Co je to vstřikovací forma?
Vstřikovací forma je nástroj používaný při vstřikování plastů k výrobě dílů vstřikováním materiálu do dutiny formy. Obvykle se vyrábí z oceli (H13, P20, 1.2312, 1.2344, S136H atd.) nebo hliníku a je pečlivě navržen tak, aby odpovídal tvaru a specifikacím konečného výrobku.
Vstřikovací forma je rozdělena na dvě poloviny, a to polovinu dutiny a polovinu jádra, které jsou během procesu vstřikování spojeny, přičemž materiál je vstřikován vtokem do dutiny formy, kde se ochladí a ztuhne do požadovaného tvaru. Jakmile je díl vytvarován, forma se otevře a díl je vyhozen. Formu lze opakovaně použít k výrobě více dílů.

Co je vstřikovací forma
Typy vstřikovacích forem
Mezi mnoha druhy vstřikovacích forem můžete najít:
Plísně specifické pro dutiny
Při použití formy s jednou dutinou může každý cyklus vstřikování vytvořit pouze jeden díl. Proces výroby dílu pomocí této formy je tak jednoduchý, že se do ní vstříkne plastová pryskyřice, počká se, až vychladne, a poté se hotový výrobek vyjme.
Při porovnání výrobních nákladů na vícevstřikové formy a formy s jednou dutinou jsou obvykle cenově výhodnější formy s jednou dutinou. Pokud by výroba malého počtu komponent najednou byla příliš nákladná, jsou tyto formy vhodné pro výrobu prototypů a malosériovou výrobu.

Forma s jednou dutinou
Mezi výhody jednorázových forem patří:
- Efektivní z hlediska nákladů: výroba formy s jedním výstřikem je často levnější než výroba formy s více výstřiky.
- Jednoduchý design: Snadná výroba a údržba díky jednoduchosti konstrukce: Jednorázové formy mají často méně složité uspořádání než formy s více záběry.
- Flexibilita: Pro využití forem s jednou dutinou je vhodná široká škála aplikací, jako je výroba prototypů a malosériová výroba.
Mezi nevýhody jednorázových forem patří:
- Omezená výroba: Toto omezení činí formy s jednou dutinou nevhodnými pro velkoobjemovou výrobu, protože jsou schopny vyrobit pouze jeden díl během každého cyklu.
- Složité díly: Pro výrobu složitých dílů s mnoha součástmi se nehodí formy s jednou dutinou.
- Neefektivita: V porovnání s vícedutinovými formami jsou formy s jedním výstřikem méně efektivní, protože mohou během každého cyklu vytvořit pouze jeden díl kvůli své omezené kapacitě.
Vícedutinové formy:
Vícedutinové formy jsou typem vstřikovacích forem, které mají více než jednu dutinu. Díky tomu může vstřikovací proces během každé otáčky vyrobit více než jeden díl. V závislosti na potřebě aplikace mohou být tyto formy vyrobeny s otvory, které jsou stejné nebo různé.
Díky své schopnosti vytvářet mnoho dílů v jednom cyklu se vícedutinové formy obvykle používají pro velkoobjemové vstřikování výrobní série. Tato funkce jim umožňuje zvýšit efektivitu výroby a zároveň snížit náklady na jeden díl.

vícedutinová forma
Mezi výhody vícedutinových forem patří:
- Velkosériová výroba: Vícedutinové formy jsou určeny pro velkosériovou výrobu, což usnadňuje výrobu velkého množství dílů.
- Nákladová efektivita: vícedutinové formy jsou obvykle levnější než formy s jednou dutinou, protože mohou vyrobit více dílů v jedné sérii.
- Složité díly: Pro výrobu složitých dílů s mnoha součástmi lze použít vícedutinové formy.
Mezi nevýhody vícedutinových forem patří:
- Komplexní design: Vícedutinové formy jsou náročnější na výrobu a údržbu než formy jednodutinové, protože jejich konstrukce je složitější.
- zvýšily náklady na formy: Více dutinové formy mohou být dražší než formy s jednou dutinou, protože různé dutiny mohou být během procesu vstřikování vystaveny různému namáhání a opotřebení. To může vést k nižší efektivitě výroby a vyšším nákladům na opravy.
Forma pro horké vtoky:
Forma pro horké vtoky je typ vstřikovací formy, která používá systém horkých kanálů k dopravě roztaveného plastového materiálu do dutin formy. Systém horkých kanálů se skládá z vyhřívaného rozdělovače, který rozvádí roztavený plast do jednotlivých tryskových hrotů, jež jsou následně vedeny do dutin formy.

Forma pro horké vtoky
Mezi výhody forem s horkými vtoky patří:
- Lepší kvalita dílů: Formy s horkými vtoky mohou vyrábět díly s lepší kvalitou, protože minimalizují množství plastu, který zůstává ve vtocích, a snižují tak riziko vzniku vad, jako jsou otřepy, krátké otřepy a stopy po propadnutí.
- Zvýšení efektivity výroby: Formy s horkými vtoky mohou zvýšit efektivitu výroby, protože eliminují nutnost ručního zásahu při vyjímání vtoků z výlisků, čímž se zkracuje doba cyklu a zvyšuje celková rychlost výroby.
- Energetická účinnost: V porovnání s tradičními formami se studeným kanálem jsou formy s horkým kanálem energeticky účinnější, protože minimalizují množství plastu, které se v kanálech ztrácí.
Mezi nevýhody forem s horkými vtoky patří:
- Komplexní design: V porovnání s tradičními formami se studenými vtoky jsou formy s horkými vtoky konstrukčně složitější, což prodražuje jejich výrobu a údržbu.
- Zvýšená údržba: Formy s horkými kanály obvykle vyžadují více údržby než formy se studenými kanály, protože mají složitější topný systém, který je třeba udržovat v dobrém stavu.
- Zranitelnost vůči ucpání: Zejména při zpracování materiálů s vysokou viskozitou nebo s velkou délkou toku mohou být formy s horkými kanály náchylné k ucpání, protože mohou způsobit ztuhnutí roztaveného plastu v kanálech. To může mít za následek snížení efektivity výroby a zvýšení nákladů na údržbu.
Stohovací formy:
Stohovací forma je typ vstřikovací formy, která umožňuje současné vstřikování více dutin v jednom strojním cyklu. Stohové formy jsou v podstatě dvě nebo více forem, které jsou naskládány na sebe, přičemž každá forma vyrábí jeden díl.

Stack Mold
Mezi výhody stohovacích forem patří:
- Zvýšení efektivity výroby: Stohovací formy umožňují lisovat více dílů současně, čímž se zvyšuje efektivita výroby a zkracuje se doba cyklu.
- Snížení množství materiálového odpadu: Stohovací formy minimalizují plýtvání materiálem, protože umožňují výrobu více dílů s použitím jediné dávky plastového materiálu.
- Nižší náklady: V porovnání s formami s jednou dutinou mohou být stohovací formy nákladově efektivnější, protože umožňují výrobu více dílů v jednom strojním cyklu.
Mezi nevýhody stohovacích forem patří:
- Komplexní design: V porovnání s formami s jednou dutinou mohou mít stohové formy složitější konstrukci, což prodražuje jejich výrobu a údržbu.
- Snížená kvalita dílů: Přítomnost více dutin může mít za následek zvýšené riziko vzniku vad, jako jsou otřepy, krátké výstřely a stopy po propadnutí.
- Zvýšená údržba: V porovnání s formami s jednou dutinou vyžadují komínové formy obvykle více údržby, protože mají složitější konstrukci, kterou je třeba udržovat v dobrém stavu.
Rodinné formy:
Rodinné formy, známé také jako vícevstřikovací formy, což je obdoba vícedutinových forem, jsou typem vstřikování, který umožňuje současné vstřikování více dílů s mírně odlišným designem v jednom strojním cyklu. Toho je dosaženo tím, že forma má více dutin, které mohou vyrábět různé díly různých tvarů a velikostí.
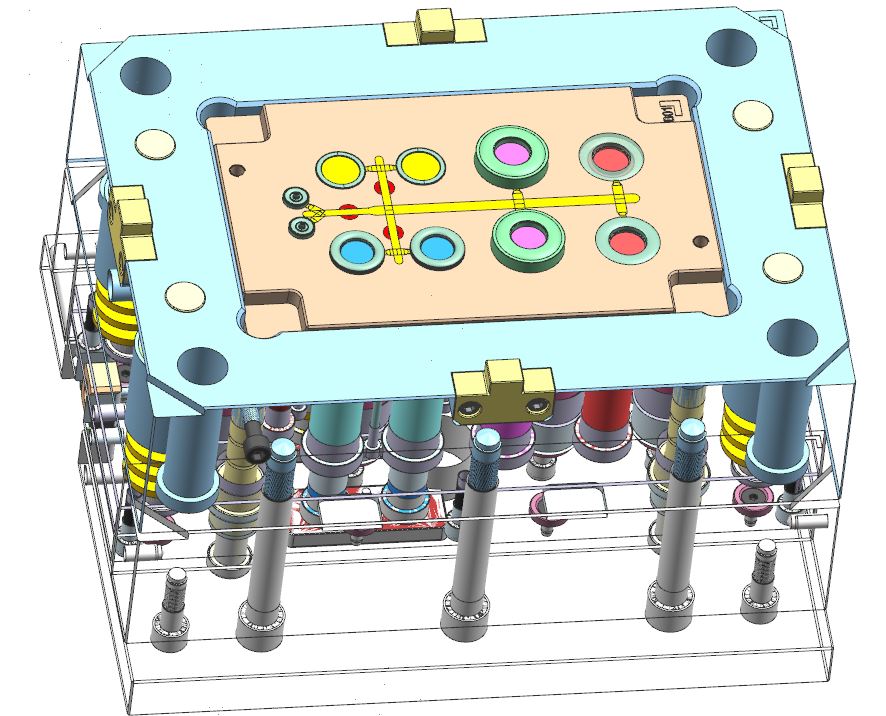
rodinná plíseň
Mezi výhody rodinných forem patří:
- Zvýšení efektivity výroby: Rodinné formy umožňují lisovat více dílů s různými konstrukcemi současně, čímž se zvyšuje efektivita výroby a zkracuje doba cyklu.
- Snížení nákladů: rodinné formy mohou být nákladově efektivnější ve srovnání s výrobou několika forem s jednou dutinou pro každý díl, protože umožňují výrobu více dílů v jednom cyklu stroje.
- Flexibilita: Rodinná forma umožňuje výrobu různých dílů s různým designem, což z ní činí univerzální volbu pro výrobce, kteří potřebují vyrábět řadu produktů.
Mezi nevýhody rodinných forem patří:
- Komplexní design: V porovnání s formami s jednou dutinou mohou mít rodinné formy složitější konstrukci, což prodražuje jejich výrobu a údržbu.
- Snížená kvalita dílů: Rodinné formy mohou vyrábět díly se sníženou kvalitou, protože přítomnost více dutin může mít za následek zvýšené riziko vzniku vad, jako jsou otřepy, krátké záběry a propadliny.
Dvoustřelové formy:
Forma se dvěma záběry (Vstřikování 2 výstřely), známý také jako overmolding nebo formy s více záběry či formy 2K jsou typem vstřikování, který umožňuje vstřikovat dva různé materiály v jednom strojním cyklu. Tento proces zahrnuje vstřikování prvního materiálu (základního materiálu) do formy a následné vstřikování druhého materiálu (nadlisovaného materiálu) na první materiál.

Dva výstřely do formy
Mezi výhody dvoustřelových forem patří:
- Rozšířená funkčnost: Dvoustřikové formy umožňují kombinovat dva různé materiály s různými vlastnostmi a vytvářet tak díly se zvýšenou funkčností.
- Vylepšený estetický vzhled: Dvoustřikové formy umožňují integrovat různé barvy nebo textury do jednoho dílu, čímž vzniká vizuálně atraktivnější výrobek.
- Zkrácení doby montáže: Díky spojení dvou materiálů do jediného dílu mohou dvoustřikové formy snížit potřebu dalších montážních kroků, a tím zkrátit výrobní čas a náklady.
Mezi nevýhody dvoustřelových forem patří:
- Komplexní design: Dvoustřelové formy jsou ve srovnání s jednostřelovými formami konstrukčně složitější, což prodražuje jejich výrobu a údržbu.
- Prodloužení doby cyklu: Dvoubodové formy mají obvykle delší dobu cyklu než formy s jedním výstřikem, protože proces zahrnuje lisování dvou materiálů v jednom cyklu stroje.
- Problémy s kompatibilitou: Proto je důležité pečlivě vybírat použité materiály, aby byly oba vstřikované materiály vzájemně kompatibilní a správně přilnuly.
Odšroubování forem:
Odšroubovací formy jsou typem vstřikovacích forem určených speciálně k výrobě dílů se šroubovým závitem, jako jsou víčka, uzávěry a nádoby. Tyto formy jsou jedinečné tím, že mají mechanismus, který umožňuje otáčení jádra formy, zatímco dutina zůstává nehybná, což umožňuje odšroubování výlisku z formy po jeho ochlazení a ztuhnutí.

odšroubování formy
Mezi výhody odšroubovacích forem patří:
- Vysoká účinnost: Odšroubovací formy umožňují efektivní výrobu závitových dílů v jednom cyklu stroje, čímž se zkracuje doba výroby a snižují náklady.
- Vylepšená přesnost: Odšroubovací formy umožňují přesnou výrobu závitových dílů s konstantním stoupáním a hloubkou závitu, což zlepšuje kvalitu a výkonnost konečného výrobku.
- Všestrannost: Odšroubovací formy lze použít k výrobě různých dílů s různými typy a velikostmi závitů, což z nich činí univerzální volbu pro mnoho různých aplikací.
Mezi nevýhody odšroubovacích forem patří:
- Komplexní design: Odšroubovací formy jsou ve srovnání s jinými typy forem konstrukčně složitější, což prodražuje jejich výrobu a údržbu.
- Prodloužení doby cyklu: Odšroubovací formy mají obvykle delší dobu cyklu ve srovnání s jinými typy forem, protože proces zahrnuje otáčení jádra formy.
- Opotřebení: Rotační mechanismus odšroubovacích forem může být časem náchylný k opotřebení a vyžaduje pravidelnou údržbu, aby forma správně fungovala.
Skládací forma s jádrem:
Formy se skládaným jádrem jsou typem vstřikovacích forem, které se používají k výrobě dutých dílů s vnitřními dutinami, jako jsou trubky, potrubí a další díly složitých tvarů. Tyto formy využívají jedinečnou konstrukci, která umožňuje, aby se jádro formy sbalilo samo do sebe a vytvořilo vnitřní dutinu dílu.

Komponenta skládací formy s jádrem
Mezi výhody forem se skládaným jádrem patří:
- Zvýšená efektivita: Formy se skládaným jádrem umožňují výrobu dutých dílů v jediném strojním cyklu, čímž se zkracuje doba výroby a snižují náklady.
- Zlepšená kvalita dílů: Formy se skládaným jádrem poskytují přesnější a konzistentnější vnitřní dutinu, což zlepšuje celkovou kvalitu finálního dílu.
- Všestrannost: Skládací formy s jádrem lze použít k výrobě široké škály různých dílů různých tvarů a velikostí, což z nich činí univerzální volbu pro mnoho různých aplikací.
Mezi nevýhody forem se skládaným jádrem patří:
- Komplexní design: V porovnání s jinými typy forem jsou formy se skládaným jádrem konstrukčně složitější, což prodražuje jejich výrobu a údržbu.
- Prodloužení doby cyklu: V porovnání s jinými typy forem je doba cyklu u forem se skládaným jádrem obvykle delší, protože proces zahrnuje skládání jádra formy.
- Opotřebení: Skládací mechanismus jádra může být časem náchylný k opotřebení a vyžaduje pravidelnou údržbu, aby forma správně fungovala.
Výhody a nevýhody vstřikovacích forem na plasty
Výhody Vstřikování:
- Velkoobjemová výroba: Vstřikování je vysoce efektivní metoda výroby velkých objemů stejných dílů. Proto je ideální pro hromadnou výrobu spotřebního zboží, automobilových dílů a dalších výrobků, které vyžadují velké množství podobných dílů.
- Přesnost: Tento proces umožňuje velmi přesnou kontrolu rozměrové přesnosti a konzistence dílů. To je dáno použitím přísně kontrolovaných podmínek zpracování a tuhostí tvářecího stroje a formy.
- Rychlost: Vstřikování je rychlý proces, u malých dílů trvá cyklus jen několik sekund. To umožňuje výrobcům vyrábět velké množství dílů v relativně krátkém čase.
- Nákladově efektivní: Náklady na výrobu dílů vstřikováním jsou s rostoucím objemem výroby ekonomičtější. Je to dáno tím, že forma může být použita k výrobě mnoha dílů po celou dobu své životnosti a náklady na jeden díl se s rostoucím objemem snižují.
- Všestrannost: Vstřikováním lze vyrábět díly ze široké škály materiálů, včetně plastů, kovů a elastomerů. Díky této univerzálnosti je oblíbenou volbou pro výrobce, kteří potřebují vyrábět díly z různých materiálů v závislosti na konkrétních požadavcích na výrobek.
- Automatizace: Vstřikovací stroje lze automatizovat, což zefektivňuje proces a snižuje potřebu ruční práce. To může také zlepšit konzistenci a kvalitu dílů.
- Složité tvary: Vstřikováním lze vyrábět složité tvary a konstrukce, včetně dílů se složitými detaily a přísnými tolerancemi. To je možné díky přesné kontrole procesu vstřikování a možnosti navrhovat vysoce detailní formy.
- Výběr materiálu: Vstřikování umožňuje výrobcům vybírat ze široké škály materiálů, z nichž každý má své jedinečné vlastnosti, jako je pevnost, pružnost a odolnost vůči teplu, chemikáliím a opotřebení. Díky tomu je možné vybrat pro každou aplikaci ten nejlepší materiál a vyrábět díly s požadovanými vlastnostmi.
Nevýhody vstřikování:
- Vysoké počáteční náklady: Počáteční náklady na vytvoření formy mohou být vysoké, zejména u složitých tvarů a konstrukcí. V případě malých množství dílů nebo prototypů tak může být tento proces méně nákladově efektivní.
- Omezená flexibilita designu: Po zhotovení formy může být změna designu obtížná a nákladná. To může omezit možnost provádět změny nebo vylepšení designu po vytvoření formy.
- Materiálový odpad: Při vstřikování vzniká značné množství odpadního materiálu, jehož likvidace může být nákladná a škodlivá pro životní prostředí. To může také zvýšit náklady na výrobu a snížit celkovou efektivitu procesu.
- Dodací lhůta: Dodací lhůta pro vytvoření formy a nastavení procesu vstřikování může být dlouhá, zejména u složitých dílů. To může zpomalit proces vývoje výrobku a omezit schopnost rychle uvést výrobky na trh.
- Omezení povrchové úpravy: Vstřikování nemusí u některých dílů, zejména u dílů se složitými detaily nebo přísnými tolerancemi, zajistit kvalitní povrchovou úpravu. To může omezit možnost výroby dílů s vysoce kvalitním estetickým vzhledem.
- Kompatibilita materiálů: Některé materiály nemusí dobře fungovat s určitými typy forem nebo vyžadují zvláštní podmínky zpracování. To může omezit možnost výroby dílů z určitých materiálů a zvýšit náklady na výrobu.
- Omezená velikost dílu: Vstřikování je omezeno velikostí formy a uzavírací silou vstřikovacího stroje. To může omezit velikost dílů, které lze vyrobit, a zvýšit náklady na výrobu větších dílů.
- Sekundární operace: Některé díly mohou po vytvarování vyžadovat sekundární operace, například ořezávání nebo dokončování. To může zvýšit náklady na výrobu a omezit celkovou efektivitu procesu, samozřejmě, že v některých případech lze tyto problémy vyřešit zdokonalením vstřikovací formy.
Běžné problémy se vstřikovací formou
Jakmile začnete pracovat v oblasti vstřikování plastů, vždy se objeví nějaký problém, který musíte každý den řešit, Zde jsou některé běžné problémy, kterým čelíte při vstřikování plastů:
Problémy s deformací:
Deformace je běžný problém, se kterým se setkáváme při vstřikování plastů, a označuje deformaci nebo zkreslení výlisku, ke kterému dochází po jeho vyjmutí z formy. K tomu může dojít v důsledku různých faktorů, včetně:

Zkreslení deformace
- Nesprávné chlazení: Pokud se díl ochladí příliš rychle nebo nerovnoměrně, může dojít k deformaci, protože materiál se smršťuje a smršťuje různou rychlostí.
- Zbytkové napětí: V důsledku vysokého tlaku při vstřikování vzniká v dílu zbytkové napětí. Toto napětí může způsobit deformaci, pokud není řádně odstraněno.
- Výběr materiálu: Některé materiály jsou náchylnější k deformaci než jiné. Například materiály s nízkou tepelnou odolností nebo nízkou rozměrovou stabilitou se deformují častěji.
- Konstrukce formy: Konstrukce formy může rovněž přispět k deformaci, zejména pokud forma neumožňuje správné chlazení nebo tok materiálu.
- Podmínky zpracování: Nestejné podmínky zpracování, jako jsou různé rychlosti vstřikování, teploty formy a úrovně tlaku, mohou způsobit deformace.
Aby se zabránilo deformaci, je důležité zvolit vhodný materiál, optimalizovat konstrukci formy a podmínky zpracování a zavést správné postupy chlazení a manipulace s materiálem. Kromě toho může být nutné použít úpravy po lisování, například žíhání, aby se snížilo zbytkové napětí a zlepšila rozměrová stabilita.
Problémy s bleskem:
Defekty vzplanutí jsou termínem používaným při vstřikování plastů, který označuje přebytečný materiál vytlačený z formy během procesu vstřikování. Bleskové vady vznikají, když materiál vytéká mimo zamýšlenou dutinu formy a dostává se do dělicí čáry nebo do prostoru mezi oběma polovinami formy.

Tvarování Třepení nebo otřepy
Záblesk může být způsoben několika faktory, včetně:
- Nesprávná konstrukce formy: Špatně navržená forma může způsobit únik materiálu do dělící čáry.
- Nevyhovující podmínky zpracování: Různé podmínky zpracování, jako je rychlost vstřikování a tlak, mohou způsobit vzplanutí.
- Kompatibilita materiálů: Některé materiály nemusí být s formou kompatibilní a mohou způsobit otřepy při vtékání do dělicí čáry.
- Opotřebení formy: V průběhu času může dojít k opotřebení formy a vzniku otřepů v důsledku úniku materiálu do dělící čáry.
Otřepy mohou mít několik negativních účinků, včetně snížení rozměrové přesnosti dílu, zvýšení zmetkovitosti a ztížení operací po lisování. Pro minimalizaci otřepů je důležité optimalizovat konstrukci formy, podmínky zpracování a výběr materiálu a pravidelně provádět údržbu a opravy formy podle potřeby.
Svařovací linky:
Svarové čáry jsou běžným problémem při vstřikování plastů a označují viditelné stopy na povrchu výlisku v místech, kde se setkávají a tuhnou dva proudy roztaveného plastového materiálu. Svarové čáry vznikají, když se materiál při proudění do formy zcela nespojí. plastové formy dutiny, přičemž na povrchu dílu zůstane viditelná čára.

Svařovací linka
Svařovací linky mohou být způsobeny několika faktory, včetně:
- Nedostatečný tok taveniny: Pokud materiál nemá dostatek času na to, aby vytekl a zcela se spojil, může se vytvořit linie svaru.
- Nesprávná konstrukce brány: Špatně navržené vtokové ústí, které je místem vstupu roztaveného materiálu do dutiny formy, může způsobit vznik sváru.
- Nevyhovující podmínky zpracování: Různé podmínky zpracování, například rychlost vstřikování a tlak, mohou způsobit vznik sváru.
- Kompatibilita materiálů: Některé materiály nemusí být s formou kompatibilní a mohou způsobit vznik sváru, když vtékají do dutiny formy.
Svarové čáry mohou oslabit pevnost dílu a snížit jeho celkovou kvalitu. Pro minimalizaci vzniku svarových linií je důležité optimalizovat konstrukci formy, podmínky zpracování a výběr materiálu a zavést správné postupy manipulace s materiálem. Kromě toho může být nutné použít speciální techniky zpracování, jako jsou formy s více dutinami nebo systémy horkých kanálů, aby se snížila tvorba svarových linií.
Značky dřezu:
Stopy po propadu, známé také jako "propad", "vakuový propad" nebo "kůže", jsou propadlé nebo propadlé oblasti na povrchu vstřikovaného plastového dílu. Obvykle jsou způsobeny řadou faktorů, včetně:
- Smršťování pryskyřice: Při ochlazování a tuhnutí pryskyřice může dojít k jejímu nerovnoměrnému smrštění, což může vést ke vzniku stop po propadnutí.
- Špatný tok materiálu: Pokud pryskyřice neproudí rovnoměrně do všech oblastí formy, mohou vzniknout dutiny nebo propadlé oblasti.
- Nedostatečný tlak při vstřikování: Pokud není vstřikovací tlak dostatečně vysoký, pryskyřice nemusí zcela vyplnit formu, což vede k propadům.
- Problémy s konstrukcí forem: Konstrukce formy, včetně umístění a velikosti vtoků, vtokového systému a odvzdušnění, může mít vliv na kvalitu výlisku a může přispět ke vzniku stop po propadnutí.
Stopy po propadnutí mohou ovlivnit estetickou kvalitu a funkčnost výlisku a mohou být zdrojem frustrace pro výrobce i koncové uživatele. Pro minimalizaci vzniku propadlin je důležité pečlivě zvážit faktory, které k nim přispívají, jako je výběr materiálu, konstrukce formy, parametry zpracování a konstrukce dílu, a podle potřeby provést úpravy pro optimalizaci procesu vstřikování.
Průtokové značky:
Stopy po proudění jsou běžným problémem při vstřikování a označují viditelné stopy nebo pruhy na povrchu vstřikovaného dílu, které jsou způsobeny prouděním roztaveného plastového materiálu při plnění dutiny formy. Stopy po proudění vznikají, když materiál proudí nerovnoměrně a zanechává na povrchu dílu viditelné stopy.
Výtokové stopy mohou být způsobeny několika faktory, včetně:
- Nedostatečný tok taveniny: Pokud materiál nemá dostatek času na to, aby vytekl a vyplnil dutinu formy, mohou se vytvořit stopy po toku.
- Nesprávná konstrukce brány: Špatně navržené vtokové ústí, které je místem vstupu roztaveného materiálu do dutiny formy, může způsobit stopy po toku.
- Nevyhovující podmínky zpracování: Různé podmínky zpracování, jako je rychlost vstřikování a tlak, mohou způsobit stopy po toku.
- Kompatibilita materiálů: Některé materiály nemusí být s formou kompatibilní a mohou způsobit stopy po toku do dutiny formy.
Stopy po toku mohou snížit celkovou kvalitu a kosmetický vzhled dílu. Pro minimalizaci stop po toku je důležité optimalizovat konstrukci formy, podmínky zpracování a výběr materiálu a zavést správné postupy manipulace s materiálem. Kromě toho může být nutné použít speciální techniky zpracování, jako jsou formy s více dutinami nebo systémy s horkými vtoky, aby se snížila tvorba stop po tečení.
Problémy se škrábanci:
Škrábance jsou viditelné stopy nebo škrábance na povrchu vstřikovaného dílu, které jsou způsobeny fyzickým kontaktem dílu s formou nebo jinými cizími předměty během procesu vstřikování. K poškrábání může dojít z několika důvodů, včetně:
- Špatná konstrukce formy: Nesprávně navržené formy nebo jejich součásti mohou způsobit poškrábání povrchu dílu.
- Nedostatečné mazání: Pokud nejsou forma a její součásti řádně namazány, mohou způsobit poškrábání povrchu dílu.
- Špatná manipulace s materiálem: Špatná manipulace se surovinami nebo hotovými díly může způsobit poškrábání povrchu dílu.
- Zbytky ve formě: Cizí předměty nebo nečistoty v dutině formy mohou způsobit poškrábání povrchu dílu.
Škrábance mohou snížit celkovou kvalitu a kosmetický vzhled dílu. Pro minimalizaci problémů s poškrábáním je důležité zavést správnou konstrukci formy, mazání, manipulaci s materiálem a postupy údržby. Pravidelné čištění a kontrola formy a jejích součástí může navíc pomoci zabránit vzniku problémů s poškrábáním.
Vyhazovací značky:
Vyhazovací stopy jsou viditelné stopy na povrchu vstřikovaného dílu, které jsou způsobeny vyhazovacími kolíky nebo jinými vyhazovacími mechanismy během procesu vstřikování. Vyhazovací stopy vznikají, když vyhazovací kolíky vytlačují výlisek z dutiny formy a zanechávají na povrchu dílu viditelné stopy.
Vyhazovací značky mohou být způsobeny několika faktory, včetně:
- Nesprávná konstrukce vyhazovacího kolíku: Pokud nejsou vyhazovací kolíky správně navrženy, mohou na povrchu dílu zanechat viditelné stopy.
- Nadměrná síla: Pokud vyhazovací kolíky působí na díl při vyhazování nadměrnou silou, mohou na povrchu dílu zanechat hlubší a výraznější stopy.
- Nekonzistentní vyhazovací síla: Pokud není vyhazovací síla u jednotlivých vyhazovacích kolíků stejná, může to mít za následek nerovnoměrné stopy po vyhazování na povrchu dílu.
- Špatná povrchová úprava: Pokud není povrch dutiny formy hladký, může to způsobit stopy po vyhazování na povrchu dílu.
Vyhazovací stopy mohou snížit celkovou kvalitu a kosmetický vzhled dílu. Aby se minimalizovaly stopy po vyhazování, je důležité optimalizovat konstrukci vyhazovacích kolíků a povrchovou úpravu dutiny formy a zavést správné postupy údržby a kontroly. Kromě toho může být nutné použít speciální vyhazovací mechanismy, jako je vyhazování za pomoci vzduchu nebo vyhazování s bočním účinkem, aby se minimalizovaly stopy po vyhazování.
Problémy s krátkou střelou:
Krátký výstřik je běžný problém při vstřikování, který nastává, když roztavený plastový materiál zcela nevyplní dutinu formy, což má za následek, že výlisek je menší než požadovaná velikost. Ke krátkému výstřiku může dojít z několika důvodů, včetně:
- Nedostatečný materiál: Pokud není dostatek materiálu k vyplnění dutiny formy, může dojít ke krátkému výstřiku.
- Nesprávné podmínky zpracování: Pokud nejsou správně nastaveny podmínky zpracování, jako je rychlost vstřikování a tlak, může dojít ke krátkému výstřelu.
- Špatná konstrukce formy: Špatně navržená forma může způsobit krátký výstřik, protože materiál nemusí být schopen proudit do všech oblastí dutiny formy.
- Degradace materiálu: Pokud materiál degradoval nebo nebyl správně skladován, může dojít ke zkratu.
Krátké záběry mohou snížit celkovou kvalitu a funkčnost dílu a vést k plýtvání materiálem a časem zpracování. Pro minimalizaci krátkých výstřiků je důležité optimalizovat konstrukci formy, podmínky zpracování a výběr materiálu a zavést správné postupy manipulace s materiálem. Pravidelné sledování a údržba lisovacího zařízení navíc může pomoci předcházet vzniku krátkých výstřiků.
Vzduchová past a stopy po popáleninách:
Vzduchové pasti a spáleniny jsou běžnými problémy při vstřikování, které mohou vzniknout v důsledku nevhodných podmínek zpracování nebo konstrukce formy.
Vzduchové pasti vznikají, když se v dutině formy během vstřikování zachytí vzduch, který způsobí, že materiál proudí kolem vzduchové kapsy, místo aby ji vyplnil. Výsledkem mohou být viditelné dutiny nebo kapsy ve výlisku. Vzduchové pasti mohou být způsobeny několika faktory, mezi které patří:
- Nedostatečný tok materiálu: Pokud materiál neproudí správně do dutiny formy, může dojít k zachycení vzduchu.
- Nesprávná konstrukce brány: Pokud není brána správně navržena, může se v dutině formy zachytit vzduch.
- Nedostatečné odvětrávání: Pokud není plíseň řádně odvětrána, může se v její dutině zachytit vzduch.
Stopy po spálení vznikají, když je plastový materiál příliš dlouho vystaven vysokým teplotám, což způsobí jeho degradaci a viditelné stopy nebo změnu barvy na povrchu dílu. Stopy po vypálení mohou být způsobeny několika faktory, mezi které patří:
- Nadměrné teploty při zpracování: Pokud jsou nastaveny příliš vysoké teploty zpracování, může dojít k degradaci materiálu a vzniku spálenin.
- Nedostatečná doba chlazení: Pokud není díl řádně ochlazen, může dojít k degradaci materiálu a vzniku spálenin.
- Špatná konstrukce formy: Špatně navržená forma může způsobit, že materiál bude vystaven vysokým teplotám příliš dlouho, což může vést ke spáleninám.
Aby se minimalizovaly vzduchové pasti a spáleniny, je důležité optimalizovat podmínky zpracování a konstrukci formy a zavést správné postupy monitorování a údržby. Kromě toho může být nutné použít speciální techniky zpracování, jako je nízkoteplotní tvarování nebo vakuové tvarování, aby se minimalizovaly vzduchové pasti a spáleniny.
Zpracování pro výrobu vstřikovací formy:
Proces výroby vstřikovací formy zahrnuje několik kroků:
Design formy:
Konstrukce vstřikovací formy je kritickým aspektem procesu vstřikování, protože přímo ovlivňuje kvalitu, účinnost a náklady na vstřikované díly.
Dobře navržená vstřikovací forma bude vyrábět díly, které splňují požadované rozměry, tvar a požadavky na kvalitu, a zároveň bude efektivní na výrobu a snadná na údržbu.
Mezi klíčové faktory, které je třeba vzít v úvahu při návrhu vstřikovací formy, patří:
- Geometrie části: Konstrukce výlisku musí zohledňovat požadovanou velikost, tvar a vlastnosti dílu.
- Výběr materiálu: Materiál, který bude použit pro formu a výlisek, musí být vybrán na základě faktorů, jako je cena, pevnost a tepelná stabilita.
- Dutiny po plísních: Počet a uspořádání dutin formy je třeba zvolit tak, aby splňovaly požadavky na objem výroby.
- Systém brány: Konstrukce vtokového systému je velmi důležitá, protože určuje, jak plastový materiál proudí do dutiny formy.
- Vyhazovací systém: Vyhazovací systém musí být navržen tak, aby bylo možné vyjmout výlisky z formy bez poškození.
- Chladicí systém: Chladicí systém musí být navržen tak, aby zajistil rovnoměrné a rychlé chlazení výlisků, čímž se zkrátí doba cyklu a zlepší kvalita.
- Návrh úhlů pohledu: Konstrukce formy musí zahrnovat vhodné úhly ponoru, aby bylo možné vyjmout výlisky z formy.
- Odvětrávání: Forma musí být odvětrána, aby mohl vzduch unikat z dutiny formy, čímž se sníží riziko vzniku vzduchových pastí a popálenin.
- Údržba a opravy: Forma musí být navržena tak, aby se dala snadno udržovat a opravovat, aby se minimalizovaly prostoje a zvýšila efektivita výroby.
Konstrukce vstřikovacích forem je složitý proces, který vyžaduje odborné znalosti v oblastech, jako je strojírenství, věda o materiálech a výroba. Je důležité spolupracovat s renomovaným konstruktérem forem, aby bylo zajištěno, že forma bude navržena správně a bude splňovat vaše potřeby.
Programování CNC:
Programování CNC (Computer Numerical Control) je zásadním krokem při výrobě vstřikovací formy. Po dokončení návrhu formy je dalším krokem CNC programování. Níže jsou uvedeny hlavní kroky, které jsou součástí CNC programování pro výrobu vstřikovacích forem:
- Překlad modelu CAD: Model CAD je přeložen do programu CAM, který se používá k vytvoření CNC kódu pro formu.
- Tvorba kódu CNC: V programu CAM se vytváří CNC kód, který dává CNC stroji pokyny, jak pohybovat a řezat součásti formy. Kód zohledňuje materiál a tloušťku součástí formy, jakož i požadované tvary a prvky.
- Vytvoření dráhy nástroje: Dráha nástroje je vytvořena v programu CAM, který definuje dráhu, po níž bude řezný nástroj obrábět součásti formy. Dráha nástroje zohledňuje tvary a vlastnosti součástí formy a možnosti CNC stroje.
- Simulace: V programu CAM se simuluje kód CNC a dráha nástroje, aby se zajistilo, že součásti formy budou obráběny správně a podle správných specifikací.
- CNC obrábění: Kód CNC je nahrán do CNC stroje, který pak pomocí kódu a dráhy nástroje obrábí součásti formy.
Programování CNC je kritickým krokem v procesu výroby vstřikovacích forem, protože určuje přesnost a kvalitu součástí forem. Je důležité spolupracovat s programátorem CNC, který má zkušenosti s programováním vstřikovacích forem, aby bylo zajištěno, že kód CNC je vytvořen správně a podle správných specifikací. V tomto kroku se také do součástí formy přidávají chladicí kanály, vyhazovací systém a další prvky, aby se zajistilo jejich správné fungování.
Nákup seznamu kusovníků forem
Seznam kusovníku formy (BOM) je komplexní seznam všech komponent a materiálů potřebných k výrobě vstřikovací formy. Obsahuje následující položky:
- Ocel pro základnu formy a vložky jádra/dutiny
- Součásti horkého běhounu
- součásti chladicího systému, jako jsou vodní potrubí a chladicí bloky.
- Součásti vyhazovacího systému, jako jsou vyhazovací čepy a pouzdra.
- Součásti stahováku vtoků
- Topné pásy a regulátory teploty
- součásti formy, jako jsou pouzdra, vodicí kolíky a zajišťovací zařízení.
- Vložky do forem, jako jsou skluzavky a zvedáky.
- Speciální předměty, jako jsou razítka s datem a vlastní loga.
Seznam kusovníku formy je důležitým nástrojem pro zadávání zakázek a výrobu, protože poskytuje přehledný a podrobný seznam součástí a materiálů potřebných k výrobě formy. Používá se k zajištění toho, aby byly objednány všechny potřebné komponenty a byly po ruce, když je forma připravena k výrobě.
Při nákupu součástí vstřikovací formy je důležité spolupracovat s renomovaným dodavatelem, protože kvalita a spolehlivost těchto součástí může mít významný vliv na účinnost a kvalitu procesu vstřikování.
Hrubé obrábění forem:
Hrubé obrábění vstřikovací formy je počáteční obrábění ocelových součástí vstřikovací formy za účelem dosažení základního tvaru a velikosti formy. Tento krok se obvykle provádí pomocí strojů s počítačovým číslicovým řízením (CNC). Následují hlavní kroky hrubého obrábění vstřikovací formy:
- Výběr oceli: Prvním krokem je výběr vhodného typu oceli pro formu, například P20 nebo H13, na základě požadovaných vlastností výlisku.
- Řezání oceli: Ocel se řeže na CNC stroji na příslušnou velikost a tvar. Tento krok může zahrnovat také vrtání a závitování otvorů pro chladicí a vyhazovací systémy.
- Profilování oceli: Ocelové součásti se poté opracují tak, aby se dosáhlo základního tvaru formy, včetně jádra a vložek dutin.
- Kontrola oceli: Ocelové součásti se poté kontrolují, aby se zajistilo, že splňují požadované tolerance a specifikace.
- Čištění oceli: Obrobené součásti se očistí a odjehlí, aby se odstranily všechny hrubé hrany nebo nečistoty.
Proces hrubého obrábění je důležitým krokem v procesu vstřikování, protože vytváří základ pro konečné, vysoce přesné obrábění a leštění, které budou následovat. Je důležité zajistit, aby hrubé obrábění bylo provedeno přesně a podle správných specifikací, aby forma správně fungovala a vyráběla díly požadované kvality.
Tepelné zpracování formovací oceli:
Tepelné zpracování oceli formy je proces zahřívání a ochlazování ocelových součástí vstřikovací formy za účelem zlepšení jejich mechanických vlastností a rozměrové stability. Účelem tepelného zpracování je kalení oceli, uvolnění zbytkových napětí a zlepšení její odolnosti proti opotřebení a houževnatosti. Toto je speciálně pro kalenou ocel vstřikovací formy, pokud se k výrobě vstřikovací formy používá předem kalená ocel, není třeba provádět toto tepelné zpracování. Níže jsou uvedeny hlavní kroky při tepelném zpracování oceli formy:
- Žíhání: Ocelové součásti se zahřejí na určitou teplotu, obvykle v rozmezí 800-900 °C, a poté se pomalu ochladí, aby se uvolnilo vnitřní pnutí a zlepšila se obrobitelnost oceli.
- Zpevnění: Ocelové součásti se zahřejí na vysokou teplotu, obvykle nad kritickou teplotu, a poté se rychle ochladí, obvykle kalením v oleji nebo ve vodě. Tento proces kalí ocel a zvyšuje její odolnost proti opotřebení.
- Kalení: Po kalení se ocelové součásti po určitou dobu zahřívají na nižší teplotu, aby se zlepšila houževnatost a rozměrová stálost oceli.
Proces tepelného zpracování je rozhodující pro zajištění požadovaných mechanických vlastností a rozměrové stability ocelových součástí vstřikovací formy, které jsou nezbytné pro výrobu vysoce kvalitních výlisků. Je důležité spolupracovat s poskytovatelem tepelného zpracování, který má zkušenosti s úpravou oceli forem, aby bylo zajištěno, že proces tepelného zpracování proběhne správně a podle správných specifikací.
Jemné opracování dutiny formy a jádra:
Jemné obrábění dutiny formy a jádra je proces přesného obrábění vnitřních povrchů dutiny formy a vložek jádra za účelem dosažení konečného tvaru a velikosti formy. Tento krok se obvykle provádí pomocí strojů s počítačovým číslicovým řízením (CNC) s vysokou přesností a precizností. Níže jsou uvedeny hlavní kroky, které jsou součástí jemného obrábění dutiny formy a jádra:
- Příprava povrchu: Povrch dutiny formy a jádrových vložek se očistí a vyleští, aby se odstranily zbytky nečistot nebo nerovnosti.
- Povrchové obrábění: Vnitřní povrchy dutiny formy a vložek jádra se obrábějí na CNC strojích, aby se dosáhlo konečného tvaru a velikosti formy. To zahrnuje vytvoření složitých detailů a prvků výlisku, jako je text, loga a podříznutí.
- Povrchová kontrola: Obrobené povrchy se kontrolují, aby se zajistilo, že splňují požadované tolerance a specifikace.
- Leštění povrchu: Vnitřní povrchy dutiny formy a vložek jádra jsou leštěny do vysoké kvality, aby se zlepšila kvalita povrchu výlisků a snížilo riziko vzniku vad.
Jemné obrábění je kritickým krokem v procesu vstřikování, protože určuje kvalitu a přesnost vstřikovaných dílů. Je důležité spolupracovat s poskytovatelem obrábění, který má zkušenosti s jemným obráběním dutin forem a jader, aby bylo zajištěno, že obrábění bude provedeno správně a podle správných specifikací. V tomto kroku se také přidává vyhazovací systém formy, chladicí kanály a další prvky, které zajišťují správnou funkci formy.
obrábění elektroerozivním obráběním:
Elektroerozivní obrábění (EDM) je proces používaný k vytváření složitých a velmi přesných tvarů kovových dílů, včetně dílů ve vstřikovací formě. Tento proces využívá elektrické jiskry k odstranění materiálu z povrchu formy a vytvoření požadovaného tvaru. Následují hlavní kroky při obrábění elektroerozivním obráběním:
- Příprava povrchu: Povrch obráběné součásti formy se očistí a vyleští, aby se odstranily zbytky nečistot nebo nerovnosti.
- Nastavení EDM: Na základě materiálu a tvaru součásti formy se EDM stroj nastaví se správnými parametry, včetně jiskřiště, délky impulsu a materiálu elektrody.
- Jiskrová eroze: EDM stroj vytváří elektrické jiskry, které odstraňují materiál ze součásti formy a vytvářejí požadovaný tvar. Tento proces probíhá postupně, přičemž EDM stroj postupně eroduje materiál, dokud není dosaženo konečného tvaru.
- Povrchová kontrola: Obrobený povrch se kontroluje, aby se zajistilo, že splňuje požadované tolerance a specifikace.
Obrábění elektroerozivním obráběním se často používá pro součásti forem, které mají složité tvary nebo malé, komplikované detaily, které jsou obtížně dosažitelné jinými obráběcími procesy. Používá se také k výrobě ostrých hran a rohů, které jsou nezbytné pro správnou funkci vstřikovací formy.
Tento proces je velmi přesný a precizní, takže je ideální pro výrobu vysoce kvalitních výlisků. Je důležité spolupracovat s dodavatelem, který má zkušenosti s obráběním vstřikovacích forem elektroerozivním obráběním, aby bylo zajištěno, že proces bude proveden správně a podle správných specifikací.
Leštění povrchu formy:
Leštění vstřikovacích forem je posledním krokem výrobního procesu vstřikovací formy. Zahrnuje vyhlazení povrchů součástí formy, aby byl zajištěn hladký a rovný povrch hotového výrobku. Následují hlavní kroky při leštění vstřikovacích forem:

leštění plastových forem
- Příprava povrchu: Povrchy součástí formy se očistí a připraví k leštění. Odstraní se všechny zbývající nerovnosti nebo stopy po obrábění, aby se zajistil hladký povrch pro leštění.
- Hrubé leštění: Prvním krokem leštění je hrubé leštění, které spočívá v odstranění všech velkých nedokonalostí povrchu součástí formy. Tento krok se obvykle provádí brusným papírem hrubé zrnitosti, například smirkovým papírem nebo brusným kartáčem.
- Jemné leštění: Dalším krokem je jemné leštění, které zahrnuje vyhlazení povrchu součástí formy na jemnější povrch. Tento krok se provádí pomocí brusiva jemnější zrnitosti, například jemnějšího brusného papíru nebo brusného kartáče.
- Broušení: Při leštění se používá lešticí kotouč a lešticí hmota k dosažení vysokého lesku na součástech formy.
- Kontrola: Po vyleštění jsou součásti formy důkladně zkontrolovány, aby se zajistilo, že mají hladký a rovný povrch bez škrábanců, prasklin nebo jiných nedokonalostí.
Leštění vstřikovacích forem je důležité, protože ovlivňuje kvalitu konečného výrobku. Výsledkem dobře vyleštěné formy je výrobek s hladkým a rovným povrchem, což je důležité pro funkčnost a estetiku výrobku. Je důležité spolupracovat se zkušeným leštičem forem, aby bylo zajištěno, že součásti formy budou vyleštěny podle správných specifikací a na požadované úrovni kvality.
Montáž formy
Montáž forem je specializovaná práce v oblasti vstřikování plastů, která zahrnuje montáž, instalaci a testování vstřikovacích forem. Mistři forem jsou zodpovědní za to, že součásti formy jsou správně sestaveny a fungují správně a že forma vyrábí díly s požadovanou kvalitou a výkonnostními standardy. Mezi hlavní povinnosti montérů forem patří např:
- Sestavení součástí formy: Mistr formy je zodpovědný za sestavení různých součástí vstřikovací formy, včetně dutiny a jádra, vtokového systému a všech pomocných součástí.
- Instalace formy na montážní stroj: Pokud nemá žádný stroj na montáž forem, pak použijte ruční způsob montáže formy, což dělá většina společností.
- Testování formy: Mistr formy je zodpovědný za testování formy, aby bylo zajištěno, že forma vyrábí díly s požadovanou kvalitou a výkonnostními standardy. To zahrnuje kontrolu dílů na případné vady, jako je deformace, smrštění nebo jiné problémy s kvalitou.
- Nastavení formy: Pokud se během testovací fáze zjistí nějaké problémy, je moldmaster zodpovědný za provedení nezbytných úprav formy, aby se zajistilo, že bude vyrábět díly, které splňují požadované specifikace.
- Řešení problémů: Musí být schopen identifikovat a řešit problémy, které se mohou vyskytnout během procesu montáže formy.
Práce při montáži forem vyžaduje kombinaci technických znalostí, manuální zručnosti a pozornosti k detailům. Montéři forem musí být schopni pracovat se širokou škálou nástrojů a strojů a rozumět složitým procesům vstřikování plastů. Pro montéry forem je důležité, aby dobře rozuměli procesu vstřikování plastů a měli zkušenosti s prací s různými typy forem a materiálů.
První zkouška vstřikování nebo střelba:
Zkušební vstřikování se týká procesu testování vstřikovací formy pro výrobu vzorového dílu pomocí vstřikovacího procesu. Tento proces je kritickým krokem v procesu vstřikování, protože umožňuje výrobci vyhodnotit výkon formy a provést případné úpravy před výrobou velkého množství dílů.
Proces zkušebního vstřikování obvykle zahrnuje následující kroky:
- Příprava: Forma se nainstaluje na vstřikovací stroj a stroj se nastaví na výstřik. Zásobník se naplní plastovou pryskyřicí.
- Regulace teploty taveniny: Teplota taveniny je řízena tak, aby se plastová pryskyřice zahřála na správnou teplotu, která umožní výrobu vysoce kvalitních dílů.
- Injekce: Tavenina plastu se vstřikuje do formy pod vysokým tlakem. Tlak se udržuje, dokud není forma naplněna plastovou pryskyřicí.
- Chlazení: Forma se ochladí, aby plastová pryskyřice ztuhla a vytvořila díl. Doba chlazení závisí na typu použité plastové pryskyřice a na velikosti a tvaru vyráběného dílu.
- Vyhazování: Po ztuhnutí je díl vyjmut z formy. K vytlačení dílu z formy se používají vyhazovací kolíky.
- Kontrola: Díl vyrobený z formy je důkladně zkontrolován, aby se zajistilo, že splňuje požadované specifikace a normy kvality.
- Úpravy: V případě potřeby lze provést úpravy procesu vstřikování, aby se zlepšila výkonnost formy a kvalita vyráběných dílů.
Proces zkušebního vstřikování je důležitým krokem v procesu vstřikování, protože umožňuje výrobci vyhodnotit výkon formy a provést případné úpravy před výrobou velkého množství dílů. Tento proces pomáhá zajistit, aby forma vyráběla vysoce kvalitní díly s požadovanými specifikacemi.
Balení formy a připravenost k výrobě:
Jakmile je forma zcela dokončena výrobcem forem, následuje masivní výroba. Balení formy a příprava na výrobu je posledním krokem v procesu vstřikování před zahájením hromadné výroby. Tento krok zahrnuje následující úkoly:
- Čištění a údržba: Forma je důkladně vyčištěna a zkontrolována, aby se zajistilo, že na ní nejsou žádné nečistoty, úlomky nebo poškození.
- Balení a skladování: Forma je pečlivě zabalena a uložena na bezpečném místě, aby se zabránilo jejímu poškození a aby byla připravena k použití v případě potřeby.
- Testování a nastavení: Forma se otestuje na případné problémy, jako jsou netěsnosti, špatné plnění nebo nesprávné vyhazování dílů, a provedou se případné úpravy, aby se zajistila správná funkce formy.
- Nastavení výroby: Forma se nainstaluje do vstřikovacího stroje a všechna potřebná nastavení, jako je teplota, tlak a rychlost vstřikování, se upraví tak, aby splňovala konkrétní výrobní požadavky.
- Zahájení výroby: Je vyrobena první dávka dílů a proces je monitorován, aby bylo zajištěno, že díly splňují požadované specifikace a normy kvality. Provedou se veškeré nezbytné úpravy, aby se optimalizoval výrobní proces a zajistila se stálá kvalita.
Příprava formy pro výrobu je celkově důležitým krokem v procesu vstřikování, který pomáhá zajistit úspěch a efektivitu výroby.
Výše uvedené informace jsou postupy pro výrobu vstřikovací formy, možná tam jsou některé malé věci vynechal, ale většina věcí jsou výše, jak můžete vidět, že vstřikovací formy není snadný případ, pokud máte vstřikovací formy projekt v rukojeti, musíte najít profesionální vstřikovací formy výrobce, aby vám služby, to bude ujistěte se, že váš projekt běží úspěšně.
Sincere Tech je profesionální Čínská forma továrna specializující se na výrobu vstřikovacích forem na zakázku. Má zkušenosti a odborné znalosti v oblasti návrhu, vývoje a výroby vysoce kvalitních vstřikovacích forem pro různá průmyslová odvětví a aplikace.
Poskytují celou řadu služeb, včetně návrhu forem, výroby prototypů, výroby forem a následného zpracování, aby zajistili, že jejich zákazníci získají nejlepší možné výsledky. Díky svému zaměření na kvalitu, přesnost a spokojenost zákazníků je společnost Sincere Tech spolehlivým a důvěryhodným partnerem pro všechny vaše potřeby v oblasti vstřikování plastů. Kontaktujte nás a získejte e cenu pro váš projekt hned teď.