의미 PMMA 사출 성형
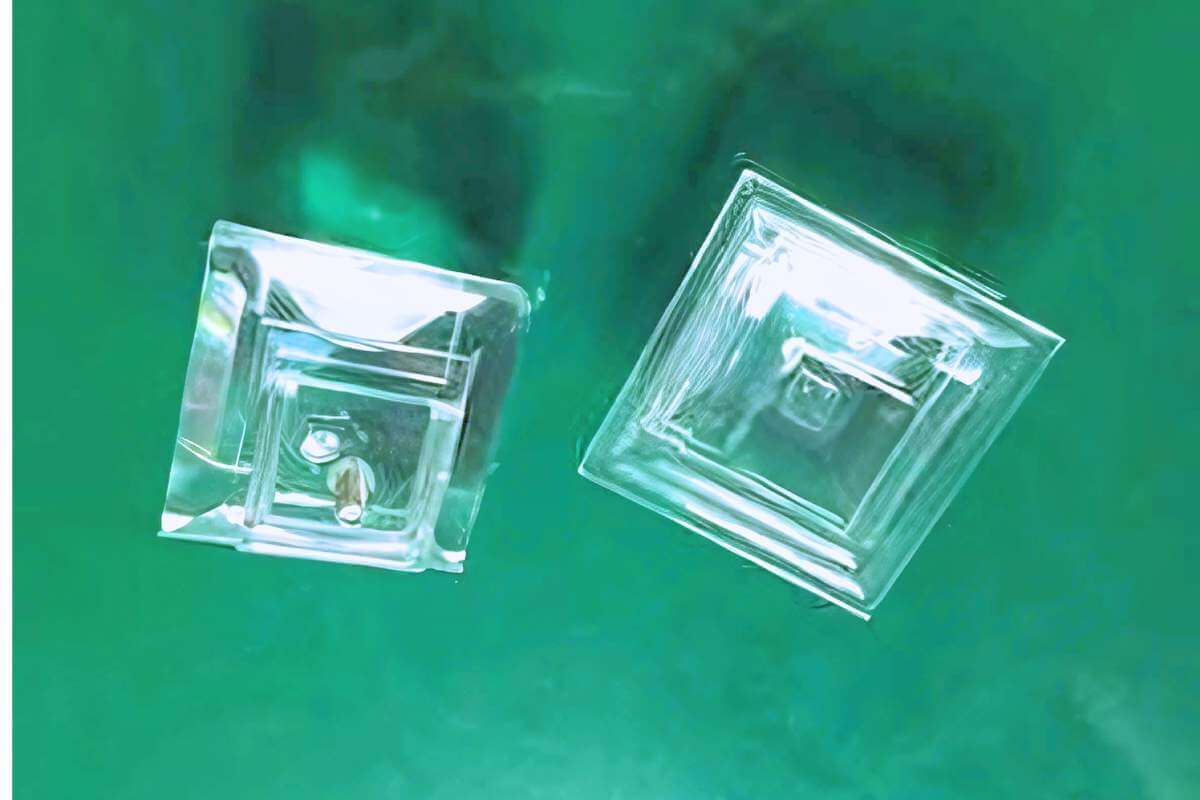
PMMA 사출 성형 기술
PMMA is the highest transperant plastic materils but PMMA is easy to break comparing to PC or ABS, so PMMA’s modification appears one after another such as copolymerization between methyl methacrylate and styrene and butadiene, a blend of PMMA and PC, etc. 372 PMMA is the copolymer of methyl methacrylate and styrene. If you add a small amount of nitrile rubber (about 50%) in the 372 PMMA, it will become 373 PMMA.
사출 성형 PMMA의 유동성은 PS, ABS보다 열악하며 용융 점도는 온도 변화에 다소 민감합니다. 성형 시 주로 사출 온도에 따라 용융 점도가 달라집니다. PMMA는 비정질 폴리머로 용융 온도가 섭씨 200도 이상이고 분해 온도는 섭씨 270도에 달할 수 있습니다.
- 플라스틱 가공
PMMA 플라스틱은 0.3-0.4%의 어느 정도의 수분 흡수율을 가지고 있습니다. 그리고 사출 성형 PMMA moisture must be less than 0.1%. Typically, it is 0.04%. The presence of moisture causes bubbles, gas lines, and low transparency. So it should be dried. Dying temperature is 80–90 degrees Celsius, and drying time is 3 hours or more. In some cases, the utilization of recycled materials can reach 100%. The actual quantity depends on the requirements for quality. Usually, it can reach 30%. You should make sure there is no pollution of recycled materials, or it will influence the transparency and nature of the finished products. - 사출 성형기 선택
사출 성형 PMMA 소재 는 사출 성형기에 대한 특별한 요구 사항이 없습니다. 용융 점도가 높기 때문에 홈이 더 깊어야 하고 노즐 구멍의 직경이 더 커야 합니다. 강도가 더 높은 제품이 필요한 경우 저온 플라스틱을 구현하려면 스크류의 종횡비가 더 큰 것을 사용해야 합니다. 또한 PMMA 성형 수지는 건조 호퍼를 사용하여 재료를 보관해야 합니다. - 몰드 및 게이트 설계
PMMA injection Mold temperature can be 60–80 °C. The diameter of the sprue should match the internal taper. The optimum angle is 5 to 7. If the wall thickness of injecting molding products is 4 mm or more, the angle should be 7, the diameter of the mainstream channel should be 8 to 10 mm, and the overall length of the gate should not exceed 50 mm.
For PMMA injection molding products with a wall thickness less than 4 mm, the diameter of the flow channel should be 6–8 mm. If the PMMA wall thickness is more than 4 mm, the diameter of the flow channel should be 8–12 mm. The depth of the fan-shaped and tab-shaped gates should be 0.7 to 0.9 t (t is the wall thickness of the product), and the diameter of the pin gate should be 0.8 to 2 mm. Injection molding PMMA Products with lower viscosity should choose the smaller size. The common venting hole’s depth is 0.05 to 0.07 mm, its width is 6 mm, the stripping slope is 30′-1, and the and the cavity portions are between 35′-1 and 30.
- 용융 온도
공기 주입 방법을 사용하여 공급업체가 제공한 정보에 따라 섭씨 210도에서 270도 사이의 온도를 측정할 수 있습니다. - 사출 온도
PMMA 사출 성형 재료로 작업할 때 높은 수준의 내부 응력 발생을 피하기 위해 급속 사출을 사용할 수 있습니다. 느리게, 빠르게, 천천히 등 다단계 사출을 사용하는 것이 적합합니다. 두꺼운 부품을 사출할 때는 느린 속도를 사용해야 합니다. - 체류 시간
온도가 섭씨 260도인 경우 체류 시간은 10분 이내입니다. 온도가 섭씨 270도인 경우 체류 시간은 8분 이내입니다.
PMMA 플라스틱 사출 성형의 응용 분야
PMMA 사출 성형 부품을 필요로 하는 산업 분야는 많습니다. 다음은 사출 성형 PMMA 부품을 사용하는 몇 가지 구성 요소입니다:
- 안경 렌즈: PMMA는 뛰어난 광학적 특성으로 인해 안경에 가장 적합한 소재 중 하나입니다. 다른 모든 플라스틱 소재 중 투명도가 가장 높은 PMMA 사출 성형으로 안경에 가장 적합한 소재입니다.
- 플렉시글라스 창문: 플렉시글라스 또는 아크릴 유리라고도 하는 PMMA는 높은 내충격성과 광학적 선명도로 인해 기존 유리창의 대안으로 널리 사용되고 있습니다. 일반적으로 건물, 수족관, 심지어 비행기 창문에도 사용됩니다.
- 휴대폰 케이스: PMMA는 내충격성, 내스크래치성, 광학 선명도가 높아 휴대폰 케이스 제조에 사용됩니다. 또한 가볍고 다양한 모양과 크기로 쉽게 성형할 수 있습니다.
- 컴퓨터 및 전자제품 케이스: 휴대폰 케이스와 마찬가지로 PMMA는 내구성, 내충격성, 광학 선명도 등의 특성으로 인해 컴퓨터 및 전자제품 케이스 제조에 사용됩니다. 또한 가볍고 다양한 모양과 크기로 쉽게 성형할 수 있습니다.
- 차량 앞유리: PMMA는 높은 내충격성과 광학적 선명도로 인해 차량 앞유리 제조에 일반적으로 사용됩니다. 또한 유리보다 가볍기 때문에 연비를 개선할 수 있습니다.
- LED 렌즈: 길거리와 집에서 볼 수 있는 조명의 내부에 있는 작은 렌즈는 PMMA 사출 성형 부품으로 만들어집니다. 이것은 조명 산업에서 매우 인기가 있습니다.
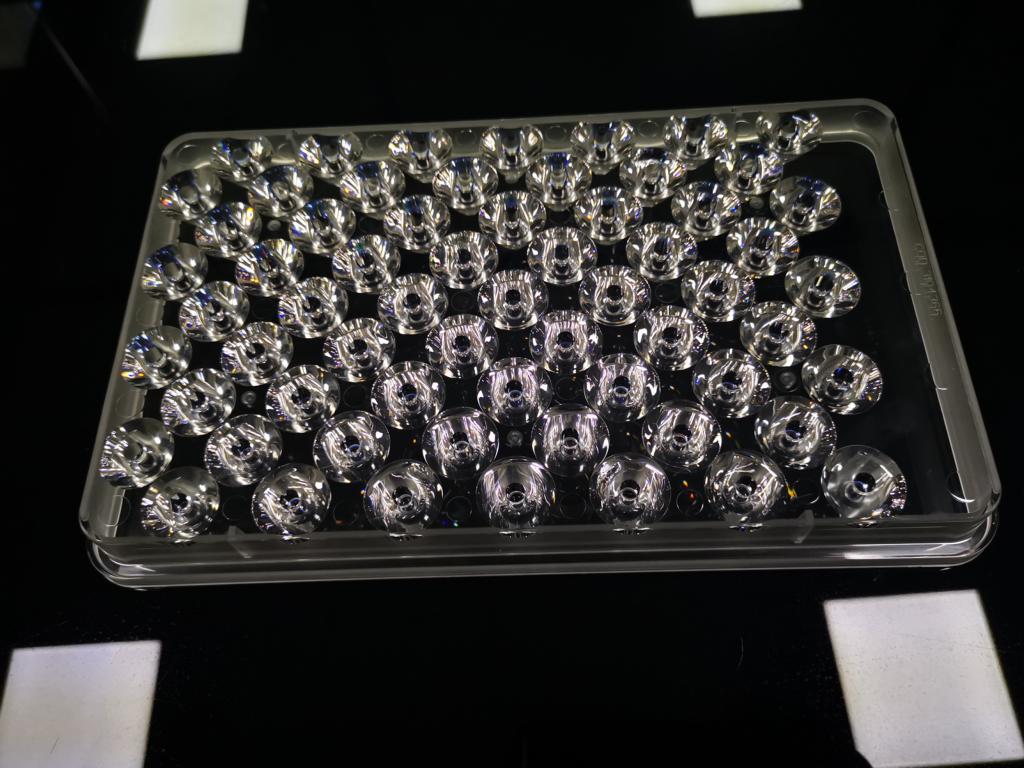
사출 성형 PMMA
PMMA 사출 성형의 장점 (아크릴 사출 몰딩)
1. 스크래치에 강한 제품을 생산합니다.
2. 광이식 제품을 생산합니다.
3. PMMA 사출 성형은 복잡한 디자인을 생산할 수 있습니다.
4. 높은 생산 효율성
5. 색상 유연성 향상
6. 투명 플라스틱 성형의 높은 요구 사항을 위한 특수 소재.
PMMA 소재 아크릴또는 플렉시글라스는 투과율이 최대 92%로 유리보다 높습니다. 이는 곧 투명 아크릴 상자 몰딩은 높은 요구 사항을 충족하는 최고의 옵션 중 하나입니다. 투명 사출 성형 부품유리, 광학 유리, 렌즈, 자동차 조명, 투명 파이프 등과 같은 다양한 소재에 사용됩니다.
아크릴 PMMA 플라스틱 사출 성형의 단점
다른 성형 제조 공정과 마찬가지로 고려해야 할 몇 가지 단점이 있습니다. 다음은 아크릴 PMMA 플라스틱 사출 성형의 몇 가지 단점입니다.
- 생산된 소재는 다음과 같이 생산된 소재에 비해 충격에 대한 저항력이 낮습니다. 금속 사출 성형.
- PMMA 사출 공정으로 생산되는 대부분의 제품은 내열성이 낮습니다(섭씨 약 80도).
- 이 공정에서 생산되는 대부분의 품목은 기계적 강도가 낮기 때문에 적재 용량이 제한됩니다.
- 일부 아크릴 제품은 내화학성이 약해 유기 화합물과 반응하기 쉽습니다.
- PMMA 사출 성형은 특수 사출 금형을 뒤집어야 하므로 초기 툴링 비용이 높습니다. 이는 소량 생산에는 적합하지 않습니다.
- 제한된 디자인 유연성. 이 공정은 단순하고 균일한 모양의 제품을 생산하는 데 가장 적합합니다. 복잡한 디테일이 있는 복잡한 디자인은 아크릴 PMMA 플라스틱 사출 성형으로는 구현하기 어려울 수 있습니다. 이러한 한계는 독특하고 혁신적인 제품을 만들고자 하는 제조업체에게는 큰 단점이 될 수 있습니다.
고품질 PMMA 사출 성형 부품을 만들기 위한 팁.
PMMA 사출 성형 부품을 만드는 것은 다른 사출 성형 부품과 약간 다릅니다. 대부분의 경우 PMMA 성형 부품을 만들 때 고 유리 PMMA 부품을 만들기 때문입니다. 이 경우 특히 일부 두꺼운 벽 PMMA 사출 성형 부품의 경우 몇 가지 특수 장비가 필요합니다. 다음은 고품질 PMMA 사출 성형 부품을 만들기위한 몇 가지 팁입니다.
금형 설계
Since PMMA is a transmission material, any flow marks will be easy to see, and this could be an issue as well. Using moldflow analysis, it will be very important to check where the best gate location is. Once the gate location has been determined, the gate shape is important as well. Mostly, we suggest designing a side gate or fan gate, which will make it easier to fill the cavity and avoid the flow marks.
사출 성형기와 온수 탱크가 사용 중입니다.
벽이 두꺼운 PMMA 사출 성형 부품을 제작하는 경우 플라스틱은 수축률이 있기 때문에 항상 싱크 및 기포 문제가 발생합니다. 벽이 두꺼울수록 수축률이 높아져 냉각 시간이 아무리 길어도 부품 내부에 기포가 발생하고, 냉각 시간이 길어지면 사이클 시간도 늘어나 비용이 증가하게 됩니다.
In that case, a hot water tank can improve these issues. Use 60–80 degree temperature water in the water tank. Once you pick the PMMA injection molding parts from the mold cavity and put them into the hot water tank for 6–12 minutes, you take out the molded parts, so the sink and bubble issues will be greatly improved.
고품질 PMMA 성형 부품을 만드는 것은 쉬운 일이 아닙니다. PMMA 성형 부품이 필요한 프로젝트가 있다면 전문 PMMA 사출 성형 계약업체를 찾는 것이 매우 중요합니다. 이를 통해 프로젝트의 성공 여부를 확인할 수 있습니다.