사출 금형 코어 및 캐비티 인서트란?
플라스틱 사출 금형 코어 및 캐비티 인서트 는 플라스틱 및 금속 부품 제조에 사용되는 금형의 구성 요소입니다.
몰드 코어(때로는 코어 인서트라고 부르는 작은 인서트)는 일반적으로 코어 쪽(이동 가능한 쪽)에 위치한 몰드의 내부 부품입니다. 이는 성형되는 부품의 내부 특징을 만듭니다. 코어는 일반적으로 1.2344, S136 등과 같은 강철로 만들어지며 일반적으로 몰드 플레이트(B 플레이트 또는 포켓 플레이트)에서 제거할 수 있습니다.
사출 금형 캐비티 인서트는 코어 인서트와 동일한 기능을 하지만 픽스 측면에 위치합니다. 성형되는 부품의 외부 모양을 만드는 금형의 외부 부품입니다. 캐비티 인서트는 일반적으로 NAK 80, S136, 1.2344 및 H13과 같은 강철로 만들어지며 일반적으로 금형에서 제거할 수 있습니다.
플라스틱 몰드 코어 및 캐비티 인서트 는 일반적으로 EDM 프로세스를 사용하여 만들어집니다(방전 가공) 및 CNC(컴퓨터 수치 제어) 가공이 이루어집니다. 그런 다음 코어와 캐비티 인서트를 몰드 베이스에 조립하여 완전한 플라스틱 몰드. 그런 다음 플라스틱 사출 금형을 사출 성형 또는 주조 공정에 사용하여 원하는 부품을 생산합니다.
물론 선반 가공, 그라인더 가공, 연마, 와이어 절단, 밀링 등과 같은 플라스틱 금형을 만드는 데는 많은 제조 공정이 있지만 사출 성형을 만드는 데 가장 중요한 제조 공정은 CNC 및 EDM 가공이며, 아래에서는 EDM 및 CNC 가공에 대해 간략하게 설명합니다:
EDM:
- 먼저 3D 모델링 소프트웨어에서 금형 디자인을 만듭니다.
- 그런 다음 작업물(캐비티 및 코어 강재)을 EDM 기계는 전기 방전을 사용하여 전도성 재료(예: 강철 또는 알루미늄)의 표면을 침식하여 원하는 코어 또는 캐비티 인서트 모양을 만드는 기계입니다.
- 그런 다음 완성된 작업물은 요구 사항에 따라 광택을 내거나 텍스처를 입힙니다.

EDM 가공 프로세스
CNC:
- 프로세스는 비슷하지만 방전 가공을 사용하는 대신 CNC 기계는 절삭 공구(엔드밀 또는 드릴 등)를 사용하여 강철 또는 알루미늄 블록에서 재료를 제거하여 원하는 코어 또는 캐비티 인서트 모양을 만듭니다.
- 완성된 공작물은 강도와 내구성을 높이기 위해 열처리되며, 수 프리하든 스틸의 경우 추가 열처리가 필요하지 않고 바로 EDM 가공 공정으로 이동할 수 있습니다.
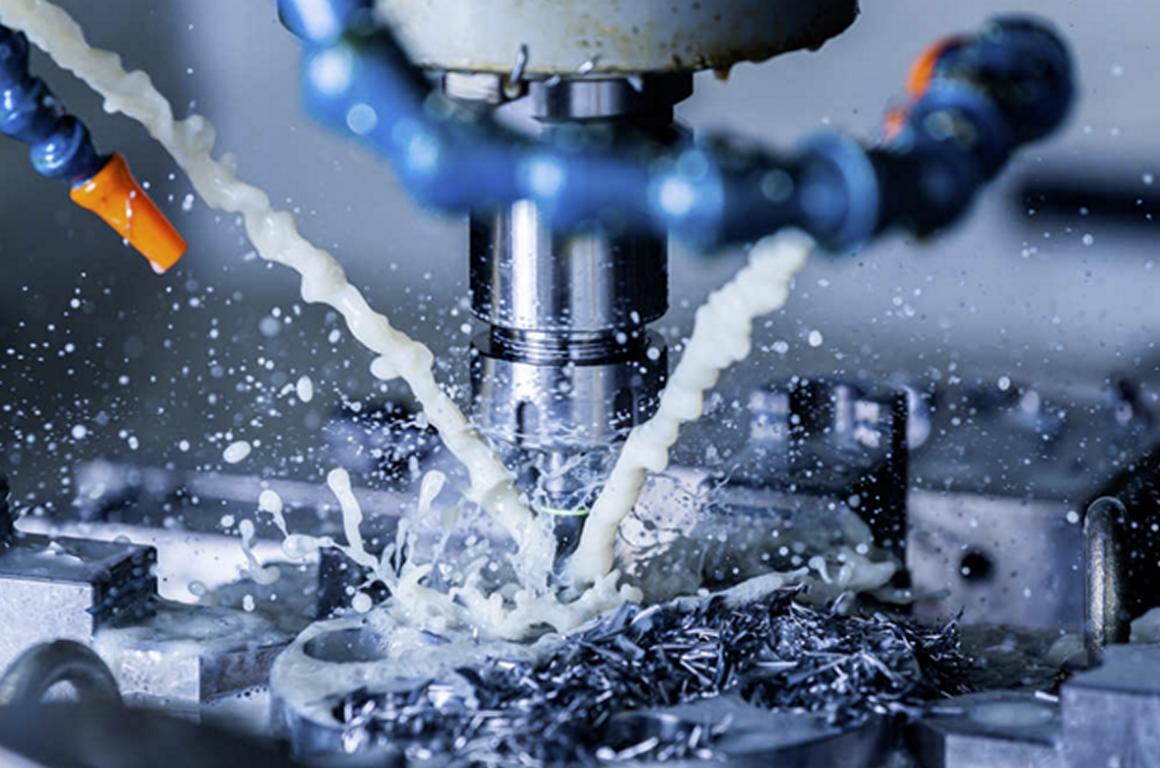
CNC 가공 프로세스
EDM과 CNC는 모두 매우 정밀하고 정확한 부품을 생산할 수 있으며 사출 금형 코어 및 캐비티 인서트 제조에 널리 사용되며, 설명해야 할 중요한 절차 중 하나는 EDM과 CNC 간의 작업 순서이며 일반적으로 CNC 가공이 먼저 시작된 다음 EDM 가공을 사용하여 CNC 가공이 할 수없는 일부 영역 (예 : 일부 모서리, 리브, 보스 등)을 제거합니다.
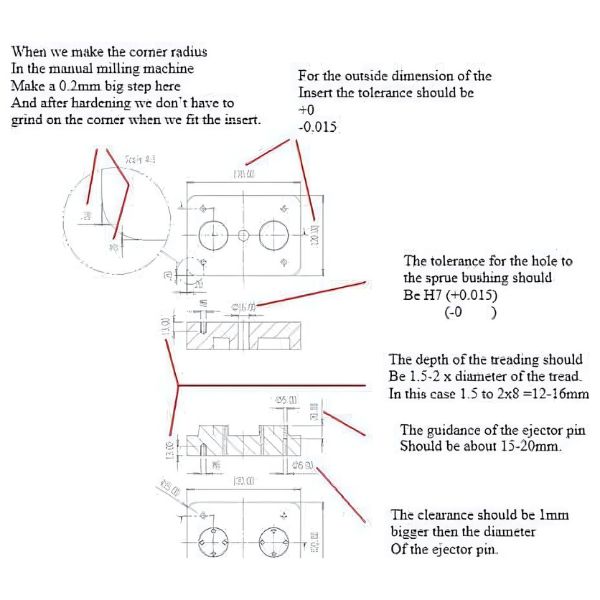
사출 금형 캐비티 및 코어 제조 가이드라인
몰드 코어 및 캐비티 인서트 제조를 위한 몇 가지 지침
제조 시 사출 금형 코어 및 캐비티 인서트 동안 금형 제조인서트 플레이트나 몰드 캐비티 또는 코어의 포켓에 잘 맞도록 약간의 공차를 두고 제조해야 하는 치수가 있습니다.
그리고 금형 캐비티와 코어를 맞출 때 작업 시간을 절약할 수 있습니다. 높은 공차와 우수한 제조 기술은 금형 마스터의 시간을 많이 절약 할 수 있습니다. 다음은 고품질 플라스틱 금형을 만들기 위해주의해야 할 몇 가지 제조 금형 코어 및 캐비티 인서트 지침입니다.
- 수동 밀링 머신에서 모서리 반경을 만들 때 0.2mm 스텝을 만들면 경화 후 인서트를 끼울 때 모서리를 연마할 필요가 없습니다.
- 외부 치수의 경우 플라스틱 사출 곰팡이 캐비티 또는 코어 삽입허용 오차는 +/-0.015mm여야 하며, 이렇게 하면 주머니에 쉽게 끼워지고 매끄럽고 좋은 품질을 얻을 수 있습니다.
- 스프 루 부싱의 구멍 공차는 H7(0/+0.015mm)이어야 합니다.
- 트레딩의 깊이는 트레드의 직경에 1.5-2를 곱한 값이어야 합니다. 이 경우 M8 나사의 경우 트레딩의 깊이는 1.5-2에 8을 곱한 12-16mm가 되어야 합니다.
- 이젝터 핀의 가이드 길이는 15~20mm 정도여야 이젝터 핀이 원활하게 배출되고 수명이 길어집니다.
- 이젝터 핀의 여유 공간은 이젝터 핀의 직경보다 1mm 더 커야 합니다. 몰드에 대한 질문이 있으시면 문의해 주세요.
만들기 사출 금형 캐비티 및 코어 인서트 사출 성형 공장을 운영하고 있고 오래된 인서트를 교체하기 위해 일부 금형 캐비티 및 코어 인서트를 만들어야하거나 캐비티와 코어를 모두 만들고 사출 성형 공장에서 조립하려는 새 금형이있는 경우 전문 플라스틱 금형 제조업체에서 만들어야하는 경우 당사에 연락하여 사출 금형 캐비티 및 코어 인서트 또는 완전히 금형 캐비티 및 코어, 금형베이스 또는 완전히 플라스틱 사출 금형을 만들 수 있습니다.
사출 금형 코어 및 캐비티 플레이트(포켓 플레이트) 제조 지침
사출 금형 제조가 쉬운 일이 아니라는 것을 이미 알고 있으므로이 분야에서 좋은 팀이나 경험이없는 경우 전문 플라스틱 금형 회사를 찾아 지원하는 것이 좋습니다. 성형 공정은 귀하의 편에서 할 수 있지만 금형 아웃소싱을 할 수 있기 때문에 플라스틱 금형을 만드는 것은 사출 성형 공정에 비해 모든 작업자에게 매우 높은 기술력이 필요하고 금형 제조는 사출 성형 서비스보다 수동 작업이 더 필요하며 높은 기술 요구 사항도 필요하며 아래는 A 판 금형의 제조 가이드 라인 중 하나입니다.
플라스틱 금형용 코어 및 캐비티 플레이트를 제조할 때 캐비티 및 코어 인서트 부품 또는 표준 금형 부품이 플레이트 포켓에 원활하게 조립되고 직선 가이드 블록이 금형베이스에 잘 맞도록 약간의 공차를 두고 제조해야 하는 치수가 있으며, 다음은 A 플레이트 제조 시 주의해야 할 몇 가지 핵심 사항입니다.
몰드 베이스의 각 측면에 직선 인터록이 있는 경우(A 및 B 플레이트), 이 치수의 공차는 H7(0/+0.015mm)이 되어야 인터록이 몰드 베이스에서 조립이 용이하면서도 고정밀 가이드 기능을 유지할 수 있습니다.
캐비티 및 코어 인서트의 포켓 치수는 공차 요구 사항 H7(0/+0.015mm)을 따라야 캐비티/코어 인서트가 포켓에 부드럽게 안내되지만 정밀한 치수를 가질 수 있습니다.
로케이팅 핀의 구멍 위치가 중요하며 클램핑 플레이트와 조립되며 치수는 클램핑 플레이트의 관련 구멍과 일치해야하므로 로케이팅 핀의 공차는 ± 0.01mm를 유지해야하며 로케이팅 핀홀은 관련 공차 H7 (0 / + 0.015mm)을 가져야 로케이팅 핀이 쉽게 들어갈 수 있습니다.
금형에 핫 러너 시스템이 제대로 작동하려면 피팅 영역의 허용 오차가 ± 0.01mm여야 합니다(아래 설명을 참조하세요).
오링 트랙 깊이의 경우 허용 오차는 ± 0.05mm, 오링 트랙 직경의 경우 ± 0.05mm입니다.
허용 오차는 ± 0.25mm이며, 이는 금형의 모든 오링에 대해 동일한 요구 사항입니다.
클램핑 플레이트 제조 가이드라인
클램핑 플레이트의 금형 캐비티 쪽을 제조할 때 표준 금형 부품 및 기타 부품이 클램핑 플레이트에 잘 맞도록 약간의 공차로 제어해야 하는 치수가 있습니다.
핀홀 위치 지정의 경우 허용 오차는 H7(0/+0.015mm)이어야 합니다.
로케이팅 링의 구멍 직경, 허용 오차는 ±0.02mm여야 합니다.
핫 러너 매니폴드 지지 인서트의 구멍 직경, 허용 오차는 ±0.05mm여야 합니다.
핫 러너 매니폴드 지지 인서트의 공기 배출 홈 높이 치수는 허용 오차가 ±0.01mm여야 합니다.
스프 루 부싱에 대한 로케이팅 핀의 슬롯, 공차는 0/+0.10mm여야 합니다.
로케이팅 핀의 구멍 위치가 중요합니다. 이것은 핫 러너 매니 폴드 플레이트 또는 A 플레이트와 같은 다른 플레이트에 연결되며, 엄격한 공차 우리는 금형베이스 어셈블리를 매우 잘 확인하고 공차는 ± 0.01mm 여야합니다.
Sincere Tech는 중국 최고의 10 대 금형 제조업체 중 하나이며 중국에서 금형 또는 성형 부품을 만들어야하는 프로젝트가있는 경우 견적 요구 사항을 보내 주시면 금형 가격 또는 금형 및 성형 단가를 모두 보낼 수 있으며 15 일 이내에 첫 번째 샘플을 빠르게 만들어 비즈니스를 지원할 수 있습니다.
당사의 플라스틱 사출 금형 중 80% 이상은 미국과 유럽으로 수출되고 있으며, 고객을 위해 플라스틱 금형을 만들뿐만 아니라 사출 성형 서비스를 제공하는 사출 성형 공장도 보유하고 있습니다.
24시간 내에 가격을 확인하려면 문의하세요.