ポリマー部品への要求が3Dプリンティングや機械加工を超える場合、製品エンジニアは射出成形に頼ることを推奨する。従来の射出成形では、適切な金型ベンダーを特定し、金型を購入する必要があり、数ヶ月かかることもある。時間はかかるし、非常に面倒だが、1個あたりのコストは比較的低い。幸いなことに、短納期のプラスチック射出成形という選択肢もある。
理解 小ロット プラスチック射出成形
少量生産の場合、短納期射出成形は長納期射出成形に比べ、より安価な金型を使用する。 大量射出成形).このプロセスはまた、多くの剛性、長いサイクルタイムと大規模な設備投資を必要とする従来の大量生産システムから脱却している。しかし、この場合、射出成形は長期的よりも短期的に適している。
仮の金型はアルミニウム製で、"硬い "生産用工具は超硬工具鋼製である。この金属は熱伝導率が高く、加工性が良いという特徴がある。アルミ製金型は鋼製金型より若干剛性が劣るが、1万個以下の生産には最適である。加えて、鋼鉄製金型よりも安価で、最終的な部品は鋼鉄製金型の場合のように数ヶ月ではなく、数週間で作られる。
小ロット射出成形は、手頃な価格と短期間で高品質のプラスチック部品を必要とするあらゆる組織に最適です。
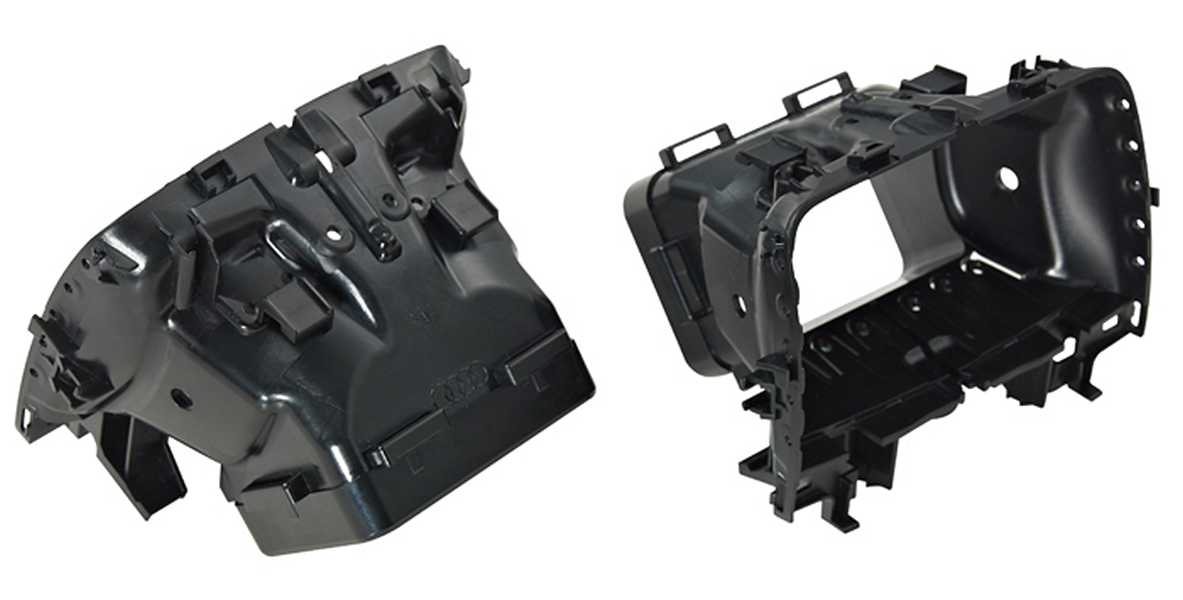
小ロット射出成形の利点
小ロット射出成形の利点は以下の通りである:
アルミ射出成形金型は、現在市販されている強化スチール金型に比べて安価です。節約の程度は、キャビティの数、部品の形状、アンダーカットやインサートなどの成形上の問題によって異なります。しかし、コストの差は通常かなり大きくなります。
しかし、そこから得られる利点はこれだけではなく、コスト面も考慮しなければならない。変更が可能でサイクルタイムが短いため、製品開発にかかる時間を短縮し、市場投入までの時間を短縮することができます。しかし、多くの組織とは異なり、当社の小ロット射出成形サービスは、顧客に大量の注文を縛ることはありません。射出成形品は生産グレードの材料で作られ、十分な表面仕上げが施されています。
部品製造のための小ロット射出成形コスト
また、少量の製品を製造するための短納期射出成形用金型の製造コストとセットアップのコストは固定されており、注文数に応じて分配しなければならないことも重要である。
一般的に、小ロット射出成形は1個から10,000個の部品に適しています。Sincere Techでは、2つの金型オプションを提供しています:通常、少なくとも2000ショットの保証に関連するプロトタイプ金型と、金型寿命保証に関連するオンデマンド生産金型です。アルミ金型がダメになった場合、同社は顧客に請求することなく金型を交換する。生産される製品の数量については、どちらのオプションもかなり安価です。
その他の特別なサービスは、初品検査、能力報告書、科学的成形プロセス開発報告書、PPAPです。一部の顧客は、短納期のアルミ金型が最終製品の金型として使用できることに気づきました。
数量が数百万個に及ぶ場合は、量産金型の方が適切かもしれない。一方、少数の部品を製造する場合は、3Dプリンティングの方が安価になることもある。メーカーの中には、3Dプリンターで試作品を作成し、小ロットで射出成形を行うところもある。
小ロット射出成形の用途
最良の戦略は、組織のニーズと組織の状況に相対するものである。例えば、新しい医療機器を開発したものの、市場の状況に疑問を抱いている医療機器製造会社は、短納期の注射器を使用することができる。これは、製品導入の間は "ペイ・アズ・ユー・ゴー "のアプローチに有利である。後日、鋼鉄製の金型に投資することを決めた場合、アルミ金型は生産金型を作るまでの暫定的な金型として使用することができる。
ブリッジ・ツールは、製品導入の立ち上げ段階だけに限定されるものではないことも重要である。ブリッジツールは、成熟したプログラムに対する保険として、かなり安価な方法で利用できる。例えば、ある家電メーカーがブリッジツールを使ってメイン金型を修正したことで、生産工程を進めることができるようになった。例えば、製品の需要が増加した場合や、現在の金型が効果的でない場合など、将来的に使用できる余分な金型を持っている。
小ロット射出成形は、3Dプリントされたモデルから鋼鉄製の生産ツールを直接使用するのに比べ、比較的低リスクで最高の金型設計と最終製品の性能を得ることができ、設計者にとって良い中間地点です。これは、医療機器のような、製品開発にかかる時間を短縮すると同時に、製品が設定された規制基準を満たしていることを確認することが重要な業界では、費用対効果が高いため、より効果的です。
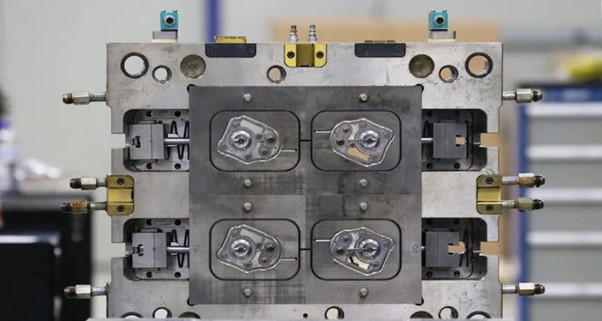
大量射出成形
当社のデジタルネットワークは、短納期の射出成形が適用できない場合に備えて、より大きく複雑な部品を大量生産することができます。当社の拡張可能なサービス範囲には以下が含まれます;
- 大型で重量があり、デザインが精巧な成形部品のプロジェクト
- 100,000以上の部品の見積もり
- 最大79インチ(2メートル)までの部品の成形能力
- モールド・テック仕上げと各種表面仕上げ(A1-A3、B1-B3、C1-C3、D1-D3)。
- 工具鋼P20、アルミニウム&スチールなどの工具、顧客の要件に応じてカラーマッチング工具。
- 小ロット射出成形についてもっと知りたいですか?ファイルをアップロードして無料で成形性をチェックし、プロトラブズの成形チームにご相談ください。プロトラブズのサービスを利用して、迅速で効果的な部品生産を始めましょう。
小ロット射出成形のコストは高いか?
射出成形で部品が作られる日用品には、電気ポット、照明器具、キーボードのキーなどがある。通常、このような製品は数十万セットから大量に生産される。
この工法には、費用対効果、材料の汎用性、柔軟性など、いくつかの利点がある。
この技法は、汎用性があり、多くの種類の材料が利用可能で、部品単価が安いため、大量生産に最も適している。素子のコストは小銭単位であり、サイクルタイムは秒単位であるため、この手順によって現在の手頃な価格設定が可能になる。これは材料の選択にも当てはまり、通常は金属を使用するところに、柔軟なエラストマーやポリマーを使用することができる。
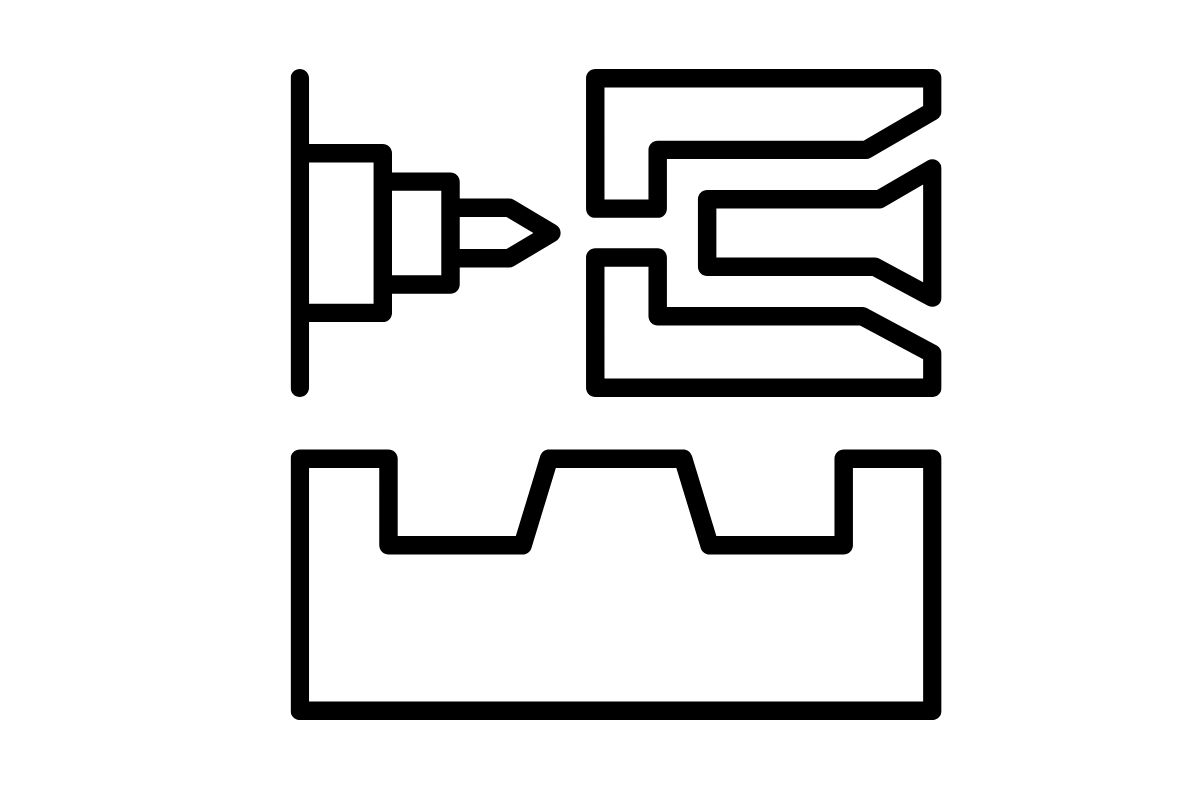
必要な部品点数が少ない場合は?
少数の部品を製造する場合、金型のコストは重要な要素となる。従来の金型製造方法は高価で、時間もかかる。しかし、今日、費用を最小限に抑えるために指摘できる多くの現代的な対応策がある。
主なコスト要因は、セットアップと定期的なメンテナンスである。
金型は成形プレスに設置され、材料/色は乾燥され、供給され、成形条件は設定され、初期品質管理サンプルはセットアップ中に採取される。金型を保護し、残りの材料を剥がし、成形サイクル後に金型を開いて保管しなければならない。このセットアップは通常、特に短納期の場合、部品単位で請求され、金型のサイズや材料/色の変更数によって、1時間から半日かかることもある。
シェイピングの手順
成形段階で発生するコストには、使用する材料のコスト、プレス機のコスト、メディアの手動または自動操作が含まれます。材料のコストは、使用する材料の種類や購入した材料の量にもよりますが、同じ材料でも少量購入するのと大量購入するのとでは大きな違いがあります。特殊な顔料も、最終製品を製造する過程で使用されるため、コスト増の原因となる。
プレスのコストに影響する要素には、1サイクルで射出されるプラスチックの量であるショット重量と、射出中に金型を閉じるために使用される力であるトン数が含まれる。大型プレスは、高い運転コストと設備の減価償却のためにコストがかかる。また、インサートの装填や排出、その他の成形後の作業など、手作業が必要な場合もコストに影響します。
完全に自動化され、一定の量を生産するツールは、小ロット用に作られ、手作業で搬送や梱包を行うツールとは区別される。
プロトタイピングの代替案
意図した生産材料での試作は非常に有利である。プロトタイプや小ロット生産の場合、金型の選択肢は多く、わずか2つのパーツを成形することも可能である。しかし、プロトタイピングと部品製造の速度はまちまちで、中には数日かかるものもあります。これは、コーティングされる構造物の表面、材質、形状による。遅延時間は通常2週間から4週間です。
工具費
金型の費用は、エレメントの複雑さ、大きさ、製作に要する時間によって異なる。金型は決して安くはなく、単純なものは2,000ポンドからだが、より複雑なものは5,000ポンドから7,000ポンド。大きいものや複雑なものは30,000ポンドになることもある。特定のプロジェクトのデータと詳細な見積もりは、正確なコスト見積もりの基礎となる。
少量の射出成形プロジェクトでは、可能なコストと実現可能な解決策をより広く理解するために、専門家の助言を求めることをお勧めします。あなたのプロジェクトに小ロット射出成形を使用することを考え、必要な数量のコストを知りたい場合は、お気軽にお問い合わせください。
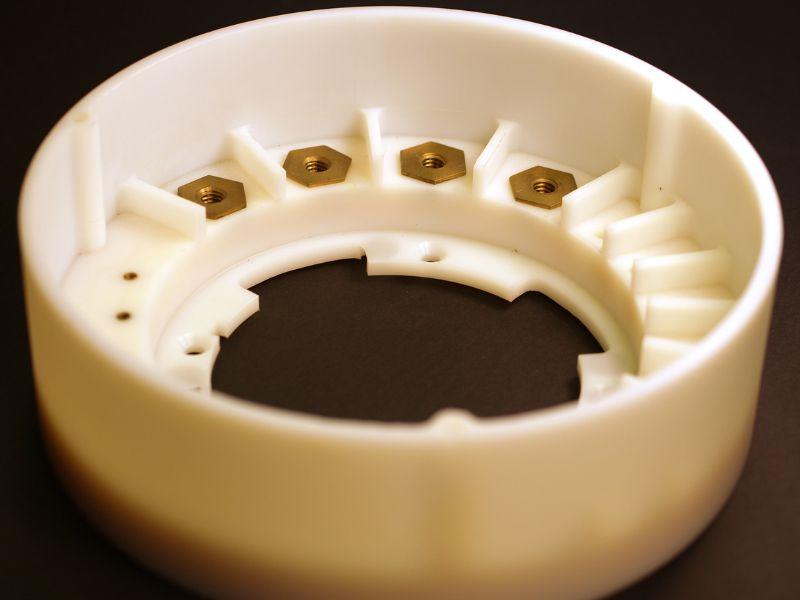
Sincere Techが提供する射出成形サービス
Sincere Techは10本のうちの1本 中国のプラスチック射出成形会社 当社は10年以上前に設立され、プラスチック射出成形部品と商品の設計と生産に携わってきました。その豊富な専門知識により、弊社は以下のような小ロット射出成形プロジェクトの全段階を効果的に管理することができます:
金型のデザイン: 最高の技術と金型製作技術で、お客様の製品にご満足いただける金型を製作いたします。お客様のオリジナルの図面、回路図、モデルを基に金型設計を作成します。AutoCAD、SolidWorks、ProE、Cimatron、CADKey形式のCADの使用に精通しています。
当社の金型製作チームは、最新のCNC加工技術を駆使し、射出成形金型の設計が完了した後、高品質で正確な寸法の金型を最短時間で製作します。これはカスタム金型の一例です。ABS、HDPE、LDPE、PE、HIPS、TPU、PETなど、さまざまな熱可塑性プラスチックのプロトタイプを作成することができます。
プロトタイピング:射出成形金型を製作する前に、3Dプリンターを使って各部品を素早く製作し、形状に合っているか、その通りに機能するかを確認します。ABS、PLA、TPUなど、さまざまな種類の材料でFDMプリントによるプロトタイプを提供しています。ウレタン鋳造、SLS、SLAなど、その他のプロトタイピング・サービスについては、他のサービス・プロバイダーと連携しています。
射出成形:射出成形 射出成形 設備は経験豊富なスタッフによって運営されており、28トンから240トンのクランプ力を発生させることができ、再現性も示すことができます。成形作業で加工する材料は、1サイクルあたり0~16オンスの範囲です。Sincere Techは、少量から大量の製品の射出成形サービスも提供しています。
Sincere Techで提供するカスタムプラスチック射出成形部品は、最高の品質、納期、リーズナブルな価格を保証します。