Die wichtige Formenbauindustrie - Chinesische Formen
China Formenbauunternehmen sind nun aufgrund der hohen Wettbewerbsfähigkeit von Spritzgussunternehmen aus Indien und Vietnam stark unter Druck. Der Grund für den starken Druck auf das chinesische Kunststoff-Spritzgießunternehmen wird im Folgenden näher erläutert.
- In Indien und Vietnam gibt es viele Unternehmen, die Kunststoffspritzgussformen herstellen, was dazu beitragen wird, dass China seinen Anteil am Markt für Formenbau erhöht.
- Die Inflation hat dazu geführt, dass die chinesischen Formenbauer seit dem Krieg mehr Materialkosten für Formenstahl und andere Materialien, insbesondere Kupfer, zahlen müssen. Außerdem hat dies zu einem erheblichen Anstieg der Gehälter geführt. Von 2009 bis 2011 stieg das allgemeine Gehalt um 40%, aber es stieg nicht jedes Jahr weiter an.
- Aufgrund der weltweiten wirtschaftlichen Rezession haben viele chinesische Gießereiunternehmen einen Auftragsrückgang zu verzeichnen. Daher konkurrieren sie alle miteinander um den Preis der Gussformen, was zu einem ständigen Preisverfall führt, wenn eine Bestellung erforderlich ist. Gleichzeitig können sie die Qualität der Formen nicht garantieren.
China Formenbauer ist einer der wichtigsten Formenbauer der Welt. China ist die Heimat verschiedener Kategorien von Formenbauer, und dies stellt für jeden, der einen Formenbauer im Land sucht, eine Herausforderung dar. Viele Erstkäufer sind oft erstaunt über die schiere Verfügbarkeit von Formenbauern, stellen aber bald fest, dass sie sich mehr Zeit für die Auswahl des am besten geeigneten Formenbauers hätten nehmen sollen.
In den meisten Industrieländern wie dem Vereinigten Königreich, Amerika oder Japan ist es relativ einfach, einen vertrauenswürdigen Formenbauer zu finden. Natürlich ist der Preis sehr hoch, aber in China ist das ganz anders. Das liegt daran, dass die zahlreichen Formenbauer in diesem Land nicht alle hochwertige Formen herstellen. Stattdessen stellen viele dieser Formenbauer in der Regel minderwertige Formen her, die in erster Linie den Anforderungen des lokalen Marktes gerecht werden.

Die Vorteile von China Schimmel
Wie oben erläutert, stehen die chinesischen Werkzeughersteller bei der Herstellung von Werkzeugen unter Druck, aber im Vergleich zu den indischen und vietnamesischen Werkzeugen hat das chinesische Werkzeug immer noch seine Vorteile. Natürlich sind diese Vorteile nicht mehr so groß wie noch vor 10 Jahren. Aber auch heute noch kaufen viele indische Unternehmen chinesische Gussformen für ihre indischen Produkte. Kunststoff-Spritzgießereien.
Eine einfache Information, die ich von einem meiner indischen Kunden erhalten habe (der für ein großes Kunststoffspritzgussunternehmen in Indien arbeitet), besagt, dass Inder keine qualitativ hochwertigen Kunststoffspritzgussformen herstellen können; wenn sie irgendwelche kleinen Probleme haben, halten sie an dem Projekt fest und tun nichts, um das Problem zu lösen. Andererseits gibt es bei den in Indien hergestellten Spritzgussformen große Probleme mit der Qualität und der Vorlaufzeit.
Hier sind einige Vorteile der Verwendung von China-Formen:
Welches ist die kostengünstigste Option, wenn Sie für Ihr Projekt eine Spritzgussform benötigen? In Bezug auf Qualität und Vorlaufzeit ist eine Form aus China die kostengünstigste Option. Nach China zu gehen, um eine Form anfertigen zu lassen, mag auf den ersten Blick etwas abschreckend wirken, aber wenn Sie weiter in diesem Artikel lesen, werden Sie verstehen, warum die meisten Menschen diese Option wählen. Hier sind einige Gründe, warum Menschen Spritzgussformen aus China kaufen:

Die Kosten sind niedriger als in den USA und Europa.
Die Produktionskosten für einen Formenhersteller in China sind viel niedriger als bei einer Bestellung in den USA oder Europa. Das liegt vor allem an den wirtschaftlichen Unterschieden, insbesondere an den niedrigeren Lohnkosten in China. Das ist kein Grund, sich schlecht zu fühlen, da es in einem angemessenen Verhältnis zu den Lebenshaltungskosten steht und mit den Arbeitskosten in vielen Branchen vergleichbar ist.
Die Qualität ist gut.
Da China über eine so große Industrielandschaft verfügt, ist das Land auf Kunststoffformen und andere Industrieprodukte spezialisiert. Sie können aus einer Reihe von chinesischen Formenfabriken wählen, die alle über umfangreiche Erfahrung in der Herstellung hochwertiger Formen verfügen.
Einfach zu arrangieren.
Über das Internet ist es sehr einfach, direkt mit chinesischen Kunststoffformenherstellern zu kommunizieren. Da sie daran gewöhnt sind, mit den USA zu verhandeln, können Sie leicht einen Vertreter finden, der Englisch spricht, und Sie können mit ihm hin und her arbeiten, bis Sie zufrieden sind.
Personalisierung
Die chinesischen Formenhersteller können maßgeschneiderte Formen nach Ihren spezifischen Anforderungen und Normen wie DME, HASCO usw. herstellen, um sicherzustellen, dass Sie eine Form erhalten, die genau Ihren Anforderungen entspricht.
Große Produktionskapazität
Mit einem großen Pool an qualifizierten Arbeitskräften und hochmodernen Produktionsanlagen verfügt China über eine große Produktionskapazität für Spritzgussformen. Das bedeutet, dass sie Formen in großen Mengen herstellen und schnell liefern können.
Große Auswahl an Materialien
Die chinesischen Formenhersteller können Formen aus einer Vielzahl von Materialien herstellen, darunter Kunststoff, Metall und Verbundwerkstoffe.
In Anbetracht der obigen Ausführungen sollten Sie bei der Beauftragung eines chinesischen Formenbauers für Ihre produktionsbezogenen Aufgaben einige entscheidende Faktoren berücksichtigen, um ein erfolgreiches Ergebnis zu erzielen. Legen Sie beispielsweise die spezifischen Ziele fest, die Sie mit der Unterstützung eines renommierten Unternehmens erreichen wollen. Dabei kann es sich entweder um Präzision oder um andere wichtige Dinge handeln, die zur Verbesserung Ihrer Produktionstätigkeit beitragen. Präzision sorgt dafür, dass die Aufgabe genau nach Anweisung ausgeführt wird.
Zusätzlich zu den oben genannten Anforderungen müssen Sie auch die Anforderungen dieses wettbewerbsintensiven Industriesektors ernsthaft berücksichtigen. Wenn Sie die neuen technologischen Entwicklungen berücksichtigen, spielt die Pünktlichkeit eine entscheidende Rolle bei der Sicherstellung eines robusten Produktionsablaufs Ihrer Waren. Je früher Sie die angeforderten Kunststoffteile erhalten, desto schneller können Sie die Produktion abschließen und so die dringend benötigte Kosteneffizienz erreichen.
Sie sollten sich auch etwas Zeit nehmen, um sich mit allen für Ihre Produktionstätigkeit relevanten Dienstleistungen im Bereich Kunststoffformen vertraut zu machen. Dies wird Ihnen helfen, die richtigen Entscheidungen zu treffen und von den Vorteilen einer globalen Tätigkeit zu profitieren. Der beste Ort für diese Aufgabe Kunststoff-Spritzgusswerkzeuge ist in China; Daher sollten Sie dies im Hinterkopf behalten, wenn Sie eine Zusammenarbeit mit einer Chinesisches Unternehmen für Formen. Die Montage und Endbearbeitung sollte später in Mexiko erfolgen. Einfach ausgedrückt: Diese Empfehlungen berücksichtigen die grundlegenden Anforderungen, nämlich Kosteneffizienz und Schnelligkeit.
Ebenso wichtig ist, dass das beste globale Unternehmen Erfahrung in der Zusammenarbeit mit einer Vielzahl von Kunden weltweit hat. Dies ist von entscheidender Bedeutung, da es die nahtlose Lieferung aller Kunststoffformen an jeden Standort weltweit gewährleistet. Um in der Fertigung erfolgreich zu sein, muss man aufkommenden Trends folgen.
Wenn Sie das nächste Mal Kunststoffspritzgussarbeiten benötigen, sollten Sie sicherstellen, dass Sie ausschließlich mit Unternehmen zusammenarbeiten, die über ein umfassendes Verständnis der globalen Geschäftstätigkeit verfügen. Das ist wichtig, denn es wird auch Ihre globalen Expansionspläne wesentlich erleichtern.
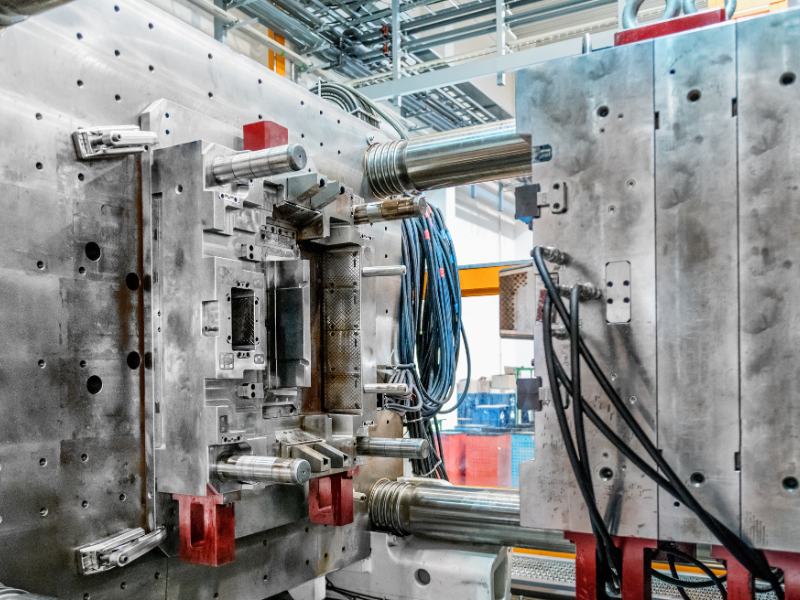
Wie man Gussformen von einem chinesischen Gussformhersteller bezieht
Das Verfahren ist viel einfacher, als Sie vielleicht denken. Sie können Hersteller von Formen aus China online finden, indem Sie nach ihnen suchen oder Empfehlungen von anderen Personen einholen. Dann können Sie Kontakt aufnehmen und die Bedingungen aushandeln. In der Regel können Sie Ihre Pläne in den USA erstellen lassen und zur Prüfung an den Hersteller schicken, oder Sie arbeiten direkt mit den Formenbauern in China zusammen.
Hier sind einige Schritte zur Beschaffung von Formen aus China:
- Bestimmen Sie die Spezifikationen Ihrer Form: Bestimmen Sie die Art der Form, die Sie benötigen, einschließlich ihrer Größe, ihres Materials und anderer Spezifikationen. Sie sollten auch eine Vorstellung von Ihrem Budget und Produktionsvolumen haben.
- Recherchieren und wählen Sie potenzielle Lieferanten von Formen in China aus: Nutzen Sie Online-Verzeichnisse, Messen, Empfehlungen, Online-Recherchen und Branchenverbände, um potenzielle Formenlieferanten in China zu ermitteln. Bewerten Sie die Lieferanten anhand ihrer Erfahrung, ihres Rufs und ihrer Fähigkeit, Ihre spezifischen Anforderungen zu erfüllen.
- Nehmen Sie Kontakt zu den chinesischen Formenbauern auf: Nehmen Sie Kontakt zu den chinesischen Formenbauern auf und senden Sie ihnen Ihre Spezifikationen. Fordern Sie von jedem Anbieter ein Angebot an und fragen Sie nach Mustern, Referenzen und Zertifizierungen.
- Bewerten Sie die Angebote und Muster: Bewerten Sie die Angebote und Muster der einzelnen Anbieter und vergleichen Sie sie mit Ihrem Budget und Ihren Spezifikationen. Sie sollten auch Faktoren wie die Vorlaufzeit, die Zahlungsbedingungen und die Qualitätskontrollverfahren des Lieferanten berücksichtigen.
- Aushandeln und Abschließen des Vertrags: Sobald Sie einen Lieferanten ausgewählt haben, verhandeln Sie die Vertragsbedingungen, einschließlich Zahlungsbedingungen, Vorlaufzeit und Qualitätskontrolle. Stellen Sie sicher, dass der Vertrag Details wie Arbeitsumfang, Spezifikationen und Liefertermine enthält.
- Überwachung der Produktion und Qualitätskontrolle: Überwachen Sie den Produktionsprozess genau, um sicherzustellen, dass die Form nach Ihren Vorgaben hergestellt wird. Sie können auch ein externes Qualitätskontrollunternehmen damit beauftragen, die Form vor dem Versand zu prüfen.
- Entgegennahme und Prüfung der Form: Sobald die Form fertig ist, nehmen Sie sie in Empfang und prüfen sie sorgfältig, um sicherzustellen, dass sie Ihren Spezifikationen entspricht. Testen Sie die Form, um sicherzustellen, dass sie qualitativ hochwertige Teile produziert.
Wenn es sich um ein neues Projekt handelt, sollten Sie immer einige Prototypen anfertigen, bevor Sie Formen bestellen. Wenn Sie mit dem Prototyp zufrieden sind, können Sie die Form bestellen und auf die Lieferung warten. Trotz Verpackung und Versand werden die Kosten viel niedriger sein als in den USA oder Europa.
Sincere Tech ist einer der Top 10 Hersteller von Formen in China. Wir bieten Kunststoff nach Maß Formen und Kunststoffspritzgussteile in die ganze Welt. Wir haben Kunden aus Deutschland, Kanada, Amerika, Spanien, Thailand, Litauen, etc.
Sie suchen einen professionellen und langjährigen Partner Chinesischer Formenbauer?
SINCERE TECH ist eines der 10 besten Unternehmen für Kunststoff-Spritzgussformen in China und bietet Spritzgießservice in verschiedene Länder der Welt mit der besten Qualität und hervorragende Kundendienstleistungen. Das Unternehmen, das als Marktführer in der China Formenherstellermit viel Engagement Sorten der Sorte Spritzgussteile. Der optimale Service, die führende Ausrüstung und die fortschrittliche Technologie sind wertvolle Gründe für den Erfolg des Unternehmens.
Sincere tech optimiert das Design auf der Grundlage der Anforderungen des Kunden, und sie sind sehr aufmerksam bei der Gestaltung der Form, wie sie ihr Geld sparen können, die Verringerung der Verarbeitung und Form Reparaturzeit für ihre Kunden.
Im Unternehmen gibt es 15 Experten für die Konstruktion von Kunststoffformen, die einen vollständigen Formenentwurf erstellen, vier Ingenieure, die den Formenentwurf überprüfen, und zwei technische Leiter, die die Formenstruktur vor der Herstellung der Form überprüfen. Dieses Team beherrscht sowohl die UG- als auch die PRO-E-Software mit voller Hingabe.
Die Ingenieure des Unternehmens sind auf das jeweilige Produkt spezialisiert, so dass sie ihren Kunden wertvolle Vorschläge und technische Unterstützung bieten können. Die Konstruktionsingenieure bieten DFM (Design for Manufacturability) innerhalb von zwei Werktagen an, und innerhalb von fünf Tagen liefern sie den Kunden fertig geformte Designs.
Die Entwicklung von Formen mit perfektem Design und die besten Verarbeitungstechnologien für den Formenbau mit konstanter Arbeit sind ihr Schlüssel zum Erfolg. Der hohe Stellenwert, den sie dem Design, den ausgeklügelten Arbeitsmitteln und den idealen Verarbeitungssystemen beimessen, sorgt für mehr Zufriedenheit bei ihren Kunden.
Sincere Tech hat drei automatische Produktionslinien in der Oberflächenbehandlung und -werkstatt eingeführt, die staubdicht sind und für die Oberflächenstrukturierung, das Oberflächenspray, IMD usw. verwendet werden. Sie bieten ihren Kunden Spritzgussformenbau und Spritzgussdienstleistungen zu niedrigen Kosten, die von ihren Konkurrenten nicht angeboten werden können. Wenn Sie einen Partner für Spritzgussformen oder Spritzgussverfahren in China suchen um Ihr Unternehmen zu unterstützen, können Sie sich an unser Team wenden, und wir werden Ihnen innerhalb von zwei Werktagen antworten.
Wir verfügen über mehr als 18 Jahre reiche Berufserfahrung und 15 Jahre Erfahrung in der Kommunikation in technischem Englisch.
Guter Preis, gute Qualität und guter Service sind unsere Grundsätze.
Wir garantieren, dass Ihr Projekt erfolgreich sein wird. Sehen Sie sich an, was unsere zufriedenen Kunden sagen.
Sind Sie bereit, Ihre Form Projekt mit China Formenbauer Jetzt beginnen,
Schicken Sie uns Ihre Anforderungen für ein Angebot, Sie werden nichts verlieren, sondern erhalten wettbewerbsfähige China Spritzgussform Preis. Prüfen Sie unten, was ist glücklich Kunde sagt
