Moldeo de caucho de silicona líquida
Método de Caucho de silicona líquida Moldura
Cuando hablamos de caucho de silicona en forma líquida (LSR), se trata de una red que se divide en dos partes. En esta red, las cadenas largas de polisiloxano están soportadas con sílice. La parte A contiene un catalizador de platino y la parte B contiene metil hidrógeno siloxano como reticulante y un inhibidor de alcohol. Los cauchos de silicona son polímeros de dos partes y pueden contener rellenos para mejorar las propiedades o reducir el costo. El caucho de silicona es en su mayor parte no reactivo, estable e impermeable a condiciones y temperaturas extremas de −55 a 300 °C (−70 a 570 °F) al mismo tiempo que mantiene sus propiedades.
Definición
Cuando definimos el caucho de silicona en forma líquida, se trata de un polímero de naturaleza inorgánica compuesto de silicio (Si), oxígeno (O), carbono (C) e hidrógeno (H). La cadena sintética vital llamada columna vertebral está compuesta de silicio y oxígeno, llamado siloxano. Se trata de una silicona curada con platino de alta calidad con una suavidad brillante. Con frecuencia se infunde en una cavidad de molde de silicona para fabricar varias piezas con gran precisión. En general, el caucho de silicona líquida tiene una baja deformación por compresión, buena estabilidad y resistencia a temperaturas extremas de calor y frío. Este material se utiliza principalmente para crear sellos, membranas de sellado, conectores eléctricos, conectores multipines y productos infantiles donde se requieren superficies lisas.
La naturaleza inorgánica del LSR lo hace ideal para aplicaciones médicas y de contacto con la piel. El LSR tiene la capacidad de combinarse con otros grupos químicos, lo que le permite lograr un rendimiento robusto. El LSR supera a muchos otros elastómeros y se utiliza en pulsadores o aplicaciones de teclado, y es el preferido para aplicaciones de bombeo, en particular si está en contacto con fluidos corporales o sustancias químicas.
Moldeo por inyección de caucho de silicona líquida
Este es un proceso muy mecanizado. Moldeo por inyección de silicona líquida Utiliza un método de mezcla mecánica que combina un compuesto de material LSR curado con platino de dos componentes que fluye hacia un molde. Sin embargo, debido a la naturaleza viscosa del LSR, se procesa fácilmente y es perfectamente adecuado para la producción de alto volumen, la calidad constante de las piezas y la mejora de la productividad. La herramienta de inyección de LSR está alojada en una prensa de moldeo por inyección específica para LSR, que está especialmente diseñada para un control preciso del tamaño de la inyección y permite la producción constante de componentes de caucho de silicona líquida. Debido a sus propiedades y procesabilidad, el caucho de silicona líquida se ha convertido en el material ideal para características de diseño intrincadas y aplicaciones críticas exigentes.
Proceso de moldeo por inyección de LSR
Este proceso es termoendurecible por naturaleza y se utiliza para fabricar piezas y productos de silicona flexibles, duraderos y resistentes al calor. En este proceso se mezclan dos compuestos que generalmente consisten en la silicona formadora de la base y el catalizador de platino. Después de eso, la mezcla se inyecta y se cura con calor dentro de un molde creando piezas de silicona flexibles. Sin embargo, estos dos compuestos requieren una mezcla distributiva intensiva mientras se mantienen a baja temperatura antes de empujarlos hacia una cavidad calentada. El caucho de silicona líquida se cura mediante calor, produciendo piezas o productos sólidos.
Este proceso se emplea ampliamente en diversas industrias, entre ellas la automotriz, la médica, la de bienes de consumo y la electrónica. El proceso de moldeo por inyección de LSR consta principalmente de los siguientes pasos principales.
1. Preparación del material
Compuestos LSR:LSR es un compuesto de dos partes que normalmente se denomina material formador de base y catalizador, que generalmente está basado en platino. Estas partes se mezclan en una proporción de 1:1 y pueden incluir componentes adicionales como pigmentos o aditivos.
Almacenamiento y manipulación: Los componentes de LSR se almacenan en contenedores o cartuchos. Un contenedor contiene el material que forma la base y otro contenedor contiene el catalizador, generalmente a base de platino. Una manipulación adecuada es muy importante para evitar la contaminación y garantizar propiedades uniformes del material.
2. Mezcla y medición
Unidad de mezcla: Una unidad de mezcla especializada combina con precisión ambos compuestos. Esta unidad también puede incorporar pigmentos u otros aditivos según sea necesario.
Mezclador estático: El LSR mezclado pasa luego a través de un mezclador estático, lo que garantiza una homogeneización completa de los componentes. Este paso es vital para garantizar un curado y unas propiedades uniformes del producto final.
Medida: En este importante paso, el LSR mezclado se dosifica en la unidad de inyección. Una dosificación precisa es esencial para mantener tamaños de inyección uniformes y reducir el desperdicio de material.
3. Máquina de moldeo por inyección
- Unidad de inyección: La unidad de inyección está diseñada específicamente para la inyección de LSR. El LSR tiene una viscosidad baja y requiere diseños de tornillos especiales. En este paso, el material se empuja dentro de la cavidad del molde.
- Unidad de sujeción: En este paso se utiliza una pinza para sujetar el molde y mantenerlo cerrado cuando se realiza la inyección. No obstante, la potencia necesaria depende del tamaño y la complejidad de la pieza.
4. Diseño de moldes
- Consideraciones materiales: Los moldes para LSR deben estar diseñados para soportar las altas temperaturas y tensiones que se aplican durante el sistema de curado. La mayoría de las veces se fabrican utilizando acero o aluminio de excelente calidad.
- Cavidad y núcleo: El molde de inyección de silicona consta de cavidades, que son formas de piezas negativas, y núcleos, que son formas de piezas positivas. Estos deben mecanizarse con precisión para lograr los aspectos de la pieza y el acabado de la superficie ideales.
- Desfogue: El aire queda atrapado y es necesario liberarlo para evitar defectos como burbujas de aire o espacios vacíos en el producto final. Por lo tanto, es importante garantizar una ventilación adecuada.
- Sistema eyector: Este paso implica la extracción de la pieza del molde que se ha curado. El sistema de expulsión debe estar cuidadosamente diseñado para manipular las piezas de LSR flexibles y pegajosas.
5. Inyección y curado
- Proceso de inyección: El molde se cierra firmemente y se sujeta con la fuerza adecuada. A continuación, se inyecta el LSR en las cavidades del molde a alta velocidad. A continuación, se llena el molde y, después, se retira el material sobrante.
- Proceso de curado: La temperatura se mantiene alta (normalmente entre 160 y 200 °C) para iniciar el proceso de curado. El tiempo de curado depende del grosor y la forma de la pieza. Por lo general, oscila entre un par de segundos y varios minutos.
6. Desmoldeo
- Enfriamiento: Una vez finalizado el curado, el molde se enfría para trabajar con expulsión de piezas y evitar deformaciones.
- Apertura: Después de eso, el molde se abre con cuidado para evitar dañar las delicadas piezas de LSR.
- Expulsión: En este paso, las piezas se expulsan del molde mediante el sistema de expulsión. Es necesario manipularlas con cuidado, ya que aún están calientes y pueden ser ligeramente flexibles.
7. Posprocesamiento
- Inspección: En esta etapa se inspecciona cada pieza para detectar defectos como rebabas, burbujas de aire o llenado incompleto. Se pueden utilizar métodos de inspección tanto automáticos como manuales.
- Guarnición: Después de eso, se elimina el material sobrante, conocido como rebaba, de las piezas. Esto se puede hacer de forma manual o con equipos automatizados.
- Operaciones secundarias: Se pueden realizar procesos adicionales como unión, ensamblaje o tratamiento de superficie según la aplicación y el requisito.
8. Control de calidad
- Pruebas: Para garantizar que las piezas entregadas cumplen con las especificaciones necesarias, se someten a diferentes pruebas, que incluyen pruebas de propiedades mecánicas, controles dimensionales y exámenes visuales.
- Documentación: Se mantienen periódicamente registros detallados del proceso de moldeo, los lotes de material y los resultados del control de calidad para la trazabilidad y el cumplimiento de los estándares de la industria.
9. Embalaje y envío
- Embalaje:Las piezas terminadas se embalan cuidadosamente para protegerlas durante el transporte. Las técnicas de embalaje varían en función del tamaño, la forma y la sensibilidad de la pieza.
- Envío: Luego, las piezas empaquetadas se envían a los clientes o a las instalaciones de procesamiento posterior, lo que garantiza una entrega oportuna y mantiene la integridad de las piezas.
Beneficios del moldeo por inyección de LSR
Este proceso ofrece algunas ventajas principales, que son las siguientes:
1. Precisión y consistencia
El moldeo por inyección de LSR ofrece valores altos, consistentes y precisos en la producción de piezas complejas, intrincadas y detalladas. Este proceso permite tolerancias estrictas y una reproducción precisa de los moldes, lo que garantiza la uniformidad en todos los lotes.
2. Amplia gama de aplicaciones
Esto ofrece una gran cantidad de aplicaciones, ya que es flexible y se puede utilizar en diferentes sectores, como la automoción, la clínica, el hardware, los productos de consumo y mucho más. La flexibilidad que ofrece el LSR lo hace adecuado para producir cualquier cosa, desde implantes médicos hasta sellos para automóviles y componentes electrónicos de consumo.
3.Durabilidad y resistencia
Estas piezas se destacan por su solidez y resistencia. Pueden soportar temperaturas extremas, compuestos sintéticos agresivos y exposición prolongada a la radiación UV sin mermar sus propiedades integrales durante un largo período de tiempo, lo que las hace ideales para muchas aplicaciones.
4.Biocompatibilidad
Estos materiales son biocompatibles y cumplen con los requisitos de los estándares de grado médico. Esta cualidad los hace apropiados para aplicaciones clínicas y de servicios médicos como implantes, herramientas quirúrgicas y dispositivos clínicos portátiles. Además, son hipoalergénicos y seguros para el contacto prolongado con la piel.
5. Resistencia química
Estos materiales ofrecen una gran protección frente a muchos productos sintéticos, incluidos disolventes, aceites y agentes de limpieza. Esta propiedad los hace apropiados para su uso en condiciones en las que la exposición a sustancias químicas es normal, como en los entornos automotrices e industriales modernos.
6. Flexibilidad y elasticidad
Estas piezas tienen la propiedad de una elasticidad y flexibilidad notables, lo que les permite deformarse y recuperar su forma única sin distorsión duradera. Esta adaptabilidad las hace ideales para su uso en aplicaciones de sellado y empaquetado donde se requiere un sellado hermético y sólido.
7. Tiempos de ciclo rápidos
Este método ofrece un tiempo de procesamiento más rápido en comparación con los métodos de moldeo de caucho convencionales, lo que permite una alta producción con tiempos de entrega rápidos y, al mismo tiempo, es rentable.
8. Reducción de residuos
El moldeo por inyección de LSR genera un desperdicio mínimo en comparación con otros procesos de fabricación. La capacidad de controlar con precisión el flujo de material y optimizar los diseños de moldes minimiza el desperdicio de material. En consecuencia, esto genera ahorros de costos y beneficios ambientales.
9. Libertad de diseño
Este proceso permite desarrollar formas y geometrías complejas que podrían resultar difíciles de lograr con otros métodos de fabricación. Esta libertad de diseño permite crear diseños de artículos imaginativos y opciones de personalización.
10. Acabado de la superficie
Estas piezas tienen un acabado superficial liso e inmaculado desde el primer momento, lo que reduce la necesidad de realizar tareas de acabado secundarias, como limpieza o pintura. Esto ahorra tiempo y costos de mano de obra, y hace que el proceso sea rentable, al tiempo que garantiza un producto final de alta calidad.
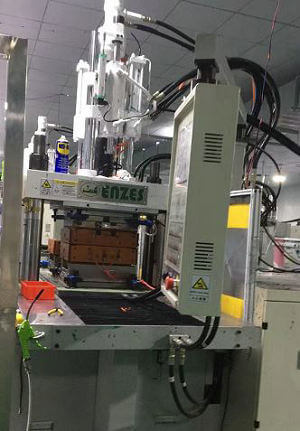
máquinas de moldeo por inyección de silicona
Limitaciones del moldeo de caucho de silicona líquida
Este proceso ofrece diversos beneficios, sin embargo como cualquier proceso de fabricación tiene algunas limitaciones que son las siguientes:
1. Alta inversión inicial
Para poner en marcha un proceso de moldeo por inyección de LSR se requiere una inversión inicial significativa, principalmente en equipos, moldes e infraestructura especializados, por lo que esto puede ser un obstáculo para los fabricantes a pequeña escala o aquellos con capital limitado.
2. Diseño de moldes complejos
Los moldes de LSR son especializados, intrincados y complejos debido a la baja viscosidad del material y a la alta temperatura de curado. Por lo tanto, el diseño de estos moldes requiere experiencia y precisión, lo que puede aumentar los costos y los plazos de entrega.
3. Opciones de materiales limitadas
Si bien el LSR ofrece excelentes propiedades como flexibilidad, resistencia al calor y biocompatibilidad, sus opciones de materiales son algo limitadas en comparación con otros tipos de caucho. En consecuencia, esto puede restringir la gama de aplicaciones en las que el LSR se puede utilizar de manera eficaz.
4.Tiempo de curado
El tiempo de curado del LSR puede ser más largo en comparación con otros métodos de moldeo de caucho, lo que puede influir en el ciclo de producción y en el rendimiento total, en particular en la fabricación de grandes volúmenes.
Aplicaciones
Se trata de un proceso único que se utiliza en gran número de sectores en vista de sus novedosas propiedades y beneficios. Las principales aplicaciones son las siguientes:
1. Dispositivos médicos
Se utiliza de forma amplia y generalizada en la industria médica para fabricar distintos dispositivos y piezas como catéteres, tubos, sellos, juntas, mascarillas respiratorias y dispositivos implantables. Propiedades como la biocompatibilidad, la esterilizabilidad y la durabilidad lo hacen adecuado para aplicaciones que requieren precisión y calidad constante en condiciones clínicas.
2. Productos para el cuidado del bebé
Debido a su seguridad, adaptabilidad y facilidad de esterilización, el LSR se utiliza habitualmente en la fabricación de artículos para el cuidado de niños, como chupetes, areolas para biberones y utensilios para el cuidado de niños. Estos artículos suelen requerir materiales que tengan las propiedades de ser inocuos, hipoalergénicos e impermeables a altas temperaturas, todas las cuales proporciona el LSR.
3. Electrónica
También se utiliza en hardware para encapsular y proteger piezas sensibles de la humedad, el polvo y otras variables ambientales. Se utiliza en aplicaciones como teclados, sellos, juntas, conectores y cubiertas protectoras debido a sus increíbles propiedades de protección eléctrica, estabilidad térmica y protección contra compuestos químicos peligrosos.
4. Configuraciones automotrices
Se utiliza ampliamente en aplicaciones automotrices para suministrar piezas como sellos, juntas, conectores y amortiguadores de vibraciones. Su protección contra temperaturas extremas, aceites y sustancias sintéticas lo hace ideal para aplicaciones de motor y piezas externas donde la resistencia y la confiabilidad son de suma importancia.
5. Artículos de consumo
También se utiliza en otros artículos de consumo, como utensilios de cocina, utensilios para hornear, sellos, juntas y suministros para exteriores, debido a sus propiedades aptas para alimentos, su adaptabilidad y su protección contra altas temperaturas. Su capacidad para soportar ciclos repetidos de calentamiento y enfriamiento lo hace adecuado para artículos que requieren un uso y lavado continuos.
6. Aplicaciones industriales
También se utiliza en entornos modernos para la fabricación de sellos, juntas, anillos tóricos y diferentes piezas donde la protección contra temperaturas extremas, sustancias sintéticas y variables ecológicas es una gran necesidad. Su robustez, confiabilidad y rendimiento a largo plazo lo hacen ideal para aplicaciones modernas.
7.Aeroespacial
En el sector de la aviónica, el LSR se utiliza generalmente en la creación de sellos, juntas, conectores y otras piezas básicas donde se requieren materiales ligeros con un alto rendimiento de élite. Sus propiedades, como la protección contra altas temperaturas, la radiación y los compuestos sintéticos, lo hacen apropiado para aplicaciones de aviación donde la calidad y la seguridad inquebrantables son de suma importancia.
8. Iluminación LED
También se utiliza en luces LED para mejorar su exposición, solidez y vida útil. Sus propiedades, como la transparencia, la estabilidad térmica y la resistencia a la radiación UV, lo convierten en una buena opción de material para proteger las piezas LED de la humedad, el polvo y otros elementos ambientales.
9.Militar y defensa
Se utiliza en aplicaciones militares para producir sellos, juntas, conectores y diferentes piezas que requieren un rendimiento superior en circunstancias extremas. Los artículos fabricados con él ofrecen un rendimiento extraordinario en condiciones adversas como altas temperaturas, humedad y exposición a compuestos sintéticos y combustibles.
Conclusión
El proceso de moldeo por inyección El caucho de silicona en forma líquida se destaca como una técnica de élite para producir piezas de silicona con alta precisión. Se trata de un proceso de fabricación adaptable y potente que ofrece diferentes ventajas con respecto a los demás métodos. La flexibilidad de diseño, la alta precisión y la consistencia combinadas con las propiedades innatas del material lo hacen ideal para muchas aplicaciones en diferentes empresas. Gracias al avance de la innovación, este procedimiento sigue avanzando y mejorando, ofreciendo así un potencial mucho mayor de desarrollo y mejora de productos en numerosas áreas.