Rapid prototyping service plays the most important role in making fast functional testing samples. There are many types of prototypes that you could use for your first idea project; those include 3D print prototypes, CNC machining prototypes, vacuum moulding prototypes, prototyping injection molding, and many more.
Rapid Prototype is a way to take an initial concept and turn it into a physical model; in other words, taking a CAD computer generated concept and create an inexpensive 3D prototyping model.
The process of 3D prototyping helps identify errors in product design, which can be corrected prior to creating tools and plastic molds for production.
What is Rapid Prototyping?
Rapid prototyping is a product development technique that employs turnkey manufacturing processes to create several versions of a part for testing and validation. In other terms, it is the quickest method of making parts or fabricating products with minimal turnaround for hands-on reviews. Rapid prototyping is most often done with the help of 3D printing because it is relatively cheap, the cost of a prototype ranges from $5 to $50, and it takes 1-3 business days to complete.
The two main concepts of rapid prototyping are speed and cost. These concepts enable several prototype designs to be produced simultaneously or a single prototype to be modified and produced again quickly. Prototypes are important as they offer information that engineers need to make design choices before proceeding to the next level of models used for functional testing and manufacturing.
Professional rapid prototyping services can help test various designs and materials since the usual financial and time risk is removed from the equation. This reduces the risk that would be experienced when an organization decides to advance a project without adequate information.
Plastic Mold Prototyping Online Services
Our facility of engineers and product designers offers professional rapid prototyping services online to help reduce the time taken in product development. Since there are numerous ways of creating prototypes, engineers must choose the most suitable process and material for their product. In recent years, additive manufacturing, especially 3D printing, has become one of the most sought-after technologies for engineers needing fast prototyping injection molding. This technology allows for the rapid and inexpensive manufacturing of parts from various metals and plastics, making it suitable for rapid prototyping applications.
Overview of Rapid 3D Printing Processes
3D printing is considered one of the most effective techniques of rapid prototyping because of its speed and cost. Sincere Tech provides fast 3D printing services where parts can be produced and delivered in one day, sometimes for a relatively small amount.
The three leading 3D printing techniques for rapid prototyping are selective laser sintering, stereolithography, and fused deposition modeling.
- Selective Laser Sintering (SLS): SLS is a versatile technology that offers speed, functional properties, detail resolution, and cost-effectiveness.
- Stereolithography (SLA): SLA provides better surface finish and detail resolution than other 3D printing technologies, making it suitable for creating complex prototypes and transparent parts, especially with the QuickClear finish.
- Fused Deposition Modeling (FDM): FDM uses materials such as ABS, PC, and ULTEM and is best suited for more significant parts since it can produce large parts quickly and in a single run.
How To Select The Right Prototyping Technique?
Typically, the appropriate selection of rapid prototyping methods depends upon various factors including; the time frame, part specification, and complexity, the intended budget, and application, and functional requirements. A delicate, and sophisticated design prototype always costs more, since they acquire more time in operation, skilled personnel, and electrical consumption. Therefore, it’s advised to seek help from reputable prototype service providers for the right process choice. Their guidance helps you make a sound choice within your limited budget.
For more detailed prototypes, usually product designers employ 3d printing, and cnc machining due to their ability to meet tight part dimensions or tolerances. For simple prototype designs, injection molding can be an optimal option to choose. Moreover, it’s economical for large batches volumes, when you need to fabricate prototypes in a limited time frame.
Rapid CNC Machining at Sincere Tech
When prototypes must be tested in the final material from fully dense stock, CNC milling, and CNC turning are ideal rapid prototyping solutions. Sincere Tech provides rapid prototype services for various materials, including metals and plastics, and many parts are produced and delivered within a week. CNC services can be accelerated during the quoting process, and Sincere Tech’s affordable rates enable engineers to produce multiple prototypes for fast product testing.
Compared to 3D printed parts, CNC machined parts usually take more time to produce because of the extra setup and running time. 3D printing is a direct digital manufacturing process that involves little or no setup or post-processing.
Sheet Metal Fabrication for Fast Turnaround with Sincere Tech
Fast sheet metal fabrication is ideal for creating flat parts that can be tested relatively quickly in the final metal material. Our professional technical experts provide these parts in a week or less, at an affordable range of budget enabling us to create several prototype designs at once in short time. Although Aluminum 5052 is the most popular material for rapid prototyping, we also offer a variety of other materials, such as steel, copper, and stainless steel.
Similarly, rapid sheet metal parts have an optimal lead time, similar to rapid CNC machined parts, but are more extended than 3D printed parts. Like CNC machining, sheet metal fabrication involves extra time for setting up the machines and their actual running time.
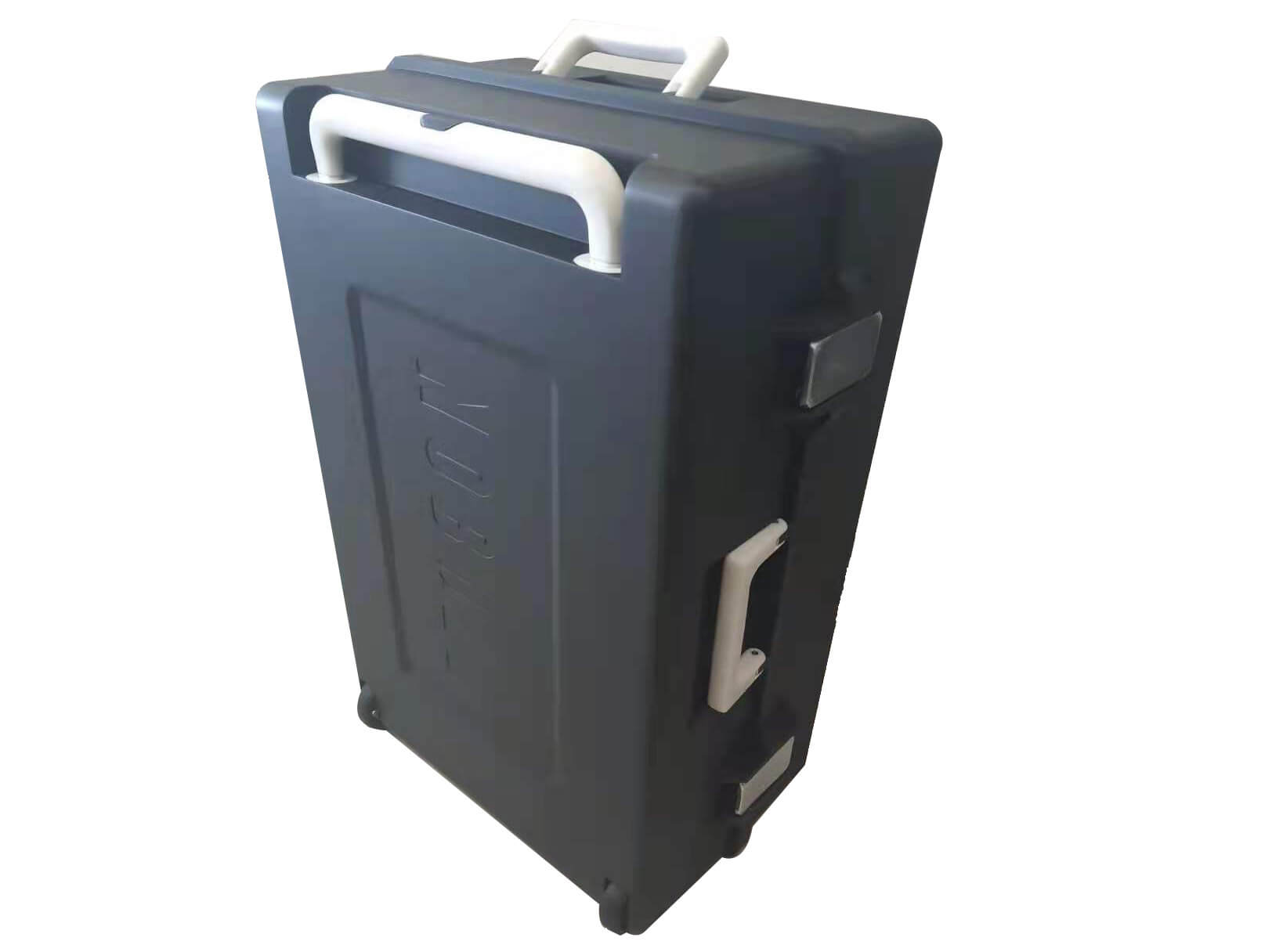
Rapid prototype service
Rapid Injection Molding Online Services
Rapid plastic injection molding is a technique that creates strong sets of similar parts ideal for various testing applications. It is precious for high-fidelity product assessments and a transitional tool during short-term production processes. The lead time for rapid tooling in injection molding is usually 2-3 weeks for first articles, but we provide a Quick-Turn Molding service that can produce parts in 5 days.
Rapid injection molding is preferred over additive manufacturing or machining where there are strict material or specific mechanical requirements to be fulfilled. Although it is not as fast as 3D printing or CNC machining, rapid injection molding is ideal for creating large quantities of parts with high accuracy and near-final dimensions, making it suitable for use in rapid prototyping.
Benefits of Using Rapid Prototyping Services
There are several compelling reasons why companies and sellers opt for rapid prototyping machining services:
- Speed: Conventional methods of mold making may take several weeks or even months to create a physical part, which slows down the testing and validation phases. Rapid prototyping services can build prototypes in hours so that the product can be tested and modified quickly.
- Cost: Direct mold-making is expensive because of the tooling and material costs. Rapid prototyping services are more economical in most cases because they do not require tooling before functional validation.
- Quality: Rapid prototyping services use 3D printing technology to produce accurate models quickly. CNC machining prototypes can be very similar to the actual molded parts, but they will be slightly more expensive than 3D printing.
- Flexibility: Rapid prototyping services allow for the creation of multiple versions of a product design quickly. This agility helps correct design flaws before the development process is complete, which is cost-effective for new functions where the function’s success is not guaranteed.
Reduce Production Lead Time & plastic mold or Tooling Costs
By introducing the rapid prototyping process in the design stage one can reduce lead time to production and reduce the cost of modifying expensive tooling.
Each case is different but in general, customers who utilize the prototyping process can reduce cost and lead-time by as much as 25-50%.
A customer of Sincere Tech explains that they find the rapid prototyping process helpful in detecting design flaws. For instance, user comfort issues can be highlighted early with a prototyping model.
Previously these issues were not discovered and they were too small to fix the production design so the client was not able to correct them. The prototyping process helps prevent compromise on the final quality of the product design.
Available Rapid Prototyping Processes
Each prototyping model has different requirements but generally, we find projects fit within three categories.
1. Appearance prototyping models (for tradeshows or sales demonstrations)
2. Fit test prototyping models
3. Functional prototyping models
Prototype Process Technologies
The three most common prototyping technologies are:
1. FDM Prototyping– Fused Deposition modeling
Pros: ABS Plastic has a fast lead time and good strength
Cons: The surface finish is rougher than Polyjet or SLA
2. Polyjet Rapid Prototyping – Jetted Photopolymer
Pros: Best detail resolution and fast lead time
Cons: More expensive than FDM and not as durable
3. SLA Prototyping – Sterolithography
Pros: Fast, good surface finish, strong
Cons: Higher cost than FDM
Urethane Molding Prototyping RTV Mold and Casting System for larger runs
The rapid prototyping process is best suited for small runs. Often for runs above 5 pieces, urethane casting becomes more cost effective.
Silicone molds are created from an SLA model reducing the cost for any additional prototyping process.
Urethane casting provides bridge tooling if there is a series of prototyping models that need to be sent out for user feedback prior to creating injection tooling.
Practical production runs for urethane casting are typically between 5 pieces to 50 pieces.
Limitations of Rapid Prototyping Services
Despite their many benefits, rapid prototyping also has some limitations. Some demerits includes;
- Size Limitations: The size of the 3D printer can limit the size of the models that the printer can create. For example, it is almost impossible to print parts that are more than one meter in size using 3D printing. Moreover, it’s key to note that even CNC machining can be challenging when working with such difficult dimensions.
- Cost: Rapid prototyping is cheaper than molding or CNC machining, but it is still costly for many organizations due to its detailed-oriented engineering approach to fabricating exact specification designs.
- Material Limitations: As mentioned earlier, there are limitations to the use of materials in rapid prototyping. Some materials used in 3D printing may not be appropriate for conventional prototype molding processes.
Our expanded capabilities
Our services cover a wide range of products manufacturing from small volumes to bulk orders aimed at meeting your manufacturing requirements effectively:
We focus on rapid prototyping, which uses modern technologies like 3D printing or CNC machining to turn ideas into tangible models quickly. These prototypes are useful for testing, redesign suggestions and general product improvement.
Precision CNC Machining enables the production of mold components with tight tolerances to meet the highest standards. This precision ensures that the final injection-molded products are accurate and variations-free.
Overmolding: We can manufacture overmolded products for handling tools and die-casting molds. Feel free to contact us for an engineered online quote on your overmoulding project needs.
Also, Insert Molding services are offered; it is similar to overmolding but uses metal parts as substrates, making it more rigid and flexible.
In Two-Shot Molding, parts with multiple materials and intricate structures can be produced in a single step, thus minimizing the number of assemblies and opening up new design opportunities. This advanced process requires specialized equipment.
We machine Engineering Prototypes from many plastics, metals ( stainless steel & aluminum) and composite materials. Customer requests typically range from one to 100 machining parts, and may focus on a single, key component, or include all of the mechanical parts in a product. Customers use our CNC machined parts for everything from thermal and RF testing to evaluating acoustical and environmental performance.
Effective use of Engineering Prototypes helps product design teams refine and stabilize the functional details of their parts and assemblies, reducing the chance that later design changes will interrupt and add cost to the tooling cycle.
Our CNC machining capabilities include vertical and horizontal milling centers, wire and die-sinking EDM, and a full complement of supporting processes including custom milling and turning, grinding, tumbling, heat treating, media blasting, and welding, and post manufacturing include powder coating, anodizing, printing, chrome, manual product assembly service, etc.
Our experience with milling plastics, both neat (unfilled) and as composites is extensive. In some cases, when specialty materials are not available as machining material, we have the capability of molding small and medium-sized billets from injection molding resins, and using these as machining material. We have also developed a custom modular fixturing system that makes these molded stock materials convenient to load and unload with automatic positioning.
3-Axis Milling
- Machines by Makino, Roku, Chiron, Fanuc and Tree
- Maximum Machining Envelope (XYZ) = 27″ x 16″ x 10″ (Fanuc)
- Maximum Tool Capacity = 40 (Makino V33)
- Fanuc Controllers on all Machines
- Vacuum Fixtures, Clamp Fixtures, Tape, Vise, and custom workholding
4-Axis Milling
- Kitamura MyCenter Horizontal
- Maximum Machining Envelope (XYZ) = 20″ x 20″ x 20″
- Maximum Tool Capacity = 40
- Fanuc Controller
- Rotary pallet changer with programmable C axis (static or dynamic)
- Chick Tombstone Pallet System
- Custom machinable ‘soft jaws’ for part fixturing
Customer Data Requirements
- 3-D CAD data in portable format (iges, stl, step, vdi) or Pro/E
- Detailed Color, Materials, and Finishes documentation for all surfaces
- All required graphics including logos, screen displays, labels
CNC Programming
- Primary Platform – Mastercam X3
- Toolpath verification – Vericut
- Toolpath optimization – Optipath
Achieving Speed and Quality
We use a combination of software tools to ensure high as-machined dimensional accuracy, good surface quality, and efficient high speed machining. The majority of our part machining is done using UG software. We maintain an extensive software definitions library of cutting tools and substrate materials, which our programmers access to ensure we machine with optimal conditions.
We have also implemented process verification software to identify risk areas in CNC machining, and ensure a high success rate. This software simulates the entire machine environment, including table, spindle, workholding, tool checking, and cutting tool library. Most recently, we have also implemented a cutting path optimizer, which maintains constant material removal rates, making sure there is a constant loading on the cutting tool. This provides us with a significant time saving.
Additional services
We can be your contract manufacturer China company that offer you all in one services from prototype, CNC machining, turning and milling machining, plastic or metals, mold & tooling, massive production and value-added processes from our local suppliers, including plating, conversion coatings, painting or powder coating. In addition, we do manual product assembly and test fixtures to support product qualification and pilot builds before delivery.
Further, we offer value-added services like product silk-screening, painting, assembly, testing, certification, packaging, and logistics support. These services help to manage your supply chain and also help to reduce costs.
If you have any project that need machining service, or need an OEM contract manufacturer in China to handle your project in qualification, you are welcome to contact us.
Working with Sincere Tech means access to high-quality services in injection molding, die casting, and machining. Our commitment to providing excellent services to our valued customers enables’ us to ensure we deliver our products quickly and with the highest quality standards. If you want a quote, please contact us right now, and our professional engineers will respond within 24 hours.