregnes den valgte plastharpiksen, for eksempel polyetylen, og legges i formen. Formen forsegles deretter veldig tett. Denne formen plasseres i en ovn der den varmes opp og roteres på to akser samtidig.
Dette gjør at den smeltede harpiksen kan dekke de innvendige overflatene jevnt. Deretter overføres formen til en kjølestasjon. Rotasjonen fortsetter til plasten er avkjølt og til slutt størknet. Etter at avkjølingen og størkningen er fullført, åpnes formen på en forsiktig måte. Plastdelen som er dannet, fjernes. Eventuelt overflødig materiale trimmes av, og kantene og overflaten glattes for å sikre en ren utløsning.
Formen inspiseres for defekter som bobler eller ufullstendig forming, og kan forsterkes for å øke holdbarheten. Et slippmiddel eller belegg påføres for å gjøre det enklere å avstøpe, og formen testes med en liten mengde betong for å sikre at den fungerer som den skal. Til slutt klargjøres formen for gjentatt bruk eller masseproduksjon, med regelmessig rengjøring og vedlikehold for å forlenge levetiden og sikre jevn ytelse. Denne omfattende prosessen resulterer i holdbare, nøyaktig formede støpeformer som er klare for effektiv produksjon av betongprodukter.
Viktige kjennetegn
Disse formene har følgende egenskaper og bruksområder.
- Disse formene har jevn veggtykkelse fordi plastmaterialet fordeles jevnt under produksjonsprosessen
- Disse formene er svært godt egnet til å forme tunge produkter på grunn av deres holdbarhet og styrke
- Rotasjonsstøpte plastformer har evnen til å forme store gjenstander som ikke er mulig å forme med andre former
Grunnleggende utnyttelse
- Rotasjonsstøpte plastformer brukes til å forme store betongmøbler, inkludert bord og benker
- Disse formene brukes til å forme strukturelle elementer som vannspeil og plantekasser
- Rotasjonsstøpte plastformer brukes også til å forme store dekorative hageartikler
4. 3D-printede plastformer
3D-printede plastformer produseres av termoplastiske materialer ved å bygge opp en form lag for lag fra en digital modell.
Kort om produksjonsprosessen
Prosessen med å lage 3D-printede støpeformer av plastbetong startes på samme måte som for andre metoder for formfremstilling. I det første trinnet utføres utformingen av formen ved hjelp av CAD-programvare. Dette trinnet utføres fordi det gir hjelp til å skape presise og detaljerte former. Etter at designen er fullført, konverteres den til et filformat. Det er viktig å merke seg at dette filformatet må være kompatibelt med 3D-utskrift. Generelt velges følgende to materialer valgt for 3D-trykte plastformer.
- Polymelkesyre
- Akrylnitril-butadien-styren
Disse utvalgte materialene lastes deretter inn i 3D-skriveren. Skriveren konstruerer deretter formen lag for lag basert på den digitale designen. Etter utskriften tas formen forsiktig ut av skriveren. Deretter rengjøres støttestrukturer og ekstra materialer, og formen inspiseres for nøyaktighet, og siste finpuss, som sliping eller forsegling, påføres for å glatte overflaten.
Et slippmiddel eller belegg tilsettes for å gjøre det lettere å fjerne betongen. Formen testes med en liten mengde betong for å sikre at den fungerer som den skal og at betongen stivner som forventet. Formen er klar til bruk når effektiviteten er bekreftet ved å gjøre eventuelle nødvendige justeringer. Det er viktig å nevne at regelmessig rengjøring og vedlikehold av formene er svært viktig av følgende to grunner.
- For å holde formen i god stand
- For å forlenge levetiden
Metoden med 3D-utskrift av plastformer gjør det mulig å produsere svært detaljerte og tilpassede former. Dette er svært godt egnet for en rekke konkrete bruksområder.
Viktige kjennetegn
3D-printede plastformer har følgende egenskaper og bruksområder.
- 3D-printede plastformer har muligheten til å produsere komplekse og unike design fordi disse formene er svært tilpasningsdyktige
- Disse formene gir mulighet for raske og gjentatte endringer, og er derfor svært godt egnet for å forme ny design
- 3D-printede plastformer har kvaliteten til å produsere detaljerte og intrikate former, så disse formene egner seg best for småskalaproduksjon
Grunnleggende utnyttelse
- 3D-printede plastformer brukes til å forme skreddersydde og allsidige pyntegjenstander
- Disse formene brukes til å produsere prototyper for å teste ut ny design og nye funksjoner
- De svært detaljerte spesialiserte elementene som hovedsakelig brukes i arkitektur, er formet av 3D-printede plastformer
Fordeler med plastformer for betong
Plastformer for betong gir mange fordeler ved betongstøping, noe som gjør dem til et populært valg i bygg- og anleggsbransjen og til dekorative formål. De fremtredende fordelene med plastformer for betong er som følger.
- Kostnadseffektivt
Plastformer er generelt rimeligere sammenlignet med metallformer. Dermed er de et attraktivt valg for både små og store prosjekter.
- Lettvekt
Plastformer er mye lettere enn metallformer. Så disse formene er lettere å håndtere, transportere og plassere. Denne evnen fører til slutt til å redusere arbeidskostnadene og gjøre støpeprosessen forenklet.
- Fleksibilitet og allsidighet
Plastformer for betong kan designes og produseres i et stort utvalg av former og størrelser. De egner seg godt til å skape komplekse og intrikate design som er vanskelige eller kostbare med andre materialer.
- Brukervennlighet
Plastformer krever mindre vedlikehold enn metallformer og er enkle å bruke. De kan forhåndsformes med presise detaljer, noe som reduserer behovet for ytterligere etterbehandling av betongen.
- Holdbarhet
Moderne plastformer for betong er produsert av materialer av høy kvalitet. Disse materialene er holdbare og kan gjenbrukes mange ganger. Dessuten er de motstandsdyktige mot støt, slitasje og mange kjemikalier. Dette bidrar til å opprettholde form og funksjonalitet over tid.
- Motstandsdyktighet mot korrosjon
Dette er en stor fordel med plastformer i forhold til metallformer. Plastformer ruster eller korroderer ikke, så denne egenskapen er spesielt fordelaktig i følgende scenarier.
- ved arbeid med betongblandinger som kan inneholde korrosive stoffer
- når formene utsettes for fuktighet
- Glatt overflatefinish
Plastformene gir en svært jevn og god overflatefinish på betongen. Dermed reduseres behovet for ytterligere overflatebehandling eller etterbehandling. Dette forbedrer den estetiske kvaliteten på det ferdige produktet og gir en kostnadseffektiv løsning.
- Rask produksjon
Plastformer gir raske produksjonshastigheter, spesielt med metoder som vakuumforming eller 3D-utskrift. Denne egenskapen ved plastformer kommer godt med i prosjekter med korte tidsfrister.
- Gjenbrukbar
Plastformer er et bærekraftig alternativ for betong fordi de er designet for å kunne gjenbrukes. Hvis de vedlikeholdes regelmessig, kan det forlenge levetiden og redusere behovet for konstant utskifting.
- Tilpasning
For å oppfylle spesifikke designkrav kan plastformene enkelt tilpasses. Denne fleksibiliteten gjør det mulig å produsere allsidige eller spesialformede betongelementer.
- Non-Stick-egenskaper
Det er viktig å merke seg at mange plastformer er behandlet eller belagt for å ha egenskaper som gjør at de ikke fester seg. Dette hindrer betongen i å feste seg til formen. Dermed blir avformingen enklere, noe som reduserer risikoen for å skade det ferdige produktet.
Grunnleggende faktorer å ta hensyn til ved bruk av plast Betong Former
Ved bruk av plaststøping i betong er det flere viktige faktorer å ta hensyn til for å oppnå best mulig resultat og lang levetid for støpeformene. Disse faktorene er beskrevet i detalj nedenfor.
- Valg av materiale
Hvilken type plast som brukes i produksjonen av formene er av stor betydning. Det er velkjent at ulike plasttyper har forskjellige egenskaper. Polyetylen med høy tetthet gir utmerket holdbarhet og slagfasthet sammenlignet med andre plastmaterialer. Dermed vil valg av riktig plast for spesifikke behov og krav bidra til å oppnå de beste resultatene og forlenge levetiden til formen.
- Formdesign
Det er relevant å nevne at kompleksiteten i formdesignen til syvende og sist påvirker sluttproduktet. Derfor må formene utformes med stor omhu for å inkludere funksjoner og aspekter som trekkvinkler og utløsningsmekanismer for å sikre at betongprodukter kommer jevnt ut og formen forblir intakt. Detaljerte design kan dessuten kreve ekstra presisjon i både formfremstilling og håndteringsprosedyrer.
- Utgivelsesagenter
Den viktigste faktoren å ta hensyn til ved bruk av plastformer for betong er påføring av riktig slippmiddel. Disse midlene brukes for å forhindre at betongen fester seg til formen. De mest brukte typene slippmidler er følgende.
- Oljebaserte slippmidler
- Vannbaserte slippmidler
- Silikonbaserte slippmidler
- Pulverfrigjøringsmidler
- Naturlige og miljøvennlige slippmidler
- Skumfrigjøringsmidler
- Slippmidler for høy temperatur
Det er viktig å merke seg at valget av slippmiddel må være kompatibelt med plastmaterialet i formen. Dette er nødvendig for å opprettholde kvaliteten og integriteten til betongproduktet.
- Temperatur og herding
Plastformer for betong kan være ganske følsomme for temperaturvariasjoner. Derfor er det viktig å håndtere herdeforholdene på en nøye måte. Dette er av stor betydning på grunn av følgende.
- For høy varme kan gjøre formen skjev
- Utilstrekkelig varme kan påvirke betongens herding
Den grunnleggende faktoren for å sikre at støpingen blir akseptabel, er derfor å sørge for at herdetemperaturen er egnet for både formen og betongblandingen.
- Rengjøring og vedlikehold
Rengjøring og vedlikehold av plastformer for betong er viktig og kritisk. Den grunnleggende årsaken til dette er at rester av betong kan skape problemer for fremtidig bruk av formene. Derfor er det viktig med regelmessig rengjøring og vedlikehold med egnede metoder. Videre må det utføres regelmessige rutinekontroller for slitasje. Dette vil til syvende og sist bidra til å bevare formens effektivitet.
- Miljøpåvirkning
Det er viktig å ta hensyn til miljøeffektene av plastformene for betong. Plastmaterialet som er valgt for mugg, hvis det ikke er biologisk nedbrytbart og ikke resirkulerbart, kan forårsake negative påvirkninger på miljøet. I motsetning til det, vil valg av resirkulerbar eller biologisk nedbrytbar plast helt sikkert ha en positiv innvirkning på miljøet. Videre er riktig avhending eller resirkulering av gamle støpeformer også av stor betydning for å redusere den negative og skadelige miljøpåvirkningen.
Konklusjon
Plastformer er et praktisk og kostnadseffektivt valg for betongstøping, med fleksibilitet og holdbarhet. Plastformer for betong gir effektive løsninger for betongstøping som gir verdi i komplekse og intrikate design. De gjør det enkelt å produsere detaljerte og tilpassede design, samtidig som de er lette og motstandsdyktige mot korrosjon. Med riktig håndtering og vedlikehold gir plastformene pålitelig ytelse og resultater av høy kvalitet på tvers av ulike bruksområder. Støpeformer av plast har evnen til å håndtere et stort utvalg av betongblandinger og støping miljøer på en effektiv måte. Regelmessig vedlikehold, forsiktig håndtering og riktig oppbevaring bidrar til å forlenge levetiden og ytelsen til plastbetongformene ytterligere. Alt i alt er de et utmerket verktøy for både dekorative og strukturelle betongprosjekter.