¿Está usted en la cruz en cuanto a si debe utilizar titanio o aluminio aleación para su proyecto? No se preocupe; no es algo que le ocurra sólo a usted, porque muchos ingenieros y diseñadores se encuentran en la misma situación. Estos metales son bastante similares y se utilizan indistintamente, pero también son distintos en sus características, y saber cómo pueden afectar esas características al rendimiento, el gasto y la adaptabilidad es fundamental. La incapacidad para tomar la decisión correcta puede suponer una pérdida de tiempo y gastos adicionales en el proyecto.
Los principales ámbitos de disparidad entre titanio y aluminio El titanio es más resistente a la corrosión y más fuerte que el aluminio en la mayoría de los casos. El titanio es más resistente a la corrosión y es más fuerte que el aluminio la mayoría de las veces, por lo que es perfecto para su uso en entornos de trabajo duro o en áreas que requieran su fuerza, mientras que el aluminio es más ligero, más barato y se adapta perfectamente a un uso normal. Por último, la decisión pasa por ciertos parámetros como el peso y las condiciones en las que se utilizará el equipo.
Ahora que ya conoce las diferencias entre el titanio y el aluminio, veamos las características individuales y los usos de cada metal. Teniendo en cuenta estos factores, podrá tomar una decisión más adecuada para su proyecto. Siga leyendo para saber qué material le conviene más.
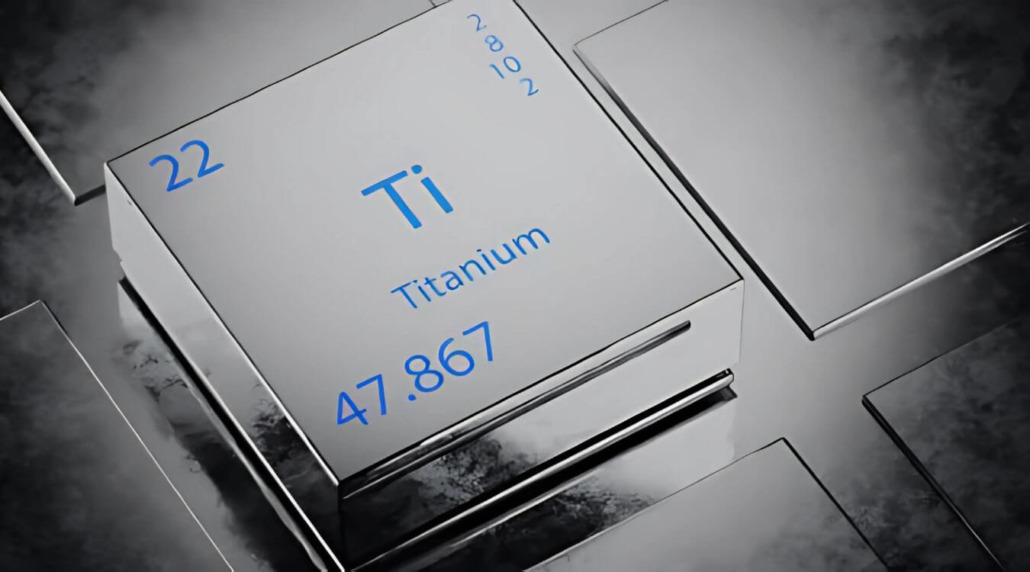
Titanio frente a aluminio: Comparación de sus propiedades
Una comparación de este tipo podría resultar incompleta si no se tienen en cuenta las distintas propiedades de cada material que afectan a su rendimiento en función de las diferentes aplicaciones. El titanio también tiene una relación resistencia-peso superior a la del acero, por lo que no sólo es fuerte, sino también ligero. También tiene una excelente resistencia a la corrosión, especialmente en condiciones severas se utiliza para la industria aeroespacial, implantes médicos, y marina. En cambio, el aluminio es un material ligero, fácil de mecanizar y relativamente más barato que el cobre. Se utiliza en aplicaciones de automoción, construcción y productos de consumo por su versatilidad y facilidad de fabricación.
Propiedades mecánicas
Quizá la más importante sea la comparación de propiedades mecánicas entre titanio y aluminio. El TiAl tiene una resistencia última a la tracción de aproximadamente 434 MPa a 1400 MPa, en función del tipo de aleación utilizada en su producción, mientras que el aluminio tiene una resistencia última a la tracción de aproximadamente 90 MPa a 700 MPa. Esto significa que el titanio puede soportar mucha tensión antes de fallar, por lo que lo ideal es utilizarlo cuando se necesita una gran resistencia. En cuanto al alargamiento, el titanio es menos dúctil que el aluminio, por lo que éste puede deformarse más fácilmente sin fracturarse, lo que da más libertad de diseño.
Consideraciones sobre el peso
Otra consideración importante a la hora de elegir entre estos metales es el peso. El aluminio es mucho más ligero que el titanio, con una densidad de 2,7 g/cm³ frente a los 4,5 g/cm³ del titanio. Esta menor densidad hace que el aluminio sea muy utilizado en industrias en las que hay que reducir el peso, por ejemplo en la fabricación de aviones y coches. Sin embargo, los elevados requisitos de resistencia, junto con el ahorro de peso, hacen que el titanio se imponga aunque sea más pesado que los demás materiales.
Resistencia a la corrosión
Ambos tienen características de resistencia a la corrosión bastante buenas, aunque la resistencia se da en medios diferentes. Afirmó que la resistencia a la corrosión del titanio es excelente en entornos de servicio severos, especialmente cuando se expone al cloro o al agua salada, y que tener una capa de óxido densa en la superficie del material impide la corrosión posterior. El aluminio también forma una capa de óxido, pero es vulnerable al ataque por picaduras en algunas condiciones específicas; por ejemplo, reacciona con agua de mar o álcali caliente. Por eso, el titanio encuentra su aplicación en las industrias naval y de procesamiento químico.
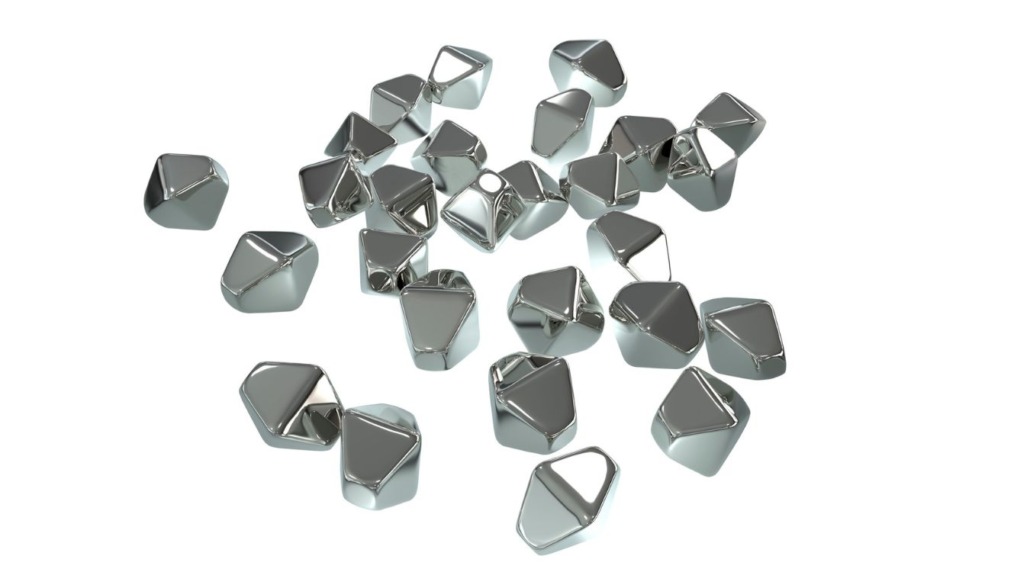
Conductividad térmica y conductividad
El coeficiente térmico también debe tenerse en cuenta a la hora de seleccionar la aleación de titanio y aluminio. En concreto, la conductividad térmica del aluminio se cifra en unos 205 W/mK, mientras que la del titanio es de unos 21,9 W/mK. Esto hace que el aluminio sea más conductor del calor en aplicaciones como intercambiadores de calor y sistemas de refrigeración. Sin embargo, tener una conductividad térmica más baja también es beneficioso en lugares donde no se necesita calor, como en espacios utilizados para la construcción de aviones, entre otros.
Coste y disponibilidad
El coste es una de las consideraciones más importantes a la hora de elegir el material que se utilizará en la construcción. En la mayoría de los casos, es probable que el aluminio esté más disponible y sea más barato que el titanio, por lo que puede ser más adecuado para varios usos. Los procesos de fabricación del aluminio también están muy bien definidos y a menudo el proceso global es menos complejo y, por tanto, más barato. En cambio, la extracción y el tratamiento del titanio son caros y difíciles, por lo que su aplicación se limita a ámbitos en los que sus propiedades ofrecen un gran valor.
Resumen de las solicitudes
Por lo tanto, existe una comparación directa entre el Titanio y el Aluminio y depende de la naturaleza del proyecto que se tenga que realizar. El titanio se ha tenido en cuenta en las industrias aeroespacial, biomédica y marina, donde son fundamentales las propiedades de alta resistencia y resistencia superior a la corrosión. El aluminio se utiliza mucho en la industria del automóvil, la construcción y otros bienes de consumo por su ligereza, bajo coste y facilidad de transformación. El conocimiento de estas propiedades puede ayudar a los ingenieros y diseñadores a tomar decisiones correctas en función de los objetivos del proyecto concreto.
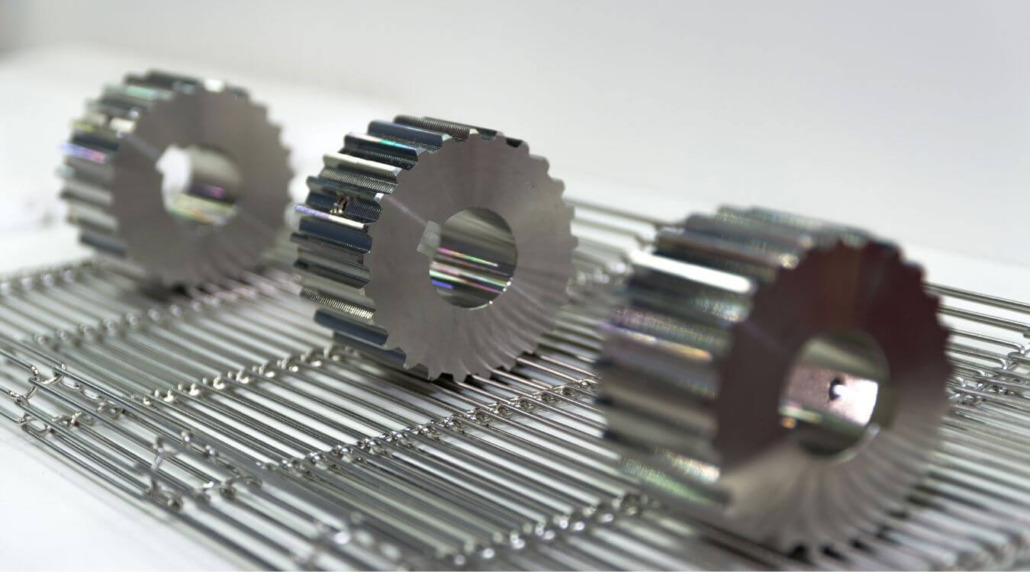
He aquí un cuadro comparativo de las propiedades del titanio y el aluminio, seguido de un resumen técnico de las principales diferencias.
Propiedad | Titanio | Aluminio |
Densidad | 4,5 g/cm³ | 2,7 g/cm³ |
Resistencia a la tracción | 434 - 1.400 MPa | 90 - 700 MPa |
Límite elástico | 880 - 1.200 MPa | 40 - 550 MPa |
Alargamiento | 10 - 30% (varía según la aleación) | 12 - 25% (varía según la aleación) |
Resistencia a la corrosión | Excelente (especialmente en ambientes salinos y agresivos) | Buena (pero susceptible a las picaduras) |
Conductividad térmica | 21,9 W/mK | 205 W/mK |
Conductividad eléctrica | 2,0 x 10^6 S/m | 3,5 x 10^7 S/m |
Punto de fusión | 1,668 °C | 660 °C |
Módulo de elasticidad | 110 - 120 GPa | 70 - 80 GPa |
Coste | Alta (más cara de extraer y procesar) | Inferior (abundante y rentable) |
Maquinabilidad | Difícil (requiere herramientas especializadas) | Bueno (más fácil de mecanizar y fabricar) |
Aplicaciones | Aeroespacial, implantes médicos, náutica, automoción | Automoción, construcción, bienes de consumo |
Introducción al aluminio
El aluminio es ligero, resistente y maleable. Es el tercer metal más abundante de la corteza terrestre y se obtiene principalmente de la bauxita. El aluminio es un metal de color plateado apreciado en las industrias aeroespacial, automovilística, de la construcción y del embalaje, entre otras. Tiene algunas propiedades como una alta resistencia a la corrosión y una buena conductividad térmica y eléctrica que lo hacen vital para muchos usos. Además, el aluminio es 100% reciclable, por lo que es respetuoso con el medio ambiente para los fabricantes y consumidores que lo prefieren.
En moldes de fundición a presión son una de las tecnologías para fabricar aleaciones de aluminio, como ADC 12, A380, etc, por supuesto hay otras tecnologías de fabricación que podrían hacer material de aluminio, esos incluyen fundición en arena, moldeo por extrusión, fundición por gravedad, mecanizado, etc.
Aplicaciones del aluminio
- Industria aeroespacial: El aluminio tiene una gran aplicación en la industria aeroespacial en forma de armazones de fuselaje, alas y trenes de aterrizaje. Gracias a su ligereza y alta resistencia, puede utilizarse para mejorar la eficacia de la combustión y el rendimiento general del avión.
- Fabricación de automóviles: En la industria del automóvil, el aluminio se aplica para crear bloques de motor, carrocerías, ruedas y estructuras de vehículos. Estas propiedades hacen que el coche sea más ligero, con lo que se consigue un mayor kilometraje y menos contaminación.
- Construcción y Arquitectura: El aluminio se utiliza ampliamente en la fabricación de ventanas, puertas, tejados y paredes mediante el uso de marcos y revestimientos. Debido a su durabilidad, no se corroe con facilidad y es fácil de mantener, por lo que es adecuado para su uso en viviendas y otros edificios.
- Soluciones de envasado: El envasado es otra de las principales aplicaciones del aluminio, que se utiliza en botellas de cerveza, latas de alimentos y láminas de aluminio. Estas propiedades lo convierten en un material excelente para la protección del contenido, es ligero y puede reciclarse.
- Electrónica y aplicaciones eléctricas: El aluminio se aplica en disipadores de calor, carcasas y conectores. Por su buena conductividad eléctrica, se utiliza en cableados y otras piezas electrónicas.
- Bienes de consumo: En bienes de consumo, el aluminio se utiliza mucho en utensilios de cocina y muebles por su aspecto moderno y su resistencia. Se utiliza sobre todo en artículos como utensilios de cocina, bicicletas y equipamiento deportivo.
- Aplicaciones marinas: La resistencia a la corrosión del aluminio lo hace adecuado para su uso en la fabricación de cascos de barcos, estructuras marinas y otras piezas susceptibles de entrar en contacto con el agua de mar.
- Equipos industriales: En aplicaciones industriales, el aluminio encuentra aplicación en piezas de maquinaria, bastidores y utillaje, ya que es fuerte para su tamaño y, por tanto, reduce la fatiga.
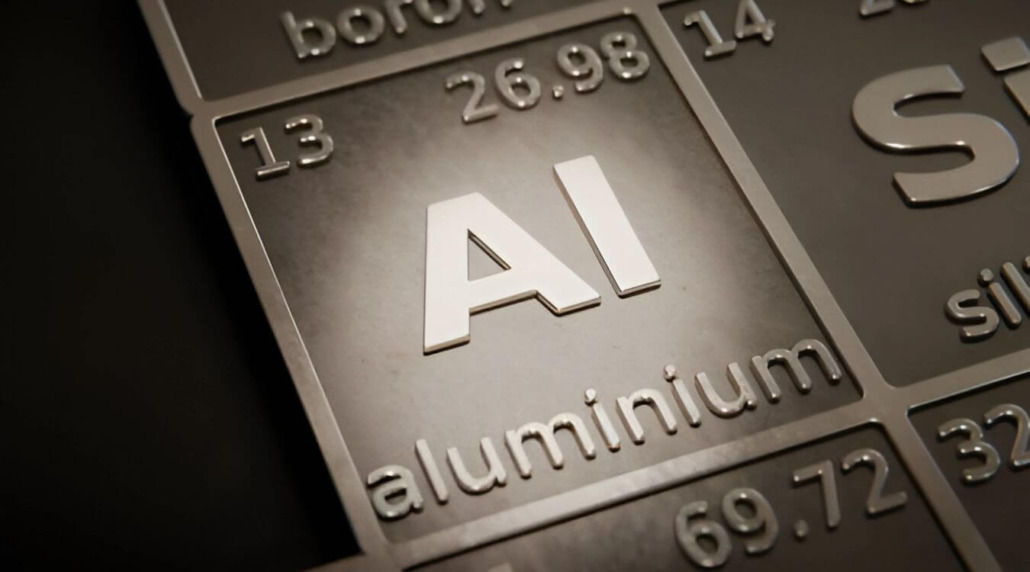
Opciones de mecanizado del aluminio
- Mecanizado CNC: El mecanizado CNC es una técnica familiar utilizada en la producción de piezas de aluminio. Puede utilizarse para cortar, taladrar y fresar formas y tamaños demasiado intrincados para otros métodos convencionales.
- Fresado: El fresado es un proceso que utiliza herramientas de corte giratorias para eliminar material de la pieza. Es relativamente fácil trabajar con fresas y fresas frontales, por lo que resulta adecuado para tallar diseños.
- Girando: En las operaciones de torneado, las piezas de aluminio se hacen girar y, mediante herramientas de corte, se elimina material para producir formas cilíndricas. Este método es especialmente adecuado para la fabricación de ejes, barras y accesorios.
- Extrusión: La extrusión de aluminio es un proceso de producción de grandes longitudes de perfiles utilizando aluminio a través de una matriz, incluyendo barras, tubos y canales a altas temperaturas. También permite una forma transversal consistente de los miembros estructurales.
- Fundición a presión: La fundición a presión es un proceso de fabricación de piezas complejas de aluminio mediante el forzado de metal fundido en un molde. Esta técnica es más aplicable en volúmenes de producción elevados en los que el diseño es complicado.
- Corte por láser: El corte por láser proporciona cortes limpios y precisos en chapas y piezas de aluminio. Esta técnica es especialmente adecuada para formas y diseños intrincados y, por tanto, ideal para su uso en diseño ornamental y práctico.
- Corte por chorro de agua: El corte por chorro de agua consiste en utilizar agua a alta presión mezclada con abrasivos para cortar aluminio. Este método es adecuado para materiales gruesos y no crea zonas afectadas por el calor.
- Doblado y conformado: El aluminio puede conformarse mediante varias técnicas, como el conformado por frenado y el conformado por laminación, porque es relativamente fácil de manipular. Estos procesos se aplican en la producción de piezas estructurales y carcasas.
Introducción al titanio
El titanio es un metal fuerte pero ligero que se caracteriza por su gran resistencia a la corrosión y, por lo general, su gran durabilidad. El titanio es el noveno componente más abundante en la corteza terrestre y se obtiene de minerales como el rutilo o la ilmenita. Al ser ~1,45 veces más ligero que el acero y también tan resistente como éste, el titanio es adecuado para todas las aplicaciones de alto rendimiento. Su capacidad para resistir condiciones corrosivas, es decir, para trabajar eficazmente en ambientes marinos, químicos y a temperaturas altas y bajas, también lo hace adecuado para aplicaciones aeroespaciales, médicas y marinas. Además, el titanio es biocompatible, lo que lo hace útil para su uso en implantes y dispositivos médicos. Las características beneficiosas del titanio son muy importantes para el desarrollo de la tecnología y la innovación en diversos ámbitos.
Aplicaciones del titanio
- Industria aeroespacial: El titanio se aplica ampliamente en la industria aeroespacial por su elevada relación resistencia-peso y su estabilidad a altas temperaturas. Se utiliza en piezas como bastidores, motores y trenes de aterrizaje para mejorar la eficiencia del combustible y el rendimiento.
- Productos sanitarios: El titanio es muy biocompatible, por lo que se utiliza en determinados implantes médicos y productos relacionados con la medicina, como implantes ortopédicos, implantes dentales, accesorios e instrumentos de corte, entre otros. Es resistente a la corrosión y se funde fácilmente con el hueso, lo que hace que estos productos sean duraderos y eficaces.
- Aplicaciones marinas: En esencia, el titanio tiene excelentes características anticorrosión para aplicaciones en agua de mar. El material se aplica a piezas como cascos de barcos, hélices y otras piezas submarinas en las que se requiere la presencia de un material muy resistente.
- Procesamiento químico: En la industria química, el uso del titanio es muy resistente a los usos químicos y a altas temperaturas. Se aplica en intercambiadores de calor, reactores y tuberías, lo que le permite ofrecer servicios duraderos, especialmente en condiciones corrosivas.
- Sector energético: Algunas de las aplicaciones específicas del titanio relacionadas con la energía son las plataformas petrolíferas en alta mar y las centrales eléctricas de gas y petróleo. Su gran solidez y excelente resistencia a la corrosión lo hacen adecuado para su uso en piezas expuestas a entornos hostiles.
- Industria del automóvil: El titanio se utiliza en vehículos de alto rendimiento para sistemas de escape y piezas del motor de combustión interna, así como en elementos estructurales ligeros. Su punto fuerte es que también reduce el peso del vehículo al tiempo que mejora el rendimiento, lo que redunda en el ahorro de combustible.
- Equipamiento deportivo: La principal aplicación del titanio es el equipamiento deportivo, como cuadros de bicicleta, palos de golf y raquetas de tenis, donde la ligereza es importante y la resistencia, imprescindible para una larga vida útil.
- Productos de consumo: El uso de titanio en productos de consumo es bastante habitual, ya que aporta resistencia, ligereza y un aspecto lujoso a relojes, joyas y herramientas.
Opciones de mecanizado para el titanio
- Mecanizado CNC: El mecanizado CNC es una técnica muy utilizada para fabricar piezas de titanio complejas y precisas. Este proceso permite realizar trabajos de gran precisión y un control dimensional estricto, y se utiliza ampliamente en aplicaciones aeroespaciales y médicas.
- Fresado: Se ha comprobado que el fresado de titanio puede realizarse utilizando herramientas y estrategias adecuadas. El fresado a alta velocidad se utiliza para reducir la tasa de eliminación de material, preservando al mismo tiempo la integridad de la superficie.
- Girando: Las operaciones de torneado se emplean ampliamente para fabricar piezas cilíndricas de titanio. En esta técnica, la pieza de titanio se mantiene inmóvil mientras la herramienta de corte se utiliza para eliminar material y formar ejes, tubos y accesorios mientras la pieza gira.
- Corte por chorro de agua: El método de corte por chorro de agua proporciona un corte eficaz del titanio sin calor, que puede alterar las propiedades del material. Esta técnica es más aplicable a formas complejas y materiales gruesos.
- Mecanizado por electroerosión EDM: EDM son las siglas en inglés de Mecanizado por Descarga Eléctrica, que se utiliza para completar formas en titanio. Se trata de un proceso de mecanizado no convencional aplicable a materiales duros con un alto nivel de precisión en formas complejas.
- Corte por láser: El titanio puede cortarse por láser para chapas y piezas, y el proceso produce bordes excepcionalmente limpios. Este método es el más adecuado para trabajos finos y en materiales delgados.
- Conformado y plegado: El titanio también puede forjarse y doblarse mediante procesos como el perfilado y el plegado. Estos procesos permiten generar elementos estructurales y envolventes que conservan las propiedades del material.
- Impresión 3D (fabricación aditiva): El titanio es el material más utilizado en la fabricación aditiva (impresión 3D) por sus ventajas y la libertad de sus diseños. Esta tecnología puede utilizarse para crear prototipos y construir productos de baja densidad.
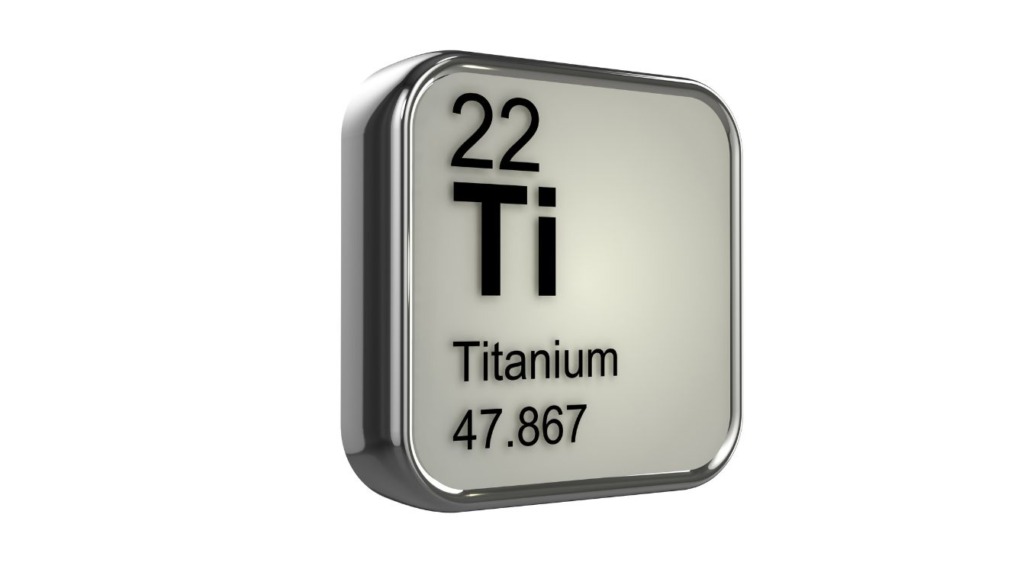
Titanio frente a aluminio: ventajas e inconvenientes
A la hora de seleccionar materiales para aplicaciones de ingeniería, es esencial sopesar las ventajas e inconvenientes del titanio y la aleación de aluminio. Cada metal tiene propiedades únicas que lo hacen adecuado para distintos escenarios. La siguiente tabla presenta un desglose lógico de los principales pros y contras de cada material.
Propiedad | Aluminio | Titanio |
Peso | Ventajas: Ligero (densidad ~2,7 g/cm³), lo que lo hace ideal para aplicaciones que requieren reducción de peso. | Ventajas: Más ligero que el acero (densidad ~4,5 g/cm³), ofrece un buen equilibrio entre resistencia y peso para aplicaciones exigentes. |
Fuerza | Contras: Resistencia a la tracción generalmente inferior (90-700 MPa) en comparación con el titanio, lo que puede limitar su uso en aplicaciones de alta tensión. | Ventajas: Alta resistencia a la tracción (434-1.400 MPa), que proporciona un rendimiento excepcional bajo carga y en entornos de altas temperaturas. |
Resistencia a la corrosión | Contras: Resistencia moderada; susceptible a las picaduras en entornos duros. | Ventajas: Excelente resistencia a la corrosión, especialmente en ambientes marinos y químicos, gracias a una capa protectora de óxido. |
Coste | Ventajas: Generalmente más económico; ampliamente disponible y menos costoso de producir. | Contras: Mayor coste debido a los complejos métodos de extracción y procesamiento, lo que la hace menos accesible para algunas aplicaciones. |
Maquinabilidad | Ventajas: Fácil de mecanizar con herramientas estándar, lo que lo hace adecuado para la producción de grandes volúmenes. | Contras: Más difícil de mecanizar; requiere herramientas y técnicas especializadas, lo que puede aumentar el tiempo y los costes de fabricación. |
Conductividad térmica | Ventajas: Alta conductividad térmica (205 W/mK), ideal para aplicaciones de disipación de calor. | Contras: Menor conductividad térmica (21,9 W/mK), lo que limita su eficacia en aplicaciones que requieren una transferencia de calor eficiente. |
Conductividad eléctrica | Ventajas: Excelente conductor eléctrico (3,5 x 10^7 S/m), adecuado para aplicaciones eléctricas. | Contras: Menor conductividad eléctrica (2,0 x 10^6 S/m), lo que la hace menos adecuada para aplicaciones eléctricas. |
Reciclabilidad | Ventajas: Altamente reciclable, conserva sus propiedades tras el reciclado, contribuyendo a la sostenibilidad. | Ventajas: También reciclable, aunque se procesa con menos frecuencia debido a los mayores costes asociados al reciclaje del titanio. |
Aplicaciones | Ventajas: Versátil; se utiliza en automoción, aeroespacial, construcción y envasado debido a sus propiedades favorables. | Ventajas: Aplicaciones especializadas; fundamentales en los sectores aeroespacial, médico y de alto rendimiento, donde la resistencia y la durabilidad son esenciales. |
Resistencia al calor | Contras: Punto de fusión más bajo (~660 °C); puede deformarse a temperaturas elevadas, lo que limita las aplicaciones a altas temperaturas. | Ventajas: Alto punto de fusión (~1.668 °C); se comporta excepcionalmente bien en condiciones térmicas extremas. |
¿Cómo elegir entre titanio y aluminio?
Para evaluar la idoneidad de los dos metales, es decir, el titanio o el aluminio, para un uso determinado, deben tenerse debidamente en cuenta varios factores técnicos que se indican a continuación. El titanio tiene una elevada relación resistencia-peso, una excelente resistencia a la corrosión, especialmente en condiciones severas, y se utiliza en piezas de alto rendimiento; sin embargo, es relativamente caro, con un precio medio entre $10 y $30 por libra.
El aluminio, por su parte, cuesta entre $1,4 y $2 por libra, tiene buena maquinabilidad y conductividad térmica y es ideal para la producción a gran escala y en zonas donde el peso es una preocupación importante. También hay que tener en cuenta los costes de transformación, porque el titanio necesita tiempo y dinero para ser mecanizado, mientras que el aluminio puede fabricarse más rápido y barato. A la larga, será posible hacer una evaluación adecuada de estos factores, especialmente los costes, así como de los requisitos de la aplicación, mediante la cual se hará la elección adecuada del material.
Hay muchos Fundición a presión en China Las empresas que fabrican piezas de fundición de aluminio y venden a todo el mundo, por lo que normalmente el aluminio será más popular en la mayoría de las industrias, por supuesto, algunas de las industrias deben utilizar matreial titanio.
Conclusión
En conclusión, la determinación de cuál de los dos metales utilizar al desarrollar su proyecto de ingeniería civil depende de las especificaciones de su proyecto. Sin embargo, debido a su mayor coste en comparación con otros metales y a sus propiedades de difícil mecanización, el titanio se está utilizando en la aviación y la medicina por su gran resistencia a la corrosión y al desgaste. Por su parte, el aluminio es popular por ser un material ligero, fácil de procesar y relativamente barato, que puede utilizarse en casi todos los sectores, como la automoción y la construcción. Por último, el conocimiento de los puntos fuertes y débiles y del coste de cada tipo de material permitirá a los ingenieros y diseñadores tomar la mejor decisión en función de los objetivos y las operaciones del proyecto.
Preguntas más frecuentes
Q1. ¿Cuáles son las principales diferencias de resistencia entre el titanio y el aluminio?
Titanio tiene una resistencia a la tracción de entre 434 y 1400 MPa, mientras que el aluminio tiene una resistencia a la tracción de entre 90 y 700 MPa, por lo que el titanio es mejor para grandes esfuerzos.
Q2. ¿Qué material, titanio frente a aluminio, tiene mejores propiedades de resistencia a la corrosión?
El titanio es más útil en condiciones corrosivas, ya que crea una capa de óxido, y el aluminio sólo presenta una corrosión moderada y puede picarse en algunas circunstancias.
Q3. ¿Cómo influye el peso en la decisión entre una aleación de aluminio y una de titanio?
El aluminio es mucho más ligero (densidad ~2,7 g/cm³), por lo que es preferible utilizarlo en aplicaciones sensibles al peso, mientras que la densidad del titanio es de ~4,5 g/cm³, lo que le confiere una mayor resistencia y, por tanto, su peso puede explicarse por determinadas aplicaciones de alto rendimiento.
Q4. ¿Cómo influyen los costes de mecanizado de la aleación de titanio y aluminio?
El aluminio es más fácil de mecanizar y más barato que el titanio, que necesita instrumentos y procesos específicos, de ahí el alto coste de mano de obra y procesamiento.
Q5. ¿En qué industria se utiliza principalmente cada metal? El titanio se utiliza ampliamente en los sectores aeroespacial, médico, automovilístico, etc., y el aluminio se emplea en las industrias del automóvil, la construcción, el envasado y otros sectores industriales debido a su bajo precio y a sus usos.