Mikä on ruiskuvalumuotti?
Ruiskuvalumuotti on työkalu, jota käytetään ruiskuvaluprosessissa osien valmistamiseen ruiskuttamalla materiaalia muottipesään. Se on tyypillisesti valmistettu teräksestä (H13, P20, 1.2312, 1.2344, S136H jne.) tai alumiinista, ja se suunnitellaan huolellisesti vastaamaan lopputuotteen muotoa ja vaatimuksia.
Ruiskuvalumuotti on jaettu kahteen puolikkaaseen, jotka ovat ontelon puolikas ja ytimen puolikas, jotka puristetaan yhteen muovausprosessin aikana, ja materiaali ruiskutetaan ruiskun läpi muotin onteloon, jossa se jäähtyy ja jähmettyy haluttuun muotoon. Kun osa on muotoiltu, muotti avataan ja osa poistetaan. Muotti voidaan käyttää uudelleen useiden osien valmistukseen.

Mikä on ruiskuvalumuotti
Ruiskuvalumuottien tyypit
Ruiskuvalumuottien monien lajikkeiden joukosta löytyy:
Ontelokohtainen muotti
Jokaisella ruiskuvaluprosessin jaksolla voidaan valmistaa vain yksi osa, kun käytetään yhden ontelon muotia. Osan valmistaminen tällä muotilla on yhtä yksinkertaista kuin muovihartsin ruiskuttaminen muottiin, sen jäähtymisen odottaminen ja valmiin tuotteen poistaminen.
Kun verrataan moniulotteisten muottien tuotantokustannuksia yhden ontelon muotteihin, edellinen on yleensä edullisempi. Kun pienen osan valmistaminen kerralla olisi liian kallista, nämä muotit soveltuvat prototyyppien ja pienen sarjan valmistukseen.

Yhden ontelon muotti
Yksittäislaukaisumuottien etuja ovat muun muassa:
- Kustannustehokas: yhden laukauksen muotin valmistus on usein edullisempaa kuin usean laukauksen muotin valmistus.
- Yksinkertainen muotoilu: Tuotannon ja huollon helppous suunnittelun yksinkertaisuuden ansiosta: Yksiosaiset muotit ovat usein ulkoasultaan yksinkertaisempia kuin moniosaiset muotit.
- Joustavuus: Yksipesäisten muottien käyttö soveltuu monenlaisiin sovelluksiin, kuten prototyyppien valmistukseen ja pieniin tuotantosarjoihin.
Yksittäislaukaisumuottien haittoja ovat muun muassa seuraavat:
- Rajoitettu tuotanto: Tämä rajoitus tekee yhden ontelon muotit sopimattomiksi suurille tuotantomäärille, koska ne pystyvät tuottamaan vain yhden osan kussakin syklissä.
- Monimutkaiset osat: Niitä varten tarvitaan moniontelomuotti tai perhemuotti.
- Tehottomuus: Ne eivät ole yhtä tehokkaita, koska ne voivat rajallisen kapasiteettinsa vuoksi valmistaa vain yhden osan kussakin syklissä.
Usean ontelon muotit:
Moniontelomuotit ovat ruiskuvalumuotteja, joissa on useampi kuin yksi ontelo. Näin ruiskuvaluprosessissa voidaan valmistaa useampi kuin yksi osa jokaisen kierroksen aikana. Sovelluksen tarpeesta riippuen näissä muoteissa voi olla samoja tai erilaisia reikiä.
Koska moniontelomuotteja käytetään yleensä monien osien valmistamiseen yhdessä syklissä, niitä käytetään yleensä seuraavissa tarkoituksissa suuren volyymin ruiskuvalu tuotantosarjat. Tämän ominaisuuden ansiosta ne voivat lisätä tuotannon tehokkuutta ja samalla alentaa kustannusta osaa kohti.

moniontelomuotti
Moniontelomuottien etuja ovat muun muassa:
- Suuren volyymin tuotanto: Tämä helpottaa monien osien valmistamista.
- Kustannustehokas: moniuramuotit ovat yleensä halvempia kuin yksiuramuotit, koska niillä voidaan valmistaa useampia osia yhdellä kertaa.
- Monimutkaiset osat: Moniurallisia muotteja voidaan käyttää monimutkaisten osien valmistukseen, joissa on useita osia.
Usean ontelon muottien haittoja ovat muun muassa seuraavat:
- Monimutkainen suunnittelu: Muotit ovat vaikeampia valmistaa ja ylläpitää kuin yksipesäiset muotit, koska niiden rakenne on monimutkaisempi.
- lisäsi muotin kustannuksia: Muotit voivat olla kalliimpia kuin yhden ontelon muotit, koska eri onteloihin voi kohdistua erilaista rasitusta ja kulumista ruiskuvaluprosessin aikana. Tämä voi johtaa tehottomampaan tuotantoon ja korkeampiin korjauskustannuksiin.
Kuumakanavan muotti:
Hot runner -muotti on eräänlainen ruiskuvalumuotti, joka käyttää kuumakanavajärjestelmää sulatetun muovimateriaalin syöttämiseksi muotin onteloihin. Kuumakanavajärjestelmä koostuu lämmitetystä jakoputkesta, joka jakaa sulatetun muovin yksittäisiin suuttimien kärkiin, jotka sitten ohjataan muotin onteloihin.

Hot runner -muotti
Kuumakanavamuottien etuja ovat:
- Parempi kappaleiden laatu: Kuumakanavamuotilla voidaan valmistaa laadukkaampia kappaleita, koska ne minimoivat juoksuputkiin jäävän muovin määrän, mikä vähentää vikojen, kuten leimahduksen, lyhyiden laukausten ja uppoamisten riskiä.
- Tuotannon tehokkuuden lisääminen: Kuumakanavamuotit voivat lisätä tuotannon tehokkuutta, koska ne poistavat manuaalisen toimenpiteen tarpeen juoksuputkien irrottamiseksi valetuista osista, mikä lyhentää sykliaikaa ja parantaa yleistä tuotantonopeutta.
- Energiatehokkuus: Ne minimoivat juoksuputkissa hukkaan menevän muovin määrän.
Kuumakanavamuottien haittoja ovat:
- Monimutkainen suunnittelu: Kuumakanavamuotit ovat rakenteeltaan monimutkaisempia kuin perinteiset kylmäkanavamuotit, mikä tekee niiden valmistuksesta ja ylläpidosta kalliimpaa.
- Lisääntynyt huolto: Niissä on monimutkaisempi lämmitysjärjestelmä, joka on pidettävä kunnossa.
- Alttius tukkeutumiselle: Kuumakanavamuotit voivat olla alttiita tukkeutumiselle erityisesti silloin, kun käsitellään materiaaleja, joiden viskositeetti on korkea tai joiden virtauspituus on pitkä, sillä nämä voivat aiheuttaa sulan muovin jähmettymisen kanaviin. Tämä voi johtaa tuotannon tehokkuuden heikkenemiseen ja huoltokustannusten kasvuun.
Pinota muotit:
Pinomuotti on eräänlainen ruiskuvalumuotti, joka mahdollistaa useiden onteloiden valamisen samanaikaisesti yhdellä koneen työjaksolla. Pinomuotit ovat periaatteessa kaksi tai useampia päällekkäin pinottuja muotteja, joista kukin tuottaa yhden osan.

Pinomuotti
Pinomuottien etuja ovat:
- Tuotannon tehokkuuden lisääminen: Tämä lisää tuotannon tehokkuutta ja lyhentää sykliaikaa.
- Materiaalijätteen vähentäminen: Pinoamismuotit minimoivat materiaalihävikin, sillä ne mahdollistavat useiden osien valmistamisen yhdellä muovipanoksella.
- Pienemmät kustannukset: Ne mahdollistavat useiden osien valmistuksen yhdellä koneen työjaksolla.
Pinomuottien haittoja ovat muun muassa:
- Monimutkainen suunnittelu: Tämä tekee niiden valmistuksesta ja ylläpidosta kalliimpaa.
- Osan laadun heikkeneminen: Useiden onteloiden olemassaolo voi lisätä vikojen, kuten leimahduksen, lyhyiden laukausten ja uppoamisten riskiä.
- Lisääntynyt huolto: Ne ovat rakenteeltaan monimutkaisempia, ja ne on pidettävä hyvässä toimintakunnossa.
Perheen homeet:
Perhemuotit, jotka tunnetaan myös nimellä monimuotti, joka on samankaltainen kuin usean ontelon muotti, ovat eräänlainen ruiskuvalutekniikka, joka mahdollistaa useiden hieman erilaisten osien valamisen samanaikaisesti yhdellä koneenjaksolla. Tämä saavutetaan siten, että muotissa on useita onteloita, joista voidaan valmistaa eri muotoisia ja kokoisia osia.
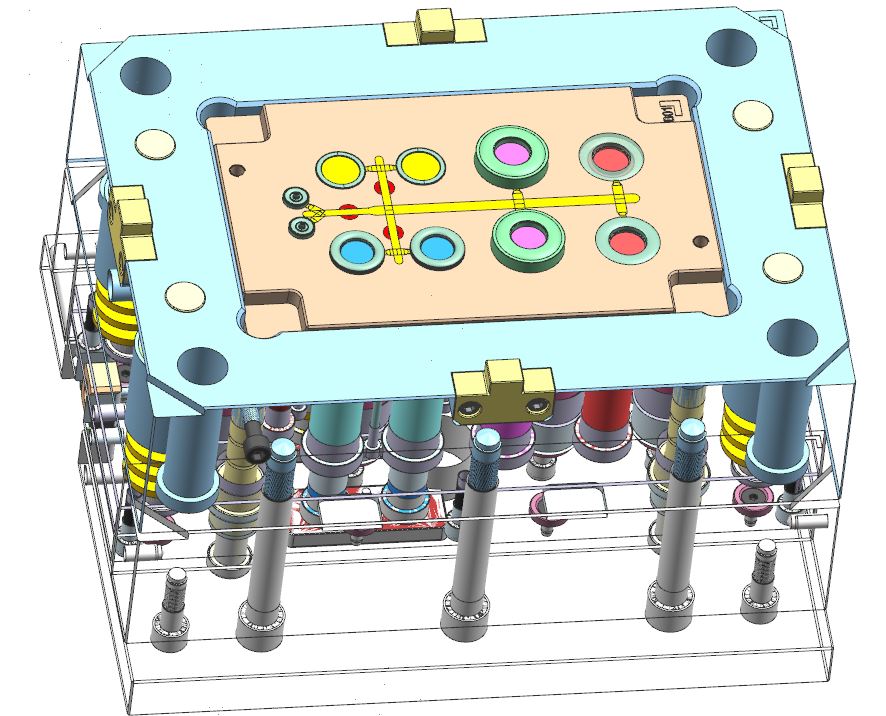
perheen home
Perhemuottien etuja ovat muun muassa:
- Tuotannon tehokkuuden lisääminen: Tämä lisää tuotannon tehokkuutta ja lyhentää sykliaikaa.
- Pienemmät kustannukset: Ne mahdollistavat useiden osien valmistuksen yhdellä koneen kierrolla.
- Joustavuus: Siksi ne ovat monipuolinen vaihtoehto valmistajille, joiden on tuotettava erilaisia tuotteita.
Perhemuottien haittoja ovat mm:
- Monimutkainen suunnittelu: Tämä tekee niiden valmistuksesta ja ylläpidosta kalliimpaa.
- Osan laadun heikkeneminen: Useiden onteloiden olemassaolo voi lisätä vikojen, kuten leimahduksen, lyhyiden laukausten ja uppoamisten riskiä.
Kahden laukauksen muotit:
Kahden laukauksen muotti (2 laukauksen ruiskuvalu), joka tunnetaan myös nimellä ylivalu tai moniulotteiset muotit tai 2K-muotti, ovat eräänlainen ruiskuvalutekniikka, jossa kaksi eri materiaalia voidaan valaa yhdessä koneessa yhdellä työjaksolla. Tässä prosessissa ensimmäinen materiaali (perusmateriaali) valetaan muottiin ja sitten toinen materiaali (ylivalumateriaali) valetaan ensimmäisen materiaalin päälle.

Kahden laukauksen muotti
Kaksoislaukaisumuottien etuja ovat muun muassa:
- Lisääntynyt toiminnallisuus: Kahden eri ominaisuuksiltaan erilaisen materiaalin yhdistäminen mahdollistaa osien toiminnallisuuden lisäämisen.
- Parempi estetiikka: Kaksoiskuvioiset muotit mahdollistavat eri värien tai tekstuurien yhdistämisen yhteen osaan, mikä luo visuaalisesti miellyttävämmän tuotteen.
- Vähentää kokoonpanoaikaa: Kaksoismuotit voivat vähentää ylimääräisten kokoonpanovaiheiden tarvetta, mikä vähentää tuotantoaikaa ja kustannuksia.
Kaksoislaukaisumuottien haittoja ovat muun muassa seuraavat:
- Monimutkainen suunnittelu: Kaksoismuotit ovat rakenteeltaan monimutkaisempia kuin yksiaukkoiset muotit, mikä tekee niiden valmistuksesta ja ylläpidosta kalliimpaa.
- Lisääntynyt kiertoaika: Koska prosessissa muovaillaan kahta materiaalia yhdellä koneen käyntikerralla, kaksi materiaalia on tyypillisesti pidempi sykliaika kuin yhden laukauksen muoteissa.
- Yhteensopivuusongelmat: Siksi on tärkeää valita käytettävät materiaalit huolellisesti.
Muottien irrottaminen:
Ruuvinpoistomuotit ovat eräänlainen ruiskuvalutyyppi, joka on suunniteltu erityisesti ruuvikierteisten osien, kuten korkkien, kansien ja säiliöiden valmistukseen. Nämä muotit ovat ainutlaatuisia siinä mielessä, että niissä on mekanismi, jonka avulla muotin ydin voi pyöriä ontelon pysyessä paikallaan, jolloin valettu osa voidaan irrottaa muotista sen jälkeen, kun se on jäähtynyt ja jähmettynyt.

muotin irrottaminen
Ruuvaamattomien muottien etuja ovat:
- Korkea hyötysuhde: Ruuvaamattomat muotit mahdollistavat kierteitettyjen osien tehokkaan valmistuksen yhdellä koneen kierroksella, mikä vähentää tuotantoaikaa ja kustannuksia.
- Parempi tarkkuus: Ruuvausmuotit mahdollistavat kierteitettyjen osien tarkan valmistuksen, jossa on tasainen nousu ja kierteiden syvyys, mikä parantaa lopputuotteen laatua ja suorituskykyä.
- Monipuolisuus: Ruuvaamattomia muotteja voidaan käyttää erilaisten osien valmistukseen, joissa on erilaisia kierretyyppejä ja -kokoja, mikä tekee niistä monipuolisen vaihtoehdon moniin eri sovelluksiin.
Muottien irrottamisen haittoja ovat muun muassa:
- Monimutkainen suunnittelu: Ne ovat rakenteeltaan monimutkaisempia kuin muuntyyppiset muotit, mikä tekee niiden valmistuksesta ja ylläpidosta kalliimpaa.
- Lisääntynyt kiertoaika: Muottien ruuvaus kestää yleensä pidempään kuin muuntyyppisten muottien, koska prosessiin kuuluu muotin ytimen pyöriminen.
- Kuluminen: Se vaatii säännöllistä huoltoa, jotta muotti toimisi moitteettomasti.
Kokoontaitettava ydinmuotti:
Kokoontaitettavat muotit ovat eräänlaisia ruiskuvalumuotteja, joita käytetään onttojen osien, joissa on sisäisiä onteloita, kuten putkien ja muiden monimutkaisen muotoisten osien valmistukseen. Näissä muoteissa käytetään ainutlaatuista rakennetta, jonka ansiosta muotin ydin voi luhistua itseensä ja muodostaa osan sisäisen ontelon.

Kokoontaitettava muottiosa
Kokoontaitettavien muottien etuja ovat:
- Parempi tehokkuus: Muotit mahdollistavat onttojen osien valmistuksen yhdellä koneistuskierroksella, mikä vähentää tuotantoaikaa ja kustannuksia.
- Parempi kappaleiden laatu: Kokoontaitettavat muotit tarjoavat tarkemman ja johdonmukaisemman sisäisen ontelon, mikä parantaa lopullisen kappaleen kokonaislaatua.
- Monipuolisuus: Muotteja voidaan käyttää monenlaisten erimuotoisten ja -kokoisten osien valmistukseen, mikä tekee niistä monipuolisen vaihtoehdon moniin eri sovelluksiin.
Kokoontaitettavien muottien haittoja ovat muun muassa:
- Monimutkainen suunnittelu: Muotit ovat rakenteeltaan monimutkaisempia kuin muuntyyppiset muotit, mikä tekee niiden valmistuksesta ja ylläpidosta kalliimpaa.
- Lisääntynyt kiertoaika: Muotit ovat tyypillisesti pidempiä kuin muuntyyppiset muotit, koska prosessiin kuuluu muotin ytimen kokoonpuristaminen.
- Kuluminen: Se vaatii säännöllistä huoltoa, jotta muotti toimisi moitteettomasti.
Edut ja haitat Muovin ruiskupuristusmuotti
Edut Ruiskuvalu:
- Suuren volyymin tuotanto: Ruiskupuristus on erittäin tehokas menetelmä, jolla voidaan valmistaa suuria määriä samanlaisia osia. Tämän vuoksi se sopii erinomaisesti kulutustavaroiden, autojen osien ja muiden sellaisten tuotteiden massatuotantoon, joissa tarvitaan suuria määriä samanlaisia osia.
- Tarkkuus: Prosessi mahdollistaa erittäin tarkan mittatarkkuuden ja kappaleiden yhdenmukaisuuden valvonnan. Tämä johtuu tiukasti valvotuista käsittelyolosuhteista sekä valukoneen ja muotin jäykkyydestä.
- Nopeus: Ruiskupuristus on nopea prosessi, ja pienten osien valmistussykli on vain muutaman sekunnin mittainen. Tämän ansiosta valmistajat voivat valmistaa suuria määriä osia suhteellisen lyhyessä ajassa.
- Kustannustehokas: Ruiskupuristamalla valmistettujen osien tuotantokustannukset muuttuvat edullisemmiksi tuotantomäärän kasvaessa. Tämä johtuu siitä, että muotilla voidaan valmistaa monia osia sen elinkaaren aikana, ja kustannukset osaa kohti laskevat volyymin kasvaessa.
- Monipuolisuus: Muovit, metallit ja elastomeerit: Ruiskupuristuksella voidaan valmistaa osia monista eri materiaaleista, kuten muoveista, metalleista ja elastomeereistä. Tämä monipuolisuus tekee siitä suositun valinnan valmistajille, joiden on tuotettava osia eri materiaaleista tuotteen erityisvaatimusten mukaan.
- Automaatio: Tämä tehostaa prosessia ja vähentää käsityön tarvetta. Tämä voi myös parantaa kappaleiden tasalaatuisuutta ja laatua.
- Monimutkaiset muodot: Ruiskupuristuksella voidaan valmistaa monimutkaisia muotoja ja malleja, kuten osia, joissa on monimutkaisia yksityiskohtia ja tiukkoja toleransseja. Tämä on mahdollista, koska muovausprosessi on tarkasti hallittavissa ja koska voidaan suunnitella erittäin yksityiskohtaisia muotteja.
- Materiaalin valinta: Jokaisella materiaalilla on omat ainutlaatuiset ominaisuutensa, kuten lujuus, joustavuus ja lämmön-, kemikaalien- ja kulutuskestävyys. Näin voidaan valita kuhunkin sovellukseen paras materiaali ja valmistaa osia, joilla on halutut ominaisuudet.
Ruiskuvalun haitat:
- Korkeat alkukustannukset: Muotin luomisen alkukustannukset voivat olla korkeat, erityisesti monimutkaisten muotojen ja mallien osalta. Tämä voi tehdä prosessista vähemmän kustannustehokkaan pienille kappalemäärille tai prototyypeille.
- Rajoitettu suunnittelun joustavuus: Muotoilun muuttaminen voi olla vaikeaa ja kallista, kun muotti on tehty. Tämä voi rajoittaa mahdollisuuksia tehdä suunnittelumuutoksia tai parannuksia sen jälkeen, kun muotti on luotu.
- Materiaalijäte: Se voi olla kallista hävittää ja ympäristölle haitallista. Tämä voi myös lisätä tuotantokustannuksia ja heikentää prosessin kokonaistehokkuutta.
- Läpimenoaika: Muotin luomisen ja ruiskuvaluprosessin käynnistämisen läpimenoaika voi olla pitkä, erityisesti monimutkaisten osien kohdalla. Tämä voi hidastaa tuotekehitysprosessia ja rajoittaa mahdollisuuksia tuoda tuotteet nopeasti markkinoille.
- Pintakäsittelyn rajoitukset: Tämä koskee erityisesti osia, joissa on monimutkaisia yksityiskohtia tai tiukkoja toleransseja. Tämä voi rajoittaa kykyä tuottaa osia, joiden ulkonäkö on esteettisesti korkealaatuinen.
- Materiaalien yhteensopivuus: Materiaalin ja muotin yhteensopivuus voi olla haaste, sillä jotkin materiaalit eivät välttämättä toimi hyvin tietyntyyppisten muottien kanssa tai vaativat erityisiä käsittelyolosuhteita. Tämä voi rajoittaa kykyä valmistaa osia tietyistä materiaaleista ja nostaa tuotantokustannuksia.
- Rajoitettu osan koko: Muotin koko ja muovauskoneen puristusvoima rajoittavat ruiskuvalua. Tämä voi rajoittaa valmistettavien osien kokoa ja nostaa suurempien osien valmistuskustannuksia.
- Toissijaiset toiminnot: Jotkut osat saattavat vaatia jälkikäsittelyjä, kuten viimeistelyä tai viimeistelyä, valun jälkeen. Tämä voi lisätä tuotantokustannuksia ja rajoittaa prosessin kokonaistehokkuutta, mutta tietysti joskus nämä ongelmat voidaan ratkaista parantamalla ruiskuvalumuotin toimintaa.
Ruiskupuristemuotin yleiset ongelmat
Kun työskentelet muovin ruiskuvalualalla, on aina jokin ongelma, joka sinun on ratkaistava joka päivä, Tässä on joitakin yleisiä haasteita, joita ruiskuvalussa kohdataan:
Vääntymisongelmat:
Vääntyminen on yleinen ongelma ruiskuvalussa, ja sillä tarkoitetaan muottiin valetun kappaleen muodonmuutosta tai vääristymää, joka tapahtuu sen jälkeen, kun se on poistettu muotista. Tämä voi johtua monista eri tekijöistä, kuten seuraavista:

Warp vääristymä
- Virheellinen jäähdytys: Jos osa jäähtyy liian nopeasti tai epätasaisesti, se voi aiheuttaa vääntymiä, koska materiaali kutistuu ja supistuu eri tahtiin.
- Jäännösjännitys: Ruiskuvaluprosessin aikana käytetyn korkean paineen vuoksi kappaleeseen syntyy jäännösjännitystä. Tämä jännitys voi aiheuttaa vääntymistä, jos sitä ei pureta asianmukaisesti.
- Materiaalin valinta: Jotkin materiaalit ovat alttiimpia vääntymiselle kuin toiset. Esimerkiksi materiaalit, joiden lämmönkestävyys tai mittapysyvyys on heikko, vääntyvät todennäköisemmin.
- Muotin suunnittelu: Varsinkin, jos muotti ei salli asianmukaista jäähdytystä tai materiaalin virtausta.
- Käsittelyolosuhteet: Epäjohdonmukaiset käsittelyolosuhteet, kuten vaihtelevat ruiskutusnopeudet, muotin lämpötilat ja painetasot, voivat aiheuttaa vääntymistä.
Vääntymisen estämiseksi on tärkeää valita sopiva materiaali, optimoida muotin suunnittelu ja käsittelyolosuhteet sekä toteuttaa asianmukaiset jäähdytys- ja materiaalinkäsittelykäytännöt. Lisäksi voi olla tarpeen käyttää muovauksen jälkeisiä käsittelyjä, kuten hehkutusta, jäännösjännityksen poistamiseksi ja mittojen vakauden parantamiseksi.
Flash-ongelmat:
Leimausviat ovat termi, jota käytetään ruiskuvalussa viittaamaan ylimääräiseen materiaaliin, joka puristuu ulos muotista muotin muovausprosessin aikana. Flash-virhe syntyy, kun materiaali valuu suunnitellun muottipesän ulkopuolelle ja erotusviivaan eli muotin kahden puoliskon väliseen tilaan.

Muotti Flash tai purseita
Välähdys voi johtua useista tekijöistä, kuten:
- Virheellinen muotin suunnittelu: Materiaalia pääsee vuotamaan jakolinjaan, mikä voi aiheuttaa leimahduksen huonosti suunnitellussa muotissa.
- Epäjohdonmukaiset käsittelyolosuhteet: Vaihtelevat käsittelyolosuhteet, kuten ruiskutusnopeus ja -paine, voivat aiheuttaa vilkkumista.
- Materiaalin yhteensopivuus: Materiaalit: Jotkin materiaalit eivät välttämättä ole yhteensopivia muotin kanssa ja voivat aiheuttaa leimahduksia, kun ne virtaavat jakolinjaan.
- Muotin kuluminen: Muotti voi ajan mittaan kulua ja aiheuttaa leimahduksen, kun materiaali vuotaa jakolinjaan.
Välähdyksellä voi olla useita kielteisiä vaikutuksia, kuten kappaleen mittatarkkuuden heikkeneminen, romun määrän lisääntyminen ja jälkivalutoimintojen vaikeutuminen. Välähdyksen minimoimiseksi on tärkeää optimoida muotin suunnittelu, käsittelyolosuhteet ja materiaalivalinnat sekä huoltaa ja korjata muotti säännöllisesti ja tarvittaessa.
Hitsauslinjat:
Hitsausviivat ovat yleinen ongelma ruiskuvalussa, ja niillä tarkoitetaan näkyviä jälkiä valetun kappaleen pinnalla, jossa kaksi sulatetun muovin virtausta kohtaa ja jähmettyy. Hitsausviivat syntyvät, kun materiaali ei täysin sulaudu yhteen, kun se virtaa muottiin. muovimuotti onteloon, jolloin kappaleen pintaan jää näkyvä viiva.

Hitsauslinja
Hitsausviivat voivat johtua useista tekijöistä, kuten:
- Riittämätön sulan virtaus: Jos materiaalilla ei ole riittävästi aikaa virrata ja sulaa täysin yhteen, voi muodostua hitsausviiva.
- Virheellinen porttisuunnittelu: Se on kohta, jossa sulanut materiaali tulee muottipesään, voi aiheuttaa hitsausviivan.
- Epäjohdonmukaiset käsittelyolosuhteet: Vaihtelevat käsittelyolosuhteet, kuten ruiskutusnopeus ja -paine, voivat aiheuttaa hitsausviivan.
- Materiaalin yhteensopivuus: Materiaalit: Jotkin materiaalit eivät välttämättä ole yhteensopivia muotin kanssa ja voivat aiheuttaa hitsausviivan, kun ne virtaavat muottipesään.
Hitsausviivat voivat heikentää osan lujuutta ja heikentää sen kokonaislaatua. Hitsiviivojen minimoimiseksi on tärkeää optimoida muotin suunnittelu, käsittelyolosuhteet ja materiaalivalinta sekä ottaa käyttöön asianmukaiset materiaalinkäsittelykäytännöt. Lisäksi voi olla tarpeen käyttää erityisiä käsittelytekniikoita, kuten moniurallisia muotteja tai kuumakanavajärjestelmiä, hitsausviivojen muodostumisen vähentämiseksi.
Upotusmerkit:
Upotusjäljet, jotka tunnetaan myös nimillä "upotus", "tyhjiöupotus" tai "iho", ovat uponneita tai painuneita alueita ruiskuvaletun muoviosan pinnalla. Ne johtuvat yleensä useista tekijöistä, kuten seuraavista:
- Hartsin kutistuminen: Kun hartsi jäähtyy ja jähmettyy, se voi kutistua epätasaisesti, mikä johtaa uppoamisjälkiin.
- Huono materiaalivirta: Jos hartsi ei virtaa tasaisesti muotin kaikille alueille, voi syntyä onteloita tai uponneita alueita.
- Riittämätön pakkauspaine: Jos ruiskutuspaine ei ole tarpeeksi korkea, hartsi ei ehkä täytä muottia kokonaan, mikä johtaa uppoamisjälkiin.
- Muotin suunnitteluun liittyvät kysymykset: Muotin suunnittelu, mukaan lukien porttien sijoittelu ja koko, juoksutusjärjestelmä ja tuuletus, voivat kaikki vaikuttaa muotin laatuun ja aiheuttaa uppoumia.
Uppoamisjäljet voivat vaikuttaa valetun kappaleen esteettiseen laatuun ja toimivuuteen, ja ne voivat aiheuttaa turhautumista valmistajille ja loppukäyttäjille. Upotusjälkien minimoimiseksi on tärkeää tarkastella huolellisesti niitä aiheuttavia tekijöitä, kuten materiaalivalintaa, muotin suunnittelua, käsittelyparametreja ja kappaleen suunnittelua, ja tehdä tarvittaessa muutoksia ruiskuvaluprosessin optimoimiseksi.
Virtausmerkit:
Virtausjäljet ovat yleinen ongelma ruiskuvalussa, ja niillä tarkoitetaan näkyviä jälkiä tai raitoja valetun kappaleen pinnalla, jotka johtuvat sulatetun muovimateriaalin virtauksesta, kun se täyttää muottipesän. Virtausjäljet syntyvät, kun materiaali virtaa epätasaisesti ja jättää näkyvän jäljen kappaleen pintaan.
Virtausjäljet voivat johtua useista tekijöistä, kuten:
- Riittämätön sulan virtaus: Jos materiaalilla ei ole riittävästi aikaa virrata ja täyttää muottipesää, voi syntyä virtausjälkiä.
- Virheellinen porttisuunnittelu: Se on kohta, jossa sulatettu materiaali tulee muottipesään, voi aiheuttaa virtausjälkiä.
- Epäjohdonmukaiset käsittelyolosuhteet: Vaihtelevat käsittelyolosuhteet, kuten ruiskutusnopeus ja -paine, voivat aiheuttaa virtausjälkiä.
- Materiaalin yhteensopivuus: Materiaalit: Jotkin materiaalit eivät välttämättä ole yhteensopivia muotin kanssa ja voivat aiheuttaa virtausjälkiä, kun ne virtaavat muottipesään.
Virtausjäljet voivat heikentää osan yleistä laatua ja kosmeettista ulkonäköä. Virtausjälkien minimoimiseksi on tärkeää optimoida muotin suunnittelu, käsittelyolosuhteet ja materiaalivalinta sekä ottaa käyttöön asianmukaiset materiaalinkäsittelykäytännöt. Lisäksi voi olla tarpeen käyttää erityisiä käsittelytekniikoita, kuten moniurallisia muotteja tai kuumakanavajärjestelmiä, virtausjälkien muodostumisen vähentämiseksi.
Naarmuuntumisongelmat:
Naarmuilla tarkoitetaan ruiskuvaletun kappaleen pinnassa näkyviä jälkiä tai naarmuja, jotka johtuvat kappaleen ja muotin tai muiden vieraiden esineiden fyysisestä kosketuksesta muovausprosessin aikana. Naarmuuntumisongelmia voi esiintyä useista eri syistä, kuten:
- Huono muotin suunnittelu: Väärin suunnitellut muotit tai muotin osat voivat aiheuttaa naarmuja osan pintaan.
- Riittämätön voitelu: Jos muotti ja muotin osat eivät ole kunnolla voideltuja, ne voivat aiheuttaa naarmuja kappaleen pintaan.
- Huono materiaalin käsittely: Raaka-aineen tai valmiiden osien huono käsittely voi aiheuttaa naarmuja osan pintaan.
- Muotissa olevat roskat: Vieraat esineet tai roskat muottipesässä voivat aiheuttaa naarmuja kappaleen pintaan.
Naarmuuntuminen voi heikentää osan yleistä laatua ja kosmeettista ulkonäköä. Naarmuuntumisongelmien minimoimiseksi on tärkeää ottaa käyttöön asianmukaiset muotin suunnittelu-, voitelu-, materiaalinkäsittely- ja huoltokäytännöt. Lisäksi muotin ja muotin osien säännöllinen puhdistus ja tarkastus voi auttaa ehkäisemään naarmuuntumista.
Heittimen jäljet:
Ulosheittojäljet ovat ruiskuvaletun kappaleen pinnalla näkyviä jälkiä, jotka johtuvat ulosheittotapeista tai muista ulosheittomekanismeista muovausprosessin aikana. Ulosheittojäljet syntyvät, kun ulosheittotapit työntävät valetun kappaleen ulos muottipesästä ja jättävät näkyviä jälkiä kappaleen pintaan.
Heittojäljet voivat johtua useista tekijöistä, kuten:
- Virheellinen heittotapin muotoilu: Jos heittotappia ei ole suunniteltu oikein, ne voivat jättää näkyviä jälkiä kappaleen pintaan.
- Liiallinen voimankäyttö: Jos ulosheittotapit kohdistavat kappaleeseen liian suuren voiman ulosheittämisen aikana, ne voivat jättää kappaleen pintaan syvempiä ja näkyvämpiä jälkiä.
- Epäjohdonmukainen ulosheittovoima: Jos heittovoima ei ole yhdenmukainen heittotapista toiseen, se voi johtaa epätasaisiin heittojälkiin kappaleen pinnalla.
- Huono pintakäsittely: Jos muottipesän pintakäsittely ei ole tasainen, se voi aiheuttaa kappaleen pintaan heittojälkiä.
Ulostyöntymisjäljet voivat heikentää osan yleistä laatua ja kosmeettista ulkonäköä. Ulosheittojälkien minimoimiseksi on tärkeää optimoida ulosheittotappien suunnittelu ja muottipesän pinnan viimeistely sekä ottaa käyttöön asianmukaiset huolto- ja tarkastuskäytännöt. Lisäksi voi olla tarpeen käyttää erityisiä ulostyöntämismekanismeja, kuten ilma-avusteista ulostyöntöä tai sivutoimista ulostyöntöä, ulostyöntöjälkien minimoimiseksi.
Lyhyitä laukauksia koskevat ongelmat:
Lyhyt laukaus on ruiskuvalussa yleinen ongelma, joka ilmenee, kun sulanut muovimateriaali ei täytä muottipesää kokonaan, jolloin valettu osa on haluttua kokoa pienempi. Lyhyitä laukauksia voi esiintyä useista eri syistä, kuten:
- Aineisto ei riitä: Jos materiaali ei riitä täyttämään muottipesää, voi syntyä lyhyt laukaus.
- Väärät käsittelyolosuhteet: Jos käsittelyolosuhteita, kuten ruiskutusnopeutta ja -paineita, ei ole asetettu oikein, voi syntyä lyhyt laukaus.
- Huono muotin suunnittelu: Materiaali ei välttämättä pääse virtaamaan muotin ontelon kaikkiin osiin.
- Materiaalin hajoaminen: Jos materiaali on hajonnut tai sitä ei ole säilytetty oikein, se voi aiheuttaa lyhytaikaisen laukauksen.
Lyhyet laukaukset voivat heikentää kappaleen kokonaislaatua ja toiminnallisuutta ja johtaa materiaalin ja työstöajan tuhlaamiseen. Lyhyiden laukausten minimoimiseksi on tärkeää optimoida muotin suunnittelu, käsittelyolosuhteet ja materiaalivalinnat sekä ottaa käyttöön asianmukaiset materiaalinkäsittelykäytännöt. Lisäksi muotinvalmistuslaitteiston säännöllinen valvonta ja huolto voi auttaa estämään lyhyiden laukausten syntymisen.
Ilmansulku ja palojäljet:
Ilmaloukut ja palojäljet ovat yleisiä ruiskuvalussa esiintyviä ongelmia, jotka voivat johtua vääristä käsittelyolosuhteista tai muotin suunnittelusta.
Ilmaloukkuja syntyy, kun ilma jää jumiin muotin onteloon ruiskuvaluprosessin aikana, jolloin materiaali virtaa ilmataskun ympärille eikä täytä sitä. Tämä voi johtaa näkyviin tyhjiöihin tai taskuihin valetussa kappaleessa. Ilmaloukut voivat johtua useista tekijöistä, kuten seuraavista:
- Riittämätön materiaalivirta: Jos materiaali ei virtaa kunnolla muottipesään, ilma voi jäädä jumiin.
- Virheellinen porttisuunnittelu: Jos porttia ei ole suunniteltu oikein, ilma voi jäädä jumiin muottipesään.
- Riittämätön tuuletus: Jos muotti ei ole tuuletettu kunnolla, ilma voi jäädä jumiin muottipesään.
Polttojäljet syntyvät, kun muovimateriaali altistuu korkeille lämpötiloille liian pitkään, jolloin se hajoaa ja aiheuttaa näkyviä jälkiä tai värimuutoksia osan pintaan. Palojäljet voivat johtua useista tekijöistä, kuten seuraavista:
- Liian korkeat käsittelylämpötilat: Jos käsittelylämpötilat asetetaan liian korkeiksi, materiaali voi hajota ja aiheuttaa palojälkiä.
- Riittämätön jäähdytysaika: Jos osaa ei jäähdytetä kunnolla, materiaali voi hajota ja aiheuttaa palojälkiä.
- Huono muotin suunnittelu: Huonosti suunniteltu muotti voi aiheuttaa sen, että materiaali altistuu korkeille lämpötiloille liian kauan, mikä aiheuttaa palojälkiä.
Ilmaloukkujen ja palojälkien minimoimiseksi on tärkeää optimoida käsittelyolosuhteet ja muotin suunnittelu sekä ottaa käyttöön asianmukaiset seuranta- ja huoltokäytännöt. Lisäksi voi olla tarpeen käyttää erityisiä käsittelytekniikoita, kuten matalalämpötilavalua tai tyhjiömuovausta, ilmansulkujen ja palojälkien minimoimiseksi.
Käsittely ruiskuvalumuotin valmistamiseksi:
Ruiskuvalumuotin valmistusprosessi sisältää useita vaiheita:
Muotin suunnittelu:
Ruiskuvalumuottien suunnittelu on tärkeä osa ruiskuvaluprosessia, sillä se vaikuttaa suoraan valettujen osien laatuun, tehokkuuteen ja kustannuksiin.
Hyvin suunniteltu ruiskuvalumuotti tuottaa osia, jotka täyttävät halutun koon, muodon ja laatuvaatimukset, mutta ovat myös tehokkaita valmistaa ja helppoja huoltaa.
Ruiskuvalumuotin suunnittelussa on otettava huomioon seuraavat keskeiset tekijät:
- Osan geometria: Valetun osan suunnittelussa on otettava huomioon osan haluttu koko, muoto ja ominaisuudet.
- Materiaalin valinta: Materiaali: Muottiin ja valettuun kappaleeseen käytettävä materiaali on valittava kustannusten, lujuuden ja lämmönkestävyyden perusteella.
- Homeontelot: Muottipesien lukumäärä ja sijoittelu on valittava tuotantomäärän vaatimusten mukaisesti.
- Porttijärjestelmä: Se määrittää, miten muovimateriaali virtaa muottipesään.
- Heittojärjestelmä: Valetut osat on voitava irrottaa muotista vahingoittumatta.
- Jäähdytysjärjestelmä: Jäähdytysjärjestelmä on suunniteltava siten, että se varmistaa, että muottiin valetut osat jäähtyvät tasaisesti ja nopeasti, mikä lyhentää kiertoaikaa ja parantaa laatua.
- Luonnoskulmat: Muotin suunnittelussa on oltava asianmukaiset vetokulmat, jotta muottiin valetut osat voidaan irrottaa muotista.
- Tuuletus: Muotti on tuuletettava, jotta ilma pääsee poistumaan muotin ontelosta, mikä vähentää ilmansulkujen ja palojälkien riskiä.
- Huolto ja korjaus: Muotti on suunniteltava niin, että se on helppo huoltaa ja korjata, jotta seisokkiaika voidaan minimoida ja tuotannon tehokkuutta lisätä.
Ruiskuvalumuottien suunnittelu on monimutkainen prosessi, joka edellyttää asiantuntemusta esimerkiksi konetekniikan, materiaalitieteen ja valmistuksen aloilta. On tärkeää työskennellä hyvämaineisen muotinsuunnittelijan kanssa, jotta voidaan varmistaa, että muotti suunnitellaan oikein ja että se vastaa tarpeitasi.
CNC-ohjelmointi:
CNC-ohjelmointi (Computer Numerical Control) on olennainen vaihe ruiskuvalumuotin valmistuksessa. Kun muotin suunnittelu on valmis, seuraava vaihe on CNC-ohjelmointi. Seuraavassa esitetään ruiskuvalumuottien valmistuksen CNC-ohjelmoinnin päävaiheet:
- CAD-mallin kääntäminen: CAD-malli käännetään tietokoneavusteiseen valmistusohjelmaan (CAM-ohjelma), jota käytetään muotin CNC-koodin luomiseen.
- CNC-koodin luominen: CNC-koodi luodaan CAM-ohjelmassa, joka antaa CNC-koneelle ohjeet muotin osien liikuttamisesta ja leikkaamisesta. Koodissa otetaan huomioon muotin osien materiaali ja paksuus sekä halutut muodot ja ominaisuudet.
- Työkalupolun luominen: CAM-ohjelmassa luodaan työkalupolku, jossa määritellään polku, jota leikkuutyökalu seuraa muottiosien työstössä. Työkaluradassa otetaan huomioon muotin osien muodot ja ominaisuudet sekä CNC-koneen ominaisuudet.
- Simulointi: CAM-ohjelmassa simuloidaan CNC-koodi ja työkalupolku sen varmistamiseksi, että muotin osat työstetään oikein ja oikeiden eritelmien mukaisesti.
- CNC-työstö: CNC-koodi ladataan CNC-koneeseen, joka sitten käyttää koodia ja työkalupolkua muottiosien työstämiseen.
CNC-ohjelmointi on kriittinen vaihe ruiskuvalumuottien valmistusprosessissa, sillä se määrittää muotin osien tarkkuuden ja laadun. On tärkeää työskennellä CNC-ohjelmoijan kanssa, jolla on kokemusta ruiskuvalumuottien ohjelmoinnista, jotta voidaan varmistaa, että CNC-koodi luodaan oikein ja oikeiden eritelmien mukaisesti. Tässä vaiheessa muotin jäähdytyskanavat, ulosheittojärjestelmä ja muut ominaisuudet lisätään muotin komponentteihin niiden asianmukaisen toiminnan varmistamiseksi.
Muotin BOM-luettelon ostaminen
Mold BOM (Bill of Materials) -luettelo on kattava luettelo kaikista ruiskuvalumuotin valmistukseen tarvittavista komponenteista ja materiaaleista. Se sisältää seuraavat kohdat:
- Teräs muottipohjaa ja ydintä/onteloa varten.
- Kuumakanavan komponentit
- Jäähdytysjärjestelmän osat, kuten vesijohdot ja jäähdytyslohkot.
- Heittojärjestelmän osat, kuten heittotapit ja -holkit.
- Ruiskun ulosvetäjän osat
- Lämmittimet ja lämpötilansäätimet
- Muotin osat, kuten holkit, ohjaustapit ja lukituslaitteet.
- Muotin lisäosat, kuten liukupalat ja nostimet.
- Erikoistuotteet, kuten päiväysleimat ja mukautetut logot.
Muotin BOM-luettelo on tärkeä työkalu hankintaa ja valmistusta varten, sillä se sisältää selkeän ja yksityiskohtaisen luettelon muotin valmistamiseen tarvittavista komponenteista ja materiaaleista. Sen avulla varmistetaan, että kaikki tarvittavat komponentit on tilattu ja niitä on saatavilla, kun muotti on valmis valmistettavaksi.
On tärkeää tehdä yhteistyötä hyvämaineisen toimittajan kanssa, kun hankitaan ruiskuvalumuotin komponentteja, sillä näiden komponenttien laadulla ja luotettavuudella voi olla merkittävä vaikutus ruiskuvaluprosessin tehokkuuteen ja laatuun.
Muotin karkea työstö:
Ruiskuvalumuotin karkeakoneistuksella tarkoitetaan ruiskuvalumuotin teräskomponenttien alkukoneistusta muotin perusmuodon ja -koon saavuttamiseksi. Tämä vaihe tehdään yleensä CNC-koneilla. Seuraavassa esitetään ruiskuvalumuotin karkeakoneistuksen päävaiheet:
- Teräksen valinta: Ensimmäinen vaihe on valita muottiin sopiva terästyyppi, kuten P20 tai H13, valettavan kappaleen haluttujen ominaisuuksien perusteella.
- Teräksen leikkaus: Teräs leikataan sopivaan kokoon ja muotoon CNC-koneella. Tähän vaiheeseen voi sisältyä myös jäähdytys- ja heittojärjestelmien reikien poraaminen ja kierteittäminen.
- Teräksen profilointi: Teräksen osat työstetään muotin perusmuodon saavuttamiseksi, mukaan lukien ydin ja ontelon insertit.
- Teräksen tarkastus: Teräksen tarkastus: Koneistetut osat tarkastetaan sen varmistamiseksi, että ne täyttävät vaaditut toleranssit ja eritelmät.
- Teräksen puhdistus: Koneistetut osat puhdistetaan ja purseenpoisto karheiden reunojen ja roskien poistamiseksi.
Karkeakäsittely on tärkeä vaihe ruiskuvaluprosessissa, sillä se luo pohjan seuraaville korkeatarkkuustyöstö- ja kiillotusvaiheille. On tärkeää varmistaa, että karkeakoneistus tehdään tarkasti ja oikeiden eritelmien mukaisesti, jotta voidaan varmistaa, että muotti toimii oikein ja tuottaa halutun laatuisia osia.
Muototeräksen lämpökäsittely:
Muototeräksen lämpökäsittely on prosessi, jossa ruiskuvalumuotin teräskomponentteja kuumennetaan ja jäähdytetään niiden mekaanisten ominaisuuksien ja mittojen vakauden parantamiseksi. Lämpökäsittelyn tarkoituksena on kovettaa terästä, poistaa jäännösjännityksiä ja parantaa sen kulutuskestävyyttä ja sitkeyttä. Tämä koskee erityisesti ruiskuvalumuotin karkaistua terästä, jos ruiskuvalumuotin valmistuksessa käytetään esikarkaistua terästä, tätä lämpökäsittelyä ei tarvitse tehdä. Seuraavat ovat muototeräksen lämpökäsittelyn päävaiheet:
- Hehkutus: Teräksen komponentit kuumennetaan tiettyyn lämpötilaan, yleensä 800-900 °C:n välille, ja jäähdytetään sitten hitaasti sisäisten jännitysten poistamiseksi ja teräksen työstettävyyden parantamiseksi.
- Karkaisu: Teräksen osat kuumennetaan korkeaan lämpötilaan, yleensä kriittisen lämpötilan yläpuolelle, ja jäähdytetään sitten nopeasti, yleensä sammuttamalla öljyssä tai vedessä. Tämä prosessi kovettaa terästä ja parantaa sen kulutuskestävyyttä.
- Karkaisu: Karkaisun jälkeen teräskomponentit karkaistaan kuumentamalla niitä alhaisemmassa lämpötilassa tietyn ajan, jotta teräksen sitkeys ja mittapysyvyys paranevat.
Lämpökäsittelyprosessi on ratkaisevan tärkeä sen varmistamiseksi, että ruiskuvalumuotin teräskomponenteilla on halutut mekaaniset ominaisuudet ja mittapysyvyys, jotka ovat välttämättömiä korkealaatuisten valettujen osien valmistamiseksi. On tärkeää työskennellä lämpökäsittelyn tarjoajan kanssa, jolla on kokemusta muototeräksen käsittelystä, jotta voidaan varmistaa, että lämpökäsittelyprosessi tehdään oikein ja oikeiden eritelmien mukaisesti.
Muotin ontelon ja ytimen hienomuokkaus:
Muottipesän ja ytimen hienomuokkaus on prosessi, jossa muottipesän ja ytimen sisäpinnat työstetään tarkasti muotin lopullisen muodon ja koon saavuttamiseksi. Tämä vaihe tehdään tyypillisesti tietokoneen numeerisen ohjauksen (CNC) koneilla, joiden tarkkuus ja tarkkuus on suuri. Seuraavassa on lueteltu muottipesän ja ytimen hienokoneistukseen liittyvät päävaiheet:
- Pinnan valmistelu: Muotin ontelon ja ydinsisäosien pinta puhdistetaan ja kiillotetaan jäännösjätteiden ja karheuden poistamiseksi.
- Pintakäsittely: CNC-koneilla työstetään muottipesän ja ydinlevyjen sisäpinnat muotin lopullisen muodon ja koon saavuttamiseksi. Tähän kuuluu myös muotin monimutkaisten yksityiskohtien ja piirteiden, kuten tekstin, logojen ja alaleikkausten luominen.
- Pintatarkastus: Koneistetut pinnat tarkastetaan sen varmistamiseksi, että ne täyttävät vaaditut toleranssit ja eritelmät.
- Pinnan kiillotus: Muotin ontelon ja ydinsisäosien sisäpinnat kiillotetaan viimeistellyksi, jotta muottiin valettujen osien pinnanlaatu paranee ja vikojen riski pienenee.
Hienomuokkaus on kriittinen vaihe ruiskuvaluprosessissa, sillä se määrittää valettujen osien laadun ja tarkkuuden. On tärkeää työskennellä koneistuksen toimittajan kanssa, jolla on kokemusta muottipesien ja -ytimien hienokoneistuksesta, jotta voidaan varmistaa, että koneistus tehdään oikein ja oikeiden eritelmien mukaisesti. Tässä vaiheessa lisätään myös muotin heittojärjestelmä, jäähdytyskanavat ja muut ominaisuudet, joilla varmistetaan muotin moitteeton toiminta.
EDM-työstö:
EDM (Electrical Discharge Machining, sähköpurkauskoneistus) on prosessi, jota käytetään monimutkaisten ja erittäin tarkkojen muotojen tekemiseen metalliosiin, myös ruiskuvalumuotissa oleviin osiin. Prosessissa käytetään sähkökipinöitä poistamaan materiaalia muotin pinnalta, jolloin saadaan aikaan haluttu muoto. Seuraavassa esitetään EDM-työstön päävaiheet:
- Pinnan valmistelu: Työstettävän muotin osan pinta puhdistetaan ja kiillotetaan, jotta mahdolliset jäännökset ja karheudet saadaan poistettua.
- EDM-asetus: Kipinävälin, pulssin keston ja elektrodimateriaalin mukaan lukien oikeat parametrit, jotka perustuvat muotin osan materiaaliin ja muotoon.
- Kipinäeroosio: Kipinät poistavat materiaalia muottiosasta ja luovat halutun muodon. Prosessi tapahtuu vaiheittain, jolloin EDM-kone syö vähitellen materiaalia, kunnes lopullinen muoto on saavutettu.
- Pintatarkastus: Työstetty pinta tarkastetaan sen varmistamiseksi, että se täyttää vaaditut toleranssit ja eritelmät.
EDM-työstöä käytetään usein muottikomponentteihin, joilla on monimutkaisia muotoja tai pieniä, monimutkaisia yksityiskohtia, joita on vaikea saavuttaa muilla työstömenetelmillä. Sitä käytetään myös sellaisten terävien reunojen ja kulmien tuottamiseen, jotka ovat välttämättömiä ruiskuvalumuotin moitteettoman toiminnan kannalta.
Prosessi on erittäin tarkka ja täsmällinen, joten se on ihanteellinen korkealaatuisten valettujen osien valmistukseen. On tärkeää työskennellä sellaisen EDM-toimittajan kanssa, jolla on kokemusta ruiskuvalumuottien EDM-työstöstä, jotta prosessi voidaan suorittaa oikein ja oikeiden eritelmien mukaisesti.
Muotin pinnan kiillotus:
Ruiskuvalumuottien kiillotus on ruiskuvaluprosessin viimeinen vaihe. Siinä muottiosien pinnat tasoitetaan, jotta lopputuotteessa on sileä ja tasainen pinta. Seuraavassa on lueteltu ruiskuvalumuottien kiillotuksen päävaiheet:

muovimuotin kiillotus
- Pinnan valmistelu: Muotin osien pinnat puhdistetaan ja valmistellaan kiillotusta varten. Jäljellä olevat karkeat kohdat tai työstöjäljet poistetaan, jotta pinta olisi sileä kiillotusta varten.
- Karkeakiillotus: Ensimmäinen vaihe kiillotuksessa on karkeakiillotus, jossa poistetaan kaikki suuret puutteet muotin osien pinnasta. Tämä vaihe tehdään tavallisesti karkealla hioma-aineella, kuten hiekkapaperilla tai hiomaharjalla.
- Hienokiillotus: Hienokiillotus on seuraava vaihe, jossa muotin osien pinta tasoitetaan hienommaksi. Tämä vaihe tehdään hienommalla hioma-aineella, kuten hienommalla hiekkapaperilla tai hiomaharjalla.
- Puhdistus: Kiillotus on kiillotuksen viimeinen vaihe, jossa käytetään kiillotuskiekkoa ja kiillotusaineita kiiltävän pinnan saamiseksi muotin osiin.
- Tarkastus: Kiillotuksen jälkeen muotin osat tarkastetaan perusteellisesti sen varmistamiseksi, että niiden pinta on sileä ja tasainen ilman naarmuja, halkeamia tai muita puutteita.
Ruiskuvalumuottien kiillotus on tärkeää, koska se vaikuttaa lopputuotteen laatuun. Hyvin kiillotetun muotin ansiosta tuotteessa on sileä ja tasainen pinta, mikä on tärkeää tuotteen toimivuuden ja esteettisyyden kannalta. On tärkeää työskennellä kokeneen muotin kiillottajan kanssa, jotta voidaan varmistaa, että muotin osat kiillotetaan oikeiden eritelmien ja halutun laatutason mukaisesti.
Muotin sovitus
Muottien asentaminen on erikoistunut työ ruiskuvalualalla, ja siihen kuuluu ruiskuvalumuottien kokoonpano, asennus ja testaus. Muottiasentajien tehtävänä on varmistaa, että muotin osat on koottu oikein ja että ne toimivat moitteettomasti ja että muotti tuottaa osia, jotka täyttävät halutut laatu- ja suorituskykyvaatimukset. Joitakin muottimestareiden tärkeimpiä vastuualueita ovat mm:
- Muotin osien kokoaminen: Muotinrakentajat vastaavat ruiskuvalumuotin eri osien kokoamisesta, mukaan lukien ontelo ja ydinkomponentit, juoksuputkijärjestelmä ja kaikki apukomponentit.
- Muotin asentaminen muotin sovituskoneeseen: Jos muotin sovituskonetta ei ole, käytä manuaalista tapaa asentaa muotti, kuten useimmat yritykset tekevät.
- Muotin testaaminen: Muottimestari on vastuussa muotin testaamisesta sen varmistamiseksi, että se tuottaa osia halutun laatu- ja suorituskykystandardin mukaisesti. Tähän kuuluu osien tarkastaminen mahdollisten vikojen, kuten vääntymisen, kutistumisen tai muiden laatuongelmien varalta.
- Muotin säätäminen: Jos testausvaiheessa havaitaan ongelmia, moldmaster on vastuussa tarvittavien säätöjen tekemisestä muottiin sen varmistamiseksi, että se tuottaa osia, jotka täyttävät halutut vaatimukset.
- Vianmääritys: Moldmasterin on kyettävä tunnistamaan ja korjaamaan kaikki muotin sovitusprosessin aikana mahdollisesti ilmenevät ongelmat.
Muottien sovitustyöt edellyttävät teknistä tietämystä, kädentaitoja ja tarkkuutta yksityiskohtiin. Muotinvalajien on osattava työskennellä monenlaisten työkalujen ja koneiden kanssa sekä ymmärrettävä ruiskuvaluun liittyviä monimutkaisia prosesseja. Muotinsovittajien on tärkeää ymmärtää ruiskuvaluprosessia sekä saada kokemusta erityyppisten muottien ja materiaalien kanssa työskentelystä.
Ensimmäinen ruiskuvalukokeilu tai ammunta:
Ruiskuvalukokeilulla tarkoitetaan prosessia, jossa ruiskuvalumuotti testataan näyteosan valmistamiseksi ruiskuvaluprosessilla. Tämä prosessi on tärkeä vaihe ruiskuvaluprosessissa, sillä sen avulla valmistaja voi arvioida muotin suorituskykyä ja tehdä tarvittavat muutokset ennen suuren kappalemäärän valmistamista.
Ruiskuvaluprosessi sisältää yleensä seuraavat vaiheet:
- Valmistelu: Muotti asennetaan ruiskuvalukoneeseen ja kone asetetaan paukutusta varten. Säiliö täytetään muovihartsilla.
- Sulan lämpötilan säätö: Sulan lämpötilaa ohjataan sen varmistamiseksi, että muovihartsi kuumennetaan oikeaan lämpötilaan korkealaatuisten osien valmistamiseksi.
- Injektio: Sulaa muovia ruiskutetaan muottiin korkeassa paineessa. Painetta pidetään yllä, kunnes muotti on täynnä muovihartsia.
- Jäähdytys: Muotti jäähdytetään muovihartsin jähmettymiseksi ja kappaleen muodostamiseksi. Jäähdytysaika määräytyy käytettävän muovihartsin tyypin sekä valmistettavan osan koon ja muodon mukaan.
- Heitto: Kun osa on jähmettynyt, se poistetaan muotista. Ulosheittotappien avulla osa työnnetään ulos muotista.
- Tarkastus: Muotista valmistettu osa tarkastetaan perusteellisesti sen varmistamiseksi, että se täyttää halutut vaatimukset ja laatustandardit.
- Säädöt: Tarvittaessa muotin suorituskyvyn ja valmistettavien osien laadun parantamiseksi voidaan tehdä säätöjä muovausprosessiin.
Ruiskuvaluprosessin koeammunta on tärkeä vaihe ruiskuvaluprosessissa, sillä sen avulla valmistaja voi arvioida muotin suorituskykyä ja tehdä tarvittavat muutokset ennen suuren kappalemäärän valmistamista. Tämän prosessin avulla voidaan varmistaa, että muotti tuottaa korkealaatuisia osia halutuilla spesifikaatioilla.
Muottipakkaus ja valmis tuotantoon:
Kun muotin valmistaja on saanut muotin täysin valmiiksi, seuraava vaihe on massiivinen tuotanto. Muotin pakkaaminen ja valmistelu tuotantoa varten on viimeinen vaihe ruiskuvaluprosessissa ennen kuin massatuotanto voi alkaa. Tähän vaiheeseen kuuluvat seuraavat tehtävät:
- Puhdistus ja huolto: Muotti puhdistetaan perusteellisesti ja tarkastetaan sen varmistamiseksi, että muotissa ei ole roskia, likaa tai vaurioita.
- Pakkaaminen ja varastointi: Muotti pakataan huolellisesti ja säilytetään turvallisessa paikassa vaurioiden välttämiseksi ja sen varmistamiseksi, että se on käyttövalmis, kun sitä tarvitaan.
- Testaus ja säätö: Muotti testataan mahdollisten ongelmien, kuten vuotojen, huonon täytön tai kappaleen virheellisen ulosheittymisen varalta, ja tarvittavat säädöt tehdään sen varmistamiseksi, että muotti toimii oikein.
- Tuotantojärjestelyt: Muotti asennetaan ruiskuvalukoneeseen ja kaikki tarvittavat asetukset, kuten lämpötila, paine ja ruiskutusnopeus, säädetään vastaamaan erityisiä tuotantovaatimuksia.
- Tuotannon aloittaminen: Ensimmäinen osaerä valmistetaan, ja prosessia valvotaan sen varmistamiseksi, että osat täyttävät vaaditut eritelmät ja laatuvaatimukset. Tuotantoprosessin optimoimiseksi ja tasaisen laadun varmistamiseksi tehdään tarvittavat muutokset.
Kaiken kaikkiaan muotin valmistelu tuotantoa varten on tärkeä vaihe ruiskupuristusprosessissa, joka auttaa varmistamaan tuotannon onnistumisen ja tehokkuuden.
Yllä olevat tiedot ovat menettelyjä ruiskuvalumuotin tekemiseksi, ehkä on joitain pieniä asioita, jotka puuttuvat, mutta useimmat asiat ovat edellä, kuten näet, ruiskuvalumuotin tekeminen ei ole helppo tapaus, jos sinulla on ruiskuvalumuottiprojekti kahvassa, sinun on löydettävä ammattimainen ruiskuvalumuotin valmistaja palvelemaan sinua, tämä varmistaa, että projektisi on käynnissä onnistuneesti.
Sincere Tech on ammattilainen Kiina muotti tehdas, joka on erikoistunut räätälöityjen ruiskuvalumuottien valmistukseen. Heillä on kokemusta ja asiantuntemusta korkealaatuisten ruiskuvalumuottien suunnittelusta, kehittämisestä ja tuotannosta eri teollisuudenaloille ja sovelluksiin.
He tarjoavat erilaisia palveluja, kuten muottien suunnittelua, prototyyppien valmistusta, muottien tuotantoa ja muottien jälkikäsittelyä, varmistaakseen, että heidän asiakkaansa saavat parhaat mahdolliset tulokset. Koska Sincere Tech keskittyy laatuun, tarkkuuteen ja asiakastyytyväisyyteen, se on luotettava ja luotettava kumppani kaikkiin ruiskuvalutarpeisiisi. Ota meihin yhteyttä saadaksesi e-hinnan projektillesi nyt.