핀 포인트 게이트 사출 성형이란?
핫 팁 게이팅 또는 다이렉트 게이팅이라고도 하는 핀 포인트 게이트 사출 성형은 정밀하고 효율적으로 플라스틱 부품을 생산하는 데 사용되는 특수 사출 성형 기술입니다. 이 공정에서는 용융된 플라스틱이 부품의 특정 지점에 위치한 작은 게이트를 통해 금형 캐비티에 직접 주입됩니다. 용융된 플라스틱이 큰 게이트를 통해 캐비티로 들어가는 기존 사출 성형과 달리 핀 포인트 게이팅을 사용하면 금형을 보다 제어되고 목표에 맞게 채울 수 있습니다.
핀 포인트 게이트 사출 성형 일반적으로 콜드 러너가있는 3 판 사출 금형과 핫 팁 게이팅을 사용하는 일부 핫 러너를 사용합니다. 이 기술은 마이크로 전자 부품 또는 의료 기기와 같은 소형 부품의 여러 캐비티 또는 게이트 마크가있는 측벽을 허용하지 않는 대형 부품의 여러 핀 포인트 게이트에 사용되며, 핀 포인트 게이트 솔루션은 일반적으로 부품 설계 및 표면 요구 사항에 따라 다릅니다.
핀 포인트 게이트는 일반적으로 성형 후 숨겨지거나 외관에 영향을 미치지 않는 위치에 위치합니다. 게이트 크기가 작기 때문에 금형 내 플라스틱 흐름을 정밀하게 제어할 수 있어 숏샷, 공기 유입, 싱크 마크와 같은 결함의 위험을 줄일 수 있습니다.
핀 포인트 사출 성형은 플라스틱의 온도와 압력, 사출 속도, 냉각 시간 등 성형 공정을 세심하게 제어해야 합니다. 또한 이 유형의 성형에는 핀 포인트 게이트의 크기가 작기 때문에 러너를 A 플레이트(캐비티)에서 빼내기 위한 추가 러너 플레이트가 필요하므로 특수 툴링(3판 사출 금형)이 필요합니다.
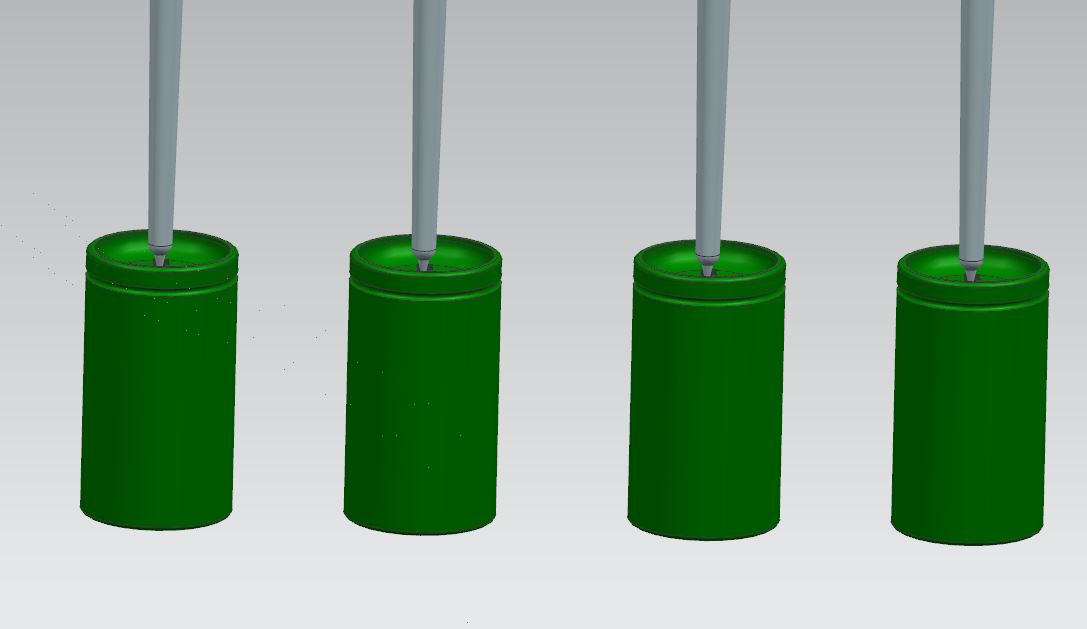
핀 포인트 게이트 사출 성형
핀 핀트 게이트 설계 방법
사출 금형용 핀 포인트 게이트 설계에는 몇 가지 주요 단계가 포함됩니다:
- 위치를 결정합니다: 핀 게이트의 위치는 완성된 부품의 모양에 영향을 미치므로 중요한 고려 사항입니다. 핀 게이트는 성형 후 라벨로 숨길 수 있는 영역이나 부품의 기능에 영향을 미치지 않는 영역에 배치해야 합니다.
- 흐름 특성을 고려합니다: 플라스틱의 흐름 특성은 금형 충진에 영향을 미치므로 핀 게이트를 설계할 때 고려해야 합니다. 핀 게이트의 크기와 모양은 핀 게이트가 러너 플레이트로 쉽게 분할되고 플라스틱이 금형에 고르게 흐르도록 선택하여 쇼트 샷, 에어 트랩 및 싱크 마크와 같은 결함의 위험을 줄여야 합니다.
- 크기를 결정합니다: 핀 게이트의 크기는 성형되는 재료의 유형과 부품의 크기에 따라 결정해야 합니다. 핀 게이트가 작을수록 게이트 마크를 최소화하는 데 도움이 될 수 있지만 플라스틱이 금형에 고르게 흐르지 않아 쇼트 샷 또는 싱크 마크 문제가 발생할 경우 결함 위험이 증가할 수 있습니다. 경험상 지름 0.8~2.5mm가 적당하며, 이는 부품 측면에 따라 다릅니다,
- 게이트 마크 최소화: 핀 게이트의 디자인은 완성된 부품에서 게이트 마크의 크기를 최소화하는 것을 목표로 해야 합니다. 이는 작은 게이트 크기를 선택하고 부품의 외관에 영향을 미치지 않는 영역에 게이트를 배치하여 달성할 수 있습니다.
- 공정 조건을 평가합니다: 온도, 압력, 사이클 시간과 같은 공정 조건을 평가하여 핀 게이트 설계에 적합한지 확인해야 합니다. 성공적인 핀 게이트 설계를 위해서는 적절한 공정 제어가 필수적이며, 일반적으로 사이클 시간은 사이드 게이트나 서브 게이트보다 길어집니다.
핀 포인트 게이트 사출 성형의 장점과 단점
핀 게이트는 다른 게이트 유형에 비해 몇 가지 장점이 있지만 비용 및 복잡성 증가와 같은 몇 가지 단점도 있습니다. 특정 애플리케이션에 대한 핀 게이트의 적합성은 성형되는 재료의 유형, 부품의 크기와 모양, 원하는 품질 수준 등 여러 요인에 따라 달라집니다. 다음과 같은 경험이 있는 금형 설계자 또는 엔지니어와 협력하는 것이 좋습니다. 사출 성형 를 사용하여 특정 애플리케이션에 대한 최적의 게이트 설계를 결정할 수 있습니다.
핀 게이트의 장점:
- 최소 마크: 핀 게이트는 작은 원형 게이트 마크를 생성하여 쉽게 숨기거나 핀 게이트를 부품 표면에 장식 마크로 디자인할 수 있습니다.
- 미관 개선: 핀 게이트 피딩은 스프 루 또는 엣지 게이트와 같은 대형 게이트 유형보다 작은 게이트 마크를 생성하여 완성된 부품의 전체적인 외관을 개선합니다.
- 품질 개선: 핀 게이트 공급 솔루션은 플라스틱이 부품 상단을 통해 금형에 주입되어 균일한 흐름과 충진을 촉진하므로 숏샷, 에어 트랩, 싱크 마크와 같은 결함 위험을 줄이는 데 도움이 됩니다.
- 다양성 증가: 핀 포인트 게이트 솔루션은 다양한 재료에 사용할 수 있어 다양한 애플리케이션에 적합하지만, 일부 매우 부드러운 재료의 경우 게이트가 부품에서 분리되지 않기 때문에 핀 포트 게이트를 사용하는 것이 좋지 않을 수 있습니다(예: TPE 점유율 30A는 핀 포트 게이트를 사용하는 것이 좋지 않습니다).
핀 게이트의 단점:
- 복잡성 증가: 핀 게이트 공급 솔루션 설계는 다른 게이트 유형보다 더 복잡하며 게이트 위치, 게이트 크기 등과 같은 요소를 신중하게 고려해야 합니다.
- 비용 증가: 핀 게이트 공급 솔루션은 일반적으로 더 복잡한 금형 툴링과 더 높은 수준의 공정 제어가 필요하므로 성형 공정의 전체 비용이 증가할 수 있으며, 핀 포인트 게이트는 일반적으로 3판 사출 금형이 필요합니다.
- 제한된 응용 분야: 핀 게이트 공급 솔루션은 다른 게이트보다 공급 거리가 길고 사출 시간 내에 부품을 완전히 채우지 못할 수 있기 때문에 크고 무거운 부품에는 적합하지 않을 수 있습니다. 따라서 성형 부품에 약간의 콜드 웰 문제가 발생할 수 있습니다.
핀 포인트 게이트 사출 성형 를 사용하여 일부 다중 캐비티 몰드를 해결할 수 있습니다. 콜드 러너 몰드 를 사용하여 매우 쉽게 3판 사출 금형때로는 금형 비용을 절약하기 위해 핫 러너를 사용할 필요가없고 하나의 금형에 여러 부품을 만들 필요가없는 경우가 있으며, 많은 유형의 게이트가 있습니다. 사출 성형자세한 내용은 게이트의 사출 금형 설계 페이지로 이동하세요.
금형 비용을 절감하고 부품에 어떤 유형의 금형이 필요한지 모르겠다면 저희에게 연락해 주세요. 우리는 상위 10위 중 하나입니다. 중국의 금형 제조업체.