Plastic molds for concrete are manufactured from different kinds of plastics in specially designed shapes. These molds are utilized to provide required shapes and designs of concrete products. Plastic molds for concrete are reusable and they are also offers flexibility to create very large range of products which are made from concrete. These concrete products can be as simple as a block or can be complicated like complex decorative item. The introduction of various plastic molds for concrete has brought revolution in the way by which concrete items are designed and shaped.
In industrial sector and DIY (Do It Yourself) applications plastic concrete mould provides a cost effective solution which is also unique. Plastic molds for concrete are much better than the traditional metal molds and wooden molds are heavier and less durable as compared to plastic molds for concrete. Moreover, plastic molds for concrete have proved to quite easily produce the desired complex and intricate shapes which is not so easy to be accomplished by utilizing metallic or wooden molds.
There is a wide range of applications of plastic molds for concrete which includes construction of architectural items, concrete furniture, creation of decorative garden ornaments and paving stones. Plastic molds for concrete are easy to use and are affordable. They provide top notch quality results in the modern era of design and construction.
Types of Plastic Concrete Molds with Brief of Manufacturing Processes, Major Characteristics and Basic Utilizations
There are many types of plastic concrete molds which are manufactured for specific applications. The basic factors on which different kinds of plastic molds for concrete are based are followings.
- Size of the concrete product
- Complexity of the concrete product
- Various details of the concrete product
The primary types of the plastic molds for concrete along with their characteristics and usage are discussed below.
-
Injection Molded Plastic Concrete Molds
These molds are prepared and manufactured by a very accurate and properly controlled manufacturing process which is called injection molding process.
Brief of Injection Molded Plastic Concrete Molds Manufacturing Process
The process starts with creation of a detailed design of the required Plastic concrete mould. This is accomplished by utilizing CAD software. The produced CAD model is then applied to create metallic mold. After that plastic pellets of selected plastic materials are prepared. In the injection molding machine these plastic pellets are heated. The resulted molten plastic is ultimately injected into the metallic mold cavity.
This is done under high pressure. The molten plastic cools down in the metallic mold and become solidified. Ejection of this molded plastic piece from the mold is then carried out. The trimming process is then adopted to remove any excess material such as flash and finishing processes are performed for finalization of the injection molded plastic molds. This manufacturing process is very suitable for the purpose of mass production. The produced molds are of consistent quality.
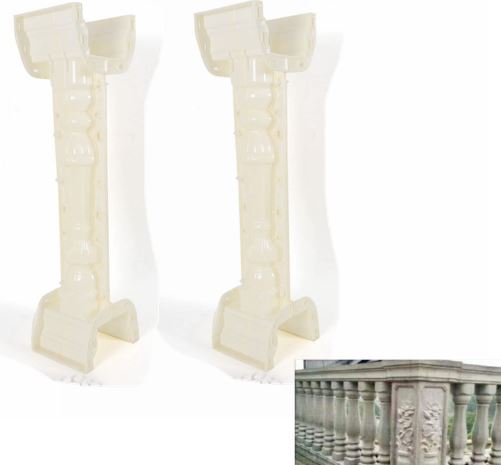
plastic concrete mould
Major Characteristics
The major characteristics of these molds are mentioned below.
- These molds bear high precision and have the ability to produce fine details and complex designs
- These molds bears high strength and durability
- These molds provides high production rates
Basic Utilization
The basic usage of injection molded plastic molds includes the followings.
- They are used in shaping numerous decorative articles such as garden ornaments and statues
- They find their usage in formation of intricate architectural elements such as ornate cornices and balusters
- They are also utilized in shaping high detailed tiles and paving stones
-
Vacuum Formed Plastic Molds
These molds are manufactured by heating a plastic sheet. This heat is maintained till the plastic sheet becomes pliable. After that vacuum suction is applied to shape it over a mold.
Brief of vacuum-formed plastic concrete molds Manufacturing Process
The process of making vacuum-formed plastic molds for concrete starts same as injection molded plastic molds. In the initial step designing of the mold shape using CAD software is carried out. After that a master pattern or model is created from materials such as wood, foam, or resin. These materials are selected based on the required design. After that the selected plastic sheet material is cut according to the required size. This sheet is placed in a vacuum forming machine. Heating of this sheet is performed until it becomes pliable.
The master pattern then is positioned on the machine’s mold table. The heated plastic sheet is lowered onto this master pattern. The plastic is sucked by a vacuum pump against the pattern which creates the desired shape. The hardened and cooled plastic is then removed from the machine. The subsequent trimming process is used for removing excess material. The plastic mold is separated from the master pattern in a careful way. The edges of the mold are smoothed to ensure a clean release of concrete when it is utilized in applications. After that the mold undergoes a quality check for defects like bubbles or incomplete forming.
If necessary, the Plastic concrete mould is reinforced for added durability. A release agent or coating is applied to help with de-molding, and the mold is tested with a small batch of concrete to ensure it works correctly. After this, the molds are prepared for production, stored properly to maintain their condition, and cleaned regularly. A final inspection is done to ensure the molds are ready for use in concrete production, ensuring they are accurately shaped and durable.
Major Characteristics
These molds bear the following characteristics and properties.
- These molds provide cost effective solution as compared to injection molded plastic molds because they are much less expensive to produce
- These molds bear the property of flexibility, thus these molds are considered ideal for the creation of large but simple shapes and designs
- Plastic sheets are utilized in these molds so these molds are easy to transport and handle
Basic Utilization
Vacuum formed plastic molds find their usage in following scenarios.
- The tiles and paving stones which are much larger in size are created by vacuum formed plastic molds
- These molds are applied for shaping garden features and basic decorative products
- Vacuum formed plastic molds are also utilized to create forms for DIY concrete projects
-
Rotationally Molded Plastic Molds
These molds are produced by rotational molding procedure. In this method a rotating mold is filled with plastic resin while at the same time it is being heated which from a hollow mold.
Brief of Plastic Concrete Mould Manufacturing Process
Creating rotationally molded plastic molding for concrete involves a detailed process to ensure high quality and durability. It starts with designing the mold using CAD software. A metal mold which is made from aluminum or steel is fabricated. Fabrication method and material are selected on the basis of the desired design. Then the selected plastic resin such as polyethylene is calculated and loaded into the mold. The mold is then sealed very tightly. This mold is placed in an oven where it is heated and rotated on two axes at the same time.
This allows the melted resin to evenly coat the interior surfaces. After that the mold is transferred to a cooling station. The rotation continues until the plastic cool down and eventually solidified. After the cooling and solidification is completed, the mold is opened in a careful way. The plastic part which is formed is removed. The excess material if any is trimmed off and the edges and surface are smoothed to make sure a clean release.
The mold is inspected for defects such as bubbles or incomplete forming and may be reinforced to enhance durability. A release agent or coating is applied to facilitate easier de-molding, and the mold is tested with a small batch of concrete to ensure it functions properly. Finally, the mold is prepared for repeated use or mass production, with regular cleaning and maintenance carried out to extend its lifespan and ensure consistent performance. This comprehensive process results in durable, accurately shaped molds ready for efficient concrete product creation.
Major Characteristics
These molds offer following characteristics and utilization.
- These molds possess uniform wall thickness because plastic material is evenly distributed during manufacturing process
- These molds are very suitable for shaping heavy duty products because of their durability and strength
- Rotationally molded plastic molds have the ability to form large items which are not possible to form by other molds
Basic Utilization
- Rotationally molded plastic molds are utilized to shape large concrete furniture products including tables and benches
- These molds are utilized to form structural elements such as water features and planters
- Rotationally molded plastic molds are also used to shape large decorative garden items
4.3D Printed Plastic Molds
3D printed plastic molds are manufactured from thermoplastic materials by building a layer by layer mold from a digital model.
Brief of Manufacturing Process
The process of making 3D printed plastic concrete molds is started in the same manner as performed for other mold making methods. In the first step the designing of the mold using CAD software is carried out. This step is performed because it provides help in creating precise and detailed shapes. After the completion of the design, it is converted into a file format. It is important to note that this file format must be compatible with 3D printing. Generally following two materials are selected selected for 3D printed plastic molds.
- Polylactic Acid
- Acrylonitrile Butadiene Styrene
These selected materials are then loaded into the 3D printer. The printer then constructs the mold layer by layer which is based on the digital design. After printing, the mold is removed from the printer very carefully. After that the cleaning of support structures and extra materials is performed.The mold is then inspected for accuracy, and finishing touches like sanding or sealing are applied to smooth the surface.
A release agent or coating is added to make removing the concrete easier. The mold is tested with a small batch of concrete to ensure it performs correctly and the concrete sets as expected. The mold is ready to be utilized once its effectiveness is confirmed by making any necessary adjustments. It is pertinent to mention that regular cleaning and maintenance of the molds is very important because of the following two reasons.
- To keep the mold in good condition
- To enhance its lifespan
The method of 3D printing of plastic molds enables the production of highly detailed and customized molds. This is very suitable for numerous concrete applications.
Major Characteristics
3D printed plastic molds provides following properties and usage.
- 3D printed plastic molds have the ability to produce complex and unique designs because these molds are highly customizable
- These molds allow for quick and repeated changes, thus these molds are very suitable for shaping new designs
- 3D printed plastic molds bear the quality to produce detailed and intricate shapes so these molds are best suited for small scale production
Basic Utilization
- 3D printed plastic molds are used to shape customized and versatile decorative items
- These molds are utilized to produce prototypes for the purpose of testing new designs and features
- The high detail specialized elements which are mainly being applied in architecture are formed by 3D printed plastic molds
Benefits of Plastic Molds for Concrete
Plastic molds for concrete offer many benefits for concrete casting which makes them a popular choice in construction and decorative applications. The prominent advantages of plastic molds for concrete are as follows.
- Cost-Effective
Plastic molds are generally more affordable as compare to metallic molds. Thus they are an attractive choice for both small and large scale projects.
- Lightweight
Plastic molds are much lighter than metallic molds. So, these molds are easier to handle, transport, and position. This ability ultimately leads to reduce the labor cost an making the casting process simplified.
- Flexibility and Versatility
Plastic molds for concrete can be designed and manufactured in a vast range of shapes and sizes. They are much suitable for creating complex and intricate designs which is difficult or costly with other materials.
- Ease of Use
Plastic molds require less maintenance compared to metallic molds and are easy to use. They can be pre-formed with precise details thus reducing the requirement for additional finishing work on the concrete.
- Durability
Modern plastic molds for concrete are manufactured from high quality materials. These materials bear the characteristics of durability and can be reused many times. Moreover, they provide resistant to impact, wear, and many chemicals. This will ultimately which helps in maintaining their shape and functionality over time.
- Corrosion Resistance
This is a much significant benefit of plastic molds over the metallic molds. Plastic molds do not rust or corrode so this property is particularly advantageous in following scenarios.
- when working with concrete mixtures that may contain corrosive agents
- when the molds are exposed to moisture
- Smooth Surface Finish
Plastic molds offer a very smooth and good surface finish on the concrete. Subsequently, it reduces the requirements of additional surface treatments or finishing. This as a result enhances the aesthetic quality of the finished product and provides cost effective solution.
- Quick Production
Plastic molds provide quick production rates, especially with methods like vacuum forming or 3D printing. This property of plastic molds comes in handy for projects with tight deadlines.
- Reusable
Plastic molds are a sustainable option for concrete because they are designed to be reusable. If they are properly maintained on regular basis it can extend their life and reduce the need for constant replacement.
- Customization
In order to meet specific design requirements plastic molds can be easily customized. This flexibility of customization allows for the production of versatile or custom shaped concrete items.
- Non-Stick Properties
It is important to note that many plastic molds are treated or coated to have the non sticking properties. Subsequently, this prevents the concrete from adhering to the mold. Thus demolding becomes easier, reducing the risk of damaging the finished product.
Basic Factors to Consider While Utilizing Plastic Concrete Molds
The utilization of plastic molding for concrete requires several key factors to consider in order to achieve the best results and longevity of the molds. The details of these factors are as follows.
- Material Choice
The type and kind of plastic used in manufacturing of the molds is of significant importance. It is well known that different plastics show different properties. High density polyethylene provides excellent durability and impact resistance as compared to other plastics. Thus selecting the right plastic for specific needs and requirement will help in achieving the best results and extending the life span of the mold.
- Mold Design
It is pertinent to mention that the complexity of the mold design ultimately affects the final product. Thus molds need to be designed with great care to include features and aspects such as draft angles and release mechanisms to ensure that concrete products come out smoothly and the mold remains intact. Moreover, detailed designs might require additional precision in both the mold making and handling procedures.
- Release Agents
The most vital factor to consider while utilizing the plastic molds for concrete is the application of the correct release agent. These agents are utilized to prevent the concrete from sticking to the mold. The generally used release agents types are the followings.
- Oil-Based Release Agents
- Water-Based Release Agents
- Silicone-Based Release Agents
- Powder Release Agents
- Natural and Eco-Friendly Release Agents
- Foam Release Agents
- High-Temperature Release Agents
It is important to note that the choice of release agent must be compatible with the plastic material of the mold. This is necessary to maintain quality and the integrity of the concrete product.
- Temperature and Curing
Plastic molds for concrete can be quite sensitive to temperature variations. So it is important to manage curing conditions in a careful way. This is of significance importance because of the followings.
- Excessive heat can warp the mold
- Insufficient heat may affect concrete setting
So the basic factor to ensure that the casting is acceptable is to make sure that curing temperature is suitable for both the mold and the concrete mix.
- Cleaning and Maintenance
Cleaning and Maintenance of plastic molds for concrete is vital and critical. This basic reason behind this is that residual concrete can create issues for future utilization of the molds. So, regular cleaning and maintenance with appropriate methods is important. Moreover, regular routine checks must be carried out for wear and tear. This will ultimately help in preserving the effectiveness of the mold.
- Environmental Impact
It is important to take in Consideration the environmental effects of the plastic molds for concrete. The plastic material selected for mold if not biodegradable and not recyclable can cause adverse affects on the environment. However, contrary to that, selecting the recyclable or biodegradable plastics will surely leave positive impact on the environment. Moreover, proper disposal or recycling of old molds is also of significant importance to reduce the adverse and harmful environmental impact.
Conclusion
Plastic molds are a practical and cost-effective choice for concrete casting, offering flexibility and durability. Plastic molds for concrete provides effective solutions for concrete casting giving value in complex and intricate designs. They make it easy to produce detailed and custom designs while being lightweight and resistant to corrosion. With proper handling and maintenance, plastic molds provide reliable performance and high-quality results across various applications. Plastic molds have the ability to handle a vast range of concrete mixtures and casting environments effectively. Regular maintenance, careful handling, and appropriate storage further enhance the long life span and performance of the plastic concrete molds. Overall, they are an excellent tool for both decorative and structural concrete projects.