What is POM injection molding?
POM injection molding or acetal injection molding, is a process for creating parts by injecting molten POM (Polyoxymethylene) material into a mold, where it cools and solidifies. POM is a thermoplastic polymer that is commonly used in precision parts such as gears, bearings, and electrical components due to its high strength, stiffness, low friction properties, mechanical and chemical properties, especially excellent rub resistance.
The POM injection molding process allows for the creation of complex and precise shapes with high dimensional accuracy and repeatability. POM (also called Acetal) is polymerized by formaldehyde and other raw materials, etc. POM-H (Polyoxymethylene homopolymer), POM-K(Polyoxymethylene copolymer) are thermoplastic engineering plastic with high density and crystallinity.
POM Injection Molding is a crystalline plastic with an obvious melting point. Once it reaches the melting point, the melt viscosity will rapidly decrease. When the temperature exceeds a certain limit or the melt is heated too long, it will cause decomposition. Copper is POM’s degradation catalyst, the areas contacting with POM melt should avoid the use of copper or copper materials.
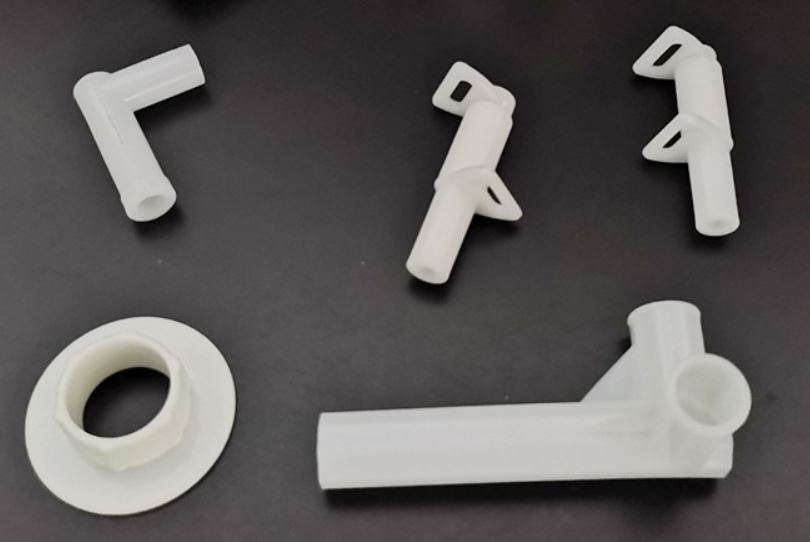
POM injection molding
Advantages of POM injection molding
POM injection molding offers several advantages over other manufacturing processes. Some of the main advantages of POM injection molding are:
- High strength and stiffness: POM is a highly durable and rigid engineering plastic that provides exceptional strength and stiffness, making it ideal for applications that require high strength and resistance to wear and tear.
- Excellent dimensional stability: POM has excellent dimensional stability, which means that it maintains its shape and size even under high temperatures or mechanical stresses. This makes it a popular choice for precision engineering and high-tolerance applications.
- Good chemical resistance: POM has good resistance to many chemicals, including solvents, fuels, and oils. This makes it suitable for use in applications where exposure to chemicals is expected.
- High heat resistance: POM has a high heat deflection temperature, which means that it can withstand high temperatures without deforming or losing its mechanical properties.
- Low friction and wear resistance: POM has a low coefficient of friction, which makes it an excellent choice for applications that require low friction and wear resistance, such as gears and bearings.
- Easy to mold: POM is easy to mold using injection molding techniques, which allows for the creation of complex geometries and intricate designs with high precision.
- Cost-effective: POM injection molding is a cost-effective manufacturing process that allows for high-volume production runs with consistent quality and minimal waste. This makes it a popular choice for mass production of plastic components.
Disadvantages of POM injection molding
Although POM injection molding offers many advantages, there are also some disadvantages to consider. Some of the main disadvantages of POM injection molding include:
- Susceptible to stress cracking: POM is susceptible to stress cracking when exposed to certain chemicals, such as strong acids, bases, and some solvents. This can result in premature failure of the molded parts.
- Limited color options: POM is naturally white, and it can be difficult to achieve vibrant colors during the injection molding process. This may limit the aesthetic appeal of the final product.
- High processing temperature: POM requires a high processing temperature during injection molding, which can result in higher energy consumption and longer cycle times.
- Poor UV resistance: POM has poor resistance to UV radiation, which can cause it to degrade and lose its mechanical properties over time when exposed to sunlight or other sources of UV radiation.
- Brittleness at low temperatures: POM becomes brittle at low temperatures, which can make it unsuitable for applications where low-temperature resistance is required.
- Environmental concerns: POM is not biodegradable, and it can take hundreds of years to break down in the environment. This may be a concern for applications where sustainability and environmental impact are important considerations.
- Tooling costs: The production of high-quality POM injection molds can be expensive, particularly for complex geometries and intricate designs, which can increase the overall cost of the manufacturing process.
Types of POM Plastic Injection Molding
Type | Characteristics | Applications |
Homopolymer POM (POM-H) | High crystallinity, excellent mechanical properties, may be susceptible to stress cracking | Gears, pulleys, bushings |
Copolymer POM (POM-C) | Improved impact resistance and stress crack resistance | Automotive parts, consumer goods |
Reinforced POM | Enhanced mechanical properties, such as strength, stiffness, and heat resistance | Structural components, automotive parts, industrial machinery |
Flame-Retardant POM | Improved fire resistance | Electrical connectors, building materials |
Food-Grade POM | Meets food safety standards | Food processing equipment, containers, packaging materials |
Medical-Grade POM | Meets biocompatibility and sterilization requirements | Surgical instruments, prosthetics, medical components |
Conductive POM | Improved electrical conductivity | Electrical connectors, EMI shielding, electronic components |
Low-Friction POM | Very low coefficient of friction | Bearings, bushings, moving parts |
High-Temperature POM | Can withstand higher temperatures | Automotive under-the-hood components |
Color-Pigmented POM | Imparts color or opacity | Consumer goods, automotive trim |
Chemical Structure and Properties:
- POM is a crystalline polymer composed of rehashing formaldehyde units. This chemical structure gives a few alluring properties:
High Quality and Firmness: POM shows amazing ductile and flexural quality, making it appropriate for applications requiring strong mechanical execution.
Dimensional Steadiness: POM has moo dimensional float and fabulous crawl resistance, guaranteeing exact resistances and long-term unwavering quality.
Fatigue Resistance: The material’s weakness quality is tall, permitting it to withstand rehashed loads without disappointment.
Chemical Resistance: POM is safe to an assortment of chemicals, counting aliphatic hydrocarbons, alcohols, and numerous solvents.
Low Coefficient of Grinding: POM has an actually moo coefficient of contact, making it a great choice for moving parts and orientation.
Good Wear Resistance: Its scraped area resistance is tall, guaranteeing long benefit life in applications subject to wear and tear.
Excellent Machinability: POM is simple to machine, permitting for complex shapes and exact resiliencies.
Tips working with POM injection molding.
- Processing of plastic POM
POM has low water absorption which generally is 0.2%-0.5%. Under normal circumstances, POM can be processed without drying, but the wet raw material must be dried. The drying temperature is above 80 Celsius degree, the drying time is above 2-4 hours which should be conducted according to the supplier’s datasheet. The utilization of recycled materials is generally within 20-30%. However, it depends on the species and final use of products; sometimes it can reach 100%. - Selection of injection molding machine
In addition to the requirement on the screw with no material banking zone, there is no special requirement on the injection molding machine; the general injection molding is available. - Design of mold and gate
During the POM injection molding process. The common mold temperature is controlled 80-90 Celsius degree, the diameter of flow channel is 3-6mm, the length of gate is 0.5mm, the size of gate depends on the thickness of plastic wall, the diameter of circular gate should be at least 0.5-0.6 times of the thickness of the products, the width of the rectangular gate is usually 2 times or more of its thickness, depth is 0.6 times of the wall thickness, stripping slope is between40′ and 1-30.
Mold Exhaust System-air venting grooves for POM
POM-H the thickness is 0.01-0.02mm and the width is 3mm.
POM-K the thickness is 0.04 mm and the width is 3mm
- Melt temperature
You can use air injection method to measure the temperature.
POM-H it can be set to 215 Celsius degree(190 -230 Celsius degree)POM-Kit can be set to 205 Celsius degree(190 -210 Celsius degree). - Injection speed
The common is middle speed which is a little fast, too slow speed is easy to produce corrugation, too fast speed is easy to produce ray lines and shear overheating. - Packing
It’s better to be lower for packing. Generally, it does not exceed 200bar. - Dwell time
If the device doesn’t have melt retention point,
POM-H In the temperature of 215 Celsius degree, the retention time is 35 minutes.
POM-K In the temperature of 205 Celsius degree, the retention time of 20 minutes will not have serious decomposition.
In the temperature of POM injection molding, the molt material cannot be stranded in the barrel for more than 20 minutes. POM-K can strand 7minutes in the 240 Celsius degree. If in the downtime, the temperature can decrease to 150 Celsius degree, if the downtime is for a long time, you must clean the barrel, turn off the heater.
- Downtime
You must use PE or PP to clean the barrel, turn off the heater and push the screw frontier area, keep the barrel and screw clean. Impurities or dirt will change the superheating stability of POM (particularly POM-H). So after exhausting the halogen-containing polymer or another acidic polymer, you should use PE to clean up and then Play PM material, or it will cause an explosion. If you use improper pigments, lubricants or GF nylon materials, it will cause the plastic degradation. - Post-processing
For the POM products used in non-normal temperature, there are higher requirements on quality; it needs to make heat treatment.
The annealing treatment effect is checked by immersing products in a hydrochloric acid solution of concentration 30% for 30 minutes, and then uses eyes observing and determining whether there are residual stress cracks.
Application of POM injection molding parts
POM injection molding parts are used in a wide range of applications across various industries. Some of the most common applications of POM injection molding parts include:
- Automotive industry: POM parts are widely used in the automotive industry for applications such as fuel systems, engine components, and interior trim parts due to their high strength, stiffness, and excellent wear resistance.
- Electrical and electronics industry: POM parts are commonly used in the electrical and electronics industry for applications such as switches, connectors, and housing components due to their excellent dimensional stability and low friction.
- Consumer goods industry: POM parts are used in the manufacturing of consumer goods such as toys, sporting equipment, and household appliances due to their durability, resistance to chemicals, and ease of processing.
- Medical industry: POM parts are used in the medical industry for applications such as surgical instruments and medical devices due to their high strength, stiffness, and resistance to sterilization.
- Industrial machinery: POM parts are commonly used in industrial machinery for applications such as gears, bearings, and other components that require low friction and wear resistance.
- Aerospace industry: POM parts are used in the aerospace industry for applications such as fuel system components, valve seats, and hydraulic system components due to their high strength and resistance to wear and tear.
POM injection molding parts are used in applications where high strength, stiffness, wear resistance, and dimensional stability are required, making them a popular choice across a wide range of industries.
The injection molding processing technology of POM
The injection molding process parameter for POM material will depend on several factors such as the specific grade of POM, the design and geometry of the part, and the injection molding machine being used. However, here are some general guidelines for injection molding parameters for POM material:
- Injection temperature: The recommended injection temperature for POM material is typically between 170°C to 230°C (338°F to 446°F), depending on the grade of POM.
- Mold temperature: The recommended mold temperature for POM material is typically between 60°C to 100°C (140°F to 212°F), depending on the grade of POM and the complexity of the part.
- Injection pressure: The recommended injection pressure for POM material is typically between 60 MPa to 140 MPa (8700 psi to 20300 psi), depending on the grade of POM and the size and complexity of the part.
- Injection speed: The recommended injection speed for POM material is typically between 50 to 100 mm/s (1.97 to 3.94 in/s), depending on the grade of POM and the size and complexity of the part.
- Holding pressure and time: The recommended holding pressure for POM material is typically between 50% to 70% of the injection pressure, depending on the grade of POM and the size and complexity of the part. The recommended holding time is typically between 10 to 30 seconds.
It’s important to note that these are general guidelines, and the optimal injection molding parameters for POM material may vary depending on the specific requirements of the application and the processing conditions. Therefore, it’s important to consult with the POM material supplier and the injection molding machine manufacturer to determine the appropriate injection molding parameters for your specific application.
POM injection molding parts has been used in various of industry and has very sensitive molding process. Sincere Tech is professional in POM injection molding process, if you have a project that needs POM injection molding parts, contact us to get a price.