Hvad er sprøjtestøbning?
Sprøjtestøbning er et værktøj, der bruges i sprøjtestøbningsprocessen til at producere dele ved at sprøjte materiale ind i et formhulrum. Det er typisk lavet af stål (H13, P20, 1.2312, 1.2344, S136H osv.) eller aluminium og er omhyggeligt designet til at matche det endelige produkts form og specifikationer.
Sprøjtestøbeformen er opdelt i to halvdele, som er en hulrumshalvdel og en kernehalvdel, der spændes sammen under støbeprocessen, hvor materialet sprøjtes ind gennem en gran i formhulrummet, hvor det afkøles og størkner til den ønskede form. Når delen er formet, åbnes formen, og delen skubbes ud. Formen kan genbruges til at producere flere dele.

Hvad er sprøjtestøbning
Typer af sprøjtestøbeforme
Blandt de mange varianter af sprøjtestøbeforme kan du finde:
Hulrumsspecifik form
Hver cyklus i sprøjtestøbningsprocessen kan kun generere én del, når man bruger en enkeltkavitetsform. Processen med at fremstille en del med denne form er så enkel som at sprøjte plastharpiks ind i den, vente på, at den afkøles, og derefter fjerne det færdige produkt.
Når man sammenligner produktionsomkostningerne for multi-shot forme med single-cavity forme, er førstnævnte normalt mere overkommelige. Når det ville være for dyrt at fremstille et lille antal komponenter på én gang, er de det bedste valg til prototyper og lavvolumenproduktion.

Form med et enkelt hulrum
Fordelene ved enkeltskudsforme er bl.a:
- Effektivt med hensyn til omkostninger: Produktionen af en single-shot form er ofte billigere end produktionen af en multi-shot form.
- Enkelt design: Nem produktion og vedligeholdelse på grund af det enkle design: Enkeltskudsforme er ofte mindre komplekse i layoutet end flerskudsforme.
- Fleksibilitet: En lang række anvendelser, som f.eks. prototyper og produktionskørsler i små mængder, er velegnede til brug af enkeltkavitetsforme.
Ulemperne ved enkeltskudsforme inkluderer:
- Begrænset produktion: Denne begrænsning gør enkeltkavitetsforme uegnede til støbning af store mængder, fordi de kun er i stand til at producere en enkelt del i hver cyklus.
- Komplekse dele: Enkeltkavitetsforme er ikke gode til at lave komplicerede dele med mange dele; til dem skal du bruge en flerkavitetsform eller en familieform.
- Ineffektivitet: Sammenlignet med forme med flere hulrum er single-shot-forme mindre effektive, fordi de kun kan skabe en enkelt del i hver cyklus på grund af deres begrænsede kapacitet.
Støbeforme med flere hulrum:
Multihulrumsforme er en type sprøjtestøbeform, der har mere end ét hulrum. Det gør, at sprøjtestøbningsprocessen kan lave mere end én del i hver omgang. Afhængigt af applikationens behov kan disse forme laves med huller, der er ens eller forskellige.
På grund af dens evne til at skabe mange dele i én cyklus bruges multihulrumsforme typisk til Sprøjtestøbning af store mængder produktionskørsler. Denne funktion giver dem mulighed for at øge produktionseffektiviteten og samtidig sænke omkostningerne pr. del.

Form med flere hulrum
Fordelene ved multihulrumsforme er bl.a:
- Produktion af store mængder: Multikavitetsforme er lavet til store produktionskørsler, hvilket gør det nemt at lave mange dele.
- Omkostningseffektivt: Multikavitetsforme er normalt billigere end enkeltkavitetsforme, fordi de kan lave flere dele i en enkelt serie.
- Komplekse dele: Multihulrumsforme kan bruges til at lave dele, der er komplicerede og har mange dele.
Ulemperne ved multihulrumsforme omfatter:
- Komplekst design: Multihulrumsforme er sværere at fremstille og vedligeholde end enkelthulrumsforme, fordi deres design er mere kompliceret.
- øgede formomkostningerne: Støbeforme med flere hulrum kan være dyrere end støbeforme med et enkelt hulrum, fordi de forskellige hulrum kan blive udsat for forskellig belastning og slitage under sprøjtestøbningsprocessen. Det kan føre til mindre effektiv produktion og højere omkostninger til reparationer.
Varmkanalsform:
Varmkanalsform er en type sprøjtestøbning, der bruger et varmkanalsystem til at levere det smeltede plastmateriale ind i formhulrummene. Varmkanalsystemet består af en opvarmet manifold, der fordeler den smeltede plast til individuelle dysespidser, som derefter ledes ind i formhulrummene.

Varmkanalsform
Fordelene ved varmkanalsforme er bl.a:
- Forbedret emnekvalitet: Varmkanalforme kan producere emner med forbedret kvalitet, da de minimerer den mængde plast, der er tilbage i kanalerne, hvilket reducerer risikoen for defekter som f.eks. flash, korte skud og synkemærker.
- Øget produktionseffektivitet: Varmkanalforme kan øge produktionseffektiviteten, da de eliminerer behovet for manuel indgriben for at fjerne kanalerne fra de støbte dele, hvilket reducerer cyklustiden og forbedrer den samlede produktionshastighed.
- Energieffektivitet: Varmkanalsforme er mere energieffektive sammenlignet med traditionelle koldkanalsforme, da de minimerer mængden af plast, der går til spilde i kanalerne.
Ulemperne ved varmkanalsforme omfatter:
- Komplekst design: Varmkanalsforme er mere komplekse i deres design end traditionelle koldkanalsforme, hvilket gør dem dyrere at producere og vedligeholde.
- Øget vedligeholdelse: Varmkanalsforme kræver typisk mere vedligeholdelse end koldkanalsforme, da de har et mere komplekst varmesystem, der skal holdes i god stand.
- Sårbarhed over for tilstopning: Varmkanalforme kan være sårbare over for tilstopning, især når de behandler materialer med høj viskositet eller med lange flowlængder, da det kan få den smeltede plast til at størkne i kanalerne. Det kan resultere i reduceret produktionseffektivitet og øgede vedligeholdelsesomkostninger.
Stabel forme:
Stabelform er en type sprøjtestøbeform, der gør det muligt at støbe flere hulrum samtidig i en enkelt maskincyklus. Stabelforme er i bund og grund to eller flere forme, der er stablet oven på hinanden, hvor hver form producerer en enkelt del.

Stabelform
Fordelene ved stabelforme er bl.a:
- Øget produktionseffektivitet: Stabelforme gør det muligt at støbe flere dele på samme tid, hvilket øger produktionseffektiviteten og reducerer cyklustiden.
- Mindre materialespild: Stabelforme minimerer materialespild, da de giver mulighed for at producere flere dele ved hjælp af et enkelt skud plastmateriale.
- Lavere omkostninger: Stabelforme kan være mere omkostningseffektive sammenlignet med forme med en enkelt kavitet, da de giver mulighed for at producere flere dele med en enkelt maskincyklus.
Ulemperne ved stabelforme inkluderer:
- Komplekst design: Stabelforme kan være mere komplekse i deres design sammenlignet med forme med en enkelt kavitet, hvilket gør dem dyrere at producere og vedligeholde.
- Reduceret delkvalitet: Stabelforme kan producere dele med nedsat kvalitet, da tilstedeværelsen af flere hulrum kan resultere i øget risiko for defekter som f.eks. flash, korte skud og synkemærker.
- Øget vedligeholdelse: Stabelforme kræver typisk mere vedligeholdelse sammenlignet med forme med en enkelt kavitet, da de har et mere komplekst design, der skal holdes i god stand.
Familiens skimmelsvamp:
Familieforme, også kendt som multi-impression molds, som svarer til multiple cavity mold, er en type sprøjtestøbning, der gør det muligt at støbe flere dele med lidt forskellige designs samtidigt i en enkelt maskincyklus. Dette opnås ved at have flere hulrum i formen, der kan producere forskellige dele med forskellige former og størrelser.
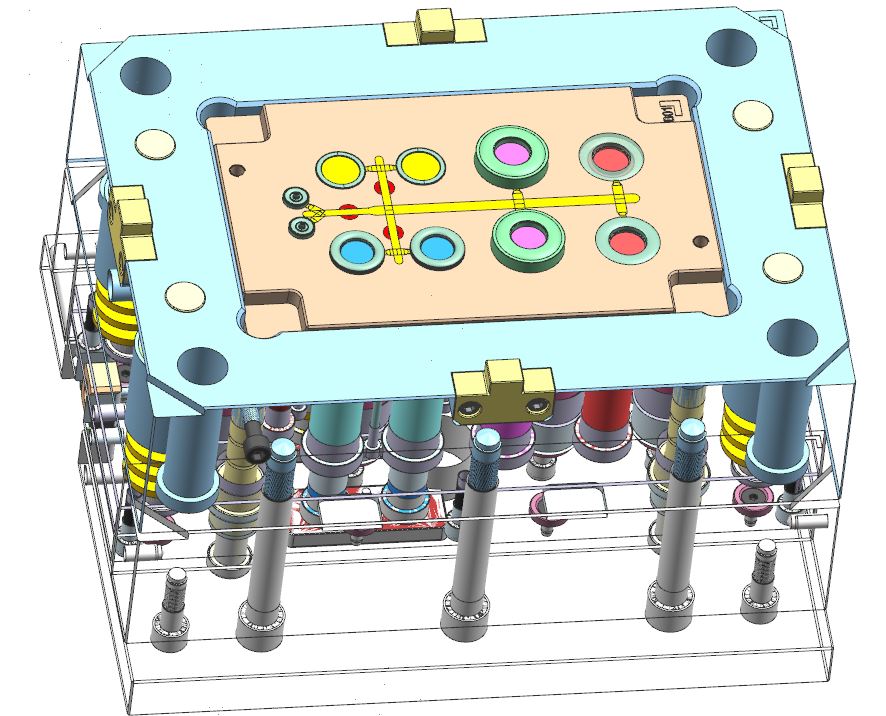
Familiens skimmelsvamp
Fordelene ved familieformer er bl.a:
- Øget effektivitet i produktionen: Familieforme gør det muligt at støbe flere dele med forskellige designs samtidig, hvilket øger produktionseffektiviteten og reducerer cyklustiden.
- Reducerede omkostninger: Familieforme kan være mere omkostningseffektive sammenlignet med at producere flere enkeltkavitetsforme til hver del, da de giver mulighed for at producere flere dele med en enkelt maskincyklus.
- Fleksibilitet: Familieforme giver mulighed for at producere forskellige dele med varierende design, hvilket gør dem til en alsidig mulighed for producenter, der har brug for at producere en række forskellige produkter.
Ulemperne ved familieskimmelsvampe inkluderer:
- Komplekst design: Familieforme kan være mere komplekse i deres design sammenlignet med forme med en enkelt kavitet, hvilket gør dem dyrere at producere og vedligeholde.
- Reduceret delkvalitet: Familieforme kan producere dele med reduceret kvalitet, da tilstedeværelsen af flere hulrum kan resultere i øget risiko for defekter som flash, korte skud og synkemærker.
To-skudsforme:
To-skudsform (Sprøjtestøbning med 2 skud), også kendt som overstøbning eller multi-shot molds eller 2K mold, er en type sprøjtestøbning, der gør det muligt at støbe to forskellige materialer sammen i en enkelt maskincyklus. Denne proces involverer støbning af et første materiale (basismateriale) i en form og derefter støbning af et andet materiale (overformningsmateriale) på det første materiale.

Form med to skud
Fordelene ved to-skudsforme inkluderer:
- Øget funktionalitet: To-skudforme giver mulighed for at kombinere to forskellige materialer med forskellige egenskaber for at skabe dele med øget funktionalitet.
- Forbedret æstetik: To-skudforme giver mulighed for at integrere forskellige farver eller teksturer i en enkelt del, hvilket skaber et mere visuelt tiltalende produkt.
- Reduceret samlingstid: Ved at kombinere to materialer i en enkelt del kan two-shot-forme reducere behovet for yderligere monteringstrin, hvilket reducerer produktionstiden og -omkostningerne.
Ulemperne ved to-shot-forme er bl.a:
- Komplekst design: To-skudforme er mere komplekse i deres design sammenlignet med enkelt-skudforme, hvilket gør dem dyrere at producere og vedligeholde.
- Øget cyklustid: Two-shot-forme har typisk en længere cyklustid sammenlignet med single-shot-forme, da processen involverer støbning af to materialer i en enkelt maskincyklus.
- Problemer med kompatibilitet: To-skudforme kræver, at de to materialer, der støbes, er kompatible med hinanden og hæfter ordentligt, hvilket gør det vigtigt nøje at vælge de materialer, der bruges.
Skruer forme af:
Skrueforme er en type sprøjtestøbning, der er specielt designet til at producere dele med skruegevind, som f.eks. hætter, låg og beholdere. Disse forme er unikke, fordi de har en mekanisme, der gør det muligt for formens kerne at rotere, mens hulrummet forbliver stationært, så den støbte del kan skrues ud af formen, når den er afkølet og størknet.

Skruer formen af
Fordelene ved at skrue forme af inkluderer:
- Høj effektivitet: Udskruningsforme giver mulighed for effektiv produktion af gevinddele i en enkelt maskincyklus, hvilket reducerer produktionstiden og -omkostningerne.
- Forbedret nøjagtighed: Skrueforme giver mulighed for præcis produktion af gevinddele med ensartet stigning og gevinddybde, hvilket forbedrer slutproduktets kvalitet og ydeevne.
- Alsidighed: Skrueforme kan bruges til at producere en række forskellige dele med forskellige gevindtyper og -størrelser, hvilket gør dem til en alsidig mulighed for mange forskellige anvendelser.
Ulemper ved at skrue forme af inkluderer:
- Komplekst design: Skrueforme er mere komplekse i designet sammenlignet med andre typer forme, hvilket gør dem dyrere at producere og vedligeholde.
- Øget cyklustid: Skrueforme har typisk en længere cyklustid sammenlignet med andre typer forme, da processen involverer rotation af formens kerne.
- Slid og slitage: Den roterende mekanisme i skrueforme kan være tilbøjelig til at blive slidt over tid, hvilket kræver regelmæssig vedligeholdelse for at få formen til at fungere korrekt.
Form med sammenklappelig kerne:
Støbeforme med sammenklappelig kerne er en type sprøjtestøbning, der bruges til at producere hule dele med indvendige hulrum, som f.eks. rør og andre komplekst formede dele. Disse forme bruger et unikt design, der gør det muligt for formens kerne at falde sammen i sig selv og skabe emnets indre hulrum.

Formkomponent med sammenklappelig kerne
Fordelene ved støbeforme med sammenklappelig kerne er bl.a:
- Forbedret effektivitet: Støbeforme med sammenklappelig kerne gør det muligt at producere hule dele i en enkelt maskincyklus, hvilket reducerer produktionstiden og -omkostningerne.
- Forbedret emnekvalitet: Støbeforme med sammenklappelig kerne giver et mere præcist og ensartet indre hulrum, hvilket forbedrer den samlede kvalitet af det endelige emne.
- Alsidighed: Støbeforme med sammenklappelig kerne kan bruges til at producere en lang række forskellige dele med forskellige former og størrelser, hvilket gør dem til en alsidig mulighed for mange forskellige anvendelser.
Ulemperne ved støbeforme med sammenklappelig kerne er bl.a:
- Komplekst design: Støbeforme med sammenklappelig kerne har et mere komplekst design end andre typer støbeforme, hvilket gør dem dyrere at producere og vedligeholde.
- Øget cyklustid: Støbeforme med sammenklappelig kerne har typisk en længere cyklustid sammenlignet med andre typer støbeforme, da processen involverer sammenklapning af formens kerne.
- Slid og slitage: Kernens sammenklappelige mekanisme kan blive udsat for slitage med tiden, hvilket kræver regelmæssig vedligeholdelse for at få formen til at fungere korrekt.
Fordele og ulemper ved plastsprøjtestøbning
Fordele ved Sprøjtestøbning:
- Produktion af store mængder: Sprøjtestøbning er en meget effektiv metode til at producere store mængder af identiske dele. Det gør den ideel til masseproduktion af forbrugsvarer, bildele og andre produkter, der kræver store mængder af ens dele.
- Præcision: Processen giver mulighed for meget præcis kontrol af dimensionsnøjagtighed og delkonsistens. Det skyldes brugen af nøje kontrollerede forarbejdningsbetingelser og støbemaskinens og formens stivhed.
- Hastighed: Sprøjtestøbning er en hurtig proces med cyklustider helt ned til et par sekunder for små dele. Det giver producenterne mulighed for at producere store mængder emner på relativt kort tid.
- Omkostningseffektivt: Omkostningerne ved at producere dele ved hjælp af sprøjtestøbning bliver mere økonomiske, når produktionsmængden øges. Det skyldes, at formen kan bruges til at producere mange dele i løbet af sin levetid, og omkostningerne pr. del falder, når mængden øges.
- Alsidighed: Sprøjtestøbning kan bruges til at fremstille dele af en lang række materialer, herunder plast, metaller og elastomerer. Denne alsidighed gør det til et populært valg for producenter, der har brug for at producere dele af forskellige materialer afhængigt af produktets specifikke krav.
- Automatisering: Sprøjtestøbemaskiner kan automatiseres, hvilket gør processen mere effektiv og reducerer behovet for manuelt arbejde. Det kan også forbedre emnernes ensartethed og kvalitet.
- Komplekse former: Sprøjtestøbning kan bruges til at fremstille komplekse former og designs, herunder dele med indviklede detaljer og snævre tolerancer. Det er muligt på grund af den præcise styring af støbeprocessen og muligheden for at designe meget detaljerede støbeforme.
- Valg af materiale: Sprøjtestøbning giver producenterne mulighed for at vælge mellem en lang række materialer, der hver især har deres egne unikke egenskaber, såsom styrke, fleksibilitet og modstandsdygtighed over for varme, kemikalier og slid. Det gør det muligt at vælge det bedste materiale til hver enkelt opgave og producere emner med de ønskede egenskaber.
Ulemper ved sprøjtestøbning:
- Høje startomkostninger: De indledende omkostninger ved at skabe formen kan være høje, især for komplekse former og designs. Det kan gøre processen mindre omkostningseffektiv for små mængder af dele eller for prototyper.
- Begrænset designfleksibilitet: Når formen er lavet, kan det være svært og dyrt at ændre designet. Det kan begrænse muligheden for at foretage designændringer eller forbedringer, når først formen er skabt.
- Materialeaffald: Sprøjtestøbning genererer en betydelig mængde skrotmateriale, som kan være dyrt at bortskaffe og miljøskadeligt. Det kan også øge produktionsomkostningerne og mindske processens samlede effektivitet.
- Gennemløbstid: Gennemløbstiden for at skabe formen og sætte sprøjtestøbningsprocessen i gang kan være lang, især for komplekse dele. Det kan bremse produktudviklingsprocessen og begrænse muligheden for hurtigt at bringe produkter på markedet.
- Begrænsninger i overfladefinish: Sprøjtestøbning giver muligvis ikke en overfladefinish af høj kvalitet på nogle dele, især dem med indviklede detaljer eller snævre tolerancer. Det kan begrænse muligheden for at producere dele med et æstetisk udseende af høj kvalitet.
- Materialekompatibilitet: Kompatibilitet mellem materiale og form kan være en udfordring, da nogle materialer måske ikke fungerer godt med visse typer forme eller kræver særlige forarbejdningsbetingelser. Det kan begrænse muligheden for at fremstille dele af bestemte materialer og øge produktionsomkostningerne.
- Begrænset emnestørrelse: Sprøjtestøbning er begrænset af formens størrelse og støbemaskinens spændekraft. Det kan begrænse størrelsen på de dele, der kan produceres, og øge omkostningerne ved at producere større dele.
- Sekundære operationer: Nogle dele kan kræve sekundære operationer, som f.eks. trimning eller efterbehandling, efter at de er blevet støbt. Det kan øge produktionsomkostningerne og begrænse processens samlede effektivitet, men nogle gange kan disse problemer løses ved at forbedre sprøjtestøbeformen.
Almindelige problemer med en sprøjtestøbning
Når du arbejder med sprøjtestøbning af plast, vil der altid være nogle problemer, som du skal løse hver dag. Her er nogle almindelige udfordringer inden for sprøjtestøbning:
Problemer med vridning:
Vridning er et almindeligt problem ved sprøjtestøbning og henviser til en deformation eller forvrængning af den støbte del, der opstår, efter at den er taget ud af formen. Dette kan ske på grund af en række faktorer, herunder:

Warp-forvrængning
- Forkert afkøling: Hvis emnet afkøles for hurtigt eller ujævnt, kan det forårsage skævheder, da materialet krymper og trækker sig sammen i forskellige hastigheder.
- Restspænding: Sprøjtestøbning skaber restspænding i emnet på grund af det høje tryk, der anvendes under støbeprocessen. Denne spænding kan forårsage vridning, hvis den ikke aflastes ordentligt.
- Valg af materiale: Nogle materialer er mere tilbøjelige til at blive skæve end andre. For eksempel er materialer med lav varmebestandighed eller lav dimensionsstabilitet mere tilbøjelige til at vride sig.
- Formens design: Formens design kan også bidrage til skævvridning, især hvis formen ikke giver mulighed for korrekt afkøling eller materialeflow.
- Forarbejdningsbetingelser: Inkonsekvente forarbejdningsforhold, som f.eks. varierende indsprøjtningshastigheder, formtemperaturer og trykniveauer, kan forårsage skævheder.
For at forhindre vridning er det vigtigt at vælge det rette materiale, optimere formdesignet og forarbejdningsbetingelserne og implementere korrekt køle- og materialehåndteringspraksis. Derudover kan det være nødvendigt at bruge behandlinger efter støbning, som f.eks. udglødning, for at afhjælpe restspænding og forbedre dimensionsstabiliteten.
Flash-problemer:
Flashdefekter er et udtryk, der bruges i sprøjtestøbning til at henvise til det overskydende materiale, der tvinges ud af formen under støbeprocessen. Flash opstår, når materialet flyder ud over det tilsigtede formhulrum og ind i skillelinjen eller mellemrummet mellem de to halvdele af formen.

Støbning Flash eller grater
Flash kan være forårsaget af flere faktorer, herunder:
- Forkert formdesign: En dårligt designet form kan forårsage flash ved at lade materiale lække ind i skillelinjen.
- Inkonsekvente forarbejdningsbetingelser: Varierende behandlingsbetingelser, som f.eks. indsprøjtningshastighed og tryk, kan forårsage flash.
- Materialekompatibilitet: Nogle materialer er muligvis ikke kompatible med formen og kan forårsage flash, når de flyder ind i skillelinjen.
- Slid og slitage på formen: Med tiden kan formen blive slidt, og det kan give flash, når materialet lækker ind i skillelinjen.
Flash kan have flere negative effekter, herunder at reducere emnets dimensionsnøjagtighed, øge skrotprocenten og gøre det vanskeligere at arbejde efter støbningen. For at minimere flash er det vigtigt at optimere formdesignet, forarbejdningsbetingelserne og materialevalget samt regelmæssigt at vedligeholde og reparere formen efter behov.
Svejselinjer:
Svejselinjer er et almindeligt problem ved sprøjtestøbning og henviser til synlige mærker på overfladen af den støbte del, hvor to strømme af smeltet plastmateriale mødes og størkner. Svejselinjer opstår, når materialet ikke smelter helt sammen, når det flyder ind i plastform hulrum, hvilket efterlader en synlig linje på emnets overflade.

Svejselinje
Svejselinjer kan være forårsaget af flere faktorer, herunder:
- Utilstrækkeligt smelteflow: Hvis materialet ikke har tid nok til at flyde og smelte helt sammen, kan der dannes en svejselinje.
- Forkert design af indkast: En dårligt designet port, som er det punkt, hvor det smeltede materiale kommer ind i formhulrummet, kan forårsage en svejselinje.
- Inkonsekvente forarbejdningsbetingelser: Varierende bearbejdningsforhold, som f.eks. indsprøjtningshastighed og tryk, kan forårsage en svejselinje.
- Materialekompatibilitet: Nogle materialer er måske ikke kompatible med formen og kan forårsage en svejselinje, når de flyder ind i formhulrummet.
Svejselinjer kan svække emnets styrke og reducere dets samlede kvalitet. For at minimere svejselinjer er det vigtigt at optimere formdesignet, forarbejdningsbetingelserne og materialevalget og at implementere korrekt materialehåndteringspraksis. Derudover kan det være nødvendigt at bruge særlige forarbejdningsteknikker, som f.eks. multihulrumsforme eller varmkanalsystemer, for at reducere dannelsen af svejselinjer.
Vaskemærker:
Sinkmærker, også kendt som "sink", "vacuum sink" eller "skin", er nedsunkne eller deprimerede områder på overfladen af en sprøjtestøbt plastdel. De er normalt forårsaget af en række faktorer, herunder:
- Krympning af harpiks: Når harpiksen afkøles og størkner, kan den krympe ujævnt, hvilket fører til synkemærker.
- Dårligt materialeflow: Hvis harpiksen ikke flyder jævnt ind i alle områder af formen, kan det skabe hulrum eller nedsunkne områder.
- Utilstrækkeligt pakningstryk: Hvis indsprøjtningstrykket ikke er højt nok, fylder harpiksen måske ikke formen helt ud, hvilket fører til synkemærker.
- Problemer med formens design: Formdesignet, herunder portplacering og -størrelse, kanalsystem og udluftning, kan alle påvirke kvaliteten af den støbte del og kan bidrage til synkemærker.
Sinkmærker kan påvirke den æstetiske kvalitet og funktionaliteten af en støbt del og kan være en kilde til frustration for producenter og slutbrugere. For at minimere synkemærker er det vigtigt nøje at overveje de faktorer, der bidrager til dem, såsom materialevalg, formdesign, forarbejdningsparametre og emnedesign, og foretage justeringer efter behov for at optimere sprøjtestøbningsprocessen.
Flowmærker:
Flydemærker er et almindeligt problem ved sprøjtestøbning og henviser til synlige mærker eller striber på overfladen af den støbte del, der skyldes strømmen af det smeltede plastmateriale, når det fylder formhulrummet. Flydemærker opstår, når materialet flyder ujævnt og efterlader et synligt mærke på emnets overflade.
Flydemærker kan være forårsaget af flere faktorer, herunder:
- Utilstrækkeligt smelteflow: Hvis materialet ikke har tid nok til at flyde og fylde formhulrummet, kan der dannes flydemærker.
- Forkert design af indkast: En dårligt designet port, som er det punkt, hvor det smeltede materiale kommer ind i formhulrummet, kan forårsage flydemærker.
- Inkonsekvente forarbejdningsbetingelser: Varierende behandlingsbetingelser, som f.eks. indsprøjtningshastighed og tryk, kan forårsage flowmærker.
- Materialekompatibilitet: Nogle materialer er måske ikke kompatible med formen og kan forårsage flydemærker, når de flyder ind i formhulrummet.
Flydemærker kan reducere emnets overordnede kvalitet og kosmetiske udseende. For at minimere flydemærker er det vigtigt at optimere formdesignet, forarbejdningsbetingelserne og materialevalget og at implementere korrekt materialehåndteringspraksis. Derudover kan det være nødvendigt at bruge særlige forarbejdningsteknikker, som f.eks. multihulrumsforme eller varmkanalsystemer, for at reducere dannelsen af flydemærker.
Problemer med ridser:
Ridser er synlige mærker eller ridser på overfladen af et sprøjtestøbt emne, som skyldes fysisk kontakt mellem emnet og formen eller andre fremmedlegemer under støbeprocessen. Ridser kan opstå af flere årsager, bl.a:
- Dårligt formdesign: Forkert designede forme eller formkomponenter kan forårsage ridser på emnets overflade.
- Utilstrækkelig smøring: Hvis formen og formkomponenterne ikke er ordentligt smurt, kan de forårsage ridser på emnets overflade.
- Dårlig materialehåndtering: Dårlig håndtering af råmaterialet eller de færdige dele kan forårsage ridser på overfladen af delen.
- Affald i formen: Fremmedlegemer eller snavs i formhulrummet kan forårsage ridser på emnets overflade.
Ridser kan reducere emnets overordnede kvalitet og kosmetiske udseende. For at minimere problemer med ridser er det vigtigt at implementere korrekt formdesign, smøring, materialehåndtering og vedligeholdelsespraksis. Derudover kan regelmæssig rengøring og inspektion af formen og formkomponenterne være med til at forhindre, at der opstår ridser.
Ejector-mærker:
Udstødermærker er synlige mærker på overfladen af et sprøjtestøbt emne, der er forårsaget af udstøderstifterne eller andre udstødermekanismer under støbeprocessen. Udkastermærker opstår, når udkasterpindene skubber den støbte del ud af formhulrummet og efterlader synlige mærker på delens overflade.
Ejector-mærker kan skyldes flere faktorer, herunder:
- Forkert design af udstøderbolte: Hvis udkastertapperne ikke er korrekt udformet, kan de efterlade synlige mærker på emnets overflade.
- Overdreven kraft: Hvis ejektorstifterne anvender for stor kraft på emnet under udskydningen, kan de efterlade dybere og mere synlige mærker på emnets overflade.
- Inkonsekvent udstødningskraft: Hvis udstødningskraften ikke er ensartet fra den ene udstødningsstift til den anden, kan det resultere i ujævne udstødningsmærker på emnets overflade.
- Dårlig overfladefinish: Hvis formhulrummets overfladefinish ikke er glat, kan det forårsage udstødningsmærker på emnets overflade.
Udkastermærker kan reducere emnets overordnede kvalitet og kosmetiske udseende. For at minimere ejektormærker er det vigtigt at optimere designet af ejektorstifterne og formhulrummets overfladefinish og at implementere korrekt vedligeholdelses- og inspektionspraksis. Derudover kan det være nødvendigt at bruge særlige udstødningsmekanismer, som f.eks. luftassisteret udstødning eller sideudstødning, for at minimere udstødningsmærker.
Problemer med korte skud:
Et kort skud er et almindeligt problem i sprøjtestøbning, der opstår, når det smeltede plastmateriale ikke fylder formhulrummet helt ud, hvilket resulterer i en støbt del, der er mindre end den ønskede størrelse. Korte skud kan opstå af flere grunde, herunder:
- Utilstrækkeligt materiale: Hvis der ikke er nok materiale til at fylde formhulrummet, kan der opstå et kort skud.
- Forkerte behandlingsbetingelser: Hvis behandlingsbetingelserne, f.eks. indsprøjtningshastighed og tryk, ikke er indstillet korrekt, kan der opstå et kort skud.
- Dårligt formdesign: En dårligt designet form kan forårsage et kort skud, da materialet måske ikke kan flyde ind i alle områder af formhulrummet.
- Nedbrydning af materialet: Hvis materialet er nedbrudt eller ikke er blevet opbevaret korrekt, kan det forårsage et kort skud.
Korte skud kan reducere emnets samlede kvalitet og funktionalitet og resultere i spildt materiale og behandlingstid. For at minimere korte skud er det vigtigt at optimere formdesignet, forarbejdningsbetingelserne og materialevalget og at implementere en korrekt materialehåndteringspraksis. Derudover kan regelmæssig overvågning og vedligeholdelse af støbeudstyret være med til at forhindre, at der opstår short shots.
Luftlås og brændemærker:
Luftfælder og brændemærker er almindelige problemer i sprøjtestøbning, der kan opstå på grund af forkerte behandlingsforhold eller formdesign.
Luftfælder opstår, når luft bliver fanget i formhulrummet under sprøjtestøbningsprocessen, hvilket får materialet til at flyde rundt om luftlommen i stedet for at fylde den. Dette kan resultere i synlige hulrum eller lommer i den støbte del. Luftfælder kan være forårsaget af flere faktorer, herunder:
- Utilstrækkeligt materialeflow: Hvis materialet ikke flyder ordentligt ind i formhulrummet, kan der blive fanget luft.
- Forkert design af porten: Hvis porten ikke er designet korrekt, kan der blive fanget luft i formhulrummet.
- Utilstrækkelig udluftning: Hvis formen ikke udluftes ordentligt, kan der blive fanget luft i formhulrummet.
Brændemærker opstår, når plastmaterialet udsættes for høje temperaturer i for lang tid, hvilket får det til at nedbrydes og give synlige mærker eller misfarvning på emnets overflade. Brændemærker kan skyldes flere faktorer, bl.a:
- For høje forarbejdningstemperaturer: Hvis forarbejdningstemperaturen indstilles for højt, kan materialet nedbrydes og give brændemærker.
- Utilstrækkelig afkølingstid: Hvis emnet ikke afkøles ordentligt, kan materialet nedbrydes og give brændemærker.
- Dårligt formdesign: En dårligt designet form kan få materialet til at blive udsat for høje temperaturer i for lang tid, hvilket resulterer i brændemærker.
For at minimere luftfælder og brændemærker er det vigtigt at optimere forarbejdningsbetingelserne og formdesignet og at implementere korrekt overvågnings- og vedligeholdelsespraksis. Derudover kan det være nødvendigt at bruge særlige forarbejdningsteknikker, som f.eks. lavtemperaturstøbning eller vakuumstøbning, for at minimere luftfælder og brændemærker.
Forarbejdning til at lave en sprøjtestøbning:
Processen med at lave en sprøjtestøbning involverer flere trin:
Formdesign:
Sprøjtestøbningsdesign er et kritisk aspekt af sprøjtestøbningsprocessen, da det direkte påvirker kvaliteten, effektiviteten og omkostningerne ved de støbte dele.
En veldesignet sprøjtestøbeform vil producere dele, der opfylder de ønskede krav til størrelse, form og kvalitet, samtidig med at den er effektiv at producere og nem at vedligeholde.
De vigtigste faktorer, man skal overveje, når man designer en sprøjtestøbeform, er bl.a:
- Emnets geometri: Designet af den støbte del skal tage højde for delens ønskede størrelse, form og funktioner.
- Valg af materiale: Det materiale, der skal bruges til formen og den støbte del, skal vælges ud fra faktorer som pris, styrke og termisk stabilitet.
- Formhulrum: Antallet og placeringen af formhulrummene skal vælges, så de opfylder kravene til produktionsmængden.
- Portsystem: Designet af gatesystemet er afgørende, da det bestemmer, hvordan plastmaterialet flyder ind i formhulrummet.
- Udstødningssystem: Udstødningssystemet skal være designet til at sikre, at de støbte dele kan fjernes fra formen uden skader.
- Kølesystem: Kølesystemet skal være designet til at sikre, at de støbte dele afkøles jævnt og hurtigt, hvilket reducerer cyklustiden og forbedrer kvaliteten.
- Udkast til vinkler: Formens design skal omfatte passende trækvinkler, så de støbte dele kan tages ud af formen.
- Udluftning: Formen skal udluftes, så luften kan slippe ud af formens hulrum, hvilket reducerer risikoen for luftfælder og brændemærker.
- Vedligeholdelse og reparation: Formen skal være designet til at være nem at vedligeholde og reparere for at minimere nedetid og øge produktionseffektiviteten.
Design af sprøjtestøbeforme er en kompleks proces, der kræver ekspertise inden for områder som maskinteknik, materialevidenskab og fremstilling. Det er vigtigt at arbejde med en velrenommeret formdesigner for at sikre, at formen er designet korrekt og opfylder dine behov.
CNC-programmering:
CNC-programmering (Computer Numerical Control) er et vigtigt trin i fremstillingen af en sprøjtestøbeform. Når formdesignet er færdigt, er næste trin CNC-programmering. Følgende er de vigtigste trin, der er involveret i CNC-programmering til fremstilling af sprøjtestøbning:
- Oversættelse af CAD-modellen: CAD-modellen oversættes til et CAM-program (Computer Aided Manufacturing), som bruges til at skabe CNC-koden til formen.
- Oprettelse af CNC-kode: CNC-koden oprettes i CAM-programmet, som giver instruktioner til CNC-maskinen om, hvordan den skal flytte og skære formkomponenterne. Koden tager højde for formkomponenternes materiale og tykkelse samt de ønskede former og funktioner.
- Oprettelse af værktøjsbane: Værktøjsstien oprettes i CAM-programmet, som definerer den sti, som det skærende værktøj skal følge for at bearbejde formkomponenterne. Værktøjsbanen tager højde for formkomponenternes former og funktioner og CNC-maskinens muligheder.
- Simulering: CNC-koden og værktøjsbanen simuleres i CAM-programmet for at sikre, at formkomponenterne bearbejdes korrekt og i henhold til de korrekte specifikationer.
- CNC-bearbejdning: CNC-koden indlæses i CNC-maskinen, som derefter bruger koden og værktøjsstien til at bearbejde formkomponenterne.
CNC-programmering er et kritisk trin i fremstillingsprocessen for sprøjtestøbeforme, da det bestemmer nøjagtigheden og kvaliteten af formkomponenterne. Det er vigtigt at arbejde med en CNC-programmør, der har erfaring med programmering af sprøjtestøbeforme, for at sikre, at CNC-koden oprettes korrekt og efter de rigtige specifikationer. Det er også i dette trin, at formens kølekanaler, ejektorsystem og andre funktioner føjes til formkomponenterne for at sikre, at de fungerer korrekt.
Indkøb af BOM-liste over støbeforme
En Mold BOM-liste (Bill of Materials) er en omfattende liste over alle de komponenter og materialer, der er nødvendige for at fremstille en sprøjtestøbeform. Den omfatter følgende elementer:
- Stål til formens bund og kerne/hulrumsindsatser
- Varmkanalkomponenter
- Kølesystemets komponenter, f.eks. vandledninger og køleblokke
- Udskydningssystemets komponenter, f.eks. udskydningsstifter og bøsninger
- Komponenter til granulatudtrækning
- Varmebånd og temperaturregulatorer
- Formkomponenter, som f.eks. bøsninger, styrestifter og låseanordninger
- Formindsatser, som f.eks. glidere og løftere
- Specialvarer som datostempler og brugerdefinerede logoer
Mold BOM-listen er et vigtigt værktøj til indkøb og produktion, da den giver en klar og detaljeret liste over de komponenter og materialer, der er nødvendige for at producere formen. Den bruges til at sikre, at alle de nødvendige komponenter er bestilt og til rådighed, når formen er klar til at blive fremstillet.
Det er vigtigt at arbejde med en velrenommeret leverandør, når man køber komponenter til en sprøjtestøbeform, da kvaliteten og pålideligheden af disse komponenter kan have en betydelig indvirkning på effektiviteten og kvaliteten af sprøjtestøbningsprocessen.
Grov bearbejdning af formen:
Grovbearbejdning af sprøjtestøbeforme refererer til den indledende bearbejdning af stålkomponenterne i en sprøjtestøbeform for at opnå formens grundlæggende form og størrelse. Dette trin udføres typisk ved hjælp af CNC-maskiner (computer numerical control). Følgende er de vigtigste trin, der er involveret i grovbearbejdning af sprøjtestøbeforme:
- Valg af stål: Det første skridt er at vælge den passende ståltype til formen, f.eks. P20 eller H13, baseret på de ønskede egenskaber for den støbte del.
- Skæring af stål: Stålet skæres til den rette størrelse og form ved hjælp af en CNC-maskine. Dette trin kan også omfatte boring og gevindskæring af huller til køle- og udstødningssystemerne.
- Profilering af stål: Stålkomponenterne bearbejdes derefter for at opnå formens grundlæggende form, inklusive kernen og hulrumsindsatserne.
- Inspektion af stål: De bearbejdede komponenter inspiceres derefter for at sikre, at de opfylder de krævede tolerancer og specifikationer.
- Rengøring af stål: De bearbejdede komponenter rengøres og afgrates for at fjerne ru kanter og snavs.
Den grove bearbejdning er et vigtigt trin i sprøjtestøbningsprocessen, da den lægger grunden til den endelige højpræcisionsbearbejdning og polering, der følger. Det er vigtigt at sikre, at grovbearbejdningen udføres nøjagtigt og efter de korrekte specifikationer for at sikre, at formen fungerer korrekt og producerer dele med den ønskede kvalitet.
Varmebehandling af formstål:
Varmebehandling af formstål er processen med at opvarme og afkøle stålkomponenterne i en sprøjtestøbeform for at forbedre deres mekaniske egenskaber og dimensionsstabilitet. Formålet med varmebehandling er at hærde stålet, aflaste restspændinger og forbedre dets slidstyrke og sejhed. Dette er specielt for det hærdede stål i sprøjtestøbeformen, hvis man bruger forhærdet stål til at lave sprøjtestøbeformen, er det ikke nødvendigt at udføre dette varmebehandlingsjob. Følgende er de vigtigste trin, der er involveret i varmebehandling af formstål:
- Udglødning: Stålkomponenterne opvarmes til en bestemt temperatur, normalt mellem 800-900 °C, og afkøles derefter langsomt for at aflaste indre spændinger og forbedre stålets bearbejdelighed.
- Hærdning: Stålkomponenterne opvarmes til en høj temperatur, typisk over den kritiske temperatur, og afkøles derefter hurtigt, som regel ved afkøling i olie eller vand. Denne proces hærder stålet og forbedrer dets slidstyrke.
- Anløbning: Efter hærdning anløbes stålkomponenterne ved at opvarme dem til en lavere temperatur i et bestemt tidsrum for at forbedre stålets sejhed og dimensionsstabilitet.
Varmebehandlingsprocessen er afgørende for at sikre, at stålkomponenterne i en sprøjtestøbeform har de ønskede mekaniske egenskaber og dimensionsstabilitet, som er afgørende for at producere støbte dele af høj kvalitet. Det er vigtigt at samarbejde med en leverandør af varmebehandling, der har erfaring med behandling af formstål, for at sikre, at varmebehandlingsprocessen udføres korrekt og i henhold til de korrekte specifikationer.
Finbearbejdning af formhulrum og kerne:
Finbearbejdning af formhulrum og kerne er processen med præcis bearbejdning af de indre overflader af formhulrummet og kerneindsatserne for at opnå formens endelige form og størrelse. Dette trin udføres typisk ved hjælp af CNC-maskiner (computer numerical control) med høj præcision og nøjagtighed. Følgende er de vigtigste trin, der er involveret i finbearbejdning af formhulrum og kerne:
- Forberedelse af overfladen: Overfladen på formhulrummet og kerneindsatserne rengøres og poleres for at fjerne eventuelle rester af snavs eller ujævnheder.
- Bearbejdning af overflader: De indvendige overflader af formhulrummet og kerneindsatserne bearbejdes ved hjælp af CNC-maskiner for at opnå formens endelige form og størrelse. Dette omfatter skabelse af de indviklede detaljer og funktioner i den støbte del, såsom tekst, logoer og underskæringer.
- Overfladeinspektion: De bearbejdede overflader inspiceres for at sikre, at de opfylder de krævede tolerancer og specifikationer.
- Overfladepolering: De indvendige overflader af formhulrummet og kerneindsatserne poleres til en høj finish for at forbedre de støbte deles overfladekvalitet og reducere risikoen for defekter.
Finbearbejdning er et kritisk trin i sprøjtestøbningsprocessen, da det bestemmer kvaliteten og nøjagtigheden af de støbte dele. Det er vigtigt at arbejde med en bearbejdningsvirksomhed, der har erfaring med finbearbejdning af formhulrum og kerne, for at sikre, at bearbejdningen udføres korrekt og efter de rigtige specifikationer. Det er også i dette trin, at formens udstødningssystem, kølekanaler og andre funktioner tilføjes for at sikre, at formen fungerer korrekt.
EDM-bearbejdning:
EDM (Electrical Discharge Machining) er en proces, der bruges til at lave indviklede og meget præcise former i metaldele, herunder dem i en sprøjtestøbeform. Processen bruger elektriske gnister til at fjerne materiale fra formens overflade og skabe den ønskede form. Følgende er de vigtigste trin, der er involveret i EDM-bearbejdning:
- Forberedelse af overfladen: Overfladen på den formkomponent, der skal bearbejdes, rengøres og poleres for at fjerne eventuelle rester af snavs eller ujævnheder.
- Opsætning af EDM: EDM-maskinen opsættes med de korrekte parametre, herunder gnistgab, pulsvarighed og elektrodemateriale, baseret på formdelens materiale og form.
- Gnisterosion: EDM-maskinen producerer elektriske gnister, der fjerner materiale fra formkomponenten og skaber den ønskede form. Denne proces foregår trinvist, hvor EDM-maskinen gradvist eroderer materialet, indtil den endelige form er opnået.
- Overfladeinspektion: Den bearbejdede overflade inspiceres for at sikre, at den opfylder de krævede tolerancer og specifikationer.
EDM-bearbejdning bruges ofte til formkomponenter, der har komplekse former eller små, indviklede detaljer, som er vanskelige at opnå med andre bearbejdningsprocesser. Det bruges også til at fremstille de skarpe kanter og hjørner, der er afgørende for, at en sprøjtestøbeform fungerer korrekt.
Processen er meget præcis og nøjagtig, hvilket gør den ideel til at producere støbte dele af høj kvalitet. Det er vigtigt at samarbejde med en EDM-leverandør, der har erfaring med EDM-bearbejdning af sprøjtestøbeforme, for at sikre, at processen udføres korrekt og efter de rigtige specifikationer.
Polering af formens overflade:
Polering af sprøjtestøbning er det sidste trin i fremstillingsprocessen for sprøjtestøbeforme. Det indebærer udjævning af formkomponenternes overflader for at sikre, at det færdige produkt har en glat og jævn overflade. Følgende er de vigtigste trin, der er involveret i polering af sprøjtestøbeforme:

Polering af plastforme
- Forberedelse af overfladen: Overfladerne på formkomponenterne rengøres og forberedes til polering. Eventuelle resterende ujævnheder eller bearbejdningsmærker fjernes for at sikre en glat overflade til polering.
- Grovpolering: Det første trin i poleringen er grovpolering, som indebærer at fjerne eventuelle store ujævnheder i overfladen på formkomponenterne. Dette trin udføres normalt med et groft slibemiddel, f.eks. sandpapir eller en slibebørste.
- Finpudsning: Finpudsning er det næste trin, som indebærer udjævning af overfladen på formkomponenterne til en finere finish. Dette trin udføres med et finere slibemiddel, f.eks. et finere sandpapir eller en slibebørste.
- Pudsning: Pudsning er det sidste trin i poleringen, hvor man bruger en pudseskive og polermiddel til at opnå en højglansfinish på formkomponenterne.
- Inspektion: Efter polering inspiceres formkomponenterne grundigt for at sikre, at de har en glat og jævn overflade uden ridser, revner eller andre ufuldkommenheder.
Polering af sprøjtestøbeforme er vigtigt, fordi det påvirker kvaliteten af det endelige produkt. En velpoleret form resulterer i et produkt med en glat og jævn overflade, hvilket er vigtigt for produktets funktionalitet og æstetik. Det er vigtigt at arbejde sammen med en erfaren formpolerer for at sikre, at formkomponenterne poleres efter de korrekte specifikationer og til det ønskede kvalitetsniveau.
Formtilpasning
Formtilpasning er et specialiseret job inden for sprøjtestøbning og involverer samling, installation og test af sprøjtestøbeforme. Formmestre er ansvarlige for at sikre, at formens komponenter er korrekt samlet og fungerer korrekt, og at formen producerer dele med de ønskede kvalitets- og ydelsesstandarder. Nogle af de vigtigste ansvarsområder for værktøjsmontører omfatter:
- Samling af formens komponenter: Formmestre er ansvarlige for at samle de forskellige komponenter i en sprøjtestøbeform, herunder hulrummet og kernekomponenterne, kanalsystemet og eventuelle hjælpekomponenter.
- Installation af formen på formtilpasningsmaskinen: Moldmaster skal være i stand til at montere formen på formtilpasningsmaskinen på en måde, der sikrer korrekt justering og funktion af formen, hvis der ikke er nogen formtilpasningsmaskine, skal du bruge den manuelle måde at montere formen på, det er det, de fleste virksomheder gør.
- Test af formen: Formmesteren er ansvarlig for at teste formen for at sikre, at den producerer dele med de ønskede kvalitets- og ydelsesstandarder. Dette omfatter inspektion af delene for eventuelle defekter, som f.eks. skævhed, krympning eller andre kvalitetsproblemer.
- Justering af formen: Hvis der opdages problemer i testfasen, er moldmaster ansvarlig for at foretage de nødvendige justeringer af formen for at sikre, at den producerer dele, der opfylder de ønskede specifikationer.
- Fejlfinding: Moldmaster skal være i stand til at identificere og fejlfinde eventuelle problemer, der måtte opstå under formtilpasningsprocessen.
Jobbet som værktøjsmontør kræver en kombination af teknisk viden, manuel fingerfærdighed og sans for detaljer. Formmontører skal kunne arbejde med en bred vifte af værktøjer og maskiner samt forstå de komplekse processer, der er involveret i sprøjtestøbning. Det er vigtigt for formmontører at have en god forståelse af sprøjtestøbningsprocessen samt erfaring med at arbejde med forskellige typer forme og materialer.
Første forsøg med sprøjtestøbning eller optagelse:
Prøvesprøjtning af sprøjtestøbning refererer til processen med at teste sprøjtestøbeformen for at producere en prøvedel ved hjælp af sprøjtestøbningsprocessen. Denne proces er et kritisk trin i sprøjtestøbningsprocessen, da den giver producenten mulighed for at evaluere formens ydeevne og foretage eventuelle nødvendige justeringer, før der produceres en stor mængde dele.
Sprøjtestøbningens prøveoptagelsesproces omfatter typisk følgende trin:
- Forberedelse: Formen installeres på sprøjtestøbemaskinen, og maskinen indstilles til skuddet. Beholderen fyldes med plastharpiks.
- Kontrol af smeltetemperatur: Smeltetemperaturen styres for at sikre, at plastharpiksen opvarmes til den korrekte temperatur for at producere dele af høj kvalitet.
- Indsprøjtning: Den smeltede plast sprøjtes ind i formen under højt tryk. Trykket opretholdes, indtil formen er fyldt med plastharpiksen.
- Afkøling: Formen afkøles for at få plastharpiksen til at størkne og forme emnet. Afkølingstiden bestemmes af den type plastharpiks, der bruges, og størrelsen og formen på den del, der produceres.
- Udstødning: Når emnet er størknet, fjernes det fra formen. Ejektorstifterne bruges til at skubbe emnet ud af formen.
- Inspektion: Den del, der produceres fra formen, inspiceres grundigt for at sikre, at den opfylder de ønskede specifikationer og kvalitetsstandarder.
- Justeringer: Hvis det er nødvendigt, kan der foretages justeringer af støbeprocessen for at forbedre formens ydeevne og kvaliteten af de dele, der produceres.
Prøvesprøjtningen er et vigtigt trin i sprøjtestøbningsprocessen, da den giver producenten mulighed for at evaluere formens ydeevne og foretage eventuelle nødvendige justeringer, før der produceres en stor mængde dele. Denne proces er med til at sikre, at formen producerer dele af høj kvalitet med de ønskede specifikationer.
Formen er pakket og klar til produktion:
Når formen er helt færdig hos formgiveren, er næste skridt den massive produktion. Pakning af formen og forberedelse til produktion er det sidste trin i sprøjtestøbningsprocessen, før masseproduktionen kan begynde. Dette trin involverer følgende opgaver:
- Rengøring og vedligeholdelse: Formen rengøres grundigt og inspiceres for at sikre, at der ikke er rester, snavs eller skader på formen.
- Pakning og opbevaring: Formen pakkes omhyggeligt og opbevares på et sikkert sted for at forhindre skader og sikre, at den er klar til brug, når der er brug for den.
- Test og justering: Formen testes for eventuelle problemer, f.eks. lækager, dårlig fyldning eller forkert udstødning af emner, og der foretages eventuelle nødvendige justeringer for at sikre, at formen fungerer korrekt.
- Opsætning af produktionen: Formen installeres i sprøjtestøbemaskinen, og alle nødvendige indstillinger, såsom temperatur, tryk og indsprøjtningshastighed, justeres for at opfylde de specifikke produktionskrav.
- Start af produktionen: Det første parti dele produceres, og processen overvåges for at sikre, at delene opfylder de krævede specifikationer og kvalitetsstandarder. Eventuelle nødvendige justeringer foretages for at optimere produktionsprocessen og sikre ensartet kvalitet.
Overordnet set er forberedelsen af formen til produktion et vigtigt trin i sprøjtestøbningsprocessen, som er med til at sikre en vellykket og effektiv produktion.
Ovenstående oplysninger er procedurer for fremstilling af en sprøjtestøbning, måske er der nogle små ting, der er gået glip af, men de fleste ting er ovenfor, som du kan se at lave en sprøjtestøbning er ikke let sag, hvis du har et sprøjtestøbningsprojekt i håndtag, skal du finde en professionel sprøjtestøbningsproducent til at servicere dig, dette vil sikre, at dit projekt kører med succes.
Sincere Tech er en professionel Kina skimmel fabrik med speciale i fremstilling af brugerdefinerede sprøjtestøbeforme. De har erfaring og ekspertise inden for design, udvikling og produktion af sprøjtestøbeforme af høj kvalitet til forskellige industrier og anvendelser.
De tilbyder en række tjenester, herunder formdesign, prototyper, produktion af forme og efterbehandling af forme, for at sikre, at deres kunder får de bedst mulige resultater. Med deres fokus på kvalitet, præcision og kundetilfredshed er Sincere Tech en pålidelig og troværdig partner til alle dine behov for sprøjtestøbning. Kontakt os for at få en pris på dit projekt nu.