ミシガン州 は、特に製造業が盛んである。 プラスチック射出成形.このプロセスは、自動車、医療機器、電子機器、包装などの産業における高精度製品の製造に幅広く応用されている。 ミシガン州のプラスチック射出成形会社 は、その信頼性と革新性で世界中の企業から高い評価を得ている。
また、ミシガン州のプラスチック射出成形会社は、ラピッドプロトタイピング、ツーリングから大量生産に至るまで、メーカーの要件に応じてサービスの膨大なリストを提供しています。この記事では、ミシガン州のプラスチック射出成形会社のいくつかを紹介します。 ミシガン州の大手プラスチック射出成形メーカー 地域と提供するサービス
1.ハイテク金型&エンジニアリング

ハイテク金型&エンジニアリング は、家族経営の2代目メーカーです。 プラスチック射出成形金型 ミシガン州メンドンに位置し、創業以来、この業界に貢献している。 1994.プラスチック金型のトップメーカーとして、同社は創造性、効率性、高品質の製品に重点を置いています。
射出成形における統合サービス
Hi-Tech Mold & Engineeringは、自動車、航空宇宙、医療機器、電気自動車業界を含む様々な業界に様々な射出成形ソリューションを提供しています。彼らの革新的な技術と30年以上の経験により、顧客の製品開発と製造の目標を達成するための効率的なサービスを提供することができます。
同社の射出成形サービスの範囲は以下を含む:
- 射出圧縮成形: インジェクションとコンプレッションの両方の長所を生かし、複雑なデザインや複雑な形状に対応します。
- ガスアシストモールディング: 部品の材料量と重量を減らし、同時に強度と耐荷重性を高めることを目的としたプロセス開発戦略。
- インサート成形: プラスチック部品の剛性などを向上させるために、ワンショットで金属などを組み込む工程。
- 低圧成形: 薄くて複雑な部品で、加工段階で高圧をかけるべきでないものに適用される。
- スマートフォイル成形: フレキシブルフィルムを使用することで、材料の使用量を抑えながら、薄くて複雑な形状の部品を作ることができる。
精密製造先端技術センター。
同社は、効率と品質を実現する最新鋭の自動化システムを採用している。ここでは、コアバック、コイニング、射出圧縮成形という最高の技術で、金型の試作と検証を行っています。このような革新的な条件により、私たちは業界最高の要件と顧客の期待に体系的に対応することができます。
専門知識とグローバル・リーチ
Hi-Tech Mold & Engineeringは、最も複雑なプログラムであっても優れたプロフェッショナリズムで提供できる企業としての地位を確立しています。小さなツールパッケージから大規模な車両プラットフォームまで、製品開発の全段階に完全なソリューションを提供しています。グローバルな提携を達成することで、完全なサービス、経済的なソリューション、効率的なプロジェクトの実行を顧客に提供することができます。
認証と品質保証
品質に対する同社のコミットメントは、IATF16949、AS9100D、および以下を含む業界認証によって裏付けられています。 ISO 9001:2015 は、効率と製品品質の着実な向上へのコミットメントを反映しています。新製品を設計・製造する場合でも、既存の製品を増産する場合でも、Hi-Tech Mold & Engineeringが必要です。
ミシガン州のプラスチック射出成形会社をお探しですか?
2.アイアンウッドプラスチックス
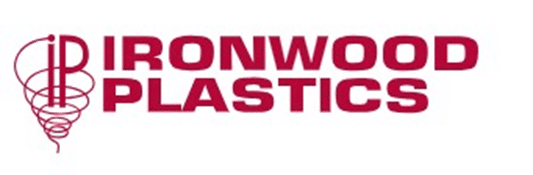
アイアンウッド・プラスチックス で始まった。 1979 ミシガン州アイアンウッドとウィスコンシン州ツーリバーズの2工場からなる。同社は、ミシガン州アイアンウッドとウィスコンシン州ツーリバーズにある2つの工場で構成されています。射出成形のマーケットリーダーとして、同社の使命は、最先端のエンジニアリングと製造技術を通じて最高品質の顧客満足を継続的に提供するという目標を見失うことはない。
能力と専門知識
アイアンウッドプラスチックスは様々なニーズに対応するため、幅広いカスタム射出成形ソリューションを開発した。彼らのエンジニアリング担当者は、業界の最新技術と基準を活用し、単純なものから複雑な成形作業まで正確に処理することができます。お客様のプロジェクトが少量生産であれ、大量生産であれ、アイアンウッドプラスチックスはお客様の目標を達成するための経験を持っています。
最先端設備への投資と継続的なスタッフ教育により、以下を含む幅広い成形技術に対応している:
- カスタム射出成形:自動車、医療機器、消費者製品、その他多くの業界向けに精密成形品を提供する。
- 二次サービス: 同社は、最終製品の厳しい品質を保証するために、組立、加飾、テストなどの二次的な作業を充実させている。
- 高度なマテリアルハンドリング: 高性能ポリマーだけでなく、一般的な熱可塑性プラスチックの加工も行っているため、特定の製品に最適なものを常に見つけることができる。
- 複雑な金型設計: 手の込んだ成形技術が必要な難しい作品に対応するため。
アイアンウッド・プラスチックスは企業として、経験とプロ意識に裏打ちされた専門的なエンジニアリングが最大の強みであると認識しています。アイアンウッド・プラスチックスは、顧客との良好な関係を築き、顧客の技術的要求を満たすサービスを確実に提供するとともに、持続可能なビジネス価値の創造に貢献しています。
サービスにおける理想的な位置づけ
- ミシガン州アイアンウッドが本社である。
1235 ウォール・ストリート, アイアンウッド, MI 49938
電話: 906.932.5025
- ウィスコンシン州トゥー・リバーズ事業部
54241 ウィスコンシン州ツーリバーズ私書箱2800号
電話: 920.793.3060
このような場所だからこそ、私たちは迅速な配送サービスや無料のカスタマーケアサービスで、北米をはじめとする世界中の顧客にアプローチすることができるのだ。
品質認証とコンプライアンス
同社はISO 9001およびIATF 16949:2016の認証を取得しており、社内の品質管理基準を維持していることを証明している。また、MAPP Manufacturing Alliance、ITARなどの規格も取り入れている。
農業および食品加工機器ソリューションを世界的に提供するCTBグループの一員として、当社は専門知識を拡大し、最新の製造技術に対応できる立場にあります。
アイアンウッドプラスチックスは、射出成形機という枠を超え、革新的なエンジニアリングソリューションと優れた精度を提供する戦略的協力者です。新製品の設計や既存製品の強化が必要な場合、必要なリソースと経験をすべて備えています。
ミシガン州のプラスチック射出成形会社をお探しですか? 製品組立サービス射出成形部品の特別な材料は、あなたの参考のためにそれらを考えるかもしれません、またはあなたのプロジェクトを引用するためにそれらをcotnact。
3.MMI エンジニアド・ソリューション

MMI エンジニアド・ソリューションズ は、低コストで高性能な軽量ソリューションの設計・製造を行うOEM用途のワンストップ・ソリューション・プロバイダーです。先進的な複合材料とエンジニアリング樹脂に焦点を当て、自動車、航空宇宙、マテリアルハンドリング市場において、高性能アプリケーション向けの優れたコンポーネントとアセンブリを提供しています。
エンジニアリング、金型製作、製造が主な専門分野であり、技術の進歩の助けを借りて最高のデザインを引き出すために、エンジニアや製造業者が最も困難な問題を解決するのに役立つ製品を提供しています。射出成形、ブロー成形、先端材料の製品への活用など、同社は生産のあらゆる段階で最高のパフォーマンスを提供します。
コア・サービス
- 射出成形とブロー成形: 正確な熱可塑性プラスチック部品、パーツ、サブアセンブリ。
- マテリアルハンドリング・ソリューション マテリアルハンドリング用途の新時代の複合樹脂およびエンジニアリング樹脂に特化。
- 工具: 高度な金型を内製・短納期で設計・製造できるツールセンター。
- デザインサービス: 当社の設計チームは3Dソフトウェア、Moldflow、FEA解析を駆使し、より創造的なソリューションを提供することができます。
グローバルなプレゼンスと拠点
- 本社米国ミシガン州サライン
- その他の拠点ミシガン州トロイ、ミシガン州ウォーレン、メキシコ・モンテレイ
その他の能力
- 社内工具: リードタイムを短縮し、競争力を高める。
- デザインサポート: 効果的な問題解決ツールとしてのCAD、Moldflow、FEAツール。
- APQPプロセス: DFMEA/PFMEA、管理計画、プロジェクトのタイミングに関する知識。
高性能ソリューションの開発と提供における成功の歴史に基づき、MMI Engineered Solutionsは、重要な設計および製造の問題に対処するために必要なツールとサポートを提供し、OEM市場のリーダーであり続けています。
プラスチックをお探しなら 近くの射出成形会社 射出成形金型製造、ブロー射出成形、設計サービスを提供するミシガン州の会社は、あなたの参考のためにそれらを考えるかもしれません、またはあなたのプロジェクトの見積もりを依頼する。
4.ジムディ・プラスティック

ジムディ・プラスティック は、高度なプラスチック射出成形を提供する業界のリーダーです。 インサート成形 サービスを提供する。設立は 1997ミシガン州アレンデールにある。中核事業は、精密射出成形部品とアセンブリーを世界中の幅広い産業に提供することである。これらの理念により、自動車、消費財、医療機器、その他多くの業界の顧客と協力し、グローバル市場にビジネス・ソリューションを提供している。
コア能力
- 射出成形: 110トンから1,100トンまでの16台のプレス機があり、少量生産から大量生産まで可能です。さらに、さまざまな種類の材料を使用し、インサート成形やオーバーモールド成形などの特殊なサービスも提供しています。
- 工具: 設計からトライアウトまで、お客様のツーリングに全責任を負います。また、国内外の金型工場と緊密な協力関係を築いており、高品質なアルミ金型や試作品を提供することが可能です。
- エンジニアリング 同社の専門エンジニアは、顧客と一緒になって、使用する適切な材料と最も適切な射出成形技術を特定する。さらに、プロトタイピングから始まり、エンド・オブ・ライフ・サービスまで、さまざまなサービスで顧客をサポートしている。
- 組み立てと二次加工: 組立ライン技術には、自動組立ステーションと手動組立ステーションのほか、音波溶接、シルクスクリーン、パッド印刷、レーザーエッチングなどがある。
各社の品質への取り組み
Jimdiプラスチックの経営陣は、品質とは目的意識を持ったアプローチと努力の結果であると認識している。彼らは高品質の部品で顧客を満足させるためにISO認証基準を厳守している。
Jimdiプラスチックを選ぶ理由
- 広いプレス範囲: 16台の印刷機を統合することで、さまざまな生産量に比較的容易に対応できるようになった。
- 革新的なソリューション: 先進的な成形技術や素材を駆使することで、お客様のニーズにお応えしています。
- エンド・ツー・エンドのサポート: 製品の設計、エンジニアリングから製品の組み立て、二次加工に至るまで、完全な製造サービスを提供している。
- グローバルなリーチ 同社は、顧客が国際市場で目標を達成できるよう、費用対効果の高い射出成形部品を供給している。
をお探しなら 近くのプラスチック射出成形会社 金型製造、インサート成形、製品組立、エンジニアリング・サービスを提供するミシガン州の同社を参考にしたり、プロジェクトの見積りを依頼することもできる。
5.PTI エンジニアド・プラスチックス

PTI エンジニアド・プラスチックス社 は、米国ミシガン州の大手プラスチック射出成形メーカーであり、プラスチックおよびプラスチック部品、アセンブリの製造業者です。30年以上にわたって事業を展開し、PTIは医療、防衛/航空宇宙、その他の分野など、さまざまな業界に対応してきました。その正確さと創造性の結果、PTIは今日、高品質のプラスチック製品を求める企業にとって貴重なサプライヤーとなっています。
コア能力
- プラスチック射出成形: PTIは、単一の試作品から大規模な生産まで、サービスを提供します。試作品や生産目的、少量生産または受託製造のために、PTIは最高水準の高品質部品を生産します。
- 社内工具: 品質は工具から始まります。PTIは30年以上の金型製作の経験があり、ツールメーカーに正確な金型を製作するために最先端の技術を採用しています。この社内能力は、短いリードタイムと、開発から完成まで、お客様の部品製造に使用される高品質の金型を提供する能力に直結します。
- プロトタイピング: プロトタイプ射出成形サービスを通じて、PTIからテストおよび設計検証用の部品を入手できます。少量部品の応用シナリオの一部では、同じプロトタイプ金型が最初の生産ラインとして機能し、部品を市場に投入するまでの時間を短縮し、コストを下げることができます。
- クリーンルーム成形: 医療や航空宇宙産業におけるクリーン製造の需要が増加しているため、PTIは、その生産能力を増強している。 クラス8クリーンルーム 以上のスペース 10,000フィート。 この拡張により、PTIは汚染のない部品を生産する能力を向上させ、ISO 13485規格に準拠する。
- 工業デザイン: PTI工業デザイングループは、製造可能な製品アイデアを開発するために、お客様と直接協力します。エンジニアや金型のスペシャリストとの直接のやり取りにより、プラスチック成形特有の試行錯誤のプロセスを減らし、設計から製造への移行を加速します。
主要市場
- メディカルだ: PTIはISO 13485に準拠しており、精度と性能が要求される機器に使用される医療グレードの部品を提供しています。手術器具、診断装置、インプラントのいずれにおいても、PTIはすべての部品が規制要件に適合していることを保証します。
- 防衛/航空宇宙 PTIは、防衛および航空宇宙市場の需要に応える特殊射出成形品を提供しています。クリーンルーム成形と高度な材料ハンドリングにより、最も困難な技術要件を満たすことができます。
- 消費者向け製品: PTIは、一般的に使用される堅牢で価格競争力のある成形部品を提供することで、消費者製品市場に貢献しています。
PTI Engineered Plasticsを選ぶ理由
- 専門知識と経験: PTIは30年以上の経験を有しており、様々な業界で困難な成形プロジェクトを請け負う際に、技術的な専門知識を提供することができます。
- 高度なクリーンルームと成形能力: 同社はクラス8クリーンルームの成形スペースを拡大し、医療用および航空宇宙用ネオプレンの厳しい要件を満たすために必要な柔軟性を備えている。
- エンド・ツー・エンド・サポート:コンセプトと設計、金型、生産会社として、PTIは品質と短納期を保証するワンストップソリューションを提供します。
ミシガン州でプラスチック射出成形会社をお探しなら、医療用射出成形、クレーンルーム・ショップ、プロトタイピング製造、工業用ダイサイン・サービスを提供している会社をご検討ください。
6.Mdbio

として プラスチック金型会社 Medbio LLCは医療機器業界で高い評価を得ており、金型の正確なソリューション、革新性、精度に特化しています。Medbioの金型メーカーは、近代的なツールルームを利用することができ、顧客の特定の要件に最適なSPIクラスの生産金型を開発することができる専門の金型設計者を雇用しています。
コア能力
高度な金型設計とエンジニアリング
メドバイオは、市場で最も先進的な金型設計および流動解析ソフトウェアを使用して金型を設計することができます。経験豊富なエンジニアのチームは、金型のリバースエンジニアリングと3Dパーツモデリングを取り入れ、成形性と金型の完全性をパーツ性能とともに向上させます。これにより、開発されるすべてのツールは、最高の製造プロセスと最高品質の製品を保証します。
金型機能アニメーション
メドバイオでは、最新のCADソフトを使用した金型機能のアニメーションビデオを用意しています。これらのアニメーションは、金型の開閉、サイドアクション、多段射出、共射出成形などの様々な動作を描写しています。この動画は、お客様が詳細なデザインレビューを行う際に役立つだけでなく、成形チームを作るプロセスをより簡単にします。
高精度成形プレス
メドバイオでは高速マシニングセンターと立形マシニングセンターを使用し、金型製作の細部にまでこだわっている。その機械には次のようなものがある:
- ミルトロニクスのVM20立形マシニングセンタは、より微細な加工に適しています。
- 高速・高精度のマシニングセンター用ローダ。
- 高精度ダイシンカー用金型 三菱 EX22
- ワイヤーカットと深穴加工の精度を誇るソディックワイヤーマシン
インハウス・ツーリング・ソリューション
金型設計から金型製作に至るまで、メドバイオは生産時間と品質を向上させる自社製金型をお客様に提供しています。精密工具に重点を置いているおかげで、非常に詳細なプロジェクトをより迅速かつ効率的に実施することを保証することができます。
見習いプログラム:
メドバイオは、金型製造のプロフェッショナルを育成するため、金型製造技能実習制度を設けています。 米国労働省およびカラマズー・バレー・コミュニティ・カレッジ.このプログラムは、講義と実習を融合させ、医療機器ツーリングで必要とされるテクニカルスキルを習得することを目的としている。
対象業界
医療機器産業:
医療用精密金型の製造に特化したメドバイオは、医療業界における規制や品質に対する高い要求を満たすことが、このようなビジネスにとって重要であることを知っている。メドバイオは、これらの重要な医療機器の品質と性能を保証する金型ソリューションを提供しています。
消費者向け製品:
メドバイオはまた、消費者製品向けの金型ソリューションも提供しており、顧客に合理的な金型ソリューションを提供している。メドバイオのサービスにより、顧客は競争の激しい消費者市場で期待される生産ニーズと期待を達成することができる。
メドビオを選ぶ理由
- エキスパート・デザインとエンジニアリング: メドバイオは、金型設計における豊富な経験と高度な技術を駆使して、医療機器やその他の消費者向け製品向けに正確で高品質な金型ソリューションを提供している。
- 最先端の製造: メドバイオは、お客様の製品に最適な金型を製造するため、業界標準の高速加工精度を備えた最新鋭の金型加工機を保有しています。
- 革新的なアプローチ: 同社は、モデリングから金型機能アニメーションに至るまで、すべてにおいて最先端技術を採用しており、どんなに複雑なプロジェクトであっても、唯一無二のソリューションの提供を保証している。
- 品質へのこだわり: メドバイオは品質に関するISO認証を取得しており、すべてのプロジェクトを正確に提供することに全力を注いでいる。
メドビオへのお問い合わせ
本社
5346 36th Street Southeast, Grand Rapids, Michigan 49512
電話番号電話番号:616 245 0214|ファックス番号:616 245 0244
クリントン・タウンシップ事務所
電話:(586) 954-2553
オーチャードパーク事務所
電話: (716) 662-8550
ウェブサイト:www.medbiollc.com
ミシガン州で医療用射出成形、専門的な金型設計、エンジニアリングサービスを提供するプラスチック射出成形会社をお探しなら、彼らのことを考え、あなたのプロジェクトの見積もりを依頼することができます。
7.ウェストフォール・テクニック社

ウェストフォール・テクニック社 は、優れたツールと高品質のカスタム製品を提供するプラスチック射出成形のトップクラスの業界です。アリゾナ州テンピを拠点とするウェストフォール・テクニックは、航空宇宙、医療、自動車、消費者製品、電子機器、工業製品業界など、さまざまな業界に膨大な顧客を持つ。同社は環境に配慮した企業であり、射出成形の分野で精度、スピード、革新的なソリューションを必要とするメーカーにとって、頼りになるサプライヤーである。
能力
カスタム射出成形
ウェストフォール・テクニックは、以下のようなさまざまな成形プロセスを通じて、高精度で精度の高い部品を製造するエキスパートです。 マイクロ成形とマルチショット射出成形.同社は、顧客が最高の仕様を満たす部品を入手できるよう、信頼性の高い生産能力を提供することで名声を確立してきた。
アドバンスド・ツーリング・ソリューション
さらに、金型設計と金型製作技術により、Westfall Technikはすべての金型が最高水準で製作されることを保証しています。同社のエンジニアリング部門は、最新の CAD技術と3Dモデリング その結果、市場投入までの時間が短縮され、全体的な生産コストも削減される。
マイクロ成形の専門知識
ウェストフォール・テクニックは、比較的小さく複雑なマイクロモールドを使った部品製造能力で知られている。
対象業界
- 自動車
- 医療機器
- 消費者製品
- エレクトロニクス
- 航空宇宙
ウェストフォール・テクニックを選ぶ理由
- 総合的なサービス: ウェストフォール・テクニックは、射出成形の要求に従って、設計、金型製作から最終組立まで、完全なソリューションを提供します。
- 先進技術: さらに同社は、金型製作から最終製品の流通に至るまで、正確さと品質を確保するために最先端の技術を導入している。
- サステナビリティへのコミットメント ウェストフォール・テクニックは組織として、生産と流通における環境への影響を最小限に抑えることを目標に掲げている。
- 経験豊富なチーム: 同社には、どんな複雑な成形も克服できる熟練したエンジニアとデザイナーのチームがいる。
連絡先
所在地
9280 S. Kyrene Rd, Suite 106
テンピ、アリゾナ州85284
電話番号+1 (702) 829-8681
Eメール:solutions@westfalltechnik.com
営業時間
月~金:午前8:00~午後6:00
ミシガン州にあるプラスチック射出成形会社をお探しですか? 二重射出成形また、マイクロ射出成形サービスも提供している。
8.ラックス・エンタープライズ
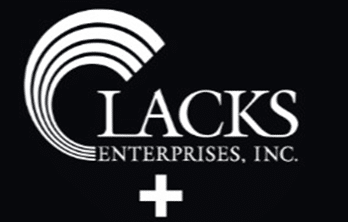
ラックス・エンタープライズ はフィニッシュ・デコレーション業界のトップランナーである。 60年.それは、デザイナーが自動車の内外装の部品を構想する方法を変えた。ラックスの使命は、革新的で完璧、かつ持続可能なソリューションを提供することである。同社の優れた製品は Tessera® 3DテクスチャーとSpinelle™金属仕上げ 設計者は、自動車設計の幅広い分野で柔軟性を開発することができます。
コア能力
インテリア
ラックスは新しいリアルメタルとクロームシリーズを発表した。同社はインテリア・トリム用にほぼ無限のテクスチャーとカラーを提供する。同社はまた、トリムレベルでの差別化を図り、自動車メーカーが自動車のインテリアの外観を向上させるのを支援する。
エクステリアの装飾
単なる装飾ではなく、Lacks社のエクステリア装飾トリムシステムは自動車ビジネスに革新をもたらします。グリルからアップリケに至るまで、同社の製品は自動車の魅力を高めると同時に、エアロダイナミクスなどの機能的側面に対するソリューションを提供する。
軽量ホイールソリューション:
Lacks社は軽量ホイール・アセンブリと部品を供給し、自動車設計者が可能性を再想像するのを支援している。同社のホイール技術は、自動車の性能を向上させるだけでなく、軽量化による燃費向上にも利用されている。
炭素繊維技術:
ラックス カーボンファイバー™ホイール は、高い性能と設計の自由度を提供している。同社の製品は主に自動車産業で使用されており、軽量でありながら強度が高いという特性を持っている。
近年のイノベーションとマーケットリーダー
- フォージライン・モータースポーツ買収 ラックスによるフォージライン・モータースポーツの買収は、ホイール性能と製造における新世代の幕開けである。この買収により、ラックスは高性能ホイールのマーケットリーダーとしての地位を固めることができる。
- ダッジ用高性能ホイール: ラックスは ダッジ 世界最速の市販車に搭載するために カーボンファイバーを欠く ホイールは、精密に設計された高性能自動車部品の最高峰であることを証明する。
- ルーシッド・モーターズによる電気自動車の設計: ラックスは、ルシッドのホイールソリューションに貢献した。 フラッグシップEV、ルーシッド・エア、 メルセデスやBMWなどの自動車大手に真っ向から挑む。
グローバル・リーチ
ラックスは世界規模で事業を展開し、主要な自動車市場に拠点を置いている。
所在地
本社米国ミシガン州グランドラピッズ
ヨーロッパを欠くドイツ、ミュンヘン
ラックス・ジャパン東京、日本
韓国を欠く韓国・ソウル
ラックス イギリスイギリス、オックスフォードシャー
ラックス・エンタープライズを選ぶ理由
- イノベーションだ: ラックスは60年以上にわたって事業を展開し、現在も自動車装飾とパフォーマンス業界に革新をもたらし続けている。
- カスタマイズ: 3Dテクスチャーやカスタム仕上げを施しながら、ラックスは他社にはないデザインの柔軟性を顧客に提供している。
- グローバルなプレゼンス ラックスは多くの国で事業を展開しているため、グローバルな顧客と仕事をすることができ、同時に特定の国の市場とも関連性を保つことができる。
ミシガン州で炭素繊維技術や電気自動車設計サービスを提供するプラスチック射出成形会社をお探しなら、彼らのことを考え、あなたのプロジェクトの見積もりを依頼することができます。
9.ADACオートモーティブ
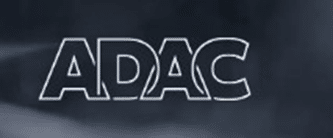
ADACオートモーティブ は、世界最高峰の自動車設計、エンジニアリング、製造ソリューション企業です。ADACオートモーティブは、アイデアの発想から最終製品に至るまで、ワンストップ・ショップ方式で最高のサービスを提供しています。 品質、創造性、エコフレンドリー.
能力
デザインとエンジニアリング:
ADACの専門デザイナーとエンジニアは、持続可能で精密に設計された製品をお届けするために、最新のスキャニング技術と計測技術を採用しています。コンセプト・デザインと製品開発において、ADACは最終製品に詳細かつ徹底した設計プロセスを保証します。
積層造形とラピッドプロトタイピング:
ラピッドプロトタイピングサービスを選択することで、少量生産や何度も修正する機会を作り、高額な金型費用を回避することができます。アディティブ・マニュファクチャリング分野におけるADACの専門知識は、製品開発サイクルを押し進め、デザインに命を吹き込む、高速でコスト効率の高いツールの提供に役立っています。
射出成形:
ADACは現在、以下のものを所有している。 射出成形プレス80台の間にある。 240トンと1200トン、 の射出成形能力は、あらゆる問題を解決することができる。同社の射出成形能力は、製造される部品の形状やサイズに関して精度の高い製品の大量生産に役立っている。
カスタマイズと仕上げ:
塗装およびカスタム仕上げサービスは、塗装済みまたはお客様のご要望に応じて提供することができ、ADACの自動車部品に優れた美的魅力と触感を与えます。
エレクトロニクスの統合:
エレクトロニクスの統合は、センサー、アクチュエーター、照明などのスマート技術を採用するADACのエンジニアリング・チームの強みである。
品質管理:
ADACで開発されるほとんどの製品の品質管理は、生産工程全体を通して高品質のアウトプットを生み出すために、ISO規格に準拠して規制されています。これは、品質を保証するための最先端の計測ツールやさまざまな検査手順によって裏付けられています。
対象業界
- 自動車
- コンシューマー・エレクトロニクス
- 航空宇宙
ADACオートモーティブを選ぶ理由
エンド・ツー・エンドのソリューション
ADACは、最初のアイデアから完成品に至るまで、設計、製造、エレクトロニクス統合のフルターンキーサービスを提供しています。このスムーズなプロセスにより、自動車産業、特に複雑な部品において、製品をより早く市場に投入することが可能になります。
先進技術:
アディティブ・マニュファクチャリング(積層造形)、ハイテク成形装置、エレクトロニクス・インテグレーション(電子機器の統合)の使用を通じて、ADACはその製品が先進的であるだけでなく、最新の技術要件に対応した機能的なものであることを保証している。
サステナビリティへのコミットメント
ADACは、素材の調達から製品に至るまで、生産工程のあらゆる面で持続可能性を重視している。
品質保証:
高品質はADACの最大の関心事であり、高品質の製品を提供することを目指し、同社は厳格な品質保証に従い、包括的なテストと検証結果を提供しています。
カスタマイズとプロトタイピング:
ADACは、ユニークな製品の製造と、短時間で製品の細部を微調整できるラピッド・プロトタイプ・モデルの製作に力を入れている。
ADACオートモーティブへのお問い合わせ
本社 5690 Eagle Dr. SE, グランドラピッズ, ミシガン 49512
電話:(616) 957-0520
ミシガン州で、自動車用射出成形、航空宇宙用射出成形サービスを提供するプラスチック射出成形会社をお探しなら、それらの会社について考え、あなたのプロジェクトの見積もりを依頼することができます。
10.ウェスト・ミシガン・プラスチックス
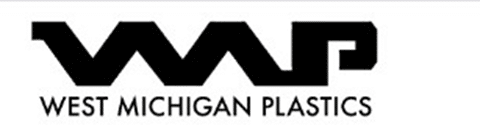
ウェスト・ミシガン・プラスチックスプラスチック射出成形を扱う。 1986.同社は、自動車、医療、政府、建設などさまざまな業界向けの精密プラスチック製品の受注生産に重点を置いている。革新的で品質と効率を重視する企業として、顧客と協力し、誰にとっても最良の製品を提供している。
コア能力
高品質の射出成形品
ウェストミシガン・プラスチックスは、最高の成形品を提供することを誇りにしている。同社のチームは顧客と一体となって、製品に最適なデザインを実現し、適切な材料を決定し、最高水準に合った正確な金型を作成する。彼らが製造する各製品は、市場にリリースされる前に厳格な品質保証プロセスを受けます。
信頼できる配達
前述のように、自動化されたワークセルを使用することで、同社のオペレーションは連続的であり、注文を迅速に納品し、通常とJITの両方の要件を満たすことができる。私たちのミッション・ステートメントに基づき、顧客の生産スケジュールに合わせて迅速かつ信頼性の高い納品を行っています。
対象業界
私たちは、以下のような幅広い業界にサービスを提供しています:
自動車:
当社の製品には、特殊プラスチック部品、内装トリム、性能を向上させ車両重量を軽減するエンジニアリングプラスチック部品などがある。
メディカルだ:
私たちが提供する医療グレードの射出成形は、非常に正確で、すべての適切な業界標準を遵守しています。当社の重点分野は、医療機器、診断機器、およびヘルスケア産業におけるその他の関連用途の部品の製造です。
建設:
建設業界のニーズに応える高強度・耐摩耗性プラスチックや、建材・建設機械用製品を生産している。
場所と連絡先
ウェスト・ミシガン・プラスチックス社
5745 W. 143rd Avenue
ホランド, MI 49423
電話:(616) 394-9269
ファックス:(616) 394-5240
Eメール:info@wmiplastics.com
プラスチックをお探しなら 射出成形 ミシガン州にある、近くの会社 自動車用射出成形積層造形やプロトタイピングのサービスを検討し、あなたのプロジェクトの見積もりに反映させることができる。
結論
ミシガン州 は、経験豊富なプラスチック射出成形会社の豊富なプールを有し、彼らは、特に自動車、医療、電子部門の多くのニーズに応えるために、さまざまなサービスや製品を提供しています。これらの企業は、その正確性、創造性、顧客のニーズを満たす能力でよく知られています。射出成形サービスを必要とする企業にとって、これらの企業はミシガン州の企業に優れたサービスを提供することができます。
しかし、米国外、特に中国での解決策を模索している人たちにとっては、そうではない、 Sincere Tech は、リーズナブルな価格で成形サービスの完全な範囲を提供する信頼できるパートナーです。Sincere Techは、数十年前から事業を展開しており、高品質の製品を顧客に提供しているため、それはあなたが中国で製造ソリューションをソースに役立つことができます。あなたは彼らの製品や彼らはあなたのビジネスを支援することができます方法についての詳細を理解するために彼らと連絡を取ることを歓迎します。