Moulage de caoutchouc de silicone liquide
Méthode de Caoutchouc de silicone liquide Moulage
Lorsque nous parlons de caoutchouc de silicone sous forme liquide (LSR), il s'agit d'un réseau divisé en deux parties. Dans ce réseau, de longues chaînes de polysiloxane sont supportées par de la silice. La partie A contient un catalyseur au platine et la partie B contient du méthylhydrogénosiloxane comme agent de réticulation et un inhibiteur d'alcool. Les caoutchoucs de silicone sont des polymères à deux parties et peuvent contenir des charges pour améliorer les propriétés ou réduire les coûts. Le caoutchouc de silicone est pour la plupart non réactif, stable et imperméable aux conditions et températures extrêmes de −55 à 300 °C (−70 à 570 °F) tout en conservant ses propriétés.
Définition
Lorsque nous définissons le caoutchouc de silicone sous forme liquide, il s'agit d'un polymère de nature inorganique encadré par du silicium (Si), de l'oxygène (O), du carbone (C) et de l'hydrogène (H). La chaîne synthétique vitale appelée la colonne vertébrale est encadrée par du silicium et de l'oxygène, appelé siloxane. Il s'agit d'un silicone durci au platine de haute qualité avec une douceur brillante. Il est fréquemment infusé dans une cavité de moule en silicone pour fabriquer diverses pièces avec une grande précision. En général, le caoutchouc de silicone liquide a une faible déformation rémanente, une bonne stabilité et une résistance aux températures extrêmes de chaleur et de froid. Ce matériau est principalement utilisé pour créer des joints, des membranes d'étanchéité, des connecteurs électriques, des connecteurs multibroches, des produits pour bébés où des surfaces lisses sont nécessaires.
La nature inorganique du LSR le rend idéal pour les applications médicales et de contact avec la peau. Le LSR a la capacité de se combiner avec d'autres groupes chimiques, ce qui lui permet d'atteindre des performances robustes. Le LSR surpasse de nombreux autres élastomères et est utilisé dans les boutons-poussoirs ou les applications de clavier, et est préféré pour les applications de pompage, en particulier en cas de contact avec des fluides corporels ou des substances chimiques.
Moulage par injection de caoutchouc de silicone liquide
Il s’agit d’un processus très mécanisé. Moulage par injection de silicone liquide Le LSR utilise une méthode de mélange mécanique qui mélange un composé de matériau LSR durci au platine à deux composants qui s'écoule dans un moule. Cependant, en raison de la nature visqueuse du LSR, il se traite facilement et est parfaitement adapté à la production en grande série, à la qualité constante des pièces et à une productivité améliorée. L'outil d'injection LSR est logé dans une presse de moulage par injection spécifique LSR, spécialement conçue pour un contrôle précis de la taille de la dose et permet la production constante de composants en caoutchouc de silicone liquide. En raison de ses propriétés et de sa facilité de traitement, le caoutchouc de silicone liquide est devenu le matériau idéal pour les caractéristiques de conception complexes et les applications critiques exigeantes.
Procédé de moulage par injection LSR
Ce procédé est de nature thermodurcissable et est utilisé pour fabriquer des pièces et des produits en silicone flexibles, durables et résistants à la chaleur. Dans ce procédé, deux composés sont mélangés, qui sont généralement constitués du silicone formant la base et du catalyseur au platine. Ensuite, le mélange est injecté et durci à chaud à l'intérieur d'un moule pour créer des pièces en silicone flexibles. Cependant, ces deux composés nécessitent un mélange distributif intensif tout en les maintenant à basse température avant de les pousser dans une cavité chauffée. Le caoutchouc de silicone liquide est durci par la chaleur, produisant des pièces ou des produits solides.
Ce procédé est largement utilisé dans diverses industries, notamment l'automobile, la médecine, les biens de consommation et l'électronique. Le procédé de moulage par injection LSR comprend principalement les étapes principales suivantes.
1. Préparation du matériel
Composés LSR:Le LSR est un composé en deux parties, généralement appelé matériau de formation de base et catalyseur, qui est généralement à base de platine. Ces parties sont mélangées dans un rapport 1:1 et peuvent inclure des composants supplémentaires tels que des pigments ou des additifs.
Stockage et manutention : Les composants LSR sont stockés dans des conteneurs ou des cartouches. Un conteneur contient le matériau formant la base et un autre conteneur abrite le catalyseur, généralement à base de platine. Une manipulation appropriée est essentielle pour éviter la contamination et garantir des propriétés matérielles uniformes.
2. Mélange et dosage
Unité de mélange : Une unité de mélange spécialisée permet de combiner avec précision les deux composés. Cette unité peut également incorporer des pigments ou d'autres additifs selon les besoins.
Mélangeur statique : Le LSR mélangé passe ensuite dans un mélangeur statique, ce qui garantit une homogénéisation complète des composants. Cette étape est essentielle pour garantir un durcissement et des propriétés homogènes du produit final.
Mesure: Au cours de cette étape importante, le LSR mélangé est dosé dans l'unité d'injection. Un dosage précis est essentiel pour maintenir des tailles d'injection uniformes et réduire le gaspillage de matériau.
3. Machine de moulage par injection
- Unité d'injection : L'unité d'injection est spécialement conçue pour l'injection de LSR. Le LSR a une faible viscosité et nécessite des conceptions de vis spéciales. Au cours de cette étape, le matériau est poussé à l'intérieur de la cavité du moule.
- Unité de serrage : Dans cette étape, la pince est utilisée pour maintenir le moule et le maintenir fermé lors de l'injection. Néanmoins, la puissance requise dépend de la taille et de la complexité de la pièce.
4. Conception du moule
- Considérations matérielles : Les moules pour LSR doivent être conçus pour supporter les températures et tensions élevées appliquées pendant le processus de durcissement. Ils sont la plupart du temps fabriqués à partir d'acier ou d'aluminium d'excellente qualité.
- Cavité et noyau : Le moule d'injection de silicone comprend des cavités qui sont des pièces de forme négative et des noyaux qui sont des pièces de forme positive. Ceux-ci doivent être usinés avec précision pour obtenir les aspects de pièce et la finition de surface idéaux.
- Ventilation : L'air est emprisonné et doit être évacué pour éviter des défauts tels que des bulles d'air ou des vides dans le produit final. Il est donc important d'assurer une ventilation adéquate.
- Système d'éjection : Cette étape consiste à retirer la pièce du moule qui est durcie. Le système d'éjection doit être soigneusement conçu pour manipuler les pièces LSR flexibles et collantes.
5. Injection et durcissement
- Processus d'injection : Le moule est fermé fermement et serré avec la force appropriée. Le LSR est ensuite injecté dans les cavités du moule à grande vitesse. Le moule est ensuite rempli et le matériau excédentaire est ensuite éliminé.
- Processus de durcissement : La température est maintenue élevée (généralement entre 160 et 200°C) pour commencer le processus de durcissement. Le temps de durcissement dépend de l'épaisseur et de la forme de la pièce. Il varie généralement de quelques secondes à plusieurs minutes.
6. Démoulage
- Refroidissement: Une fois le durcissement terminé, le moule est refroidi pour travailler avec l'expulsion des pièces et éviter toute déformation.
- Ouverture: Après cela, le moule est ouvert doucement pour éviter d'endommager les pièces délicates du LSR.
- Éjection: Au cours de cette étape, les pièces sont éjectées du moule à l'aide du système d'éjection. Il faut manipuler les pièces avec précaution, car elles sont encore chaudes et peuvent être légèrement malléables.
7. Post-traitement
- Inspection: Au cours de cette étape, chaque pièce est inspectée pour déceler des défauts tels que des bavures, des bulles d'air ou un remplissage incomplet. Des méthodes d'inspection automatisées ou manuelles peuvent être utilisées.
- Garniture: Ensuite, l'excédent de matière, appelé bavure, est éliminé des pièces. Cette opération peut être effectuée manuellement ou à l'aide d'un équipement automatisé.
- Opérations secondaires : des processus supplémentaires tels que le collage, l'assemblage ou le traitement de surface peuvent être effectués en fonction de l'application et des exigences.
8. Contrôle de la qualité
- Essai: Afin de garantir que les pièces livrées répondent aux spécifications requises, elles sont soumises à différents tests. Ces tests comprennent des tests de propriétés mécaniques, des contrôles dimensionnels et des examens visuels.
- Documentation: Des enregistrements détaillés du processus de moulage, des lots de matériaux et des résultats du contrôle qualité sont conservés régulièrement à des fins de traçabilité et de conformité aux normes de l'industrie.
9. Emballage et expédition
- Conditionnement:Les pièces finies sont ensuite soigneusement emballées pour les protéger pendant le transport. Les techniques d'emballage varient en fonction de la taille, de la forme et de la sensibilité de la pièce.
- Expédition: Les pièces emballées sont ensuite expédiées aux clients ou aux installations de traitement ultérieures, garantissant une livraison dans les délais et préservant l'intégrité des pièces.
Avantages du moulage par injection de LSR
Ce procédé offre quelques avantages principaux, qui sont les suivants :
1. Précision et cohérence
Le moulage par injection LSR permet d'obtenir des valeurs élevées de cohérence et de précision dans la production de pièces complexes, élaborées et détaillées. Ce procédé permet des tolérances strictes et une réplication précise des moules, garantissant l'uniformité de tous les lots.
2. Vaste gamme d'applications
Ce matériau offre de nombreuses possibilités d'application car il est flexible et peut être utilisé dans différents secteurs, notamment l'automobile, le secteur clinique, le matériel informatique, les produits de consommation et bien plus encore. La flexibilité offerte par le LSR le rend adapté à la production de tout, des implants médicaux aux joints automobiles en passant par les composants électroniques grand public.
3. Durabilité et résistance
Ces pièces se distinguent par leur solidité et leur résistance. Elles peuvent supporter des températures extrêmes, des composés synthétiques agressifs et une exposition prolongée aux rayons UV sans compromettre leurs propriétés intégrales pendant une longue période, ce qui les rend idéales pour de nombreuses applications.
4. Biocompatibilité
Ces matériaux sont biocompatibles et répondent aux exigences des normes de qualité médicale. Cette qualité les rend adaptés aux applications cliniques et médicales telles que les implants, les outils chirurgicaux et les gadgets cliniques portables. De plus, ils sont hypoallergéniques et sans danger pour un contact prolongé avec la peau.
5. Résistance chimique
Ces matériaux offrent une excellente protection contre de nombreux produits synthétiques, notamment les solvants, les huiles et les agents de nettoyage. Cette propriété les rend adaptés à une utilisation dans des conditions où l'exposition aux substances chimiques est normale, comme dans les environnements automobiles et industriels modernes.
6. Flexibilité et élasticité
Ces pièces ont la propriété d'une élasticité et d'une flexibilité remarquables, ce qui leur permet de se déformer et de retrouver leur forme unique sans distorsion durable. Cette adaptabilité les rend idéales pour les applications d'étanchéité et de joint où une étanchéité solide et étanche est requise.
7. Temps de cycle rapides
Cette méthode offre un temps de traitement plus rapide que les méthodes de moulage de caoutchouc conventionnelles. Cela permet une production élevée avec des délais d'exécution rapides et en même temps une rentabilité optimale.
8. Réduction des déchets
Le moulage par injection LSR génère un minimum de déchets par rapport aux autres procédés de fabrication. La possibilité de contrôler précisément le flux de matière et d'optimiser la conception des moules minimise le gaspillage de matière. Par conséquent, cela conduit à des économies de coûts et à des avantages environnementaux.
9. Liberté de conception
Ce procédé permet de développer des formes et des géométries complexes qui pourraient être difficiles à réaliser avec d'autres méthodes de fabrication. Cette liberté de conception permet de créer des modèles d'articles imaginatifs et des choix de personnalisation.
10. Finition de surface
Ces pièces présentent une finition de surface lisse et impeccable dès leur sortie du moule. Par conséquent, cela réduit le besoin de tâches de finition secondaires telles que le nettoyage ou la peinture. Cela permet d'économiser du temps et des coûts de main-d'œuvre et de rendre le processus rentable tout en garantissant un produit final de haute qualité.
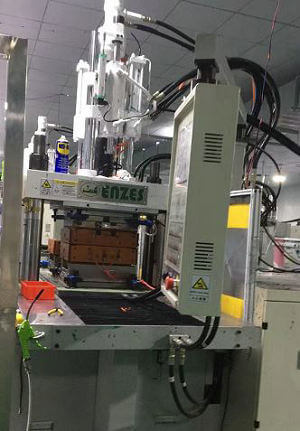
machines de moulage par injection de silicone
Limitations du moulage du caoutchouc de silicone liquide
Ce procédé offre divers avantages, cependant comme tout procédé de fabrication, il présente certaines limites qui sont les suivantes :
1. Investissement initial élevé
La mise en place d'un procédé de moulage par injection LSR nécessite un investissement initial important, principalement en termes d'équipements, de moules et d'infrastructures spécialisés. Cela peut donc constituer un obstacle pour les fabricants à petite échelle ou ceux qui disposent d'un capital limité.
2.Conception de moule complexe
Les moules LSR sont spécialisés, complexes et élaborés en raison de la faible viscosité du matériau et de sa température de durcissement élevée. La conception de ces moules nécessite donc une expertise et une précision qui peuvent augmenter les coûts et les délais.
3. Options matérielles limitées
Bien que le LSR offre d'excellentes propriétés telles que la flexibilité, la résistance à la chaleur et la biocompatibilité, ses options de matériaux sont quelque peu limitées par rapport à d'autres types de caoutchouc. Par conséquent, cela peut restreindre la gamme d'applications dans lesquelles le LSR peut être utilisé efficacement.
4. Temps de durcissement
Le temps de durcissement du LSR peut être plus long que celui des autres méthodes de moulage du caoutchouc. Cela peut avoir une incidence sur le cycle de production et le rendement total, en particulier pour la fabrication en grande série.
Applications
Il s'agit d'un procédé unique qui présente un grand nombre d'applications dans diverses entreprises en raison de ses propriétés et avantages novateurs. Les principales applications sont les suivantes :
1.Dispositifs médicaux
Il est largement et généralement utilisé dans le secteur clinique pour la fabrication de divers dispositifs et pièces tels que des cathéters, des tubes, des joints, des joints d'étanchéité, des voiles respiratoires et des dispositifs implantables. Des propriétés telles que la biocompatibilité, la stérilisabilité et la robustesse le rendent adapté aux applications nécessitant une précision et une qualité inébranlable dans les conditions cliniques.
2. Produits de soins pour bébé
En raison de sa sécurité, de son adaptabilité et de sa simplicité de stérilisation, le LSR est généralement utilisé dans la fabrication d'articles de puériculture tels que des sucettes, des tétines pour biberons et des ustensiles de puériculture. Ces articles nécessitent souvent des matériaux qui doivent avoir les propriétés d'être non nocifs, hypoallergéniques et imperméables aux températures élevées, ce que le LSR offre.
3. Électronique
Il est également utilisé dans le matériel informatique pour encapsuler et protéger les pièces sensibles de l'humidité, de la poussière et d'autres variables environnementales. Il est utilisé dans des applications telles que les claviers, les joints, les joints d'étanchéité, les connecteurs et les capots de protection en raison de ses propriétés de protection électrique étonnantes, de sa stabilité thermique et de sa protection contre les composés chimiques dangereux.
4. Configurations automobiles
Il est largement utilisé dans les applications automobiles pour fournir des pièces telles que des joints, des joints d'étanchéité, des connecteurs et des amortisseurs de vibrations. Sa protection contre les températures extrêmes, les huiles et les substances synthétiques le rend idéal pour les applications de moteur et les pièces extérieures où la robustesse et la fiabilité sont d'une importance primordiale.
5. Biens de consommation
Il est également utilisé dans d'autres produits de consommation tels que les ustensiles de cuisine, les ustensiles de cuisson, les joints, les joints d'étanchéité et les fournitures d'extérieur en raison de ses propriétés de qualité alimentaire, de sa flexibilité et de sa protection contre les températures élevées. Sa capacité à supporter des cycles répétés de réchauffement et de refroidissement le rend idéal pour les articles qui nécessitent une utilisation et un lavage continus.
6. Applications industrielles
Il trouve également ses applications dans les environnements modernes pour la fabrication de joints, de joints toriques et de différentes pièces où la protection contre les températures extrêmes, les matières synthétiques et les variables écologiques est une grande nécessité. Sa robustesse, sa fiabilité et ses performances à long terme le rendent idéal pour les applications modernes.
7. Aérospatiale
Dans le secteur de l'avionique, le LSR est généralement utilisé dans la création de joints, de joints statiques, de connecteurs et d'autres pièces de base où des matériaux légers aux performances de pointe sont nécessaires. Ses propriétés telles que la protection contre les températures élevées, les radiations et les composés synthétiques le rendent approprié aux applications aéronautiques où une qualité et une sécurité sans faille sont d'une importance primordiale.
8. Éclairage LED
Il trouve également son application dans les éclairages LED pour améliorer leur exposition, leur solidité et leur durée de vie. Ses propriétés telles que la transparence, la stabilité thermique et la résistance aux rayons UV en font un choix de matériau judicieux pour protéger les pièces LED de l'humidité, de la poussière et d'autres éléments écologiques.
9. Militaire et Défense
Il est utilisé dans les applications militaires pour produire des joints, des joints d'étanchéité, des connecteurs et différentes pièces qui nécessitent des performances prédominantes dans des conditions extrêmes. Les articles fabriqués à l'aide de ce procédé offrent des performances extraordinaires dans des conditions difficiles telles que les températures élevées, l'humidité et l'exposition aux composés synthétiques et aux carburants.
Conclusion
Le processus de moulage par injection Le procédé de fabrication de caoutchouc de silicone sous forme liquide est une technique d'élite pour la fabrication de pièces en silicone avec une grande précision. Il s'agit d'un procédé de fabrication adaptable et puissant qui offre différents avantages par rapport aux autres méthodes. La flexibilité de conception, la haute précision et la cohérence combinées aux propriétés innées du matériau en font un procédé idéal pour de nombreuses applications dans différentes entreprises. Grâce aux progrès de l'innovation, ce procédé continue de progresser et de s'améliorer, offrant ainsi un potentiel de développement et d'amélioration des produits beaucoup plus important dans de nombreux domaines.