Somos Silicona Moldeo por Inyección China empresa que ofrece moldes de plástico / servicio de moldeo, moldes de caucho, Moldeo por inyección de silicona, piezas de moldeo por inyección de silicona líquida al mundo, envíenos su dibujo y le cotizaremos en 24 horas.
¿Qué es el Moldeo por inyección de silicona
La silicona es un tipo de materia prima respetuosa con el medio ambiente, el material de silicona es amado por la gente con sus diversas propiedades perfectas. pieza moldeada por inyección de silicona tiene la suavidad y las propiedades libres de veneno para que ampliamente utilizado en el sellado industrial y dispositivos médicos. Especialmente su temperatura de trabajo: entre menos 60 a 250 grados ninguna empresa de plásticos comparar sus ventajas. El uso de silicona para sellar piezas de metal o de plástico para formar algunas nuevas propiedades y hace que el producto suave y duro. Por ejemplo, la silicona sobremoldeado espátula de cocina es respetuoso con el medio ambiente y es amado por los consumidores. Piezas de moldeo por inyección de silicona y piezas de plástico tienen muy similares, pero tienen diferente procesamiento.
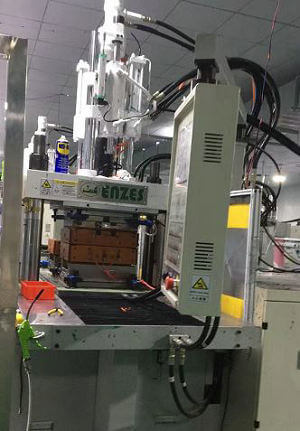
máquinas de moldeo por inyección de silicona
Para trabajar con nosotros es tan fácil, sólo tiene que enviarnos su dibujo y su requisito, entonces su asiento hacia atrás y esperar a que las piezas para la prueba hasta que apruebe las piezas o moldes, vamos a tomar todos los trabajos para su diseño de moldes, fabricación de moldes, muestreo, producción masiva, montaje y entrega a los dioses directamente a su vivienda de almacenamiento, tenemos la mejor agencia de envío que podría ahorrar hasta 30% de costo de envío que otros,
Moldeo por inyección de silicona producen componentes moldeados de silicona. El caucho de silicona es un material bicomponente, sintético, flexible y similar al caucho, fabricado a partir de elastómeros de silicona que pueden curarse a temperatura ambiente hasta convertirse en un elastómero sólido utilizado en moldeo. Es resistente al calor, duradero y no contiene alérgenos ni sustancias químicas lixiviables. La silicona líquida es similar a la silicona normal, pero tiene características de procesamiento diferentes.
Se adquiere como materia prima bicomponente con una viscosidad similar a la grasa.
Hoy en día, el moldeo por inyección de caucho de silicona líquida es cada vez más importante. Uno de los motivos es el aumento de los requisitos de rendimiento de los artículos acabados. Además, cada vez más productores de piezas de caucho ven ventajas en el alto nivel de automatización y productividad.
Varias formas de moldeo por inyección de silicona líquida
Los procesos de moldeo utilizados por los proveedores de servicios de moldeo de silicona incluyen el moldeo por colada, el moldeo por compresión, el moldeo por inmersión, el moldeo por inyección, el moldeo por inyección de reacción, el moldeo rotacional y el moldeo por transferencia.
Mientras que en el proceso de moldeo por fundiciónel material líquido se vierte en un molde abierto, en moldeo por compresión se presiona un trozo de silicona entre 2 mitades de molde calentadas. Por otra parte moldeo por inmersión es un proceso similar al revestimiento por inmersión en caliente, en el que el producto acabado es el plastisol fundido desmoldeado del molde de inmersión. Sin embargo, en moldeo por inyección, silicona líquida se introduce a presión en un molde enfriado. En el Moldeo por inyección de reacción (RIM), dos o más productos químicos reactivos se mezclan a gran velocidad mientras se inyectan en un molde. En moldeo rotacional unos moldes huecos rellenos de material de silicona se fijan a unos radios en forma de tubo que salen de un cubo central. En moldeo por transferenciaA continuación, las dos mitades del molde se sujetan entre sí y la silicona se introduce a presión en el molde.
Por qué el uso preferente del caucho de silicona en moldeo por inyección
El caucho de silicona silástica es un material escurridizo, por lo que su viscosidad depende de la velocidad de cizallamiento. A medida que aumenta la velocidad de cizallamiento, el producto pierde viscosidad. Este efecto es muy favorable para el proceso de moldeo por inyección. Al principio del proceso de inyección, el perfil de velocidad de inyección debe programarse de tal manera que el flujo de volumen sea lo suficientemente alto para que el caucho de silicona líquido no empiece a vulcanizarse antes de que se llene la cavidad, con el fin de evitar que el material se chamusque. Así, el caucho de silicona líquida se utiliza ampliamente para el proceso de moldeo por inyección debido a sus siguientes características:
- Sin disolventes con viscosidad baja y versátil.
- Fácil mezcla y pigmentación
- Procesamiento rápido en comparación con la dispersión con disolventes y, por lo general, permite aplicar un revestimiento completo en una sola pasada.
- La imprimación se adhiere menos al vidrio y a algunos otros sustratos.
- El caucho de silicona líquido mezclado con medidor puede recubrirse por inmersión o alimentarse a un travesaño para el recubrimiento por extrusión con soporte.
Los productos de caucho de silicona vulcanizado tienen las siguientes característicass:
(1) la propiedad resistente a altas y bajas temperaturas: con uso prolongado a 200 ℃y flexibilidad a -60 ℃;
(2) Propiedades de aislamiento eléctrico: el caucho de silicona ofrece excelentes propiedades dieléctricas, muy superiores a las del caucho orgánico general, especialmente a altas temperaturas, con una rigidez dieléctrica casi independiente de la temperatura en el rango de 20-200 ℃.
(3) Excelentes prestaciones de resistencia a la intemperie, resistencia al ozono y resistencia a la radiación ultravioleta sin agrietarse incluso tras un uso prolongado en exteriores. En general, se considera que el caucho de silicona puede utilizarse en exteriores durante más de 20 años.
(4) Excelente propiedad de deformación permanente bajo compresión a alta temperatura.
(5) Las excelencias incluyen un buen rendimiento de procesamiento, fácil de moldear, etc.; se puede hacer una variedad de productos exprimiendo aire caliente con métodos de moldeo de vulcanización, moldeo de patrones, moldeo de extensión, etc.
Con un excelente rendimiento y un buen efecto técnico y económico, los productos de caucho de silicona tienen una amplia gama de aplicaciones en diversas áreas de la aviación, la industria aeroespacial, la energía atómica, los implementos eléctricos, la electrónica, la instrumentación, el automóvil, la maquinaria, la metalurgia, la industria química, la salud médica y la vida cotidiana.
Aplicación y características de los productos de silicona líquida moldeados por inyección:
Tienen una excelente transparencia, excelente resistencia al desgarro, buena elasticidad, excelente estabilidad térmica y resistencia a la intemperie, resistencia al amarilleamiento, resistencia al envejecimiento por calor y se utiliza principalmente en el molde de la torta, chupetes infantiles, catéteres médicos, artesanía de moldeo por inyección y así sucesivamente.
Ventajas de trabajar con el moldeo por inyección de silicona China
Moldeo de caucho de silicona ha recorrido un largo camino en las dos últimas décadas. Desde sus orígenes en unas pocas aplicaciones especializadas en las que las propiedades físicas superiores contaban más que el precio superior, este termoestable se hizo un hueco pequeño pero sólido en los campos de la medicina y la automoción. Ahora, entre la proliferación de nuevas aplicaciones, ese nicho ha empezado a reventar.
Si usted va a ejecutar su negocio con moldeo por inyección de silicona o moldeo de caucho? De cualquier o su nuevo proyecto que necesita piezas de moldeo por inyección de silicona, le sugerimos que encuentre una empresa china de moldeo por inyección de silicona para cooperar su negocio, cuando se trabaja con una empresa china, usted tendrá algunas ventajas para su nuevo modelo y su negocio.
Número uno,
Cuando trabaje con moldeo por inyección de silicona china proveedores, usted tendrá un precio muy competitivo, por lo que podría ahorrar su presupuesto en su nuevo modelo, especialmente si usted es la primera vez que ejecuta su un negocio, este será uno lo más importante para decidir si su negocio va a ir sin problemas o no.
Las ventajas número dos,
Si elige un molde de inyección china proveedor para sus piezas de moldeo de plástico, piezas de moldeo de caucho de silicona, se moverá más rápido que su proveedor local, todos los Empresas chinas de moldeo de silicona son trabajadores, tiempo de entrega rápida, esto ahorrará su tiempo y trabajar su proyecto más rápido en el mercado, cuando se pone algo de dinero en el proyecto, más rápido será más rápido para obtener algunos beneficios de su proyecto.
Por supuesto, hay algunas desventajas cuando se trabaja con un Empresa china de moldeo de siliconapor ejemplo, el idioma. Pero aquí usted no necesita preocuparse más, en nuestra fábrica tenemos un gerente técnico profesional que habla con fluidez Inglés que va a resolver todas sus cuestiones, usted podría ponerse en contacto con nosotros por correo electrónico o por teléfono.