Moldes de plástico para hormigón Se fabrican a partir de diferentes tipos de plásticos en formas especialmente diseñadas. Estos moldes se utilizan para proporcionar las formas y los diseños requeridos de productos de hormigón. Los moldes de plástico para hormigón son reutilizables y también ofrecen flexibilidad para crear una amplia gama de productos fabricados a partir de hormigón. Estos productos de hormigón pueden ser tan simples como un bloque o pueden ser tan complicados como un elemento decorativo complejo. La introducción de varios moldes de plástico para hormigón ha supuesto una revolución en la forma en que se diseñan y dan forma a los artículos de hormigón.
En el sector industrial y aplicaciones DIY (Do It Yourself) molde de hormigón de plástico Proporciona una solución rentable y única. Los moldes de plástico para hormigón son mucho mejores que los moldes de metal tradicionales y los moldes de madera son más pesados y menos duraderos en comparación con los moldes de plástico para hormigón. Además, se ha demostrado que los moldes de plástico para hormigón producen con bastante facilidad las formas complejas e intrincadas deseadas, algo que no es tan fácil de lograr utilizando moldes metálicos o de madera.
Existe una amplia gama de aplicaciones de moldes de plástico para hormigón, que incluyen la construcción de elementos arquitectónicos, muebles de hormigón, creación de adornos decorativos para jardín y adoquines. Los moldes de plástico para hormigón son fáciles de usar y asequibles. Proporcionan resultados de primera calidad en la era moderna del diseño y la construcción.
Tipos de plástico Concreto Moldes con Resumen de Procesos de Fabricación, Principales Características y Utilizaciones Básicas
Existen muchos tipos de moldes de plástico para hormigón que se fabrican para aplicaciones específicas. Los factores básicos en los que se basan los diferentes tipos de moldes de plástico para hormigón son los siguientes:
- Tamaño del producto de hormigón
- Complejidad del producto concreto
- Diversos detalles del producto de hormigón.
A continuación se analizan los principales tipos de moldes de plástico para hormigón junto con sus características y usos.
-
Moldes de hormigón de plástico moldeado por inyección
Estos moldes se preparan y fabrican mediante un proceso de fabricación muy preciso y adecuadamente controlado que se denomina proceso de moldeo por inyección.
Resumen del proceso de fabricación de moldes de hormigón moldeados por inyección de plástico
El proceso comienza con la creación de un diseño detallado del molde de hormigón plástico requerido. Esto se logra utilizando un software CAD. A continuación, el modelo CAD producido se aplica para crear un molde metálico. Después, se preparan gránulos de plástico de los materiales plásticos seleccionados. En la máquina de moldeo por inyección, estos gránulos de plástico se calientan. El plástico fundido resultante se inyecta finalmente en la cavidad del molde metálico.
Esto se hace bajo alta presión. El plástico fundido se enfría en el molde metálico y se solidifica. A continuación, se lleva a cabo la expulsión de esta pieza de plástico moldeada del molde. A continuación, se adopta el proceso de recorte para eliminar cualquier exceso de material, como rebabas, y se realizan procesos de acabado para finalizar los moldes de plástico moldeados por inyección. Este proceso de fabricación es muy adecuado para la producción en masa. Los moldes producidos son de calidad constante.
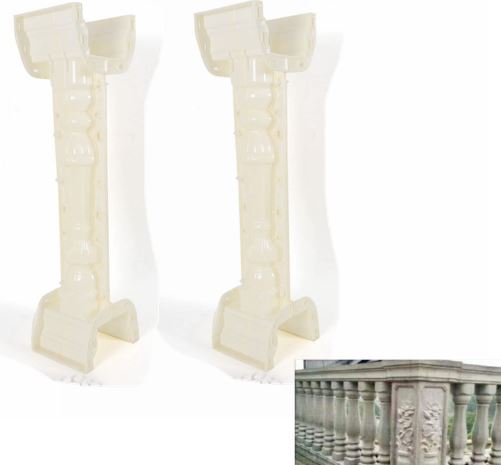
molde de hormigón de plástico
Características principales
A continuación se mencionan las principales características de estos moldes.
- Estos moldes tienen una alta precisión y tienen la capacidad de producir detalles finos y diseños complejos.
- Estos moldes tienen alta resistencia y durabilidad.
- Estos moldes proporcionan altas tasas de producción.
Utilización básica
El uso básico de los moldes de plástico moldeados por inyección incluye lo siguiente.
- Se utilizan para dar forma a numerosos artículos decorativos como adornos de jardín y estatuas.
- Se utilizan en la formación de elementos arquitectónicos intrincados, como cornisas y balaustres ornamentados.
- También se utilizan para dar forma a baldosas y adoquines con gran detalle.
-
Moldes de plástico formados al vacío
Estos moldes se fabrican calentando una lámina de plástico. Este calor se mantiene hasta que la lámina de plástico se vuelve maleable. Después de eso, se aplica succión al vacío para darle forma sobre un molde.
Breve descripción del proceso de fabricación de moldes de hormigón plástico formados al vacío
El proceso de fabricación de moldes de plástico formados al vacío para hormigón comienza igual que el de los moldes de plástico moldeados por inyección. En el paso inicial se lleva a cabo el diseño de la forma del molde mediante un software CAD. Después se crea un patrón o modelo maestro a partir de materiales como madera, espuma o resina. Estos materiales se seleccionan en función del diseño requerido. Después se corta el material de lámina de plástico seleccionado según el tamaño requerido. Esta lámina se coloca en una máquina de formado al vacío. Se calienta esta lámina hasta que se vuelve maleable.
A continuación, el patrón maestro se coloca en la mesa de moldeo de la máquina. La lámina de plástico calentada se baja sobre este patrón maestro. El plástico es succionado por una bomba de vacío contra el patrón, lo que crea la forma deseada. A continuación, el plástico endurecido y enfriado se retira de la máquina. El proceso de recorte posterior se utiliza para eliminar el exceso de material. El molde de plástico se separa del patrón maestro de forma cuidadosa. Los bordes del molde se alisan para garantizar una liberación limpia del hormigón cuando se utiliza en aplicaciones. Después de eso, el molde se somete a un control de calidad para detectar defectos como burbujas o un moldeado incompleto.
Si es necesario, se refuerza el molde de hormigón de plástico para que dure más. Se aplica un agente desmoldante o un revestimiento para facilitar el desmoldeo y se prueba el molde con un lote pequeño de hormigón para garantizar que funciona correctamente. Después de esto, los moldes se preparan para la producción, se almacenan adecuadamente para mantener su estado y se limpian con regularidad. Se realiza una inspección final para garantizar que los moldes estén listos para su uso en la producción de hormigón, lo que garantiza que tengan la forma correcta y sean duraderos.
Características principales
Estos moldes tienen las siguientes características y propiedades.
- Estos moldes proporcionan una solución rentable en comparación con los moldes de plástico moldeados por inyección porque son mucho menos costosos de producir.
- Estos moldes tienen la propiedad de flexibilidad, por lo que estos moldes se consideran ideales para la creación de formas y diseños grandes pero simples.
- En estos moldes se utilizan láminas de plástico, por lo que son fáciles de transportar y manipular.
Utilización básica
Los moldes de plástico formados al vacío encuentran su uso en los siguientes escenarios.
- Las baldosas y adoquines, que son mucho más grandes, se crean mediante moldes de plástico formados al vacío.
- Estos moldes se utilizan para dar forma a elementos de jardín y productos decorativos básicos.
- Los moldes de plástico formados al vacío también se utilizan para crear formas para proyectos de hormigón de bricolaje.
-
Moldes de plástico moldeados por rotación
Estos moldes se fabrican mediante el procedimiento de moldeo rotacional. En este método, un molde rotatorio se llena con resina plástica mientras que al mismo tiempo se calienta desde un molde hueco.
Breve descripción del proceso de fabricación de moldes de hormigón plástico
Creación de moldeado rotacional Moldeo de plástico para hormigón El proceso de fabricación implica un proceso detallado para garantizar una alta calidad y durabilidad. Comienza con el diseño del molde mediante un software CAD. Se fabrica un molde de metal hecho de aluminio o acero. El método de fabricación y el material se seleccionan en función del diseño deseado. A continuación, se calcula la resina plástica seleccionada, como el polietileno, y se carga en el molde. A continuación, el molde se sella muy herméticamente. Este molde se coloca en un horno donde se calienta y gira sobre dos ejes al mismo tiempo.
Esto permite que la resina fundida cubra uniformemente las superficies interiores. Después de eso, el molde se transfiere a una estación de enfriamiento. La rotación continúa hasta que el plástico se enfría y finalmente se solidifica. Una vez que se completa el enfriamiento y la solidificación, el molde se abre de manera cuidadosa. La pieza de plástico que se forma se retira. El exceso de material, si lo hubiera, se recorta y los bordes y la superficie se alisan para garantizar un desmoldeo limpio.
Se inspecciona el molde para detectar defectos como burbujas o un conformado incompleto y se puede reforzar para aumentar su durabilidad. Se aplica un agente desmoldante o un revestimiento para facilitar el desmoldeo y se prueba el molde con un lote pequeño de hormigón para garantizar su correcto funcionamiento. Por último, se prepara el molde para su uso repetido o para la producción en masa, y se realiza una limpieza y un mantenimiento periódicos para prolongar su vida útil y garantizar un rendimiento constante. Este proceso integral da como resultado moldes duraderos y con la forma precisa, listos para la creación eficiente de productos de hormigón.
Características principales
Estos moldes ofrecen las siguientes características y utilización.
- Estos moldes poseen un espesor de pared uniforme porque el material plástico se distribuye uniformemente durante el proceso de fabricación.
- Estos moldes son muy adecuados para dar forma a productos de alta resistencia debido a su durabilidad y resistencia.
- Los moldes de plástico moldeados por rotación tienen la capacidad de formar artículos grandes que no es posible formar con otros moldes.
Utilización básica
- Los moldes de plástico moldeados por rotación se utilizan para dar forma a grandes productos de muebles de hormigón, incluidas mesas y bancos.
- Estos moldes se utilizan para formar elementos estructurales como fuentes de agua y jardineras.
- Los moldes de plástico moldeados por rotación también se utilizan para dar forma a grandes elementos decorativos para el jardín.
4.Moldes de plástico impresos en 3D
Los moldes de plástico impresos en 3D se fabrican a partir de materiales termoplásticos construyendo un molde capa por capa a partir de un modelo digital.
Breve descripción del proceso de fabricación
El proceso de fabricación de piezas impresas en 3D moldes de plastico para hormigon El proceso se inicia de la misma manera que el de otros métodos de fabricación de moldes. En el primer paso se realiza el diseño del molde mediante un software CAD. Este paso se realiza porque proporciona ayuda para crear formas precisas y detalladas. Una vez finalizado el diseño, se convierte a un formato de archivo. Es importante tener en cuenta que este formato de archivo debe ser compatible con la impresión 3D. En general, se seleccionan los dos materiales siguientes para los moldes de plástico impresos en 3D.
- Ácido poliláctico
- Acrilonitrilo butadieno estireno
Estos materiales seleccionados se cargan luego en la impresora 3D, que construye el molde capa por capa basándose en el diseño digital. Después de la impresión, el molde se retira de la impresora con mucho cuidado. Después se realiza la limpieza de las estructuras de soporte y los materiales adicionales. Luego se inspecciona el molde para comprobar su precisión y se aplican los toques finales, como lijarlo o sellarlo, para alisar la superficie.
Se añade un agente desmoldante o revestimiento para facilitar la extracción del hormigón. Se prueba el molde con un lote pequeño de hormigón para garantizar que funciona correctamente y que el hormigón fragua como se espera. El molde está listo para utilizarse una vez que se confirma su eficacia haciendo los ajustes necesarios. Es pertinente mencionar que la limpieza y el mantenimiento periódicos de los moldes son muy importantes por las dos razones siguientes.
- Para mantener el molde en buen estado
- Para aumentar su vida útil
El método de impresión 3D de moldes de plástico permite la producción de moldes muy detallados y personalizados, lo que resulta muy adecuado para numerosas aplicaciones de hormigón.
Características principales
Los moldes de plástico impresos en 3D ofrecen las siguientes propiedades y usos.
- Los moldes de plástico impresos en 3D tienen la capacidad de producir diseños complejos y únicos porque estos moldes son altamente personalizables.
- Estos moldes permiten cambios rápidos y repetidos, por lo que son muy adecuados para dar forma a nuevos diseños.
- Los moldes de plástico impresos en 3D tienen la calidad de producir formas detalladas e intrincadas, por lo que estos moldes son los más adecuados para la producción a pequeña escala.
Utilización básica
- Los moldes de plástico impresos en 3D se utilizan para dar forma a artículos decorativos personalizados y versátiles.
- Estos moldes se utilizan para producir prototipos con el fin de probar nuevos diseños y características.
- Los elementos especializados de alto detalle que se aplican principalmente en arquitectura están formados por moldes de plástico impresos en 3D.
Beneficios de los moldes de plástico para hormigón
Los moldes de plástico para hormigón ofrecen muchas ventajas para el vaciado de hormigón, lo que los convierte en una opción popular en aplicaciones de construcción y decoración. Las principales ventajas de los moldes de plástico para hormigón son las siguientes:
- Rentable
Los moldes de plástico suelen ser más asequibles que los de metal, por lo que son una opción atractiva tanto para proyectos de pequeña como de gran escala.
- Ligero
Los moldes de plástico son mucho más ligeros que los de metal, por lo que son más fáciles de manipular, transportar y colocar. Esta capacidad, en última instancia, reduce el coste de mano de obra y simplifica el proceso de fundición.
- Flexibilidad y versatilidad
Los moldes de plástico para hormigón se pueden diseñar y fabricar en una amplia gama de formas y tamaños. Son muy adecuados para crear diseños complejos e intrincados que resultan difíciles o costosos con otros materiales.
- Facilidad de uso
Los moldes de plástico requieren menos mantenimiento que los moldes metálicos y son fáciles de usar. Pueden preformarse con detalles precisos, lo que reduce la necesidad de realizar trabajos de acabado adicionales en el hormigón.
- Durabilidad
Los moldes de plástico modernos para hormigón se fabrican con materiales de alta calidad. Estos materiales tienen las características de durabilidad y pueden reutilizarse muchas veces. Además, son resistentes a los impactos, al desgaste y a muchos productos químicos. Esto, en última instancia, ayuda a mantener su forma y funcionalidad a lo largo del tiempo.
- Resistencia a la corrosión
Esta es una ventaja mucho más significativa de los moldes de plástico en comparación con los moldes metálicos. Los moldes de plástico no se oxidan ni se corroen, por lo que esta propiedad es particularmente ventajosa en los siguientes casos.
- cuando se trabaja con mezclas de hormigón que puedan contener agentes corrosivos
- Cuando los moldes están expuestos a la humedad.
- Acabado de superficie lisa
Los moldes de plástico ofrecen un acabado superficial muy liso y bueno en el hormigón. Por consiguiente, reducen la necesidad de tratamientos superficiales o acabados adicionales. Esto, como resultado, mejora la calidad estética del producto terminado y proporciona una solución rentable.
- Producción rápida
Los moldes de plástico permiten una producción rápida, especialmente con métodos como el moldeado al vacío o la impresión 3D. Esta propiedad de los moldes de plástico resulta muy útil para proyectos con plazos ajustados.
- Reutilizable
Los moldes de plástico son una opción sostenible para el hormigón porque están diseñados para ser reutilizables. Si se les realiza un mantenimiento adecuado de forma regular, pueden prolongar su vida útil y reducir la necesidad de reemplazos constantes.
- Personalización
Para cumplir con requisitos de diseño específicos, los moldes de plástico se pueden personalizar fácilmente. Esta flexibilidad de personalización permite la producción de artículos de hormigón con formas versátiles o personalizadas.
- Propiedades antiadherentes
Es importante tener en cuenta que muchos moldes de plástico están tratados o recubiertos para que tengan propiedades antiadherentes. Posteriormente, esto evita que el hormigón se adhiera al molde. De esta manera, el desmoldeo se vuelve más fácil, lo que reduce el riesgo de dañar el producto terminado.
Factores básicos a tener en cuenta al utilizar plástico Concreto Moldes
La utilización de moldes de plástico para hormigón requiere que se tengan en cuenta varios factores clave para lograr los mejores resultados y la mayor longevidad de los moldes. Los detalles de estos factores son los siguientes.
- Elección del material
El tipo y clase de plástico utilizado en la fabricación de los moldes es de gran importancia. Es bien sabido que los distintos plásticos presentan diferentes propiedades. El polietileno de alta densidad ofrece una excelente durabilidad y resistencia al impacto en comparación con otros plásticos. Por lo tanto, seleccionar el plástico adecuado para las necesidades y los requisitos específicos ayudará a lograr los mejores resultados y a prolongar la vida útil del molde.
- Diseño de moldes
Es pertinente mencionar que la complejidad del diseño del molde afecta en última instancia al producto final. Por lo tanto, los moldes deben diseñarse con sumo cuidado para incluir características y aspectos como ángulos de desmoldeo y mecanismos de liberación para garantizar que los productos de concreto salgan sin problemas y que el molde permanezca intacto. Además, los diseños detallados pueden requerir precisión adicional tanto en la fabricación del molde como en los procedimientos de manipulación.
- Agentes desmoldantes
El factor más importante a tener en cuenta al utilizar moldes de plástico para hormigón es la aplicación del agente desmoldante adecuado. Estos agentes se utilizan para evitar que el hormigón se adhiera al molde. Los tipos de agentes desmoldantes que se utilizan habitualmente son los siguientes.
- Agentes desmoldantes a base de aceite
- Agentes desmoldantes a base de agua
- Agentes desmoldantes a base de silicona
- Agentes desmoldantes en polvo
- Agentes desmoldantes naturales y ecológicos
- Agentes desmoldantes de espuma
- Agentes desmoldantes de alta temperatura
Es importante tener en cuenta que la elección del desmoldante debe ser compatible con el material plástico del molde. Esto es necesario para mantener la calidad y la integridad del producto de hormigón.
- Temperatura y curado
Los moldes de plástico para hormigón pueden ser bastante sensibles a las variaciones de temperatura, por lo que es importante gestionar las condiciones de curado con cuidado. Esto es de gran importancia por los siguientes motivos:
- El calor excesivo puede deformar el molde.
- El calor insuficiente puede afectar el fraguado del hormigón.
Por lo tanto, el factor básico para garantizar que el molde sea aceptable es asegurarse de que la temperatura de curado sea adecuada tanto para el molde como para la mezcla de hormigón.
- Limpieza y mantenimiento
La limpieza y el mantenimiento de los moldes de plástico para hormigón son fundamentales. La razón básica es que el hormigón residual puede crear problemas para el uso futuro de los moldes. Por lo tanto, es importante realizar una limpieza y un mantenimiento periódicos con los métodos adecuados. Además, se deben realizar controles periódicos para comprobar el desgaste. Esto, en última instancia, ayudará a preservar la eficacia del molde.
- Impacto ambiental
Es importante tener en cuenta los efectos medioambientales de los moldes de plástico para hormigón. El material plástico seleccionado para el molde, si no es biodegradable ni reciclable, puede causar efectos adversos sobre el medio ambiente. Sin embargo, por el contrario, la selección de plásticos reciclables o biodegradables sin duda tendrá un impacto positivo sobre el medio ambiente. Además, la eliminación o el reciclaje adecuados de los moldes viejos también son de gran importancia para reducir el impacto medioambiental adverso y dañino.
Conclusión
Los moldes de plástico son una opción práctica y rentable para el vaciado de hormigón, ya que ofrecen flexibilidad y durabilidad. Los moldes de plástico para hormigón ofrecen soluciones eficaces para el vaciado de hormigón, lo que aporta valor a diseños complejos e intrincados. Facilitan la producción de diseños detallados y personalizados, a la vez que son ligeros y resistentes a la corrosión. Con un manejo y un mantenimiento adecuados, los moldes de plástico proporcionan un rendimiento fiable y resultados de alta calidad en diversas aplicaciones. Moldes de plástico tienen la capacidad de manejar una amplia gama de mezclas de hormigón y fundición Los moldes de plástico para hormigón se pueden utilizar en entornos de forma eficaz. El mantenimiento regular, la manipulación cuidadosa y el almacenamiento adecuado mejoran aún más la vida útil y el rendimiento de los moldes de hormigón de plástico. En general, son una herramienta excelente tanto para proyectos de hormigón decorativo como estructural.