Siete indecisi se usare o meno il titanio o alluminio per il vostro progetto? Non preoccupatevi, non è un caso unico, perché molti ingegneri e progettisti si trovano nella stessa situazione. Questi metalli sono abbastanza simili e usati in modo intercambiabile, ma anche diversi nelle loro caratteristiche, e sapere come queste caratteristiche possono influenzare le prestazioni, i costi e l'adattabilità è fondamentale. L'incapacità di prendere la decisione giusta può comportare perdite di tempo e spese aggiuntive per il progetto.
Le principali aree di disparità tra titanio e alluminio Il rapporto resistenza/peso, la corrosione e le caratteristiche termiche. Il titanio è più resistente alla corrosione e nella maggior parte dei casi è più forte dell'alluminio, il che lo rende perfetto per l'uso in ambienti di lavoro intensivi o in aree che richiedono la sua forza, mentre l'alluminio è più leggero, più economico e perfettamente adatto a un uso normale. Infine, la decisione dipende da alcuni parametri come il peso e le condizioni di utilizzo dell'apparecchiatura.
Avendo una conoscenza generale delle differenze tra titanio e alluminio, analizziamo le caratteristiche e gli utilizzi di ciascun metallo. Grazie a questi fattori, sarete in grado di prendere una decisione più adatta al vostro progetto. Continuate a leggere per scoprire il materiale più adatto a voi.
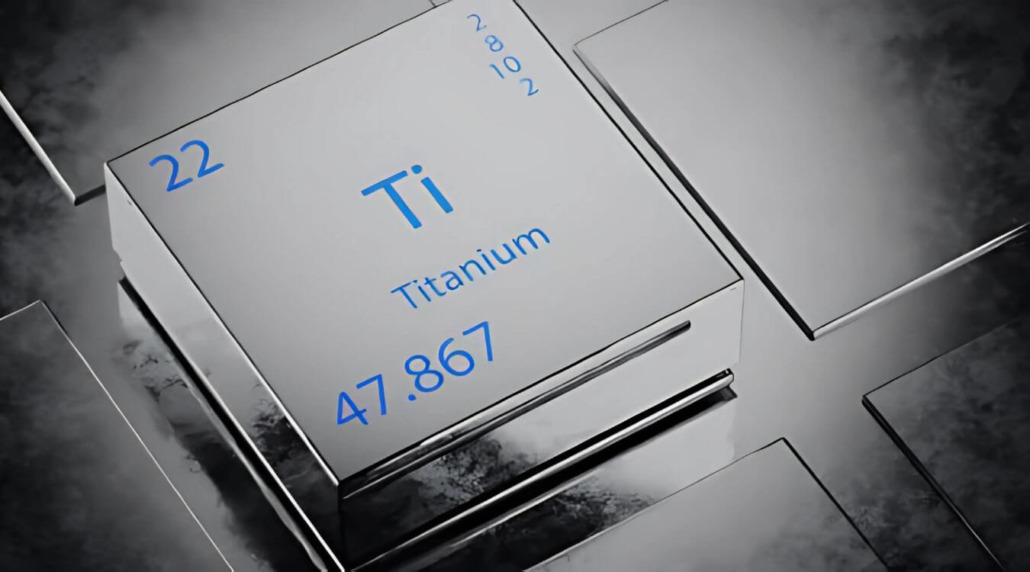
Titanio e alluminio: Confronto tra le loro proprietà
Un confronto di questo tipo potrebbe essere incompleto se non si tiene conto delle diverse proprietà di ciascun materiale che ne influenzano le prestazioni e le diverse applicazioni. Il titanio ha anche un rapporto resistenza/peso superiore a quello dell'acciaio, quindi non solo è forte, ma anche leggero. Ha anche un'eccellente resistenza alla corrosione, soprattutto in condizioni severe, come nel settore aerospaziale, degli impianti medici e della marina. L'alluminio, invece, è un materiale leggero, facile da lavorare e relativamente più economico del rame. Viene utilizzato nelle applicazioni automobilistiche, nell'edilizia e nei prodotti di consumo per la sua versatilità e facilità di fabbricazione.
Proprietà meccaniche
Forse il più importante di questi è il confronto delle proprietà meccaniche tra titanio e alluminio. Il TiAl ha un carico di rottura di circa 434 MPa - 1400 MPa, in base al tipo di lega utilizzata nella sua produzione, mentre l'alluminio ha un carico di rottura di circa 90MPa - 700 MPa. Ciò significa che il titanio può sopportare molte sollecitazioni prima di cedere, pertanto è preferibile utilizzarlo nei casi in cui è necessaria un'elevata resistenza. Per quanto riguarda l'allungamento, il titanio è meno duttile dell'alluminio, il che rende più facile la deformazione dell'alluminio senza fratture e quindi una maggiore libertà di progettazione.
Considerazioni sul peso
Un'altra considerazione importante nella scelta tra questi metalli è il peso. L'alluminio è molto più leggero del titanio, con una densità di 2,7 g/cm³ rispetto ai 4,5 g/cm³ del titanio. Questa minore densità fa sì che l'alluminio sia ampiamente utilizzato nei settori in cui è necessario ridurre il peso, ad esempio nella produzione di aerei e automobili. Tuttavia, gli elevati requisiti di resistenza e il risparmio di peso fanno sì che il titanio abbia la meglio, anche se è più pesante degli altri materiali.
Resistenza alla corrosione
Entrambi hanno caratteristiche di resistenza alla corrosione abbastanza buone, anche se la resistenza è in mezzi diversi. La resistenza alla corrosione del titanio è eccellente in ambienti di servizio severi, soprattutto quando è esposto al cloro o all'acqua salata, e la presenza di un denso strato di ossido sulla superficie del materiale impedisce un'ulteriore corrosione. Anche l'alluminio forma uno strato di ossido, ma è vulnerabile all'attacco di pitting in alcune condizioni specifiche; ad esempio, reagisce con l'acqua di mare o con gli alcali caldi. Per questo motivo, il titanio trova applicazione nelle industrie marine e di trasformazione chimica.
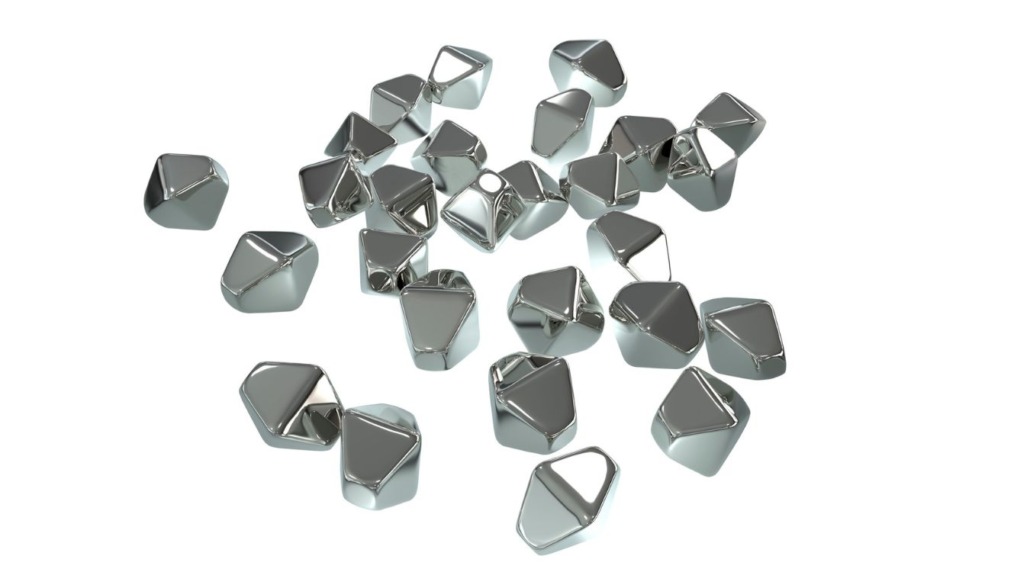
Conduttività termica e conduttività
Nella scelta della lega titanio-alluminio si deve tenere conto anche del coefficiente termico. In particolare, la conducibilità termica dell'alluminio è di circa 205 W/mK, mentre quella del titanio è di circa 21,9 W/mK. Ciò rende l'alluminio più conduttivo di calore in applicazioni come gli scambiatori di calore e i sistemi di raffreddamento. La minore conducibilità termica, tuttavia, è vantaggiosa anche in luoghi in cui il calore non è richiesto, come ad esempio negli spazi utilizzati per la costruzione di aerei.
Costo e disponibilità
Il costo è una delle considerazioni più importanti nella scelta del materiale da utilizzare per le costruzioni. Nella maggior parte delle condizioni, l'alluminio è probabilmente più disponibile e più economico del titanio e quindi può essere più adatto per diversi usi. I processi di produzione dell'alluminio sono inoltre molto ben definiti e spesso il processo complessivo è meno complesso e quindi più economico. D'altra parte, l'estrazione e la lavorazione del titanio sono costose e difficili, quindi la sua applicazione è limitata a settori in cui le sue proprietà offrono un grande valore.
Sintesi delle applicazioni
Pertanto, il confronto diretto tra titanio e alluminio dipende dalla natura del progetto da realizzare. Il titanio è stato preso in considerazione nei settori aerospaziale, biomedico e marino, dove l'alta resistenza e le proprietà superiori di resistenza alla corrosione sono fondamentali. L'alluminio è ampiamente utilizzato nei settori automobilistico, edile e dei beni di consumo per la sua leggerezza, il basso costo e la facilità di lavorazione. La conoscenza di queste proprietà può aiutare ingegneri e progettisti a prendere decisioni corrette in base agli obiettivi del progetto specifico.
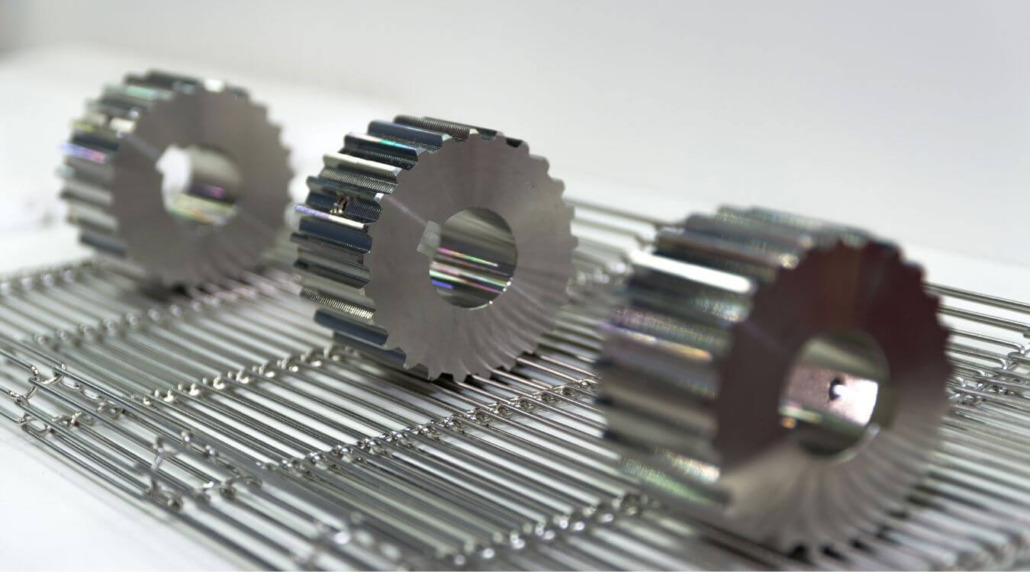
Ecco una tabella delle proprietà che mette a confronto il titanio e l'alluminio, seguita da una sintesi tecnica delle principali differenze.
Proprietà | Titanio | Alluminio |
Densità | 4,5 g/cm³ | 2,7 g/cm³ |
Resistenza alla trazione | 434 - 1.400 MPa | 90 - 700 MPa |
Resistenza allo snervamento | 880 - 1.200 MPa | 40 - 550 MPa |
Allungamento | 10 - 30% (varia a seconda della lega) | 12 - 25% (varia a seconda della lega) |
Resistenza alla corrosione | Eccellente (soprattutto in ambienti salini e difficili) | Buono (ma suscettibile di vaiolatura) |
Conduttività termica | 21,9 W/mK | 205 W/mK |
Conducibilità elettrica | 2,0 x 10^6 S/m | 3,5 x 10^7 S/m |
Punto di fusione | 1,668 °C | 660 °C |
Modulo di elasticità | 110 - 120 GPa | 70-80 GPa |
Costo | Alto (più costoso da estrarre e lavorare) | Inferiore (abbondante e conveniente) |
Lavorabilità | Difficile (richiede strumenti specializzati) | Buono (più facile da lavorare e fabbricare) |
Applicazioni | Aerospaziale, impianti medicali, nautica, automotive | Automotive, edilizia, beni di consumo |
Introduzione all'alluminio
L'alluminio è leggero, resistente e malleabile. È il terzo metallo più abbondante sulla crosta terrestre e si ottiene principalmente dalla bauxite. L'alluminio è un metallo di colore argento apprezzato, tra l'altro, nell'industria aerospaziale, automobilistica, edile e degli imballaggi. Ha alcune proprietà come un'elevata resistenza alla corrosione e una buona conducibilità termica ed elettrica che lo rendono indispensabile per molti usi. Inoltre, l'alluminio è 100% riciclabile, il che lo rende ecologico per i produttori e i consumatori che lo preferiscono.
IL stampi per pressofusione sono una delle tecnologie per la produzione di leghe di alluminio, come l'ADC 12, l'A380, ecc. Naturalmente ci sono altre tecnologie di produzione che possono produrre materiale in alluminio, come la colata in sabbia, lo stampaggio per estrusione, la colata a gravità, la lavorazione, ecc.
Applicazioni dell'alluminio
- Industria aerospaziale: L'alluminio trova ampia applicazione nell'industria aerospaziale sotto forma di telai di fusoliere, ali e carrelli di atterraggio. Grazie alla sua leggerezza e all'elevata resistenza, può essere utilizzato per migliorare l'efficienza della combustione del carburante e le prestazioni generali dell'aereo.
- Produzione automobilistica: Nell'industria automobilistica, l'alluminio viene utilizzato per creare blocchi motore, carrozzerie, ruote e strutture dei veicoli. Queste proprietà rendono l'auto più leggera e, di conseguenza, più chilometrica e meno inquinante.
- Costruzione e architettura: L'alluminio è ampiamente utilizzato nella fabbricazione di finestre, porte, tetti e pareti attraverso l'uso di telai e rivestimenti. Grazie alla sua durata, non si corrode facilmente ed è facile da mantenere, quindi è adatto per l'uso in case e altri edifici.
- Soluzioni di imballaggio: L'imballaggio è un'altra importante applicazione dell'alluminio, che viene utilizzato nelle bottiglie di birra, nelle lattine per alimenti e nei fogli di alluminio. Queste proprietà lo rendono un materiale eccellente per la protezione del contenuto, è leggero e può essere riciclato.
- Applicazioni elettroniche ed elettriche: L'alluminio viene utilizzato nei dissipatori di calore, negli alloggiamenti e nei connettori. Grazie alla sua buona conducibilità elettrica, viene utilizzato nei cablaggi e in altre parti elettroniche.
- Beni di consumo: Nei beni di consumo l'alluminio è ampiamente utilizzato negli utensili da cucina e nei mobili, grazie al suo aspetto moderno e alla sua resistenza. È più comunemente utilizzato in articoli come pentole, biciclette e attrezzature sportive.
- Applicazioni marine: La resistenza alla corrosione dell'alluminio lo rende adatto alla produzione di scafi di imbarcazioni, strutture marine e altre parti che possono entrare in contatto con l'acqua di mare.
- Attrezzature industriali: Nelle applicazioni industriali, l'alluminio trova applicazione in parti di macchinari, telai e utensili, poiché è forte per le sue dimensioni e quindi riduce la fatica.
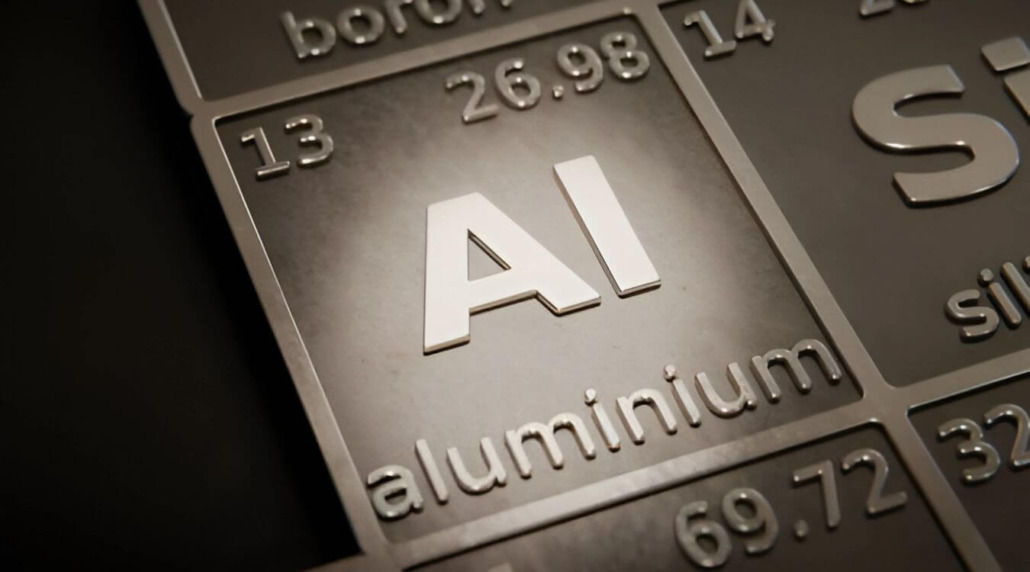
Opzioni di lavorazione dell'alluminio
- Lavorazione CNC: La lavorazione CNC è una tecnica familiare utilizzata nella produzione di componenti in alluminio. Può essere utilizzata per tagliare, forare e fresare forme e dimensioni troppo complesse per altri metodi convenzionali.
- Fresatura: La fresatura è un processo che utilizza utensili da taglio rotanti per eliminare il materiale dal pezzo. È relativamente facile lavorare con le frese a candela e le frese frontali, quindi è adatta per i progetti di intaglio.
- Trasformazione: Nelle operazioni di tornitura i pezzi di alluminio vengono fatti ruotare e, con l'ausilio di utensili da taglio, il materiale viene rimosso per produrre forme cilindriche. Questo metodo è particolarmente adatto alla produzione di alberi, aste e raccordi.
- Estrusione: L'estrusione di alluminio è un processo di produzione di profili di lunga lunghezza utilizzando l'alluminio attraverso una filiera, comprese barre, tubi e canali ad alte temperature. Consente inoltre di ottenere una forma coerente della sezione trasversale dei componenti strutturali.
- Pressofusione: La pressofusione è un processo di produzione di pezzi complessi in alluminio attraverso la forzatura del metallo fuso in uno stampo. Questa tecnica si applica soprattutto in caso di volumi di produzione elevati e di progettazione complicata.
- Taglio laser: Il taglio laser consente di eseguire tagli netti e precisi su lamiere e parti in alluminio. Questa tecnica è particolarmente adatta a forme e disegni intricati e, pertanto, è ideale per l'utilizzo nel design ornamentale e pratico.
- Taglio a getto d'acqua: Il taglio a getto d'acqua consiste nell'utilizzo di acqua ad alta pressione miscelata con abrasivi per tagliare l'alluminio. Questo metodo è adatto a materiali spessi e non crea zone termicamente alterate.
- Piegatura e formatura: L'alluminio può essere formato con diverse tecniche, come la formatura a freno e la formatura a rullo, perché è relativamente facile da manipolare. Questi processi sono applicati nella produzione di parti strutturali e gusci.
Introduzione al titanio
Il titanio è un metallo forte ma leggero, caratterizzato da un'elevata resistenza alla corrosione e da una durata generalmente elevata. Il titanio è il nono componente più abbondante della crosta terrestre e si ottiene da minerali come il rutilo o l'ilmenite. Essendo ~1,45 volte più leggero dell'acciaio e altrettanto resistente, il titanio è adatto a tutte le applicazioni ad alte prestazioni. La sua capacità di resistere a condizioni corrosive, cioè di lavorare efficacemente in ambiente marino, chimico, ad alte e basse temperature, lo rende adatto anche ad applicazioni aerospaziali, mediche e marine. Inoltre, il titanio è biocompatibile, il che lo rende utile per l'uso in impianti e dispositivi medici. Le caratteristiche benefiche del titanio sono ampiamente importanti per lo sviluppo di tecnologie e innovazioni in diversi settori.
Applicazioni del titanio
- Industria aerospaziale: Il titanio è ampiamente utilizzato nelle industrie aerospaziali grazie al suo elevato rapporto resistenza/peso e alla stabilità alle alte temperature. Viene utilizzato in parti che comprendono telai, motori e carrelli di atterraggio per migliorare l'efficienza del carburante e le prestazioni.
- Dispositivi Medici: Il titanio è altamente biocompatibile ed è quindi utilizzato in alcuni impianti medici e prodotti correlati, tra cui impianti ortopedici, impianti dentali, dispositivi e strumenti da taglio. È resistente alla corrosione e si fonde facilmente con l'osso, rendendo questi prodotti durevoli ed efficienti.
- Applicazioni marine: In sostanza, il titanio ha eccellenti caratteristiche di corrosione per le applicazioni in acqua di mare. Il materiale viene applicato a parti come scafi di navi, eliche e altre parti subacquee in cui è richiesta la presenza di un materiale altamente resistente.
- Elaborazione chimica: Nell'industria chimica, il titanio è altamente resistente alle sostanze chimiche e alle alte temperature. Viene applicato negli scambiatori di calore, nei reattori e nelle tubazioni, il che gli consente di fornire servizi di lunga durata, soprattutto in condizioni corrosive.
- Settore energetico: Alcune delle applicazioni specifiche del titanio nel settore energetico sono le piattaforme petrolifere offshore e le centrali elettriche a gas e petrolio. L'elevata forza e l'eccellente resistenza alla corrosione lo rendono adatto all'uso in parti esposte ad ambienti ostili.
- Industria automobilistica: Il titanio viene utilizzato nei veicoli ad alte prestazioni per i sistemi di scarico e le parti del motore a combustione interna, oltre che per i componenti strutturali leggeri. Il suo punto di forza è che riduce il peso del veicolo, migliorando al contempo le prestazioni, con conseguente risparmio di carburante.
- Attrezzature sportive: L'applicazione principale del titanio è nelle attrezzature sportive come telai di biciclette, mazze da golf e racchette da tennis, dove la leggerezza è importante e la resistenza è indispensabile per una lunga durata.
- Prodotti di consumo: L'uso del titanio nei prodotti di consumo è piuttosto comune, poiché conferisce resistenza, leggerezza e un aspetto lussuoso a orologi, gioielli e utensili.
Opzioni di lavorazione per il titanio
- Lavorazione CNC: La lavorazione CNC è una tecnica popolare per fabbricare pezzi in titanio complessi e precisi. Questo processo consente di lavorare con precisione e di avere un controllo dimensionale ravvicinato ed è ampiamente utilizzato per i lavori di precisione richiesti nelle applicazioni aerospaziali e mediche.
- Fresatura: È emerso che la fresatura del titanio può essere eseguita utilizzando strumenti e strategie appropriate. La fresatura ad alta velocità viene utilizzata per ridurre la velocità di asportazione del materiale, preservando l'integrità della superficie.
- Trasformazione: Le operazioni di tornitura sono ampiamente utilizzate per produrre pezzi cilindrici in titanio. In questa tecnica, il pezzo di titanio viene tenuto fermo mentre l'utensile da taglio viene utilizzato per rimuovere il materiale per formare alberi, tubi e raccordi mentre il pezzo viene ruotato.
- Taglio a getto d'acqua: Il metodo di taglio a getto d'acqua consente di tagliare efficacemente il titanio senza l'uso di calore che potrebbe alterare le proprietà del materiale. Questa tecnica si applica soprattutto a forme complesse e materiali spessi.
- Lavorazione per elettroerosione a scintilla: L'elettroerosione è l'acronimo di Electrical Discharge Machining (lavorazione a scarica elettrica), utilizzata per completare le forme del titanio. È un processo di lavorazione non convenzionale applicabile a materiali duri con un elevato livello di precisione in forme complesse.
- Taglio laser: Il titanio può essere tagliato al laser per lastre e pezzi e il processo produce bordi eccezionalmente puliti. Questo metodo è particolarmente indicato per lavori di precisione e su materiali sottili.
- Formatura e piegatura: Il titanio può anche essere forgiato e piegato utilizzando processi come la profilatura e la pressatura. Questi processi consentono di generare elementi strutturali e involucri mantenendo le proprietà del materiale.
- Stampa 3D (produzione additiva): Il titanio è più comunemente utilizzato nella produzione additiva (stampa 3D) per i suoi vantaggi e la libertà dei suoi progetti. Questa tecnologia può essere utilizzata per creare prototipi e realizzare prodotti a bassa densità.
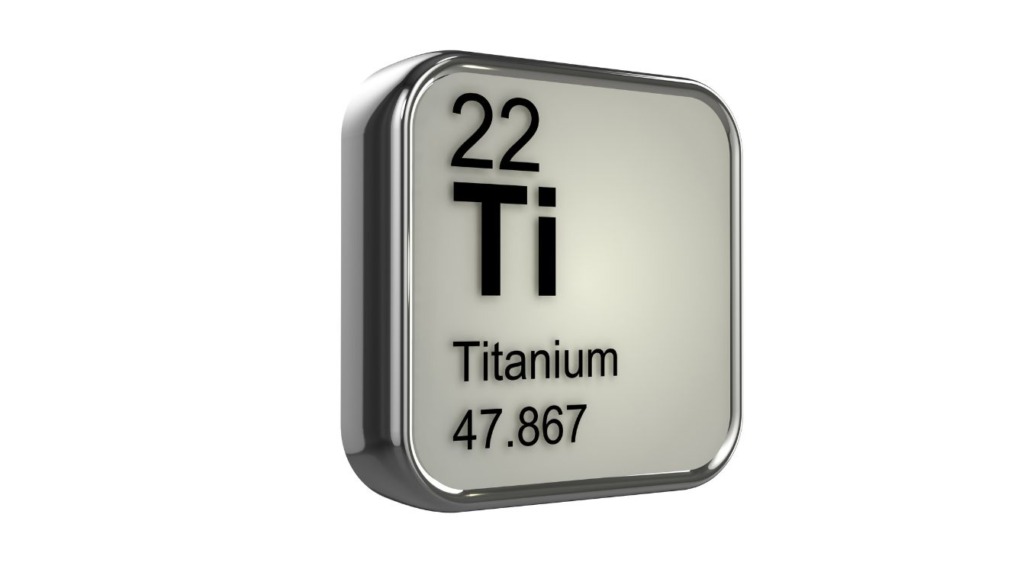
Titanio vs. alluminio: vantaggi e svantaggi
Nella scelta dei materiali per le applicazioni ingegneristiche, è essenziale soppesare i vantaggi e gli svantaggi del titanio e della lega di alluminio. Ogni metallo ha proprietà uniche che lo rendono adatto a scenari diversi. La tabella seguente presenta una ripartizione logica dei principali pro e contro di ciascun materiale.
Proprietà | Alluminio | Titanio |
Peso | Pro: Leggero (densità ~2,7 g/cm³), ideale per le applicazioni che richiedono una riduzione del peso. | Pro: Più leggero dell'acciaio (densità ~4,5 g/cm³), offre un buon equilibrio tra resistenza e peso per le applicazioni più impegnative. |
Forza | Contro: resistenza alla trazione generalmente inferiore (90-700 MPa) rispetto al titanio, che può limitarne l'uso in applicazioni ad alta sollecitazione. | Pro: Elevata resistenza alla trazione (434-1.400 MPa), che garantisce prestazioni eccezionali sotto carico e in ambienti ad alta temperatura. |
Resistenza alla corrosione | Contro: resistenza moderata; suscettibile di vaiolatura in ambienti difficili. | Pro: Eccellente resistenza alla corrosione, soprattutto in ambienti marini e chimici, grazie a uno strato di ossido protettivo. |
Costo | Pro: Generalmente più economici; ampiamente disponibili e meno costosi da produrre. | Contro: costo più elevato a causa dei complessi metodi di estrazione e lavorazione, che lo rendono meno accessibile per alcune applicazioni. |
Lavorabilità | Pro: Facile da lavorare con utensili standard, è adatto alla produzione di grandi volumi. | Contro: più difficile da lavorare; richiede strumenti e tecniche specializzate, che possono aumentare i tempi e i costi di produzione. |
Conduttività termica | Pro: Elevata conducibilità termica (205 W/mK), ideale per applicazioni di dissipazione del calore. | Contro: la minore conducibilità termica (21,9 W/mK) ne limita l'efficacia nelle applicazioni che richiedono un efficiente trasferimento di calore. |
Conducibilità elettrica | Pro: Eccellente conduttore elettrico (3,5 x 10^7 S/m), adatto per applicazioni elettriche. | Contro: conducibilità elettrica inferiore (2,0 x 10^6 S/m), che lo rende meno adatto alle applicazioni elettriche. |
Riciclabilità | Pro: Altamente riciclabile, mantiene le sue proprietà dopo il riciclo, contribuendo alla sostenibilità. | Pro: Anch'esso riciclabile, anche se meno comunemente trattato a causa dei costi più elevati associati al riciclaggio del titanio. |
Applicazioni | Pro: Versatile; utilizzato nei settori automobilistico, aerospaziale, edile e dell'imballaggio grazie alle sue proprietà favorevoli. | Pro: Applicazioni specializzate; critiche nei settori aerospaziale, medico e ad alte prestazioni, dove resistenza e durata sono essenziali. |
Resistenza al calore | Contro: punto di fusione più basso (~660 °C); può deformarsi a temperature elevate, limitando le applicazioni ad alto calore. | Pro: Elevato punto di fusione (~1.668 °C); prestazioni eccezionali in condizioni termiche estreme. |
Come scegliere tra titanio e alluminio?
Per valutare l'idoneità di due metalli, il titanio o l'alluminio, per un determinato uso, è necessario tenere in debita considerazione alcuni fattori tecnici indicati di seguito. Il titanio ha un elevato rapporto forza-peso, un'eccellente resistenza alla corrosione, soprattutto in condizioni severe, ed è utilizzato in componenti ad alte prestazioni; tuttavia, è relativamente costoso, con un prezzo medio compreso tra $10 e $30 per libbra.
L'alluminio, invece, costa tra $1,4 e $2 per libbra, ha una buona lavorabilità e conducibilità termica ed è ideale per la produzione di grandi dimensioni e in aree in cui il peso è una preoccupazione importante. Bisogna anche considerare i costi di lavorazione, perché il titanio richiede tempo e denaro per essere lavorato, mentre l'alluminio può essere fabbricato più velocemente e a costi inferiori. A lungo termine, sarà possibile effettuare una valutazione adeguata di questi fattori, in particolare dei costi, nonché dei requisiti dell'applicazione, in base ai quali sarà effettuata la scelta corretta del materiale.
Ci sono molti Cina pressofusione aziende che producono parti in alluminio per la pressofusione e vendono in tutto il mondo, quindi normalmente l'alluminio sarà più popolare nella maggior parte delle industrie, naturalmente alcune industrie devono utilizzare il matreiale in titanio.
Conclusione
In conclusione, la scelta di quale dei due metalli utilizzare nello sviluppo del progetto di ingegneria civile dipende dalle specifiche del progetto stesso. Tuttavia, a causa dei costi più elevati rispetto ad altri metalli e delle proprietà difficili da lavorare, il titanio trova impiego nell'aviazione e in campo medico, grazie alla sua super resistenza, alla corrosione e all'usura. L'alluminio, invece, è apprezzato per la sua leggerezza, la facilità di lavorazione e il costo relativamente basso, che lo rendono adatto a quasi tutti i settori industriali, come quello automobilistico e delle costruzioni. Infine, la conoscenza dei punti di forza e di debolezza e dei costi di ciascun tipo di materiale consentirà agli ingegneri e ai progettisti di prendere la decisione migliore in base agli obiettivi e alle operazioni del progetto.
FAQ tecniche
Q1. Quali sono le principali differenze di resistenza tra titanio e alluminio?
Titanio ha una resistenza alla trazione compresa tra 434 e 1400 MPa, mentre l'alluminio ha una resistenza alla trazione compresa tra 90 e 700 MPa, quindi il titanio è migliore per le sollecitazioni elevate.
Q2. Quale materiale, il titanio o l'alluminio, ha migliori proprietà di resistenza alla corrosione?
Il titanio è più utile in condizioni corrosive in quanto crea uno strato di ossido, mentre l'alluminio presenta solo una corrosione moderata e può spaccarsi in alcune circostanze.
Q3. Che ruolo ha il peso nella scelta tra la lega di alluminio e quella di titanio?
L'alluminio è molto più leggero (densità ~2,7 g/cm³), il che ne rende preferibile l'uso in applicazioni sensibili al peso, mentre la densità di ~4,5 g/cm³ del titanio gli conferisce una maggiore resistenza e quindi il suo peso può essere spiegato da applicazioni ad alte prestazioni.
Q4. In che modo i costi di lavorazione influenzano la lega di alluminio e titanio?
L'alluminio è più facile da lavorare e più economico del titanio, che necessita di strumenti e processi specifici, con conseguenti costi elevati di manodopera e lavorazione.
Q5. In quale settore viene utilizzato principalmente ciascun metallo? Il titanio è ampiamente utilizzato nel settore aerospaziale, medico, automobilistico e così via, mentre l'alluminio è impiegato nell'industria automobilistica, nell'edilizia, nell'imballaggio e in altri settori industriali, grazie al suo costo contenuto e ai suoi utilizzi.