Moulage par injection de plastique est un procédé de fabrication très répandu. Dans le monde d'aujourd'hui, cette méthode est devenue essentielle pour la production de pièces plastiques à grande échelle. Sa popularité est due à son fonctionnement rapide, précis et très efficace.
Le moulage par injection de plastique vous permet généralement de créer d'innombrables articles en plastique. La plupart de ces pièces en plastique font partie de votre quotidien, qu'il s'agisse du moulage de votre smartphone ou de la poignée de votre brosse à dents.
Moulage par injection de plastique vous permet de fabriquer des milliers, voire des millions, de pièces identiques. Bien entendu, ces pièces en plastique sont assorties de tolérances serrées pouvant aller jusqu'à 0,01 mm. Ce niveau de précision permet de créer des conceptions et des produits précis qui rendent le produit efficace et esthétique. Les produits moulés par injection sont largement utilisés dans les secteurs de l'automobile, des biens de consommation et de l'électronique.
Moulage par injection de plastique comporte plusieurs étapes clés. Chacune d'entre elles est cruciale. Dans cet article, nous allons nous pencher sur ces étapes afin que vous puissiez voir comment les produits passent du plastique brut à des pièces prêtes à l'emploi. En outre, vous découvrirez les services de moulage par injection de plastique proposés dans une usine. Cet article sera un guide complet, alors commençons.
Qu'est-ce que le moulage par injection de matières plastiques ?
Moulage par injection est une méthode de fabrication courante. Le terme se divise en "injection" et "moulage". Comme son nom l'indique, ce procédé consiste à injecter un matériau dans un moule. Le moulage par injection de plastique fait référence à l'utilisation de plastique.
Cette méthode permet de façonner des pièces de différentes conceptions en injectant le matériau fondu dans le moule. moule d'injection plastique. Il est largement utilisé pour fabriquer des pièces en plastique rapidement et avec précision. Une fois le moule prêt, vous pouvez créer des centaines ou des millions de pièces en plastique. Le processus est très efficace et offre une qualité constante. C'est pourquoi les gens préfèrent cette méthode pour créer des formes complexes et des détails précis.
Cette procédure ne se limite pas aux pièces de jouets ou aux conteneurs en plastique. Le moulage par injection de plastique est essentiel pour de nombreuses industries. Prenons l'exemple de l'industrie automobile. Presque tous les véhicules en circulation aujourd'hui comportent des composants moulés par injection, comme les tableaux de bord.
Les produits électroniques tels que les ordinateurs portables, les smartphones et autres dépendent largement de ce processus. La plupart de leurs composants internes, boîtiers et joints sont moulés par injection.
Dans l'industrie médicale, la précision est essentielle, et c'est précisément ce que permet le moulage par injection. Ce procédé permet d'obtenir des tolérances précises pour les outils chirurgicaux, les seringues et d'autres articles médicaux.
Il y a ensuite l'industrie des biens de consommation. Le moulage par injection permet principalement de fabriquer nos articles de tous les jours. Des exemples typiques sont les ustensiles de cuisine, les pots en plastique, les bouteilles, les meubles, les récipients alimentaires, etc.

Avantages du moulage par injection plastique par rapport à d'autres méthodes
Il existe différents types de méthodes de mise en forme du plastique. Les plus courantes sont le moulage par extrusion, le moulage par compression, le moulage par soufflage et le moulage par rotation. Quels sont les avantages que vous pouvez tirer de ces méthodes ? moulage par injection de plastique méthode ?
Précision et complexité
L'un des avantages du moulage par injection de matières plastiques est sa précision et sa complexité. Le moulage par extrusion ou par compression concerne généralement des formes plus simples. Ces méthodes ne conviennent donc pas aux formes complexes.
Moulage par injection de plastiqueEn revanche, elle permet de traiter des géométries plus complexes avec la structure du moule correspondante. Cette méthode permet également de travailler avec des parois minces, des tolérances serrées et des détails petits et fins. Vous pouvez obtenir des produits en plastique de la plus haute qualité par rapport à d'autres méthodes.
Vitesse de production élevée
Le temps est précieux, surtout dans l'industrie manufacturière. Moulage par injection de plastique est conçu pour la vitesse. Une fois le moule d'injection mis en place, il peut produire des pièces rapidement, bien plus vite que le moulage traditionnel ou le moulage par soufflage. Cette rapidité fait du procédé de moulage par injection de plastique une option de choix pour la production de gros volumes. C'est l'une des méthodes les plus rapides qui soient.
Vous serez surpris d'apprendre que le moulage par injection de plastique permet de fabriquer des milliers de pièces en plastique en une heure. Cette méthode permet d'économiser à la fois du temps et de l'argent.
Un minimum de déchets
Moulage par injection de plastique est efficace dans l'utilisation des matériaux. Si vous pouvez fabriquer le moule correctement et injecter le plastique avec précision, vous pouvez minimiser les excès du moulage par extrusion de plastique, où le flux continu de matériaux conduit souvent à des déchets.
Dans le cas du moulage par injection de plastique, les plastiques supplémentaires peuvent être réutilisés, ce qui réduit les coûts de moulage par injection et contribue à la protection de l'environnement.
Qualité constante
Le moulage par injection plastique garantit également l'uniformité des produits. L'un d'entre eux moule d'injection plastique peut produire des millions de produits en plastique ayant la même forme et les mêmes propriétés. Il est difficile d'obtenir une uniformité exacte avec la compression et le moulage par soufflage, mais vous pouvez le faire avec précision avec le moulage par injection. Il permet de réduire les coûts et de répondre à la demande de produits de haute qualité.
Choix de matériaux polyvalents
Il existe de nombreux types de plastiques qui sont largement utilisés dans de nombreuses applications. Ils ne sont pas tous identiques et chaque type a une application unique. Le moulage par injection peut facilement s'adapter à une large gamme de matériaux. Cette flexibilité vous permet de répondre à un besoin spécifique. Cela signifie qu'il est possible de répondre à des exigences précises en matière de résistance, de durabilité et de flexibilité.
Finition supérieure
Le moulage par injection permet de créer des pièces aux surfaces lisses et à la finition nette. Cette méthode élimine ou réduit la nécessité d'un post-traitement. Le rotomoulage, en revanche, est assez délicat et nécessite des finitions supplémentaires.

Qu'est-ce qu'une machine de moulage par injection ?
Une machine de moulage par injection de plastique est un équipement simple. Elle comporte plusieurs composants essentiels qui fonctionnent ensemble pour produire des pièces en plastique. En général, une machine de moulage par injection de plastique se compose de trois unités centrales. Chaque élément joue un rôle crucial dans le processus de moulage par injection de plastique.
Unité de serrage
L'unité de fermeture maintient fermement le moule en place pendant le processus d'injection. Elle agit comme une poignée pour que le moule ne glisse pas, ce qui vous permet de le modifier en fonction de la conception du produit final.
Lorsque la machine démarre, l'unité de fermeture ferme les deux moitiés du moule. Elle utilise une pression élevée, principalement hydraulique, pour empêcher le plastique de fuir pendant l'injection.
Une fois la pièce refroidie, l'unité de fermeture ouvre le moule pour libérer le produit fini. Sans cette unité, le processus serait désordonné.
Unité d'injection
L'unité d'injection, quant à elle, est le cœur de la machine. Elle fait fondre les granulés de plastique et les injecte dans le moule. L'unité d'injection dispose d'une trémie qui alimente le plastique dans un tonneau chauffé. Le matériau est fondu à l'intérieur du tonneau jusqu'à ce qu'il atteigne un état liquide. Ensuite, une vis ou un piston pousse le plastique fondu dans le moule.
Unité de contrôle
Il convient de noter que l'ensemble de ce processus doit être contrôlé de manière appropriée. Dans le cas contraire, le produit final risque d'être désordonné. Par exemple, le contrôle de la température est essentiel dans ce processus. Vous devez régler la température au bon niveau pour que votre produit final ne présente pas de défauts. D'autre part, le temps d'injection, le temps d'éjection et la force de poussée doivent également être contrôlés de manière adéquate.
Qu'est-ce qu'un moule à injection ?
Comme indiqué dans la section précédente, l'unité de fermeture contient généralement le moule d'injection. Le moule d'injection fait partie de l'unité de fermeture et donne au plastique fondu des formes spécifiques.
Les moules à injection sont généralement fabriqués en acier à outils. Divers aciers à outils peuvent être utilisés pour fabriquer des moules à injection. On peut citer le P-20 28-30 RC, l'acier à outils prétrempé S-7 56 RC, le H-13 et le 420. Ces aciers à outils sont solides et durables, et le matériau doit être suffisamment résistant pour supporter des millions de produits en plastique.
Un moule à injection comprend deux parties essentielles : la cavité et le noyau. La cavité est l'espace creux que le plastique occupe. Elle détermine la forme extérieure du composant. Le noyau, quant à lui, détermine les détails intérieurs. Ensemble, ils créent une pièce complète.
Vous pouvez vous rendre compte de l'importance d'un moule de haute qualité pour la fabrication de pièces plastiques moulées par injection. La qualité du moule d'injection détermine également la qualité des pièces finales. Par conséquent, vous devez d'abord vous assurer de la qualité du moule d'injection.
Un moule bien conçu produit moins de défauts et réduit les délais et les coûts de production. Une mauvaise conception peut entraîner des déformations et une qualité irrégulière. Il est donc judicieux de demander l'aide d'un professionnel lors de la conception de votre premier moule d'injection.

Comment fonctionne le moulage par injection ?
Vous avez déjà suivi une étude complète sur le moulage par injection. Vous connaissez également les différents composants d'une machine de moulage par injection. Dans cette section, vous apprendrez comment fonctionne le moulage par injection.
Serrage
La première étape du processus de moulage par injection est le serrage. Il s'agit de réunir les deux moitiés du moule. Il s'agit d'une étape cruciale. Si le moule n'est pas fermement serré, du plastique fondu peut s'échapper, ce qui peut entraîner des défauts dans vos pièces finales.
L'unité de fermeture maintient les moitiés du moule ensemble avec une force significative. La force ou la pression doit être suffisante pour résister à la pression du matériau injecté. Si elle est trop faible, le moule s'ouvrira pendant l'injection et provoquera un désordre. Une force trop importante peut endommager le moule.
Alors, comment déterminer la force de serrage correcte ? Prenez en compte des aspects tels que la taille de la pièce et le plastique utilisé. Par exemple, les pièces plus grandes nécessitent une force plus importante. L'objectif est d'obtenir un ajustement serré sans en faire trop. Une fois le moule fermement fermé, nous passons à l'étape suivante.
Injection
C'est à ce stade que la matière plastique est introduite dans la machine de moulage par injection. Le plastique brut, généralement sous forme de granulés, est chauffé jusqu'à ce qu'il fonde en une substance épaisse et gluante.
Il s'agit de verser du sirop dans un moule. Le plastique fondu est versé dans la cavité du moule sous haute pression, en veillant à ce qu'il en remplisse tous les coins et recoins. Si la pression est trop faible, le moule ne peut pas se remplir. Il est important de noter qu'une pression inadéquate peut entraîner des portions faibles ou incomplètes.
La vitesse est également essentielle lors de l'injection. Plus le matériau est injecté rapidement, moins il a le temps de refroidir avant de remplir le moule. Mais il y a un problème. La rapidité peut créer des turbulences, qui sont la cause principale de quelques défauts. Il faut donc équilibrer soigneusement la vitesse et la pression.
Logement
La phase de logement est également cruciale dans la méthode de moulage par injection de plastique. Comme vous le savez, vous devez maintenir une pression appropriée lors du remplissage du moule. Lorsque le plastique est injecté, il ne remplit pas toujours le moule de manière uniforme. Il peut y avoir des poches d'air ou des espaces vides. Pour éviter ce problème, vous devez maintenir une pression constante. De cette façon, vous pouvez vous assurer qu'il n'y a pas d'air emprisonné à l'intérieur. C'est là qu'intervient la phase d'habitation.
Le temps de séjour peut varier en fonction du matériau et de la conception de la pièce. Un temps de séjour trop court peut conduire à des pièces incomplètes, tandis qu'un temps de séjour trop long peut entraîner une perte de temps et d'énergie.
Refroidissement
Une fois la phase d'habitation terminée, il est temps de passer au refroidissement. C'est là que se produit la véritable transformation. Le plastique fondu commence à se solidifier en refroidissant. La phase de refroidissement doit être maintenue correctement pour fixer la forme de la pièce.
Cette étape est généralement plus longue que celle de l'habitation. Dans ce cas, la température de la moisissure joue généralement un rôle prépondérant. Vous pouvez utiliser un système de refroidissement à l'air ou à l'eau. Le moule peut se déformer s'il est trop froid, alors attention !
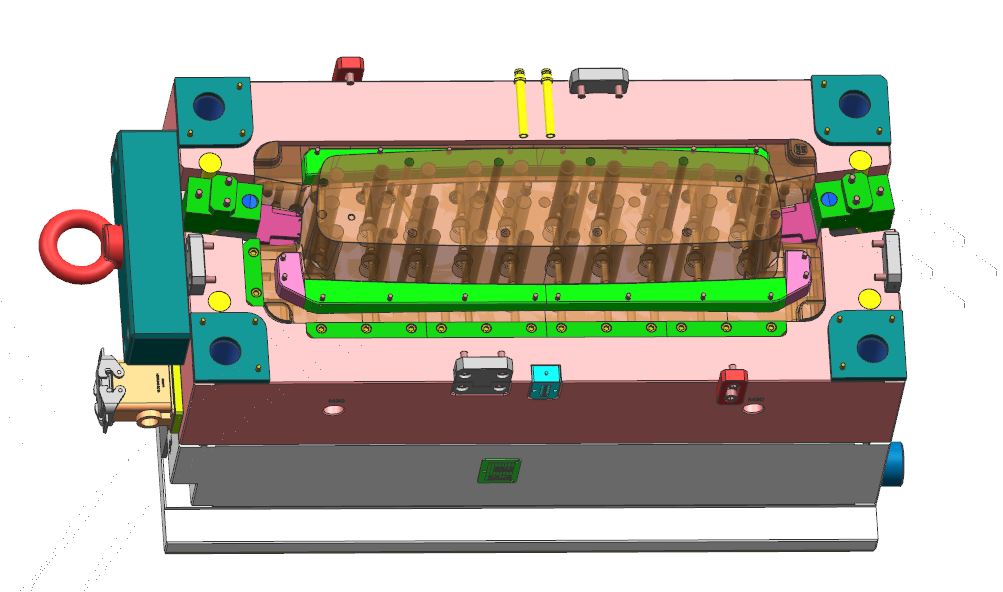
Ouverture des moules et enlèvement des produits
Après refroidissement, il est temps de libérer la pièce finale. En général, c'est la goupille d'éjection qui s'en charge. L'unité de fermeture relâche la pression, ce qui permet généralement aux deux moitiés de se séparer. Si vous ne le faites pas correctement, vous risquez d'endommager le moule ou la pièce finie.
Une fois le moule ouvert, vous pouvez le retirer à l'aide d'outils ou à la main. Une fois démoulée, la pièce est à nouveau inspectée. Elle peut subir d'autres traitements, tels que l'ébarbage ou la finition de surface.
Matériaux de moulage par injection de plastique
L'un des principaux avantages du moulage par injection de plastique est sa polyvalence. Vous pouvez généralement travailler avec différents matériaux de moulage par injection plastique dans la fabrication de moules par injection. Le choix du matériau approprié parmi cette liste variée dépend des besoins de votre projet. N'oubliez pas que chaque matériau a ses propres forces et faiblesses. Vous avez besoin de flexibilité ? Optez pour le PE ou le PP. Vous voulez de la robustesse ? Essayez l'ABS ou le PC.

Polyéthylène (PE)
Ce plastique est incroyablement léger et flexible. Il est également très résistant aux produits chimiques et à l'humidité, ce qui en fait un choix populaire pour les récipients et les bouteilles.
Le polyéthylène est l'une des matières plastiques les plus utilisées dans le monde en raison de son incroyable légèreté, de sa flexibilité et de sa rentabilité. Il est également très résistant aux produits chimiques et à l'humidité, ce qui en fait un choix populaire pour les conteneurs et les bouteilles.
Il existe différents types de matériaux PE, notamment Polyéthylène basse densité (LDPE), Polyéthylène haute densité (PEHD), et Polyéthylène à très haut poids moléculaire (UHMWPE)Chacun d'entre eux utilise des applications différentes mais très similaires.
Propriétés: Léger, souple, résistant à l'humidité et à de nombreux produits chimiques. Le PE est relativement mou mais présente une bonne résistance aux chocs. Il peut supporter des températures basses, mais sa résistance aux températures élevées est limitée.
Types de matériaux PE:
- PEBD: Connu pour sa flexibilité, il est couramment utilisé dans les applications de film telles que les sacs en plastique.
- PEHD: Plus solide et plus rigide, il est utilisé dans des articles tels que les bidons de lait, les bouteilles de détergent et les tuyaux.
- UHMWPE: Extrêmement robuste avec une excellente résistance à l'usure, souvent utilisé dans des applications industrielles, telles que les bandes transporteuses et les gilets pare-balles.
Applications: En raison de sa variété, le PE est utilisé dans toutes les industries pour les conteneurs, les tuyauteries et même les applications à forte usure. Dans l'industrie alimentaire, il est idéal pour les récipients et les emballages alimentaires en raison de sa résistance à l'humidité. Aller à Modélisation de l'injection de PE et Moulage par injection de PEHD pour en savoir plus sur ce matériau PE.
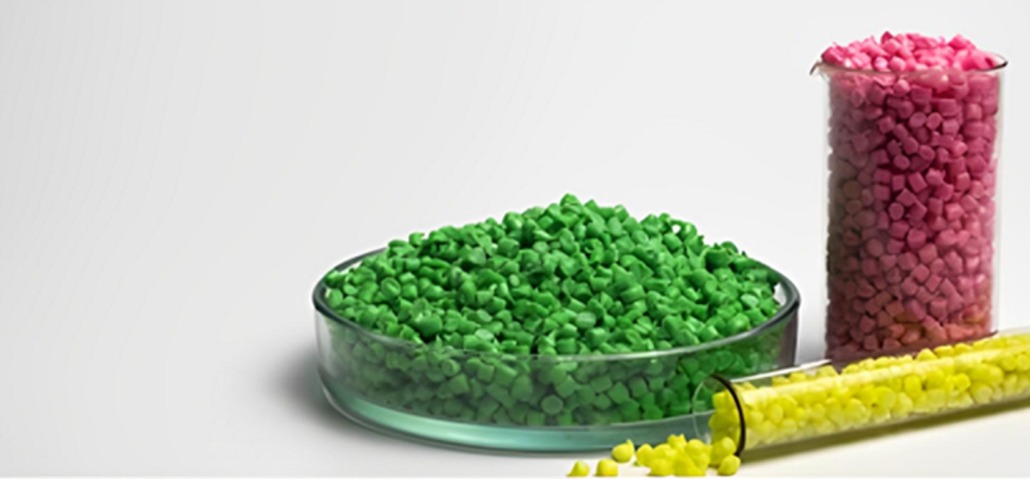
Polypropylène (PP)
Le polypropylène est un autre choix populaire. Il est disponible sous forme d'homopolymère et de copolymère, chaque variante convenant à des applications spécifiques.
Propriétés: Solide, durable, résistant à la fatigue et à la température. Le PP peut supporter des flexions répétitives, ce qui le rend approprié pour des applications telles que les charnières.
Avantages: Le PP offre une résistance chimique élevée et est léger, tout en étant plus solide que le PE. Il résiste également à l'absorption de l'humidité, ce qui en fait un matériau idéal pour les produits à longue durée de vie.
Applications:
- Automobile: Fréquemment utilisé dans les pièces automobiles telles que les pare-chocs, les tableaux de bord et les boîtiers de batterie.
- Biens de consommation: On le trouve dans les conteneurs réutilisables, les meubles, les textiles et les emballages. Sa résistance à la fatigue le rend utile pour les charnières des produits ménagers et des conteneurs de stockage.
- Médical: Stérilisable et résistant aux bactéries, le plastique PP est également utilisé pour les seringues et les flacons médicaux. Aller à moulage par injection de polypropylène page pour en savoir plus.

Acrylonitrile butadiène styrène (ABS)
L'ABS est un plastique utilisé pour le moulage par injection. Il est connu pour sa robustesse, ce qui le rend idéal pour les pièces qui doivent résister aux chocs. Il a une finition brillante et est donc souvent utilisé dans l'électronique et les jouets. L'ABS pourrait être votre meilleur choix si vous voulez un objet esthétique et durable.
Propriétés: L'ABS est robuste, résistant aux chocs et léger, avec une finition brillante. Il est également relativement abordable et allie solidité et attrait visuel.
Avantages: Connu pour son excellente résistance aux chocs, l'ABS est idéal pour les produits qui doivent résister à des manipulations brutales. L'ABS est également très facile à usiner et à peindre, ce qui lui confère une grande polyvalence esthétique et fonctionnelle.
Applications des produits en plastique ABS:
Électronique: Utilisé pour les boîtiers, les claviers et les boîtiers d'écran en raison de sa finition esthétique et de sa durabilité.
Automobile: Tableaux de bord, enjoliveurs et boîtiers de rétroviseurs.
Jouets et produits de consommation: Particulièrement populaire pour les jouets (tels que les blocs de construction) qui nécessitent une durabilité et une apparence agréable. Aller à Moulage par injection d'ABS et Qu'est-ce que le matériau ABS page pour en savoir plus sur ce matériel.

Polycarbonate (PC)
Ce matériau plastique est relativement plus lourd que les autres plastiques. Ce matériau peut être votre meilleur choix lorsque vous avez besoin d'une solution durable. Il est pratiquement incassable et très transparent. Ce matériau est utilisé dans les lunettes de sécurité et les luminaires. Il s'agit d'une option solide lorsque la transparence et la résilience sont nécessaires.
Propriétés: Le polycarbonate est plus lourd que la plupart des plastiques, mais il est pratiquement incassable et très transparent. Il peut résister aux chocs et à la chaleur, ce qui le rend adapté aux applications de sécurité.
Avantages: C'est l'un des plastiques transparents les plus solides disponibles, avec une excellente résistance à la chaleur. Il est également facile à mouler, ce qui permet de concevoir des pièces et des composants complexes.
Applications:
Équipement de sécurité: Utilisé pour les lunettes de sécurité, les casques et les boucliers en raison de sa qualité de résistance aux chocs.
Supports optiques: Courant dans les lentilles et les DVD en raison de sa clarté.
Construction et éclairage: Utilisé dans les puits de lumière, les luminaires et le verre pare-balles pour sa durabilité et sa transparence. Aller à moulage par injection de polycarbonate et Polycarbonate ou acrylique pour en savoir plus sur ce matériau plastique PC.
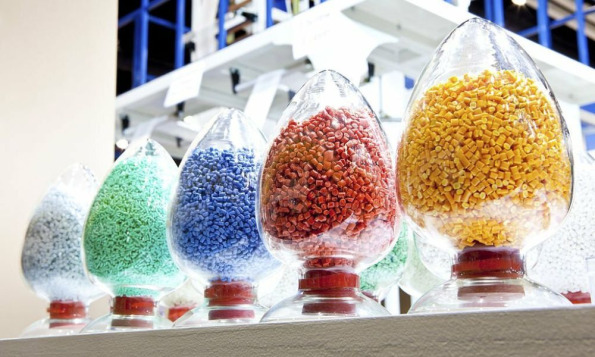
Nylon (PA)
Le nylon est une matière plastique dotée d'une excellente résistance et d'une grande souplesse. Il est également très résistant à l'usure et à l'abrasion. Disponible en différentes qualités (Nylon 6, Nylon 6/6, etc.), chacune ayant des propriétés spécifiques, il est largement utilisé dans les applications industrielles nécessitant de la robustesse. Il peut également supporter des températures élevées.
Propriétés: Excellente solidité, flexibilité, résistance à l'abrasion et à l'usure. Le nylon peut supporter des températures élevées et offre une bonne résistance aux produits chimiques.
Avantages: La grande durabilité et la résistance à la chaleur du nylon en font un choix de premier ordre pour les pièces mécaniques, tandis que son faible coefficient de frottement le rend adapté aux engrenages et aux roulements.
Applications:
Composants mécaniques: Souvent utilisé dans les engrenages, les roulements, les coussinets et autres pièces sujettes à l'usure en raison de sa résistance et de sa durabilité.
Textiles: Il est souvent utilisé dans les tissus en raison de sa résistance et de sa résilience, notamment dans les équipements et les vêtements de plein air.
Automobile: Utilisé dans les composants du moteur, les réservoirs de carburant et les pièces sous le capot en raison de sa résistance à la chaleur. Aller à moulage par injection de nylon page pour en savoir plus.
Chaque plastique offre des avantages spécifiques qui le rendent idéal pour des applications particulières. Le choix dépend de facteurs tels que les exigences de résistance, les conditions environnementales, les préférences esthétiques et les coûts de fabrication. Ce guide aide à comprendre quel plastique peut être le mieux adapté à diverses exigences de produits dans différents secteurs, des biens de consommation aux composants industriels.

Services de moulage par injection de plastique
Une usine typique de moulage par injection de plastique peut vous offrir des services uniques. Chacun de ces services peut vous être utile dans votre entreprise. Cette section vous permettra de vous familiariser avec quelques services de moulage par injection de matières plastiques. services de moulage par injection.

Service #1 Soutien à la conception et à l'ingénierie
Soutien à la conception et à l'ingénierie sont des éléments essentiels de la conception des moules et des produits. Un moule d'injection parfait peut garantir une injection efficace et la meilleure qualité des produits. Chaque entreprise de fabrication de moules se spécialise dans ce domaine afin de répondre aux demandes spécifiques des clients. L'équipe d'ingénieurs collabore avec les clients pour optimiser la conception des pièces.
De cette manière, ils peuvent garantir une bonne fabricabilité et l'efficacité de l'ensemble du processus. Ils évaluent également la conception initiale et suggèrent des modifications pour gagner du temps et réduire les coûts.
DFM est un terme utilisé pour la fabrication de moules d'injection en plastique. La conception pour la fabrication se concentre sur la facilité ou la difficulté de fabrication d'une conception. Elle permet d'identifier les problèmes potentiels à un stade précoce du processus. En appliquant les principes de la DFM, les concepteurs peuvent réduire les problèmes de production. Vous le saurez lorsque vous serez confronté au processus de conception des moules d'injection.
Service #2 Fabrication de moules sur mesure
La fabrication de moules sur mesure est un autre service essentiel d'une entreprise de moulage par injection. Pour lancer de nouveaux produits en plastique, il faut commencer par créer un moule d'injection plastique sur mesure.
Le processus de fabrication des moules commence par les étapes de conception et d'ingénierie. De quelle forme avez-vous besoin ? Quelle doit être l'épaisseur des parois ? Ces questions guident les étapes de la conception du moule.
Plusieurs autres facteurs jouent également un rôle crucial à cet égard. Le premier est le choix du matériau. Comme nous l'avons déjà mentionné, les moules d'injection sont généralement fabriqués à partir d'aciers à outils de haute qualité. Lors de la fabrication des moules, la tolérance est le paramètre le plus critique. La méthode de fabrication doit donc être judicieusement choisie.
Les deux méthodes de fabrication de moules à injection les plus populaires sont l'usinage CNC et le moulage. L'usinage CNC peut être de différents types. La méthode CNC varie en fonction de votre conception. Parfois, vous pouvez avoir besoin de plusieurs méthodes d'usinage CNC. Par exemple, le fraisage CNC permet de créer des rainures, des trous et des formes intérieures. Les autres méthodes CNC comprennent le tournage CNC, l'alésage, le perçage, etc.
Le moulage en métal est une autre méthode de fabrication de la cavité ou du noyau du moule d'injection, spécialement utilisée pour les produits liés aux jouets de poupée en plastique. Il s'agit d'une méthode assez complexe qui nécessite une attention particulière pour fabriquer n'importe quel type de moule d'injection en plastique. L'usinage CNC et l'EDM (usinage par décharge électrique) sont deux procédés de fabrication courants pour créer des moules d'injection en plastique.
Service #3 Pièces en plastique personnalisées
Il se peut que vous n'ayez pas la possibilité d'installer des moules sur mesure. D'autre part, la mise en place de telles installations peut nécessiter des coûts élevés. C'est pourquoi la plupart des fabricants de moules à injection proposent également de fabriquer diverses pièces en plastique sur mesure. De cette façon, vous pouvez économiser beaucoup de coûts d'investissement et gagner de l'argent plus rapidement. Il vous suffit d'acheter les moules d'injection et d'envoyer vos moules à votre fournisseur de moulage par injection de plastique, qui se chargera de la fabrication de toutes les pièces. produits en palstique sur mesure sur la base de votre moule d'injection personnalisé.
Ce processus commence également par une conception claire. Une fois le moule prêt, le plastique est injecté à haute pression dans le moule. Lorsque le plastique refroidit et se solidifie, la pièce prend forme. Vous connaissez déjà les avantages et le processus de fabrication détaillé.
Service #4 Contrôle de la qualité et essais
Une entreprise de moulage par injection de plastique offre des services d'essai et de contrôle de la qualité en plus des trois services susmentionnés.
Le contrôle de la qualité est essentiel dans le domaine du moulage par injection. C'est le filet de sécurité qui permet d'appréhender les problèmes à venir lorsqu'ils se produisent. Différents processus de contrôle de la qualité peuvent être nécessaires en fonction du moule et de ses produits.
Les contrôles dimensionnels constituent l'une des premières lignes de test. Ce processus mesure les pièces par rapport aux tolérances spécifiées. Ont-elles la bonne taille ? S'emboîtent-elles comme il se doit ? Si ce n'est pas le cas, les ingénieurs procèdent aux ajustements nécessaires avant la production en série. L'essai de résistance est la méthode d'essai suivante. Cette méthode permet de s'assurer que les pièces peuvent résister à l'usage auquel elles sont destinées. Il existe également d'autres tests, tels que l'état de surface, les tests de pression, les tests d'éperon, les tests de défauts et bien d'autres encore.
Questions fréquemment posées
Combien coûte le moulage par injection ?
Le coût du moulage par injection varie généralement en fonction de la conception et de la taille - la moyenne se situe entre $1000 et $5000. Si vous avez besoin de moules plus grands, le coût peut être plus élevé. Le coût des pièces en plastique moulées par injection dépend quant à lui du type de matériau. Le plastique PC est généralement plus cher que le PVC ou l'ABS.
Quel est le problème du procédé de moulage par injection ?
Tout processus a ses ratés, et le moulage par injection ne fait pas exception à la règle. Parmi les problèmes les plus courants, citons le gauchissement, qui se produit lorsque la pièce est refroidie de manière irrégulière.
Le flash est un autre problème lié au processus de moulage par injection. Il s'agit de l'excès de matière qui s'échappe du moule. Avez-vous vu des bords indésirables sur vos pièces en plastique ? Si oui, c'est le signe d'une bavure. En revanche, les courts-circuits se produisent lorsque le moule ne se remplit pas complètement.
Combien de temps faut-il pour fabriquer un moule en plastique ?
Le temps nécessaire à la création d'un moule en plastique peut varier de quelques semaines à plusieurs mois. Ce délai n'est pas fixe. Tout dépend de la complexité et des spécificités de votre projet.
Comment ajouter de la texture au moule ?
L'ajout de texture à un moule peut améliorer l'aspect de votre produit. C'est une question d'esthétique et de fonctionnalité. Il existe plusieurs méthodes pour y parvenir. L'une des plus populaires est la gravure, qui crée des motifs sur la surface du moule avant qu'il ne soit utilisé. Une autre option est la gravure au laser.

Dernières paroles
Le moulage par injection de plastique est l'un des procédés de fabrication de plastique les plus populaires. Il s'agit d'un moyen efficace de fabriquer des pièces plastiques complexes et de haute précision. Tout au long de cet article, nous avons parlé de ce processus, en particulier du moulage par injection de plastique.
Nous sommes parmi les 10 premiers Sociétés de moulage par injection de plastique en ChineL'entreprise est spécialisée dans la fabrication de moules d'injection plastique et de moulage par injection. Elle exporte des pièces en plastique de Chine vers divers pays du monde. Plus de 40 clients satisfaits nous ont fourni la meilleure qualité, et ils sont entièrement satisfaits de notre qualité et de notre service. Vous êtes les bienvenus si vous avez besoin de notre soutien. Nous espérons sincèrement pouvoir vous servir dans un avenir proche, et vous serez certainement heureux comme nos autres clients satisfaits.
La production de produits en plastique thermoplastique fait appel à diverses méthodes commerciales. Chacune d'entre elles présente des exigences de conception spécifiques ainsi que des limites. En général, la conception, la taille et la forme de la pièce déterminent clairement le meilleur procédé. Parfois, le concept de la pièce se prête à plus d'un procédé. Étant donné que le développement du produit diffère en fonction du procédé, votre équipe de conception doit décider du procédé à suivre dès le début du développement du produit.
Cette section explique brièvement les processus courants utilisés pour les thermoplastiques de Bayer Corporation. Aujourd'hui, de nombreuses entreprises achètent des pièces moulées par injection à des entreprises de moulage par injection en Chine. Si vous avez besoin pièces moulées par injection pour votre entreprise, vous devez vraiment y réfléchir.
Le processus de moulage par injection décrit ci-dessus utilise une machine de moulage par injection pour fabriquer des produits en plastique. Les machines se composent de deux parties principales : l'unité d'injection et l'unité de fermeture. Visitez notre moulage par injection pour plus d'informations.
Vous avez besoin de moulage par injection ou vous recherchez un partenaire chinois pour créer des moules en plastique et fabriquer vos pièces moulées en plastique ? Envoyez-nous un courriel et nous vous répondrons dans les deux jours ouvrables.
Nous sommes l'un des 10 premiers Sociétés de moulage par injection de plastique en Chine qui fournit des services personnalisés services de fabrication de moules d'injection et de moulage par injection pour une variété de produits en plastique dans le monde entier. Nous proposons la conception de pièces, la conception de moules, la conception de circuits imprimés, les prototypes, la fabrication de moules, la production en série, les tests, les certificats, la peinture, le placage, la sérigraphie, l'impression, l'assemblage et la livraison, le tout dans des services à guichet unique.
Connaissez-vous le nom du procédé par lequel la plupart des matières plastiques solides sont produites ? Il s'appelle moulage par injection. C'est l'un des meilleurs procédés de moulage pour fabriquer des millions de pièces moulées par injection en très peu de temps. Cependant, la première l'outillage pour les moules d'injection le coût est assez élevé par rapport aux autres méthodes d'usinage, mais ce coût d'outillage d'injection sera récupéré par la production à grande échelle ultérieure, et ce processus a un taux de déchets faible, voire nul.
Qu'est-ce que le moulage par injection
Moulage par injection (ou moulage par injection) est une technologie de fabrication permettant de produire des produits en plastique. La résine plastique fondue est injectée à haute pression dans un moule d'injection, qui est fabriqué selon la forme de la pièce souhaitée, qui a été créée par un concepteur à l'aide d'un logiciel de conception CAO (tel que UG, Solidworks, etc.).
Le moule est fabriqué par une entreprise de moulage (ou fabricant de moules) à partir de matériaux métalliques ou d'aluminium et usiné avec précision pour former les caractéristiques de la pièce souhaitée par des machines de haute technologie comme les machines CNC, les machines EDM, les machines à mousser, les rectifieuses, les machines de découpe de fil, etc., étape par étape pour créer la base de la cavité du moule final sur exactement la forme et la taille de la pièce souhaitées, que nous avons appelée un moule d'injection.
Les injection processus de moulage Le moulage par injection est largement utilisé pour produire une grande variété de produits en plastique, du plus petit composant aux gros pare-chocs de voitures. Il s'agit de la technologie de moulage la plus courante dans le monde aujourd'hui, avec des produits couramment fabriqués, notamment des contenants alimentaires, des seaux, des bacs de rangement, des équipements de cuisine pour la maison, des meubles d'extérieur, des composants automobiles, des composants médicaux, des jouets moulés, etc.
Types de moulage par injection – Il existe essentiellement 7 types de processus de moulage par injection, comme indiqué ci-dessous
- Moulage par injection et réaction
- Moulage par injection de liquide
- Moulage par injection assistée par gaz
- Moulage par co-injection
- Moulage par injection à 2 coups (ou moulage par double injection)
- Moulage par injection de noyaux fusibles
- Moulage par injection rapide
Équipement de moulage par injection
Machine de moulage par injection
Les presses à injection, généralement appelées presses à injection, fixent notre moule d'injection sur mesure dans la machine. La machine à injection est classée en fonction du tonnage, qui indique la quantité de force de serrage que la presse peut générer. Cette force de serrage maintient le moule fermé pendant le processus de moulage par injection. Il existe différentes spécifications pour les machines de moulage par injection, de moins de 5 tonnes à 6 000 tonnes ou même plus.
En général, la machine de moulage par injection de base se compose d'un système de moulage, d'un système de contrôle, d'un système d'injection, d'un système hydraulique et d'un système Pinpin. La pince de tonnage et la taille de l'injection sont utilisées pour identifier les dimensions d'une machine de moulage par injection thermoplastique, ce qui est un facteur majeur dans le processus global. Un autre élément à prendre en compte est l'épaisseur du moule, la pression, le taux d'injection, la distance entre la tige de liaison et la conception de la vis.
Machine de moulage par injection horizontale
Machines horizontales ou verticales
Il existe normalement deux types de machines de moulage par injection : les machines de moulage horizontales et verticales.
Cela signifie que les machines de moulage fixent le moule en position horizontale ou verticale. La majorité sont des machines de moulage par injection horizontales, mais les machines verticales sont utilisées dans certaines applications de niche telles que moulage d'insertion de câble, moulage par injection de filtre, moulage par insertion, ou certaines exigences de processus de moulage spéciales. Certaines machines d'injection peuvent produire deux, trois ou quatre pièces moulées colorées en une seule étape ; nous les appelons machines de moulage par injection à double injection ou machines de moulage par injection 2K (plus de couleurs seront des machines de moulage 3K ou 4K).
Unité de serrage
Les machines sont classées principalement en fonction du type de système d'entraînement qu'elles utilisent : hydraulique, électrique ou hybride. Les presses hydrauliques ont toujours été la seule option disponible pour les mouleurs jusqu'à ce que Nissei présente la première machine entièrement électrique en 1983. La presse électrique, également connue sous le nom de technologie de machine électrique (EMT), réduit les coûts d'exploitation en diminuant la consommation d'énergie et répond également à certaines des préoccupations environnementales entourant la presse hydraulique.
Les presses à injection électriques se sont révélées plus silencieuses, plus rapides et plus précises. Cependant, ces machines sont plus chères. Les machines de moulage par injection hybrides tirent parti des meilleures caractéristiques des systèmes hydrauliques et électriques. Les machines hydrauliques sont le type prédominant dans la plupart des pays, à l'exception du Japon.
Résumé final pour la machine de moulage par injection : La machine de moulage par injection convertit les granulés ou granules de plastique bruts en pièces de moule finales à l'aide de cycles de fusion, d'injection, de conditionnement et de refroidissement thermoplastiques.
Moule à injection- Types de moules d'injection
Expliquez simplement que le moule d'injection est fabriqué sur mesure à partir de la forme de pièce souhaitée en découpant l'acier ou l'aluminium et en produisant le moule qui peut être utilisé dans la machine de moulage par injection, que nous avons appelée moule d'injection ou moule d'injection plastique. Accédez à notre moulage plastique section pour en savoir plus sur la fabrication de moules d'injection plastique. Mais faire moule d'injection en fait ce n'est pas facile ; il faut avoir une équipe professionnelle (un mouliste, un concepteur de moules) et des équipements de fabrication de moules comme des machines CNC, des machines EDM, des machines de découpe de fil, etc.
Il existe deux principaux types de moules d'injection: moule à canaux froids (modèles à deux et trois plaques) et moules à canaux chauds (le plus courant des moules sans canal). La différence significative est la présence d'une carotte et d'un canal avec chaque pièce moulée dans le type à canal froid. Ce composant moulé supplémentaire doit être séparé de la pièce moulée souhaitée, le canal chaud ne contient pratiquement aucun déchet de canal ou de petits déchets de canal.
Moule à canaux froids
Développé pour permettre l'injection de matériau thermodurcissable soit directement dans la cavité, soit via une carotte et un petit sous-canal et une porte dans la cavité du moule, il existe essentiellement deux types de canaux froids qui sont principalement utilisés dans l'industrie du moule, le moule à deux plaques et le moule à trois plaques.
Moule à deux plaques
Le conventionnel moule à deux plaques Le moule est constitué de deux moitiés fixées aux deux plateaux de l'unité de serrage de la machine de moulage. Lorsque l'unité de serrage est ouverte, les deux moitiés du moule s'ouvrent, comme illustré en (b). La caractéristique la plus évidente du moule est la cavité, qui est généralement formée en retirant du métal des surfaces d'accouplement des deux moitiés. Les moules peuvent contenir une seule cavité ou plusieurs cavités pour produire plus d'une pièce en une seule fois. La figure montre un moule avec deux cavités. Les surfaces de séparation (ou la ligne de séparation dans une vue en coupe transversale du moule) sont les endroits où le moule s'ouvre pour retirer la ou les pièces.
Outre la cavité, le moule comporte d'autres éléments indispensables au cours du cycle de moulage. Le moule doit être doté d'un canal de distribution par lequel le polymère fondu s'écoule de la buse du cylindre d'injection vers la cavité du moule. Le canal de distribution se compose (1) d'une carotte qui mène de la buse vers le moule ; (2) de canaux qui mènent de la carotte vers la cavité (ou les cavités) ; et (3) de portes qui limitent l'écoulement du plastique dans la cavité. Il y a une ou plusieurs portes pour chaque cavité du moule.
Moule à trois plaques
Le moule à deux plaques est le moule le plus courant dans le moulage par injection. Une alternative est un moule d'injection à trois plaques. Cette conception de moule présente des avantages. Tout d'abord, le flux de plastique fondu s'effectue à travers une porte située à la base de la pièce en forme de coupelle plutôt que sur le côté. Cela permet une répartition plus uniforme de la matière fondue le long des côtés de la coupelle. Dans la conception à porte latérale du moule à deux plaques, le plastique doit s'écouler autour du noyau et se joindre sur le côté opposé, ce qui peut créer une faiblesse au niveau de la ligne de soudure.
Deuxièmement, le moule à trois plaques permet un fonctionnement plus automatique de la machine de moulage. Lorsque le moule s'ouvre, il se divise en trois plaques séparées par deux ouvertures. Cela force la déconnexion des canaux et des pièces, qui tombent par gravité (avec l'aide éventuelle d'air soufflé ou d'un bras robotisé) dans différents conteneurs situés sous le moule.
Moule à canaux chauds
Moulage à canaux chauds Le moulage par injection comprend des pièces chauffées physiquement. Ces types de moulage permettent de transférer rapidement le plastique fondu de la machine, en l'introduisant directement dans la cavité du moule. On l'appelle également moule sans canal. Le système de canaux chauds est très utile pour certains des volumes élevés de produits qui permettront d'économiser d'énormes coûts de production en utilisant le système de moulage par canaux chauds. La carotte et le canal dans un moule conventionnel à deux ou trois plaques représentent des déchets.
Dans de nombreux cas, ils peuvent être broyés et réutilisés ; cependant, dans certains cas, le produit doit être fabriqué à partir de plastique « vierge » (matière plastique brute d'origine) ou il existe un moule à cavités multiples (par exemple 24 cavités ou 48 cavités, 96 cavités, 128 cavités ou même plus de cavités). moule à canaux chauds élimine la solidification de la carotte et du canal en plaçant les éléments chauffants autour des canaux correspondants du canal. Pendant que le plastique dans la cavité du moule se solidifie, le matériau dans la carotte et les canaux du canal reste fondu, prêt à être injecté dans la cavité lors du cycle suivant.
Type de système à canaux chauds.
Il existe essentiellement deux types de systèmes à canaux chauds : l'un appelé moule à carotte chaude (sans la plaque collectrice et la plaque à canaux chauds) et l'autre appelé moule à canaux chauds (avec la plaque collectrice et la plaque à canaux chauds).
Le moule à carotte chaude (sans la plaque collectrice et la plaque à canaux chauds) utilise la buse chaude (carotte) pour alimenter le matériau dans la cavité du moule, directement ou indirectement.
Le moule à canaux chauds (avec la plaque collectrice et la plaque à canaux chauds) signifie que le système à canaux chauds comprend la plaque à canaux chauds, la plaque collectrice et la carotte sous-canaux chauds. Les images ci-dessous sont des explications simples pour deux types de systèmes à canaux chauds.
Avantages et inconvénients du moulage à canaux froids
Le moulage à canaux froids présente quelques avantages étonnants, tels que :
- Le moulage à canaux froids est moins cher et plus facile à entretenir.
- Vous pouvez changer rapidement de couleur.
- Son temps de cycle est plus rapide.
- Il est plus flexible que le moulage par canaux chauds.
- Les emplacements des portes peuvent être facilement modifiés ou fixés.
Bien que le moulage à canaux froids présente de nombreux avantages, il présente également quelques inconvénients. Les inconvénients du moulage à canaux froids sont les suivants :
- Vous devez avoir des dimensions plus épaisses par rapport au moule à canaux chauds.
- Vous ne pouvez utiliser que certains types de buses, raccords et collecteurs.
- Le moulage à canaux froids peut entraîner un temps de production plus lent lorsque vous retirez les carottes et les canaux.
- Vous devez séparer manuellement les coureurs et les pièces après le moulage.
- Vous risquez de gaspiller les matières plastiques si vous ne les réinitialisez pas après chaque exécution.
Si vous souhaitez en savoir plus, rendez-vous sur le moule à canaux froids page pour consulter plus de détails.
Avantages et inconvénients du moulage par canaux chauds
Le moulage par canaux chauds présente quelques avantages, tels que :
- Le moulage par canaux chauds a un temps de cycle très rapide.
- Vous pouvez économiser sur les coûts de production en utilisant le moulage par canaux chauds.
- Moins de pression est nécessaire pour injecter le moulage.
- Vous avez plus de contrôle sur le moulage par canaux chauds.
- Le moulage à canaux chauds peut s'adapter à une grande variété de portails.
- Plusieurs cavités du moule peuvent être facilement remplies en utilisant le système de canaux chauds.
Les inconvénients de l’utilisation de moulages à canaux chauds sont les suivants :
- Il est plus coûteux de fabriquer un moule à canaux chauds qu'un moule à canaux froids.
- Il est difficile d'entretenir et de réparer le moule à canaux chauds.
- Vous ne pouvez pas utiliser le moulage par canaux chauds sur des matériaux sensibles à la chaleur.
- Vous devrez faire inspecter vos machines plus souvent que les machines de moulage à canaux froids.
- Il est difficile de changer les couleurs dans le système de moulage à canaux chauds.
Vous souhaitez en savoir plus ? Bienvenue sur le moule à canaux chauds section.
Traitement de moulage par injection ?
Le moulage par injection est l'un des meilleurs moyens de façonner des produits en plastique en injectant un matériau thermoplastique. Au cours du processus de moulage par injection, la matière plastique est placée dans la machine de moulage par injection et le système de fusion de l'unité d'injection est utilisé pour faire fondre le plastique dans le liquide. Le matériau liquide est ensuite injecté sous haute pression dans un moule (un moule de fabrication sur mesure) qui est assemblé dans cette machine de moulage par injection. Le moule est fabriqué à partir de n'importe quel métal, comme l'acier ou l'aluminium. La forme fondue est ensuite laissée refroidir et se solidifier.
La matière plastique ainsi formée est ensuite éjectée hors de la moule en plastique. Le processus réel de moulage plastique n'est qu'une extension de ce mécanisme de base. Le plastique est introduit dans un baril ou une chambre par gravité ou est alimenté de force. Au fur et à mesure qu'il descend, la température croissante fait fondre la résine plastique. Ensuite, le plastique fondu est injecté de force dans le moule sous le baril avec un volume approprié. Lorsque le plastique refroidit, il se solidifie. pièces moulées par injection comme cela, ils ont une forme inversée par rapport au moule. Une variété de formes, à la fois 2D et 3D, peuvent être produites par le procédé.
Le processus de moulage plastique est bon marché en raison de la simplicité impliquée, et la qualité du matériau plastique est modifiable en changeant les facteurs impliqués dans la personnalisation processus de moulage par injection. La pression d'injection peut être modifiée pour modifier la dureté du produit final. L'épaisseur du moule détermine également la qualité de l'article produit.
La température de fusion et de refroidissement détermine la qualité du plastique formé. AVANTAGES Le principal avantage du moulage par injection est qu'il est très économique et rapide. En outre, contrairement aux procédés de découpe, ce procédé élimine les bords tranchants indésirables. De plus, ce procédé permet d'obtenir des produits lisses et finis qui ne nécessitent aucune finition supplémentaire. Découvrez ci-dessous les avantages et les inconvénients détaillés.
Avantages du moulage par injection
Bien que le moulage par injection soit utilisé par de nombreuses entreprises différentes et qu'il s'agisse sans aucun doute de l'une des méthodes les plus populaires pour produire des produits moulés par injection, son utilisation présente certains avantages, tels que :
- Précision et esthétique—Parce que dans ce procédé de moulage par injection, vous pouvez fabriquer votre pièce en plastique avec n'importe quelle forme et finition de surface (texture et finition brillante), certaines des finitions de surface spéciales peuvent encore être satisfaites par le procédé de finition de surface secondaire. La pièce moulée par injection est la répétabilité de ses formes et dimensions.
- Efficacité et rapidité : un seul processus de production, même pour les produits les plus complexes, dure de quelques secondes à plusieurs dizaines de secondes.
La possibilité d'une automatisation complète du processus de production, qui dans le cas des entreprises s'occupant de la production de composants en plastique se traduit par un faible effort de production et la possibilité d'une production en série. - Écologie:car, par rapport au travail des métaux, nous avons affaire à une réduction significative du nombre d'opérations technologiques, à une moindre consommation directe d'énergie et d'eau et à de faibles émissions de composés nocifs pour l'environnement.
Les plastiques sont des matériaux qui, bien que connus relativement récemment, sont même devenus indispensables dans nos vies, et grâce à des processus de production de plus en plus modernes, ils contribueront d'année en année encore davantage à économiser de l'énergie et d'autres ressources naturelles.
Inconvénients du moulage par injection
- Le coût élevé des machines de moulage par injection et souvent le coût de l'outillage (moules) qui l'accompagne entraînent un temps d'amortissement prolongé et des coûts élevés de démarrage de la production.
- En raison de ce qui précède, la technologie d’injection n’est rentable que pour la production de masse.
- Le besoin d'employés de supervision technique hautement qualifiés qui doivent connaître les spécificités du traitement de moulage par injection.
- La nécessité d'exigences techniques élevées pour la fabrication de moules d'injection
- La nécessité de maintenir des tolérances étroites pour les paramètres de traitement.
- Un long temps de préparation pour la production en raison de la mise en œuvre laborieuse des moules d'injection.
Durée du cycle de moulage par injection
Le temps du cycle d'injection de base comprend la fermeture du moule, l'avance du chariot d'injection, le temps de remplissage du plastique, le dosage, la rétraction du chariot, le maintien de la pression, le temps de refroidissement, l'ouverture du moule et l'éjection des pièces.
Le moule est fermé par la machine de moulage par injection et le plastique fondu est injecté dans le moule par la pression de la vis d'injection. Les canaux de refroidissement aident ensuite à refroidir le moule et le plastique liquide devient solide pour former la pièce en plastique souhaitée. Le système de refroidissement est l'une des parties les plus importantes du moule. Un refroidissement inapproprié peut entraîner des produits de moulage déformés et le temps de cycle sera augmenté, ce qui augmentera également le coût du moulage par injection.
Essai de moulage
Lors de l'injection moule en plastique a été fabriqué par le moule fabricant, la première chose que nous devons faire est de faire l'essai du moule. C'est le seul moyen de vérifier la qualité du moule pour voir s'il a été fabriqué selon les exigences personnalisées ou non. Pour tester le moule, nous remplissons normalement le plastique avec le moulage étape par étape, en utilisant d'abord un remplissage à court terme et en augmentant progressivement le poids du matériau jusqu'à ce que le moule soit rempli de 95 à 99%.
Une fois ce statut atteint, une petite pression de maintien sera ajoutée et le temps de maintien augmenté jusqu'à ce que le gel de la porte se produise. La pression de maintien est ensuite augmentée jusqu'à ce que la pièce moulée soit exempte de retassures et que le poids de la pièce soit stable. Une fois que la pièce est suffisamment bonne et a passé tous les tests techniques spécifiques, une fiche de paramètres de la machine doit être enregistrée pour une production massive à l'avenir.
Défauts de moulage par injection plastique
Le moulage par injection est une technologie complexe et des problèmes peuvent survenir à chaque fois. Un nouveau moule d'injection personnalisé présente quelques problèmes, ce qui est tout à fait normal. Pour résoudre le problème du moule, nous devons réparer et tester le moule plusieurs fois. Normalement, deux ou trois essais peuvent résoudre complètement tous les problèmes, mais dans certains cas, un seul essai de moule peut approuver les échantillons. Et enfin, tous les problèmes sont complètement résolus. Vous trouverez ci-dessous la plupart des défauts de moulage par injection et les compétences de dépannage pour résoudre ces problèmes.
Numéro I : Défauts de tir court- Qu'est-ce qu'un problème de tir court ?
Lors de l'injection de matière dans la cavité, la matière fondue ne remplit pas complètement la cavité, ce qui entraîne un manque de matière dans le produit. C'est ce qu'on appelle un moulage court ou un moulage court, comme le montre l'image. Il existe de nombreuses raisons pouvant entraîner des problèmes de moulage court.
Analyse des défauts et méthode de correction des défauts
- Mauvaise sélection de la machine de moulage par injection : Lors du choix d'une machine d'injection plastique, le poids maximal de l'injection de la machine doit être supérieur au poids du produit. Lors de la vérification, le volume total d'injection (y compris le produit plastique, le canal et la garniture) ne doit pas dépasser 85% de la capacité de plastification de la machine.
- Approvisionnement insuffisant en matériel : Le bas de la position d'alimentation peut présenter un phénomène de « pontage du trou ». La course de tir du piston d'injection doit être augmentée pour augmenter l'alimentation en matériau.
- Faible facteur d'écoulement de la matière première: améliorer le système d'injection du moule, par exemple, en concevant correctement l'emplacement du canal d'injection, en agrandissant les portes, le canal d'injection et la taille du dispositif d'alimentation, et en utilisant une buse plus grande, etc. En attendant, l'additif peut être ajouté à la matière première pour améliorer le débit de la résine ou changer le matériau pour avoir un meilleur débit.
- Surdosage d'utilisation du lubrifiant : réduire le lubrifiant et ajuster l'écart entre le canon et le piston d'injection pour récupérer la machine, ou fixer le moule de manière à ce qu'il n'y ait pas besoin de lubrifiant pendant le processus de moulage.
- Des substances étrangères froides ont bloqué le coureur. Ce problème se produit généralement avec les systèmes à canaux chauds. Démontez et nettoyez la buse de la pointe du canal chaud ou agrandissez la cavité du matériau froid et la section transversale du canal.
- Conception incorrecte du système d'alimentation par injection:Lors de la conception du système d'injection, il faut veiller à l'équilibre des portes. Le poids du produit de chaque cavité doit être proportionnel à la taille de la porte, de sorte que chaque cavité puisse être entièrement remplie simultanément, et les portes doivent être positionnées dans des parois épaisses. Un schéma de canaux séparés équilibrés peut également être adopté. Si la porte ou le canal est petit, fin ou long, la pression du matériau fondu sera trop réduite pendant l'alimentation et le débit sera bloqué, ce qui entraînera un mauvais remplissage. Pour résoudre ce problème, les sections transversales de la porte et du canal doivent être agrandies et plusieurs portes doivent être utilisées si nécessaire.
- Manque de ventilation : Vérifiez s'il y a un puits de refroidissement ou si la position du puits de refroidissement est correcte. Pour les moules avec une cavité profonde ou des nervures profondes, des fentes d'aération ou des rainures d'aération doivent être ajoutées aux positions de moulage court (fin de la zone d'alimentation). En principe, il y a toujours des rainures d'aération sur la ligne de séparation ; la taille des rainures d'aération peut être de 0,02 à 0,04 mm et de 5 à 10 mm de largeur, 3 mm à proximité de la zone d'étanchéité, et l'ouverture d'aération doit être à la fin du remplissage de la position.
Lors de l'utilisation de matières premières avec une teneur excessive en humidité et en matières volatiles, une grande quantité de gaz (air) sera également générée, ce qui entraînera des problèmes de piège à air dans la cavité du moule. Dans ce cas, les matières premières doivent être séchées et débarrassées des substances volatiles. De plus, pendant le processus d'injection, une mauvaise ventilation peut être résolue en augmentant la température du moule, en réduisant la vitesse d'injection, en réduisant l'obstruction du système d'injection et la force de serrage du moule et en élargissant les espaces entre les moules. Mais le problème de tir court se produit dans la zone des nervures profondes. Pour évacuer l'air, vous devez ajouter un insert de ventilation pour résoudre ce problème de piège à air et de tir court. - La température du moule est trop basseAvant de commencer la production de moulage, le moule doit être chauffé à la température requise. Au début, vous devez connecter tous les canaux de refroidissement et vérifier si la ligne de refroidissement fonctionne bien, en particulier pour certains matériaux spéciaux comme le PC, le PA66, le PA66+GF, le PPS, etc. La conception de refroidissement parfaite est indispensable pour ces matières plastiques spéciales.
- La température du matériau fondu est trop basse. Dans une fenêtre de processus de moulage appropriée, la température du matériau est proportionnelle à la longueur de remplissage. Le matériau fondu à basse température est peu fluide et la longueur de remplissage est raccourcie. Il convient de noter qu'une fois le barillet d'alimentation chauffé à la température requise, il doit rester constant pendant un certain temps avant de commencer la production de moulage.
Dans le cas où une injection à basse température doit être utilisée pour empêcher la dissolution du matériau fondu, le temps du cycle d'injection peut être prolongé pour surmonter le manque de temps. Si vous avez un opérateur de moulage professionnel, il devrait très bien le savoir. - La température de la buse est trop basseLors de l'ouverture du moule, la buse doit être partiellement éloignée de l'éperon du moule pour réduire l'influence de la température du moule sur la température de la buse et maintenir la température de la buse dans la plage requise par le processus de moulage.
- Pression d'injection ou pression de maintien insuffisante : La pression d'injection est proche d'une proportion positive par rapport à la distance de remplissage. La pression d'injection est trop faible, la distance de remplissage est courte et la cavité ne peut pas être entièrement remplie. L'augmentation de la pression d'injection et de la pression de maintien peut améliorer ce problème.
- La vitesse d'injection est trop lente. La vitesse de remplissage du moule est directement liée à la vitesse d'injection. Si la vitesse d'injection est trop faible, le remplissage du matériau fondu est lent tandis que le matériau fondu à écoulement lent est facile à refroidir, ce qui réduit encore les propriétés d'écoulement et entraîne une injection courte. Pour cette raison, la vitesse d'injection doit être augmentée correctement.
- La conception des produits en plastique n’est pas raisonnable. Si l'épaisseur de la paroi est disproportionnée par rapport à la longueur du produit en plastique, la forme du produit est très complexe et la zone de formage est grande, le matériau fondu se bloque facilement au niveau de la paroi mince du produit, ce qui entraîne un remplissage insuffisant. Par conséquent, lors de la conception de la forme et de la structure des produits en plastique, notez que l'épaisseur de la paroi est directement liée à la longueur de remplissage limite de fusion. Lors du moulage par injection, l'épaisseur du produit doit être comprise entre 1 et 3 mm et 3 à 6 mm pour les produits de grande taille. En général, il n'est pas bon pour le moulage par injection si l'épaisseur de la paroi est supérieure à 8 mm ou inférieure à 0,4 mm, donc ce type d'épaisseur doit être évité lors de la conception.
Problème n° II : Défauts de coupe (bavures ou bavures)
I. Qu'est-ce que le scintillement ou les bavures ?
Lorsque de la matière plastique fondue supplémentaire est expulsée de la cavité du moule à partir du joint de moulage et forme une feuille mince, un rognage est généré. Si la feuille mince est grande, on parle de bavure.
Bavures ou bavures de moulage
II. Analyse des défauts et méthode de correction
- La force de serrage du moule n'est pas suffisante. Vérifiez si le surpresseur est en surpression et vérifiez si le produit de la surface projetée de la pièce en plastique et de la pression de formage dépasse la force de serrage de l'équipement. La pression de formage est la pression moyenne dans le moule ; normalement, elle est de 40 MPa. Si le produit calculé est supérieur à la force de serrage du moule, cela indique que la force de serrage est insuffisante ou que la pression de positionnement de l'injection est trop élevée. Dans ce cas, la pression d'injection ou la section de la porte d'injection doit être réduite ; le maintien de la pression et le temps de pressurisation peuvent également être raccourcis ; les courses du piston d'injection peuvent être réduites ; le nombre de cavités d'injection peut être réduit ; ou une machine d'injection de moule avec un tonnage plus important peut être utilisée.
- La température du matériau est trop élevée. La température du cylindre d'alimentation, de la buse et du moule doit être correctement abaissée pour réduire le cycle d'injection. Pour les matières fondues à faible viscosité, comme le polyamide, il est difficile de résoudre les défauts de débordement en modifiant simplement les paramètres de moulage par injection. Pour résoudre complètement ce problème, la meilleure solution est de réparer le moule, par exemple en améliorant l'ajustement du moule et en rendant la ligne de séparation et la zone de projection plus précises.
- Défaut de moisissureLes défauts du moule sont la principale cause des débordements. Le moule doit être soigneusement examiné et la ligne de séparation du moule doit être revérifiée pour assurer le pré-centrage du moule. Vérifiez si la ligne de séparation s'ajuste bien, si l'espace entre les pièces coulissantes dans la cavité et le noyau est hors tolérance, s'il y a une adhérence de corps étrangers sur la ligne de séparation, si les plaques du moule sont plates et s'il y a une flexion ou une déformation, si la distance entre les plaques du moule est ajustée pour s'adapter à l'épaisseur du moule, si le bloc de moule de surface est endommagé, si la tige de traction est déformée de manière inégale et si la fente ou les rainures d'aération sont trop grandes ou trop profondes.
- Mauvaise qualité du processus de moulage. Si la vitesse d'injection est trop élevée, le temps d'injection est trop long, la pression d'injection dans la cavité du moule est déséquilibrée, la vitesse de remplissage du moule n'est pas constante ou il y a une suralimentation de matériau, un surdosage de lubrifiant peut entraîner des flashs ; par conséquent, des mesures correspondantes doivent être prises en fonction de la situation spécifique pendant le fonctionnement.
Numéro III. Défauts de soudure (ligne de joint)
I. Quel est le défaut de la ligne de soudure ?
Ligne de soudure
Lors du remplissage de la cavité du moule avec de la matière plastique fondue, si deux ou plusieurs flux de matière fondue ont refroidi au préalable avant la confluence dans la zone de joint, les flux ne pourront pas s'intégrer totalement et une doublure est produite à la confluence, formant ainsi une ligne de soudure, également appelée ligne de joint
II. Analyse des défauts et méthode de correction
- La température du matériau est trop basseLes flux de matière fondue à basse température ont une mauvaise performance de confluence et la ligne de soudure se forme facilement. Si des marques de soudure apparaissent au même endroit à l'intérieur et à l'extérieur d'un produit en plastique, il s'agit généralement d'une soudure inappropriée causée par la basse température du matériau. Pour résoudre ce problème, les températures du cylindre d'alimentation et de la buse peuvent être correctement augmentées, ou le cycle d'injection peut être prolongé pour augmenter la température du matériau. En attendant, le débit du liquide de refroidissement à l'intérieur du moule doit être régulé pour augmenter correctement la température du moule.
En général, la résistance de la ligne de soudage des produits en plastique est relativement faible. Si la position du moule avec la ligne de soudage peut être partiellement chauffée pour augmenter partiellement la température au niveau de la position de soudage, la résistance au niveau de la ligne de soudage peut être améliorée. Lorsqu'un procédé de moulage par injection à basse température est utilisé pour des besoins spéciaux, la vitesse et la pression d'injection peuvent être augmentées pour améliorer les performances de confluence. Une petite dose de lubrifiant peut également être ajoutée à la formule de la matière première pour augmenter les performances d'écoulement en fusion. - Défaut de moisissure. Il faut adopter un nombre réduit de portes et une position raisonnable de la porte pour éviter une vitesse de remplissage irrégulière et une interruption du flux de fusion. Dans la mesure du possible, une porte à un seul point doit être adoptée. Pour éviter que le matériau fondu à basse température ne génère une marque de soudure après avoir été injecté dans la cavité du moule, abaissez la température du moule et ajoutez plus d'eau froide dans le moule.
- Mauvaise solution d'évacuation des moisissures. Vérifiez d'abord si la fente d'aération est bloquée par du plastique solidifié ou une autre substance (en particulier un matériau en fibre de verre), et vérifiez s'il y a une substance étrangère au niveau de la porte. S'il reste des points de carbonatation après avoir retiré les blocs supplémentaires, ajoutez une rainure d'aération au niveau de la convergence du flux dans le moule ou modifiez l'emplacement de la porte. Réduisez la force de serrage du moule et augmentez les intervalles d'aération pour accélérer la convergence des flux de matière. En termes de processus de moulage, il est possible de réduire la température du matériau et la température du moule, de raccourcir le temps d'injection à haute pression et de diminuer la pression d'injection.
- Utilisation inappropriée des agents de démoulage. Dans le moulage par injection, on applique généralement une petite quantité d'agent de démoulage de manière uniforme sur le filetage et dans d'autres endroits difficiles à démouler. En principe, l'utilisation d'agent de démoulage doit être réduite autant que possible. Dans le cas d'une production en série, il ne faut jamais utiliser d'agent de démoulage.
- La structure des produits en plastique n'est pas raisonnablement conçue. Si la paroi du produit en plastique est trop fine, si l'épaisseur diffère considérablement ou s'il y a trop d'inserts, cela entraînera une mauvaise soudure. Lors de la conception d'un produit en plastique, il faut veiller à ce que la partie la plus fine du produit soit supérieure à l'épaisseur de paroi minimale autorisée lors du formage. De plus, réduisez le nombre d'inserts et rendez l'épaisseur de paroi aussi uniforme que possible.
- L'angle de soudage est trop petitChaque type de plastique possède son propre angle de soudage. Lorsque deux flux de plastique fondu convergent, la marque de soudage apparaît si l'angle de convergence est inférieur à l'angle de soudage limite et disparaît si l'angle de convergence est supérieur à l'angle de soudage limite. En général, l'angle de soudage limite est d'environ 135 degrés.
- Autres causesDifférents degrés de mauvaise soudure peuvent être causés par l'utilisation de matières premières avec une teneur excessive en humidité et en matières volatiles, des taches d'huile dans le moule qui ne sont pas nettoyées, un matériau froid dans la cavité du moule ou une répartition inégale de la charge de fibres dans le matériau fondu, une conception déraisonnable du système de refroidissement du moule, une solidification rapide de la masse fondue, une basse température de l'insert, un petit trou de buse, une capacité de plastification insuffisante de la machine d'injection ou une perte de pression importante dans le piston ou le cylindre de la machine.
Pour résoudre ces problèmes, différentes mesures, telles que le pré-séchage des matières premières, le nettoyage régulier du moule, la modification de la conception des canaux de refroidissement du moule, le contrôle du débit d'eau de refroidissement, l'augmentation de la température des inserts, le remplacement des buses par des ouvertures plus grandes et l'utilisation de machines d'injection avec des spécifications plus importantes, peuvent être prises au cours du processus de fonctionnement.
Numéro IV : Distorsion de chaîne – Qu’est-ce que la distorsion de chaîne ?
En raison du rétrécissement interne du produit, la contrainte interne est différente et une distorsion se produit.
Analyse des défauts et méthode de correction
1. L'orientation moléculaire est déséquilibrée. Afin de minimiser la distorsion de la chaîne causée par la diversification de l'orientation moléculaire, créez des conditions pour réduire l'orientation de l'écoulement et relâcher la contrainte d'orientation. La méthode la plus efficace consiste à réduire la température du matériau fondu et la température du moule. Lorsque cette méthode est utilisée, il est préférable de la combiner avec un traitement thermique des pièces en plastique ; sinon, l'effet de réduction de la diversification de l'orientation moléculaire est souvent de courte durée. La méthode de traitement thermique est la suivante : après le démoulage, conserver la produit en plastique à haute température pendant un certain temps, puis refroidir progressivement jusqu'à température ambiante. De cette manière, la contrainte d'orientation dans le produit plastique peut être en grande partie éliminée.
2. Refroidissement incorrect. Lors de la conception d'une structure de produit en plastique, la section transversale de chaque position doit être cohérente. Le plastique doit être conservé dans le moule pendant une durée suffisante pour le refroidissement et le formage. Pour la conception d'un système de refroidissement de moule, les conduites de refroidissement doivent être situées à des endroits où la température est facile à augmenter et la chaleur est relativement concentrée. Quant aux positions qui refroidissent facilement, un refroidissement progressif doit être adopté pour assurer un refroidissement équilibré de chaque position du produit.
3. Le système de porte du moule n'est pas correctement conçu. Lors de la détermination de la position de la porte, il faut savoir que le matériau fondu n'aura pas d'impact direct sur le noyau et s'assurer que la contrainte des deux côtés du noyau est la même. Pour les grandes pièces en plastique rectangulaires plates, une porte à membrane ou une porte multipoint doit être utilisée pour les matières premières en résine à orientation moléculaire et retrait larges, et une porte latérale ne doit pas être utilisée ; pour les pièces annulaires, une porte à disque ou une porte à roue doit être utilisée, et une porte latérale ou une porte ponctuelle ne doit pas être utilisée ; pour les pièces de boîtier, une porte droite doit être utilisée et une porte latérale ne doit pas être utilisée dans la mesure du possible.
4. Le système de démoulage et de ventilation n'est pas correctement conçu. La conception du moule, l'angle de dépouille, la position et le nombre d'éjecteurs doivent être raisonnablement conçus pour améliorer la résistance du moule et la précision de positionnement. Pour les moules de petite et moyenne taille, des moules anti-gauchissement peuvent être conçus et fabriqués en fonction de leur comportement au gauchissement. En ce qui concerne le fonctionnement du moule, la vitesse d'éjection ou la course d'éjection doivent être correctement réduites.
5. Processus de fonctionnement incorrect. Le paramètre du processus doit être ajusté en fonction de la situation réelle.
Numéro V : Défauts de retassure – Qu’est-ce qu’une retassure ?
Les affaissements sont des rétrécissements inégaux de la surface causés par l'épaisseur inégale de la paroi du produit en plastique.
Analyse des défauts et méthode de correction
- Les conditions de moulage par injection ne sont pas correctement contrôlées. Augmentez correctement la pression et la vitesse d'injection, augmentez la densité de compression du matériau fondu, prolongez le temps d'injection et de maintien de la pression, compensez le naufrage du matériau fondu et augmentez la capacité tampon de l'injection. Cependant, la pression ne doit pas être trop élevée, sinon des marques convexes apparaîtront. Si des marques d'affaissement se trouvent autour de la porte, la prolongation du temps de maintien de la pression peut éliminer les marques d'affaissement ; si des marques d'affaissement se trouvent sur la paroi épaisse, la prolongation du temps de refroidissement du produit en plastique dans le moule ; si les marques d'affaissement autour de l'insert sont causées par un retrait partiel du matériau fondu, la raison principale est que la température de l'insert est trop basse ; essayez d'augmenter la température de l'insert pour éliminer les marques d'affaissement ; si les marques d'affaissement sont causées par une alimentation insuffisante en matériau, augmentez le matériau. En plus de tout cela, le produit en plastique doit être entièrement refroidi dans le moule.
- Défauts de moule. En fonction de la situation réelle, agrandissez correctement la section transversale de la porte et du canal, et la porte doit être dans une position symétrique. L'entrée d'alimentation doit être dans la paroi épaisse. Si des marques d'affaissement apparaissent loin de la porte, la cause est généralement que l'écoulement de la matière fondue n'est pas régulier à une certaine position du moule, ce qui entrave la transmission de la pression. Pour résoudre ce problème, agrandissez le système d'injection pour permettre au canal de s'étendre jusqu'à la position des marques d'affaissement. Pour les produits à parois épaisses, une porte de type aile est préférée.
- Les matières premières ne peuvent pas répondre aux exigences de moulage. produits en plastique pour des normes de finition élevées, une résine à faible retrait doit être utilisée, ou le dosage approprié de lubrifiant peut également être ajouté à la matière première.
- Conception incorrecte de la structure du produit. L'épaisseur de la paroi du produit doit être uniforme ; si l'épaisseur de la paroi diffère beaucoup, le paramètre de structure du système d'injection ou l'épaisseur de la paroi doivent être ajustés.
Numéro VI : Flow Mark – Qu’est-ce que Flow Mark ?
La marque d'écoulement est une trace linéaire sur la surface d'un produit moulé qui indique la direction d'écoulement du matériau en fusion.
Analyse des défauts et méthode de correction
- Les marques d'écoulement en forme d'anneau sur la surface de la pièce en plastique avec la porte comme centre sont causées par un mauvais mouvement d'écoulement. Pour remédier à ce type de marque d'écoulement, augmentez la température du moule et de la buse, augmentez le taux d'injection et la vitesse de remplissage, prolongez le temps de maintien de la pression ou ajoutez un élément chauffant au niveau de la porte pour augmenter la température autour de la porte. Une extension appropriée de la zone de la porte et du canal peut également fonctionner, tandis que la section de la porte et du canal est de préférence circulaire, ce qui peut garantir le meilleur remplissage. Cependant, si la porte se trouve dans la zone faible de la pièce en plastique, elle sera carrée. De plus, un grand puits de limace froide doit être placé au bas de l'orifice d'injection et à l'extrémité du canal ; plus l'influence de la température du matériau sur les performances d'écoulement de la masse fondue est grande, plus il faut prêter attention à la taille du puits de limace froide. Le puits de limace froide doit être placé à l'extrémité de la direction d'écoulement de la masse fondue à partir de l'orifice d'injection.
- Les marques d'écoulement tourbillonnant sur la surface de la pièce en plastique sont causées par l'écoulement irrégulier du matériau fondu dans le canal d'injection. Lorsque le matériau fondu s'écoule du canal d'injection à section étroite vers la cavité à section plus grande ou que le canal d'injection du moule est étroit et que la finition est médiocre, le flux de matériau est susceptible de former des turbulences, ce qui entraîne une marque d'écoulement tourbillonnant sur la surface de la pièce en plastique. Pour remédier à ce type de marque d'écoulement, réduisez la vitesse d'injection de manière appropriée ou contrôlez la vitesse d'injection en mode lent-rapide-lent. La porte du moule doit être à paroi épaisse et de préférence sous la forme d'une poignée, d'un ventilateur ou d'un film. Le canal d'injection et la porte peuvent être agrandis pour réduire la résistance à l'écoulement du matériau.
- Les traces d'écoulement en forme de nuage sur la surface de la pièce en plastique sont causées par des gaz volatils. Lorsque de l'ABS ou d'autres résines copolymérisées sont utilisées, si la température de traitement est élevée, le gaz volatil produit par la résine et le lubrifiant formera des traces d'ondulation en forme de nuage sur la surface du produit. Afin de résoudre ce problème, il est nécessaire de réduire la température du moule et du cylindre, d'améliorer la ventilation du moule, de réduire la température du matériau et la vitesse de remplissage, d'agrandir correctement la section de la porte et d'envisager de changer le type de lubrifiant ou de réduire l'utilisation de lubrifiant.
Numéro VII : Les traces de fibres de verre – Qu'est-ce que les traces de fibres de verre
Aspect de la surface : Produits de moulage en plastique avec de la fibre de verre présentent divers défauts de surface, tels qu'une couleur terne et terne, une texture grossière et des taches métalliques brillantes, etc. Ceux-ci sont particulièrement évidents dans la partie convexe de la zone d'écoulement du matériau, à proximité de la ligne de joint où le fluide se retrouve.
Cause physique
Si la température d'injection et la température du moule sont trop basses, le matériau contenant des fibres de verre a tendance à se solidifier rapidement sur la surface du moule et les fibres de verre ne fondront plus dans le matériau. Lorsque deux flux se rencontrent, l'orientation des fibres de verre est dans la direction de chaque flux, ce qui entraînera une texture de surface irrégulière à l'intersection, entraînant la formation de joints ou de lignes d'écoulement.
Ce type de défaut est plus évident si la matière fondue n'est pas complètement mélangée dans le cylindre. Par exemple, si la course de la vis est trop longue, la matière sous-mélangée sera également injectée.
Les causes liées aux paramètres du processus et aux améliorations peuvent être identifiées :
- La vitesse d'injection est trop faible. Pour augmenter la vitesse d'injection, envisagez d'utiliser une méthode d'injection en plusieurs étapes comme le mode lent-rapide.
- La température du moule est basse ; l'augmentation de la température du moule pourrait améliorer les stries de fibre de verre.
- La température du matériau fondu est trop basse ; augmentez la température du cylindre et la contre-pression de la vis pour l'améliorer.
- La température du matériau fondu varie beaucoup : si le matériau fondu n'est pas complètement mélangé, augmentez la contre-pression de la vis, réduisez la vitesse de la vis et utilisez le canon le plus long pour raccourcir la course.
Numéro VIII : Marques d’éjection : Que sont les marques d’éjection ?
Aspect de surface : Les phénomènes de blanchiment sous contrainte et de remontée de contrainte se retrouvent du côté du produit qui fait face à la buse, c'est-à-dire là où se trouve la tige d'éjection du côté éjecteur du moule.
Cause physique
Si la force de démoulage est trop élevée ou si la surface de la tige d'éjection est relativement petite, la pression de surface sera ici très élevée, provoquant une déformation et éventuellement un blanchiment au niveau de la zone d'éjection.
Les causes liées aux paramètres du processus et aux améliorations peuvent être appliquées :
- La pression de maintien est trop élevée ; diminuez la pression tout en maintenant la pression.
- Le temps de maintien de la pression est trop long ; raccourcissez le temps de maintien de la pression.
- Le temps de maintien du pressostat est trop tardif. Avancez le pressostat de maintien
- Le temps de refroidissement est trop court ; augmenter le temps de refroidissement
Les causes liées à la conception et aux améliorations du moule peuvent être appliquées :
- L'angle de dépouille n'est pas suffisant ; augmentez l'angle de dépouille selon les spécifications, en particulier dans la zone de la marque d'éjection.
- La finition de surface est trop rugueuse ; le moule doit être bien poli dans le sens du démoulage.
- Un vide se forme du côté de l'éjection. Installez une soupape d'air dans le cor
Conclusion
En raison des propriétés spécifiques des plastiques, moulage par injection Il s'agit d'un processus technologique très complexe. Contrairement au procédé apparenté de moulage sous pression des métaux, il ne s'agit pas d'un procédé mécanique mais d'un procédé mécanique et physique. Dans le procédé de moulage par injection, on obtient une pièce moulée. Elle se caractérise non seulement par une forme spécifique, mais aussi par une structure spécifique résultant de l'écoulement de la matière plastifiée dans le moule et du déroulement de sa solidification.
Étant donné que ces processus se déroulent sous forme d'injection, le concepteur de cet outil doit prendre en compte, en plus des problèmes typiquement mécaniques, des problèmes liés à la nature physique de la transformation du matériau. La construction d'une forme fonctionnelle rationnelle exige, en même temps, de la part du concepteur une connaissance approfondie des capacités techniques de la presse à injecter, car il s'agit d'une machine aux possibilités extrêmement riches offertes par son équipement et ses nombreux programmes de travail.
Si vous souhaitez en savoir plus, rendez-vous sur nos autres moule en plastique page. Si vous cherchez services de moulage par injection, n'hésitez pas à nous faire part de vos besoins pour un devis.
Si vous avez un nouveau projet ou un projet en cours qui nécessite un Entreprise chinoise de moulage par injection Pour vous accompagner, nous sommes à votre disposition. Appelez-nous ou envoyez-nous un e-mail.
Un fabricant de moules en plastique est un fabricant professionnel ou une entreprise qui conçoit et fabrique des moules en plastique utilisés pour produire des produits en plastique par le biais d'un processus de moulage par injection. Le fabricant de moules en plastique utilise diverses méthodes, machines et techniques pour fabriquer des moules en plastique durables, précis et capables de produire des milliers, voire des millions de produits en plastique de la même qualité.
Parmi les processus de fabrication de moules qu'un mouliste en plastique peut effectuer, citons : la conception de moules, l'analyse de l'écoulement des moules, l'usinage CNC, l'usinage EDM, l'usinage en mousse, l'usinage par fraisage, l'ajustement, l'assemblage et le test des moules, et les modifications apportées pour améliorer les performances des moules afin d'obtenir un moule final parfait ; toutes ces tâches sont effectuées par le mouliste en plastique professionnel. Les fabricants de moules en plastique jouent un rôle crucial dans les industries manufacturières.
Quels sont les avantages de l’utilisation d’un fabricant de moules en plastique ?
L'utilisation d'un fabricant de moules en plastique pour vos besoins de fabrication présente un certain nombre d'avantages qu'il convient de prendre en considération.
Tout d'abord, les fabricants de moules en plastique sont en mesure de produire des moules en plastique extrêmement précis et adaptés à vos exigences de conception particulières. Vos problèmes seront ainsi résolus, car cela garantit que le produit final que vous fabriquez est de haute qualité et cohérent.
Deuxièmement, l'utilisation d'un fabricant de moules en plastique peut également contribuer à réduire les coûts de production à long terme, ce qui nous amène à notre deuxième point. Une fois le moule original construit, il peut être utilisé à plusieurs reprises pour produire de grandes quantités d'articles en plastique, ce qui permet d'économiser du temps et de l'argent sur les frais d'outillage et d'installation. Bien que le coût initial du moule en plastique soit important, il peut être utilisé pour produire des milliers de produits en plastique.
En outre, les fabricants de moules en plastique peuvent contribuer à l'amélioration de l'efficacité de la production en accélérant le processus de fabrication proprement dit. Lorsque vous utilisez des moules sur mesure, vous êtes en mesure de fabriquer des produits à un rythme plus rapide et avec moins de déchets, ce qui conduit en fin de compte à une réduction des déchets et à une augmentation de la production et de la rentabilité.
Types de moules en plastique
Il existe différents types de moules en plastique ; chacun d'entre eux a des utilisations particulières. Nous allons examiner quelques-uns des types de moules en plastique les plus utilisés sur le marché.
moules d'injection : Les moules à injection sont le type de moules en plastique le plus fréquemment utilisé dans le monde des affaires. Les fabricants les utilisent pour produire une large gamme de produits en plastique, tels que des articles ménagers, des composants électroniques et des pièces automobiles. La moitié fixe d'un moule à injection et la moitié mobile du moule se serrent simultanément pendant le processus de moulage. Nous appliquons une pression élevée pour injecter du plastique fondu dans la cavité du moule, ce qui lui permet de refroidir et de durcir pour prendre la forme souhaitée.
Moules soufflés : Les bouteilles, les conteneurs et les réservoirs ne sont que quelques exemples de produits en plastique creux fabriqués à l'aide de moules soufflés. Pour que le plastique se dilate et prenne la forme du moule, de l'air est injecté dans une paraison, qui est un tube creux rempli de plastique fondu, à l'intérieur de la cavité du moule. Nous pouvons construire des moules de soufflage à partir de divers matériaux, notamment l'acier, le plastique et l'aluminium, en fonction des besoins.
Moules à compression : Les moules à compression produisent des articles en plastique d'une précision et d'une résistance exceptionnelles. La cavité du moule reçoit une feuille ou une pastille de plastique chauffée, qui subit une pression de compression intense pour prendre la forme souhaitée. Les fabricants utilisent largement les moules à compression pour produire des produits de conception complexe et de dimensions précises, comme les pièces d'automobiles et d'avions.
Moules rotatifs : Également appelés rotomoules, ces moules permettent de créer de grands objets creux en plastique, tels que des équipements d'aires de jeux, des réservoirs et des conteneurs. La procédure consiste à chauffer la chambre du moule et à la faire tourner dans deux directions perpendiculaires afin que le plastique en fusion recouvre uniformément la surface interne du moule. Les moules rotatifs sont incroyablement adaptables et peuvent créer des formes complexes avec une épaisseur de paroi constante.
Moules de thermoformage : Les fabricants utilisent des moules de thermoformage pour créer des produits à parois fines en plastique, tels que des récipients à clapet, des plateaux d'emballage et des gobelets jetables. Un bouchon mécanique ou une pression sous vide aide à former une feuille thermoplastique sur une cavité de moule après l'avoir chauffée jusqu'à ce qu'elle devienne malléable. Les moules pour le thermoformage sont économiques et conviennent à la fabrication à grande échelle.
Les différents secteurs d'activité se prêtent à différents types de moules en plastique personnalisés, chacun présentant des avantages et des limites qui lui sont propres. Un mouliste plastique peut vous aider à choisir le meilleur moule en fonction de votre projet. Si vous ne savez pas quel type de moule utiliser, contactez-nous pour un devis, et nous vous proposerons un type de moule adapté à votre projet.
Quel est le processus de fabrication d’un moule en plastique ?
En règle générale, le processus de création d'un moule en plastique comporte les étapes simples suivantes :
Conception de pièces : L'étape initiale de la création d'une moule en plastique est de concevoir la pièce que vous souhaitez utiliser ou vendre.
Prototype : Une fois la conception achevée, il est essentiel de tester sa fonctionnalité et d'apporter toutes les améliorations nécessaires. Il peut s'agir de tester le prototype par impression 3D ou par usinage CNC jusqu'à ce qu'il fonctionne parfaitement.
Conception du moule : Le fabricant de moules en plastique doit commencer la conception du moule dès que la conception de la pièce est approuvée. Le mouliste utilisera cette conception pour développer et fabriquer un moule qui donne une forme précise à la pièce en plastique requise.
Usinage : Une fois la conception du moule achevée et approuvée par le client, les composants du moule sont fabriqués en métal ou dans d'autres matériaux, tels que le cuivre, l'aluminium, etc., à l'aide de machines CNC (à commande numérique par ordinateur), d'usinage par électroérosion, d'usinage par découpe au fil, d'usinage à la mousse, de polissage, etc.
Assemblage : Une fois le processus d'usinage terminé, les pièces usinées sont insérées dans la base de moulage pour former le moule. Il peut s'agir de fixer les composants en place à l'aide de boulons, de soudures ou d'autres techniques.
Essais : Le moule est soumis à des essais pour s'assurer de sa fonctionnalité et de sa capacité à produire la bonne pièce en plastique. Pour améliorer les performances, il peut être nécessaire de modifier ou d'ajuster les composants du moule.
Finition : pour s'assurer que le moule répond aux normes requises, il peut subir un revêtement, un polissage ou d'autres traitements destinés à prolonger sa durée de vie.
Qualification : Le moule répond aux exigences requises et peut produire des composants en plastique de haute qualité.
La fabrication d'un moule en plastique est une opération difficile qui nécessite de la précision, des connaissances et certains outils. Un fabricant de moules en plastique compétent possède l'expertise et les compétences requises pour garantir le succès de votre processus de fabrication de plastique.
La moisissure est un champignon qui se développe sur divers matériaux. Les moisissures obtiennent de l'énergie en consommant d'autres substances, contrairement aux plantes, qui tirent leur nourriture de la photosynthèse. Par exemple, s'il y a de la moisissure sur votre pain, elle est probablement en train de manger le pain lui-même. De même, il est possible que le bois et d'autres composants des murs soient à l'origine de la moisissure.
Si vous avez un projet qui nécessite des moules en plastique, la meilleure solution est de trouver un fabricant de moules en plastique professionnel qui fabriquera les moules pour vous.
Si vous êtes intéressé par les fabricants de moules à injection plastique mais ne savez pas où les chercher, vous devriez envisager quelques options spécifiques. Vous pouvez être sûr d'obtenir la meilleure qualité et le meilleur rapport qualité-prix en choisissant ces fabricants de moules à injection spécifiques plutôt que d'autres, ce qui est évidemment essentiel pour tout le monde.
Mettre en jeu l'utilisation de mouleurs en plastique :
Les Fabricant de moules en plastique Cette ressource est considérée comme la meilleure source d'information sur Internet en ce qui concerne les machines et les résines. Le processus de moulage par injection et l'industrie des plastiques sont véritablement devenus une incroyable industrie de plusieurs milliards de dollars, et le moulage par injection a rendu possible la construction bon marché et durable de divers articles de consommation et industriels, qui ont eu un impact profond sur la société.
L'entreprise vise à former les clients et les ingénieurs en fournissant des informations sur les fabricants, les résines, les matériaux et d'autres sujets liés au moulage par injection.
L'équipement utilisé pour le moulage par injection :
Leurs produits comprennent des cires pour moules, des solutions barrières filmogènes à base d'alcool polyvinylique ou de PVA, produits de polissage pour moules et les produits de polissage, ainsi que les nettoyants pour moisissures. L'avantage de ces produits est que la plupart d'entre eux sont respectueux de l'environnement et ne contiennent que des ingrédients non dangereux.
La fabrication de moules par injection consiste à placer le matériau de moulage dans une cavité ouverte et chauffée. Ensuite, une force supérieure puissante ou un bouchon ferme le moule, en appliquant une pression pour forcer le matériau à entrer en contact avec toutes les zones du moule, et en maintenant une chaleur et une pression adéquates jusqu'à ce que le matériau de moulage durcisse complètement.
Les Fabricant de moules en plastique Le procédé de fabrication de moules en plastique utilise des résines plastiques à un stade partiellement durci, sous forme de granulés, de masses pâteuses ou de préformes. Il est essentiel de comprendre que la machine à mouler les plastiques est une méthode de moulage à haut volume et à haute pression qui répond à divers objectifs, notamment le moulage de renforts en fibre de verre complexes et très résistants.
Sincere Tech, nous sommes l'un des principaux fournisseurs de produits en plastique. usine de moules en Chine. Nous proposons une large gamme de moules d'injection plastique sur mesure, de moules de coulée sous pression, de pièces métalliques, d'usinage CNC et de composants de moules. Grâce à des investissements continus dans la recherche et le développement, nous fournissons des solutions de pointe qui répondent aux besoins changeants de nos clients. En tant que l'un des meilleurs moule d'injection Fournisseurs en Chine, nous sommes fiers de notre engagement envers l'excellence.
La qualité est de la plus haute importance pour nous. Pour nous assurer que nous fabriquons des moules de haute qualité, nous utilisons une machine à mesurer CMM pour mesurer tous les composants du moule, les électrodes et les pièces de moulage finales. Pour nous assurer que toutes les dimensions sont conformes aux tolérances, nous testons le fonctionnement des pièces et des matériaux afin de nous assurer que la pièce finale répondra à vos exigences.
Lorsque vous vous associez à Sincere Tech en tant que partenaire privilégié Fabricant de moules en ChineVous pouvez compter sur le plus haut niveau de professionnalisme, d'expertise et d'innovation. Nous nous engageons à transformer vos idées en réalité, en fabriquant des produits de premier ordre qui se distinguent par leurs performances, leur durabilité et leur rentabilité.
Nos capacités élargies comprennent :
- Prototypage rapide : Nous proposons des services de prototypage rapide (impression 3D ou usinage CNC de prototypes) afin de transformer rapidement vos ébauches en prototypes utilisables et en tests, en suggestions de reconception, etc.
- Usinage CNC de précision : Grâce à nos machines CNC de pointe, nous pouvons créer des composants de moules de haute qualité avec des tolérances serrées, ce qui garantit la tolérance et la précision des produits moulés par injection.
- Surmoulage: Nous réalisons des surmoulages pour certains outils à manche ; certains surmoulages sont également utilisés dans les moules de moulage sous pression. Contactez-nous pour un devis pour votre projet de surmoulage.
- Moulage par insertion:Le moulage par insertion est similaire au surmoulage mais sera un peu différent ; le moulage par insertion utilise normalement des pièces métalliques comme substrat et le surmoulage utilise des pièces en plastique comme substrat.
- Moulage en deux étapes: Le moulage en deux temps permet de produire des composants complexes et multi-matériaux en une seule opération, ce qui réduit les besoins d'assemblage et augmente les possibilités de conception. Le moulage en deux temps est plus complexe que le moulage par insertion ou le surmoulage, et il nécessite des machines de moulage par injection en deux temps.
- Services à valeur ajoutée : Outre le moulage par injection, le moulage sous pression et l'usinage, nous proposons une gamme de services à valeur ajoutée, notamment la sérigraphie des produits, la peinture, l'assemblage, les essais, les certificats, l'emballage et le soutien logistique, afin de rationaliser votre chaîne d'approvisionnement et de réduire les coûts.
Faites appel à Sincere Tech China Mold Maker pour vos besoins en matière de moulage par injection, de moulage sous pression et d'usinage ; nous vous offrirons la meilleure qualité et des délais de livraison rapides. Contactez-nous pour un devis dans les 24 heures.
À propos de nous
Sincere Tech est un contrat fournisseur de moules en Chine, qui propose des services de recherche et de développement de nouveaux produits électroniques ainsi que des services d'assemblage. Contactez-nous pour plus d'informations.
Service complet pour le développement de nouveaux produits, depuis la conception des pièces, la conception des circuits imprimés, le prototypage, les essais, la fabrication des moules, des matrices et des outillages, la production massive, l'assemblage, l'inspection et l'emballage.
Contact
Building 1, No. 30 Huan Zhen Rd, Shang Dong village, Qi Shi Town, Dongguan City, Guangdong province China, 523000
Mobile : +86 135 30801277
Weichat/whatsup No. : + 86 135 3080 1277
Courriel : info@plasticmold.net
Web : https://plasticmold.net
Commentaires de nos clients
"Bonjour Steve, les moules fonctionnent très bien, bon travail, j'espère que vous vous portez bien, dès que j'aurai un nouveau projet, je m'adresserai à vous.
Client de Hansaplastic aux USA-----
"Nous sommes très satisfaits de votre gestion et de votre communication en anglais, vous êtes remarquables dans la résolution des problèmes et dans la rapidité de réponse, franchement, vous êtes les meilleurs. moule en plastique et l'entreprise de moulage pour laquelle j'ai travaillé".
Client du Canada------
- Les 10 premières entreprises de moulage par injection dans l'Indiana2024年11月20日 - après-midi1:02
- Les 10 meilleures entreprises de moulage par injection de plastique dans le Michigan2024年11月20日 - après-midi12:43
- Les 9 meilleures entreprises de moulage par injection de plastique à Chicago2024年11月16日 - après-midi3:29
- Les 9 meilleures entreprises de moulage par injection du Wisconsin2024年11月10日 - après-midi1:03
- Les 10 meilleures entreprises de moulage par injection de l'Ohio2024年11月10日 - suis9:44