Qu'est-ce qu'un rapport d'analyse de flux de moule ?
Analyse de l'écoulement des moules (MFA) est un outil de simulation utilisé pour prédire et optimiser l'écoulement de la résine plastique dans un moule pendant le processus de moulage par injection. La simulation prend en compte les propriétés de la résine et la géométrie du moule, et prédit le comportement du plastique lorsqu'il remplit le moule et refroidit.
Rapport d'analyse de l'écoulement du moule peut aider à identifier et à résoudre les problèmes potentiels liés au processus de moulage par injection, tels que les injections courtes, les déformations, les lignes de soudure, les pièges à air, les marques d'affaissement, etc. Rapport d'analyse de l'écoulement du moule peut également être utilisé pour optimiser le processus de moulage par injection en identifiant le meilleur emplacement pour les portes et les canaux, en déterminant la vitesse d'injection optimale et en prédisant le meilleur temps et la meilleure température de refroidissement. Cela peut aider à réduire le temps de cycle, à améliorer la qualité des pièces et à augmenter l'efficacité de la production.
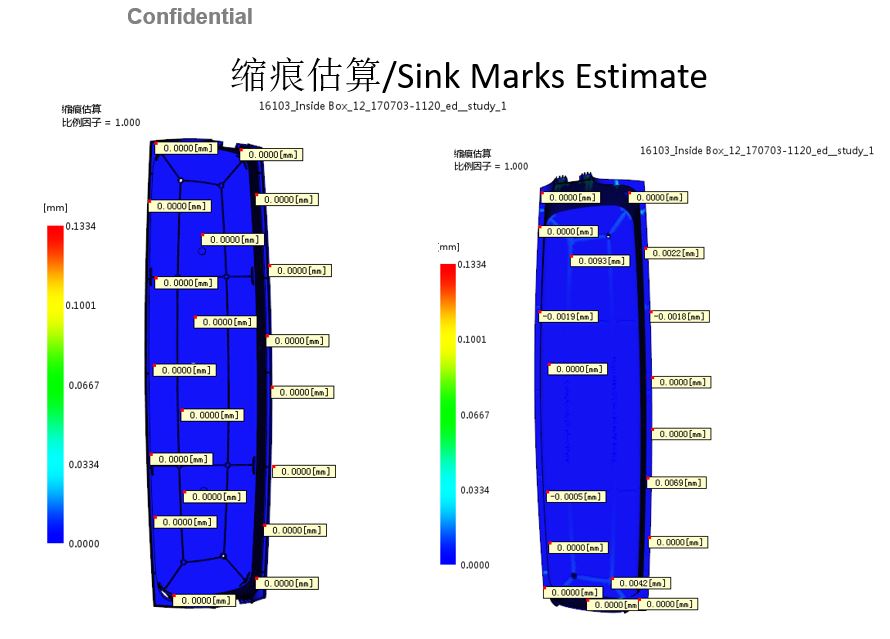
Rapport d'analyse de l'écoulement du moule
Résumé des résultats de l'analyse de l'écoulement des moules
Une fois que nous avons terminé la conception du moule, avant de commencer la fabrication du moule, pour nous assurer que tout ne pose aucun problème, nous devons effectuer les opérations suivantes : analyse du flux des moules pour vérifier les problèmes potentiels, c'est un moyen de sécurité pour éviter les erreurs, en particulier pour les gros moules. Vous trouverez ci-dessous quelques points que nous devons vérifier lors de la rédaction du rapport d'analyse du flux de moule.
Temps de remplissage du moule – Le temps de remplissage est le temps nécessaire pour remplir la cavité de la pièce. Le tracé du temps de remplissage fournit également une animation du remplissage de la cavité du moule. Le temps de remplissage peut également être contrôlé pendant l'analyse pour résoudre les problèmes de qualité tels que les contraintes de cisaillement élevées.
Pression d'injection – Une machine de moulage par injection standard est capable de pressuriser le flux de matière fondue à 20 000 psi (pression manométrique hydraulique de 2 000 psi). Une partie de la pression est utilisée pour pousser le plastique à travers le système de canaux, une autre partie de la pression est utilisée pour pousser le plastique dans le cavité du moule, et une partie de la pression est utilisée pour « emballer » la pièce après son remplissage. Si la pièce et le système de canal nécessitent plus de pression que ce que la machine est capable de faire, la pièce sera alors un coup court ou aura une pression profonde marques d'affaissement.
Lignes de soudure Défauts – Les lignes de soudure se forment lorsque deux fronts d’écoulement se rencontrent et se « soudent » ensemble. Les lignes de soudure sont généralement une ligne visible sur la pièce et peuvent constituer un problème d’apparence. Les lignes de soudure peuvent également réduire la résistance de la pièce de 10% à 20%, créant potentiellement un problème structurel en fonction de leur emplacement. Si l’analyse de l’écoulement du moule n’est pas utilisée pour résoudre ces problèmes avant la construction de l’outil, le mouleur sera obligé de : augmenter la pression d’injection, augmenter la température de fusion, augmenter la température du moule, agrandir les évents, changer l’emplacement du point d’injection et/ou modifier l’épaisseur de la pièce. Toutes ces « solutions » prennent du temps et de l’argent à mettre en œuvre et/ou augmentent le coût de la pièce.
Pièges à air Défauts – Des pièges à air se forment lorsque le plastique fondu emprisonne de l’air dans la cavité de la pièce pendant qu’il se remplit. Si ces pièges à air ne sont pas ventilés, ils peuvent entraîner des problèmes de qualité tels que des marques de brûlure, des coups courts, des lignes de soudure prononcées et un remplissage incomplet. Nos tracés de pièges à air permettent au fabricant d’outils de savoir exactement où les évents doivent être placés lors de la fabrication de l’outil. Les pièges à air qui se trouvent dans des endroits difficiles à évacuer peuvent être déplacés vers de meilleurs emplacements en déplaçant la porte. Effectuer ce travail avant la fabrication de l’outil peut permettre d’économiser sur la quantité de débogage et de modifications de moule nécessaires.
Qualité – La définition d’une pièce moulée de qualité ne se limite pas à un remplissage complet de la pièce. Une pièce moulée de qualité doit également être exempte de dégradation du matériau et avoir une faible contrainte de moulage. Le graphique de qualité montre la gravité et les zones qui souffrent de problèmes de qualité. Les problèmes détectés comprennent une contrainte de cisaillement et un taux de cisaillement excessifs et des zones difficiles à remplir. Des suggestions telles que des ajustements d’épaisseur, des changements de conditions de traitement et des ajustements de temps de remplissage peuvent être essayés pour éliminer les problèmes de qualité.
Traces d'affaissement Défauts – Les retassures sont des dépressions localisées à la surface des pièces moulées par injection, causées par un rétrécissement non uniforme du plastique pendant le refroidissement. Dans les pièces critiques sur le plan esthétique, elles peuvent constituer un problème sérieux. Les retassures sont souvent une surprise lorsque l'outil est terminé. Si les retassures sont désagréables pour le client, le mouleur est souvent chargé de les « éliminer ». Cela signifie généralement faire fonctionner la machine de moulage aux extrémités de la fenêtre de processus, ce qui peut allonger les temps de cycle et augmenter la quantité de contraintes moulées et de dégradation du matériau.
Temps de refroidissement – Il a été démontré que le temps de refroidissement représente en moyenne environ 50% du cycle de moulage. Si le matériau utilisé est une résine de base, le coût de moulage dépasse de loin le coût du matériau. Dans ce cas, une réduction du temps de refroidissement entraîne une réduction importante du coût de la pièce. Notre analyse du refroidissement peut réduire votre cycle de refroidissement et optimiser votre système de refroidissement en éliminant les points chauds et les déformations.
MFA est un outil puissant qui peut aider à améliorer l'efficacité et la qualité du processus de moulage par injection, en simulant le comportement de la résine plastique lorsqu'elle s'écoule dans le moule et se refroidit. Il permet d'identifier les problèmes potentiels et d'optimiser le processus pour minimiser les défauts et améliorer la qualité du produit final.
Nous effectuons des analyses de flux de moule pour votre projet
Si vous avez un projet qui présente de nombreux soucis, veuillez nous contacter, nous vérifierons tous les dessins de vos pièces et réaliserons Rapport DFM et flux de moule analyse pour vous et résume tous les problèmes possibles dans la fiche technique et vous est renvoyée.