Kunststoffformen für Beton werden aus verschiedenen Kunststoffarten in speziell entwickelten Formen hergestellt. Diese Formen werden verwendet, um Betonprodukten die erforderlichen Formen und Designs zu verleihen. Kunststoffformen für Beton sind wiederverwendbar und bieten außerdem die Flexibilität, eine sehr große Produktpalette aus Beton herzustellen. Diese Betonprodukte können so einfach wie ein Block oder so kompliziert wie komplexe Dekorationsgegenstände sein. Die Einführung verschiedener Kunststoffformen für Beton hat die Art und Weise revolutioniert, wie Betongegenstände entworfen und geformt werden.
Im industriellen Bereich und bei Heimwerkeranwendungen Kunststoff-Betonform bietet eine kostengünstige und zugleich einzigartige Lösung. Kunststoffformen für Beton sind viel besser als die traditionellen Metallformen, und Holzformen sind schwerer und weniger haltbar als Kunststoffformen für Beton. Darüber hinaus haben sich Kunststoffformen für Beton als recht einfach erwiesen, um die gewünschten komplexen und komplizierten Formen herzustellen, was mit Metall- oder Holzformen nicht so einfach zu erreichen ist.
Es gibt ein breites Anwendungsspektrum für Kunststoffformen für Beton, darunter den Bau von Architekturelementen, Betonmöbeln, die Herstellung dekorativer Gartenornamente und Pflastersteine. Kunststoffformen für Beton sind einfach zu verwenden und erschwinglich. Sie liefern erstklassige Qualitätsergebnisse im modernen Zeitalter von Design und Konstruktion.
Kunststoffarten Beton Formen mit kurzer Beschreibung der Herstellungsverfahren, Hauptmerkmale und grundlegenden Verwendungszwecke
Es gibt viele Arten von Kunststoffbetonformen, die für bestimmte Anwendungen hergestellt werden. Die grundlegenden Faktoren, auf denen verschiedene Arten von Kunststoffformen für Beton basieren, sind folgende.
- Größe des Betonproduktes
- Komplexität des Betonproduktes
- Verschiedene Details des Betonproduktes
Im Folgenden werden die wichtigsten Arten von Kunststoffformen für Beton sowie ihre Eigenschaften und Verwendung erläutert.
Spritzgegossene Betonformen aus Kunststoff
Diese Formen werden in einem sehr präzisen und sorgfältig kontrollierten Herstellungsverfahren vorbereitet und hergestellt, das als Spritzgussverfahren bezeichnet wird.
Kurzbeschreibung des Herstellungsprozesses für spritzgegossene Kunststoff-Betonformen
Der Prozess beginnt mit der Erstellung eines detaillierten Entwurfs der erforderlichen Kunststoffbetonform. Dies wird mithilfe einer CAD-Software erreicht. Das erstellte CAD-Modell wird dann zur Erstellung einer Metallform verwendet. Danach werden Kunststoffpellets aus ausgewählten Kunststoffmaterialien hergestellt. In der Spritzgussmaschine werden diese Kunststoffpellets erhitzt. Der resultierende geschmolzene Kunststoff wird schließlich in den Hohlraum der Metallform gespritzt.
Dies geschieht unter hohem Druck. Der geschmolzene Kunststoff kühlt in der Metallform ab und verfestigt sich. Anschließend wird dieses geformte Kunststoffstück aus der Form ausgeworfen. Anschließend wird der Trimmvorgang durchgeführt, um überschüssiges Material wie Grate zu entfernen, und es werden Endbearbeitungsprozesse durchgeführt, um die Spritzgussformen aus Kunststoff fertigzustellen. Dieses Herstellungsverfahren eignet sich sehr gut für die Massenproduktion. Die hergestellten Formen sind von gleichbleibender Qualität.
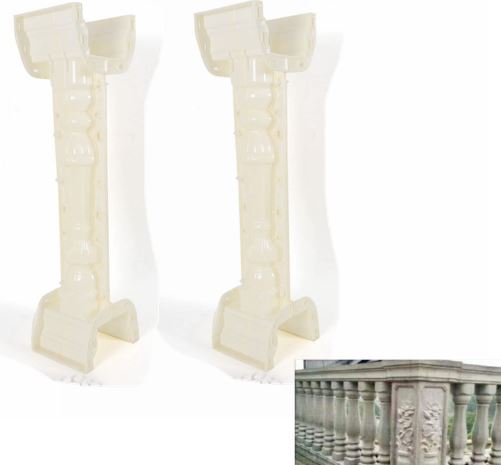
Kunststoff-Betonform
Hauptmerkmale
Die wichtigsten Eigenschaften dieser Formen sind unten aufgeführt.
- Diese Formen sind hochpräzise und können feine Details und komplexe Designs erzeugen.
- Diese Formen weisen eine hohe Festigkeit und Haltbarkeit auf
- Diese Formen bieten hohe Produktionsraten
Grundlegende Nutzung
Zu den grundlegenden Verwendungszwecken von Spritzgussformen für Kunststoffe gehört Folgendes.
- Sie werden zur Herstellung zahlreicher Dekorationsartikel wie Gartenornamente und Statuen verwendet.
- Sie finden ihre Verwendung in der Bildung von komplizierten architektonischen Elementen wie verzierten Gesimsen und Balustern
- Sie werden auch zur Gestaltung von hochdetaillierten Fliesen und Pflastersteinen verwendet.
Vakuumgeformte Kunststoffformen
Diese Formen werden durch Erhitzen einer Kunststofffolie hergestellt. Diese Hitze wird aufrechterhalten, bis die Kunststofffolie biegsam wird. Danach wird Vakuum angelegt, um sie über einer Form zu formen.
Kurzbeschreibung des Herstellungsprozesses für vakuumgeformte Kunststoffbetonformen
Der Prozess der Herstellung von vakuumgeformten Kunststoffformen für Beton beginnt wie bei Spritzgussformen aus Kunststoff. Im ersten Schritt wird die Form mithilfe einer CAD-Software entworfen. Danach wird ein Mastermuster oder Modell aus Materialien wie Holz, Schaumstoff oder Harz erstellt. Diese Materialien werden basierend auf dem erforderlichen Design ausgewählt. Danach wird das ausgewählte Kunststoffplattenmaterial auf die erforderliche Größe zugeschnitten. Diese Platte wird in eine Vakuumformmaschine gelegt. Diese Platte wird erhitzt, bis sie biegsam wird.
Anschließend wird das Urmodell auf dem Formtisch der Maschine positioniert. Die erhitzte Kunststoffplatte wird auf dieses Urmodell abgesenkt. Der Kunststoff wird von einer Vakuumpumpe gegen das Modell gesaugt, wodurch die gewünschte Form entsteht. Der ausgehärtete und abgekühlte Kunststoff wird dann aus der Maschine entfernt. Der anschließende Trimmvorgang dient zum Entfernen überschüssigen Materials. Die Kunststoffform wird vorsichtig vom Urmodell getrennt. Die Kanten der Form werden geglättet, um eine saubere Entformung des Betons bei der Verwendung zu gewährleisten. Anschließend wird die Form einer Qualitätskontrolle auf Mängel wie Blasen oder unvollständige Formgebung unterzogen.
Bei Bedarf wird die Kunststoffbetonform verstärkt, um die Haltbarkeit zu erhöhen. Ein Trennmittel oder eine Beschichtung wird aufgetragen, um das Entformen zu erleichtern, und die Form wird mit einer kleinen Menge Beton getestet, um sicherzustellen, dass sie richtig funktioniert. Danach werden die Formen für die Produktion vorbereitet, ordnungsgemäß gelagert, um ihren Zustand zu erhalten, und regelmäßig gereinigt. Eine Endkontrolle wird durchgeführt, um sicherzustellen, dass die Formen für die Betonproduktion bereit sind und dass sie präzise geformt und haltbar sind.
Hauptmerkmale
Diese Formen weisen die folgenden Merkmale und Eigenschaften auf.
- Diese Formen bieten eine kostengünstige Lösung im Vergleich zu Spritzgussformen aus Kunststoff, da ihre Herstellung viel weniger kostet
- Diese Formen tragen die Eigenschaft der Flexibilität, daher gelten diese Formen als ideal für die Erstellung großer, aber einfacher Formen und Designs
- In diesen Formen werden Kunststoffplatten verwendet, so dass diese Formen leicht zu transportieren und zu handhaben sind
Grundlegende Nutzung
Vakuumgeformte Kunststoffformen finden in folgenden Szenarien Verwendung.
- Die Fliesen und Pflastersteine, die viel größer sind, werden durch vakuumgeformte Kunststoffformen hergestellt
- Diese Formen werden für die Gestaltung von Gartenelementen und grundlegenden dekorativen Produkten verwendet
- Vakuumgeformte Kunststoffformen werden auch verwendet, um Formen für DIY-Betonprojekte zu erstellen
Rotationsgeformte Kunststoffformen
Diese Formen werden im Rotationsgussverfahren hergestellt. Bei diesem Verfahren wird eine rotierende Form mit Kunststoffharz gefüllt und gleichzeitig erhitzt, wodurch eine Hohlform entsteht.
Kurzbeschreibung des Herstellungsprozesses von Kunststoffbetonformen
Erstellen von Rotationsformteilen Kunststoffformteil für Beton beinhaltet einen detaillierten Prozess, um hohe Qualität und Haltbarkeit zu gewährleisten. Es beginnt mit dem Entwurf der Form mithilfe einer CAD-Software. Eine Metallform aus Aluminium oder Stahl wird hergestellt. Fertigungsmethode und Material werden auf Grundlage des gewünschten Designs ausgewählt. Dann wird das ausgewählte Kunststoffharz wie Polyethylen berechnet und in die Form geladen. Die Form wird dann sehr dicht verschlossen. Diese Form wird in einen Ofen gelegt, wo sie erhitzt und gleichzeitig um zwei Achsen gedreht wird.
Dadurch kann das geschmolzene Harz die Innenflächen gleichmäßig bedecken. Anschließend wird die Form in eine Kühlstation überführt. Die Rotation wird fortgesetzt, bis der Kunststoff abgekühlt und schließlich erstarrt ist. Nachdem das Abkühlen und Erstarren abgeschlossen ist, wird die Form vorsichtig geöffnet. Das geformte Kunststoffteil wird entfernt. Eventuell vorhandenes überschüssiges Material wird abgeschnitten und die Kanten und die Oberfläche werden geglättet, um ein sauberes Lösen zu gewährleisten.
Die Form wird auf Mängel wie Blasen oder unvollständige Formgebung untersucht und kann verstärkt werden, um die Haltbarkeit zu verbessern. Ein Trennmittel oder eine Beschichtung wird aufgetragen, um das Entformen zu erleichtern, und die Form wird mit einer kleinen Menge Beton getestet, um sicherzustellen, dass sie ordnungsgemäß funktioniert. Schließlich wird die Form für den wiederholten Gebrauch oder die Massenproduktion vorbereitet. Regelmäßige Reinigung und Wartung werden durchgeführt, um ihre Lebensdauer zu verlängern und eine gleichbleibende Leistung sicherzustellen. Dieser umfassende Prozess führt zu langlebigen, präzise geformten Formen, die für die effiziente Herstellung von Betonprodukten bereit sind.
Hauptmerkmale
Diese Formen bieten folgende Eigenschaften und Verwendungsmöglichkeiten.
- Diese Formen besitzen eine gleichmäßige Wandstärke, da das Kunststoffmaterial während des Herstellungsprozesses gleichmäßig verteilt wird
- Diese Formen eignen sich aufgrund ihrer Haltbarkeit und Festigkeit sehr gut zum Formen von Hochleistungsprodukten.
- Rotationsgeformte Kunststoffformen haben die Fähigkeit, große Gegenstände zu formen, die mit anderen Formen nicht geformt werden können.
Grundlegende Nutzung
- Rotationsgeformte Kunststoffformen werden verwendet, um große Möbelstücke aus Beton, darunter Tische und Bänke, zu formen.
- Diese Formen werden verwendet, um Strukturelemente wie Wasserspiele und Pflanzgefäße zu formen
- Rotationsgeformte Kunststoffformen werden auch verwendet, um große dekorative Gartenartikel zu formen
4.3D-gedruckte Kunststoffformen
3D-gedruckte Kunststoffformen werden aus thermoplastischen Materialien hergestellt, indem aus einem digitalen Modell schichtweise eine Form aufgebaut wird.
Kurze Beschreibung des Herstellungsprozesses
Der Prozess der Herstellung von 3D-Druck Kunststoffbetonformen wird auf die gleiche Weise begonnen wie bei anderen Formenbauverfahren. Im ersten Schritt wird die Form mithilfe einer CAD-Software entworfen. Dieser Schritt wird durchgeführt, weil er dabei hilft, präzise und detaillierte Formen zu erstellen. Nach Abschluss des Entwurfs wird dieser in ein Dateiformat konvertiert. Es ist wichtig zu beachten, dass dieses Dateiformat mit dem 3D-Druck kompatibel sein muss. Im Allgemeinen werden für 3D-gedruckte Kunststoffformen die folgenden zwei Materialien ausgewählt.
- Polymilchsäure
- Acrylnitril-Butadien-Styrol
Diese ausgewählten Materialien werden dann in den 3D-Drucker geladen. Der Drucker baut dann die Form Schicht für Schicht auf, die auf dem digitalen Design basiert. Nach dem Drucken wird die Form sehr vorsichtig aus dem Drucker entfernt. Danach werden Stützstrukturen und zusätzliche Materialien gereinigt. Die Form wird dann auf Genauigkeit überprüft und der letzte Schliff wie Schleifen oder Versiegeln wird angewendet, um die Oberfläche zu glätten.
Um das Entfernen des Betons zu erleichtern, wird ein Trennmittel oder eine Beschichtung hinzugefügt. Die Form wird mit einer kleinen Menge Beton getestet, um sicherzustellen, dass sie richtig funktioniert und der Beton wie erwartet aushärtet. Die Form ist einsatzbereit, sobald ihre Wirksamkeit durch die Vornahme aller erforderlichen Anpassungen bestätigt wurde. Es ist wichtig zu erwähnen, dass die regelmäßige Reinigung und Wartung der Formen aus den folgenden zwei Gründen sehr wichtig ist.
- Um die Form in gutem Zustand zu halten
- Um die Lebensdauer zu verlängern
Das Verfahren des 3D-Drucks von Kunststoffformen ermöglicht die Herstellung hochdetaillierter und individueller Gussformen. Dieses eignet sich sehr gut für zahlreiche konkrete Anwendungsgebiete.
Hauptmerkmale
3D-gedruckte Kunststoffformen bieten folgende Eigenschaften und Verwendungsmöglichkeiten.
- Mit 3D-gedruckten Kunststoffformen können komplexe und einzigartige Designs hergestellt werden, da diese Formen in hohem Maße anpassbar sind
- Diese Formen ermöglichen schnelle und wiederholte Änderungen, daher sind diese Formen sehr gut für die Gestaltung neuer Designs geeignet
- 3D-gedruckte Kunststoffformen haben die Qualität, detaillierte und komplizierte Formen zu produzieren, daher sind diese Formen am besten für die Produktion in kleinem Maßstab geeignet
Grundlegende Nutzung
- 3D-gedruckte Kunststoffformen werden verwendet, um individuelle und vielseitige Dekorationsartikel zu gestalten
- Diese Formen werden zur Herstellung von Prototypen verwendet, um neue Designs und Funktionen zu testen.
- Die hochdetaillierten Spezialelemente, die vor allem in der Architektur eingesetzt werden, werden durch 3D-gedruckte Kunststoffformen hergestellt.
Vorteile von Kunststoffformen für Beton
Kunststoffformen für Beton bieten viele Vorteile für den Betonguss, was sie zu einer beliebten Wahl in Bau- und Dekorationsanwendungen macht. Die wichtigsten Vorteile von Kunststoffformen für Beton sind die folgenden.
- Kostengünstig
Kunststoffformen sind im Allgemeinen günstiger als Metallformen. Daher sind sie sowohl für kleine als auch für große Projekte eine attraktive Wahl.
- Leicht
Kunststoffformen sind viel leichter als Metallformen. Daher sind diese Formen einfacher zu handhaben, zu transportieren und zu positionieren. Dies führt letztendlich zu geringeren Arbeitskosten und vereinfacht den Gussprozess.
- Flexibilität und Vielseitigkeit
Kunststoffformen für Beton können in einer Vielzahl von Formen und Größen entworfen und hergestellt werden. Sie eignen sich sehr gut für die Erstellung komplexer und komplizierter Designs, die mit anderen Materialien schwierig oder kostspielig sind.
- Benutzerfreundlichkeit
Kunststoffformen erfordern im Vergleich zu Metallformen weniger Wartung und sind einfach zu verwenden. Sie können mit präzisen Details vorgeformt werden, wodurch der Bedarf an zusätzlichen Nacharbeiten am Beton reduziert wird.
- Haltbarkeit
Moderne Kunststoffformen für Beton werden aus hochwertigen Materialien hergestellt. Diese Materialien sind langlebig und können viele Male wiederverwendet werden. Darüber hinaus sind sie stoß- und verschleißfest sowie beständig gegen viele Chemikalien. Dies trägt letztendlich dazu bei, dass ihre Form und Funktionalität im Laufe der Zeit erhalten bleibt.
- Korrosionsbeständigkeit
Dies ist ein wesentlicher Vorteil von Kunststoffformen gegenüber Metallformen. Kunststoffformen rosten oder korrodieren nicht, daher ist diese Eigenschaft in folgenden Szenarien besonders vorteilhaft.
- beim Arbeiten mit Betonmischungen, die korrosive Stoffe enthalten können
- wenn die Formen Feuchtigkeit ausgesetzt sind
- Glatte Oberflächenbeschaffenheit
Kunststoffformen bieten eine sehr glatte und gute Oberflächenbeschaffenheit auf dem Beton. Folglich ist weniger zusätzliche Oberflächenbehandlung oder -veredelung erforderlich. Dies verbessert die ästhetische Qualität des fertigen Produkts und bietet eine kostengünstige Lösung.
- Schnelle Produktion
Kunststoffformen ermöglichen schnelle Produktionsraten, insbesondere mit Methoden wie Vakuumformen oder 3D-Druck. Diese Eigenschaft von Kunststoffformen ist bei Projekten mit knappen Fristen praktisch.
- Wiederverwendbar
Kunststoffformen sind eine nachhaltige Option für Beton, da sie wiederverwendbar sind. Wenn sie regelmäßig und ordnungsgemäß gewartet werden, kann ihre Lebensdauer verlängert werden und der Bedarf an ständigem Austausch verringert werden.
- Anpassung
Um speziellen Designanforderungen gerecht zu werden, können Kunststoffformen leicht angepasst werden. Diese Anpassungsflexibilität ermöglicht die Herstellung vielseitiger oder individuell geformter Betongegenstände.
- Antihaft-Eigenschaften
Es ist wichtig zu beachten, dass viele Kunststoffformen behandelt oder beschichtet sind, um eine Antihaftwirkung zu erzielen. Dies verhindert, dass der Beton an der Form haftet. Dadurch wird das Entformen erleichtert und das Risiko einer Beschädigung des fertigen Produkts verringert.
Grundlegende Faktoren, die bei der Verwendung von Kunststoff zu berücksichtigen sind Beton Formen
Bei der Verwendung von Kunststoffformteilen für Beton müssen mehrere Schlüsselfaktoren berücksichtigt werden, um optimale Ergebnisse und eine lange Lebensdauer der Formen zu erzielen. Im Folgenden werden diese Faktoren im Einzelnen beschrieben.
- Materialauswahl
Die Art und der Kunststoff, der bei der Herstellung der Formen verwendet wird, sind von großer Bedeutung. Es ist bekannt, dass verschiedene Kunststoffe unterschiedliche Eigenschaften aufweisen. Polyethylen hoher Dichte bietet im Vergleich zu anderen Kunststoffen eine hervorragende Haltbarkeit und Schlagfestigkeit. Die Auswahl des richtigen Kunststoffs für spezifische Bedürfnisse und Anforderungen trägt daher dazu bei, die besten Ergebnisse zu erzielen und die Lebensdauer der Form zu verlängern.
- Formenbau
Es ist wichtig zu erwähnen, dass die Komplexität des Formendesigns letztendlich das Endprodukt beeinflusst. Daher müssen Formen mit großer Sorgfalt entworfen werden, um Merkmale und Aspekte wie Entformungsschrägen und Freigabemechanismen zu berücksichtigen, damit Betonprodukte reibungslos herauskommen und die Form intakt bleibt. Darüber hinaus können detaillierte Designs zusätzliche Präzision sowohl bei der Herstellung als auch bei der Handhabung der Formen erfordern.
- Trennmittel
Der wichtigste Faktor, den Sie bei der Verwendung von Kunststoffformen für Beton berücksichtigen sollten, ist die Anwendung des richtigen Trennmittels. Diese Mittel werden verwendet, um zu verhindern, dass der Beton an der Form klebt. Die im Allgemeinen verwendeten Trennmitteltypen sind die folgenden.
- Ölbasierte Trennmittel
- Trennmittel auf Wasserbasis
- Silikonbasierte Trennmittel
- Pulver-Trennmittel
- Natürliche und umweltfreundliche Trennmittel
- Schaumtrennmittel
- Hochtemperatur-Trennmittel
Es ist wichtig zu beachten, dass das gewählte Trennmittel mit dem Kunststoffmaterial der Form kompatibel sein muss. Dies ist notwendig, um die Qualität und Integrität des Betonprodukts zu erhalten.
- Temperatur und Aushärtung
Kunststoffformen für Beton können sehr empfindlich auf Temperaturschwankungen reagieren. Daher ist es wichtig, die Aushärtungsbedingungen sorgfältig zu handhaben. Dies ist aus folgenden Gründen von großer Bedeutung.
- Übermäßige Hitze kann die Form verformen
- Unzureichende Wärme kann das Aushärten des Betons beeinträchtigen
Der grundlegende Faktor für die Eignung des Gussstücks besteht darin, sicherzustellen, dass die Aushärtungstemperatur sowohl für die Form als auch für die Betonmischung geeignet ist.
- Reinigung und Wartung
Die Reinigung und Wartung von Kunststoffformen für Beton ist wichtig und kritisch. Der Hauptgrund dafür ist, dass Restbeton Probleme bei der zukünftigen Verwendung der Formen verursachen kann. Daher ist eine regelmäßige Reinigung und Wartung mit geeigneten Methoden wichtig. Darüber hinaus müssen regelmäßige Routinekontrollen auf Verschleiß durchgeführt werden. Dies trägt letztendlich dazu bei, die Wirksamkeit der Form zu erhalten.
- Umweltauswirkungen
Es ist wichtig, die Umweltauswirkungen der Kunststoffformen für Beton zu berücksichtigen. Das für die Form ausgewählte Kunststoffmaterial kann, wenn es nicht biologisch abbaubar und nicht recycelbar ist, negative Auswirkungen auf die Umwelt haben. Im Gegensatz dazu wird die Auswahl von recycelbarem oder biologisch abbaubarem Kunststoff jedoch sicherlich positive Auswirkungen auf die Umwelt haben. Darüber hinaus ist auch die ordnungsgemäße Entsorgung oder das Recycling alter Formen von großer Bedeutung, um die negativen und schädlichen Auswirkungen auf die Umwelt zu verringern.
Schlussfolgerung
Kunststoffformen sind eine praktische und kostengünstige Wahl für den Betonguss und bieten Flexibilität und Haltbarkeit. Kunststoffformen für Beton bieten effektive Lösungen für den Betonguss und verleihen komplexen und komplizierten Designs einen Mehrwert. Sie erleichtern die Herstellung detaillierter und individueller Designs und sind gleichzeitig leicht und korrosionsbeständig. Bei richtiger Handhabung und Wartung bieten Kunststoffformen zuverlässige Leistung und qualitativ hochwertige Ergebnisse für verschiedene Anwendungen. Kunststoffformen sind in der Lage, eine große Bandbreite an Betonmischungen zu verarbeiten und Gießen Umgebungen effektiv. Regelmäßige Wartung, sorgfältige Handhabung und entsprechende Lagerung erhöhen die Lebensdauer und Leistung der Kunststoffbetonformen zusätzlich. Insgesamt sind sie ein hervorragendes Werkzeug sowohl für dekorative als auch für strukturelle Betonprojekte.