Flüssigsilikonkautschukformung
Methode der Flüssiger Silikonkautschuk Formen
Wenn wir von Silikonkautschuk in flüssiger Form (LSR) sprechen, handelt es sich um ein Netzwerk, das in zwei Teile unterteilt ist. In diesem Netzwerk werden lange Ketten aus Polysiloxan mit Kieselsäure unterstützt. Teil A enthält einen Platinkatalysator und Teil B enthält Methylwasserstoffsiloxan als Vernetzer und einen Alkoholinhibitor. Silikonkautschuke sind Polymere aus mehreren Teilen und können Füllstoffe enthalten, um die Eigenschaften zu verbessern oder die Kosten zu senken. Silikonkautschuk ist größtenteils nicht reaktiv, stabil und unempfindlich gegenüber extremen Bedingungen und Temperaturen von −55 bis 300 °C (−70 bis 570 °F), während er gleichzeitig seine Eigenschaften beibehält.
Definition
Wenn wir Silikonkautschuk in flüssiger Form definieren, handelt es sich um ein Polymer anorganischer Natur, das aus Silizium (Si), Sauerstoff (O), Kohlenstoff (C) und Wasserstoff (H) besteht. Die lebenswichtige synthetische Kette, die als Rückgrat bezeichnet wird, besteht aus Silizium und Sauerstoff, genannt Siloxan. Dies ist ein hochreines, platingehärtetes Silikon mit brillanter Glätte. Es wird häufig in eine Silikonformhohlkammer eingegossen, um verschiedene Teile mit hoher Genauigkeit herzustellen. Im Allgemeinen hat flüssiger Silikonkautschuk einen geringen Druckverformungsrest, eine gute Stabilität und ist widerstandsfähig gegen extreme Hitze und Kälte. Dieses Material wird hauptsächlich zur Herstellung von Dichtungen, Dichtungsmembranen, elektrischen Steckverbindern, Mehrfachsteckern und Babyprodukten verwendet, bei denen glatte Oberflächen erforderlich sind.
Die anorganische Beschaffenheit von LSR macht es ideal für medizinische Anwendungen und Anwendungen mit Hautkontakt. LSR kann sich mit anderen chemischen Gruppen verbinden, wodurch es robuste Leistungen erzielt. LSR übertrifft viele andere Elastomere und wird in Drucktasten oder Tastaturen verwendet. Es wird bevorzugt für Pumpanwendungen eingesetzt, insbesondere bei Kontakt mit Körperflüssigkeiten oder chemischen Substanzen.
Spritzguss von Flüssigsilikonkautschuk
Dies ist ein hochmechanisierter Prozess. Flüssigsilikon-Spritzguss verwendet ein mechanisches Mischverfahren, bei dem eine zweikomponentige, platingehärtete LSR-Materialverbindung vermischt wird, die dann in eine Form fließt. Aufgrund der viskosen Beschaffenheit von LSR lässt es sich jedoch leicht verarbeiten und eignet sich perfekt für die Produktion großer Stückzahlen, gleichbleibende Teilequalität und verbesserte Produktivität. Das LSR-Spritzwerkzeug ist in einer LSR-spezifischen Spritzgusspresse untergebracht, die speziell für die präzise Kontrolle der Schussgröße entwickelt wurde und die gleichbleibende Produktion von Flüssigsilikonkautschukkomponenten ermöglicht. Aufgrund seiner Eigenschaften und Verarbeitbarkeit ist Flüssigsilikonkautschuk das ideale Material für komplizierte Designmerkmale und anspruchsvolle kritische Anwendungen geworden.
LSR-Spritzgussverfahren
Dieser Prozess ist von Natur aus duroplastisch und wird zur Herstellung flexibler, langlebiger und hitzebeständiger Silikonteile und -produkte verwendet. Bei diesem Verfahren werden zwei Verbindungen gemischt, die im Allgemeinen aus dem basisbildenden Silikon und dem Platinkatalysator bestehen. Danach wird die Mischung in eine Form gespritzt und wärmegehärtet, wodurch flexible Silikonteile entstehen. Diese beiden Verbindungen erfordern jedoch eine intensive, verteilende Mischung, während sie bei niedriger Temperatur gehalten werden, bevor sie in einen beheizten Hohlraum gepresst werden. Der flüssige Silikonkautschuk wird durch Hitze ausgehärtet, wodurch feste Teile oder Produkte entstehen.
Dieses Verfahren wird in vielen Branchen eingesetzt, darunter in der Automobil-, Medizin-, Konsumgüter- und Elektronikindustrie. Der LSR-Spritzgussprozess besteht im Wesentlichen aus den folgenden Hauptschritten.
1.Materialvorbereitung
LSR-Verbindungen: LSR ist eine Zweikomponentenverbindung, die typischerweise als basisbildendes Material und Katalysator bezeichnet wird und im Allgemeinen auf Platin basiert. Diese Teile werden im Verhältnis 1:1 gemischt und können zusätzliche Komponenten wie Pigmente oder Additive enthalten.
Lagerung und Handhabung: LSR-Komponenten werden in Behältern oder Kartuschen gelagert. Ein Behälter enthält das basisbildende Material und ein anderer Behälter den Katalysator, der normalerweise auf Platin basiert. Die ordnungsgemäße Handhabung ist äußerst wichtig, um Verunreinigungen zu vermeiden und gleichbleibende Materialeigenschaften sicherzustellen.
2. Mischen und Dosieren
Mischeinheit: Eine spezielle Mischeinheit kombiniert beide Verbindungen präzise. Diese Einheit kann bei Bedarf auch Pigmente oder andere Zusatzstoffe einarbeiten.
Statischer Mischer: Anschließend durchläuft das gemischte LSR einen statischen Mischer, der eine gründliche Homogenisierung der Komponenten gewährleistet. Dieser Schritt ist entscheidend, um die gleichmäßige Aushärtung und die Eigenschaften des Endprodukts sicherzustellen.
Messung: In diesem wichtigen Schritt wird das gemischte LSR in die Spritzeinheit dosiert. Eine präzise Dosierung ist unerlässlich, um konstante Schussgrößen beizubehalten und Materialabfall zu reduzieren.
3. Spritzgussmaschine
- Injektionseinheit: Die Spritzeinheit ist speziell für das Einspritzen von LSR ausgelegt. LSR hat eine niedrige Viskosität und erfordert spezielle Schneckenkonstruktionen. In diesem Schritt wird das Material in den Formhohlraum gedrückt.
- Klemmeinheit: In diesem Schritt wird die Form mit einer Klemme gehalten und während des Einspritzvorgangs geschlossen gehalten. Die erforderliche Kraft hängt jedoch von der Größe und Komplexität des Teils ab.
4. Formenbau
- Wesentliche Überlegungen: Formen für LSR müssen so beschaffen sein, dass sie den hohen Temperaturen und Spannungen standhalten, die während des Aushärtungsprozesses auftreten. Sie werden meist aus hochwertigem Stahl oder Aluminium hergestellt.
- Hohlraum und Kern: Die Silikon-Spritzgussform besteht aus Hohlräumen, die negative Teilformen sind, und Kernen, die positive Teilformen sind. Diese sollten präzise bearbeitet werden, um das ideale Teilaspekt und die ideale Oberflächenbearbeitung zu erreichen.
- Entlüftung: Die eingeschlossene Luft muss entweichen, um Defekte wie Luftblasen oder Hohlräume im Endprodukt zu vermeiden. Daher ist es wichtig, für eine ausreichende Entlüftung zu sorgen.
- Auswerfersystem: In diesem Schritt wird das Teil aus der ausgehärteten Form entfernt. Das Auswerfersystem muss sorgfältig ausgelegt sein, um die flexiblen und klebrigen LSR-Teile handhaben zu können.
5. Injektion und Aushärtung
- Injektionsprozess: Die Form wird fest geschlossen und mit der entsprechenden Kraft festgeklemmt. Anschließend wird das LSR mit hoher Geschwindigkeit in die Formhohlräume eingespritzt. Anschließend wird die Form gefüllt und überschüssiges Material entfernt.
- Aushärtungsprozess: Die Temperatur wird hoch gehalten (normalerweise zwischen 160 und 200 °C), um den Aushärtungsprozess zu starten. Die Aushärtungszeit hängt von der Dicke und Form des Teils ab. Sie beträgt in der Regel einige Sekunden bis mehrere Minuten.
6. Entformen
- Kühlung: Wenn die Aushärtung abgeschlossen ist, wird die Form abgekühlt, um mit dem Ausstoßen von Teilen zu arbeiten und Verformungen zu vermeiden.
- Öffnung: Anschließend wird die Form vorsichtig geöffnet, um eine Beschädigung der empfindlichen LSR-Teile zu verhindern.
- Auswurf: In diesem Schritt werden die Teile mithilfe des Auswerfersystems aus der Form ausgeworfen. Dabei ist ein vorsichtiger Umgang mit den Teilen erforderlich, da sie noch warm und möglicherweise leicht biegsam sind.
7. Nachbearbeitung
- Inspektion: In dieser Phase wird jedes Teil auf Defekte wie Grate, Luftblasen oder unvollständige Füllung geprüft. Es können sowohl automatisierte als auch manuelle Prüfmethoden verwendet werden.
- Beschneiden: Anschließend wird überschüssiges Material, auch Grat genannt, von den Teilen entfernt. Dies kann manuell oder mithilfe automatisierter Geräte erfolgen.
- Sekundäroperationen: Je nach Anwendung und Anforderung können zusätzliche Prozesse wie Kleben, Montage oder Oberflächenbehandlung durchgeführt werden.
8. Qualitätskontrolle
- Testen: Um sicherzustellen, dass gelieferte Teile die erforderlichen Spezifikationen erfüllen, werden sie verschiedenen Tests unterzogen. Diese Tests umfassen die Prüfung mechanischer Eigenschaften, Maßprüfungen und Sichtprüfungen.
- Dokumentation: Zur Rückverfolgbarkeit und Einhaltung der Industrienormen werden regelmäßig detaillierte Aufzeichnungen des Formprozesses, der Materialchargen und der Ergebnisse der Qualitätskontrolle geführt.
9. Verpackung und Versand
- Verpackung: Fertige Teile werden dann sorgfältig verpackt, um sie während des Transports zu schützen. Die Verpackungstechniken ändern sich je nach Größe, Form und Empfindlichkeit des Teils.
- Versand: Verpackte Teile werden dann an Kunden oder an die Weiterverarbeitungsanlagen versandt. Dadurch wird eine pünktliche Lieferung sichergestellt und die Teileintegrität gewahrt.
Vorteile des Spritzgusses von LSR
Dieses Verfahren bietet einige wesentliche Vorteile:
1. Präzision und Konsistenz
LSR-Spritzguss bietet hohe konsistente und präzise Werte bei der Herstellung komplizierter, komplexer und detaillierter Teile. Dieses Verfahren ermöglicht enge Toleranzen und eine genaue Replikation von Formen und gewährleistet so Einheitlichkeit über alle Chargen hinweg.
2. Großes Anwendungsspektrum
Dies bietet zahlreiche Anwendungsmöglichkeiten, da es flexibel ist und in verschiedenen Branchen eingesetzt werden kann, darunter Automobil, Medizin, Hardware, Konsumgüter und vieles mehr. Die Flexibilität, die LSR bietet, macht es für die Herstellung von allem geeignet, von medizinischen Implantaten über Autodichtungen bis hin zu Komponenten für Unterhaltungselektronik.
3. Haltbarkeit und Stärke
Diese Teile zeichnen sich durch ihre Robustheit und Festigkeit aus. Sie können extremen Temperaturen, aggressiven synthetischen Verbindungen und längerer UV-Bestrahlung standhalten, ohne dass ihre wesentlichen Eigenschaften über einen langen Zeitraum beeinträchtigt werden, was sie für viele Anwendungen ideal macht.
4.Biokompatibilität
Diese Materialien sind biokompatibel und erfüllen die Anforderungen medizinischer Standards. Diese Qualität macht sie für klinische und medizinische Anwendungen wie Implantate, chirurgische Instrumente und tragbare klinische Geräte geeignet. Darüber hinaus sind sie hypoallergen und für längeren Hautkontakt unbedenklich.
5.Chemische Beständigkeit
Diese Materialien bieten einen hervorragenden Schutz gegen viele synthetische Stoffe, darunter Lösungsmittel, Öle und Reinigungsmittel. Dank dieser Eigenschaft eignen sie sich für den Einsatz unter Bedingungen, in denen der Kontakt mit chemischen Substanzen normal ist, wie etwa in der Automobilindustrie und modernen Industrieumgebungen.
6. Flexibilität und Elastizität
Diese Teile sind bemerkenswert elastisch und flexibel, sodass sie verformt werden können und ihre ursprüngliche Form ohne dauerhafte Verformung wiederherstellen. Diese Anpassungsfähigkeit macht sie ideal für Dichtungs- und Dichtungsanwendungen, bei denen eine dichte, solide Abdichtung erforderlich ist.
7. Schnelle Zykluszeiten
Dieses Verfahren bietet im Vergleich zu herkömmlichen Gummiformverfahren eine schnelle Prozesszeit. Dies ermöglicht eine hohe Produktion mit schnellen Durchlaufzeiten und ist gleichzeitig kostengünstig.
8.Reduzierte Abfallmenge
Beim LSR-Spritzgießen entsteht im Vergleich zu anderen Herstellungsverfahren nur minimaler Abfall. Durch die Möglichkeit, den Materialfluss präzise zu steuern und die Formkonstruktionen zu optimieren, wird der Materialabfall minimiert. Dies führt folglich zu Kosteneinsparungen und Umweltvorteilen.
9. Gestaltungsfreiheit
Dieser Prozess ermöglicht die Entwicklung komplizierter Formen und komplexer Geometrien, die mit anderen Fertigungsmethoden möglicherweise nur schwer zu erreichen wären. Diese Möglichkeit der Gestaltungsfreiheit ermöglicht fantasievolle Produktdesigns und Anpassungsoptionen.
10.Oberflächenbeschaffenheit
Diese Teile haben direkt aus der Form eine glatte und makellose Oberfläche. Folglich ist kein Nachbearbeitungsaufwand wie Reinigen oder Lackieren mehr erforderlich. Dies spart Zeit und Arbeitskosten und macht den Prozess kostengünstig, während gleichzeitig ein qualitativ hochwertiges Endprodukt gewährleistet wird.
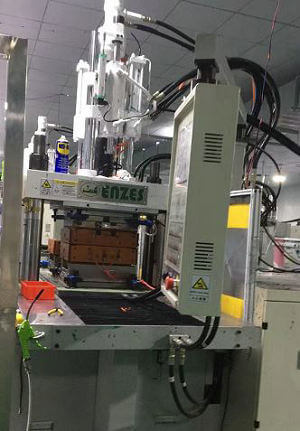
Silikon-Spritzgussmaschinen
Einschränkungen beim Formen von Flüssigsilikonkautschuk
Dieses Verfahren bietet verschiedene Vorteile, unterliegt jedoch wie jedes Herstellungsverfahren einigen Einschränkungen:
1.Hohe Anfangsinvestition
Für die Einrichtung eines LSR-Spritzgussverfahrens sind erhebliche Anfangsinvestitionen erforderlich, vor allem in Spezialausrüstung, Formen und Infrastruktur. Daher kann dies für Kleinhersteller oder solche mit begrenztem Kapital ein Hindernis darstellen.
2.Komplexes Formendesign
Aufgrund der niedrigen Viskosität und der hohen Aushärtungstemperatur des Materials sind LSR-Formen spezialisiert, kompliziert und komplex. Die Konstruktion dieser Formen erfordert daher Fachwissen und Präzision, was zu höheren Kosten und längeren Vorlaufzeiten führen kann.
3. Begrenzte Materialoptionen
Obwohl LSR hervorragende Eigenschaften wie Flexibilität, Hitzebeständigkeit und Biokompatibilität bietet, sind die Materialoptionen im Vergleich zu anderen Gummiarten etwas eingeschränkt. Folglich kann dies den Anwendungsbereich einschränken, in dem LSR effektiv eingesetzt werden kann.
4. Aushärtezeit
Die Aushärtezeit für LSR kann im Vergleich zu anderen Gummiformverfahren länger sein. Dies kann den Produktionszyklus und den gesamten Durchsatz beeinflussen, insbesondere bei der Fertigung großer Stückzahlen.
Anwendungen
Dies ist ein einzigartiger Prozess, der aufgrund seiner neuartigen Eigenschaften und Vorteile in zahlreichen Branchen Anwendung findet. Die wichtigsten Anwendungen sind wie folgt:
1.Medizinprodukte
Es wird in der medizinischen Industrie weithin und häufig zur Herstellung verschiedener Geräte und Komponenten wie Katheter, Schläuche, Dichtungen, Dichtungsringe, Atemmasken und implantierbare Geräte verwendet. Eigenschaften wie Biokompatibilität, Sterilisierbarkeit und Robustheit machen es für Anwendungen geeignet, die Genauigkeit und Zuverlässigkeit unter klinischen Bedingungen erfordern.
2.Babypflegeprodukte
Aufgrund seiner Sicherheit, Flexibilität und einfachen Sterilisation wird LSR häufig bei der Herstellung von Babyartikeln wie Schnullern, Flaschenhaltern und Babypflegeutensilien verwendet. Diese Artikel erfordern häufig Materialien, die unschädlich, hypoallergen und hitzebeständig sein müssen. All diese Eigenschaften bietet LSR.
3.Elektronik
Dies wird zusätzlich in der Hardware verwendet, um empfindliche Teile einzukapseln und vor Feuchtigkeit, Staub und anderen Umweltvariablen zu schützen. Es wird in Anwendungen wie Tastaturen, Dichtungen, Dichtungsringen, Steckverbindern und Schutzabdeckungen aufgrund seiner erstaunlichen elektrischen Schutzeigenschaften, thermischen Stabilität und des Schutzes vor gefährlichen chemischen Verbindungen verwendet.
4.Automotive-Setups
Es wird häufig in Automobilanwendungen zur Herstellung von Teilen wie Dichtungen, Dichtungsringen, Verbindungsstücken und Schwingungsdämpfern verwendet. Seine Beständigkeit gegen extreme Temperaturen, Öle und synthetische Substanzen macht es ideal für Motoranwendungen und Außenteile, bei denen Robustheit und Zuverlässigkeit von größter Bedeutung sind.
5.Konsumgüter
Aufgrund seiner Lebensmittelechtheit, Flexibilität und Beständigkeit gegen hohe Temperaturen wird es auch in anderen Konsumgütern wie Kochgeschirr, Backgeschirr, Dichtungen und Outdoor-Zubehör verwendet. Da es wiederholte Erwärmungs- und Abkühlungszyklen übersteht, ist es für Produkte geeignet, die ständig verwendet und gewaschen werden müssen.
6.Industrielle Anwendungen
Es wird auch in modernen Umgebungen zur Herstellung von Dichtungen, Dichtungsringen, O-Ringen und anderen Teilen eingesetzt, bei denen Schutz vor extremen Temperaturen, Kunststoffen und Umweltvariablen eine große Notwendigkeit darstellt. Seine Robustheit, Zuverlässigkeit und langfristige Leistung machen es ideal für moderne Anwendungen.
7.Luft- und Raumfahrt
In der Avionikbranche wird LSR im Allgemeinen zur Herstellung von Dichtungen, Dichtungsringen, Verbindungsstücken und anderen Basisteilen verwendet, für die leichte Materialien mit höchster Leistungsfähigkeit erforderlich sind. Seine Eigenschaften wie Schutz vor hohen Temperaturen, Strahlung und synthetischen Verbindungen machen es für Luftfahrtanwendungen geeignet, bei denen unerschütterliche Qualität und Sicherheit von größter Bedeutung sind.
8.LED-Beleuchtung
Es wird auch in LED-Leuchten verwendet, um deren Leistung, Robustheit und Lebensdauer zu verbessern. Eigenschaften wie Transparenz, Wärmestabilität und UV-Beständigkeit machen es zu einer guten Materialwahl zum Schutz von LED-Komponenten vor Feuchtigkeit, Staub und anderen Umwelteinflüssen.
9.Militär und Verteidigung
Dies wird in militärischen Anwendungen zur Herstellung von Dichtungen, Dichtungsringen, Verbindungsstücken und anderen Teilen genutzt, die unter extremen Bedingungen eine herausragende Leistung erfordern. Die damit hergestellten Produkte bieten außergewöhnliche Leistung unter rauen Bedingungen wie hohen Temperaturen, Feuchtigkeit und Kontakt mit Chemikalien und Kraftstoffen.
Schlussfolgerung
Der Prozess der Spritzgießen aus Silikonkautschuk in flüssiger Form ist eine hervorragende Technik zur Herstellung von Silikonteilen mit hoher Genauigkeit. Dies ist ein anpassungsfähiger und leistungsstarker Herstellungsprozess, der gegenüber anderen Methoden verschiedene Vorteile bietet. Die Designflexibilität, hohe Genauigkeit und Konsistenz in Kombination mit den inhärenten Eigenschaften des Materials machen es ideal für viele Anwendungen in verschiedenen Branchen. Durch den Fortschritt der Innovation wird auch dieses Verfahren ständig weiterentwickelt und verbessert und bietet somit in zahlreichen Bereichen ein viel größeres Potenzial für Weiterentwicklung und Produktverbesserung.