ما هو قالب الحقن؟
قالب الحقن هي أداة تستخدم في عملية القولبة بالحقن لإنتاج أجزاء عن طريق حقن المواد في تجويف القالب. وهي مصنوعة عادة من الفولاذ (H13، P20، 1.2312، 1.2344، S136H، إلخ) أو الألومنيوم، وهي مصممة بعناية لتتناسب مع شكل ومواصفات المنتج النهائي.
يتم تقسيم قالب الحقن إلى نصفين، نصف تجويف ونصف قلب، يتم تثبيتهما معًا أثناء عملية التشكيل، مع حقن المادة من خلال مجرى في تجويف القالب حيث تبرد وتتصلب إلى الشكل المطلوب. بمجرد تشكيل الجزء، يفتح القالب ويتم إخراج الجزء. يمكن إعادة استخدام القالب لإنتاج أجزاء متعددة.

ما هو قالب الحقن
أنواع قوالب الحقن
من بين العديد من أنواع قوالب الحقن، قد تجد:
قالب خاص بالتجويف
لا يمكن لكل دورة من عملية القولبة بالحقن أن تنتج سوى جزء واحد عند استخدام قالب تجويف واحد. عملية صنع جزء باستخدام هذا القالب بسيطة مثل حقن راتنج بلاستيكي فيه، وانتظاره حتى يبرد، ثم إزالة المنتج النهائي.
عند مقارنة تكاليف إنتاج القوالب متعددة اللقطات بالقوالب ذات التجويف الواحد، نجد أن الأولى عادة ما تكون أكثر تكلفة. وعندما يكون تصنيع عدد صغير من المكونات في وقت واحد مكلفًا للغاية، فإن هذه القوالب هي الخيار الأمثل للنماذج الأولية وعمليات التصنيع ذات الحجم المنخفض.

قالب تجويف واحد
تتضمن مزايا قوالب اللقطة الواحدة ما يلي:
- فعالة من حيث التكلفة: إن إنتاج قالب طلقة واحدة يكون في كثير من الأحيان أقل تكلفة من إنتاج قالب طلقات متعددة.
- تصميم بسيط: سهولة الإنتاج والصيانة بسبب بساطة التصميم: غالبًا ما تكون القوالب ذات اللقطة الواحدة أقل تعقيدًا في التخطيط من القوالب ذات اللقطات المتعددة.
- المرونة: مجموعة واسعة من التطبيقات، مثل النماذج الأولية وعمليات الإنتاج ذات الحجم المنخفض، مناسبة لاستخدام قوالب التجويف الواحد.
تشمل عيوب قوالب اللقطة الواحدة ما يلي:
- الإنتاج المحدود: يجعل هذا القيد القوالب ذات التجويف الفردي غير مناسبة لعمليات إنتاج القوالب ذات الحجم الكبير لأنها قادرة فقط على إنتاج جزء واحد خلال كل دورة.
- الأجزاء المعقدة: القوالب ذات التجويف الواحد ليست جيدة لصنع أجزاء معقدة مكونة من أجزاء عديدة؛ لذلك، ستحتاج إلى قالب متعدد التجاويف أو قالب عائلي.
- عدم الكفاءة: بالمقارنة مع قوالب التجاويف المتعددة، فإن قوالب اللقطة الواحدة تكون أقل كفاءة لأنها لا تستطيع إنشاء سوى جزء واحد خلال كل دورة بسبب قدرتها المحدودة.
قوالب متعددة التجاويف:
القوالب متعددة التجاويف هي نوع من قوالب الحقن التي تحتوي على أكثر من تجويف. وهذا يسمح لعملية الحقن بصنع أكثر من جزء واحد أثناء كل دورة. واعتمادًا على احتياجات التطبيق، يمكن تصنيع هذه القوالب بفتحات متماثلة أو مختلفة.
نتيجة لقدرتها على إنشاء العديد من الأجزاء في دورة واحدة، يتم استخدام قوالب متعددة التجاويف عادةً حقن كميات كبيرة من المواد عمليات الإنتاج. تتيح لهم هذه الميزة زيادة كفاءة الإنتاج مع خفض التكلفة لكل جزء.

قالب تجويف متعدد
تتضمن مزايا القوالب متعددة التجاويف ما يلي:
- إنتاج بكميات كبيرة: يتم تصنيع قوالب متعددة التجاويف لعمليات الإنتاج واسعة النطاق، مما يجعل من السهل تصنيع الكثير من الأجزاء.
- فعّالة من حيث التكلفة: عادةً ما تكون القوالب متعددة التجاويف أرخص من القوالب ذات التجويف الواحد لأنها يمكن أن تصنع المزيد من الأجزاء في عملية تشغيل واحدة.
- الأجزاء المعقدة: يمكن استخدام القوالب متعددة التجاويف لصنع أجزاء معقدة وتحتوي على العديد من الأجزاء.
تشمل عيوب القوالب متعددة التجاويف ما يلي:
- التصميم المعقد: إن تصنيع القوالب متعددة التجاويف وصيانتها أكثر صعوبة من القوالب ذات التجاويف المفردة لأن تصميماتها أكثر تعقيدًا.
- زيادة تكلفة القالب: يمكن أن تكون القوالب متعددة التجاويف أكثر تكلفة من القوالب ذات التجويف الواحد لأن التجاويف المختلفة قد تتعرض لمقادير مختلفة من الإجهاد والتآكل أثناء عملية الصب بالحقن. وقد يؤدي هذا إلى إنتاج أقل كفاءة وتكاليف أعلى للإصلاحات.
قالب العداء الساخن:
قالب العداء الساخن هو نوع من قوالب الحقن التي تستخدم نظام مجرى ساخن لتوصيل مادة البلاستيك المذابة إلى تجاويف القالب. يتكون نظام المجرى الساخن من مشعب ساخن يوزع البلاستيك المذاب على أطراف فوهات فردية، والتي يتم توجيهها بعد ذلك إلى تجاويف القالب.

قالب العداء الساخن
تتضمن مزايا قوالب العداء الساخن ما يلي:
- تحسين جودة الأجزاء: يمكن أن تنتج قوالب الممر الساخن أجزاء بجودة محسنة، حيث إنها تقلل من كمية البلاستيك المتبقية في الممرات، مما يقلل من خطر العيوب مثل الوميض، واللقطات القصيرة، وعلامات الغرق.
- زيادة كفاءة الإنتاج: يمكن أن تعمل قوالب الجري الساخن على زيادة كفاءة الإنتاج، حيث إنها تلغي الحاجة إلى التدخل اليدوي لإزالة الجري من الأجزاء المصبوبة، مما يقلل من وقت الدورة ويحسن سرعة الإنتاج الإجمالية.
- كفاءة الطاقة: تعتبر قوالب الممر الساخن أكثر كفاءة في استخدام الطاقة مقارنة بقوالب الممر البارد التقليدية، حيث إنها تقلل من كمية البلاستيك المهدرة في الممرات.
تشمل عيوب قوالب الجري الساخن ما يلي:
- تصميم معقد: تعتبر قوالب الممر الساخن أكثر تعقيدًا في التصميم مقارنة بقوالب الممر البارد التقليدية، مما يجعلها أكثر تكلفة في الإنتاج والصيانة.
- زيادة الصيانة: تتطلب قوالب الجري الساخن عادةً مزيدًا من الصيانة مقارنة بقوالب الجري البارد، حيث تحتوي على نظام تدفئة أكثر تعقيدًا يحتاج إلى الحفاظ عليه في حالة عمل جيدة.
- التعرض للانسداد: قد تكون قوالب الممر الساخن عرضة للانسداد، وخاصة عند معالجة المواد ذات اللزوجة العالية أو ذات أطوال التدفق الطويلة، حيث يمكن أن يتسبب ذلك في تصلب البلاستيك المنصهر في الممرات. وقد يؤدي هذا إلى انخفاض كفاءة الإنتاج وزيادة تكاليف الصيانة.
قوالب التكديس:
قالب المكدس هو نوع من قوالب الحقن التي تسمح بتشكيل تجاويف متعددة في وقت واحد في دورة ماكينة واحدة. تتكون قوالب التكديس في الأساس من قالبين أو أكثر مكدسين فوق بعضهما البعض، حيث ينتج كل قالب جزءًا واحدًا.

قالب المكدس
تتضمن مزايا قوالب المكدس ما يلي:
- زيادة كفاءة الإنتاج: تسمح قوالب التكديس بتشكيل أجزاء متعددة في وقت واحد، مما يزيد من كفاءة الإنتاج ويقلل من وقت الدورة.
- تقليل هدر المواد: تعمل قوالب التكديس على تقليل هدر المواد، حيث إنها تسمح بإنتاج أجزاء متعددة باستخدام طلقة واحدة من مادة بلاستيكية.
- تكاليف أقل: يمكن أن تكون قوالب التكديس أكثر فعالية من حيث التكلفة مقارنة بالقوالب ذات التجويف الفردي، لأنها تسمح بإنتاج أجزاء متعددة بدورة آلة واحدة.
تشمل عيوب قوالب المكدس ما يلي:
- التصميم المعقد: يمكن أن تكون قوالب المكدس أكثر تعقيدًا في التصميم مقارنة بالقوالب ذات التجويف الفردي، مما يجعلها أكثر تكلفة في الإنتاج والصيانة.
- انخفاض جودة الأجزاء: يمكن أن تنتج قوالب التكديس أجزاء ذات جودة منخفضة، حيث أن وجود تجاويف متعددة يمكن أن يؤدي إلى زيادة خطر العيوب مثل الوميض، واللقطات القصيرة، وعلامات الغرق.
- زيادة الصيانة: تتطلب قوالب المكدس عادةً مزيدًا من الصيانة مقارنة بالقوالب ذات التجويف الفردي، حيث أن لديها تصميمًا أكثر تعقيدًا يحتاج إلى الحفاظ عليه في حالة عمل جيدة.
قوالب العائلة:
القوالب العائلية، والمعروفة أيضًا باسم قوالب الطباعة المتعددة والتي تشبه قوالب التجاويف المتعددة، هي نوع من قوالب الحقن التي تسمح بتشكيل أجزاء متعددة بتصميمات مختلفة قليلاً في وقت واحد في دورة ماكينة واحدة. يتم تحقيق ذلك من خلال وجود تجاويف متعددة في القالب يمكنها إنتاج أجزاء مختلفة بأشكال وأحجام مختلفة.
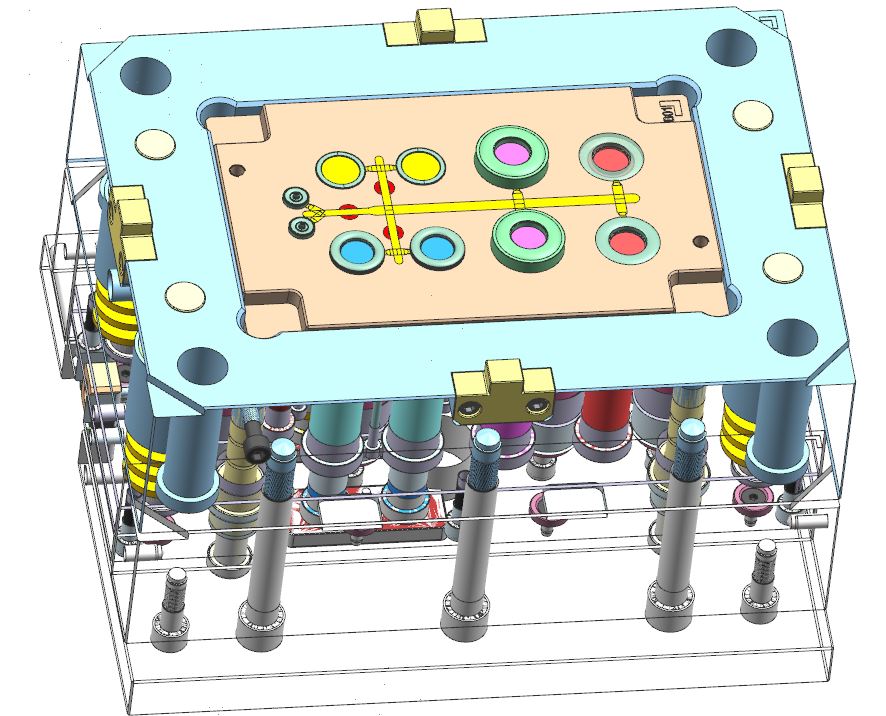
قالب العائلة
تتضمن مزايا قوالب العائلة ما يلي:
- زيادة كفاءة الإنتاج: تسمح القوالب العائلية بتشكيل أجزاء متعددة بتصميمات مختلفة في وقت واحد، مما يزيد من كفاءة الإنتاج ويقلل من وقت الدورة.
- انخفاض التكاليف: يمكن أن تكون القوالب العائلية أكثر فعالية من حيث التكلفة مقارنة بإنتاج قوالب متعددة ذات تجويف واحد لكل جزء، لأنها تسمح بإنتاج أجزاء متعددة بدورة آلة واحدة.
- المرونة: تسمح القوالب العائلية بإنتاج أجزاء مختلفة بتصميمات متنوعة، مما يجعلها خيارًا متعدد الاستخدامات للشركات المصنعة التي تحتاج إلى إنتاج مجموعة من المنتجات.
تشمل عيوب القوالب العائلية ما يلي:
- التصميم المعقد: يمكن أن تكون قوالب العائلة أكثر تعقيدًا في التصميم مقارنة بالقوالب ذات التجويف الفردي، مما يجعلها أكثر تكلفة في الإنتاج والصيانة.
- انخفاض جودة الأجزاء: يمكن أن تنتج القوالب العائلية أجزاء ذات جودة منخفضة، حيث أن وجود تجاويف متعددة يمكن أن يؤدي إلى زيادة خطر العيوب مثل الوميض، واللقطات القصيرة، وعلامات الغرق.
قوالب ذات لقطتين:
قالب ذو لقطتين (حقن القالب بطلقتين)، والمعروفة أيضًا باسم صب فوق القالب أو قوالب متعددة اللقطات أو قوالب 2K، هي نوع من أنواع القولبة بالحقن التي تسمح بتشكيل مادتين مختلفتين معًا في دورة ماكينة واحدة. تتضمن هذه العملية تشكيل مادة أولى (مادة أساسية) في قالب ثم تشكيل مادة ثانية (مادة فوقية) على المادة الأولى.

قالب لقطتين
تتضمن مزايا قوالب اللقطتين ما يلي:
- وظائف متزايدة: تسمح القوالب ذات اللقطتين بدمج مادتين مختلفتين بخصائص مختلفة لإنشاء أجزاء ذات وظائف متزايدة.
- تحسين المظهر الجمالي: تسمح القوالب ذات اللقطتين بدمج ألوان أو أنسجة مختلفة في جزء واحد، مما يؤدي إلى إنشاء منتج أكثر جاذبية من الناحية البصرية.
- تقليل وقت التجميع: من خلال الجمع بين مادتين في جزء واحد، يمكن لقوالب اللقطتين تقليل الحاجة إلى خطوات تجميع إضافية، مما يقلل من وقت الإنتاج والتكاليف.
تشمل عيوب القوالب ذات اللقطتين ما يلي:
- التصميم المعقد: تعتبر القوالب ذات اللقطتين أكثر تعقيدًا في التصميم مقارنة بالقوالب ذات اللقطتين المفردتين، مما يجعلها أكثر تكلفة في الإنتاج والصيانة.
- زيادة وقت الدورة: عادةً ما يكون لقوالب اللقطتين وقت دورة أطول مقارنة بقوالب اللقطتين، حيث تتضمن العملية صب مادتين في دورة آلة واحدة.
- مشكلات التوافق: تتطلب القوالب ذات اللقطتين أن تكون المادتان اللتان يتم تشكيلهما متوافقتين مع بعضهما البعض وأن تلتصقان بشكل صحيح، مما يجعل من المهم اختيار المواد المستخدمة بعناية.
فك القوالب:
قوالب فك البراغي هي نوع من قوالب الحقن المصممة خصيصًا لإنتاج أجزاء ذات خيوط لولبية، مثل الأغطية والأغطية والحاويات. تتميز هذه القوالب بأنها تحتوي على آلية تسمح لقلب القالب بالدوران بينما يظل التجويف ثابتًا، مما يسمح بفك الجزء المصبوب من القالب بعد تبريده وتصلبه.

فك القالب
تتضمن مزايا فك القوالب ما يلي:
- كفاءة عالية: تسمح قوالب الفك بإنتاج فعال للأجزاء الملولبة في دورة آلة واحدة، مما يقلل من وقت الإنتاج والتكاليف.
- دقة محسنة: تسمح قوالب الفك بإنتاج دقيق للأجزاء الملولبة بدرجة ثابتة من الدقة وعمق الخيط، مما يحسن جودة المنتج النهائي وأدائه.
- التنوع: يمكن استخدام قوالب فك البراغي لإنتاج مجموعة متنوعة من الأجزاء المختلفة بأنواع وأحجام خيوط مختلفة، مما يجعلها خيارًا متعدد الاستخدامات للعديد من التطبيقات المختلفة.
تشمل عيوب فك القوالب ما يلي:
- التصميم المعقد: تعتبر قوالب فك البراغي أكثر تعقيدًا في التصميم مقارنة بأنواع أخرى من القوالب، مما يجعلها أكثر تكلفة في الإنتاج والصيانة.
- زيادة وقت الدورة: عادةً ما يكون لقوالب الفك وقت دورة أطول مقارنةً بأنواع أخرى من القوالب، حيث تتضمن العملية تدوير قلب القالب.
- التآكل والتلف: يمكن أن تكون آلية الدوران لقوالب الفك عرضة للتآكل والتلف بمرور الوقت، مما يتطلب صيانة منتظمة للحفاظ على عمل القالب بشكل صحيح.
قالب ذو قلب قابل للطي:
قوالب القلب القابل للطي هي نوع من قوالب الحقن التي تستخدم لإنتاج أجزاء مجوفة ذات تجاويف داخلية، مثل الأنابيب والأنابيب والأجزاء الأخرى ذات الشكل المعقد. تستخدم هذه القوالب تصميمًا فريدًا يسمح لقلب القالب بالانهيار على نفسه، مما يؤدي إلى إنشاء تجويف داخلي للجزء.

مكون القالب ذو القلب القابل للطي
تتضمن مزايا القوالب ذات القلب القابل للطي ما يلي:
- كفاءة محسنة: تسمح القوالب ذات القلب القابل للطي بإنتاج أجزاء مجوفة في دورة آلة واحدة، مما يقلل من وقت الإنتاج والتكاليف.
- تحسين جودة الأجزاء: توفر القوالب ذات القلب القابل للطي تجويفًا داخليًا أكثر دقة وثباتًا، مما يحسن الجودة الشاملة للجزء النهائي.
- التنوع: يمكن استخدام القوالب ذات القلب القابل للطي لإنتاج مجموعة واسعة من الأجزاء المختلفة بأشكال وأحجام مختلفة، مما يجعلها خيارًا متعدد الاستخدامات للعديد من التطبيقات المختلفة.
تشمل عيوب القوالب ذات القلب القابل للطي ما يلي:
- تصميم معقد: تعتبر القوالب ذات القلب القابل للطي أكثر تعقيدًا في التصميم مقارنة بأنواع أخرى من القوالب، مما يجعلها أكثر تكلفة في الإنتاج والصيانة.
- زيادة وقت الدورة: عادةً ما يكون لقوالب القلب القابل للطي وقت دورة أطول مقارنة بأنواع أخرى من القوالب، حيث تتضمن العملية انهيار قلب القالب.
- التآكل والتلف: يمكن أن تكون آلية الانهيار في القلب عرضة للتآكل والتلف بمرور الوقت، مما يتطلب صيانة منتظمة للحفاظ على عمل القالب بشكل صحيح.
مميزات وعيوب قوالب الحقن البلاستيكية
مزايا القولبة بالحقن:
- الإنتاج بكميات كبيرة: تعتبر عملية القولبة بالحقن طريقة فعالة للغاية لإنتاج كميات كبيرة من الأجزاء المتطابقة. وهذا يجعلها مثالية للإنتاج الضخم للسلع الاستهلاكية وقطع غيار السيارات وغيرها من المنتجات التي تتطلب كميات كبيرة من الأجزاء المتشابهة.
- الدقة: تسمح هذه العملية بالتحكم الدقيق للغاية في دقة الأبعاد واتساق الأجزاء. ويرجع هذا إلى استخدام ظروف معالجة خاضعة لرقابة صارمة وصلابة آلة التشكيل والقالب.
- السرعة: عملية القولبة بالحقن هي عملية سريعة، حيث تصل مدة الدورة إلى بضع ثوانٍ فقط للأجزاء الصغيرة. وهذا يسمح للمصنعين بإنتاج كميات كبيرة من الأجزاء في فترة زمنية قصيرة نسبيًا.
- فعالية التكلفة: تصبح تكلفة إنتاج الأجزاء من خلال عملية القولبة بالحقن أكثر اقتصادية مع زيادة حجم الإنتاج. ويرجع هذا إلى حقيقة مفادها أنه يمكن استخدام القالب لإنتاج العديد من الأجزاء على مدار عمره الافتراضي، كما تنخفض تكلفة كل جزء مع زيادة الحجم.
- التنوع: يمكن استخدام عملية القولبة بالحقن لإنتاج أجزاء من مجموعة واسعة من المواد، بما في ذلك البلاستيك والمعادن والمطاط الصناعي. وهذا التنوع يجعلها خيارًا شائعًا للمصنعين الذين يحتاجون إلى إنتاج أجزاء من مواد مختلفة اعتمادًا على المتطلبات المحددة للمنتج.
- الأتمتة: يمكن أتمتة ماكينات قولبة الحقن، مما يجعل العملية أكثر كفاءة ويقلل الحاجة إلى العمل اليدوي. يمكن أن يؤدي هذا أيضًا إلى تحسين اتساق الأجزاء وجودتها.
- الأشكال المعقدة: يمكن استخدام عملية القولبة بالحقن لإنتاج أشكال وتصميمات معقدة، بما في ذلك الأجزاء ذات التفاصيل المعقدة والتفاوتات الضيقة. وهذا ممكن بفضل التحكم الدقيق في عملية القولبة والقدرة على تصميم قوالب عالية التفاصيل.
- اختيار المواد: تسمح عملية القولبة بالحقن للمصنعين بالاختيار من بين مجموعة واسعة من المواد، ولكل منها خصائصها الفريدة، مثل القوة والمرونة ومقاومة الحرارة والمواد الكيميائية والتآكل. وهذا يجعل من الممكن اختيار أفضل مادة لكل تطبيق وإنتاج أجزاء بالخصائص المرغوبة.
عيوب عملية القولبة بالحقن:
- التكلفة الأولية المرتفعة: يمكن أن تكون التكلفة الأولية لإنشاء القالب مرتفعة، وخاصة بالنسبة للأشكال والتصميمات المعقدة. وهذا من شأنه أن يجعل العملية أقل فعالية من حيث التكلفة بالنسبة للكميات الصغيرة من الأجزاء أو النماذج الأولية.
- مرونة التصميم المحدودة: بمجرد إنشاء القالب، قد يكون تغيير التصميم أمرًا صعبًا ومكلفًا. وقد يحد هذا من القدرة على إجراء تغييرات أو تحسينات على التصميم بمجرد إنشاء القالب.
- نفايات المواد: تولد عملية حقن البلاستيك كمية كبيرة من المواد الخردة، والتي قد تكون مكلفة للتخلص منها وضارة بالبيئة. كما يمكن أن يؤدي هذا إلى زيادة تكلفة الإنتاج وتقليل الكفاءة الإجمالية للعملية.
- مهلة التسليم: قد تكون مهلة التسليم اللازمة لإنشاء القالب وإعداد عملية صب الحقن طويلة، وخاصة بالنسبة للأجزاء المعقدة. وقد يؤدي هذا إلى إبطاء عملية تطوير المنتج والحد من القدرة على طرح المنتجات في السوق بسرعة.
- حدود التشطيب السطحي: قد لا تنتج عملية القولبة بالحقن تشطيبًا سطحيًا عالي الجودة لبعض الأجزاء، وخاصة تلك التي تحتوي على تفاصيل معقدة أو تحمُّلات ضيقة. وقد يحد هذا من القدرة على إنتاج أجزاء ذات مظهر جمالي عالي الجودة.
- التوافق بين المواد: قد يشكل التوافق بين المواد والقالب تحديًا، حيث قد لا تعمل بعض المواد بشكل جيد مع أنواع معينة من القوالب أو تتطلب ظروف معالجة خاصة. وقد يحد هذا من القدرة على إنتاج أجزاء من مواد معينة ويزيد من تكلفة الإنتاج.
- حجم القطعة المحدود: إن عملية القولبة بالحقن محدودة بحجم القالب وقوة تثبيت آلة القولبة. وهذا من شأنه أن يحد من حجم الأجزاء التي يمكن إنتاجها ويزيد من تكلفة إنتاج الأجزاء الأكبر حجمًا.
- العمليات الثانوية: قد تتطلب بعض الأجزاء عمليات ثانوية، مثل التشذيب أو التشطيب، بعد تشكيلها. وقد يؤدي هذا إلى زيادة تكلفة الإنتاج والحد من الكفاءة الإجمالية للعملية، وبالطبع يمكن حل هذه المشكلات في بعض الأحيان عن طريق تحسين قالب الحقن
المشاكل الشائعة التي تواجهها قوالب الحقن
بمجرد العمل في مجال قولبة الحقن البلاستيكية، سيكون هناك دائمًا بعض المشكلات التي تحتاج إلى حلها كل يوم، وفيما يلي بعض التحديات الشائعة التي تواجهها في قولبة الحقن:
مشاكل التشويه:
الانحناء هو مشكلة شائعة تواجهها عملية القولبة بالحقن ويشير إلى تشوه أو انحراف الجزء المصبوب الذي يحدث بعد إزالته من القالب. يمكن أن يحدث هذا بسبب مجموعة متنوعة من العوامل، بما في ذلك:

تشوه الانحناء
- التبريد غير السليم: إذا تم تبريد الجزء بسرعة كبيرة أو بشكل غير متساوٍ، فقد يتسبب ذلك في حدوث تشوه حيث تتقلص المادة وتتقلص بمعدلات مختلفة.
- الإجهاد المتبقي: يتسبب القالب بالحقن في إحداث إجهاد متبقي في القطعة بسبب الضغط العالي المستخدم أثناء عملية القالب. يمكن أن يتسبب هذا الإجهاد في حدوث تشوه إذا لم يتم تخفيفه بشكل صحيح.
- اختيار المواد: بعض المواد أكثر عرضة للانحناء من غيرها. على سبيل المثال، المواد ذات المقاومة المنخفضة للحرارة أو الاستقرار الأبعادي المنخفض تكون أكثر عرضة للانحناء.
- تصميم القالب: يمكن أن يساهم تصميم القالب أيضًا في الانحناء، خاصةً إذا كان القالب لا يسمح بالتبريد المناسب أو تدفق المواد.
- ظروف المعالجة: يمكن أن تؤدي ظروف المعالجة غير المتسقة، مثل سرعات الحقن المختلفة، ودرجات حرارة القالب، ومستويات الضغط، إلى حدوث تشوهات.
لمنع الانحناء، من المهم اختيار المادة المناسبة، وتحسين تصميم القالب وظروف المعالجة، وتنفيذ ممارسات التبريد والتعامل مع المواد المناسبة. بالإضافة إلى ذلك، قد يكون من الضروري استخدام معالجات ما بعد القالب، مثل التلدين، لتخفيف الإجهاد المتبقي وتحسين الاستقرار البعدي.
مشاكل الفلاش:
عيوب الوميض هو مصطلح يستخدم في عملية القولبة بالحقن للإشارة إلى المادة الزائدة التي يتم إخراجها قسراً من القالب أثناء عملية القولبة. يحدث الوميض عندما تتدفق المادة خارج تجويف القالب المقصود إلى خط الفصل، أو المساحة بين نصفي القالب.

صب فلاش أو نتوءات
يمكن أن يحدث الفلاش بسبب عدة عوامل، بما في ذلك:
- تصميم القالب غير المناسب: يمكن أن يؤدي القالب المصمم بشكل سيئ إلى حدوث وميض من خلال السماح للمواد بالتسرب إلى خط الفصل.
- ظروف المعالجة غير المتسقة: يمكن أن تؤدي ظروف المعالجة المتغيرة، مثل سرعة الحقن والضغط، إلى حدوث وميض.
- توافق المواد: قد لا تكون بعض المواد متوافقة مع القالب وقد تسبب وميضًا أثناء تدفقها إلى خط الفصل.
- التآكل والتلف في القالب: بمرور الوقت، قد يتآكل القالب ويسبب وميضًا حيث تتسرب المادة إلى خط الفصل.
يمكن أن يكون للوميض العديد من التأثيرات السلبية، بما في ذلك تقليل دقة أبعاد القطعة، وزيادة معدل الخردة، وجعل عمليات ما بعد التشكيل أكثر صعوبة. لتقليل الوميض، من المهم تحسين تصميم القالب وظروف المعالجة واختيار المواد، والصيانة المنتظمة وإصلاح القالب حسب الحاجة.
خطوط اللحام:
خطوط اللحام هي مشكلة شائعة في عملية القولبة بالحقن وتشير إلى علامات مرئية على سطح الجزء المصبوب حيث يلتقي تياران من مادة البلاستيك المنصهرة ويتصلبان. تحدث خطوط اللحام عندما لا تندمج المادة معًا بشكل كامل أثناء تدفقها إلى قالب بلاستيكي تجويف يترك خطًا مرئيًا على سطح الجزء.

خط اللحام
يمكن أن تحدث خطوط اللحام بسبب عدة عوامل، بما في ذلك:
- تدفق غير كافٍ للذوبان: إذا لم يكن لدى المادة الوقت الكافي للتدفق والاندماج الكامل معًا، فقد يتشكل خط لحام.
- تصميم غير مناسب للبوابة: يمكن للبوابة المصممة بشكل سيئ، وهي النقطة التي تدخل منها المادة المنصهرة إلى تجويف القالب، أن تتسبب في حدوث خط لحام.
- ظروف المعالجة غير المتسقة: يمكن أن تؤدي ظروف المعالجة المتغيرة، مثل سرعة الحقن والضغط، إلى حدوث خط لحام.
- توافق المواد: قد لا تكون بعض المواد متوافقة مع القالب وقد تتسبب في حدوث خط لحام أثناء تدفقها إلى تجويف القالب.
يمكن أن تؤدي خطوط اللحام إلى إضعاف قوة القطعة وتقليل جودتها الإجمالية. لتقليل خطوط اللحام، من المهم تحسين تصميم القالب وظروف المعالجة واختيار المواد وتنفيذ ممارسات مناولة المواد المناسبة. بالإضافة إلى ذلك، قد يكون من الضروري استخدام تقنيات معالجة خاصة، مثل قوالب متعددة التجاويف أو أنظمة المجرى الساخن، لتقليل تكوين خطوط اللحام.
علامات الحوض:
علامات الغرق، والمعروفة أيضًا باسم "الغرق" أو "الغرق الفراغي" أو "الجلد"، هي مناطق غائرة أو منخفضة على سطح جزء بلاستيكي مصبوب بالحقن. وعادةً ما تكون ناجمة عن عدد من العوامل، بما في ذلك:
- انكماش الراتينج: عندما يبرد الراتينج ويتصلب، فإنه قد يتقلص بشكل غير متساوٍ، مما يؤدي إلى ظهور علامات الغرق.
- تدفق المواد الضعيف: إذا لم يتدفق الراتينج بالتساوي في جميع مناطق القالب، فقد يؤدي ذلك إلى إنشاء فراغات أو مناطق غائرة.
- ضغط التعبئة غير الكافي: إذا لم يكن ضغط الحقن مرتفعًا بدرجة كافية، فقد لا يملأ الراتينج القالب بالكامل، مما يؤدي إلى ظهور علامات الغرق.
- مشاكل تصميم القالب: يمكن أن يؤثر تصميم القالب، بما في ذلك وضع البوابة وحجمها ونظام الجري والتهوية، على جودة الجزء المصبوب وقد يساهم في ظهور علامات الغرق.
يمكن أن تؤثر علامات الغرق على الجودة الجمالية ووظيفة القطعة المصبوبة ويمكن أن تكون مصدر إحباط للمصنعين والمستخدمين النهائيين. لتقليل علامات الغرق، من المهم النظر بعناية في العوامل التي تساهم فيها، مثل اختيار المواد وتصميم القالب ومعايير المعالجة وتصميم القطعة، وإجراء التعديلات حسب الحاجة لتحسين عملية القولبة بالحقن.
علامات التدفق:
تعتبر علامات التدفق مشكلة شائعة في عملية القولبة بالحقن وتشير إلى علامات أو خطوط مرئية على سطح الجزء المصبوب والتي تحدث بسبب تدفق مادة البلاستيك المذابة أثناء ملء تجويف القالب. تحدث علامات التدفق عندما تتدفق المادة بشكل غير متساوٍ، تاركة وراءها علامة مرئية على سطح الجزء.
يمكن أن تحدث علامات التدفق بسبب عدة عوامل، بما في ذلك:
- تدفق غير كافي للذوبان: إذا لم يكن لدى المادة الوقت الكافي للتدفق وملء تجويف القالب، فقد تتشكل علامات التدفق.
- تصميم غير مناسب للبوابة: يمكن للبوابة ذات التصميم السيئ، وهي النقطة التي تدخل منها المادة المنصهرة إلى تجويف القالب، أن تتسبب في ظهور علامات التدفق.
- ظروف المعالجة غير المتسقة: يمكن أن تؤدي ظروف المعالجة المتغيرة، مثل سرعة الحقن والضغط، إلى ظهور علامات التدفق.
- توافق المواد: قد لا تكون بعض المواد متوافقة مع القالب وقد تسبب علامات تدفق أثناء تدفقها إلى تجويف القالب.
يمكن أن تؤدي علامات التدفق إلى تقليل الجودة الشاملة والمظهر الجمالي للقطعة. لتقليل علامات التدفق، من المهم تحسين تصميم القالب وظروف المعالجة واختيار المواد وتنفيذ ممارسات مناولة المواد المناسبة. بالإضافة إلى ذلك، قد يكون من الضروري استخدام تقنيات معالجة خاصة، مثل قوالب متعددة التجاويف أو أنظمة الجري الساخن، لتقليل تكوين علامات التدفق.
مشاكل الخدش:
تشير مشكلات الخدش إلى العلامات أو الخدوش المرئية على سطح جزء مصبوب بالحقن والتي تحدث بسبب التلامس المادي بين الجزء والقالب أو الأجسام الغريبة الأخرى أثناء عملية الصب. يمكن أن تحدث مشكلات الخدش لعدة أسباب، بما في ذلك:
- تصميم القالب السيئ: يمكن أن تتسبب القوالب أو مكونات القالب المصممة بشكل غير صحيح في حدوث خدوش على سطح القطعة.
- عدم التشحيم الكافي: إذا لم يتم تشحيم القالب ومكونات القالب بشكل صحيح، فقد يتسبب ذلك في حدوث خدوش على سطح القطعة.
- سوء التعامل مع المواد: قد يؤدي سوء التعامل مع المواد الخام أو الأجزاء النهائية إلى حدوث خدوش على سطح القطعة.
- الحطام في القالب: يمكن للأجسام الغريبة أو الحطام الموجود في تجويف القالب أن يسبب خدوشًا على سطح القطعة.
يمكن أن تؤدي مشكلات الخدش إلى تقليل الجودة الشاملة والمظهر الجمالي للقطعة. لتقليل مشكلات الخدش، من المهم تنفيذ تصميم القالب والتزييت ومناولة المواد وممارسات الصيانة المناسبة. بالإضافة إلى ذلك، يمكن أن يساعد التنظيف والتفتيش المنتظم للقالب ومكونات القالب في منع حدوث مشكلات الخدش.
علامات القاذف:
علامات القذف هي علامات مرئية على سطح جزء مصبوب بالحقن والتي تسببها دبابيس القذف أو آليات القذف الأخرى أثناء عملية الصب. تحدث علامات القذف عندما تدفع دبابيس القذف الجزء المصبوب خارج تجويف القالب وتترك وراءها علامات مرئية على سطح الجزء.
يمكن أن تحدث علامات القاذف بسبب عدة عوامل، بما في ذلك:
- تصميم دبوس القذف غير المناسب: إذا لم يتم تصميم دبابيس القذف بشكل صحيح، فإنها يمكن أن تترك علامات مرئية على سطح الجزء.
- القوة المفرطة: إذا كانت دبابيس القذف تطبق قوة مفرطة على الجزء أثناء القذف، فإنها يمكن أن تترك علامات أعمق وأكثر وضوحًا على سطح الجزء.
- قوة القذف غير المتسقة: إذا لم تكن قوة القذف متسقة من دبوس قذف واحد إلى آخر، فقد يؤدي ذلك إلى ظهور علامات قذف غير متساوية على سطح القطعة.
- تشطيب سطح رديء: إذا لم يكن تشطيب سطح تجويف القالب ناعمًا، فقد يتسبب ذلك في ظهور علامات القاذف على سطح القطعة.
يمكن أن تؤدي علامات القذف إلى تقليل الجودة الشاملة والمظهر الجمالي للقطعة. لتقليل علامات القذف، من المهم تحسين تصميم دبابيس القذف واللمسة النهائية لسطح تجويف القالب، وتنفيذ ممارسات الصيانة والتفتيش المناسبة. بالإضافة إلى ذلك، قد يكون من الضروري استخدام آليات قذف خاصة، مثل القذف بمساعدة الهواء أو القذف الجانبي، لتقليل علامات القذف.
قضايا قصيرة المدى:
تعتبر الطلقة القصيرة مشكلة شائعة في عملية القولبة بالحقن تحدث عندما لا تملأ المادة البلاستيكية المنصهرة تجويف القالب بالكامل، مما يؤدي إلى جزء مصبوب أصغر من الحجم المطلوب. يمكن أن تحدث الطلقات القصيرة لعدة أسباب، بما في ذلك:
- مادة غير كافية: إذا لم تكن هناك مادة كافية لملء تجويف القالب، فقد يحدث لقطة قصيرة.
- ظروف المعالجة غير المناسبة: إذا لم يتم ضبط ظروف المعالجة، مثل سرعة الحقن والضغط، بشكل صحيح، فقد يحدث لقطة قصيرة.
- تصميم سيئ للقالب: يمكن أن يؤدي القالب المصمم بشكل سيئ إلى حدوث لقطة قصيرة، حيث قد لا تتمكن المادة من التدفق إلى جميع مناطق تجويف القالب.
- تدهور المواد: إذا تدهورت المادة أو لم يتم تخزينها بشكل صحيح، فقد يؤدي ذلك إلى حدوث لقطة قصيرة.
يمكن أن تؤدي اللقطات القصيرة إلى تقليل الجودة الشاملة ووظائف القطعة وتؤدي إلى إهدار المواد ووقت المعالجة. لتقليل اللقطات القصيرة، من المهم تحسين تصميم القالب وظروف المعالجة واختيار المواد وتنفيذ ممارسات مناولة المواد المناسبة. بالإضافة إلى ذلك، يمكن أن تساعد المراقبة والصيانة المنتظمة لمعدات القولبة في منع حدوث اللقطات القصيرة.
فخ الهواء وعلامات الحروق:
تعتبر مصائد الهواء وعلامات الحروق من المشكلات الشائعة في عملية القولبة بالحقن والتي قد تحدث بسبب ظروف المعالجة غير المناسبة أو تصميم القالب.
تحدث مصائد الهواء عندما يتم حبس الهواء في تجويف القالب أثناء عملية القولبة بالحقن، مما يتسبب في تدفق المادة حول جيب الهواء بدلاً من ملئه. يمكن أن يؤدي هذا إلى ظهور فراغات أو جيوب مرئية في الجزء المصبوب. يمكن أن تحدث مصائد الهواء بسبب عدة عوامل، بما في ذلك:
- عدم تدفق المواد بشكل كافٍ: إذا لم تتدفق المواد بشكل صحيح إلى تجويف القالب، فقد يصبح الهواء محاصرًا.
- تصميم غير مناسب للبوابة: إذا لم يتم تصميم البوابة بشكل صحيح، فقد يحاصر الهواء في تجويف القالب.
- التهوية غير الكافية: إذا لم يتم تهوية القالب بشكل صحيح، يمكن أن يحبس الهواء في تجويف القالب.
تحدث علامات الحرق عندما تتعرض المادة البلاستيكية لدرجات حرارة عالية لفترة طويلة جدًا، مما يؤدي إلى تدهورها وإنتاج علامات مرئية أو تغير في اللون على سطح القطعة. يمكن أن تحدث علامات الحرق بسبب عدة عوامل، بما في ذلك:
- درجات حرارة المعالجة المفرطة: إذا تم ضبط درجات حرارة المعالجة على درجة عالية جدًا، فقد تتدهور المادة وتنتج علامات حرق.
- وقت تبريد غير كافٍ: إذا لم يتم تبريد الجزء بشكل صحيح، فقد تتدهور المادة وتنتج علامات حرق.
- تصميم سيئ للقالب: يمكن أن يؤدي القالب المصمم بشكل سيئ إلى تعرض المادة لدرجات حرارة عالية لفترة طويلة جدًا، مما يؤدي إلى ظهور علامات حرق.
لتقليل مصائد الهواء وعلامات الحرق، من المهم تحسين ظروف المعالجة وتصميم القالب، وتنفيذ ممارسات المراقبة والصيانة المناسبة. بالإضافة إلى ذلك، قد يكون من الضروري استخدام تقنيات معالجة خاصة، مثل القولبة في درجات حرارة منخفضة أو القولبة بالفراغ، لتقليل مصائد الهواء وعلامات الحرق.
المعالجة لصنع قالب الحقن:
تتضمن عملية تصنيع قالب الحقن عدة خطوات:
تصميم القالب:
يعد تصميم قالب الحقن جانبًا مهمًا في عملية القولبة بالحقن، لأنه يؤثر بشكل مباشر على جودة وكفاءة وتكلفة الأجزاء المصبوبة.
إن قالب الحقن المصمم جيدًا سوف ينتج أجزاء تلبي الحجم والشكل ومتطلبات الجودة المطلوبة، مع كونها أيضًا فعالة في الإنتاج وسهلة الصيانة.
تشمل العوامل الرئيسية التي يجب مراعاتها عند تصميم قالب الحقن ما يلي:
- هندسة الجزء: يجب أن يأخذ تصميم الجزء المصبوب في الاعتبار الحجم والشكل والميزات المطلوبة للجزء.
- اختيار المواد: يجب اختيار المواد المستخدمة في القالب والجزء المصبوب بناءً على عوامل مثل التكلفة والقوة والاستقرار الحراري.
- تجاويف القالب: يجب اختيار عدد وترتيب تجاويف القالب لتلبية متطلبات حجم الإنتاج.
- نظام البوابة: يعد تصميم نظام البوابة أمرًا بالغ الأهمية، لأنه يحدد كيفية تدفق المادة البلاستيكية إلى تجويف القالب.
- نظام القذف: يجب تصميم نظام القذف لضمان إمكانية إزالة الأجزاء المصبوبة من القالب دون حدوث أي ضرر.
- نظام التبريد: يجب تصميم نظام التبريد لضمان تبريد الأجزاء المصبوبة بالتساوي وبسرعة، مما يقلل من وقت الدورة ويحسن الجودة.
- زوايا السحب: يجب أن يتضمن تصميم القالب زوايا سحب مناسبة للسماح بإزالة الأجزاء المصبوبة من القالب.
- التهوية: يجب تهوية القالب للسماح للهواء بالخروج من تجويف القالب، مما يقلل من خطر احتباس الهواء وعلامات الحروق.
- الصيانة والإصلاح: يجب تصميم القالب ليكون سهل الصيانة والإصلاح، لتقليل وقت التوقف وزيادة كفاءة الإنتاج.
يعد تصميم قوالب الحقن عملية معقدة تتطلب خبرة في مجالات مثل الهندسة الميكانيكية وعلوم المواد والتصنيع. من المهم العمل مع مصمم قوالب حسن السمعة لضمان تصميم القالب بشكل صحيح وتلبية احتياجاتك.
برمجة CNC:
تعتبر برمجة التحكم الرقمي بالحاسوب (CNC) خطوة أساسية في تصنيع قالب الحقن. بمجرد الانتهاء من تصميم القالب، تكون الخطوة التالية هي برمجة التحكم الرقمي بالحاسوب. فيما يلي الخطوات الرئيسية المتضمنة في برمجة التحكم الرقمي بالحاسوب لتصنيع قالب الحقن:
- ترجمة نموذج CAD: يتم ترجمة نموذج CAD إلى برنامج التصنيع بمساعدة الكمبيوتر (CAM)، والذي يستخدم لإنشاء كود CNC للقالب.
- إنشاء كود CNC: يتم إنشاء كود CNC في برنامج CAM، والذي يوفر تعليمات لآلة CNC حول كيفية تحريك وقطع مكونات القالب. يأخذ الكود في الاعتبار مادة وسمك مكونات القالب، بالإضافة إلى الأشكال والميزات المطلوبة.
- إنشاء مسار الأداة: يتم إنشاء مسار الأداة في برنامج CAM، والذي يحدد المسار الذي ستتبعه أداة القطع لتصنيع مكونات القالب. يأخذ مسار الأداة في الاعتبار أشكال وخصائص مكونات القالب وقدرات آلة CNC.
- المحاكاة: يتم محاكاة كود CNC ومسار الأداة في برنامج CAM للتأكد من أن مكونات القالب سيتم تشغيلها بشكل صحيح ووفقًا للمواصفات الصحيحة.
- التصنيع باستخدام الحاسب الآلي: يتم تحميل كود CNC في آلة CNC، والتي تستخدم بعد ذلك الكود ومسار الأداة لتصنيع مكونات القالب.
تعتبر برمجة CNC خطوة بالغة الأهمية في عملية تصنيع قوالب الحقن، حيث تحدد دقة وجودة مكونات القالب. ومن المهم العمل مع مبرمج CNC لديه خبرة في برمجة قوالب الحقن لضمان إنشاء كود CNC بشكل صحيح ووفقًا للمواصفات الصحيحة. وهذه الخطوة هي أيضًا حيث تتم إضافة قنوات التبريد الخاصة بالقالب ونظام القذف والميزات الأخرى إلى مكونات القالب لضمان عملها بشكل صحيح.
شراء قائمة المواد الخام للقوالب
قائمة المواد الخام للقوالب هي قائمة شاملة لجميع المكونات والمواد اللازمة لتصنيع قالب الحقن. وهي تتضمن العناصر التالية:
- فولاذ لقاعدة القالب وإدخالات القلب/التجويف
- مكونات العداء الساخن
- مكونات نظام التبريد، مثل خطوط المياه وكتل التبريد
- مكونات نظام القذف، مثل دبابيس القذف والأكمام
- مكونات ساحب المجرى
- أشرطة التدفئة ووحدات التحكم في درجة الحرارة
- مكونات القالب، مثل البطانات ودبابيس التوجيه وأجهزة القفل
- إدخالات القالب، مثل الشرائح والرافعات
- العناصر المتخصصة، مثل طوابع التاريخ والشعارات المخصصة
قائمة المواد الخام للقوالب هي أداة مهمة للشراء والتصنيع، حيث توفر قائمة واضحة ومفصلة بالمكونات والمواد اللازمة لإنتاج القالب. يتم استخدامها لضمان طلب جميع المكونات الضرورية وتوافرها عندما يكون القالب جاهزًا للتصنيع.
من المهم العمل مع مورد حسن السمعة عند شراء مكونات قالب الحقن، حيث أن جودة وموثوقية هذه المكونات يمكن أن يكون لها تأثير كبير على كفاءة وجودة عملية قولبة الحقن.
تصنيع القوالب الخام:
يشير التشغيل الخشن لقالب الحقن إلى التشغيل الأولي للمكونات الفولاذية لقالب الحقن لتحقيق الشكل والحجم الأساسي للقالب. تتم هذه الخطوة عادةً باستخدام آلات التحكم العددي بالحاسوب (CNC). فيما يلي الخطوات الرئيسية المشاركة في التشغيل الخشن لقالب الحقن:
- اختيار الفولاذ: الخطوة الأولى هي اختيار نوع الفولاذ المناسب للقالب، مثل P20 أو H13، بناءً على الخصائص المطلوبة للجزء المصبوب.
- قطع الفولاذ: يتم قطع الفولاذ بالحجم والشكل المناسبين باستخدام آلة CNC. قد تتضمن هذه الخطوة أيضًا حفر وتركيب ثقوب لأنظمة التبريد والقذف.
- تشكيل الفولاذ: يتم بعد ذلك تصنيع مكونات الفولاذ لتحقيق الشكل الأساسي للقالب، بما في ذلك إدخالات القلب والتجويف.
- فحص الفولاذ: يتم بعد ذلك فحص المكونات المصنعة للتأكد من أنها تلبي التسامحات والمواصفات المطلوبة.
- تنظيف الفولاذ: يتم تنظيف المكونات الميكانيكية وإزالة النتوءات منها لإزالة أي حواف خشنة أو حطام.
تعتبر عملية التصنيع الخشن خطوة مهمة في عملية القولبة بالحقن، حيث أنها تضع الأساس لخطوات التصنيع والتلميع النهائية عالية الدقة التي ستليها. من المهم التأكد من أن التصنيع الخشن يتم بدقة ووفقًا للمواصفات الصحيحة لضمان عمل القالب بشكل صحيح وإنتاج الأجزاء بالجودة المطلوبة.
المعالجة الحرارية لقالب الفولاذ:
المعالجة الحرارية للفولاذ القالبي هي عملية تسخين وتبريد مكونات الفولاذ في قالب الحقن لتحسين خصائصها الميكانيكية واستقرارها البعدي. الغرض من المعالجة الحرارية هو تقوية الفولاذ وتخفيف الضغوط المتبقية وتحسين مقاومته للتآكل ومتانته. هذا مخصص بشكل خاص للفولاذ المقسى لقالب الحقن، إذا كنت تستخدم فولاذًا مقسى مسبقًا لصنع قالب الحقن فلا داعي للقيام بأعمال المعالجة الحرارية هذه. فيما يلي الخطوات الرئيسية المتضمنة في المعالجة الحرارية للفولاذ القالبي:
- التلدين: يتم تسخين مكونات الفولاذ إلى درجة حرارة محددة، عادة ما بين 800-900 درجة مئوية، ثم يتم تبريدها ببطء لتخفيف الضغوط الداخلية وتحسين قابلية تصنيع الفولاذ.
- التصلب: يتم تسخين مكونات الفولاذ إلى درجة حرارة عالية، عادة أعلى من درجة الحرارة الحرجة، ثم يتم تبريدها بسرعة، عادة عن طريق التبريد في الزيت أو الماء. تعمل هذه العملية على تصلب الفولاذ وتحسين مقاومته للتآكل.
- التقسية: بعد التصلب، يتم تقسية مكونات الفولاذ عن طريق تسخينها إلى درجة حرارة أقل لمدة زمنية محددة لتحسين صلابة الفولاذ واستقراره الأبعادي.
تعتبر عملية المعالجة الحرارية بالغة الأهمية لضمان أن تتمتع المكونات الفولاذية لقالب الحقن بالخصائص الميكانيكية المطلوبة والاستقرار البعدي، وهو أمر ضروري لإنتاج أجزاء مصبوبة عالية الجودة. من المهم العمل مع مزود معالجة حرارية يتمتع بخبرة في معالجة الفولاذ المصبوب لضمان إجراء عملية المعالجة الحرارية بشكل صحيح ووفقًا للمواصفات الصحيحة.
التشغيل الدقيق لتجويف القالب واللب:
إن المعالجة الدقيقة لتجويف القالب واللب هي عملية معالجة دقيقة للأسطح الداخلية لتجويف القالب والحشوات الأساسية لتحقيق الشكل والحجم النهائي للقالب. تتم هذه الخطوة عادةً باستخدام آلات التحكم الرقمي بالحاسوب (CNC) ذات الدقة العالية. فيما يلي الخطوات الرئيسية المتضمنة في المعالجة الدقيقة لتجويف القالب واللب:
- إعداد السطح: يتم تنظيف وتلميع سطح تجويف القالب وإدخالات القلب لإزالة أي حطام متبقي أو خشونة.
- تصنيع الأسطح: تتم معالجة الأسطح الداخلية لتجويف القالب والأجزاء الداخلية باستخدام آلات CNC لتحقيق الشكل والحجم النهائيين للقالب. ويشمل ذلك إنشاء التفاصيل والميزات المعقدة للجزء المصبوب، مثل النصوص والشعارات والتخفيضات.
- فحص السطح: يتم فحص الأسطح المصنعة للتأكد من أنها تلبي التسامحات والمواصفات المطلوبة.
- تلميع السطح: يتم تلميع الأسطح الداخلية لتجويف القالب وإدخالات القلب إلى مستوى عالٍ لتحسين جودة سطح الأجزاء المصبوبة وتقليل مخاطر العيوب.
تعد المعالجة الدقيقة خطوة بالغة الأهمية في عملية القولبة بالحقن، حيث إنها تحدد جودة ودقة الأجزاء المصبوبة. ومن المهم العمل مع مزود معالجة يتمتع بخبرة في المعالجة الدقيقة لتجويف القالب واللب لضمان إجراء المعالجة بشكل صحيح ووفقًا للمواصفات الصحيحة. كما يتم في هذه الخطوة إضافة نظام إخراج القالب وقنوات التبريد والميزات الأخرى لضمان الأداء السليم للقالب.
تصنيع EDM:
EDM (التشغيل بالتفريغ الكهربائي) هي عملية تستخدم لصنع أشكال معقدة ودقيقة للغاية في الأجزاء المعدنية، بما في ذلك تلك الموجودة في قالب الحقن. تستخدم العملية شرارات كهربائية لإزالة المواد من سطح القالب، مما يؤدي إلى إنشاء الشكل المطلوب. فيما يلي الخطوات الرئيسية المشاركة في التشغيل بالتفريغ الكهربائي:
- إعداد السطح: يتم تنظيف سطح مكون القالب المراد تشغيله وتلميعه لإزالة أي حطام متبقي أو خشونة.
- إعداد EDM: يتم إعداد آلة EDM بالمعلمات الصحيحة، بما في ذلك فجوة الشرارة، ومدة النبضة، ومادة القطب، بناءً على مادة وشكل مكون القالب.
- التآكل بالشرارة: تنتج آلة EDM شرارات كهربائية تعمل على إزالة المادة من مكون القالب، مما يؤدي إلى إنشاء الشكل المطلوب. تتم هذه العملية بشكل تدريجي، حيث تعمل آلة EDM على تآكل المادة تدريجيًا حتى يتم تحقيق الشكل النهائي.
- فحص السطح: يتم فحص السطح الميكانيكي للتأكد من أنه يلبي التسامحات والمواصفات المطلوبة.
تُستخدم عملية تصنيع EDM غالبًا في تصنيع مكونات القوالب ذات الأشكال المعقدة أو التفاصيل الصغيرة المعقدة التي يصعب تحقيقها باستخدام عمليات تصنيع أخرى. كما تُستخدم أيضًا لإنتاج الحواف والزوايا الحادة الضرورية للعمل السليم لقالب الحقن.
تتميز هذه العملية بالدقة والإتقان الشديدين، مما يجعلها مثالية لإنتاج أجزاء مصبوبة عالية الجودة. من المهم العمل مع مزود EDM الذي يتمتع بخبرة في تصنيع EDM لقوالب الحقن لضمان تنفيذ العملية بشكل صحيح ووفقًا للمواصفات الصحيحة.
تلميع سطح القالب:
تلميع قوالب الحقن هي الخطوة الأخيرة في عملية تصنيع قالب الحقن. وهي تتضمن تنعيم أسطح مكونات القالب لضمان أن المنتج النهائي له سطح أملس ومستوٍ. فيما يلي الخطوات الرئيسية التي تنطوي عليها عملية تلميع قالب الحقن:

تلميع قوالب البلاستيك
- إعداد السطح: يتم تنظيف أسطح مكونات القالب وتجهيزها للتلميع. تتم إزالة أي بقع خشنة أو علامات تشغيل متبقية لضمان سطح أملس للتلميع.
- التلميع الخشن: الخطوة الأولى في التلميع هي التلميع الخشن، والذي يتضمن إزالة أي عيوب كبيرة في سطح مكونات القالب. تتم هذه الخطوة عادةً باستخدام مادة كاشطة خشنة، مثل ورق الصنفرة أو فرشاة الصنفرة.
- التلميع الناعم: التلميع الناعم هو الخطوة التالية، والتي تتضمن تنعيم سطح مكونات القالب للحصول على تشطيب ناعم. تتم هذه الخطوة باستخدام مادة كاشطة ذات حبيبات ناعمة، مثل ورق الصنفرة الناعم أو فرشاة الصنفرة.
- التلميع: التلميع هو الخطوة الأخيرة في التلميع، والتي تتضمن استخدام عجلة التلميع ومركب التلميع لتحقيق لمسة نهائية شديدة اللمعان على مكونات القالب.
- التفتيش: بعد التلميع، يتم فحص مكونات القالب بدقة للتأكد من أنها ذات سطح أملس ومتساوي، بدون خدوش أو شقوق أو أي عيوب أخرى.
إن صقل قوالب الحقن أمر مهم لأنه يؤثر على جودة المنتج النهائي. فالقوالب المصقولة جيدًا تنتج منتجًا بسطح أملس ومستوٍ، وهو أمر مهم لوظائف المنتج وجمالياته. ومن المهم العمل مع مصقول قوالب ذي خبرة لضمان صقل مكونات القالب وفقًا للمواصفات الصحيحة ومستوى الجودة المطلوب.
تركيب القالب
تركيب القالب هو وظيفة متخصصة في مجال حقن القالب وتتضمن تجميع وتركيب واختبار قوالب الحقن. ويتحمل خبراء القالب مسؤولية التأكد من تجميع مكونات القالب بشكل صحيح وعملها بشكل صحيح، وأن القالب ينتج أجزاء بمعايير الجودة والأداء المطلوبة. وتتضمن بعض المسؤوليات الرئيسية لخبراء تركيب القالب ما يلي:
- تجميع مكونات القالب: يكون صانعو القالب مسؤولين عن تجميع المكونات المختلفة لقالب الحقن، بما في ذلك مكونات التجويف والقلب، ونظام التشغيل، وأي مكونات مساعدة.
- تركيب القالب على آلة تركيب القالب: يجب أن يكون Moldmaster قادرًا على تركيب القالب على آلة تركيب القالب بطريقة تضمن المحاذاة الصحيحة وعمل القالب، إذا لم يكن لديه أي آلة تركيب قالب، فاستخدم الطريقة اليدوية لتركيب القالب، وهذا ما تفعله معظم الشركات.
- اختبار القالب: يكون صانع القالب مسؤولاً عن اختبار القالب للتأكد من أنه ينتج أجزاءً وفقًا لمعايير الجودة والأداء المطلوبة. ويتضمن ذلك فحص الأجزاء بحثًا عن أي عيوب، مثل الانحناء أو الانكماش أو مشكلات الجودة الأخرى.
- ضبط القالب: إذا تم العثور على أي مشاكل أثناء مرحلة الاختبار، يكون صانع القالب مسؤولاً عن إجراء أي تعديلات ضرورية على القالب لضمان إنتاج أجزاء تلبي المواصفات المطلوبة.
- استكشاف الأخطاء وإصلاحها: يجب أن يكون Moldmaster قادرًا على تحديد واستكشاف أي مشاكل قد تنشأ أثناء عملية تركيب القالب.
تتطلب أعمال تركيب القوالب مزيجًا من المعرفة الفنية والبراعة اليدوية والاهتمام بالتفاصيل. يجب أن يكون صانعو القوالب قادرين على العمل بمجموعة واسعة من الأدوات والآلات، بالإضافة إلى فهم العمليات المعقدة المشاركة في عملية صب الحقن. من المهم أن يكون لدى صانعي القوالب فهم جيد لعملية صب الحقن، بالإضافة إلى الخبرة في العمل مع أنواع مختلفة من القوالب والمواد.
أول تجربة أو تصوير لقوالب الحقن:
تشير عملية اختبار حقن القالب إلى عملية اختبار قالب الحقن لإنتاج جزء عينة باستخدام عملية حقن القالب. تعد هذه العملية خطوة بالغة الأهمية في عملية حقن القالب، حيث إنها تسمح للمصنع بتقييم أداء القالب وإجراء أي تعديلات ضرورية قبل إنتاج كمية كبيرة من الأجزاء.
تتضمن عملية تجربة عملية حقن القالب عادةً الخطوات التالية:
- التحضير: يتم تثبيت القالب على آلة التشكيل بالحقن ويتم إعداد الآلة للرصاصة. يتم ملء القادوس بالراتنج البلاستيكي.
- التحكم في درجة حرارة الذوبان: يتم التحكم في درجة حرارة الذوبان لضمان تسخين الراتينج البلاستيكي إلى درجة الحرارة الصحيحة لإنتاج أجزاء عالية الجودة.
- الحقن: يتم حقن البلاستيك المنصهر في القالب تحت ضغط مرتفع، ويتم الحفاظ على الضغط حتى يمتلئ القالب بالراتنج البلاستيكي.
- التبريد: يتم تبريد القالب لتصلب الراتينج البلاستيكي وتشكيل القطعة. يتم تحديد وقت التبريد حسب نوع الراتينج البلاستيكي المستخدم وحجم وشكل القطعة التي يتم إنتاجها.
- القذف: بمجرد تصلب القطعة، يتم إزالتها من القالب. يتم استخدام دبابيس القذف لدفع القطعة خارج القالب.
- التفتيش: يتم فحص الجزء المنتج من القالب بدقة للتأكد من أنه يلبي المواصفات والمعايير الجودة المطلوبة.
- التعديلات: إذا لزم الأمر، يمكن إجراء تعديلات على عملية التشكيل لتحسين أداء القالب وجودة الأجزاء التي يتم إنتاجها.
تعتبر عملية التصوير التجريبي لقوالب الحقن خطوة مهمة في عملية حقن القالب، حيث تسمح للمصنع بتقييم أداء القالب وإجراء أي تعديلات ضرورية قبل إنتاج كمية كبيرة من الأجزاء. تساعد هذه العملية على ضمان أن القالب ينتج أجزاء عالية الجودة بالمواصفات المطلوبة.
تعبئة القالب وتجهيزه للإنتاج:
بمجرد الانتهاء من القالب بالكامل بواسطة صانع القالب، فإن الخطوة التالية هي الإنتاج الضخم. تعد تعبئة القالب وإعداده للإنتاج الخطوة الأخيرة في عملية صب الحقن قبل أن يبدأ الإنتاج الضخم. تتضمن هذه الخطوة المهام التالية:
- التنظيف والصيانة: يتم تنظيف القالب جيدًا وفحصه للتأكد من عدم وجود أي حطام أو أوساخ أو ضرر في القالب.
- التعبئة والتخزين: يتم تعبئة القالب بعناية وتخزينه في مكان آمن لمنع التلف والتأكد من أنه جاهز للاستخدام عند الحاجة إليه.
- الاختبار والتعديل: يتم اختبار القالب بحثًا عن أي مشكلات، مثل التسربات أو الملء السيئ أو إخراج الأجزاء بشكل غير صحيح، ويتم إجراء أي تعديلات ضرورية لضمان عمل القالب بشكل صحيح.
- إعداد الإنتاج: يتم تثبيت القالب في آلة القولبة بالحقن ويتم ضبط جميع الإعدادات الضرورية، مثل درجة الحرارة والضغط وسرعة الحقن، لتلبية متطلبات الإنتاج المحددة.
- بدء الإنتاج: يتم إنتاج الدفعة الأولى من الأجزاء، ويتم مراقبة العملية للتأكد من أن الأجزاء تلبي المواصفات المطلوبة ومعايير الجودة. يتم إجراء أي تعديلات ضرورية لتحسين عملية الإنتاج وضمان الجودة الثابتة.
بشكل عام، يعد تحضير القالب للإنتاج خطوة مهمة في عملية القولبة بالحقن والتي تساعد على ضمان نجاح وكفاءة عملية الإنتاج.
المعلومات المذكورة أعلاه هي إجراءات لصنع قالب الحقن، ربما هناك بعض الأشياء الصغيرة التي تم تفويتها ولكن معظم الأشياء المذكورة أعلاه، كما ترون صنع قالب الحقن ليس بالأمر السهل، إذا كان لديك مشروع قالب حقن في التعامل معه، فأنت بحاجة إلى العثور على صانع قالب حقن محترف لخدمتك، وهذا سيضمن تشغيل مشروعك بنجاح.
Sincere Tech هو محترف قالب صيني مصنع متخصص في تصنيع قوالب الحقن المخصصة. لديهم خبرة ومهارة في تصميم وتطوير وإنتاج قوالب الحقن عالية الجودة لمختلف الصناعات والتطبيقات.
إنهم يقدمون مجموعة من الخدمات، بما في ذلك تصميم القالب، والنماذج الأولية، وإنتاج القالب، ومعالجة ما بعد القالب، لضمان حصول عملائهم على أفضل النتائج الممكنة. مع تركيزهم على الجودة والدقة ورضا العملاء، فإن Sincere Tech هي شريك موثوق به لجميع احتياجاتك من صب الحقن. اتصل بنا للحصول على سعر لمشروعك الآن.