Mi az a fröccsöntőforma?
Injekciós penész a fröccsöntési eljárás során használt eszköz, amellyel alkatrészeket állítanak elő azáltal, hogy anyagot fecskendeznek egy szerszámüregbe. Általában acélból (H13, P20, 1.2312, 1.2344, S136H stb.) vagy alumíniumból készül, és gondosan úgy tervezik, hogy megfeleljen a végtermék alakjának és specifikációinak.
A fröccsöntőforma két félre van osztva, amelyek az üreg és a mag fele, az öntési folyamat során össze vannak szorítva, és az anyagot egy öntőcsövön keresztül fecskendezik a forma üregébe, ahol lehűl és megszilárdul a kívánt formára. Miután az alkatrész kialakult, a szerszám kinyílik, és az alkatrész kilökődik. Az öntőforma több alkatrész gyártásához újra felhasználható.

Mi a fröccsöntőforma
A fröccsöntőszerszámok típusai
A fröccsöntőformák számos fajtája között megtalálható:
Üregspecifikus penész
A fröccsöntési folyamat minden egyes ciklusa csak egy alkatrész előállítására képes, ha egy üregű szerszámot használunk. Egy alkatrész előállítása ezzel a szerszámmal olyan egyszerű, mint a műanyag gyanta befecskendezése, a lehűlés megvárása, majd a kész termék eltávolítása.
Ha összehasonlítjuk a többlövetű szerszámok gyártási költségeit az együregű szerszámokkal, az előbbi általában kedvezőbb. Ha kis számú alkatrész egyszerre történő előállítása túl drága lenne, akkor ezek a prototípusok és kis sorozatú gyártási folyamatok esetében a legmegfelelőbbek.

Egy üregű penész
Az egylövetű öntőformák előnyei a következők:
- Költséghatékonyság: az egylövetű öntőforma előállítása gyakran olcsóbb, mint a többlövetű öntőforma előállítása.
- Egyszerű kialakítás: Könnyű gyártás és karbantartás a tervezés egyszerűségének köszönhetően: Az egylövetű szerszámok elrendezése gyakran kevésbé bonyolult, mint a többlövetű szerszámoké.
- Rugalmasság: A legkülönbözőbb alkalmazások, például a prototípusgyártás és a kis sorozatú gyártás, alkalmasak az együregű szerszámok használatára.
Az egylövetű öntőformák hátrányai a következők:
- Korlátozott gyártás: Ez a korlátozás az egy üregű szerszámokat alkalmatlanná teszi a nagy volumenű öntvénygyártásra, mivel minden ciklusban csak egyetlen alkatrész előállítására képesek.
- Összetett alkatrészek: Ezekhez több üregű szerszámra vagy családi szerszámra van szükség.
- Hatékonyság: A több üregű szerszámokhoz képest az egylövetű szerszámok kevésbé hatékonyak, mivel korlátozott kapacitásuk miatt minden ciklusban csak egyetlen alkatrészt tudnak létrehozni.
Több üregű formák:
A több üregű szerszámok olyan típusú fröccsöntőszerszámok, amelyek egynél több üreggel rendelkeznek. Ez lehetővé teszi, hogy a fröccsöntési folyamat során egynél több alkatrész készüljön minden egyes forduló során. Az alkalmazás igényeitől függően ezek a szerszámok azonos vagy különböző furatokkal készülhetnek.
Mivel egy ciklusban sok alkatrész létrehozására képes, a több üregű szerszámokat jellemzően a következő célokra alkalmazzák nagy volumenű fröccsöntés gyártás. Ez a funkció lehetővé teszi számukra, hogy növeljék a termelés hatékonyságát, miközben csökkentik az alkatrészenkénti költségeket.

több üregű penész
A több üregű szerszámok előnyei a következők:
- Nagy volumenű gyártás: A több üregű szerszámok nagy sorozatgyártásra készülnek, ami megkönnyíti a nagy mennyiségű alkatrész gyártását.
- Költséghatékony: a több üregű szerszámok általában olcsóbbak, mint az egy üregű szerszámok, mivel több alkatrészt tudnak egy menetben előállítani.
- Összetett alkatrészek: A több üregű szerszámok bonyolult és sok részből álló alkatrészek gyártására használhatók.
A több üregű formák hátrányai közé tartoznak:
- Komplex tervezés: A több üregű formákat nehezebb elkészíteni és karbantartani, mint az egy üregű formákat, mivel a kialakításuk bonyolultabb.
- növelte a penész költségét: A több üregű szerszámok drágábbak lehetnek, mint az egy üregű szerszámok, mivel a különböző üregek különböző mértékű igénybevételnek és kopásnak lehetnek kitéve a fröccsöntési folyamat során. Ez kevésbé hatékony gyártáshoz és magasabb javítási költségekhez vezethet.
Forrócsatornás penész:
Hot runner penész olyan típusú fröccsöntőforma, amely forrócsatornás rendszert használ az olvasztott műanyagnak a szerszámüregekbe történő juttatására. A forrócsatornás rendszer egy fűtött elosztócsőből áll, amely az olvasztott műanyagot az egyes fúvókacsúcsokhoz juttatja, amelyeket aztán a szerszámüregekbe irányít.

Hot runner penész
A forrócsatornás szerszámok előnyei a következők:
- Jobb alkatrészminőség: A forrócsatornás szerszámok jobb minőségű alkatrészeket állíthatnak elő, mivel minimalizálják a futókban maradó műanyag mennyiségét, csökkentve az olyan hibák kockázatát, mint a villanás, a rövid lövések és a süllyedésnyomok.
- Fokozott termelési hatékonyság: A forrócsatornás szerszámok növelhetik a termelés hatékonyságát, mivel kiküszöbölik a manuális beavatkozás szükségességét a futók eltávolításához a formázott alkatrészekből, csökkentve a ciklusidőt és javítva a teljes gyártási sebességet.
- Energiahatékonyság: A forrócsatornás szerszámok energiatakarékosabbak a hagyományos hidegcsatornás szerszámokhoz képest, mivel minimalizálják a futókban elvesztegetett műanyag mennyiségét.
A forrócsatornás szerszámok hátrányai a következők:
- Komplex tervezés: A melegcsatornás szerszámok összetettebb kialakításúak, mint a hagyományos hidegcsatornás szerszámok, így előállításuk és karbantartásuk drágább.
- Fokozott karbantartás: A melegcsatornás szerszámok általában több karbantartást igényelnek, mint a hidegcsatornás szerszámok, mivel összetettebb fűtőrendszerrel rendelkeznek, amelyet jó állapotban kell tartani.
- A dugulással szembeni sebezhetőség: A forrócsatornás szerszámok sérülékenyek lehetnek az eltömődésre, különösen nagy viszkozitású vagy hosszú folyási hosszúságú anyagok feldolgozása esetén, mivel ezek miatt az olvadt műanyag megszilárdulhat a csatornákban. Ez a termelés hatékonyságának csökkenését és a karbantartási költségek növekedését eredményezheti.
Halmozott öntőformák:
Stack penész egy olyan típusú fröccsöntőforma, amely lehetővé teszi, hogy egyetlen gépi ciklusban egyszerre több üreg fröccsöntése történjen. Az egymásra helyezett szerszámok lényegében két vagy több egymásra helyezett szerszámot jelentenek, amelyek mindegyike egyetlen alkatrészt állít elő.

Stack Mold
A rakóformák előnyei a következők:
- Fokozott termelési hatékonyság: Az egymásra épülő szerszámok lehetővé teszik több alkatrész egyidejű öntését, ami növeli a termelés hatékonyságát és csökkenti a ciklusidőt.
- Csökkentett anyaghulladék: Az egymásra épülő szerszámok minimalizálják az anyagpazarlást, mivel lehetővé teszik több alkatrész gyártását egyetlen adag műanyag felhasználásával.
- Alacsonyabb költségek: Az egy üregű szerszámokhoz képest költséghatékonyabbak lehetnek, mivel lehetővé teszik több alkatrész gyártását egyetlen gépciklus alatt.
A rakóformák hátrányai a következők:
- Komplex tervezés: Az egy üregű szerszámokhoz képest a halmazszerszámok összetettebb kialakításúak lehetnek, így előállításuk és karbantartásuk drágább.
- Csökkentett alkatrészminőség: A több üreg jelenléte miatt megnövekedhet az olyan hibák kockázata, mint a villanás, a rövid lövések és a süllyedésnyomok.
- Fokozott karbantartás: Az egy üregű formákhoz képest általában több karbantartást igényelnek, mivel összetettebb kialakításúak, amelyeket jó állapotban kell tartani.
Családi penészgombák:
A családi öntőformák, más néven többszörös lenyomatú öntőformák, amelyek hasonlóak a több üregű öntőformához, a fröccsöntés egy olyan típusa, amely lehetővé teszi, hogy több, kissé eltérő kialakítású alkatrészt egyidejűleg, egyetlen gépi ciklusban öntsenek. Ezt úgy érik el, hogy a szerszámban több üreg van, amelyek különböző formájú és méretű alkatrészek előállítására alkalmasak.
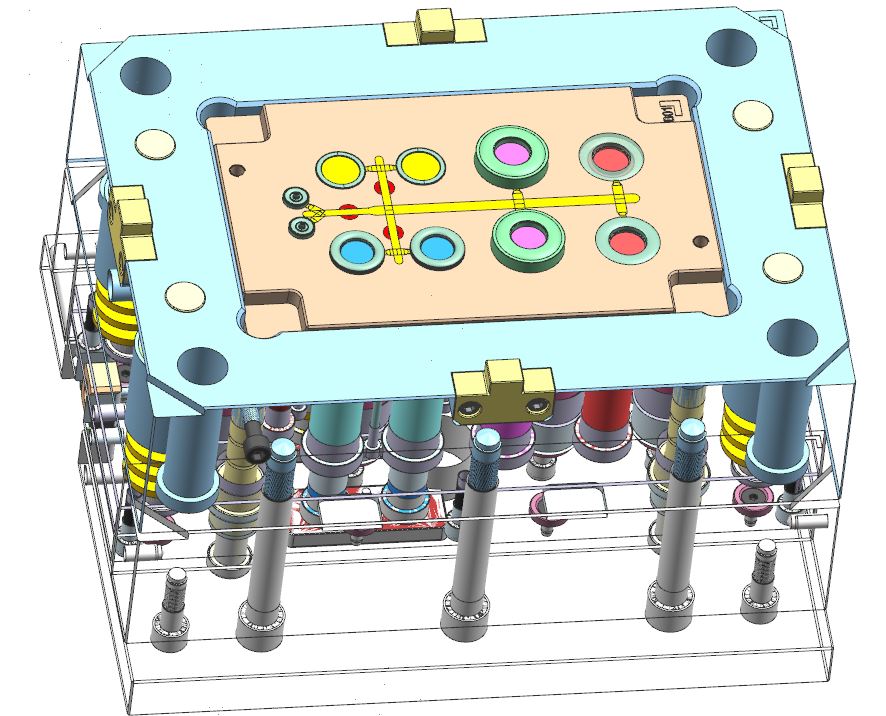
családi penész
A családi penészgombák előnyei a következők:
- Fokozott termelési hatékonyság: A családi szerszámok lehetővé teszik, hogy egyszerre több, különböző kialakítású alkatrészt öntsenek, növelve ezzel a termelés hatékonyságát és csökkentve a ciklusidőt.
- Csökkentett költségek: A családi szerszámok költséghatékonyabbak lehetnek, mintha minden egyes alkatrészhez több együregű szerszámot gyártanának, mivel lehetővé teszik több alkatrész gyártását egyetlen gépciklus alatt.
- Rugalmasság: A családi formák lehetővé teszik a különböző formatervezésű alkatrészek gyártását, így sokoldalú megoldást jelentenek azon gyártók számára, akiknek számos terméket kell előállítaniuk.
A családi penészgombák hátrányai közé tartoznak:
- Komplex tervezés: A családi öntőformák összetettebb kialakításúak lehetnek az egy üregű öntőformákhoz képest, így előállításuk és karbantartásuk drágább.
- Csökkentett alkatrészminőség: A családi formák csökkentett minőségű alkatrészeket állíthatnak elő, mivel a több üreg jelenléte a hibák, például a villanás, a rövid lövések és a süllyedésnyomok megnövekedett kockázatát eredményezheti.
Kétlövetű formák:
Kétlövetű penész (2 lövéses fröccsöntés), más néven túlformázás vagy többlövetű szerszámok vagy 2K szerszámok, a fröccsöntés egy olyan típusa, amely lehetővé teszi két különböző anyag egy gépi ciklusban történő öntését. Ez az eljárás egy első anyag (alapanyag) öntését jelenti egy szerszámba, majd egy második anyag (overmold anyag) öntését az első anyagra.

Két lövéses penész
A kétlövetű szerszámok előnyei a következők:
- Fokozott funkcionalitás: A kétlövetű szerszámok lehetővé teszik két különböző tulajdonságú anyag kombinálását, így nagyobb funkcionalitású alkatrészek hozhatók létre.
- Javított esztétika: A kétlövetű szerszámok lehetővé teszik a különböző színek vagy textúrák integrálását egyetlen alkatrészbe, ami vizuálisan vonzóbb terméket eredményez.
- Csökkentett összeszerelési idő: Azáltal, hogy két anyagot egyesítenek egyetlen alkatrészben, a kétlövetű szerszámok csökkenthetik a további összeszerelési lépések szükségességét, ami csökkenti a gyártási időt és a költségeket.
A kétlövetű öntőformák hátrányai a következők:
- Komplex tervezés: A kétlövetű szerszámok összetettebb kialakításúak, mint az egylövetű szerszámok, így előállításuk és karbantartásuk drágább.
- Megnövekedett ciklusidő: A kétlövetű szerszámok általában hosszabb ciklusidővel rendelkeznek az egylövetű szerszámokhoz képest, mivel a folyamat során két anyagot kell egyetlen gépi ciklusban megformázni.
- Kompatibilitási problémák: A kétlövetű formák megkövetelik, hogy a két formázandó anyag kompatibilis legyen egymással, és megfelelően tapadjon, ezért fontos, hogy gondosan válasszuk ki a felhasznált anyagokat.
Formák kicsavarása:
A kicsavarható szerszámok a fröccsöntés egy olyan típusa, amelyet kifejezetten csavarmenettel rendelkező alkatrészek, például kupakok, fedelek és tartályok gyártására terveztek. Ezek a szerszámok egyedülállóak abban, hogy olyan mechanizmussal rendelkeznek, amely lehetővé teszi, hogy a szerszám magja forogjon, miközben az üreg helyben marad, így a formázott alkatrész kicsavarható a szerszámból, miután az lehűlt és megszilárdult.

kicsavarható penész
A kicsavarható formák előnyei a következők:
- Nagy hatékonyság: A kicsavaró szerszámok lehetővé teszik a menetes alkatrészek hatékony gyártását egyetlen gépi ciklusban, csökkentve a gyártási időt és a költségeket.
- Javított pontosság: A kicsavarható formák lehetővé teszik a menetes alkatrészek pontos gyártását egyenletes menetemelkedéssel és menetmélységgel, javítva a végtermék minőségét és teljesítményét.
- Sokoldalúság: A kicsavaró formák különböző típusú és méretű menetekkel rendelkező alkatrészek gyártására használhatók, így sokoldalúan felhasználhatók számos különböző alkalmazáshoz.
A kicsavarható formák hátrányai a következők:
- Komplex tervezés: A kicsavarható formák más típusú formákhoz képest összetettebb kialakításúak, így előállításuk és karbantartásuk drágább.
- Megnövekedett ciklusidő: A kicsavaró szerszámok jellemzően hosszabb ciklusidővel rendelkeznek más típusú szerszámokhoz képest, mivel a folyamat a szerszám magjának forgatásával jár.
- Kopás és elhasználódás: A kicsavarható szerszámok forgó mechanizmusa idővel hajlamos lehet a kopásra, és rendszeres karbantartást igényel a szerszám megfelelő működésének fenntartása érdekében.
Összecsukható magvas penész:
Az összecsukható magvas szerszámok a fröccsöntés egy olyan típusa, amelyet belső üregekkel rendelkező üreges alkatrészek, például csövek, csövek és más összetett alakú alkatrészek gyártására használnak. Ezek a szerszámok olyan egyedi kialakítást alkalmaznak, amely lehetővé teszi, hogy a szerszám magja önmagába omoljon, létrehozva az alkatrész belső üregét.

Összecsukható magvas szerszámkomponens
Az összecsukható magvas szerszámok előnyei a következők:
- Javított hatékonyság: Az összecsukható magvas szerszámok lehetővé teszik az üreges alkatrészek gyártását egyetlen gépi ciklusban, ami csökkenti a gyártási időt és a költségeket.
- Javított alkatrészminőség: Az összecsukható magvas szerszámok pontosabb és következetesebb belső üreget biztosítanak, ami javítja a végleges alkatrész általános minőségét.
- Sokoldalúság: Az összecsukható magvas szerszámok különböző formájú és méretű alkatrészek széles skálájának gyártására használhatók, így sokoldalúan felhasználhatók számos különböző alkalmazáshoz.
Az összecsukható magvas szerszámok hátrányai a következők:
- Komplex tervezés: Az összecsukható magvas szerszámok más típusú szerszámokhoz képest összetettebb kialakításúak, így előállításuk és karbantartásuk drágább.
- Megnövekedett ciklusidő: Az összecsukható magú szerszámok jellemzően hosszabb ciklusidővel rendelkeznek más típusú szerszámokhoz képest, mivel a folyamat során a szerszám magja összecsukódik.
- Kopás és elhasználódás: A mag összecsukható mechanizmusa idővel hajlamos lehet az elhasználódásra, és rendszeres karbantartást igényel a forma megfelelő működésének fenntartása érdekében.
Előnyei és hátrányai műanyag fröccsöntő penész
A Fröccsöntés:
- Nagy volumenű termelés: A fröccsöntés rendkívül hatékony módszer nagy mennyiségű azonos alkatrész gyártására. Ezáltal ideális a fogyasztási cikkek, autóipari alkatrészek és más, nagy mennyiségű hasonló alkatrészt igénylő termékek tömegtermeléséhez.
- Precizitás: Az eljárás lehetővé teszi a méretpontosság és az alkatrész konzisztenciájának nagyon pontos ellenőrzését. Ez a szigorúan ellenőrzött feldolgozási körülményeknek, valamint a formázógép és a szerszám merevségének köszönhető.
- Gyorsaság: A fröccsöntés gyors folyamat, a ciklusidő kis alkatrészek esetén mindössze néhány másodperc. Ez lehetővé teszi a gyártók számára, hogy viszonylag rövid idő alatt nagy mennyiségű alkatrészt állítsanak elő.
- Költséghatékony: Az alkatrészek fröccsöntéssel történő gyártásának költségei a gyártási mennyiség növekedésével egyre gazdaságosabbá válnak. Ez annak köszönhető, hogy a szerszámmal sok alkatrész gyártható az élettartama alatt, és az alkatrészenkénti költség a mennyiség növekedésével csökken.
- Sokoldalúság: A fröccsöntés az anyagok széles skálájából, többek között műanyagokból, fémekből és elasztomerekből készíthető alkatrészek előállítására használható. Ez a sokoldalúság teszi népszerű választássá a gyártók számára, akiknek a termék egyedi követelményeitől függően különböző anyagokból kell alkatrészeket gyártaniuk.
- Automatizálás: Ez hatékonyabbá teszi a folyamatot, és csökkenti a kézi munka szükségességét. Ez javíthatja az alkatrészek konzisztenciáját és minőségét is.
- Összetett formák: A fröccsöntéssel összetett formák és formatervek készíthetők, beleértve a bonyolult részletekkel és szűk tűrésekkel rendelkező alkatrészeket is. Ez az öntési folyamat pontos vezérlésének és a rendkívül részletes formák tervezésének köszönhetően lehetséges.
- Anyagválasztás: A fröccsöntés lehetővé teszi a gyártók számára, hogy az anyagok széles skálájából válasszanak, amelyek mindegyike egyedi tulajdonságokkal rendelkezik, például szilárdsággal, rugalmassággal, hő-, vegyszer- és kopásállósággal. Ez lehetővé teszi az egyes alkalmazásokhoz a legjobb anyag kiválasztását, és a kívánt tulajdonságokkal rendelkező alkatrészek gyártását.
A fröccsöntés hátrányai:
- Magas kezdeti költségek: A kezdeti költségek magasak lehetnek, különösen az összetett formák és formatervek esetében. Ez az eljárást kevésbé költséghatékonnyá teheti kis darabszámú alkatrészek vagy prototípusok esetében.
- Korlátozott tervezési rugalmasság: A forma elkészülte után nehéz és költséges lehet a formaterv megváltoztatása. Ez korlátozhatja a tervezési változtatások vagy fejlesztések lehetőségét, ha a szerszám már elkészült.
- Anyaghulladék: A fröccsöntés jelentős mennyiségű hulladékanyagot termel, amelynek ártalmatlanítása költséges és környezetkárosító lehet. Ez a gyártási költségeket is növelheti, és csökkentheti a folyamat általános hatékonyságát.
- Átfutási idő: Az öntőforma létrehozásának és a fröccsöntési folyamat beállításának átfutási ideje hosszú lehet, különösen az összetett alkatrészek esetében. Ez lelassíthatja a termékfejlesztési folyamatot, és korlátozhatja a termékek gyors piacra vitelét.
- Felületkikészítési korlátozások: A fröccsöntés nem biztos, hogy jó minőségű felületet eredményez egyes alkatrészeknél, különösen a bonyolult részletekkel vagy szűk tűrésekkel rendelkező alkatrészeknél. Ez korlátozhatja a kiváló minőségű esztétikai megjelenésű alkatrészek előállításának lehetőségét.
- Anyagkompatibilitás: Az anyag és a szerszám közötti kompatibilitás kihívást jelenthet, mivel egyes anyagok nem működnek jól bizonyos típusú szerszámokkal, vagy speciális feldolgozási feltételeket igényelnek. Ez korlátozhatja az egyes anyagokból való alkatrészgyártás lehetőségét, és növelheti a gyártási költségeket.
- Korlátozott alkatrészméret: A fröccsöntést a szerszám mérete és a fröccsöntőgép záróereje korlátozza. Ez korlátozhatja az előállítható alkatrészek méretét, és növelheti a nagyobb alkatrészek előállítási költségeit.
- Másodlagos műveletek: Egyes alkatrészeknél a formázás után másodlagos műveletekre, például trimmelésre vagy utómunkára lehet szükség. Ez növelheti a gyártási költségeket és korlátozhatja a folyamat általános hatékonyságát, természetesen ezek a problémák bizonyos esetekben megoldhatók a fröccsöntőforma javításával.
A fröccsöntőformával szembesülő gyakori problémák
Ha egyszer a műanyag fröccsöntés területén dolgozik, mindig lesz néhány olyan probléma, amelyet minden nap meg kell oldania, Itt van néhány gyakori kihívás, amellyel a fröccsöntés során szembesül:
Torzítási problémák:
A vetemedés gyakori probléma a fröccsöntés során, és a fröccsöntött alkatrész deformációjára vagy torzulására utal, amely a szerszámból való eltávolítás után következik be. Ez számos tényező miatt történhet, többek között a következők miatt:

Warp torzítás
- Nem megfelelő hűtés: Ha az alkatrész túl gyorsan vagy egyenetlenül hűl le, az az anyag különböző sebességgel zsugorodik és húzódik össze, ez vetemedést okozhat.
- Maradó feszültség: A fröccsöntés során alkalmazott nagy nyomás miatt az alkatrészben maradványfeszültség keletkezik. Ez a feszültség vetemedést okozhat, ha nem oldják fel megfelelően.
- Anyagválasztás: Egyes anyagok hajlamosabbak a vetemedésre, mint mások. Például az alacsony hőállóságú vagy alacsony méretstabilitású anyagok nagyobb valószínűséggel vetemednek.
- Formakialakítás: Különösen akkor, ha a forma nem teszi lehetővé a megfelelő hűtést vagy anyagáramlást.
- Feldolgozási feltételek: A nem következetes feldolgozási körülmények, például a különböző befecskendezési sebességek, szerszámhőmérsékletek és nyomásszintek vetemedést okozhatnak.
A vetemedés megelőzése érdekében fontos a megfelelő anyag kiválasztása, az öntőforma kialakításának és a feldolgozási körülmények optimalizálása, valamint a megfelelő hűtési és anyagkezelési gyakorlatok alkalmazása. Ezenkívül szükség lehet a formázás utáni kezelésekre, például lágyításra, a maradó feszültségek enyhítésére és a méretstabilitás javítására.
Flash problémák:
A fröccsenő hibák a fröccsöntésben használt kifejezés, amely a fröccsöntési folyamat során a szerszámból kiszoruló felesleges anyagra utal. Flash akkor keletkezik, amikor az anyag a tervezett formaüregből a választóvonalba, vagyis a szerszám két fele közötti térbe folyik.

Formázási villanás vagy göröngyök
A villanást több tényező is okozhatja, többek között:
- Helytelen szerszámtervezés: A rosszul megtervezett szerszám okozhat flash-t, mivel az anyag a választóvonalba szivároghat.
- Ellentmondásos feldolgozási feltételek: A változó feldolgozási körülmények, például a befecskendezési sebesség és a nyomás, okozhatnak villogást.
- Anyagkompatibilitás: Egyes anyagok nem kompatibilisek az öntőformával, és az elválasztó vonalba áramláskor felcsapódást okozhatnak.
- A penész elhasználódása: Az idő múlásával az öntőforma elhasználódhat, és az anyag a választóvonalba szivárogva felvillanást okozhat.
A peregésnek számos negatív hatása lehet, többek között csökkentheti az alkatrész méretpontosságát, növelheti a selejt arányát, és megnehezítheti a fröccsöntés utáni műveleteket. A lobbanás minimalizálása érdekében fontos a szerszám kialakításának, a feldolgozási körülményeknek és az anyagválasztásnak az optimalizálása, valamint a szerszám rendszeres karbantartása és szükség szerinti javítása.
Hegesztési vonalak:
A hegesztési vonalak gyakori probléma a fröccsöntés során, és a fröccsöntött alkatrész felületén látható jeleket jelentik, ahol két olvadt műanyagáram találkozik és megszilárdul. A hegesztési vonalak akkor keletkeznek, amikor az anyag nem olvad össze teljesen, ahogyan a formába folyik. műanyag forma az üregbe, látható vonalat hagyva az alkatrész felületén.

Hegesztősor
A hegesztési vonalakat számos tényező okozhatja, többek között:
- Elégtelen olvadékáramlás: Ha az anyagnak nincs elég ideje az áramláshoz és a teljes összeolvadáshoz, hegesztési vonal alakulhat ki.
- Helytelen kapu kialakítás: A rosszul megtervezett kapu, amely az a pont, ahol az olvadt anyag belép a formaüregbe, hegesztési vonalat okozhat.
- Ellentmondásos feldolgozási feltételek: Változó feldolgozási körülmények, például a befecskendezési sebesség és nyomás, hegesztési vonalat okozhatnak.
- Anyagkompatibilitás: Egyes anyagok nem kompatibilisek a formával, és a formaüregbe áramláskor hegesztési vonalat okozhatnak.
A hegesztési vonalak gyengíthetik az alkatrész szilárdságát és csökkenthetik annak általános minőségét. A hegesztési vonalak minimalizálása érdekében fontos a szerszámtervezés, a feldolgozási feltételek és az anyagválasztás optimalizálása, valamint a megfelelő anyagkezelési gyakorlatok alkalmazása. Ezen túlmenően a hegesztési vonalak kialakulásának csökkentése érdekében szükség lehet speciális megmunkálási technikák, például több üregű szerszámok vagy forrócsatornás rendszerek alkalmazására.
Süllyedési jelek:
A süllyedésnyomok, más néven "süllyedés", "vákuumos süllyedés" vagy "bőr" a fröccsöntött műanyag alkatrész felületén lévő süllyedt vagy mélyedő területek. Ezeket általában számos tényező okozza, többek között:
- Gyanta zsugorodás: A gyanta lehűlésével és megszilárdulásával egyenetlenül zsugorodhat, ami süllyedésnyomokat okozhat.
- Rossz anyagáramlás: Ha a gyanta nem folyik egyenletesen az öntőforma minden területére, akkor üregek vagy süllyedt területek keletkezhetnek.
- Nem megfelelő tömítési nyomás: Ha a befecskendezési nyomás nem elég magas, a gyanta nem tölti ki teljesen a formát, ami süllyedésnyomokhoz vezet.
- Szerszámtervezési kérdések: Az öntőforma kialakítása, beleértve a kapuk elhelyezését és méretét, a futórendszert és a szellőztetést, mind befolyásolhatja a formázott alkatrész minőségét, és hozzájárulhat a süllyedési nyomok kialakulásához.
A süllyedésnyomok befolyásolhatják az öntött alkatrész esztétikai minőségét és funkcionalitását, és frusztrációt okozhatnak a gyártók és a végfelhasználók számára. A süllyedésnyomok minimalizálása érdekében fontos, hogy gondosan mérlegelje az azokat előidéző tényezőket, például az anyagválasztást, a szerszámtervezést, a feldolgozási paramétereket és az alkatrésztervezést, és szükség szerint kiigazításokat végezzen a fröccsöntési folyamat optimalizálása érdekében.
Áramlási jelek:
A folyásnyomok gyakori probléma a fröccsöntés során, és a fröccsöntött alkatrész felületén látható nyomokat vagy csíkokat jelentik, amelyeket az olvadt műanyag áramlása okoz, miközben az kitölti a szerszámüregeket. A folyásnyomok akkor keletkeznek, amikor az anyag egyenetlenül folyik, és látható nyomot hagy maga után az alkatrész felületén.
A folyásnyomokat számos tényező okozhatja, többek között:
- Elégtelen olvadékáramlás: Ha az anyagnak nincs elég ideje az áramláshoz és a formaüreg kitöltéséhez, folyásnyomok alakulhatnak ki.
- Helytelen kapu kialakítás: A rosszul megtervezett kapu, amely az a pont, ahol az olvadt anyag belép a formaüregbe, folyásnyomokat okozhat.
- Ellentmondásos feldolgozási feltételek: A változó feldolgozási körülmények, például a befecskendezési sebesség és nyomás, folyásnyomokat okozhatnak.
- Anyagkompatibilitás: Egyes anyagok nem kompatibilisek a szerszámmal, és folyásnyomokat okozhatnak, amikor a szerszám üregébe áramlanak.
A folyásnyomok csökkenthetik az alkatrész általános minőségét és kozmetikai megjelenését. Az áramlási nyomok minimalizálása érdekében fontos a szerszámtervezés, a feldolgozási feltételek és az anyagválasztás optimalizálása, valamint a megfelelő anyagkezelési gyakorlatok alkalmazása. Ezen túlmenően szükség lehet speciális feldolgozási technikák, például több üregű szerszámok vagy forrócsatornás rendszerek alkalmazására az áramlási nyomok kialakulásának csökkentése érdekében.
Karcolásos problémák:
A karcolások a fröccsöntött alkatrész felületén látható jeleket vagy karcolásokat jelentik, amelyeket az alkatrész és a szerszám vagy más idegen tárgyak fizikai érintkezése okoz a fröccsöntési folyamat során. A karcolás több okból is előfordulhat, többek között:
- Rossz szerszámtervezés: A nem megfelelően megtervezett öntőformák vagy öntőforma-alkatrészek karcolásokat okozhatnak az alkatrész felületén.
- Elégtelen kenés: Ha a szerszám és a szerszám alkatrészei nincsenek megfelelően kenve, karcolásokat okozhatnak az alkatrész felületén.
- Rossz anyagkezelés: A nyersanyag vagy a kész alkatrészek rossz kezelése karcolásokat okozhat az alkatrész felületén.
- Törmelék a formában: A szerszám üregében lévő idegen tárgyak vagy törmelék karcolásokat okozhat az alkatrész felületén.
A karcolások csökkenthetik az alkatrész általános minőségét és kozmetikai megjelenését. A karcolási problémák minimalizálása érdekében fontos a megfelelő szerszámtervezés, kenés, anyagkezelés és karbantartási gyakorlatok alkalmazása. Ezenkívül a szerszám és a szerszámalkatrészek rendszeres tisztítása és ellenőrzése segíthet megelőzni a karcolási problémák kialakulását.
Kidobójelek:
A kidobónyomok a fröccsöntött alkatrész felületén látható nyomok, amelyeket a kidobócsapok vagy más kidobómechanizmusok okoznak a fröccsöntési folyamat során. A kilökőnyomok akkor keletkeznek, amikor a kilökőcsapok kilökik a fröccsöntött alkatrészt a szerszámüregből, és látható nyomokat hagynak maguk után az alkatrész felületén.
A kidobásnyomokat számos tényező okozhatja, többek között:
- Helytelen kidobócsap kialakítás: Ha a kidobócsapok nem megfelelően vannak kialakítva, akkor látható nyomokat hagyhatnak az alkatrész felületén.
- Túlzott erőszak: Ha a kidobócsapok a kidobás során túlzott erőt fejtenek ki az alkatrészre, mélyebb és észrevehetőbb nyomokat hagyhatnak az alkatrész felületén.
- Következetlen kilövőerő: Ha a kidobóerő nem egyenletes az egyik kidobócsapról a másikra, az egyenetlen kidobónyomokat eredményezhet az alkatrész felületén.
- Rossz felületkezelés: Ha a szerszám üregének felülete nem sima, akkor ez kidobónyomokat okozhat az alkatrész felületén.
A kidobásnyomok csökkenthetik az alkatrész általános minőségét és kozmetikai megjelenését. A kidobónyomok minimalizálása érdekében fontos a kidobócsapok kialakításának és a szerszámüreg felületének optimalizálása, valamint a megfelelő karbantartási és ellenőrzési gyakorlatok alkalmazása. Ezenkívül a kilökőnyomok minimalizálása érdekében szükség lehet speciális kilökőmechanizmusok, például levegővel segített kilökés vagy oldalirányú kilökés alkalmazására.
Rövid lövésekkel kapcsolatos problémák:
A rövid lövés egy gyakori probléma a fröccsöntés során, amikor az olvadt műanyag nem tölti ki teljesen a szerszámüregeket, ami a kívánt méretnél kisebb méretű öntött alkatrészt eredményez. A rövid lövés több okból is előfordulhat, többek között:
- Elégtelen anyag: Ha nincs elég anyag a formaüreg kitöltéséhez, rövid lövés következhet be.
- Nem megfelelő feldolgozási körülmények: Ha a feldolgozási feltételek, például a befecskendezési sebesség és a nyomás nem megfelelően vannak beállítva, rövid lövés léphet fel.
- Rossz szerszámtervezés: A rosszul megtervezett forma rövid lövést okozhat, mivel az anyag nem tud a formaüreg minden területére beáramlani.
- Anyagromlás: Ha az anyag lebomlott vagy nem megfelelően tárolták, az rövidzárlatot okozhat.
A rövid lövések csökkenthetik az alkatrész általános minőségét és funkcionalitását, valamint anyagveszteséget és megmunkálási időt eredményezhetnek. A rövid lövések minimalizálása érdekében fontos a szerszámtervezés, a feldolgozási feltételek és az anyagválasztás optimalizálása, valamint a megfelelő anyagkezelési gyakorlatok alkalmazása. Emellett a rövid lövések kialakulásának megelőzésében segíthet az öntőberendezés rendszeres ellenőrzése és karbantartása.
Levegőcsapda és égési nyomok:
A légcsapdák és az égési nyomok gyakori problémák a fröccsöntés során, amelyek a nem megfelelő feldolgozási körülmények vagy a szerszámtervezés miatt fordulhatnak elő.
A légcsapdák akkor keletkeznek, amikor a fröccsöntési folyamat során a levegő beszorul a szerszám üregébe, és az anyag a légzseb körül áramlik, ahelyett, hogy kitöltené azt. Ez látható üregeket vagy zsebeket eredményezhet az öntött alkatrészben. A légcsapdákat számos tényező okozhatja, többek között:
- Elégtelen anyagáramlás: Ha az anyag nem áramlik megfelelően a formaüregbe, a levegő csapdába eshet.
- Helytelen kapu kialakítás: Ha a kapu nem megfelelően van kialakítva, a levegő beszorulhat a formaüregbe.
- Nem megfelelő szellőzés: Ha a penész nem szellőzik megfelelően, a levegő beszorulhat a penész üregébe.
Az égésnyomok akkor keletkeznek, amikor a műanyag túl sokáig van kitéve magas hőmérsékletnek, ami a műanyag lebomlásához vezet, és látható nyomokat vagy elszíneződést eredményez az alkatrész felületén. Az égésnyomokat több tényező okozhatja, többek között:
- Túl magas feldolgozási hőmérséklet: Ha a feldolgozási hőmérsékletet túl magasra állítják be, az anyag lebomolhat és égési nyomokat hagyhat.
- Elégtelen hűtési idő: Ha az alkatrészt nem hűtik le megfelelően, az anyag lebomolhat és égési nyomokat hagyhat maga után.
- Rossz szerszámtervezés: A rosszul megtervezett öntőforma miatt az anyag túl sokáig lehet magas hőmérsékletnek kitéve, ami égési nyomokat eredményezhet.
A légcsapdák és az égési nyomok minimalizálása érdekében fontos a feldolgozási feltételek és a szerszámok kialakításának optimalizálása, valamint a megfelelő ellenőrzési és karbantartási gyakorlatok alkalmazása. Ezen túlmenően szükség lehet speciális feldolgozási technikák alkalmazására, például alacsony hőmérsékletű öntésre vagy vákuumformázásra a légcsapdák és égési nyomok minimalizálása érdekében.
Feldolgozás fröccsöntőforma készítéséhez:
A fröccsöntőforma készítésének folyamata több lépésből áll:
Formakialakítás:
A fröccsöntőszerszámok tervezése a fröccsöntési folyamat kritikus szempontja, mivel közvetlenül befolyásolja a fröccsöntött alkatrészek minőségét, hatékonyságát és költségeit.
Egy jól megtervezett fröccsöntőforma olyan alkatrészeket állít elő, amelyek megfelelnek a kívánt méret-, alak- és minőségi követelményeknek, ugyanakkor hatékonyan gyárthatók és könnyen karbantarthatók.
A fröccsöntőszerszám tervezésénél figyelembe veendő legfontosabb tényezők a következők:
- Részgeometria: A formázott alkatrész tervezésénél figyelembe kell venni az alkatrész kívánt méretét, alakját és jellemzőit.
- Anyagválasztás: Az öntőforma és az öntött alkatrész anyagát olyan tényezők alapján kell kiválasztani, mint a költség, a szilárdság és a hőstabilitás.
- Penész üregek: A formaüregek számát és elrendezését úgy kell megválasztani, hogy megfeleljen a gyártási volumen követelményeinek.
- Kapuzatrendszer: A rácsőrendszer kialakítása kritikus fontosságú, mivel ez határozza meg, hogy a műanyag hogyan áramlik a szerszámüregbe.
- Kilövő rendszer: A kilökő rendszert úgy kell megtervezni, hogy a fröccsöntött alkatrészek sérülés nélkül eltávolíthatók legyenek a szerszámból.
- Hűtőrendszer: A hűtőrendszert úgy kell megtervezni, hogy a fröccsöntött alkatrészek egyenletesen és gyorsan hűljenek, csökkentve ezzel a ciklusidőt és javítva a minőséget.
- Tervezési szögek: A szerszám tervezése során megfelelő merülési szögeket kell kialakítani, hogy a formázott alkatrészeket ki lehessen venni a szerszámból.
- Szellőztetés: A formát ki kell szellőztetni, hogy a levegő távozhasson a formaüregből, csökkentve ezzel a légcsapdák és az égési nyomok kockázatát.
- Karbantartás és javítás: Az állásidő minimalizálása és a termelés hatékonyságának növelése érdekében a szerszámot úgy kell megtervezni, hogy az könnyen karbantartható és javítható legyen.
A fröccsöntőszerszámok tervezése összetett folyamat, amely olyan területeken igényel szakértelmet, mint a gépészet, az anyagtudomány és a gyártás. Fontos, hogy jó hírű szerszámtervezővel dolgozzon együtt annak érdekében, hogy a szerszámot helyesen tervezzék meg, és az megfeleljen az Ön igényeinek.
CNC programozás:
A CNC (számítógépes számjegyvezérlésű) programozás a fröccsöntőformák gyártásának alapvető lépése. Miután a szerszámtervezés elkészült, a következő lépés a CNC-programozás. A következőkben a fröccsöntőszerszámok gyártásához szükséges CNC-programozás főbb lépései következnek:
- CAD-modell fordítása: A CAD-modellt lefordítják egy számítógépes gyártási (CAM) programba, amelyből létrehozzák a szerszám CNC-kódját.
- CNC-kódok létrehozása: A CNC-kódot a CAM-programban hozzák létre, amely utasításokat ad a CNC-gépnek arra vonatkozóan, hogyan kell mozgatni és vágni az öntőforma-alkatrészeket. A kód figyelembe veszi az öntőforma-alkatrészek anyagát és vastagságát, valamint a kívánt formákat és jellemzőket.
- Szerszámpálya létrehozása: A szerszámpálya létrehozása a CAM-programban történik, amely meghatározza azt az utat, amelyet a vágószerszám követni fog a formaelemek megmunkálásához. A szerszámpálya figyelembe veszi az öntőforma-alkatrészek formáit és jellemzőit, valamint a CNC-gép képességeit.
- Szimuláció: A CNC-kódot és a szerszámpályát a CAM-programban szimulálják annak biztosítása érdekében, hogy az öntőforma-alkatrészek megmunkálása helyesen és a megfelelő specifikációknak megfelelően történjen.
- CNC megmunkálás: A CNC-kódot betöltik a CNC-gépbe, amely ezután a kódot és a szerszámpályát használja az öntőforma-alkatrészek megmunkálásához.
A CNC-programozás kritikus lépés a fröccsöntőformák gyártási folyamatában, mivel ez határozza meg a formaalkatrészek pontosságát és minőségét. Fontos, hogy olyan CNC-programozóval dolgozzon együtt, aki rendelkezik tapasztalattal a fröccsöntőformák programozásában, hogy a CNC-kódot helyesen és a megfelelő specifikációknak megfelelően hozza létre. Ebben a lépésben a szerszám hűtőcsatornáit, a kilökő rendszert és más funkciókat is hozzáadnak a szerszámalkatrészekhez, hogy biztosítsák azok megfelelő működését.
Mold BOM lista beszerzése
A Mold BOM (Bill of Materials) lista egy átfogó lista a fröccsöntőforma gyártásához szükséges összes alkatrészről és anyagról. A következő elemeket tartalmazza:
- Acél az öntőforma alapjához és a mag/üreg betétekhez
- Forrócsatorna-alkatrészek
- Hűtőrendszer-alkatrészek, például vízvezetékek és hűtőblokkok
- Kilövőrendszer-alkatrészek, például kilövőcsapok és hüvelyek
- Forráshúzó alkatrészek
- Fűtőszalagok és hőmérséklet-szabályozók
- Formakomponensek, például perselyek, vezetőcsapok és reteszelőberendezések
- Szerszámbetétek, mint például csúszkák és emelők
- Speciális termékek, például dátumbélyegzők és egyedi logók
A szerszám BOM-lista fontos eszköz a beszerzés és a gyártás szempontjából, mivel egyértelmű és részletes listát ad a szerszám előállításához szükséges alkatrészekről és anyagokról. Arra szolgál, hogy az összes szükséges alkatrész megrendelésre kerüljön és kéznél legyen, amikor a szerszámot legyártják.
Fontos, hogy a fröccsöntőforma alkatrészeinek beszerzésekor jó hírű beszállítóval dolgozzon együtt, mivel ezen alkatrészek minősége és megbízhatósága jelentős hatással lehet a fröccsöntési folyamat hatékonyságára és minőségére.
Formák durva megmunkálása:
A fröccsöntőforma durva megmunkálása a fröccsöntőforma acél alkatrészeinek kezdeti megmunkálását jelenti a forma alapformájának és méretének elérése érdekében. Ezt a lépést általában számítógépes numerikus vezérlésű (CNC) gépekkel végzik. A következőkben a fröccsöntőszerszámok durva megmunkálásának főbb lépései következnek:
- Acélválaszték: Az első lépés a formázott alkatrész kívánt tulajdonságai alapján a megfelelő acéltípus kiválasztása a szerszámhoz, például P20 vagy H13.
- Acélvágás: Az acélt CNC-gépen vágják a megfelelő méretre és alakra. Ez a lépés magában foglalhatja a hűtő- és kilövőrendszerekhez szükséges furatok fúrását és menetfúrását is.
- Acélprofilozás: Az acél alkatrészeket ezután megmunkálják, hogy elérjék a szerszám alapformáját, beleértve a magot és az üregbetéteket.
- Acélvizsgálat: A megmunkált alkatrészeket ezután ellenőrzik, hogy megfelelnek-e az előírt tűréshatároknak és előírásoknak.
- Acéltisztítás: A megmunkált alkatrészeket megtisztítjuk, és a durva élek és törmelékek eltávolítása érdekében letisztítjuk.
A durva megmunkálás a fröccsöntési folyamat fontos lépése, mivel megalapozza az ezt követő végső, nagy pontosságú megmunkálási és polírozási lépéseket. Fontos, hogy a durva megmunkálás pontosan és a megfelelő specifikációknak megfelelően történjen, hogy a szerszám megfelelően működjön és a kívánt minőségű alkatrészeket állítson elő.
Formacél hőkezelés:
A szerszámacél hőkezelése a fröccsöntőszerszám acél alkatrészeinek melegítése és hűtése a mechanikai tulajdonságok és a méretstabilitás javítása érdekében. A hőkezelés célja az acél edzése, a maradó feszültségek enyhítése, valamint a kopásállóság és a szívósság javítása. Ez kifejezetten a fröccsöntőszerszámok keményített acéljára vonatkozik, ha a fröccsöntőszerszámok készítéséhez előkeményített acélt használnak, akkor nincs szükség erre a hőkezelési munkára. A következők a szerszámacél hőkezelésének fő lépései:
- Izzítás: Az acélalkatrészeket egy meghatározott hőmérsékletre, általában 800-900 °C közé melegítik, majd lassan lehűtik, hogy a belső feszültségeket enyhítsék és javítsák az acél megmunkálhatóságát.
- Keményedés: Az acél alkatrészeket magas hőmérsékletre, jellemzően a kritikus hőmérséklet fölé hevítik, majd gyorsan lehűtik, általában olajban vagy vízben történő oltással. Ez a folyamat megkeményíti az acélt és javítja a kopásállóságát.
- Edzés: Az edzés után az acél alkatrészeket alacsonyabb hőmérsékleten, meghatározott ideig történő melegítéssel edzik, hogy javítsák az acél szívósságát és méretstabilitását.
A hőkezelési folyamat kritikus fontosságú annak biztosítása szempontjából, hogy a fröccsöntőszerszám acél alkatrészei a kívánt mechanikai tulajdonságokkal és méretstabilitással rendelkezzenek, amelyek elengedhetetlenek a kiváló minőségű öntött alkatrészek előállításához. Fontos, hogy olyan hőkezelővel dolgozzon együtt, aki rendelkezik tapasztalattal a szerszámacélok kezelésében, hogy a hőkezelési folyamatot helyesen és a megfelelő előírásoknak megfelelően végezzék el.
Szerszámüreg és mag finom megmunkálása:
A formaüreg és a mag finom megmunkálása a formaüreg és a magbetétek belső felületeinek pontos megmunkálása a forma végső alakjának és méretének elérése érdekében. Ezt a lépést jellemzően számítógépes numerikus vezérlésű (CNC) gépekkel végzik, nagy pontossággal és precizitással. A következőkben a formaüreg és a mag finom megmunkálásának főbb lépései következnek:
- Felület előkészítése: A szerszámüreg és a magbetétek felületét megtisztítják és polírozzák, hogy eltávolítsák a maradék törmeléket vagy érdességet.
- Felületi megmunkálás: A szerszám üregének és a magbetéteknek a belső felületeit CNC-gépekkel megmunkálják, hogy elérjék a szerszám végső alakját és méretét. Ez magában foglalja az öntött alkatrész bonyolult részleteinek és jellemzőinek, például a szövegnek, logóknak és alulvágásoknak a létrehozását.
- Felületi ellenőrzés: A megmunkált felületeket ellenőrzik, hogy azok megfeleljenek az előírt tűréshatároknak és előírásoknak.
- Felületpolírozás: Az öntőforma üreg és a magbetétek belső felületét magas színvonalúra polírozzák, hogy javítsák az öntött alkatrészek felületi minőségét és csökkentsék a hibák kockázatát.
A finom megmunkálás a fröccsöntési folyamat kritikus lépése, mivel ez határozza meg a fröccsöntött alkatrészek minőségét és pontosságát. Fontos, hogy olyan megmunkálóval dolgozzon együtt, aki rendelkezik tapasztalattal a szerszámüreg és a mag finom megmunkálásában, hogy a megmunkálást helyesen és a megfelelő specifikációknak megfelelően végezzük el. Ebben a lépésben kerül sor a szerszám kilökő rendszerének, hűtőcsatornáinak és egyéb jellemzőinek hozzáadására is a szerszám megfelelő működésének biztosítása érdekében.
EDM megmunkálás:
Az EDM (elektromos kisüléses megmunkálás) egy olyan eljárás, amelyet a fém alkatrészek bonyolult és rendkívül pontos formáinak kialakítására használnak, beleértve a fröccsöntőformában lévő alkatrészeket is. Az eljárás elektromos szikrák segítségével távolítja el az anyagot a szerszám felületéről, létrehozva a kívánt formát. Az EDM megmunkálás főbb lépései a következők:
- Felület előkészítése: A megmunkálandó alkatrész felületét megtisztítják és polírozzák, hogy eltávolítsák a maradék törmeléket vagy érdességet.
- EDM beállítás: A szikraforgácsoló gépet a megfelelő paraméterekkel állítják be, beleértve a szikrahézagot, az impulzus időtartamát és az elektróda anyagát, a szerszámalkatrész anyaga és alakja alapján.
- Szikraerózió: Az EDM gép elektromos szikrákat termel, amelyek eltávolítják az anyagot a formadarabról, létrehozva a kívánt formát. Ez a folyamat fokozatosan történik, a szikraforgácsoló gép fokozatosan erodálja az anyagot, amíg el nem éri a végső formát.
- Felületi ellenőrzés: A megmunkált felületet ellenőrzik, hogy az megfeleljen az előírt tűréshatároknak és előírásoknak.
Az EDM megmunkálást gyakran használják olyan összetett formájú vagy apró, bonyolult részletekkel rendelkező szerszámalkatrészekhez, amelyeket más megmunkálási eljárásokkal nehéz elérni. A fröccsöntőszerszámok megfelelő működéséhez elengedhetetlen éles élek és sarkok előállítására is használják.
Az eljárás rendkívül precíz és pontos, így ideális a kiváló minőségű öntött alkatrészek gyártásához. Fontos, hogy olyan EDM-szolgáltatóval dolgozzon együtt, amely rendelkezik tapasztalattal a fröccsöntőformák EDM megmunkálásában, hogy a folyamatot helyesen és a megfelelő specifikációknak megfelelően végezzük el.
Szerszámfelület polírozása:
Fröccsöntőforma polírozás a fröccsöntési forma gyártási folyamatának utolsó lépése. Ez magában foglalja az öntőforma-alkatrészek felületének kisimítását, hogy a késztermék felülete sima és egyenletes legyen. A következőkben a fröccsöntőszerszámok polírozásának főbb lépései következnek:

műanyag formák polírozása
- Felület előkészítése: Az öntőforma-alkatrészek felületét megtisztítják és előkészítik a polírozáshoz. A megmaradt érdes foltokat vagy megmunkálási nyomokat eltávolítjuk, hogy a polírozáshoz sima felületet biztosítsunk.
- Durva polírozás: A polírozás első lépése a durva polírozás, amelynek során eltávolítjuk az öntőforma-alkatrészek felületén található nagyobb hibákat. Ezt a lépést általában durva szemcsés csiszolóanyaggal, például csiszolópapírral vagy csiszolókefével végzik.
- Finompolírozás: A finompolírozás a következő lépés, amely a szerszámalkatrészek felületének finomabbra simítását jelenti. Ezt a lépést finomabb szemcseméretű csiszolóanyaggal, például finomabb csiszolópapírral vagy csiszolókefével végzik.
- Polírozás: A polírozás utolsó lépése a polírozás, amely magában foglalja a polírozó kerék és a polírozószer használatát, hogy magas fényű felületet érjen el a formadarabokon.
- Ellenőrzés: A polírozás után az öntőforma-alkatrészeket alaposan megvizsgálják, hogy a felületük sima és egyenletes legyen, karcolások, repedések és egyéb hibák nélkül.
A fröccsöntőformák polírozása azért fontos, mert befolyásolja a végtermék minőségét. Egy jól polírozott szerszám sima és egyenletes felületű terméket eredményez, ami fontos a termék funkcionalitása és esztétikája szempontjából. Fontos, hogy tapasztalt szerszámpolírozóval dolgozzon együtt, hogy a szerszámalkatrészek polírozása a megfelelő specifikációknak és a kívánt minőségi szintnek megfelelően történjen.
Szerszám szerelvény
A szerszámszerelés a fröccsöntés területén belül egy speciális munka, amely a fröccsöntőszerszámok összeszerelését, telepítését és tesztelését foglalja magában. A szerszámmesterek felelősek annak biztosításáért, hogy a szerszám alkatrészei megfelelően legyenek összeszerelve és megfelelően működjenek, valamint hogy a szerszám a kívánt minőségi és teljesítménynormáknak megfelelő alkatrészeket állítson elő. A szerszámkészítők néhány fő feladata a következő:
- Az öntőforma alkatrészeinek összeszerelése: A szerszámmesterek felelősek a fröccsöntőszerszám különböző alkatrészeinek összeszereléséért, beleértve az üreg és a mag alkatrészeit, a kifutórendszert és a segédalkatrészeket.
- A szerszám felszerelése a szerszámszerelő gépre: Ha nincs szerszámszerelő gép, akkor kézzel kell felszerelni a szerszámot, ez a legtöbb vállalatnál így van.
- A penész tesztelése: A szerszámmester felelős a szerszám teszteléséért annak biztosítása érdekében, hogy az a kívánt minőségi és teljesítménynormáknak megfelelő alkatrészeket állítson elő. Ez magában foglalja az alkatrészek ellenőrzését az esetleges hibák, például a vetemedés, zsugorodás vagy más minőségi problémák szempontjából.
- A forma beállítása: Ha a tesztelési fázis során bármilyen problémát találnak, a moldmaster felelős a szükséges beállítások elvégzéséért a szerszámon, hogy az a kívánt specifikációknak megfelelő alkatrészeket állítson elő.
- Hibaelhárítás: A szerszámkészítőnek képesnek kell lennie a szerszámillesztési folyamat során felmerülő problémák azonosítására és elhárítására.
A szerszámszerelői munkák a műszaki ismeretek, a kézügyesség és a részletekre való odafigyelés kombinációját igénylik. A szerszámkészítőknek képesnek kell lenniük a szerszámok és gépek széles skálájával dolgozni, valamint érteniük kell a fröccsöntés összetett folyamatait. Fontos, hogy a szerszámszerelők jól értsék a fröccsöntési folyamatot, valamint tapasztalatot szerezzenek a különböző típusú szerszámokkal és anyagokkal való munkavégzésben.
Első fröccsöntési próba vagy forgatás:
A fröccsöntési próbafelvétel a fröccsöntési öntőforma tesztelésének folyamatára utal, amelynek célja egy mintaalkatrész előállítása a fröccsöntési folyamat segítségével. Ez a folyamat a fröccsöntési folyamat kritikus lépése, mivel lehetővé teszi a gyártó számára, hogy értékelje a szerszám teljesítményét, és elvégezze a szükséges módosításokat, mielőtt nagy mennyiségű alkatrészt gyártana.
A fröccsöntési próbafelvételi folyamat jellemzően a következő lépésekből áll:
- Előkészítés: A szerszámot a fröccsöntőgépre szerelik, és a gépet beállítják a lövésre. A tartály megtelik a műanyag gyantával.
- Olvadékhőmérséklet-szabályozás: Az olvadékhőmérséklet szabályozása biztosítja, hogy a műanyag gyanta a megfelelő hőmérsékletre melegedjen a kiváló minőségű alkatrészek előállításához.
- Injekció: Az olvadt műanyagot nagy nyomás alatt fecskendezik a formába. A nyomást addig tartják fenn, amíg a szerszám meg nem telik a műanyag gyantával.
- Hűtés: Az öntőforma lehűtése a műanyag gyanta megszilárdulásához és az alkatrész kialakításához. A hűtési időt a felhasznált műanyag gyanta típusa, valamint a gyártandó alkatrész mérete és alakja határozza meg.
- Kidobás: Miután az alkatrész megszilárdult, eltávolítják a szerszámból. A kilökőcsapok segítségével az alkatrész kinyomható a szerszámból.
- Ellenőrzés: A szerszámból előállított alkatrészt alaposan ellenőrzik, hogy az megfeleljen a kívánt specifikációknak és minőségi előírásoknak.
- Beállítások: Ha szükséges, a formázási folyamatot módosítani lehet a szerszám teljesítményének és a gyártott alkatrészek minőségének javítása érdekében.
A fröccsöntési próbafelvételi eljárás fontos lépés a fröccsöntési folyamatban, mivel lehetővé teszi a gyártó számára, hogy értékelje a szerszám teljesítményét, és elvégezze a szükséges módosításokat, mielőtt nagy mennyiségű alkatrészt gyártana. Ez a folyamat segít biztosítani, hogy a szerszám a kívánt specifikációknak megfelelő minőségű alkatrészeket állítson elő.
Mold csomagolás és készen áll a gyártásra:
Miután a penész teljesen elkészült az öntőforma készítője által, a következő lépés a tömeges gyártás. A szerszámcsomagolás és a gyártás előkészítése a fröccsöntési folyamat utolsó lépése, mielőtt a tömeggyártás megkezdődhet. Ez a lépés a következő feladatokat foglalja magában:
- Tisztítás és karbantartás: A penész alaposan megtisztítják és ellenőrzik, hogy a penészen ne legyenek törmelékek, szennyeződések vagy sérülések.
- Csomagolás és tárolás: A formát gondosan csomagolják és biztonságos helyen tárolják, hogy megelőzzék a sérüléseket és biztosítsák, hogy szükség esetén használatra kész legyen.
- Tesztelés és beállítás: Az öntőformát tesztelik az esetleges problémák, például szivárgás, rossz töltés vagy nem megfelelő alkatrész-kidobás szempontjából, és elvégzik a szükséges beállításokat annak érdekében, hogy a forma megfelelően működjön.
- Gyártási beállítások: A szerszámot beépítik a fröccsöntőgépbe, és az összes szükséges beállítást, például a hőmérsékletet, a nyomást és a fröccsöntési sebességet úgy állítják be, hogy megfeleljen az adott gyártási követelményeknek.
- A gyártás megkezdése: Az alkatrészek első tételének gyártása, és a folyamat ellenőrzése annak biztosítása érdekében, hogy az alkatrészek megfeleljenek az előírt specifikációknak és minőségi előírásoknak. A gyártási folyamat optimalizálása és az egyenletes minőség biztosítása érdekében minden szükséges kiigazítást elvégeznek.
Összességében a szerszám gyártásra való előkészítése a fröccsöntési folyamat fontos lépése, amely hozzájárul a gyártás sikerének és hatékonyságának biztosításához.
A fenti információk a fröccsöntőforma készítésére vonatkozó eljárások, talán van néhány kis dolog, ami hiányzik, de a legtöbb dolog fent van, mint láthatja, hogy a fröccsöntőforma készítése nem könnyű eset, ha van egy fröccsöntőforma projektje a fogantyúban, meg kell találnia egy professzionális fröccsöntőforma-gyártót, hogy kiszolgálja Önt, ez biztosítja, hogy a projektje sikeresen fut.
Sincere Tech egy profi Kína penész egyedi fröccsöntőformák gyártására szakosodott gyár. Tapasztalattal és szakértelemmel rendelkeznek a különböző iparágak és alkalmazások számára készült kiváló minőségű fröccsöntőformák tervezésében, fejlesztésében és gyártásában.
Számos szolgáltatást nyújtanak, beleértve a szerszámtervezést, a prototípusgyártást, a szerszámgyártást és a szerszám utáni feldolgozást, hogy ügyfeleik a lehető legjobb eredményt kapják. A minőségre, pontosságra és az ügyfelek elégedettségére összpontosítva az Sincere Tech megbízható és megbízható partner az Ön fröccsöntési igényeihez. Vegye fel velünk a kapcsolatot, hogy e árat kapjon a projektjéhez most.