コンクリート用プラスチック型 は、特別に設計された形状の異なる種類のプラスチックから製造されています。これらの金型は、コンクリート製品の必要な形状やデザインを提供するために利用されています。コンクリート用プラスチック金型は再利用可能であり、彼らはまた、コンクリートから作られている製品の非常に広い範囲を作成するための柔軟性を提供しています。これらのコンクリート製品は、ブロックのように単純であるか、または複雑な装飾品のように複雑にすることができます。コンクリート用の様々なプラスチック金型の導入は、具体的な項目が設計され、成形される方法に革命をもたらしました。
産業分野およびDIY(Do It Yourself)アプリケーションにおいて プラスチックコンクリート型 もユニークな費用対効果の高いソリューションを提供します。コンクリート用プラスチック金型は、コンクリート用プラスチック金型に比べて、従来の金属金型や木型は重く、耐久性が低いよりもはるかに優れています。また、コンクリート用プラスチック金型は、金属や木製の金型を利用することによって達成されることはそれほど容易ではない所望の複雑で複雑な形状を非常に容易に製造することが証明されている。
コンクリート用プラスチック金型の用途は幅広く、建築物の建築、コンクリート家具、庭の装飾品や敷石の作成などが含まれる。コンクリート用プラスチック型は使いやすく、手頃な価格です。彼らはデザインと建設の現代で一流の品質の結果を提供します。
プラスチックの種類 コンクリート 金型の製造工程、主な特徴、および基本的な利用方法
特定の用途のために製造されているプラスチックコンクリート金型の多くの種類があります。コンクリート用プラスチック金型の異なる種類が基づいている基本的な要因は、次のとおりです。
- コンクリート製品のサイズ
- コンクリート製品の複雑さ
- コンクリート製品の詳細
コンクリート用プラスチック金型の主な種類を、その特徴や使用方法とともに以下に説明する。
射出成形プラスチックコンクリート金型
これらの金型は、射出成形プロセスと呼ばれる非常に正確で適切に制御された製造プロセスによって準備され、製造される。
射出成形プラスチックコンクリート金型製造工程の概要
このプロセスは、必要なプラスチックコンクリート型の詳細設計を作成することから始まります。これは、CADソフトウェアを利用することによって達成される。作成されたCADモデルは、金属型を作成するために適用されます。その後、選択されたプラスチック材料のプラスチックペレットが準備されます。射出成形機では、これらのプラスチックペレットが加熱される。出来上がった溶融プラスチックは、最終的に金型のキャビティに注入される。
これは高圧下で行われる。溶融したプラスチックは金型内で冷却され、固化する。成形されたプラスチックは金型から排出される。その後、バリなどの余分なものを取り除くトリミング工程が行われ、射出成形されたプラスチック金型の最終仕上げが行われる。この製造工程は大量生産の目的に非常に適している。生産された金型は安定した品質です。
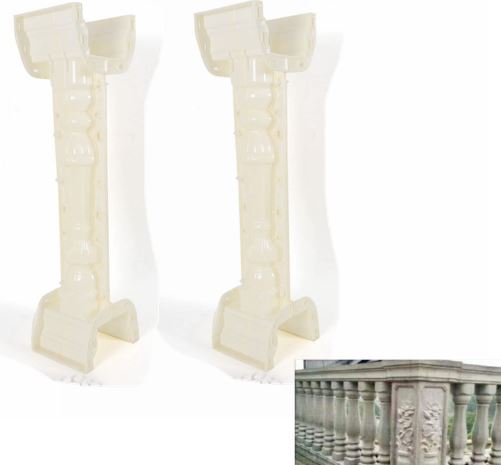
プラスチックコンクリート型
主な特徴
これらの金型の主な特徴を以下に挙げる。
- これらの金型は高い精度を持ち、細かいディテールや複雑なデザインを作り出す能力を持っている。
- これらの金型は高い強度と耐久性を誇る。
- これらの金型は高い生産性を提供する
基本的な利用
射出成形プラスチック金型の基本的な用途には、次のようなものがある。
- 庭の装飾品や彫像など、多くの装飾品を形成するために使用される。
- 装飾的なコーニスや手すりなど、複雑な建築要素の形成に使用される。
- また、高精細なタイルや敷石の成形にも利用されている。
真空成形プラスチック金型
これらの金型は、プラスチックシートを加熱することによって製造される。この熱はプラスチックシートが柔軟になるまで維持される。その後、真空吸引して金型上に成形する。
真空成形プラスチックコンクリート型の概要 製造工程
コンクリート用真空成形プラスチック金型の製造工程は、射出成形プラスチック金型と同じです。最初の段階では、CADソフトを使って金型の形状を設計する。その後、木材、発泡スチロール、樹脂などの材料からマスターパターンやモデルを作成します。これらの材料は、必要なデザインに基づいて選択されます。その後、選択されたプラスチックシート材料が必要なサイズに従って切断されます。このシートを真空成形機に入れる。このシートがしなやかになるまで加熱する。
その後、マスターパターンが機械の金型テーブル上に配置される。加熱されたプラスチックシートがこのマスターパターンの上に下ろされる。プラスチックは真空ポンプで吸引され、希望する形状に成形される。その後、硬化し冷却されたプラスチックが機械から取り出される。続くトリミング工程では、余分な材料を取り除きます。プラスチック型は慎重にマスターパターンから切り離される。金型のエッジは、それがアプリケーションで使用されるときにコンクリートのきれいなリリースを確保するために平滑化される。その後、金型は気泡や不完全な成形などの欠陥がないか品質検査を受けます。
必要に応じて、プラスチック・コンクリート型は耐久性を高めるために補強されます。脱型を助けるために離型剤やコーティングが施され、型が正しく機能することを確認するために少量のコンクリートでテストされます。この後、金型は生産の準備をし、状態を維持するために適切に保管され、定期的に清掃されます。最終検査は、型がコンクリート製造に使用できる状態であることを確認するために行われ、型が正確に成形され、耐久性があることを確認します。
主な特徴
これらの金型は、次のような特徴や特性を備えている。
- これらの金型は、射出成形プラスチック金型に比べて生産コストがはるかに低いため、費用対効果の高いソリューションを提供します。
- したがって、これらの金型は、大きくてもシンプルな形やデザインを作るのに理想的であると考えられている。
- これらの金型にはプラスチックシートが使用されているため、持ち運びや取り扱いが容易である。
基本的な利用
真空成形プラスチック金型は、次のような場面で使用されている。
- より大きなサイズのタイルや敷石は、真空成形されたプラスチック型によって作られる。
- これらの金型は、庭園の特徴や基本的な装飾品を成形するために使用されます。
- 真空成形プラスチック型は、DIYコンクリート・プロジェクトの型枠を作るのにも利用されている。
回転成形プラスチック金型
これらの金型は回転成形法によって作られる。この方法では、回転する金型にプラスチック樹脂を充填すると同時に、中空の金型から加熱します。
プラスチックコンクリート金型製造工程の概要
回転成形 コンクリート用プラスチック成形品 は、高い品質と耐久性を保証するための詳細なプロセスを伴います。CADソフトを使って金型を設計することから始まる。アルミやスチール製の金型を製作します。希望するデザインに基づき、製作方法と素材を選択する。その後、ポリエチレンなどのプラスチック樹脂を計算し、金型に装填します。その後、金型をしっかりと密閉します。この金型をオーブンに入れて加熱し、同時に2軸で回転させます。
これにより、溶けた樹脂が内面を均一にコーティングする。その後、金型は冷却ステーションに移される。樹脂が冷え、やがて固まるまで回転は続く。冷却と固化が完了したら、慎重に金型を開きます。成形されたプラスチック部品が取り出される。余分な材料があれば切り落とし、エッジと表面を滑らかにして、きれいな離型ができるようにする。
型は、気泡や不完全な成形などの欠陥がないか検査され、耐久性を高めるために補強されることもある。脱型を容易にするために離型剤やコーティングが施され、型が正しく機能することを確認するために少量のコンクリートでテストされます。最後に、金型の寿命を延ばし、安定した性能を確保するために、定期的な洗浄とメンテナンスを行い、繰り返し使用したり、大量生産したりするための準備をします。この包括的なプロセスにより、効率的なコンクリート製品の製造に適した、耐久性があり、正確な形状の型が出来上がります。
主な特徴
これらの金型は、次のような特徴と利用法を提供する。
- これらの金型は、製造工程でプラスチック材料が均等に分散されるため、均一な肉厚を有する。
- これらの金型は、その耐久性と強度のため、ヘビーデューティー製品を成形するために非常に適しています。
- 回転成形されたプラスチック金型は、他の金型では成形できない大きなものを成形する能力がある。
基本的な利用
- 回転成形されたプラスチック金型は、テーブルやベンチなどの大型コンクリート家具の成形に利用されている。
- これらの型は、水場やプランターなどの構造要素を形成するために利用される。
- 回転成形されたプラスチック金型は、大型の装飾的なガーデンアイテムの成形にも使用される。
4.3Dプリントプラスチック金型
3Dプリントプラスチック金型は、デジタルモデルからレイヤーごとに金型を構築することにより、熱可塑性材料から製造される。
製造工程の概要
3Dプリントの製造工程 プラスチックコンクリート金型 は、他の金型製造方法と同じ方法で開始されます。最初のステップでは、CADソフトウェアを使用して金型の設計が行われます。このステップは、正確で詳細な形状を作成するのに役立つので実行されます。設計が完了したら、それをファイル形式に変換します。このファイル形式は、3Dプリントに対応していなければならないことに注意することが重要です。3Dプリントされたプラスチック金型には、一般的に以下の2つの材料が選択される。
- ポリ乳酸
- アクリロニトリル・ブタジエン・スチレン
これらの選択された材料は、3Dプリンターにロードされます。その後、プリンターがデジタルデザインに基づいた金型を1層ずつ造形していく。プリント後、金型は慎重にプリンターから取り出される。その後、サポート構造や余分な材料の洗浄が行われます。その後、金型の精度が検査され、表面を滑らかにするためにサンディングやシーリングなどの仕上げが行われます。
コンクリートの除去を容易にするために、離型剤やコーティングが加えられる。型が正しく機能し、コンクリートが期待通りに固まることを確認するため、少量のコンクリートでテストします。必要な調整を行い、その有効性が確認されれば、型枠を使用する準備が整います。以下の2つの理由から、型の定期的な清掃とメンテナンスが非常に重要であることを述べておく。
- 金型を良い状態に保つ
- 寿命を延ばすために
プラスチック金型を3Dプリントする方法は、非常に詳細でカスタマイズされた金型の製造を可能にする。これは、数多くの具体的な用途に非常に適している。
主な特徴
3Dプリンターで作られたプラスチック金型は、次のような特性や用途があります。
- 3Dプリンターで作られたプラスチック金型は、高度なカスタマイズが可能なため、複雑でユニークなデザインを作り出す能力がある。
- これらの金型は、迅速かつ繰り返し変更することができますので、これらの金型は、新しいデザインを形成するために非常に適しています。
- 3D印刷されたプラスチック金型は、詳細かつ複雑な形状を作成するための品質を負担するので、これらの金型は、小規模生産に最適です。
基本的な利用
- 3Dプリントされたプラスチック金型は、カスタマイズされた多目的な装飾品を成形するために使用される。
- これらの金型は、新しいデザインや機能をテストする目的でプロトタイプを製造するために利用される。
- 主に建築に適用される高詳細の特殊要素は、3Dプリントされたプラスチック金型によって形成される。
コンクリート用プラスチック金型の利点
コンクリート用プラスチック型は、コンクリート鋳造に多くの利点を提供し、建築や装飾用途で人気のある選択肢となっている。コンクリートのためのプラスチック型の顕著な利点は次のとおりである。
- 費用対効果
プラスチック金型は、金属金型に比べて一般的に手頃な価格である。そのため、小規模なプロジェクトから大規模なプロジェクトまで、魅力的な選択肢となります。
- 軽量
プラスチック型は金属型に比べてはるかに軽い。そのため、扱いやすく、運びやすく、位置決めしやすい。この能力は最終的に人件費の削減につながり、鋳造プロセスを簡素化する。
- 柔軟性と多用途性
コンクリートのためのプラスチック型は、形状やサイズの広大な範囲で設計し、製造することができる。彼らは、他の材料では困難または高価である複雑で複雑なデザインを作成するためにはるかに適しています。
- 使いやすさ
プラスチック型は金属型に比べてメンテナンスが少なく、使いやすい。精密な細部をあらかじめ形成することができるため、コンクリートへの追加仕上げ作業の必要性を減らすことができます。
- 耐久性
現代のコンクリート用プラスチック型は、高品質の材料から製造されている。これらの材料は、耐久性の特性を負担し、何度も再利用することができます。さらに、彼らは、衝撃、摩耗、および多くの化学物質に対する耐性を提供します。これは、最終的に時間が経つにつれて、その形状と機能性を維持するのに役立ちます。
- 耐食性
これは、金属金型よりもプラスチック金型のはるかに重要な利点です。プラスチック金型は錆びたり腐食したりしないので、この特性は次のような場面で特に有利です。
- 腐食剤を含む可能性のあるコンクリート混合物を扱う場合
- カビが湿気にさらされると
- 滑らかな表面仕上げ
プラスチック型は、コンクリート上に非常に滑らかで良好な表面仕上げを提供します。その後、追加の表面処理や仕上げの要件を減らすことができます。この結果、完成品の美的品質が向上し、費用対効果の高いソリューションを提供します。
- クイック・プロダクション
プラスチック金型は、特に真空成形や3Dプリンティングのような方法で、迅速な生産速度を提供します。このプラスチック金型の特性は、納期が厳しいプロジェクトで重宝される。
- 再利用可能
プラスチック型は再利用できるように設計されているため、コンクリートのための持続可能なオプションです。定期的に適切なメンテナンスを行えば、寿命を延ばし、常に交換する必要性を減らすことができる。
- カスタマイズ
特定の設計要件を満たすために、プラスチック金型は簡単にカスタマイズすることができます。このカスタマイズの柔軟性により、汎用性の高い、またはカスタム形状のコンクリートアイテムの生産が可能になります。
- 非粘着性
ここで重要なのは、多くのプラスチック型は非粘着性を持たせるために処理またはコーティングされていることである。その結果、コンクリートが金型に付着するのを防ぐことができる。そのため、脱型が容易になり、完成品を損傷するリスクを減らすことができる。
プラスチック利用時に考慮すべき基本的要素 コンクリート 金型
コンクリートへのプラスチック成形の利用は、最良の結果と型の寿命を達成するために考慮すべきいくつかの重要な要素を必要とする。その詳細は以下の通りである。
- 素材の選択
金型の製造に使用されるプラスチックの種類や種類は非常に重要である。プラスチックによって特性が異なることはよく知られている。高密度ポリエチレンは、他のプラスチックと比較して、優れた耐久性と耐衝撃性を提供します。このように、特定のニーズや要件に適したプラスチックを選択することは、最高の結果を達成し、金型の寿命を延ばすのに役立ちます。
- 金型設計
金型設計の複雑さが最終的な製品に影響することは言うまでもありません。そのため金型は、ドラフト角度や離型機構など、具体的な製品がスムーズに出てきて金型が無傷であることを保証するための特徴や側面を含むよう、細心の注意を払って設計される必要があります。さらに、詳細な設計は、金型製作と取り扱い手順の両方でさらなる精度を必要とするかもしれません。
- リリースエージェント
コンクリート用プラスチック型を利用する際に考慮すべき最も重要な要素は、適切な離型剤の塗布である。これらの離型剤は、コンクリートが型に付着するのを防ぐために利用される。一般的に使用される離型剤の種類は以下の通りです。
- 油性離型剤
- 水性離型剤
- シリコーン系離型剤
- 粉体離型剤
- 天然で環境に優しい離型剤
- 発泡剤
- 高温放出剤
離型剤の選択は、金型のプラスチック材料に適合していなければならないことに注意することが重要である。これは、コンクリート製品の品質と完全性を維持するために必要なことです。
- 温度と硬化
コンクリート用のプラスチック型は、温度変化にかなり敏感です。そのため、養生条件を慎重に管理することが重要である。これは次のような理由から重要な意味を持つ。
- 過度の熱は金型を歪ませる
- 不十分な熱はコンクリートの硬化に影響を与える
そのため、鋳造に問題がないようにするための基本的な要素は、養生温度が鋳型とコンクリートミックスの両方に適していることを確認することである。
- クリーニングとメンテナンス
コンクリート用プラスチック金型の洗浄とメンテナンスは極めて重要であり、重要である。この基本的な理由は、残留コンクリートが金型の将来の利用に問題を引き起こす可能性があるためです。そのため、適切な方法による定期的な洗浄とメンテナンスが重要です。さらに、定期的な日常点検を行い、摩耗や破損の有無を確認する必要がある。これは、最終的に金型の有効性を維持するのに役立ちます。
- 環境への影響
コンクリート用プラスチック金型の環境への影響を考慮することは重要である。生分解性でなく、リサイクル可能でないプラスチック材料は、環境に悪影響を与える可能性があります。しかし、それとは逆に、リサイクル可能なプラスチックや生分解性プラスチックを選択することは、確実に環境にプラスの影響を残します。さらに、古い金型を適切に廃棄したりリサイクルしたりすることも、環境への悪影響を減らすために重要です。
結論
プラスチック型はコンクリート鋳造のための実用的で費用効果が高い選択であり、柔軟性と耐久性を提供します。コンクリート用プラスチック型は、複雑で入り組んだデザインに価値を与えるコンクリート鋳造のための効果的なソリューションを提供します。軽量で耐腐食性に優れながら、細部までこだわったカスタムデザインを容易に実現します。適切な取り扱いとメンテナンスにより、プラスチック鋳型は様々な用途で信頼できる性能と高品質の結果を提供します。 プラスチック金型 様々なコンクリート混合物を扱う能力がある。 キャスティング 環境下で効果的に使用できる。定期的なメンテナンス、慎重な取り扱い、適切な保管は、プラスチックコンクリート型の寿命と性能をさらに高めます。全体的に、それらは装飾的および構造的なコンクリートプロジェクトのための優れたツールです。