Plastic Mold China is a major supplier of custom plastic molds due to its relatively low labor costs and strong manufacturing infrastructure. Many global companies source their plastic molding needs from China, taking advantage of the country’s capabilities in mold design, engineering, and production.
Mold-produced gifts are of vital value throughout a wide variety of industries. Bringing on a China mold maker can simplify the process for all of the companies in the world. Plastic mold Manufacturers in China is a topic that has piqued the interest of major companies. However, when businesses aim to compete in their respective markets, they must consider the fundamentals of the method itself.

Why you should use plastic mold China service?
There are several reasons why companies choose to use the Plastic Mold China service:
- Cost-effective: Labor costs in China are lower compared to other countries, making plastic molding services more affordable. This results in significant cost savings for companies that source their plastic molding needs from China.
- Experienced workforce: China boasts a vast pool of skilled and experienced workers, particularly in the plastic mold industry. The experienced workforce guarantees the production of plastic molds that meet the highest quality and precision standards.
- Advanced technology: Chinese mold manufacturers have access to and invest in the latest technology and equipment, including computer-aided design (CAD) and computer-aided manufacturing (CAM) systems. This allows them to produce high-quality molds with intricate designs and precise dimensions.
- Large production capacity: China is one of the largest producers of plastic molds in the world, with the ability to handle large-scale production runs. This means that companies can meet their high-volume plastic molding needs in a timely and efficient manner.
- Strategic location: China is a global manufacturing hub, and its proximity to other Asian countries makes it an ideal location for companies looking to source their plastic molding needs. This also allows for simple and efficient transportation of finished products to other markets.
- Quality control: Many Chinese mold companies have strict quality control processes in place, ensuring that the finished products meet the highest standards of quality. This helps companies ensure that they receive consistent, high-quality plastic molds that meet their specific requirements.
The combination of cost-effectiveness, experienced workforce, advanced technology, large production capacity, strategic location, and quality control makes plastic molding services in China a cost-effective and efficient solution for companies looking to produce plastic parts at scale.

These factors make the Plastic Mold China service a cost-effective and efficient solution for companies looking to produce plastic parts at scale.
Sincere Tech is a China plastic injection molding company. We offer custom plastic mold and injection molded products to America, Europe, and the world. If you have a project in hand that needs plastic mold China companies to help you, simply send us your part design or sample pictures, and we will send you the best price and solutions for your project.
We guarantee we will never copy or share your data with any other third parties. We can sign an NDA (non-disclosure agreement) contract to protect your project.
Plastic injection molding is one of the emergent commodities available on the market. The generation has the facility to create merchandise that may be difficult to create. To sculpt molds correctly, machines must be optimized.
China mold manufacturing companies are currently working with a wide array of industries the world over. This has helped China mold makers establish themselves as a global standard. Engaging with those outside industries will be a highly effective strategy for expanding the current supply line.
Some industrial owners are interested in purchasing a variety of custom plastic products from Chinese plastic mold companies. These mold makers typically specialize in manufacturing various plastic components.
Knowledge within the industry could help piece these together. Some business owners are capable of assembling these items independently. Others might want to hire a workforce to regulate this process from beginning to end.
Plastic Mold China has created a very powerful variable for the bottom line that companies need to understand. Many people are eager to follow the blueprints these manufacturers create.
They’re going to be keen to show off their manufacturing procedure when they sign up for a freelance deal. Those deals will usually remain for a time frame, giving owners a chance to evaluate the process itself.
The mold manufacturing industry is capable of handling certain tasks exclusively. A few mold manufacturing companies in China offer exclusive deals to attract business owners. Viewing a gallery of projects will give customers a chance to understand what they’re dealing with.
The injection plastic mold industry in China has been instrumental in helping some overseas companies reinvent themselves. For instance, if you have been conducting market research on a new project for a year or more, you may discover that it has the potential to be a significant global market.
Once your design and prototype testing are complete, you should seek a contract manufacturer to produce your new model. While they may have numerous components to source, your first step should be to identify a plastic mold company and inquire about their assembly service offerings.
Sincere Tech is one of the top 10 mold manufacturers in China. We offer custom plastic mold/molding service, die casting parts service, painting, chrome, spray, and assembly—all in one service here to support you.

The advantages of choosing Sincere Tech as your China Plastic mold Maker
Sincere Tech supplies many kinds of injection molds, injection molding parts, plastic materials, and several plastic molding technologies based on the customer’s requirements. The R&D department takes the responsibility of analyzing and designing the plastic parts according to the needs of the clients. The project department of the company will perform the foreseen inspection of plastic parts moldings structure, process, and related parts situation. The analysis is also done by the professionals to determine whether the moldings are manufactured according to the design.
Sincere Tech will prepare a professional mold flow analysis report for all molds prior to manufacturing, which will include temperature control, gate assignment, cooling time, and an analysis of the injection process, all of which will enhance the mold design.
The project manager is responsible for the outline process, precision machining, rough machining, machine process, assembly inspection, colliding, and assembly and molding tests. The project manager conducts a molding test to verify the dimensions of the injection molding parts and their alignment with the corresponding parts. The company’s Quality Control (QC) department will inspect the plastic parts mold, focusing on the product size, injection process, appearance, and physical performance.
Sincere Tech will measure all dimensions using a CMM machine, and will also conduct numerous tests to ensure the product can withstand pressure, tensile strength, impulse loading, temperature resistance, and impact resistance. The company applies its abundant experience in producing plastic part moldings to ensure the customers receive products of superior quality.
We subject the plastic parts to various surface treatments to ensure they have an excellent shape that aligns with the customers’ needs. According to the order documents, the company will perform a strict inspection before the shipping of the products. If you are interested in learning more about injection molding parts, or if you have a project that requires an injection mold manufacturing company in China to support the production of injection molds and injection molding parts, feel free to send us your Request for Quotation (RFQ). We will provide you with a quote within two working days.
Our engineers speak fluent English and possess extensive technical experience, ensuring that all issues are resolved after the initial mold trial. The technical specialist oversees the project from start to finish. Most of our project is approved by the customers after the first samples are received; all of these successes are credited to our professional team.
Are you seeking a China injection mold company for plastic molds? Send us an email to get a price. Call us to discuss your project.
What is plastic injection mold press
Plastic injection mold press is simple called press. Plastic injection mold press holds the plastic mold in which the components are shaped. Mold press is rated by tonnage, which expresses the amount of clamping force that the machine can generate. This pressure keeps the mold closed during the injection process. Tonnage can vary from less than 5 tons and big than 5000 tons, with the higher figures used in comparatively few manufacturing operations.
Plastic injection mold press can fasten the plastic molds in either a horizontal or vertical position. The majority is horizontally oriented, but vertical machines are used in some niche applications such as insert molding ( click here to know more about insert molding) allowing the machine to take advantage of gravity.
Plastic injection mold press is used to create many things such as milk cartons, packaging, bottle caps, automotive dashboards, pocket combs, and most other plastic products available today. It is known that injection molding is the most common method of part manufacturing. It is ideal for producing high volumes of the same object. Go to injection molding page to know more about injection moulding.
Basic Components of a Plastic Injection Mold Press
The basic components of a Plastic Injection Mold Press are integral to its functionality, contributing to the precision and efficiency of the injection molding process. Sincere Tech China Mold Maker, a prominent player in the industry, understands the significance of each component in delivering top-notch manufacturing solutions. Let’s delve into the essential elements that constitute a Plastic Injection Mold Press:
1. Injection Unit:
- Hopper:
- The hopper serves as the reservoir for raw plastic material. Sincere Tech ensures that the hopper design facilitates efficient material loading and prevents contamination.
- Barrel:
- Within the barrel, the plastic material is subjected to controlled heating and pressurization. Sincere Tech’s barrels are designed for optimal heat transfer and durability, ensuring uniform melting of the plastic.
- Screw or Plunger:
- The screw or plunger is responsible for conveying the molten plastic material from the barrel to the mold. Sincere Tech’s precision-engineered screws and plungers ensure a consistent and reliable injection process.
2. Clamping Unit:
- Mold:
- The mold defines the shape and features of the final product. Sincere Tech specializes in custom mold designs, tailored to the specific requirements of clients across diverse industries.
- Clamping Mechanism:
- The clamping mechanism ensures that the mold remains securely closed during the injection process. Sincere Tech’s robust clamping systems guarantee stability and accuracy in the molding process.
- Cooling System:
- Efficient temperature control is critical for the solidification of the plastic within the mold. Sincere Tech integrates advanced cooling systems to maintain precise temperature levels, contributing to the overall quality of the molded products.
These components work seamlessly together during the injection molding process, reflecting Sincere Tech’s commitment to excellence in every facet of Plastic Injection Mold Press technology. Their attention to detail in the design and manufacturing of these components ensures that clients receive reliable and high-performance machinery for their production needs.
Advantages of Plastic Injection Mold Press
Sincere Tech China Mold Maker’s Plastic Injection Mold Press technology comes with a multitude of advantages, positioning it as a preferred choice for manufacturers seeking precision, efficiency, and versatility. Here are the key advantages associated with Plastic Injection Mold Press:
1. High Precision and Accuracy:
- Sincere Tech’s Plastic Injection Mold Press technology excels in producing intricate and complex designs with exceptional precision. The advanced control systems and precise engineering contribute to the consistent replication of detailed molds, meeting the strictest quality standards.
2. Efficient Production Rates:
- The efficiency of Sincere Tech’s Plastic Injection Mold Press technology translates into high production rates. Rapid injection cycles, coupled with reliable and durable components, ensure that manufacturers can meet demanding production schedules and reduce time-to-market for their products.
3. Versatility in Material Usage:
- Sincere Tech understands the importance of material flexibility in manufacturing. Their Plastic Injection Mold Press technology accommodates a wide range of materials, from traditional polymers to advanced engineering plastics. This versatility enables clients to choose the most suitable material for their specific application.
4. Reduced Material Waste:
- Precision control over the injection process minimizes material waste. Sincere Tech’s technology ensures that the right amount of material is injected into the mold, reducing excess and optimizing resource utilization. This commitment to sustainability aligns with global environmental goals.
5. Cost-Effectiveness:
- The efficiency and accuracy of Sincere Tech’s Plastic Injection Mold Press technology contribute to cost-effectiveness in manufacturing. Reduced waste, faster production cycles, and reliable operation result in overall cost savings for clients.
6. Scalability:
- Whether dealing with small-scale production or large-volume manufacturing, Sincere Tech’s Plastic Injection Mold Press technology is scalable to meet varying production needs. This scalability is crucial for adapting to market demands and business growth.
7. Consistent Quality Control:
- Sincere Tech places a strong emphasis on quality control throughout the manufacturing process. The precise control mechanisms in their Plastic Injection Mold Press technology ensure consistent product quality, minimizing defects and rejections.
8. Tailored Solutions for Diverse Industries:
- Sincere Tech’s expertise allows them to provide tailored solutions for diverse industries, including automotive, consumer goods, medical devices, and packaging. Their understanding of industry-specific requirements ensures that clients receive customized solutions that align with their unique needs.
In essence, Sincere Tech China Mold Maker’s Plastic Injection Mold Press technology offers a comprehensive package of advantages, making it a reliable and efficient choice for manufacturers seeking excellence in plastic injection molding processes.
Types of Plastic Injection Mold Press
Sincere Tech China Mold Maker offers a range of Plastic Injection Mold Press technologies, each catering to specific needs and preferences. Here are the primary types of Plastic Injection Mold Press provided by Sincere Tech:
1. Hydraulic Injection Mold Press:
- Description: Hydraulic injection mold presses utilize hydraulic systems to power the various components of the machine. These systems provide high force and are known for their robustness.
- Advantages:
- High clamping force suitable for large molds.
- Versatility in handling a variety of materials.
- Reliable and durable, with lower maintenance requirements.
2. Electric Injection Mold Press:
- Description: Electric injection mold presses rely on electric servo motors to drive the machine’s components. This type is appreciated for its precision, energy efficiency, and accuracy.
- Advantages:
- Higher energy efficiency and reduced operating costs.
- Enhanced precision and control over the injection process.
- Quieter operation compared to hydraulic counterparts.
3. Hybrid Injection Mold Press:
- Description: Hybrid injection mold presses combine hydraulic and electric systems to optimize performance. They often use electric motors for plasticizing and hydraulic systems for clamping.
- Advantages:
- Balances the energy efficiency of electric systems with the power of hydraulic systems.
- Provides flexibility in adapting to different production requirements.
- Offers improved precision in injection molding processes.
Sincere Tech China Mold Maker excels in delivering these types of Plastic Injection Mold Press machines, ensuring that clients have the flexibility to choose the technology that best suits their specific production needs. The company’s commitment to innovation and customization enables them to stay at the forefront of the industry, meeting the evolving demands of various manufacturing sectors.
If you are a plastic mold manufacturing company that produces anything from plastic molding toys to car parts and you are not using Plastic injection mold press to produce your parts, you will spend too much money. Indeed, using Plastic injection mold press provides additional savings to manufacturers because plastic is less expensive than metal and manufacturers pay for fewer parts. As a result, they are widely used because of the high quality of the end product.
One of Plastic injection mold press you can choose in the market is Plastic Injection Molder (YS-1180). This machine has moving platen featuring box type bridge structure and full-connected rear high-rigidity mold platen. Through finite element analysis, it can prevent deforming of mold platen, resist against fatigue, have high repetition accuracy, distribute mold closing force uniformly, greatly increase mold’s service life and reduce injection molding cost.
Another option of Plastic injection mold press is HDT-200 200ton plastic injection molder. This machine comes in two series; HDT series and HDF series. The HDT machines’ clamping force is from 80 tons to 2200 tons and the shot weight is from 80g to 2kg. These machines have strong locking force and a very good injection precise also a stable performance etc.
Meanwhile, the HDF machines are a type of high-speed Plastic injection mold press. The machine’s cycle time is very short (2.6 seconds-3.6 seconds) with a high injection pressure (to be possible to reach 240MPA) and a high-speed injection (to be possible to reach 600MM/S). This machine can be used to produce the thin-wall products, especially the thin-wall snack boxes and containers (with the wall thickness of 0.4mm).
Or you can choose another option among other Plastic injection mold press available in the market. Just choose the one based on your needs and budget, and you will surely find the one you are looking for.
Related Info to Plastic injection mold press
Plastic Injection Molding Machine
Plastic injection molding machine, also known as an injection press, is a machine for manufacturing plastic products by the injection molding process. Plastic injection molding … read more
Plastic Injection Molding Process
Plastic injection molding process requires the use of an injection molding machine, raw plastic material, and a plastic mold. In this process, the plastic is melted …read more
Blow Molding Machine
Blow molding machine is a machine used in blow forming jobs that become a multibillion-dollar business. It is a manufacturing process in which hollow … read more
Is your project ready for molding? Send us your requirement for quotation, we will send you the price in 24 hours, you will not lose anything but have our competitive price for reference.
Plastic Injection Molding Service
Looking for plastic injection molding service?
Contact us to get quote, we are A Custom injection mold maker in China that offers plastic injection molding services.
The excellent quality of our plastic molds and molded parts, coupled with our experience and the performance of our services give us today a high international recognition. Indeed, the company is specialized in International Business and has customers all over the world. SINCERE TECH has very high standards of quality control and always runs long tests to make sure that our Plastic Injection Molding Service reaches all the expectations of our customers. We believe that the quality of a company and its products are seen through time and this is why we like to build strong long-term partnerships with our customer
What is plastic injection molding process?
Plastic injection molding is a manufacturing process in which melted plastic is injected into a mold and then cooled to form a solid part. The mold is created from a metal or plastic tool (1.2344, H13, NDK80, etc.) and is typically made in two halves that are clamped together. The plastic material is heated in a barrel and then forced into the mold under high pressure where it cools and solidifies into the desired shape. This process is used to produce large quantities of identical parts with high precision and repeatability.
When do you need plastic injection molding service?
You may need plastic injection molding service when you require mass production of plastic parts with consistent quality and high precision. This process is ideal for producing large quantities of the same part, as the mold can be used multiple times to produce identical pieces. Additionally, plastic injection molding is well-suited for producing complex and intricate shapes that would be difficult or impossible to achieve with other manufacturing methods. This process is often used in various industries such as automotive, consumer goods, medical devices, and electronics.
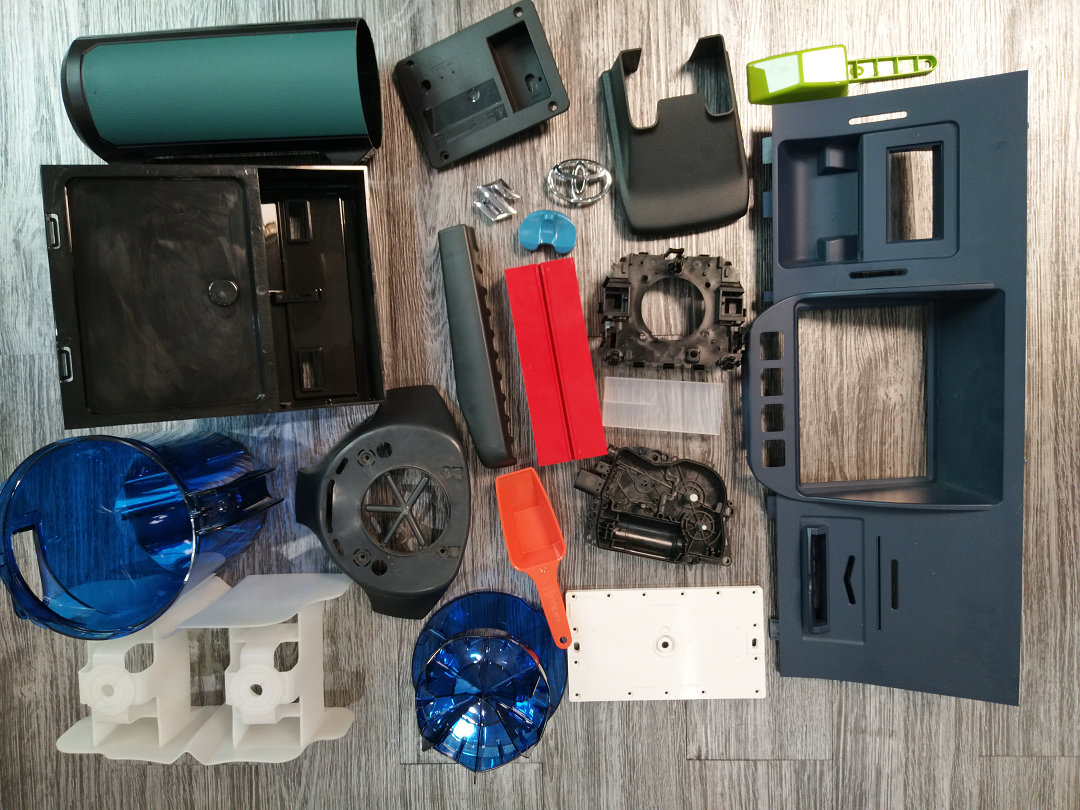
plastic molding services
Benefits of plastic injection molding service
The benefits of plastic injection molding service include:
- High volume production: Plastic injection molding is ideal for high volume production of identical parts, as the mold can be used multiple times.
- Consistent quality: The process is highly repeatable, which leads to consistent quality of parts produced.
- Complex shapes: Plastic injection molding can produce complex and intricate shapes that would be difficult or impossible to achieve with other manufacturing methods.
- Material flexibility: A wide variety of plastic materials can be used in the injection molding process, including thermoplastics, thermosets, and elastomers.
- Cost-effective: The process is efficient and cost-effective for producing large quantities of parts, as the cost of the mold can be spread over many parts.
- Precision: The process can produce parts with high dimensional accuracy and minimal tolerance variation.
- Automation: Plastic injection molding machines can be automated for increased productivity and reduced labor costs.
Plastic injection molding is a versatile and reliable manufacturing process that can provide significant benefits for producing large quantities of complex and high-precision plastic parts.
Plastic Injection Molding Service in China
We are the manufacturer of our own moulds (toolmaker or plastic injection tooling) and support the production of Injection molded parts allowing reducing your numbers of suppliers. Our injection machines have clamping forces going from 60 to 1050 Tons (2000 Tons outside). Plastic injection molding is the process of producing parts from thermosetting and thermoplastic materials.
Our qualified teams of Designers, Quality controllers and our Research and Development Department allow us to complete our policy: achieving Customer Satisfaction through Improvement and Innovation. The quality of our products and organization permits us to obtain quality certifications (ISO 9001, ) and be awarded numerous times of “Quality Supplier” from different customers. We integrate constantly new resources into our process in order to anticipate any future need of the plastic injection molds market and we became one of the most innovative companies in the sector. The modernity and the organization of our facilities allow us to adapt very quickly to the customer’s needs.
SINCERE TECH has always the objective to stay one of the innovative leaders of the sector and play an important role in our customer’s development. The firm can now propose a total solution from mould design to the semi-finished product (All in-house). SINCERE TECH is always willing to integrate new processes to the solution proposed by staying aware of new technologies. If a customer has a special requirement, we will do everything to fulfill its needs.
Plastic Materials /Commodities
We are used to working with all the classic and less classic plastic materials except PVC (PP, PE, PC, ABS, PC+ABS, PA 6, PA 6.6, PBT, PMMA, TPU, PC+GF, AS, PTFE, POM, PEHD, PEEK…). Our main suppliers are Sabic, Bayer, and Chimei.
About the steel used for our moulds, for export plastic molds we work only with the best steel suppliers like Assab (Sweden), Buderus (Germany), Daido Steel (Japan) LKM( the biggest one in China). For our standard component suppliers, we work with Hasco and DME.
We are used to working with our suppliers the same way we work with our customers. It means good long-term relationships with high-quality policy.
Complex moulds: SINCERE TECH has a rich experience in difficult plastic mould and parts, complex moulds and is an expert in finding solutions to your issues. SINCERE TECH is a real specialist in difficult tooling. To give a classic example: many design companies create plastic products without thinking about mould construction. Then, when the designs are sent to toolmakers, it can be hard for them to make the exact parts (Difficult design, many sliders, many lifters, double injection with materials non-bonding well together, many details in awkward places…).
Most of the classic toolmakers will accept the parts and say that they are able to do it. And then, they will have problems with the plastic injection mould construction, the lead time will be extended and the quality of the tool will not be as expected. Often, these companies have to contact SINCERE TECH to help them to resolve their problems. If you are not sure about the complexity of your part, be sure about your mould maker’s professionalism. SINCERE TECH works closely with its customers in order to resolve any issues.
Thin Wall injection molding: it permits a precise, very accurate molding of plastics and gives better details to the product. This is the name referring to products with a wall thickness lower than 2mm. Usually, the flow is quick, permits a short cycle time and a cost-saving.
Hot runner mold: the special process of injection of plastics where the plastic is kept hot when going through cavities of the mould while the rest of the mould is getting cold to solidify the plastic part and create the molded part: this permits to save plastic material. This is mainly used for parts with medium or large sizes. We are used to working with all popular companies like Yudo, INCOE, Synventive, Husky, HRS… We also have the technology to make our own hot runner systems if the production of the parts (Molding) is made in-house. This again allows our customers to save costs.
Optical Lens Molding: precision molding for glass plastic. This is the technique to produce transparent plastic molded parts (For example Security cameras parts such as the dome cover or also phone frames).
Gas-assist Injection Molding: the plastic parts are gas-assisted molded which means that gas (Most often is nitrogen) is injected at the final stage of the part creation process. It permits to reduce the cycle time, the product weight, the risk of deformation and also the pressure tons injection needed. Moreover, it makes the part’s structure stronger with a better look.
LED/LCD frame molding: injection of plastics used for example to manufacture television screen monitors, computer back-light modules, GPS frames…
IMD, IMF, IML, IMR Molding: In-mold decoration. The decoration of the part is made inside the mould through a film. The film is printed before the molding with the designs wanted. It permits better productivity and extends the decoration’s lifetime. If the customer wants to change the design/decoration of the part, it is not necessary to make another mould but only to change the film. SINCERE TECH is experienced with In-mould forming, in-mold-labeling, and in-mold by roller.
Overmolding: this technique permits to join several components together with a thermoplastic material. This reduces assembly and labor costs. Because the parts are made together, this allows less risk of improper termination or misalignment and increases the design flexibility. Moreover, thermoplastic provides better resistance to vibration or shocks. This technique permits to increase resistance, reduce costs and weights.
Insert Molding: this is a technique where a small part (Stamping part, optical part…) is added or inserted to the Injection molded part.
Two-Shot Molding: 2 independent injection units using 2 different materials and/or colors. The first material is injected; then, the mould rotates and the second material is injected to make 1 part. It permits a 2-colour-molding or also called double injection, 2 shot molding, two-shot injection, overmolding, 2K injection, two colour injection, bi-injection, dual shot molding or multi-component molding.
CNC Technology. CNC is an abbreviation for Computer Numerical Control. This is a machine extremely accurately controlled by computer programs permitting a CAM (Computer-aided Manufacturing) through a CAD (Computer-Aided Design). Any plastic injection tool manufacturer uses it but the value-added of SINCERE TECH is the experience, professionalism, and training of the staff.
FMMS Molding or can be called RHCM (Rapid Heat Cycle Molding): excellence surface appearance: permits to take off the welding line. This process is integrated into the molding to save time. It is used for example for clear plastic parts.
US Welding: Ultrasonic Welding: process to weld/ join/ assemble plastic parts thanks to ultra-sounds.
Silk-Screen Printing: this is to print logos or designs on parts.
Dip-Coating: this is the process of putting the component inside a liquid solution to apply a thin film on it. It permits to manage, change the hardness, the strength of the part by protecting it and expanding the lifetime of the product. Then, the excess liquid has to be drained and evaporation of the solvent is done to create the thin layer.
Laser Etching: this process is made for cutting a shape, a pattern, an image on the plastic part. It is also called laser graving.
Sputtering coating: this is the process of creating a very thin layer of conducting material on the component. It is also called Plasma Enhanced Chemical Vapor Deposition (PECVD) and can be done with most metals like aluminum, stainless steel, copper…
EMI shielding: protect parts from electromagnetic interferences. It is used to protect electrical signals from the outside world. For instance, we use it with marine radars for Garmin.
Waterproof technology: SINCERE TECH has the experience to make water-resistant parts and is able to ensure in-house tests thanks to the IP68 tests.
Sub-assembly: this is the pre-assembly of a component who will be later on being assembled in a larger product.
R&D: SINCERE TECH has its own Research and Development department in order to work with the customers on their projects, advise them on designs, resolve issues and study the feasibility of those.
Quality Control: We have very high standards of quality control in order to respect any requirements from our customers. We have a 100% quality control on our plastic molded parts, it means we control any part coming out of our production.
At Sincere Tech China mold maker, our unwavering commitment to staying at the forefront of the plastic mold industry drives us to embrace advancements and anticipate future trends. We continuously explore innovative materials and composites that offer enhanced performance and promote sustainability. By investing in ongoing research and development, we consistently deliver cutting-edge solutions that meet the evolving needs of our valued customers. As a trusted injection mold supplier in China, we take pride in our unwavering dedication to excellence.
Aligned with our sustainability goals, we place a high priority on environmentally friendly practices. We actively seek out sustainable alternatives, such as biodegradable polymers, and implement recycling initiatives to minimize the environmental impact of our manufacturing processes. By choosing our custom injection molding services, you can align your brand with sustainable manufacturing practices and contribute to a greener future.
Ensuring quality is our topmost priority, and we maintain rigorous quality control measures throughout the entire manufacturing process. Equipped with state-of-the-art facilities and staffed by skilled technicians, we subject each product to thorough inspection and testing. This guarantees exceptional performance, reliability, and customer satisfaction.
When you choose Sincere Tech as plastic injection molding service partner in China, you can expect the highest level of professionalism, expertise, and innovation. Our dedicated team is committed to helping you bring your ideas to life, delivering superior products that excel in performance, durability, and cost-effectiveness.
Partner with Sincere Tech Mould suppliers for your custom plastic injection molding service, and benefit from our comprehensive capabilities, unwavering commitment to quality and sustainability, and our drive to exceed your expectations at every step of the process. Together, let’s bring your innovative ideas to life.
About Us
Sincere Tech is Contract mould supplier in China that offers electronic new product research and development services as well as assembly company services. Contact us for more information.
All in one service for new product development from part design, PCB design, prototyping, testing, mold/die/tooling making, massive production, assembly, inspection, and packing.
Contact Info
Building 1, No. 30 Huan Zhen Rd, Shang Dong village, Qi Shi Town, Dongguan City, Guangdong province China, 523000
Mobile: +86 135 30801277
Weichat/whatsup No.: + 86 135 3080 1277
Email: info@plasticmold.net
Web: https://plasticmold.net
Our Customers feedback
“Hi Steve, Molds work very well good job, I hope you are doing well, as son as I have new project will come to you”
Customer from Hansaplastic in USA————–
“We are very happy with your management & English communication, you are outstanding in issue solving and fast replier, frankly say you are the best plastic mold maker and the molding company I have been working up to know”
Customer from Canada—————–
- Top 10 Injection Molding Companies in Indiana2024年11月20日 - pm1:02
- Top 10 Plastic Injection Molding Companies In Michigan2024年11月20日 - pm12:43
- Top 9 Plastic Injection Molding Companies in Chicago2024年11月16日 - pm3:29
- Top 9 Injection Molding Companies In Wisconsin2024年11月10日 - pm1:03
- Top 10 Injection Molding Companies in Ohio2024年11月10日 - am9:44