의미 PMMA 사출 성형
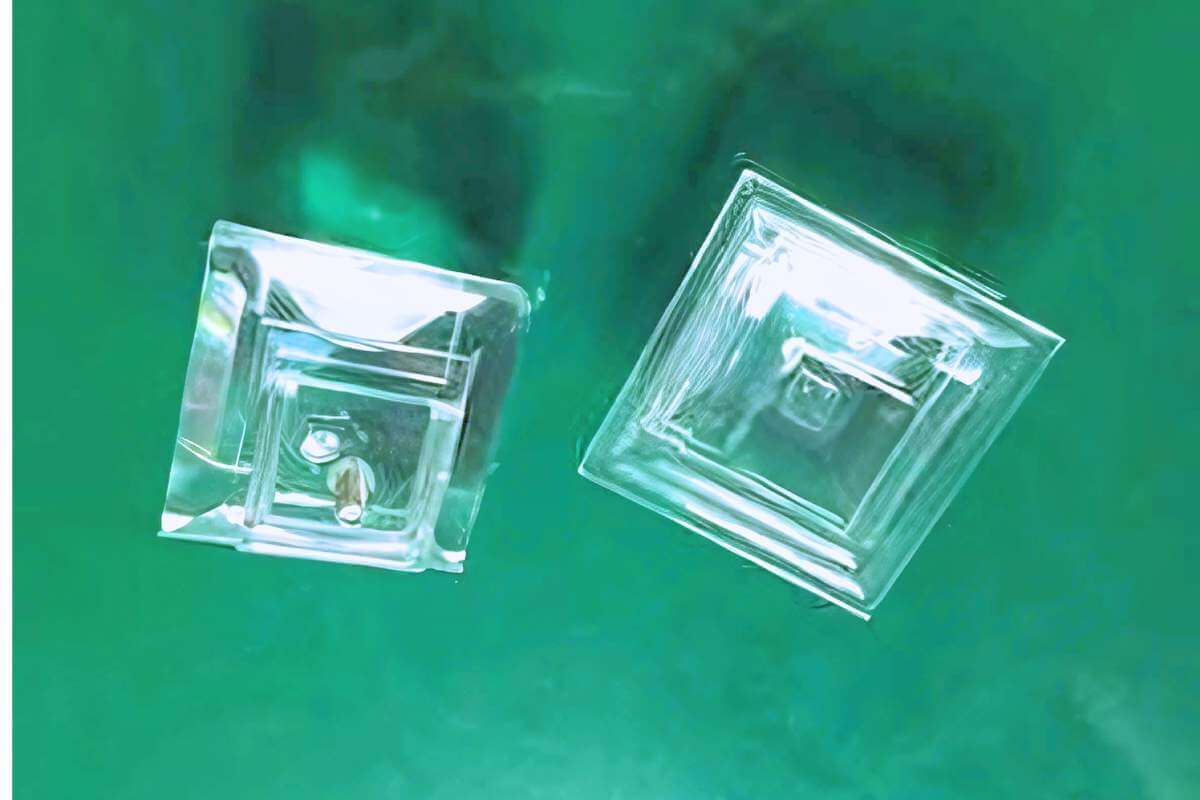
PMMA 사출 성형 기술
PMMA는 가장 높은 이식용 플라스틱 소재이지만 PC나 ABS에 비해 잘 깨지기 때문에 메틸 메타크릴레이트와 스티렌의 공중합, PMMA와 PC의 혼합물인 부타디엔 등 PMMA의 변형이 속속 등장하고 있습니다. 372 PMMA는 메틸 메타크릴레이트와 스티렌의 공중합체입니다. 372 PMMA에 소량의 니트릴 고무(약 50%)를 첨가하면 373 PMMA가 됩니다.
사출 성형 PMMA의 유동성은 PS, ABS보다 열악하며 용융 점도는 온도 변화에 다소 민감합니다. 성형 시 주로 사출 온도에 따라 용융 점도가 달라집니다. PMMA는 비정질 폴리머로 용융 온도가 섭씨 200도 이상이고 분해 온도는 섭씨 270도에 달할 수 있습니다.
- 플라스틱 가공
PMMA 플라스틱은 0.3-0.4%의 어느 정도의 수분 흡수율을 가지고 있습니다. 그리고 사출 성형 PMMA 수분은 0.1% 미만이어야 합니다. 일반적으로 0.04%입니다. 수분이 있으면 기포, 가스 라인 및 낮은 투명도가 발생합니다. 따라서 건조시켜야 합니다. 건조 온도는 섭씨 80-90도, 건조 시간은 3시간 이상입니다. 경우에 따라 재활용 재료의 활용도는 100%에 달할 수 있습니다. 실제 수량은 품질 요구 사항에 따라 다릅니다. 일반적으로 30%에 도달할 수 있습니다. 재활용 재료의 오염이 없는지 확인해야 하며, 그렇지 않으면 완제품의 투명성과 특성에 영향을 미칩니다. - 사출 성형기 선택
사출 성형 PMMA 소재 는 사출 성형기에 대한 특별한 요구 사항이 없습니다. 용융 점도가 높기 때문에 홈이 더 깊어야 하고 노즐 구멍의 직경이 더 커야 합니다. 강도가 더 높은 제품이 필요한 경우 저온 플라스틱을 구현하려면 스크류의 종횡비가 더 큰 것을 사용해야 합니다. 또한 PMMA 성형 수지는 건조 호퍼를 사용하여 재료를 보관해야 합니다. - 몰드 및 게이트 설계
PMMA 사출 금형 온도는 60-80°C일 수 있습니다. 스프 루의 직경은 내부 테이퍼와 일치해야합니다. 최적의 각도는 5 ~ 7입니다. 사출 성형 제품의 벽 두께가 4mm 이상인 경우 각도는 7, 주류 채널의 직경은 8 ~ 10mm, 게이트의 전체 길이는 50mm를 초과하지 않아야합니다.
벽 두께가 4mm 미만인 PMMA 사출 성형 제품의 경우 흐름 채널의 직경은 6~8mm여야 합니다. PMMA 벽 두께가 4mm 이상인 경우 흐름 채널의 직경은 8~12mm여야 합니다. 팬 모양 및 탭 모양 게이트의 깊이는 0.7 ~ 0.9 t (t는 제품의 벽 두께)여야하며 핀 게이트의 직경은 0.8 ~ 2mm 여야합니다. 점도가 낮은 사출 성형 PMMA 제품은 더 작은 크기를 선택해야 합니다. 일반적인 배출 구멍의 깊이는 0.05~0.07mm, 폭은 6mm, 스트리핑 경사는 30′-1, 캐비티 부분은 35′-1에서 30 사이입니다.
- 용융 온도
공기 주입 방법을 사용하여 공급업체가 제공한 정보에 따라 섭씨 210도에서 270도 사이의 온도를 측정할 수 있습니다. - 사출 온도
PMMA 사출 성형 재료로 작업할 때 높은 수준의 내부 응력 발생을 피하기 위해 급속 사출을 사용할 수 있습니다. 느리게, 빠르게, 천천히 등 다단계 사출을 사용하는 것이 적합합니다. 두꺼운 부품을 사출할 때는 느린 속도를 사용해야 합니다. - 체류 시간
온도가 섭씨 260도인 경우 체류 시간은 10분 이내입니다. 온도가 섭씨 270도인 경우 체류 시간은 8분 이내입니다.
PMMA 플라스틱 사출 성형의 응용 분야
PMMA 사출 성형 부품을 필요로 하는 산업 분야는 많습니다. 다음은 사출 성형 PMMA 부품을 사용하는 몇 가지 구성 요소입니다:
- 안경 렌즈: PMMA는 뛰어난 광학적 특성으로 인해 안경에 가장 적합한 소재 중 하나입니다. 다른 모든 플라스틱 소재 중 투명도가 가장 높은 PMMA 사출 성형으로 안경에 가장 적합한 소재입니다.
- 플렉시글라스 창문: 플렉시글라스 또는 아크릴 유리라고도 하는 PMMA는 높은 내충격성과 광학적 선명도로 인해 기존 유리창의 대안으로 널리 사용되고 있습니다. 일반적으로 건물, 수족관, 심지어 비행기 창문에도 사용됩니다.
- 휴대폰 케이스: PMMA는 내충격성, 내스크래치성, 광학 선명도가 높아 휴대폰 케이스 제조에 사용됩니다. 또한 가볍고 다양한 모양과 크기로 쉽게 성형할 수 있습니다.
- 컴퓨터 및 전자제품 케이스: 휴대폰 케이스와 마찬가지로 PMMA는 내구성, 내충격성, 광학 선명도 등의 특성으로 인해 컴퓨터 및 전자제품 케이스 제조에 사용됩니다. 또한 가볍고 다양한 모양과 크기로 쉽게 성형할 수 있습니다.
- 차량 앞유리: PMMA는 높은 내충격성과 광학적 선명도로 인해 차량 앞유리 제조에 일반적으로 사용됩니다. 또한 유리보다 가볍기 때문에 연비를 개선할 수 있습니다.
- LED 렌즈: 길거리와 집에서 볼 수 있는 조명의 내부에 있는 작은 렌즈는 PMMA 사출 성형 부품으로 만들어집니다. 이것은 조명 산업에서 매우 인기가 있습니다.
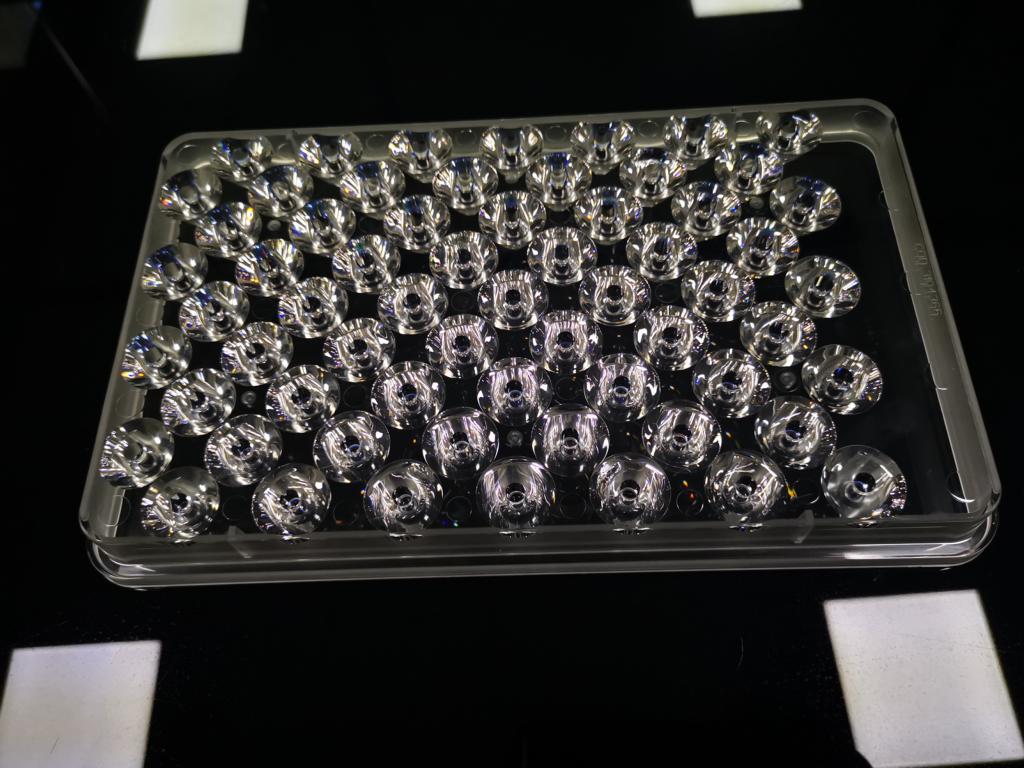
사출 성형 PMMA
PMMA 사출 성형의 장점 (아크릴 사출 몰딩)
1. 스크래치에 강한 제품을 생산합니다.
2. 광이식 제품을 생산합니다.
3. PMMA 사출 성형은 복잡한 디자인을 생산할 수 있습니다.
4. 높은 생산 효율성
5. 색상 유연성 향상
6. 투명 플라스틱 성형의 높은 요구 사항을 위한 특수 소재.
PMMA 소재 아크릴또는 플렉시글라스는 투과율이 최대 92%로 유리보다 높습니다. 이는 곧 투명 아크릴 상자 몰딩은 높은 요구 사항을 충족하는 최고의 옵션 중 하나입니다. 투명 사출 성형 부품유리, 광학 유리, 렌즈, 자동차 조명, 투명 파이프 등과 같은 다양한 소재에 사용됩니다.
아크릴 PMMA 플라스틱 사출 성형의 단점
다른 성형 제조 공정과 마찬가지로 고려해야 할 몇 가지 단점이 있습니다. 다음은 아크릴 PMMA 플라스틱 사출 성형의 몇 가지 단점입니다.
- 생산된 소재는 다음과 같이 생산된 소재에 비해 충격에 대한 저항력이 낮습니다. 금속 사출 성형.
- PMMA 사출 공정으로 생산되는 대부분의 제품은 내열성이 낮습니다(섭씨 약 80도).
- 이 공정에서 생산되는 대부분의 품목은 기계적 강도가 낮기 때문에 적재 용량이 제한됩니다.
- 일부 아크릴 제품은 내화학성이 약해 유기 화합물과 반응하기 쉽습니다.
- PMMA 사출 성형은 특수 사출 금형을 뒤집어야 하므로 초기 툴링 비용이 높습니다. 이는 소량 생산에는 적합하지 않습니다.
- 제한된 디자인 유연성. 이 공정은 단순하고 균일한 모양의 제품을 생산하는 데 가장 적합합니다. 복잡한 디테일이 있는 복잡한 디자인은 아크릴 PMMA 플라스틱 사출 성형으로는 구현하기 어려울 수 있습니다. 이러한 한계는 독특하고 혁신적인 제품을 만들고자 하는 제조업체에게는 큰 단점이 될 수 있습니다.
고품질 PMMA 사출 성형 부품을 만들기 위한 팁.
PMMA 사출 성형 부품을 만드는 것은 다른 사출 성형 부품과 약간 다릅니다. 대부분의 경우 PMMA 성형 부품을 만들 때 고 유리 PMMA 부품을 만들기 때문입니다. 이 경우 특히 일부 두꺼운 벽 PMMA 사출 성형 부품의 경우 몇 가지 특수 장비가 필요합니다. 다음은 고품질 PMMA 사출 성형 부품을 만들기위한 몇 가지 팁입니다.
금형 설계
PMMA는 투과성 소재이므로 모든 흐름 자국이 쉽게 눈에 띄기 때문에 이 또한 문제가 될 수 있습니다. 금형 흐름 분석을 사용하여 최적의 게이트 위치가 어디인지 확인하는 것이 매우 중요합니다. 게이트 위치가 결정되면 게이트 모양도 중요합니다. 대부분 사이드 게이트 또는 팬 게이트를 설계하는 것이 좋으며, 이는 캐비티를 더 쉽게 채우고 흐름 표시를 피할 수 있습니다.
사출 성형기와 온수 탱크가 사용 중입니다.
벽이 두꺼운 PMMA 사출 성형 부품을 제작하는 경우 플라스틱은 수축률이 있기 때문에 항상 싱크 및 기포 문제가 발생합니다. 벽이 두꺼울수록 수축률이 높아져 냉각 시간이 아무리 길어도 부품 내부에 기포가 발생하고, 냉각 시간이 길어지면 사이클 시간도 늘어나 비용이 증가하게 됩니다.
이 경우 온수 탱크를 사용하면 이러한 문제를 개선할 수 있습니다. 온수 탱크에는 60~80도 온도의 물을 사용합니다. 금형 캐비티에서 PMMA 사출 성형 부품을 골라 온수 탱크에 6~12분 동안 넣은 후 성형 부품을 꺼내면 싱크 및 기포 문제가 크게 개선됩니다.
고품질 PMMA 성형 부품을 만드는 것은 쉬운 일이 아닙니다. PMMA 성형 부품이 필요한 프로젝트가 있다면 전문 PMMA 사출 성형 계약업체를 찾는 것이 매우 중요합니다. 이를 통해 프로젝트의 성공 여부를 확인할 수 있습니다.